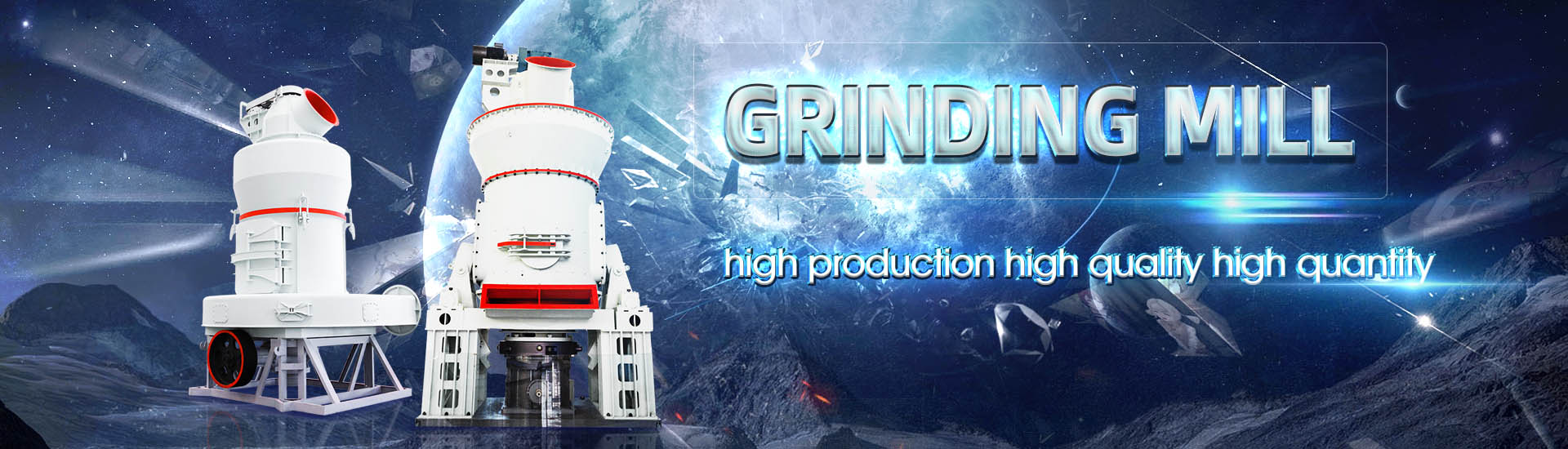
Raymond mill pulverized coal sleeve in smelting plant
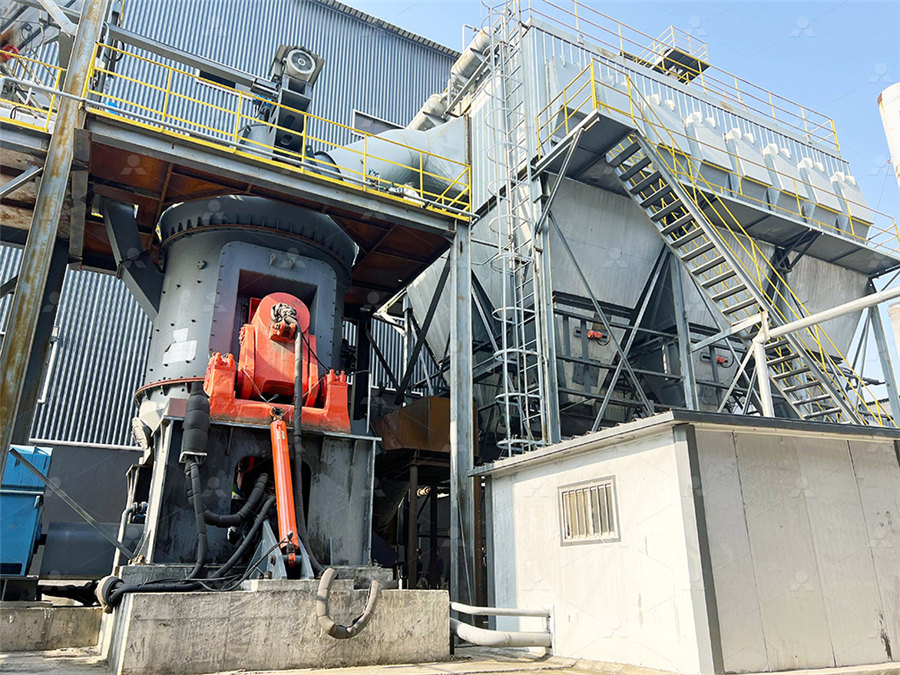
Raymond® Bowl Mill Coperion
The Raymond® Bowl Mill is considered the finest vertical roller mill available for pulverizing coal Each bowl mill system is designed to achieve the best solution for the processing application The mill, feeder, classifier, fan, cyclone, dust 2012年11月17日 The document discusses coal mill/pulverizers used in thermal power plants It describes how pulverized coal is dried, ground, circulated, and classified within the mill to Coal mill pulverizer in thermal power plants PPT SlideShareThe pulverizer mill is a critical component in the coalfired power plant As the age of the mill increases, the maintenance costs required for continued operation also increase With the Pulverizer Maintenance Guide, Volume 1 Raymond Bowl MillsPulverized coal (PC) combustion is presently the system of choice for coalfired powergenerating plants In PC combustion, the coal is dried and is ground to a specified fineness, with a Pulverised Coal an overview ScienceDirect Topics
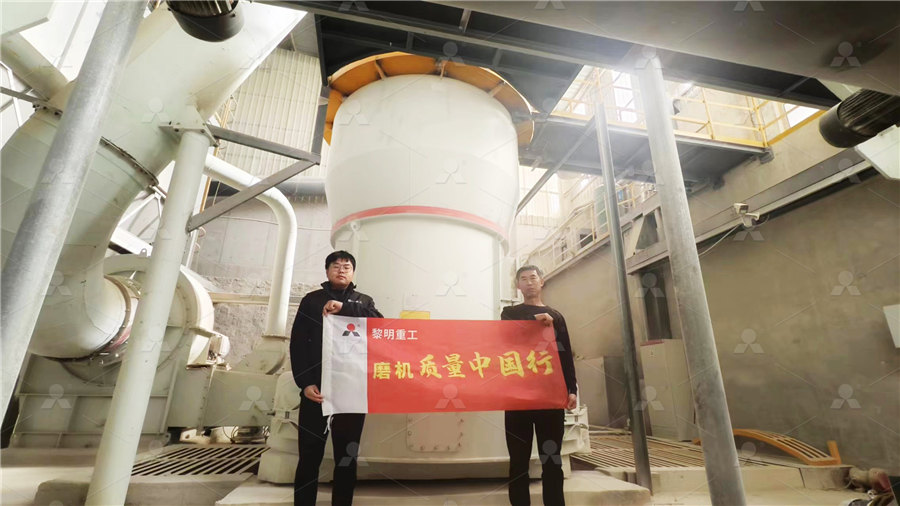
Coal and Mill PDF Mill (Grinding) Mechanical Engineering
The document discusses pulverized coal mills used in power plants It describes different types of mills including tube mills, ball mills, and bowl mills Tube mills are low speed while bowl mills 2018年12月15日 Results from an experimental study on the behavior of a CE 312 Raymond Bowl Mill while processing pure coal and blends of coal and biomass were simulated using Analysis of particle behavior inside the classifier of a Raymond In pulverized coalfired (PCF) thermal power plants (TPPs), coal burners are typically used to inject pulverized coal to the boiler furnace combustion zone After coals are pulverized andNUMERICAL AND EXPERIMENTAL INVESTIGATION OF A 2016年4月5日 This study presents a methodology for the online monitoring of the (i) coal particle size distribution and (ii) coal flow distribution between burners at the outlet of a roller mill Online monitoring of coal particle size and flow distribution in coal
.jpg)
Performance optimisation of vertical spindle coal pulverisers
Coal pulverisers’ performance optimisation is an important process in power generation plants Pulveriser operation is costly; reliability and availability is key to power generation and cost RAYMOND BARTLETT SNOW Vertical Roller Mill (VRM) specialized for Coal grinding for PCI in Blast furnace With over 5,000 units in place worldwide, the Vertical Roller Mill is considered to Raymond Bartlett Snow Milling Technologies SpecializedThe transport air that carries the coal from the mill to the burners is a small fraction of the total combustion air It is kept at low temperature, The most common type of coalfired power plant is pulverized coal combustion (PCC), shown in Figure 21 A mixture of pulverized coal and air is blown into a low NO x burnerPulverised Coal Combustion an overview ScienceDirect Topics2014年1月1日 The emission factors of kiln end, kiln head, coal mill, crushing and cement mill was 0156 clinker g/t, 3914 clinker g/t, 1538 coal g/t, 0016 stone g/t and 0056 cement g/t respectively, the (PDF) MPS mills for coal grinding ResearchGate
.jpg)
Coal Mill – Coal Mill In Cement Plant AGICO Cement
The coal mill grinding system is an important part of the dry process cement manufacturing In cement plants, we usually adopt the air swept coal mill system or vertical mill system as the pulverized coal preparation system, which is In bowl mill pulveriser raw coal coming from feeder gets ground between the grinding rolls and bull ring segments installed on the revolving Bowl If you want to share some suggestion or if u have any question regarding coal handling plant contact me through my id info@coalhandlingplants; Website Information Sitemaps, About, Pulveriser in Thermal Power Plant Bowl Mill Ball MillA coal mill is also called a coal pulverizer or coal grinder It is a mechanical device used to grind raw coal into pulverized coal powders The most used coal mills in cement plants are airswept ball mills and vertical roller mills At present, most cement plants use coal as the main fuel in the clinker production processCoal Mill in Cement Plant Vertical Roller Mill AirSwept Ball Mill2020年6月29日 COAL MILL PERFORMANCE TEST The pulverisers are the “heart” of a pulverized coal fired power plant and as such, must be set up for maximum effectiveness so that the best furnace performance can be achieved Poor mill performance affects combustion , boiler losses , heat rate of unit , capacity of unit , APH , ESP performance , aux powerclassifications and working of mills in a power plant PPT
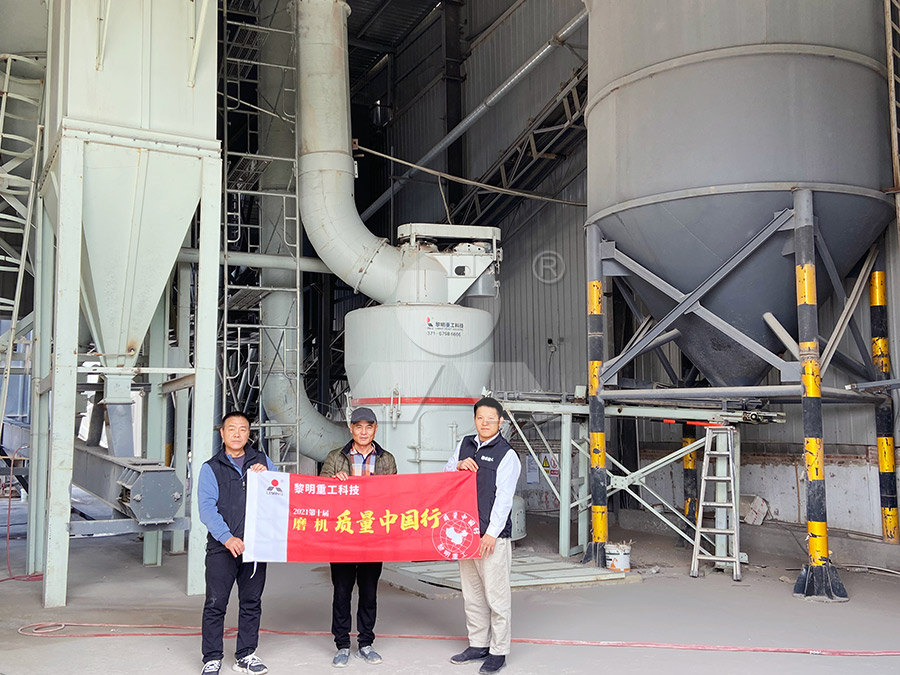
Raymond Mill : The Ultimate FAQ Guide Dry Mortar Plant
2021年12月29日 We produce four kinds of grinding mills: Raymond mill, highpressure grinding mill, highstrength grinding mill, and ultrafine grinding mill You can choose the most suitable mill according to your material, fineness, and output requirements Raymond Mill Get a quotation High Pressure Grinding Mill Get a quotation2020年9月11日 Schematic of pulverized coal injection in the lower part (lanceblowpipetuyereracewaycoke bed) of a BF [49] Technological advancements in evaluating the performance of 2024年10月28日 The calculations of blast furnace smelting modes with PCF injection were carried out in the program based on the method of Prof A N Ramm []The following indicators were entered into the developed program from the MHB for the basic period of blast furnace smelting: the degree of CO and H 2 usage for the blast furnace gas; the degree of direct iron Improvement of the efficiency of blast furnace smelting 2024年3月16日 A vertical coal mill is a type of industrial milling equipment used to crush and grind coal into powder for use in thermal power 85tph Cement Ball Mill In Indian Cement Plant; Ore Dressing Line; the pulverized coal is carried upward by a highspeed airflow generated by the rotating table and directed towards a How Does a Vertical Coal Mill Work Coal Grinding Mill In Cement Plant
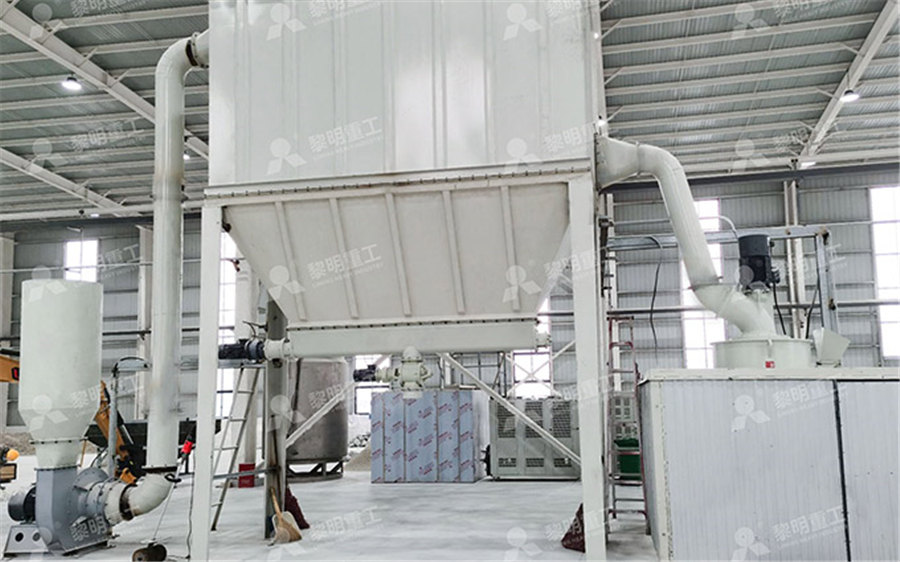
Numerical and experimental analysis of pulverized coal mill
2014年10月1日 In a pulverized coalfired (PCF) thermal power plant (TPP), mixture of coal, air and gas is supplied into the furnace volume via the mill duct system and coal/air distribution should ideally be 2024年9月4日 Raymond Mill Ultrafine Mill: This machine is used for grinding extremely fine materials, even down to 3000 mesh It’s often used for materials that are challenging to process with regular milling machines, such as What is Raymond Mill? How Does It Work? alwepo1996年4月10日 Exhaust gas temperature in coalfired power plants can reach approximately 120 °C to 140 °C, with the thermal energy accounting for approximately 3% to 8% of the total input energyDevelopments in Pulverized CoalFired Boiler TechnologyIn the half century since blast furnace pulverized coal injection has been widely applied in the industrialized area, the market the status of blast furnace injection coal in the iron and steel smelting process is increasing, and it Raymond Mill Case Grinding mill, MTW European Type Trapezium Mill, Vertical
.jpg)
PH’s 1st integrated steel mill, smelting plant to rise in
2022年6月26日 The steel mill and smelting plant has targeted to produce 15 metric tons of steel per year and to generate up to 20,000 jobs It would eventually create about 1,000 downstream industries and The main processes of this process include drying, calcination (Lateritic Nickel Rotary Kiln), prereduction (electric furnace smelting), refining, and other processes The newly built ferronickel project in the state of Para, Brazil uses the rotary kilnelectric furnace process to process nickel laterite ore to produce ferronickelRKEF Nickel Process In Nickel Smelting Plant2016年1月2日 Download Citation Prediction for the burnout of pulverized coal in a coalfired power plant by combining proximate analysis, Raymond Mill (RM), Rolls Crusher (RC) and Ball Mill (BM)Prediction for the burnout of pulverized coal in a coalfired The Raymond mill is an efficient, ecofriendly grinder for processing nonmetallic minerals into fine powder Step 3 The pulverized powder is blown by the circulating air of the blower to the classifier for classifying Coal slag grinding plant in Thailand Output 300 kiloton/annually Finished particle size 100 mesh (0149 mm Highefficient Raymond Mill Fote Machinery
CFB石灰石脱硫剂制备64.jpg)
TPS Coal Mills and Fan Performance PPT SlideShare
2019年5月8日 7 Maintenance Strategy Maintenance Significant Item Inspection / Execution Task Coal Measure HGI (hard grove index), moisture content, abrasiveness and size of coal fed to mill Pulverised fuel (PF) Measure particle size distribution, PF velocity and temperature Grinding media (Balls and Rings) Measure ball diameter, ring depth profile and material A simple energy balance model of the coal mill is derived in (Odgaard and Mataji 2006), this model is based on a more detailed model found in (Rees and Fan 2003)In this model the coal mill is seen as one body with the mass m mThe following variables are defined: T(t) is the temperature in the coal dust flow in the mill, ṁ PA (t) is the primary air mass flow, T PA (t) is Coal Mill an overview ScienceDirect Topics1996年10月1日 Replacement of metallurgical coke by pulverized coal (PC) injected in blast furnace (BF) tuyeres is a major economical challenge, due to the high price of coke and unfavorable effect of its Increase of Pulverized Coal Use Efficiency in Blast Furnace2019年1月1日 on Distribution of Pulverized Coal to the Feed Ducts of a Power Plant Burner, Thermal Science, 13 (2009), 4, pp 79 90 [28] Radovanović, P et al , Therm oTechnical Measurements, Inspection (PDF) Review of the investigations of pulverized coal
.jpg)
Analysis of the Coal Milling Operations to the Boiler Parameters
2020年4月2日 Milling system in coal power plant purposely to process the raw coal to become as pulverise fuel and burners system provides pulverized coal to the Coal mill motor power (kW) 0 4171 Vertical Coal Mill (VCM) is equipment for grinding and pulverizing coal into micron size Rotary kilns then use the powders as fuel burners The VCM has a housing section equipped with a lining The layout of the coal mill with a rotary classifier【Raymond Mill Plant】 The Raymond mill plant usually contains a cyclone collector, pipe fittings, dust collector, storage hopper, elevator, crusher, electric control cabinet, feeder, main plant, blower, separator, etc, Structural Features The whole mill is of spatial structure, less premise and systemic strong The whole system from roughing, transportation, powder collecting to Raymond Grinding Mill JXSC MachineMill connection: the circulating fan is connected to the explosionproof bag dust collector and the inert gas supplement pipe: the inert gas supplement pipe is connected to a heat source system that supplements the low oxygen content heat source gas to the pulverized coal vertical mill to control the low oxygen in the extracorporeal circulation system The limiting oxygen content What is the process flow of vertical mill to produce pulverized coal?
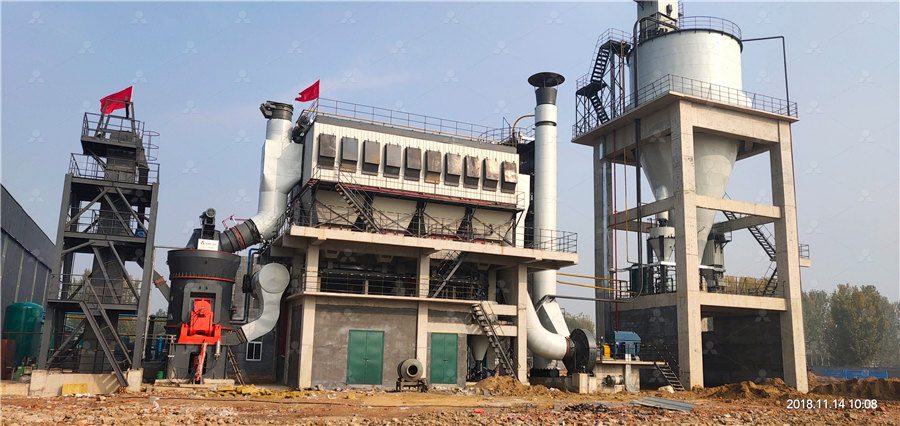
Technology of BlastFurnace Smelting of Iron using Pulverized Coal
2020年9月25日 The problems of using pulverized coal to save coke during iron smelting in the NLMK blast furnaces are considered The iron smelting technology was implemented in two stages: (i) commissioning of the pulverizedcoal preparation and charging system and (ii) selection of charging system and blast conditions that ensure the maximum utilization of 2010年10月7日 In another plant, asfound test data show that coal pipe flow far exceeded the recommended ±10% deviation limit and that there was high variability in coal fineness Source: Storm Technologies Pulverized Coal Pipe Testing and Balancing POWER Magazine2017年5月1日 The introduction of pulverizedcoal injection at Yenakiieve Iron and Steel Works in 2016 is described The state of the lining of the blastfurnace shaft and hearth is analyzedIntroduction of pulverizedcoal injection at Yenakiieve Iron Download scientific diagram The schematic process flow of pulverized coal power plant from publication: Optimization of a 660 MW e Supercritical Power Plant PerformanceA Case of Industry 40 The schematic process flow of pulverized coal power plant
.jpg)
Raymond Roller Mill PartsUltimate Guide Fote
2023年2月15日 Main parts of Raymond roller mill Main parts of Raymond mill include grinding roller, grinding ring, powder collector, classifier, air blower, reducer, base plate, shovel, Raymond mill pendulum, star stack, etc Main 2020年8月12日 This study shows the performance of a currently running vertical roller coal mill (VRM) in an existing coalfired power plant In a power plant, the coal mill is the critical equipment, whose An investigation of performance characteristics and 2021年11月3日 Abstract This article discusses the improvement methods of blast furnace energy efficiency by combined injection of preheated pulverized coal fuel and iron oxides (concentrates of advanced beneficiation, flue dust, and others) into its tuyeres The reasonability of the aforementioned measures is substantiated Based on the overall energy balance, their Improvement of Blast Furnace Energy Efficiency by Injection of Since the first application using an MPS mill to process pulverized coal in Germany in the mid 1960s, there have been over 2,000 different MPS mill installations operating in coalfired power plants worldwide As one of the most popular coal pulverizers in the utility industry, the MPS mill was first introduced into the US in the early 1970sCoal Pulverizer Design Upgrades to Meet the Demands of Low
.jpg)
WorldProven Coal Pulverizer Technology Debuts in the US
1800 rpm primary air fan, and four mill outlets supplying pulverized coal to one of the three horizontal rows of (4) dualfuel burners When operating at boiler MCR, each mill had a coal throughput of approximately 53,000 #ffir Specified product fineness was 70% thru 200 mesh and 98% thru 50 mesh Diminishing supply of the original Kansas coalBefore going into the details, let us look at the quantity of coal processed in a power plant A 2000 MW power station could be handling coal in the range of 1600 tons/hr or around 12 million tons of coal annuallyWhy Pulverized Coal is Used in a Power Plant Bright Hub 2013年5月10日 Pulverized Coal Injection in a Blast Furnace satyendra; May 10, 2013; 5 Comments ; blast furnace, deadman, Dense flow, Distributor, HGI, inert gas, Injection lance, PCI, Pulverizer, raceway, Tuyere,; Pulverized Coal Injection in a Blast Furnace Pulverized coal injection (PCI) is a process which involves injecting large volumes of fine coal particles into the Pulverized Coal Injection in a Blast Furnace – IspatGuru2017年10月25日 In order to replace expensive coke, various fuels are added to the blast sent to the blast furnace: pulverized coal, natural gas, cokeoven gas, fuel oil, etc A less common alternative is to introduce chunk anthracite through the charge hole The use of chunk anthracite may considerably reduce the coke consumption and the production costs of the hot metal in Blastfurnace operation with pulverizedcoal injection and
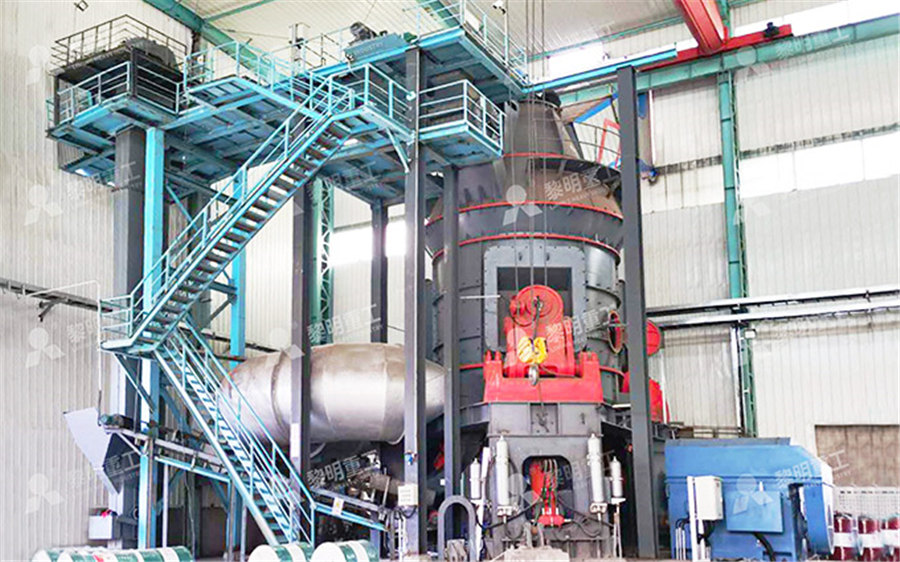
Pulveriser Mill Performance Analysis Optimisation in Super
in the mining or coal processing operations Fig3 Mill fuel piping connections to furnace II COAL MILL SPECIFICATIONS PERFORMANCE ANALYSIS Typical Coal Pulveriser Mill Details in 660 MW SuperCritical [3] Unit is as given in table Table No 1 Table1 Coal mill Type Bowl Type Mediumspeed Coal mill Number of Mills 6set/ boiler