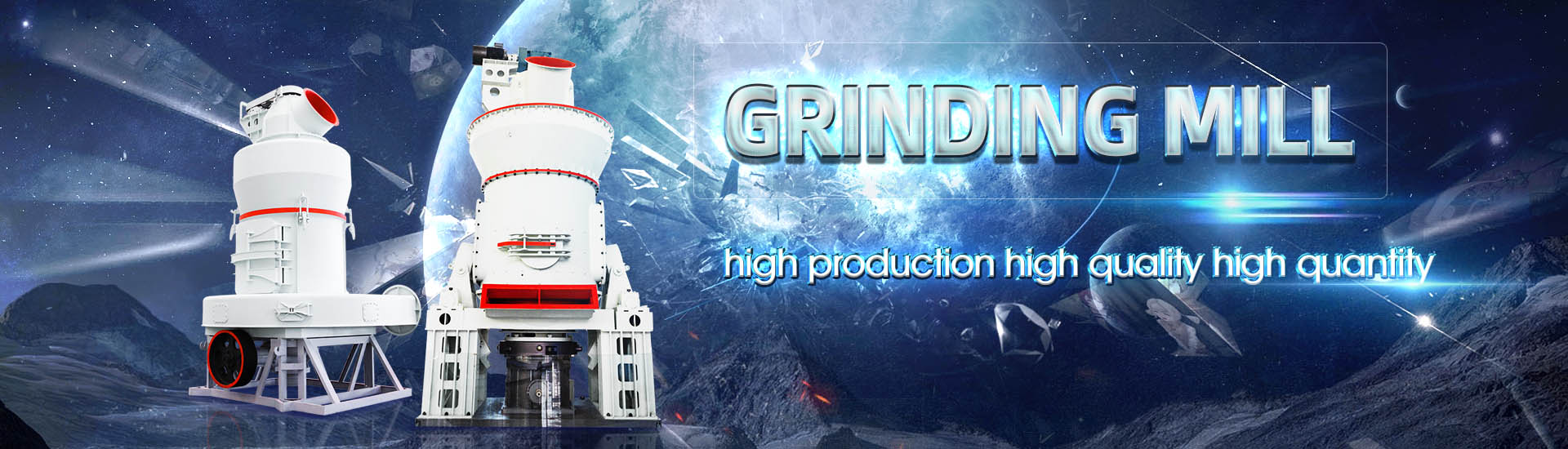
Limestone gypsum desulfurization efficiency
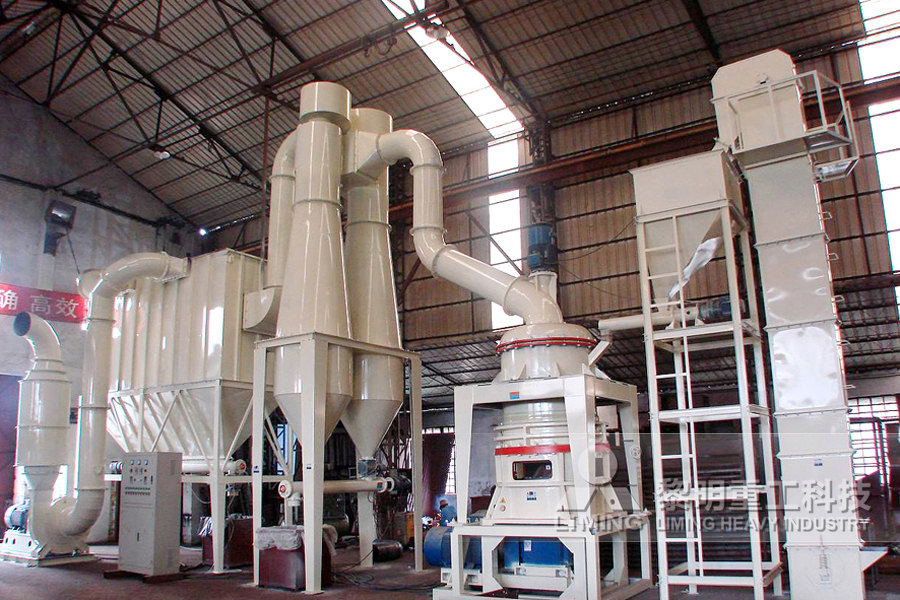
Production and resource utilization of flue gas desulfurized
2021年11月1日 This method is the most used desulfurization method because of its high desulfurization efficiency (90%–98%), large capacity, low cost, and easy recovery of by 2008年11月1日 In this paper, a model of limestone/gypsum wet flue gas desulfurization (WFGD) system was developed based on unsteady theory The models of processes of absorption A model for performance optimization of wet flue gas 2020年11月11日 Wet flue gas desulfurization was simulated to improve gypsum production using lowgrade limestone Highgrade limestone with 94 wt% CaCO3 content is used for Modeling of the wet flue gas desulfurization system to utilize low 2019年3月13日 As a precondition for the optimization of the operating parameters, the target of desulfurization efficiency (η) and SO 2 emissions should be set according to the requirements Moreover, optimal parameters such as Full article: Modeling and optimization of wet flue gas
.jpg)
Diagnosis and Traceability Analysis of Slurry Foaming of Limestone
2023年2月6日 Based on problem diagnosis and sample analysis of a typical case of wet fluegas desulfurization (WFGD) slurry foaming, this study deeply explored and traced the slurry Adding 1030 mmol/L acetic acid, degree of desulphurization was increased to 95% and the limestone utilization was enhanced to 935%, comparison with fine limestone, the New LimestoneGypsum Flue Gas Desulfuization Technology2001年5月19日 A detailed process model of the wet limestone flue gas desulfurization system has been presented This model can be used to calculate indispensable parameters for Model of the Wet Limestone Flue Gas Desulfurization Process for 2019年12月1日 In this study we reviewed the Flue Gas Desulfurization processes and the different options to improve its efficiency as Nonregenerable Wet and Dry methods, the Recent advances in flue gas desulfurization gypsum processes and
.jpg)
Sustainable Operation Strategy for Wet Flue Gas Desulfurization
2024年9月30日 Compared with the original operation condition, the operation under optimized parameters could improve the desulfurization efficiency by 025% on average and reduce 2021年2月1日 LimestoneGypsum Wet Flue Gas Desulfurization Wastewater Treatment Tingting Ni 1,2, Yunzhong Wang 2, Chenghui Huang 2, Dongsheng Jiang 1 and Qingyu Liu 1 Published under licence by IOP Publishing Ltd IOP Conference Series: Earth and Environmental Science, Volume 651, 3rd International Conference on Green Energy and Sustainable LimestoneGypsum Wet Flue Gas Desulfurization Wastewater 2019年6月1日 Coalfired power plants are considered a major source of fine particle emissions in China Aimed to improve the removal efficiency of fine particles during the limestonegypsum wet flue gas desulfurization (WFGD) process, a novel technology using chemical agglomeration to abate the emission of fine particles is presented hereinImproving the removal of fine particles by chemical agglomeration 2009年10月1日 Prediction of SO 2 removal efficiency for wet Flue Gas Desulfurization Author links open overlay panel Binlin Dou a, Weiguo Pan a, Qiang Jin b, Wenhuan Wang a, Yu Li b Show more Add to and limestone/gypsum wet FGD The limestone/gypsum wet FGD is the most widely used because of its high SO 2 removal efficiency, reliable and Prediction of SO2 removal efficiency for wet Flue Gas Desulfurization
.jpg)
Formation and migration of soluble ions in condensable
2024年2月1日 In the limestonegypsum WFGD system, the standard operating conditions were as follows: flue gas volume flow of 06 Nm 3 /h (where Nm 3 refers to a cubic meter at normal conditions of 27315 K and 101325 kPa), inlet flue gas temperature of 120 ℃, desulfurization solution temperature of 40 ℃, pH of desulfurization solution of 55, desulfurizing solution 2021年12月1日 Furthermore, the desulfurization product mainly consisted of gypsum and the decrease in LGL particle size can greatly enhance the gypsum crystal formation These investigations are of significant importance for providing insights to improve WFGD efficiency with the utilization of lowgrade limestoneInsights into the desulfurization mechanism of lowgrade limestone 2008年11月1日 It is well known that sulfur dioxide is not only harmful to health, but also contributes to acidification of soil and water The emission of SO 2 from coalfired boilers is regulated strictly in many countries There are many methods available for controlling the emission of SO 2 of coalfired boilers Because of its high efficiency and reliability, A model for performance optimization of wet flue gas desulfurization 2023年2月6日 Limestonegypsum wet flue gas desulfurization (WFGD) process is widely used in coalfired power plants in China because of its technical characteristics of high desulfurization efficiency, mature process, and strong adjustability (Córdoba, 2017; Wang et al, 2010)With the continuous improvement of atmospheric emission standards, the demands for slurry quality Diagnosis and Traceability Analysis of Slurry Foaming of Limestone
.jpg)
Lime / Limestone Wet Scrubbing System for Flue Gas Desulfurization
aboveThe lime or limestone reacts with the SO 2 in the flue gas to create insoluble calcium sulfite (CaSO 3) as in the equations below Limestone: CaCO 3 (s) + SO 2 (g) → CaSO 3 (s) + CO 2 (g) Lime: Ca(OH) 2 (s) + SO 2 (g) → CaSO 3 (s) + H 2O (l) The resultant calcium sulfite may be further reacted with oxygen to produce gypsum (CaSO ¬4 2022年7月29日 During the desulfurization process of coalfired power plants, there are many related parameters that affect the desulfurization efficiency So it is very difficult to measure the desulfurization efficiency directly In this paper, in order to reflect the relationship between monitoring process parameters and desulfurization efficiency better, a novel prediction model A novel prediction model of desulfurization efficiency based on 2020年5月16日 Numerous mitigation techniques have been incorporated to capture or remove SO2 with flue gas desulfurization (FGD) being the most common method Regenerative FGD method is advantageous over other methods due to high desulfurization efficiency, sorbent regenerability, and reduction in waste handling The capital costs of regenerative methods are Sulfur dioxide removal: An overview of regenerative flue gas 2016年3月1日 Based on the fundamentals of heterogeneous nucleation, a method to eliminate sulfuric acid aerosol associated with water recycling in the process of limestonegypsum desulfurization was investigatedImproving the removal efficiency of sulfuric acid droplets from
.jpg)
Fine Particle Characteristics from Limestone–Gypsum Desulfurization
In the experiments, limestone was used as SO 2 absorbent to simulate the desulfurization processes in the spray scrubber The flue gas temperature at the inlet of spray scrubber was 120 °C and the liquid to gas ratio was 20 L/m 3 22 Measurement Technique The particle concentration and size distribution were measured in real time by means of an electrical low 2022年1月15日 Wet desulfurization technology includes limestonegypsum desulfurization, dualalkali desulfurization, magnesium oxide desulfurization, zinc oxide Prospects Based on the study of dry desulfurization, semidry desulfurization, and wet desulfurization, the research progress of various desulfurization processes, mass transfer mechanisms and process parameters are Summary of research progress on industrial flue gas desulfurization 2002年4月1日 In this article the method of cost optimization of the “Wet Limestone Flue Gas Desulfurization System” is presented The optimization calculations include process and cost modelsOptimum Values of Process Parameters of the “Wet Limestone The limestonegypsum wet desulfurization system includes the following systems: limestone feeding and slurry preparation system, Technological Advantages 1) It is the mature technology and has wide application range with high desulfurization efficiency which is up to 95% 2) Limestone is cheap and easy to get 3) LimestoneGypsum FGD Wet Desulphurization
.jpg)
Limestonegypsum wet flue gas desulfurization based on Cyber
The limestonegypsum wet flue gas desulfurization system has been widely used due to its remarkable desulfurization effect, but there are still problems such as high operation and maintenance costs, difficult control of process indicators, and large energy consumption In view of the above problems, this paper proposes to apply the CyberPhysical System (CPS) to the 2022年6月15日 However, the desulfurization efficiency would be definitely less optimistic for WFGD process when using lowgrade limestone as absorbent in view of its relatively large contents of impurities including CaMg(CO 3) 2, SiO 2, Al 2 O 3 and Fe 2 O 3 [13]As such, possibly effective attempts to upgrade the lowgrade limestone have been actively studied in Enhancement of citric acid on lowgrade limestone wet desulfurization Flue gas desulfurization gypsum (FGDG) is an industrial byproduct generated during the flue gas desulfurization process in coalfired power plants Song H A study on the desulfurization efficiency of limestone sludge with various admixtures J Korean Chem Soc, 52 (2015), pp 479–482 [Google Scholar]Recent advances in flue gas desulfurization gypsum processes 2001年5月19日 Warych et al [43, 44] established a model of the thermal power plant flue gas desulfurization process based on the thin film theory, which simulated the SO 2 absorption process and limestone Model of the Wet Limestone Flue Gas Desulfurization
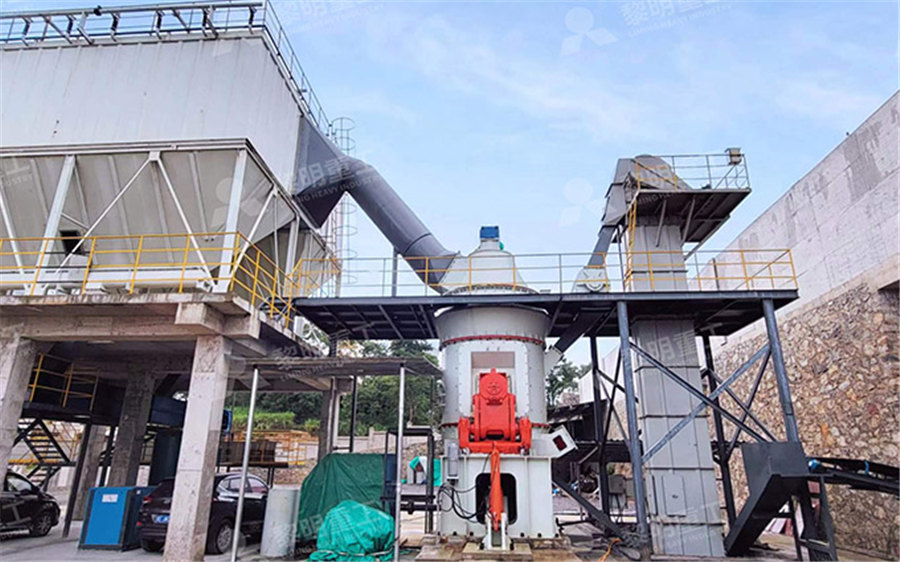
Current Status of Zero Liquid Discharge Technology for Desulfurization
2024年3月20日 Desulfurization wastewater is industrial wastewater with a high salt content, high metal ions, and high hardness produced by flue gas desulfurization of the limestonegypsum method in coalfired power plants This paper summarizes the source of desulfurization wastewater, water quality characteristics, water quality impacts, and other factors, combined 2024年3月18日 2 Limestone (Lime) – Gypsum Desulfurization The limestone (lime) – gypsum method is the most technically mature, widely applied, and stable desulfurization process in the world Its notable advantages include: first, high desulfurization efficiency (in some cases, with a Ca/S ratio of 1 [3], the efficiency can exceed 90%); second, highAdvancement of Environmental Sustainability: A Comparative 2015年11月30日 The flue gas desulfurization (FGD) process is one of the most effective methods to reduce the amount of SO₂ gas (up to 90%) generated by the use of fossil fuel Limestone is usually used as a desulfurizing agent in the wettype FGD process; however, the limestone reserves of domestic mines have become exhausted In this study, limestone sludge A Study on the Desulfurization Efficiency of Limestone Sludge 2015年1月1日 By contrast, as the most mature technology, limestone–gypsum wet flue gas desulfurization (WFGD), primarily due to high efficiency of SO 2 absorption, low investment cost, reliable operation, and low price of absorbent, has been widely used in the most power plants worldwide, especially in China [7], [8], [9]A concise algorithm for calculating absorption height in spray
.jpg)
Limestonegypsum wetmethod flue gas desulfurization additive
Fired power generating unit can give off a large amount of SO in coal fired power generation 2, atmospheric environment is produced pollutionLimestonegypsum Wet Flue Gas Desulfurization Process technique becomes most widely used in the world a kind of desulfur technology because its technical maturity, desulfuration efficiency are high, nearly 400,000,000 kilowatts of the Adding 1030 mmol/L acetic acid, degree of desulphurization was increased to 95% and the limestone utilization was enhanced to 935%, comparison with fine limestone, the desulphurization efficiency and limestone utilization were respective 88% and 929% at the same operating conditions Adding organic acid, buffer capacity of system was enhancedNew LimestoneGypsum Flue Gas Desulfuization Technology2015年3月15日 In order to obtain highquality FGDgypsum from Flue Gas Desulphurisation, the FGD process must attain (1) a high efficiency of particulate controls; (2) causing a low Cl − and F − in FGDgypsum; (3) a high efficiency of the forced oxidation process to oxidise the CaSO 3 ⋅2H 2 O and/or Ca(HSO 3) 2 to CaSO 4 ⋅2H 2 O; (4) using a highpurity limestone to reduce FGD Status of Flue Gas Desulphurisation (FGD) systems from coal 2009年10月1日 Flue gas desulfurization gypsum was found to be very effective in improving the efficiency of limestone scrubbers for removing SO2 from coalfired power plant flue gasesNew LimestoneGypsum Flue Gas Desulfuization Technology
.jpg)
Fluegas desulfurization Wikipedia
Before flue gas desulfurization was installed, the emissions from the Four Corners Generating Station in New Mexico contained a significant amount of sulfur dioxide The G G Allen Steam Station scrubber (North Carolina) Fluegas desulfurization (FGD) is a set of technologies used to remove sulfur dioxide (SO 2) from exhaust flue gases of fossilfuel power plants, and from the 2011年1月14日 Among them, wetprocesses, especially the limestonegypsum process, have earned widespread use due to high SO 2 removal efficiency, reliability and low utility consumption [4], Prediction of SO 2 removal efficiency for wet flue gas desulfurization Energy Convers Manage, 50 (2009), pp 25472553Flue gas desulphurization based on limestonegypsum with a For process optimization, the following constraints were set: 93 wt% gypsum purity, 94% desulfurization efficiency, and 3,710 kg/h total limestone usage, which maximized the mass flow of lowgrade limestone The maximum blending quantity of lowgrade limestone for 2,100 kg highgrade limestone that satisfied the constraints was ~1,610 kg Modeling of the wet flue gas desulfurization system to utilize low 2023年8月22日 SO 2 removal efficiency of wellperforming wet scrubbers is generally more than 90% traditional raw materials, such as natural gypsum and OPC ii) Investigate the various production techniques of FGD gypsum, including wet limestone, wet lime, and seawater scrubbing (flue gas desulfurization) gypsum as a sustainable building A comprehensive review of flue gas desulphurized gypsum:
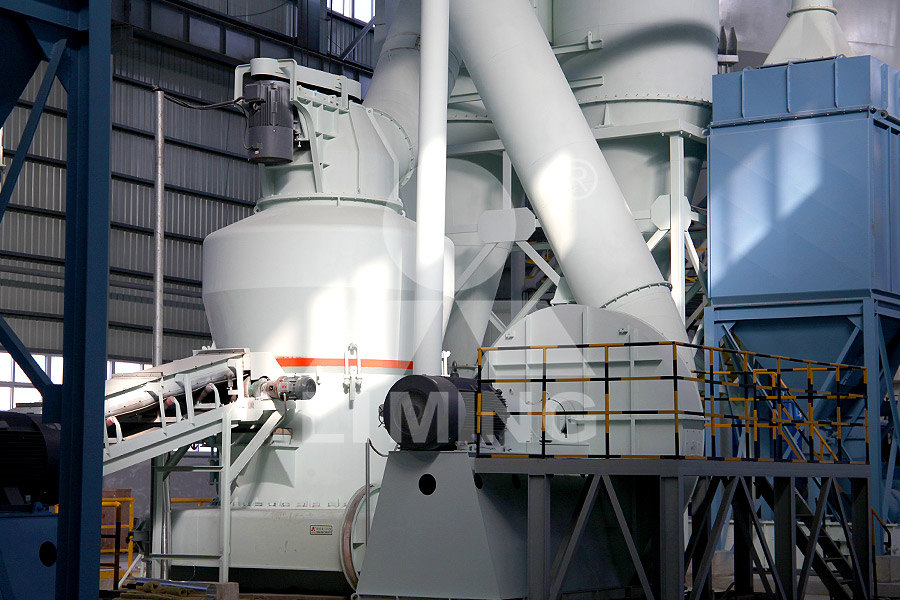
Model of the Wet Limestone Flue Gas Desulfurization Process
2001年5月19日 A detailed process model of the wet limestone flue gas desulfurization system has been presented This model can be used to calculate indispensable parameters for estimating costs and next to minimize capital and operating costs The process model describes most important stage of SO2 removal running in an absorber and a holding tank It includes 2017年7月1日 And due to the higher SO2 removal efficiency and lower utility consumption, limestone/gypsum Wet Flue Gas Desulfurization (WFGD) system usually with correspondent production of gypsum is mostly applied, and occupies more than 90% of the market share in China (Antonio et al, 2007; Dou et al, 2009; Shi et al, 2017; Gisi et al, 2017)Enhancing the recovery of gypsum in limestonebased wet flue Improving the removal of fine particles by chemical agglomeration during the limestonegypsum wet flue gas desulfurization process Lei Zhou1, Yong Liu1, Lvyuan Luo1, Zhulin Yuan1, Linjun Yang1,⁎, Hao Wu2,⁎ 1 Key Laboratory of Energy Thermal Conversion and Control of Ministry of Education, Southeast University, Nanjing , ChinaImproving the removal of fine particles by chemical agglomeration 2022年8月15日 To achieve highefficiency desulfurization at high SO 2 concentrations, dualloop WFGD technology has been proposed and has attracted attention [34], Calcium bisulfite oxidation rate in the wet limestone gypsum flue gas desulfurization process Environ Sci Technol, 33 (11) (1999), pp 19311935 View in Scopus Google ScholarLimestonebased dualloop wet flue gas desulfurization under
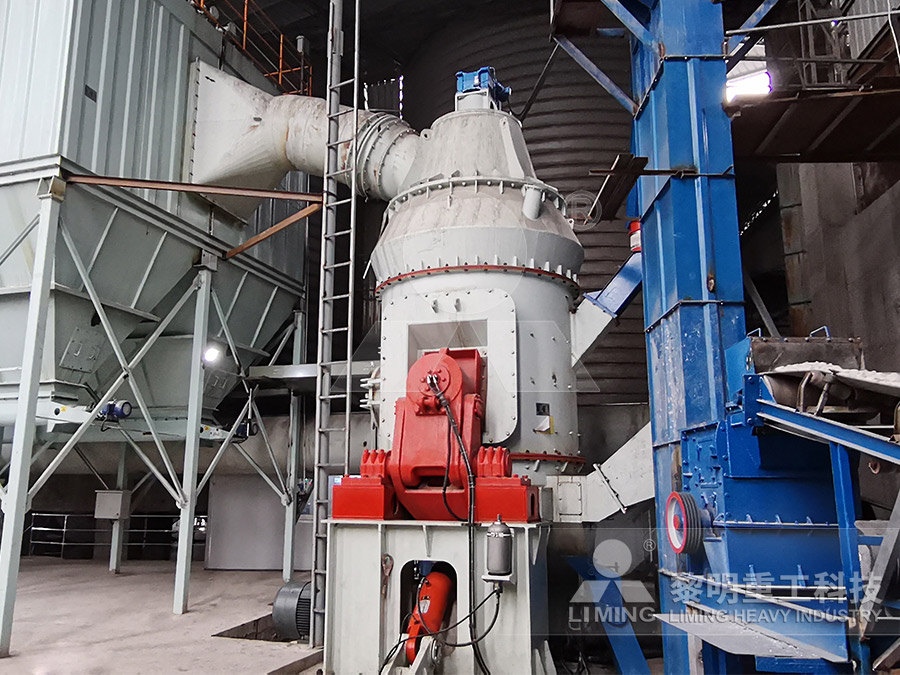
Investigation on Removal Characteristics of SO3 Acid Mist
2018年10月29日 With the increasing attention on SO3 emission in coalfired power plants, the removal of SO3 acid mist in a limestonegypsum wet flue gas desulfurization (WFGD) system was investigated The generation properties of SO3 acid mist were analyzed with an experimental system, and the effects of flue gas properties and technologies for ultralow emission on the 2016年6月16日 Request PDF Abatement of Fine Particle Emission by Heterogeneous Vapor Condensation During Wet LimestoneGypsum Flue Gas Desulfurization The fine particles in desulfurized flue gas comprise Abatement of Fine Particle Emission by HeterogeneousDownload scientific diagram Schematic diagram of the limestonegypsum spraying desulfurization system from publication: A concise algorithm for calculating absorption height in spray tower for Schematic diagram of the limestonegypsum spraying desulfurization 2024年9月30日 The objectives of optimization in this study include unit energy consumption, desulfurization efficiency, limestone slurry usage, A Concise Algorithm for Calculating Absorption Height in Spray Tower for Wet Limestone–Gypsum Flue Gas Desulfurization Fuel Process Technol 2015, 129, 15–23 [Google Scholar]Sustainable Operation Strategy for Wet Flue Gas Desulfurization
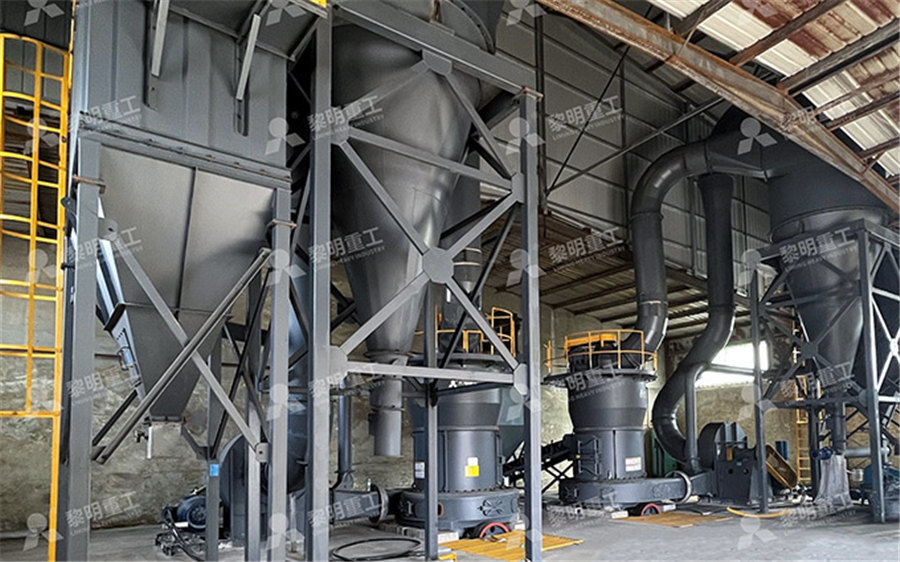
Energy conservation and efficiency improvement by coupling
2021年2月1日 Limestone–gypsum wet flue gas desulfurization (WFGD) is the most effective desulfurization technique However, to achieve ultralow SO 2 emissions, the efficiency of WFGD should be improved and its energy consumption reduced To address these aims, a technology of coupling WFGD with condensation desulfurization using a condensing heat exchanger (CHE)