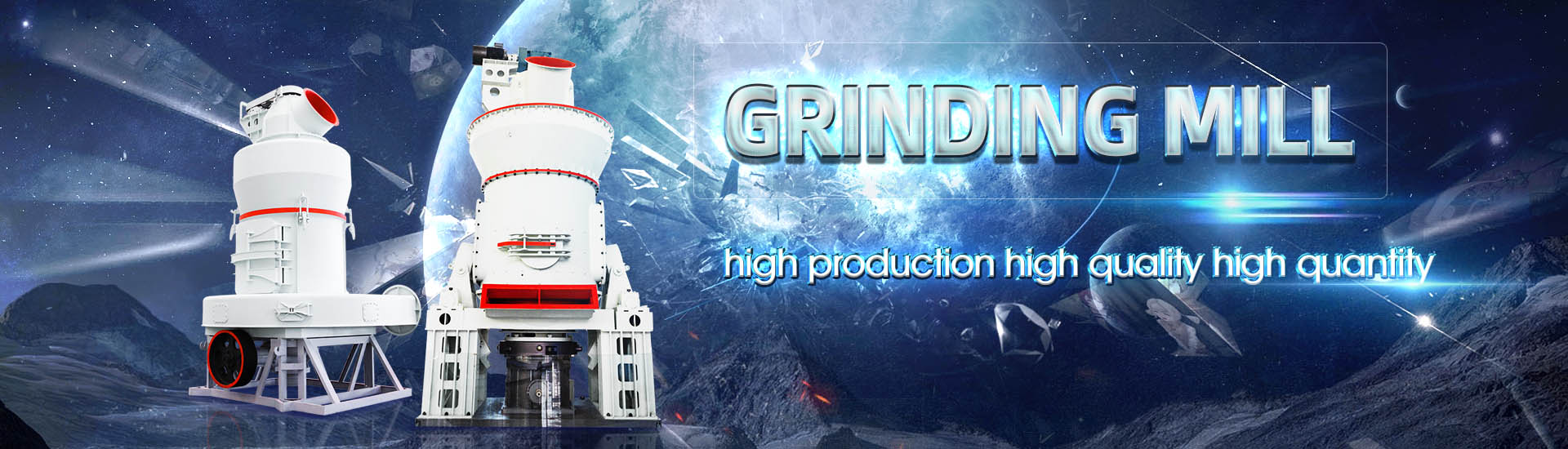
i111 electrolytic aluminum waste residue grinding mill calcium carbonate grinding mill
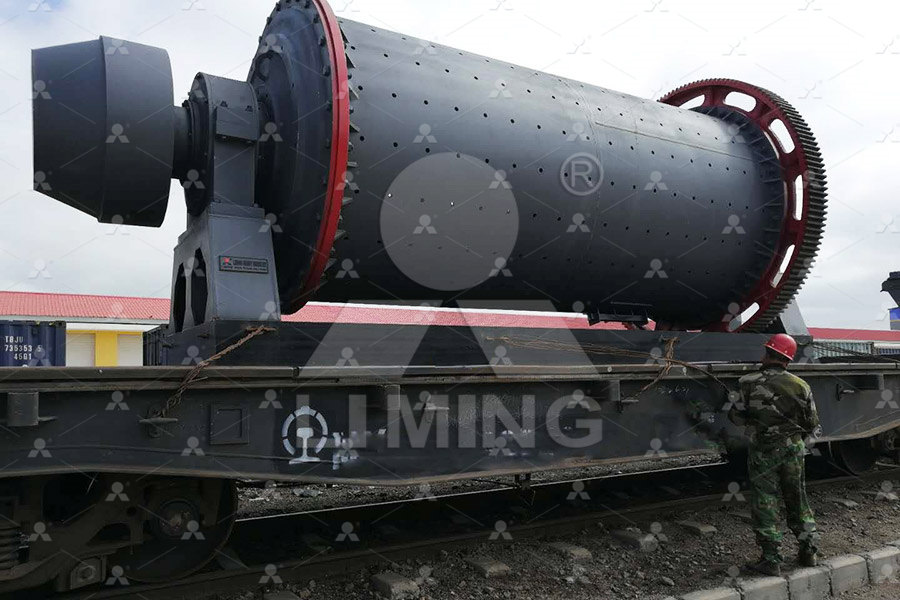
The recycling of carbonrich solid wastes from aluminum
2024年5月23日 Here, we review carbonrich solid wastes with focus on sources and hazards, detoxification, separation, recovery, recycling and disposal Treatment techniques include 2023年10月1日 The composition of leaching residue is similar to that of the regular aluminum electrolyte used in an aluminum smelter, and the content of lithium was reduced from 220% to Efficient extraction and recovery of lithium from waste aluminum 2024年6月29日 In this study, the calcification roasting–twostage leaching process was introduced to extract lithium and potassium separately from aluminum electrolyte wastes, and Stepwise extraction of lithium and potassium and recovery of 2021年10月1日 In this paper, a novel approach is developed for achieving the separation/recovery of lithium from spent lithiumcontaining aluminum electrolyte by a sodium A novel approach for lithium recovery from waste lithium
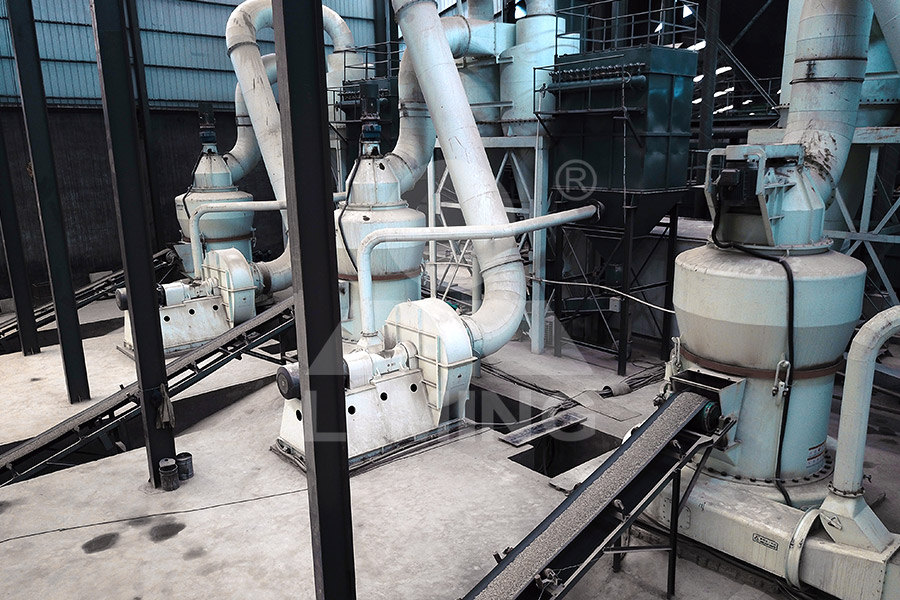
Efficient lithium recovery from electrolytic aluminum slag via an
2024年2月1日 The electrolytic aluminum industry generates a large amount lithium (Li)containing electrolytic aluminum slag (EAS) annually, and this can result in severe Both acid leaching and alkali leaching methods require pretreatment of electrolytic aluminum waste by grinding Firstly, dry the waste residue to reduce its moisture content to below 5% How to extract lithium from electrolytic aluminum waste residue?In this study, grinding characteristics of spent carbon anode from aluminum electrolysis in both ball mill and rod mill were analyzed, and compared based on the utilization of theSelective comminution and grinding mechanisms of spent carbon 2023年4月13日 This paper aims to explore the possibility of using spent carbon anode residue (SCA) from aluminum electrolysis as anode materials for lithiumion batteriesA comprehensive review of aluminium electrolysis and the waste
.jpg)
Research on the Coprocessing of Mixed Electrolytic Aluminum
This study collected electrolytic aluminum waste cathodes, anodes, limestone and other materials After grinding the materials with an electric mill, 50 grams of electrolytic aluminum waste In this study, the calcification roasting–twostage leaching process was introduced to extract lithium and potassium separately from aluminum electrolyte wastes, and the fluoride in the Stepwise extraction of lithium and potassium and recovery of 2018年4月1日 Electrolytic manganese residue (EMR) is a solid waste produced in the process of electrolytic manganese metal (EMM) production In recent years, the accumulation of EMR has caused increasingly Activation of Silicon in the Electrolytic Manganese Residue by 2024年5月23日 16 Million metric tons of spent carbon electrodes modify carbonrich solid wastes from aluminum electrolysis are produced annually, threatening ecosystems by cyanide and fluoride pollution Here, we review carbonrich solid wastes with focus on sources and hazards, detoxification, separation, recovery, recycling and disposal Treatment techniques The recycling of carbonrich solid wastes from aluminum electrolytic
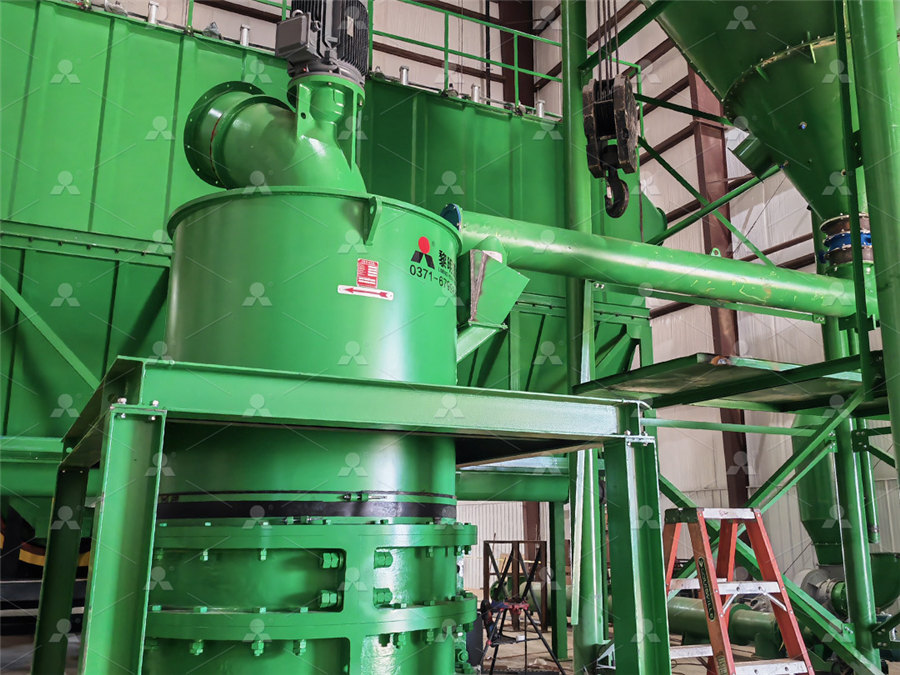
Calcium carbonate waste from an integrated pulp and paper mill
2007年7月24日 Calcium carbonate is used in large amounts in the pulp and paper industry as a paper filler When it is manufactured, the calcium carbonate waste is purged from the process Here we demonstrate that, due to the elevated calcium concentration of 1685 g kg−1 dry weight (dw), alkaline pH of 126 and neutralizing (liming) effect value of 424% expressed as Ca As a byproduct of production, aluminum plant waste residue is also increasing The total loss of aluminum content in the waste residue of aluminum plant in the production process is 112% HCMilling (Gulin Hong Cheng) can provide you with the best quality aluminum plant slag grinding mill machine and serviceWhat’s The Use Of Aluminum Plant Waste? The Price Of Aluminum Waste 2022年1月10日 Selective comminution and grinding mechanisms of spent carbon anode from aluminum electrolysis using ball and rod mills January 2022 Physicochemical Problems of Mineral Processing 58(3):Selective comminution and grinding mechanisms of spent carbon 2021年5月6日 Every year a million tonnes of calcium rich agro and industrial waste are generated around the whole globe These calcium rich waste like finger citron, shells of cockle, mussel, oysters etc, and egg shell are biological sources which have various organic compounds The inorganic calcium rich waste includes gypsum, dolomite, sludge etc, which are produced The Processing of Calcium Rich Agricultural and Industrial Waste
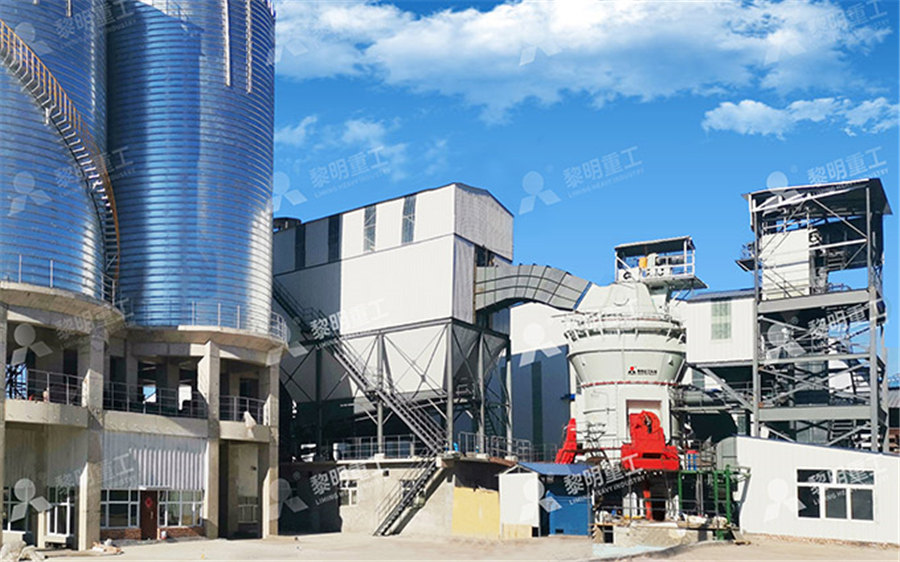
Research on the Coprocessing of Mixed Electrolytic Aluminum Waste
This study collected electrolytic aluminum waste cathodes, anodes, limestone and other materials After grinding the materials with an electric mill, 50 grams of electrolytic aluminum waste samples were sieved to 0075 mm The sample was then dried for 2 hours at a temperature of 110 °C in the dryer, then stored in aThe main production technologies of light calcium carbonate at home Carbonation method Calcining the raw materials such as limestone to generate lime (ingredient for calcium oxide); then adding water to digest lime to generate lime milk (ingredient for calcium hydroxide) and then passing into the carbon dioxide carbide lime milk for calcium carbonate precipitation; lastly, the Grinding mill for Calcium carbonate2021年5月1日 Steps involved in the synthesis of calcium carbonate nanoparticles from cockle shells Islam et al (2012) reported an easy, costeffective, and novel method for the synthesis of CCPs (aragonite The Processing of Calcium Rich Agricultural and Industrial Waste Calcium Carbonate grinding Mill is the new type mining equipment for making micro powders, fine powders,which is widely applied in the industries of metallurgy, mining, chemistry, cement, construction, refractory materials, ceramics, and so onThe purpose of the micro powder grinding millis for superfine grinding materials with hardness less than 9 in Moh's scale and humidity Calcium Carbonate Grinding Mill
.jpg)
Exploring Different Grinding Mills for Calcium Carbonate
2023年9月28日 The material is fed into the grinding chamber between the grinding roller and the grinding ring, and the grinding roller applies pressure to the material, resulting in grinding and pulverizing of the calcium carbonate particlesThey are commonly used in the production of calcium carbonate powders with a fineness ranging from 80 mesh to 600 mesh2021年8月5日 EMR is waste residue generated during the production of electrolytic manganese after leaching with concentrated sulfuric acid, neutralization with ammonia, and filtration by plate filter pressing (Wang et al, 2019, Zhang et al, 2020)Due to historical and technical reasons, the existing open storage EMR in China is as high as 80 million tons; thus (Tian et al, 2019, Ayala Selective recovery of manganese from electrolytic manganese residue 2024年3月20日 The main constituents of rhodochrosite are manganese carbonate, natural silicoaluminous minerals, and a certain amount of calcium carbonate and magnesium carbonate The particle size of EMR mainly distributes ranging from 1 to 200 μm, with an average of 6704 μm and a specific surface area of 5778 m 2 /kgEfficient leaching of manganese from electrolytic manganese residue 2021年6月16日 Aluminum and aluminum alloys are among the most used metals in fabrication,construction, and in the creation of good all around you It is such a useful and versatile metal, but there are some special considerations you need to make when working with it We have put together this expert guide to fabricating, grinding, and finishing aluminum to Ultimate Guide – Aluminum Fabrication, Grinding, and Finishing
.jpg)
CALCIUM CARBONATE (GCC) Hosokawa Alpine
ANRCL + Cell Mill Specific energy consumption (kWh / t) Product fineness d 97 (µm) 100 50 20 10 5 2 SOSF ATR ANR with Cell Mill SO AWM AWMF SOSF = Ball Mill Super Orion SUPER FINE SO = Ball Mill Super Orion ATR = Agitated Ball Mill AWM = Table Roller Mill AWMF = Latestgeneration table roller mill ANR =Vertical Agitated Mill for wet grinding2024年2月2日 Calcium carbide slag is a difficult industrial waste to treat Millions of tons of calcium carbide slag are piled up in China yearly, occupying a large amount of land and easily causing secondary pollution []The main component of calcium carbide slag is Ca(OH) 2, with 71–95% content []Therefore, the current recycling methods of calcium carbide slag mainly Research on Using Carbide Slag to Mineralize the Carbon Dioxide We are a calcium carbonate ball mill plant factory with over 30 years of work experience in this industry, and are at the leading domestic level in the grinding and grading technology of ball mills We can screen and evaluate the raw materials to see if the raw materials can meet the requirements of ball mill productionCalcium Carbonate Ball Mill Plant DASWELLCalcium carbonate ultrafine vertical mill, integrating powder grinding, Calcium carbonate ultrafine vertical mill, integrating powder grinding, grading, conveying, secondary powder selection, and finished product packaging +17 [ protected] language >Shibang Industry Technology Group, Shanghai Ultrafine Powder Tech Co, LtdCalcium Carbonate Ultrafine Vertical Mill SBM Ultrafine
.jpg)
Activation of silicon in the electrolytic manganese residue by
2018年8月10日 Based on its chemical composition, mainly of SiO 2 and small amounts of Al 2 O 3 and Fe 2 O 3, EMR is considered to be a type of silicate mining and metallurgy wasteSeveral researchers attempted to recycle manganese and ammonium from EMR by electrolytic processes (Shu et al, 2016a, Shu et al, 2016b), wet processes, and biological methods (Xin et al, 2011)2021年3月1日 Request PDF Selective recovery of manganese from electrolytic manganese residue by using water as extractant under mechanochemical ball grinding: Mechanism and kinetics This research aimed to Selective recovery of manganese from electrolytic manganese residue It solves the leakage phenomenon when grinding the calcium carbonate, improves the grinding efficiency, eliminates the impact on the main shaft, prolonging the service life of the roller shaft, greatly improves the precision Calcium Carbonate Grinding Mill2022年10月22日 Carbon capture, utilization, and storage (CCUS) technologies are being developed to address the increasing CO2 emissions, mitigating the global warming and climate change In this context, chemical precipitation has been advanced to enhance the performance, energyefficiency and profitability of CCUS In this review, we first present the fundamentals of A review on chemical precipitation in carbon capture, utilization
.jpg)
Calcium Carbonate Ultrafine Powder Vertical Mill
SBM high quality calcium carbonate ultrafine powder vertical mill is widely used in many fields +17 [ protected] language they would drop to the lower cavity of grinding mill and next be sent into the discharging port by scarper installed at the bottom of grinding plate and finally be discharged out of the grinding mill2023年3月8日 Electrolytic manganese residue (EMR) is a solid waste produced in the process of electrolytic manganese metal (EMM) production In recent years, the accumulation of EMR has caused increasingly serious environmental problems To better understand the state of EMR recycling in recent years, this paper used a comprehensive literature database to conduct a Progress in comprehensive utilization of electrolytic manganese residue 2024年2月1日 Aluminum metal was produced using the cryolitealumina molten salt electrolysis method (Ishak et al, 2017)A large amount electrolytic aluminum slag (EAS) is generated during the electrolysis process, as the falling of carbon particles on the anode into the electrolysis cells and the accumulation of lithium fluorine result in energy consumption and electrolyte scrapping Efficient lithium recovery from electrolytic aluminum slag via an In the production of ultrafine calcium carbonate additives, various aspects must be considered when selecting and deciding among available types of processing systems: Fineness range, annual output (uncoated and coated GCC), dry or wet grinding, specific energy consumption, investment costs, plant engineering, running costs and logistical aspectsCalcium Carbonate (GCC) Hosokawa Alpine
.jpg)
Progress of BioCalcium Carbonate Waste Eggshell and Seashell
Disposal of massive amounts of eggshells and seashells from processing industries is a challenge In recent years, there has been a focus to reuse these waste resources in the production of new thermoplastic and thermoset polymer materials This paper reviews eggshell and seashell production by country and provides a perspective on the quantity of biocalcium 2024年6月7日 The nonmetallic mineral grinding ring roller mill pulverizes nonmetallic minerals into fine powder Now, the tire’s airtight rubber mainly uses light calcium carbonate Read More » Differences in uses and properties between heavy Roller Mill Calcium Carbonate Production Line2023年11月1日 Although the utilization of EMR has achieved some results, there is presently no case of largescale industrial promotion and use No matter what treatment method is adopted, it is necessary to ensure the environmental performance of EMR as the premise, which is the control of harmful substances in EMR (Tian et al, 2019)The main harmful substances in EMR Remediation treatment and resource utilization trends of electrolytic 2022年11月1日 Roasting mechanism of lightweight lowaluminum–silicon ceramisite derived from municipal solid waste incineration fly ash and electrolytic manganese residue(PDF) Roasting mechanism of lightweight low

Resource utilization of solid waste carbide slag: a brief review of
China is the largest producer and consumer of calcium carbide in the world The calcium carbide industry is an indispensable industry to support the basic life of people The huge production capacity of calcium carbide is accompanied by a large number of solid waste carbide slag Due to the immature treatment technology of carbide slag, a large number of carbide slag are stacked Calcium carbonate Mill,Calcium carbonate grinding mill,Calcium carbonate grinder,Calcium carbonate grinding machine,Calcium carbonate grinding plant —— fiveCalcium carbonate Mill,Calcium carbonate grinding Quarried limestone is often too big to feed into calcium carbonate grinding mill Besides, different calcium carbonate grinding mill have different feed material required sizes So there is great need of primary and even secondary crushers Usually, the jaw crusher is used to crush the basic materials such as limestone or marbleCustomize Suitable Calcium Carbonate Plant DASWELLBoth methods have their own advantages and disadvantages, and the specific choice depends on the composition and characteristics of the waste residue Both acid leaching and alkali leaching methods require pretreatment of electrolytic aluminum waste by grinding Firstly, dry the waste residue to reduce its moisture content to below 5%How to extract lithium from electrolytic aluminum waste residue?
.jpg)
A novel approach for lithium recovery from waste lithium
2021年10月1日 Currently, the HallHeroult method is adopted for industrial aluminum smelting, with alumina as the raw material and cryolite as the solvent (Tarcy et al, 2011)According to statistics, China's primary aluminum output was 3708 million tons in 2020, of which the capacity of using domestic bauxite to produce alumina accounts for approximately 47% (National 2023年7月10日 The present literature review explores the energyefficient ultrafine grinding of particles using stirred mills The review provides an overview of the different techniques for size reduction and the impact of energy requirements on the choice of stirred mills It also discusses the factors, including the design, operating parameters, and feed material properties, EnergyEfficient Advanced Ultrafine Grinding of Particles Using2017年10月24日 Aluminum production is accompanied by production of fluorinecontaining solid waste Every year in the Bratsk Aluminum Plant 40000 tons of this waste is produced with a high fluorine and carbon content Technology for producing calcium fluoride is developed in order to regenerate fluorine Optimum conditions are studied and determined for leaching fluorine from Technology for Preparing Calcium Fluoride from Aluminum Production Waste2021年8月1日 Electrolytic manganese residue (EMR) is a kind of solid waste with a high silicon content Most of the silicon in EMR, however, exist in the state of SiO2, which cannot be directly absorbed by plantsKinetic study on siliconactivation reaction of sodium carbonate
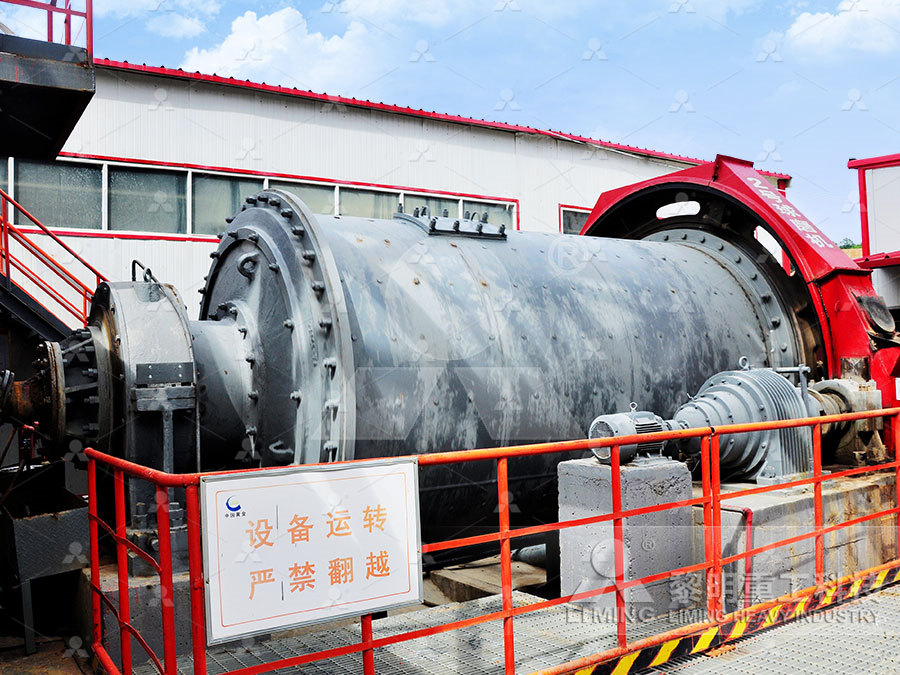
The design and optimization process of ball mill to reduce particle
2020年11月16日 The raw materials were ground from the big particle size to the smallest possible by using multistep grinding In the laboratory, the common method to be used as the ball mill This work aims to design a simple horizontal ball mill Calcium carbonate material from limestone and eggshells powder was ground using the developed ball mill