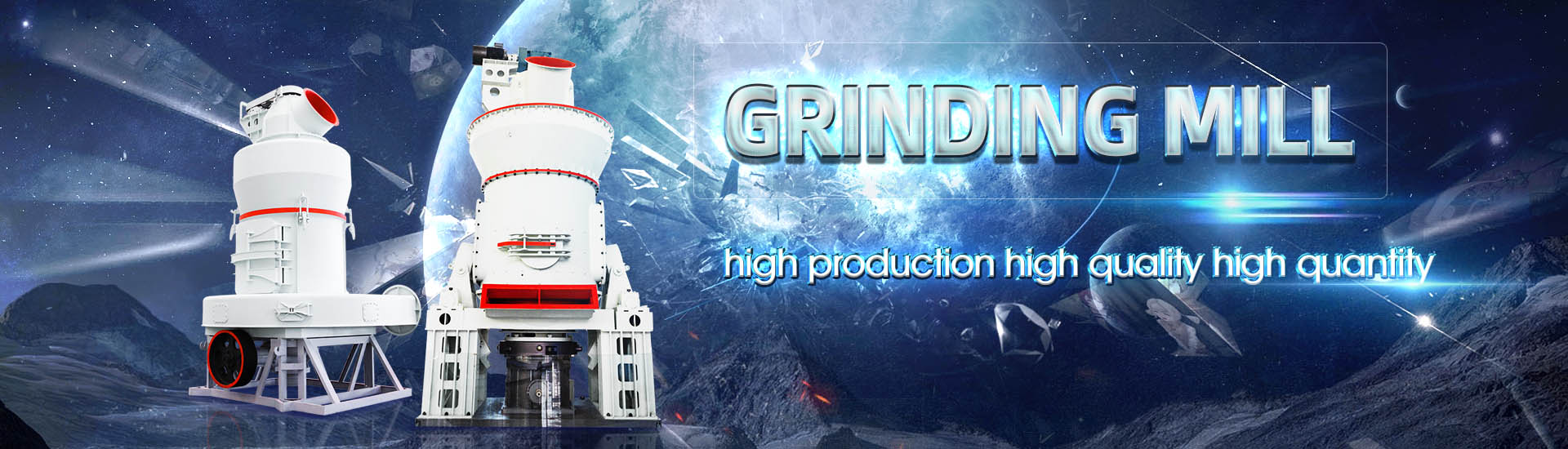
Coal mill steel ball model
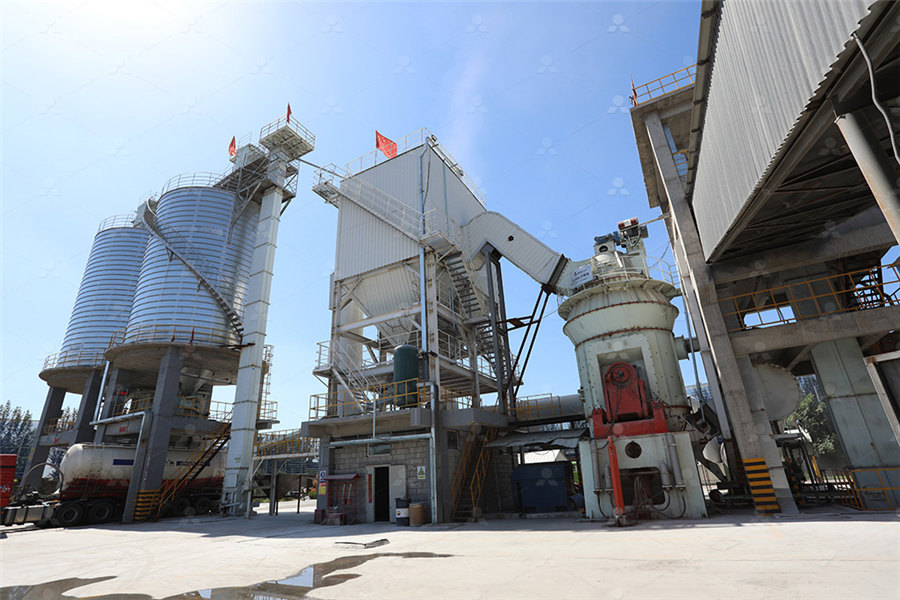
Model Predictive Control of Duplex Inlet and Outlet Ball Mill
2019年3月7日 Zeng et al established the mathematical model of duplex inlet and outlet ball mill system by taking the humidity of coal as an important parameter and adopted the extended Ball adding device is low speed coal mill, especially the vitals of doubleinlet and doubleoutlet steel ball coal mill positive pressure direct blowing powder systemLow speed coal mill is when grinding coal dust, and the steel ball in mill constantly weares and teares, thereby cause grinding, interior ball load declines, the reduction of exerting oneselfFor this reason, need to adopt ball Ball charging device for steel ball coal mill Google PatentsReliable coal pulverizer performance is essential for sustained fullload operation of today's power plants An effective pulverizer must be capable of handling a wide variety of coals and accommodating load swings in utility boilers as large Reliable Coal Pulverizers and Mills Babcock Wilcox2019年10月1日 Comprehensive treatment,we should have a test on the 300 MV unit steel ball coal mill pulverizing systemAt the same time,analyze the main operating parameters before modificationTransform the pulverizing system and optimize the run mode of the pulverizing system by comprehensive treatmentSo we can control the pulverizing unit consumption under Optimization and transformation of 300MV units steel ball coal mill
.jpg)
Vertical Grinding Mill (Coal Pulverizer) Explained saVRee
Introduction This article concerns itself with vertical grinding mills used for coal pulverization only (coal pulverizers), although vertical grinding mills can and are used for other purposes The 3D model in the saVRee database represents a vertical grinding bowl millOther grinding mill types include the ball tube mill, hammer mill, ball and race mill, and , roll and ring mill2016年8月1日 Given that the continuous rotation of coal mill cylinder, the steel balls and raw coal inside coal mill are constantly thrown up and smashed down, thus the instantaneous fill level signal has a significant noise component Control Modeling and control of ball mill system considering coal moisture2019年11月7日 Comprehensive treatment,we should have a test on the 300 MV unit steel ball coal mill pulverizing systemAt the same time,analyze the main operating parameters before modificationTransform the Optimization and transformation of 300MV units steel ball coal mill 2024年2月19日 The ratio of steel balls in the ball mill depends on the effective length of your mill, whether it has a roller press, the size of the feed particles, the lining and structure used, the expected sieve residue fineness and ratio, how many chromium balls to operate, and the rotation speed How much and other factors make a comprehensive judgmentBall Mill Steel Balls: Quality And Gradation JXSC Mineral
.jpg)
Modular HO Steel Mill Coal Mine layout Model Train Forum
2016年1月25日 I just finished designing an HO scale model railroad layout This layout is based on the steel mill and coal mine operations of the Union Railroad in Pittsburgh Pennsylvania The layout is 140" by 80" or about 115 ft by 65 feet Or if you prefer metric about 35 meters by 2 meters It's a very small table layoutThe paper presents a mathematical model and its Matlab/Simulink realization for ball mill coalpulverizing system (BMCPS) Based on the analysis of mass and energy balance, the physical models for all controlrelated subprocesses of BMCPS are developed respectively Then the integrated dynamic mathematic model is constructed with Matlab/Simulink Validation using Modeling and simulation of ball mill coalpulverizing systemFigure 1 Typical Arrangement of the Riley Ball Tube Mill System DESCRIPTION OF PULVERIZERS AND FUEL SYSTEMS Ball Tube Mill The Ball Tube Mill (BTM) is a cylindrical lowspeed grinding mill It consists of a steel barrel, lined with cast abrasionresistant liners and partially filled with hardened steel balls Coal and preheated primary airA Comparison of Three Types of Coal Pulverizers Babcock PowerThe four most common coal pulverizers types are: BallTube Mills This type of mill consists of a rotating tube filled with cast alloy balls Coal is introduced through two hollow trunnions on each side of the tube As the tube rotates, the balls tumble onto the coal, crushing and pulverizing it Coal Pulverizer – Power Plant Pall Corporation
.jpg)
Modeling and control of ball mill system considering coal moisture
2016年4月1日 This study analyzes the dynamic characteristics of duplex inlet and outlet ball mill direct firing pulverizing system A mass and energy balancebased model is built by thermodynamic analysisObserverBased and Regression ModelBased Detection of Emerging Faults in Coal Mills Peter Fogh Odgaard, Sten Bay Jørgensen, in Fault Detection, Supervision and Safety of Technical Processes 2006, 2007 2 THE COAL MILL The work presented in this paper, is based on a Babcock MPS 212 coal mill used at Elsam’s Nordjyllandsværktet Unit 3 However, the Coal Mill an overview ScienceDirect TopicsThere are various high quality and durable mgs doubleinlet doubleoutlet steel ball coal mill here in our factory As one of China's leading mechanical equipment manufacturers and suppliers, we also support customized service on mgs doubleinlet doubleoutlet steel ball coal mill Welcome to contact us for detailsMGS Doubleinlet Doubleoutlet Steel Ball Coal Mill SNM Pulverized coal preparation system is one of main backup system of fuelburning power plant, because barrelshaped steel ball mill is the strongest to the adaptability of coal, is domestic most widely used a kind of coal pulverizerCoal pulverizer is the key equipment of pulverized coal preparation system, and can it normally move and whether operate in optimum condition, is CNA Thermal power plant ball mill load softsensing

A unified thermomechanical model for coal mill operation
2015年11月1日 Dynamic coal mill model based on conservation laws and empirical relations These mills include bowl mills, roller mills, ball – race mills, etc The details about its operation are provided in (Rees Fan (2003), Wikipedia (2014), Coal pulverization (2005), Central Electricity Generating Board (1971))Figure 2 Tube Ball Mill Structure II MATHEMATICAL MODEL OF TUBEBALL MILL The procedure for coal mill modelling can be broken down into the following steps: 1) ΔTo derive the basic mill model dynamic equations through analyzing the milling process, applying physics and engineering principles and integrating the knowledge of experienced engineersDevelopment of a Tubeball Coal Mill Mathematical Model Using 2009年5月25日 Stable control of a coalpulverizing system with balltube mill usually cannot be hold due to some disturbances, such as coal hardness and steel ball wearing, etc A hierarchical structure with a direct control layer and a setpoint optimization layer is applied to this typical system Based on steadystate gain models of different operating points, a grid search method Setpoint optimization and control of coal Semantic Scholar2014年5月1日 Tube mills use steel balls as grinding media A simulation model combining milling circuit and ball size distribution was used to determine the best makeup ball charge An analysis of the energy split for grinding coal/calcite mixture in a ballandrace mill Minerals Engineering, Volume 93, 2016, Exploring ball size distribution in coal grinding mills
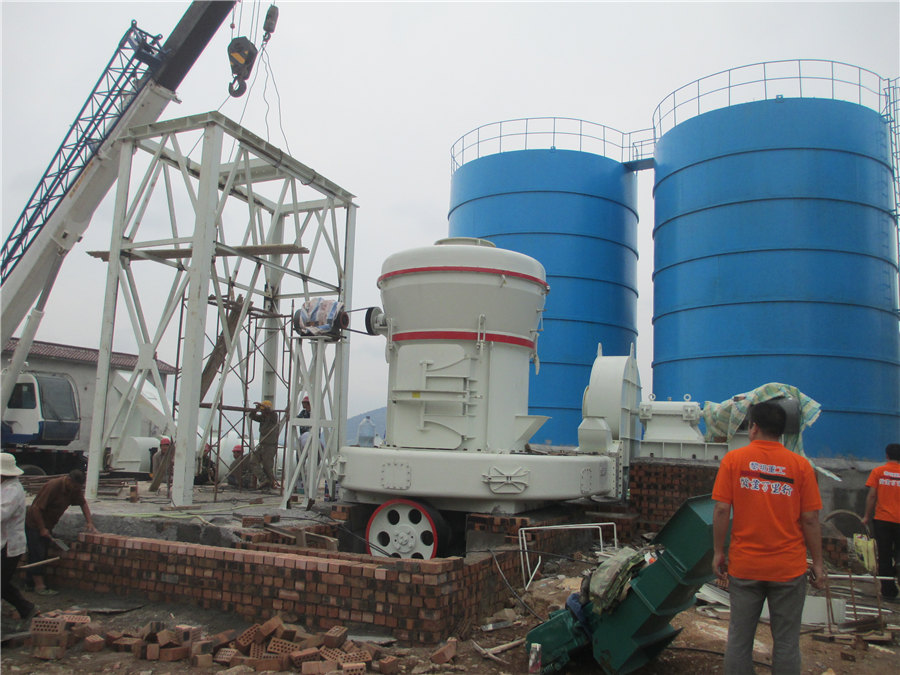
Modeling and control of ball mill system considering coal moisture
2016年8月1日 Fig 1 shows the structure of a duplex inlet and outlet ball mill The system is equivalent to two parallel cylinders joined together in one ball mill to achieve high milling efficiency Milling work is carried out by the collision, squeezing and grinding of the steel balls inside the mill The working principle described as follows [10]They use steel balls to crush and grind the coal material, 20tph Coal Ball Mill For Clean Coal Powder Production Line In Vietnam Read More 85tph Cement Ball Mill Put Into Operation In Indian Cement Plant Read More Previous slide Next slide Free Material TestingWhat is a Coal Grinding Mill1 When you use the ball mill for the first time In the first time, the grinding steel balls must be added at 80% of the maximum ball loading capacity of the ball mill And three sizes of balls, namely, large, medium and small, are required for Choose the Best Grinding Steel Balls for Your Ball Mill 2023年4月27日 At present, the economic benefits of double inlet and double outlet ball mills, which are commonly used in coalfired power plants, need to be improved Based on this, this paper explores the factors influencing the output of double inlet and double outlet ball mill by establishing the output system of double inlet and double outlet ball millSystem dynamics model of output of ball mill Sciendo
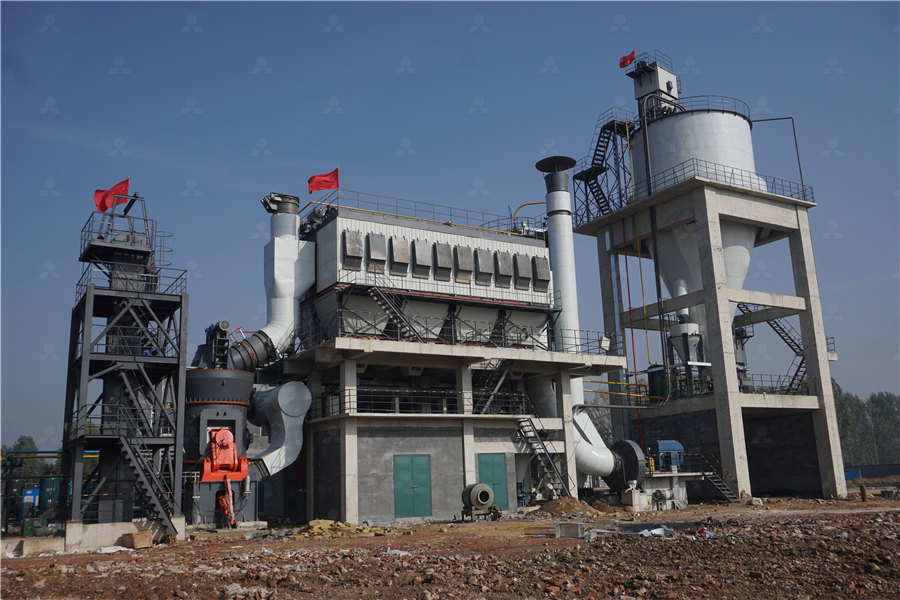
LOESCHEMILLS
1927 First Loesche coal mill delivered for the Klingenberg power station in Berlin 1953 500th coal mill plant sold worldwide 1961 Introduction of hydraulic spring assembly system 1965 Construction of first pressure mill (LM 122 D) 1980 Delivery of first modular coal mill (LM 263 D) 1985 Delivery of first selfinerting coal grinding plant (LM 212 D) for the steel industry (PCI 2012年6月1日 As the cylinder starts to rotate, the grinding balls inside the cylinder crush and grind the feed material, generating mechanical energy that aids in breaking bonds, activating the catalyst, and Grinding in Ball Mills: Modeling and Process ControlOptimization and transformation of 300MV units steel ball coal mill Pulverizing System To cite this article: Wenlan Wang et al 2019 IOP Conf Ser: Mater SciOptimization and transformation of 300MV units steel ball coal mill What is the difference between a ball mill and a coal pulverizer? A ball mill is a machine that grinds materials up to a consistent size using steel balls as the grinding medium A coal pulverizer is a machine that pulverizes coal to a fine powder for combustion in power generation, cement production, and other industries How does the ball How Is Coal Pulverized in a Ball Mill?
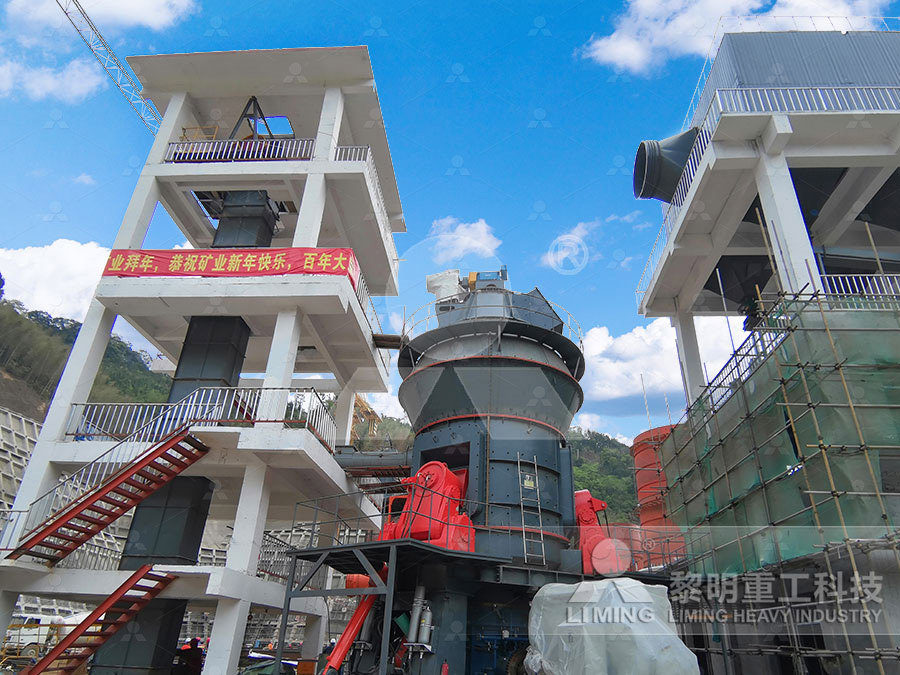
Pulveriser in Thermal Power Plant Bowl Mill Ball Mill
Types Of Coal Pulveriser Slow speed mills like ball mill; Medium speed mills like bowl mill; High speed impact mill; The slow speed and medium speed mills are selected for coals ranging from subbituminous to anthracite The highspeed mills are used mainly for lignite2015年3月1日 There are three basic structures among the coal grinding, t: AirSwept or Wet Tumbling Ball Mill, RollerRace or BallRace Mill and Hammer or Impact Mill [7–10] The type of the mill and its efficiency depend on the type of coal, its moisture, input and output fraction of the material and the grinding susceptibility of the coalModelling of vertical spindle mills Part 2: Integrated models 2011年3月1日 They are used to pulverize raw coal into fine powder of desired temperature and fineness Although there are plenty of coal mines in China, the quality of raw coals varies greatly Therefore, ball mill coalpulverizing systems are widely used to grind various raw coals The flowchart of ball mill coalpulverizing system is shown in Fig 1Multiple models and neural networks based decoupling control of ball Air swept ball mill is also called air swept coal mill or coal mill It a ball grinding mill that merges grinding and drying into a single The quill shaft is made of cast steel and the rotary gear is manufactured by casting hobbing Ball Air Swept Coal Mill AGICO Ball Grinding Mill ball
R)8OC`6F[ZIB.jpg)
Derivation and validation of a coal mill model for control
2012年5月1日 Coal fired power plants are heavily used due to large and long lasting coal resources compared with oil or natural gas An important bottleneck in the operation of this particular kind of plants, however, is the coal pulverization process, which gives rise to slow takeup rates and frequent plant shutdowns (Rees Fan, 2003)In typical coal fired power plants, The characteristic tumbling motion of these mills has given them the name ‘tumbling mills’, which include the ball mill, tube mill and rod mill Ball mills are horizontal rotating cylindrical or conical steel chambers, approximately one third to half full of steel, alloy steel or iron balls, like that shown in Fig 410 A–C , or flint stonesBall Mill an overview ScienceDirect Topics2019年1月30日 Mill power models have been used in a variety of ways in industrial practice since power directly equates to throughput and fineness of ground product We first start with HoggFuerstenau Power Model and show how this model successfully predicted the power draw of many grinding mills in several mining operations Then, we show how this model was on the The Evolution of Grinding Mill Power Models Mining, mill model parameters and dynamics estimating the quality of deposit coal in the mill, which is essential for predicting potential mill fires The thesis reports the work completed and the main contributions of the thesis are summarized as follows: The pulverized coal mill mathematical model for EType vertical spindle millsDevelopment of a tube ball mill mathematical model for mill
.jpg)
BBD double In/Out steel ball millspower plant equipment
Scheme 2: install three coal mills, two for design coal and three for check coal Therefore, P max1 > P max2, P max1 is the maximum raw coal flow rate, P max1 must be considered in the selection of pulverizer 42 Calculation of shaft power of coal mill 421 Calculation of ball filling rate of coal millPlanetary Ball Mill PM 400 for size reduction with the highest degree of fineness powerful short grinding times reproducible results Learn The PM 400 is a robust floor model with 4 grinding stations and accepts grinding jars with a nominal volume from 12 ml to 500 hardened stainless steel, tungsten carbide, agate, Planetary Ball Mill PM 400 RETSCH powerful and quick grindingThe Planetary Ball Mill PM 100 is a powerful benchtop model with a single grinding station and an easytouse counterweight hardened stainless steel, tungsten carbide cellulose, cement clinker, ceramics, charcoal, chemical products, clay minerals, coal, coke, compost, concrete, electronic scrap, fibres, glass, gypsum, hair Planetary Ball Mill PM 100 RETSCH highest fineness2023年10月27日 The ball mill is a rotating cylindrical vessel with grinding media inside, which is responsible for breaking the ore particles Grinding media play an important role in the comminution of mineral ores in these mills This work reviews the application of balls in mineral processing as a function of the materials used to manufacture them and the mass loss, as A Review of the Grinding Media in Ball Mills for Mineral
.jpg)
Differences in dry and wet grinding with a high solid
2019年8月1日 By comparison, the point load on the particles in ball mills is conducive to the attrition process (Bu et al, 2019b;Bu et al, 2020a) Abrasion and attrition result in rounder (more spherical