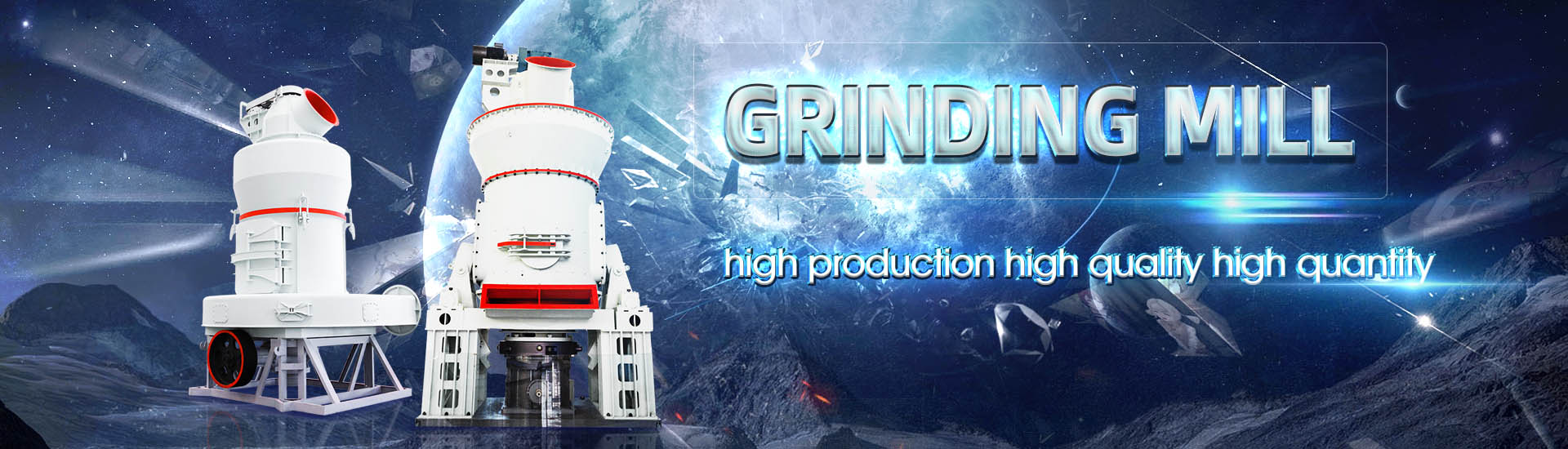
Alkaline furnace lining material powder making process
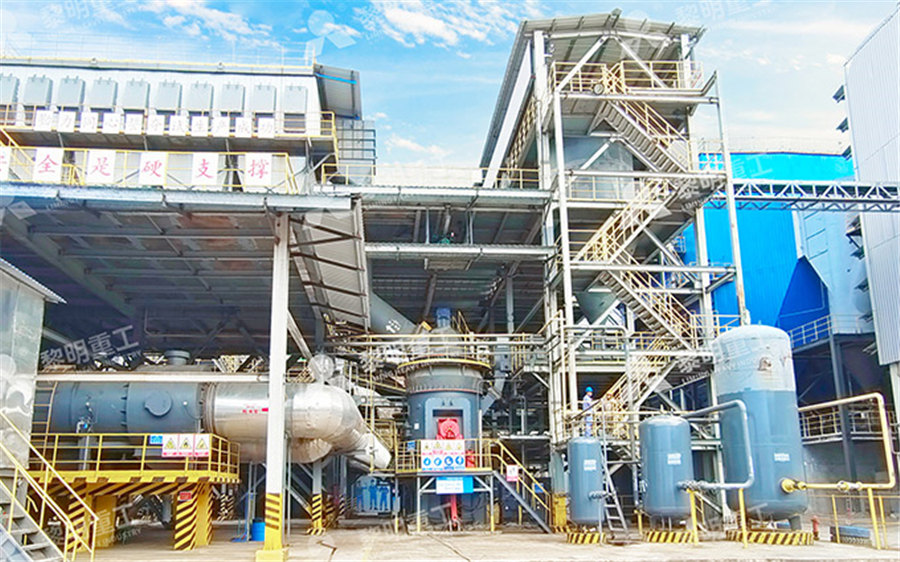
Innovative Refractory Technology for Coreless Induction Furnaces
A new range of silica based lining materials (Reference Figure 1) has been developed utilizing advanced large grain technology (ALGT) The material employs a grain size of up to 12 mm in Main objective of this thesis is to characterize the physical properties of Alumina (Al2O3) based refractory applied on inductionfurnace lining, which are: to find out the size and shape of PHYSICAL CHARACTERIZATION OF ALUMINA (Al2O3) BASED 2019年9月16日 For the lining of induction furnace, refractory materials are normally monolithic refractories made of dry powder which is required to be compacted with homogenous density Further, there are heat losses by Refractory Lining of Coreless Induction Furnace2024年1月1日 Alkaline furnace lining is made of magnesia with magnesium oxide content more than 85%, used for smelting of special steel and nickelbased alloy Generally, the crucible is Induction Furnace Melting SpringerLink
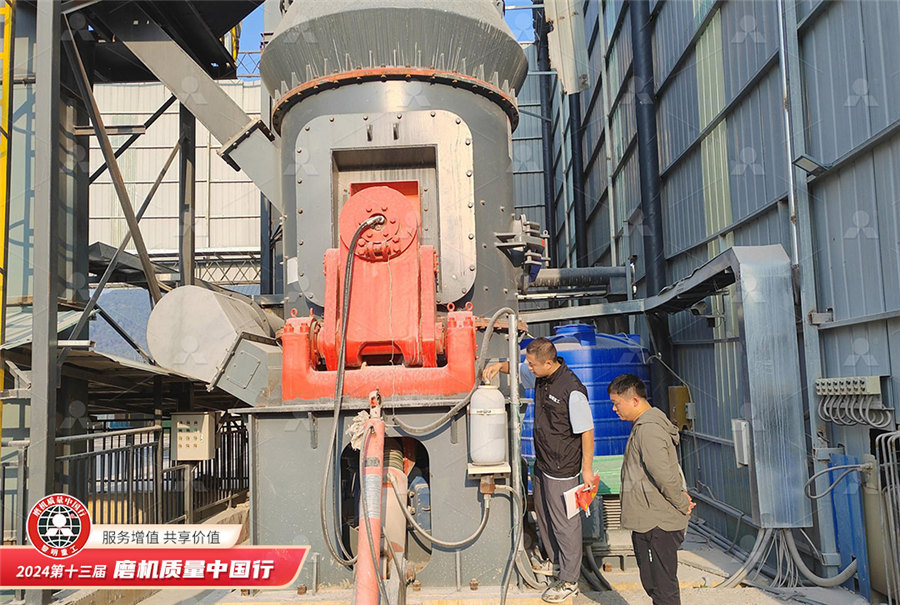
Induction Furnace Lining and Industrial Vibrator Design Theseus
Refractory material lining requires two steps for induction furnaces: Floor portion: Floor material is filled and compacted Wall portion: Liner form is positioned on the bottom refractoryThis means lining concepts and process solutions for any type of primary furnace, slag cleaning furnaces, electric arc furnaces (AC and DC), PS converters, anode furnaces, ladles and Lining Concepts for the Nonferrous Metal Industry RHI MagnesitaInduction furnace melting is a process of melting metal by using electromagnetic induction to produce eddy current heating in metal materials in induction furnace, also called induction Induction Furnace Melting2023年7月5日 Furnace lining refractory material according to the simulation results should focus on refractoriness under load, wear resistance, high temperature mechanical properties and Effects of induction furnace conditions on lining refractory via
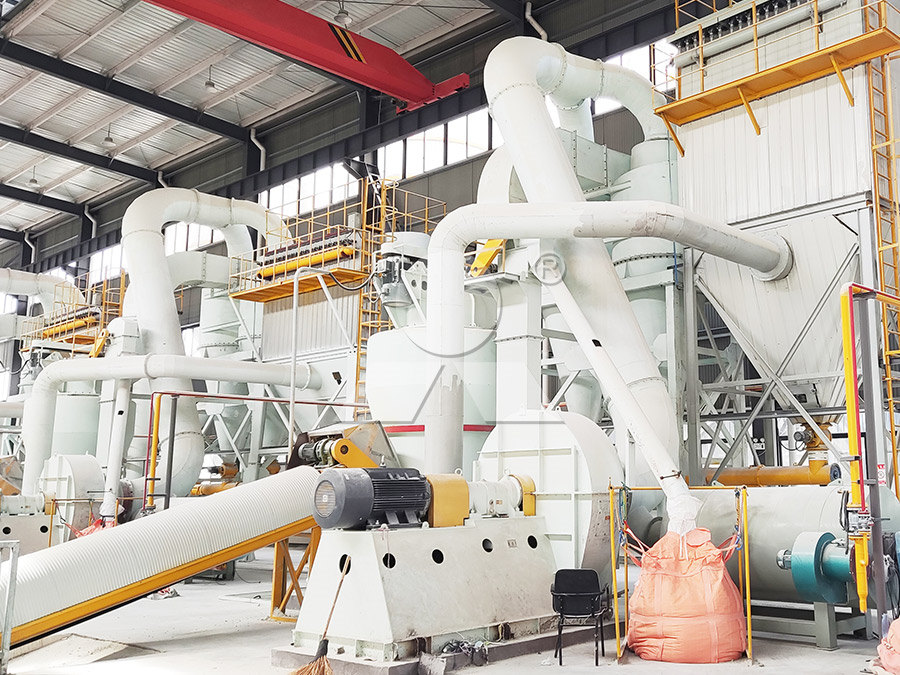
Powder Processing Furnaces Thermal Systems From 500 to 3000°C
Harper is trusted worldwide for high temperature powder processing furnaces for powders and granular materials, including inorganic chemicals, catalysts, phosphors and powdered metals2024年3月14日 The refractory materials used in acid steelmaking are the same as those used in smelting cast iron, while neutral or alkaline refractory materials are used in alkaline steelmaking 3 When making steel in small coreless Selection and application of nine different refractory Lining materials for coretype induction furnace The cored or channel induction furnace lining should be made of refractory castables that are resistant to corrosion, and erosion resistance and have high chemical stability Usually, Induction Furnace Refractory AGRM Refractories2024年8月19日 This material has a good effect on a 16ton industrial frequency copper melting furnace in a copper material factory, and the furnace lining life exceeds three years (more than 700 furnaces) Moreover, the furnace lining size does not change by more than 5% from beginning to end, thus ensuring the normal use of the furnace with high efficiency from Refractory Materials for 30 tons Copper Melting Furnace Lining Materials
.jpg)
ALKALINE CARBONATES IN BLAST FURNACE PROCESS
ALKALINE CARBONATES IN BLAST FURNACE PROCESS Received Primljeno: Accepted – Prihvaćeno: posits on the refractory lining of blast furnaces and they accelerate their wear [3] Heavy metals have similar ef blast furnace raw material The amount of Na 2 2020年6月10日 Globally, steel products have been mainly manufactured via primary steelmaking process that constitutes two major routes These are integrated Blast Furnace–LD Process/Basic Oxygen Furnace Route (BF–LD/BOF) and Directly Reduced Iron–Electric Arc Furnace (DRI–EAF) steelmaking practiceIron and SteelMaking Process SpringerLinkHigh duty lining developed to withstand elevated temperatures and retain a good level of powder at the back face Ceramic: 1700* 1750† Coral SMC: Incorporates complex chromes for improved slag resistance Ceramic: 1700* 1750† Coral 85: High performance lining designed for large furnaces operating at high temperatures Ceramic: 1700* 1750 Coreless Induction Furnace Linings Capital Refractories2024年3月4日 Blast furnace dust (BFD) is the solid powder and particulate matter produced by dust removal process in ironmaking industry The element composition of BFD is complex, and a direct return to sintering will lead to heavy metal enrichment and blast furnace lining corrosion In recent years, the application of BFD in wastewater treatment has attracted widespread Review in application of blast furnace dust in wastewater
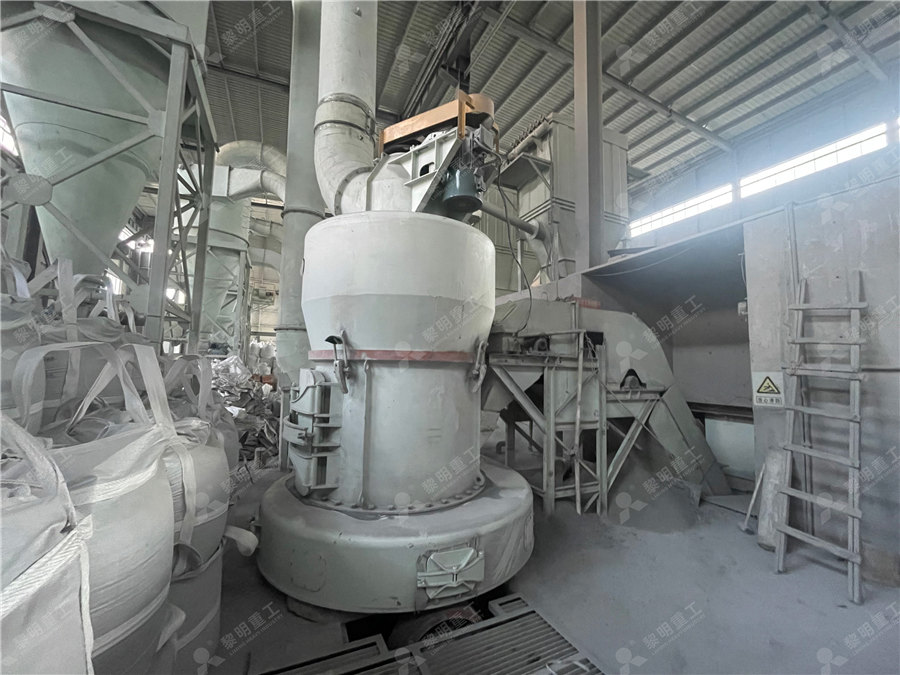
EFFECT OF ALKALINE ELEMENTS ON COKE STRUCTURE UNDER BLAST FURNACE
2016 D Ç î ñ Z r î ó Z î ì í ò U v } U Ì Z Z µ o ] U h 81 Table 4 Effect of K on CRI and CSR Sample Property (CRI/CSR) No Added K Medium K Content High K ContentThe lining practice best suited to a particular furnace depends upon the capacity and design of the furnace, operation practice adopted during making of a heat, and furnace output For successful and consistent performance of the lining, the important aspects are (i) use of proper grade and quality of the lining material, (ii) careful and systematic lining practice, and (iii) consistency in Induction Furnace and Steelmaking IspatGuruSmelting Process 1) The Furnace Lining Materials Required Shall Be Selected According to the Type of Smelting Steel Some steel grades are only suitable for smelting in alkaline furnaces When smelting high manganese steel grades and alloys in an acid furnace, Therefore, during the induction furnace steel making process, Induction Furnace Steel Making Hani Metallurgy2016年3月21日 With increasing demand of highquality clean steel, cleanliness is of paramount importance in steel production and casting Tundish plays an important role in controlling the continuously cast steel quality as it links a Tundish Technology for Casting Clean Steel: A Review
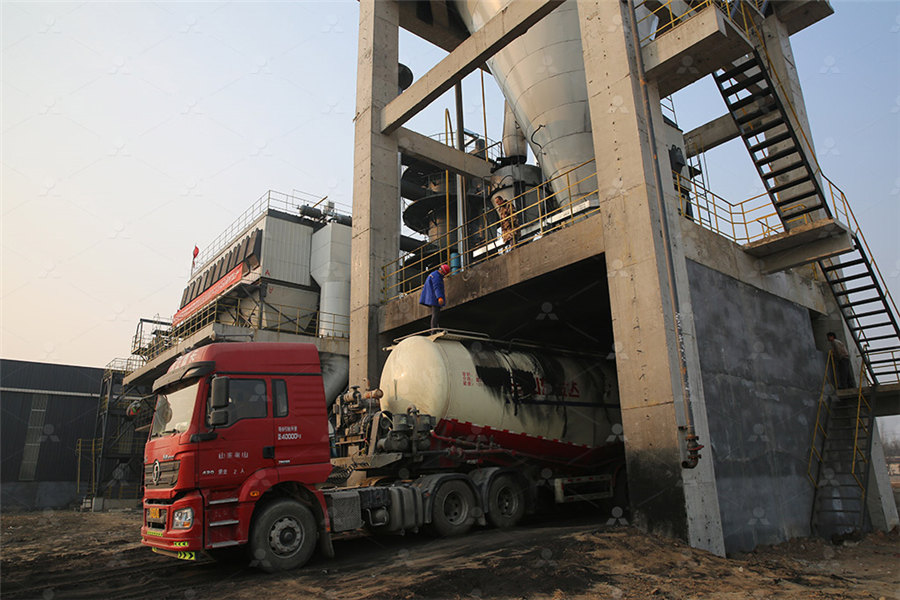
Design, fabrication and properties of lightweight wear lining
2022年3月1日 As shown in Fig 1, a conventional refractory lining structure has a wear lining, safety layer, and an insulation layerThe wear lining resists erosion, wear, corrosion and thermomechanical loads of molten melts, while the insulation layer reduces the thermal transfer through refractory lining2017年5月30日 4 Select the right material for furnace rebuilds Some repairs identified by infrared thermology scanning can be too large to address online, and instead, the unit must be shut down for a furnace reline or process heater Ensuring Effective Furnace Lining Efficiency Thermal In order to ensure electromagnetic induction efficiency, the wall of the crucible is thin, and the inner side bears the erosion and pressure of hightemperature molten steel The furnace lining of coreless induction furnace (crucible) has two types: acidic and alkaline Acid furnace lining is made of quartz sand with silica content more than 98%Induction Furnace Melting SpringerLink2021年5月23日 The prevention of carbonphase oxidation in magnesiacarbon bricks is vital for improving their performance The effect of Al and Si metal powder addition on the oxidation of MgOC bricks was Indispensability and Vulnerability of Magnesiacarbon Bricks for

Five Tips for Achieving Furnace Lining Efficiency
Thermal Ceramics is a business of Morgan Advanced Materials Five Tips for Achieving Furnace Lining Efficiency By Steve Chernack, Morgan Advanced Materials lining without the proper expansion joints, the brick could grow and end up pushing the entire lining off the furnace wall Tip 5 – Proper installation is key to success2024年8月19日 This material has a good effect on a 16ton industrial frequency copper melting furnace in a copper material factory, and the furnace lining life exceeds three years (more than 700 furnaces)Refractory Materials for 30 tons Copper Melting Furnace — Lining 2023年9月5日 Powder metallurgy is a manufacturing process that involves using metal powder, or a mixture of metal powder and nonmetal powder, as a raw material The powder is then formed and sintered to produce a range of metal materials, composite materials, and various types of articlesPowder Metallurgy: A Comprehensive Guide for Beginners2020年4月15日 One of the causes of corrosion and destruction of refractory lining in pyrometallurgical processes is the occurrence of melts in the most intensively altered zones of refractory material(PDF) Causes of the Quartzite Lining Destruction during Operation
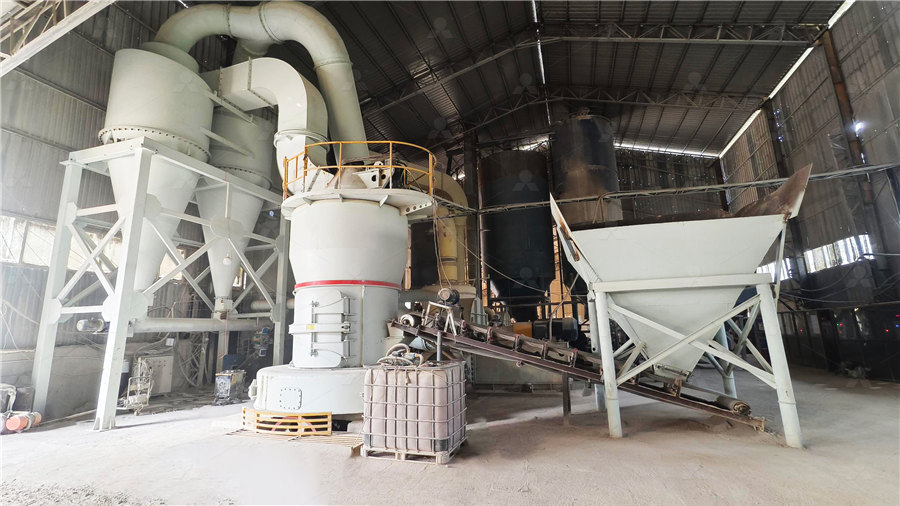
Traditional Electric arc furnace steelmaking smelting process
2024年2月19日 The third phase of the smelting process of traditional Electric arc furnace steel making, refining and alloying in one furnace, including the melting period, oxidation period and reduction period In the furnace, the melting of scrap steel, dephosphorization, decarburization, degassing, etc of the molten steel must be completed Remove inclusions and raise 2024年7月22日 Performance Requirements for Electric Furnace Lining Refractory Materials There are two types of refractory materials used in electric furnace linings: alkaline and acidic At present, most electric furnaces use alkaline linings, and acidic lining electric furnaces are only used to produce steel castings or gray cast ironElectric Furnace Refractory Lining Material RS Refractories Materials2019年7月19日 Carbon may also be introduced to a much smaller extent from fluxing materials and other process additives that are charged to the furnace Using the default values in the IPCC Guidelines for iron (004) and steel (001) for the fraction of carbon gives an emission factor of 011 tCO 2 /tcs for carbon removed from the iron as CO 2 Basic Oxygen Furnace: Most Efficient Technologies for Greenhouse 2014年1月1日 The OH process started as an acid process with acid lining in the furnace, and then adopted the basic lining and new steelmaking practice as well The process had two main differences relative to the Bessemer process: (1) pig iron and scrap of any composition could be melted in any ratio and (2) better control of the steel quality was possibleConverter Steelmaking ScienceDirect
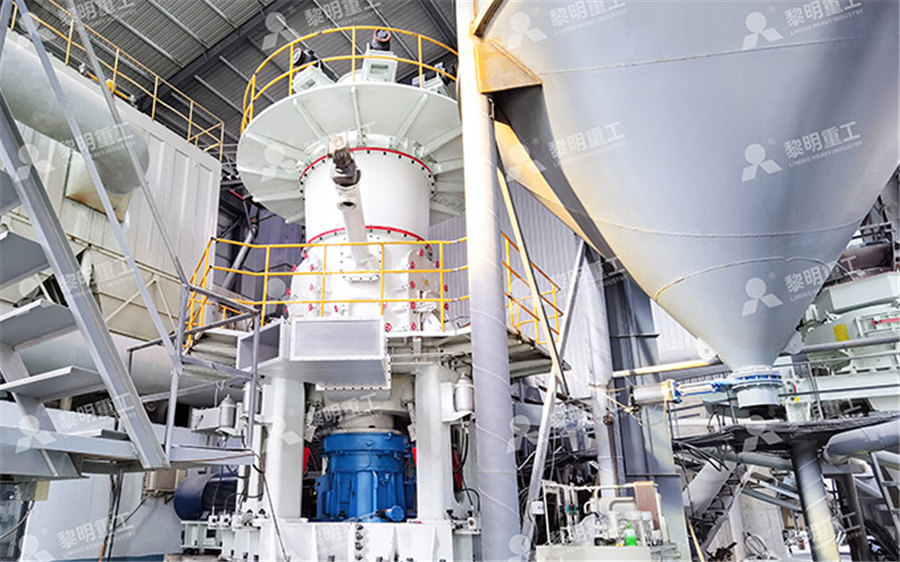
Powder Detergent: Ingredients Manufacturing Process Explained
2021年6月21日 Powder detergent spray drying process explained Modern powder detergents comprise a lightweight, freeflowing, puffed mass In those terms, compared to dry mixing and agglomeration processes, spray drying delivers a superior productRefractory bricks in a torpedo car used for hauling molten iron In materials science, a refractory (or refractory material) is a material that is resistant to decomposition by heat or chemical attack and that retains its strength and rigidity at high temperatures [1] They are inorganic, nonmetallic compounds that may be porous or nonporous, and their crystallinity varies widely: they may Refractory WikipediaThermal Ceramics is a business of Morgan Advanced Materials Five Tips for Achieving Furnace Lining Efficiency By Steve Chernack, Morgan Advanced Materials lining without the proper expansion joints, the brick could grow and end up pushing the entire lining off the furnace wall Tip 5 – Proper installation is key to successFive Tips for Achieving Furnace Lining Efficiency2023年10月20日 Thermodynamic calculations were carried out to study the extent of MgO solubility in a ladle furnace slag using FactSage™ v82 FactPS and FToxid databases []Figure 3 illustrates the calculated isothermal section of the Al 2 O 3CaOMgO slag at 1650 °C (stable liquid phase regions corresponding to different SiO 2 contents from 5 wt% to 20 wt% have Postmortem Analysis of MagnesiaCarbon Refractories from
.jpg)
Ramming Mass in Steel Industries Enhancing Melting Processes
Use Case: Used in basic oxygen furnaces (BOF) and other alkaline steelmaking processes Key Features: • Superior resistance to alkaline slags • Wellsuited for environments with high basicity Applications: • Basic ramming mass is essential for furnaces where the steelmaking process involves the use of alkaline materials 3 Neutral 2005年11月30日 Typically, the refractory lining of a blast furnace consists of a combination of different refractory materials chosen for different portions of the furnace, as well as distinct process conditions Wear mechanism for blast furnace hearth refractory lining2003年1月20日 Thermal shock resistance The mm test specimens were heated to 1100uC, under a reducing atmosphere, at a rate of 125 K h–1, and kept at this temperature for 3 hAfter this soaking step Wear mechanism for blast furnace hearth refractory lining2020年5月6日 Refractory Lining of the Electric Arc Furnace satyendra; May 6, 2020; 0 Comments ; AC EAF, DC EAF, EAF, EBT, Fettling, guniting, hearth, magnesite, Monolithic lining, roof, Taphole,; Refractory Lining of the Electric Refractory Lining of the Electric Arc Furnace –
.jpg)
The Chemistry, Physics and Manufacturing of Glaze
The process is triggered by low melting compounds (like boric acid, borax, alkaline carbonates, feldspars) and subsequently accelerated by them to melting and dissolve the more refractory materials like quartz sand, zircon flour, 2023年1月28日 Many binders contain alkali metal components such as K2O and Na2O The lowmelting compound formed by alkali metal and alkaline earth not only plays a cementing role, but also catalyzes carbothermal reduction But Iron ore pellets for blast furnace a technical guideElectric furnace lining tools: reduce the labor intensity of workers; improve the quality of furnace construction and furnace life cycle 7: Crucible for intermediate frequency furnace: Silicon carbide, clay graphite, white corundum crucible: 8: Intermediate frequency furnace lining materialCentrifugal atomizing metal powder making machine cdocastHarper International's Powder Processing Furnaces Continuous High Temperature Kilns Calciners for Powders and Granular Materials Made in the USAPowder Processing Furnaces Thermal Systems From 500 to
.jpg)
Effects of induction furnace conditions on lining refractory via
2023年7月5日 Coreless induction furnace is one of the most widely used equipment in the steelmaking sector, while the lining refractory are the key factors in determining the lifetime of the induction furnace The multiphysics field dominates the operating conditions of the lining refractory which can be wellstudied using numerical simulation techniques Based on the 2023年11月23日 Abstract Ladle slag is a byproduct formed during the ladle refining stage of steel making It is a dusty material that has been considered industrial waste This concrete had lower compressive strength but could be used as a furnace lining in hightemperature furnaces making the process energyefficient 59Ladle Furnace Slag: Synthesis, Properties, and Applicationsin induction furnace lining that are monolithic This dry powder must be compacted with homogenous density Because lining material’s lifetime, depends on this fact Refractory ramming process has been done by pneumatic vibrators operated manually so far Doing this process by hand cannot guarantee homogenous ramming which willInduction Furnace Lining and Industrial Vibrator DesignCoral CXL General purpose lining with a wide melting temperature range Coral HB High duty, hard wearing lining suitable for most melting applications Coral SXL High duty for elevated temperatures Coral Vac High duty for high temperatures Coral SMC Incorporates complex chromes for improved slag resistance Coral 85 High performance lining for large furnaces Refractories for Induction Furnaces
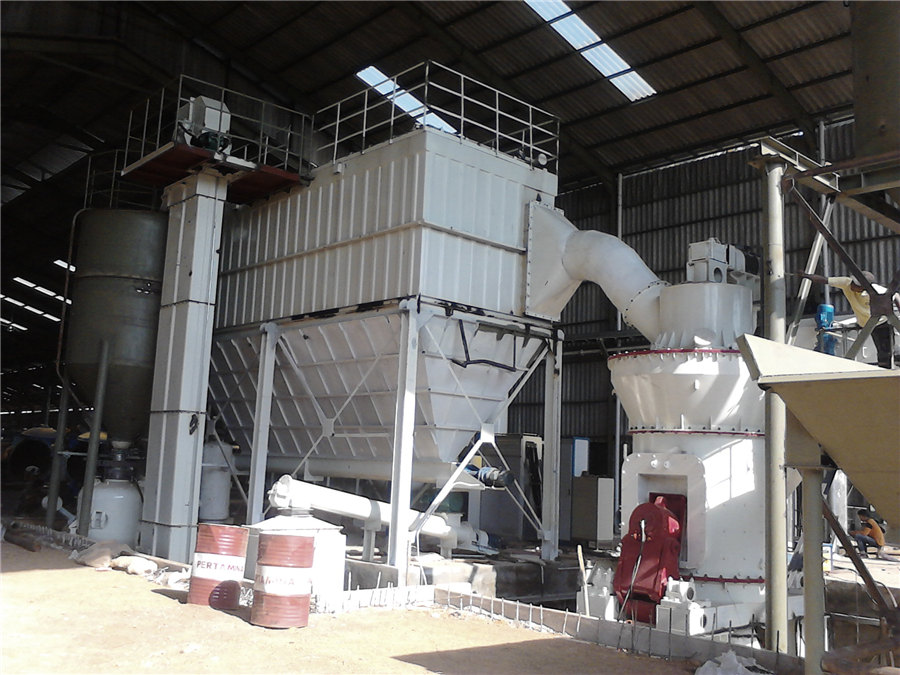
Induction Furnace Lining Procedure – Melting Hani Metallurgy
②Magnetic separation, completely remove magnetic impurities, prevent accidents such as leakage or breakdown induction furnace: ③ The raw materials are dried slowly at a temperature above 200°C and kept warm for a period of time Induction furnace lining sintering is the process of forming the lining into a solid whole