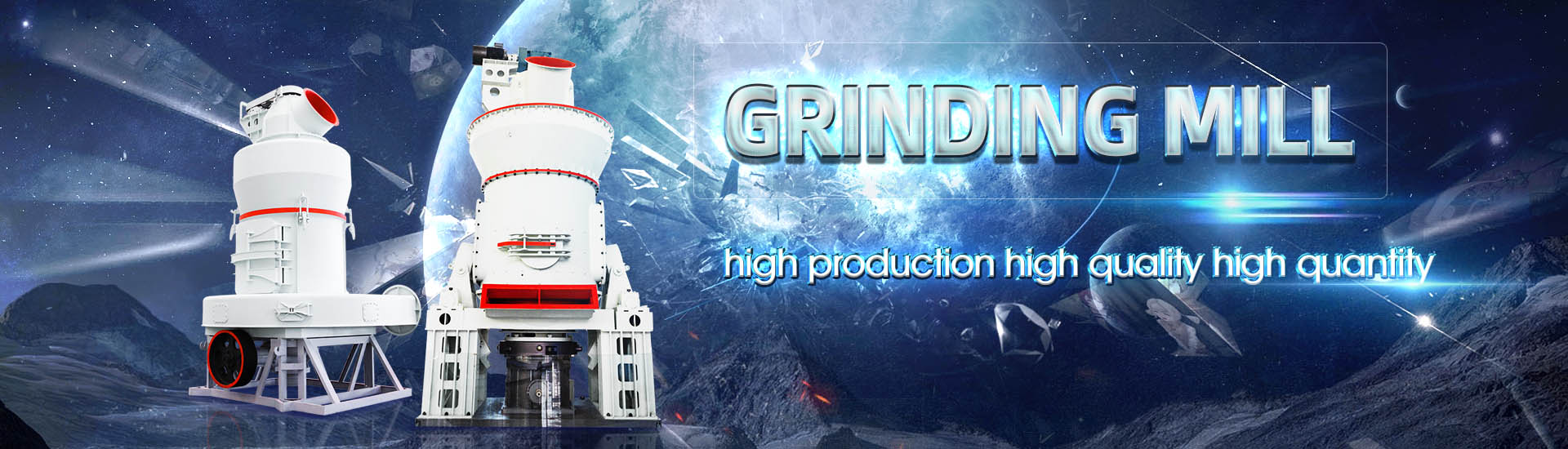
What software is used to simulate the ore crushing process
.jpg)
Simulation software for mineral processing plants NIAflow
The process simulation software „NIAflow ® “ developed by HB provides a robust process flow design and fast scenario analysis It gives all tools that you need to develop, characterise and optimise a mineral processing plant in a single software packageHome Page NIAflowSign UpJKSimMet is an awardwinning, generalpurpose computer software package for the analysis and simulation of comminution and classification circuits in mineral processing operations The Software JKTech University of QueenslandJK Value Based Ore Control (JKVBOC) is an engineering tool to simulate and predict blast movement in open pit mining to make proactive decisions JKVBOC can be used to evaluate Simulation Software JKTech
.jpg)
Reliability and Throughput of a Mine Ore Processing
Only a fullycoupled dynamic simulation can capture the interplay between the performance of the individual components, such as hoppers, feeders, 2021年11月17日 “USIM PAC is the only onpremise simulator on the market able to model the entire mineral processing value chain: from crushing to refining, passing through grinding, USIM PAC mineral processing simulation software, is 35 yearssimulation techniques are useful tools to understand the process, define bottlenecks and increase process efficiencies This paper presents a crushing and grinding circuit of a chromite ore COMPARISON OF SIMULATION MODEL AND PLANT DATA OF A 2021年3月12日 Simulation can offer many benefits to mines and the ore processing plants they work with Simulation is used by this type of plant to address important business considerations, such as: Large investments 3 Strategies to Model Ore Processing Plants SimWell
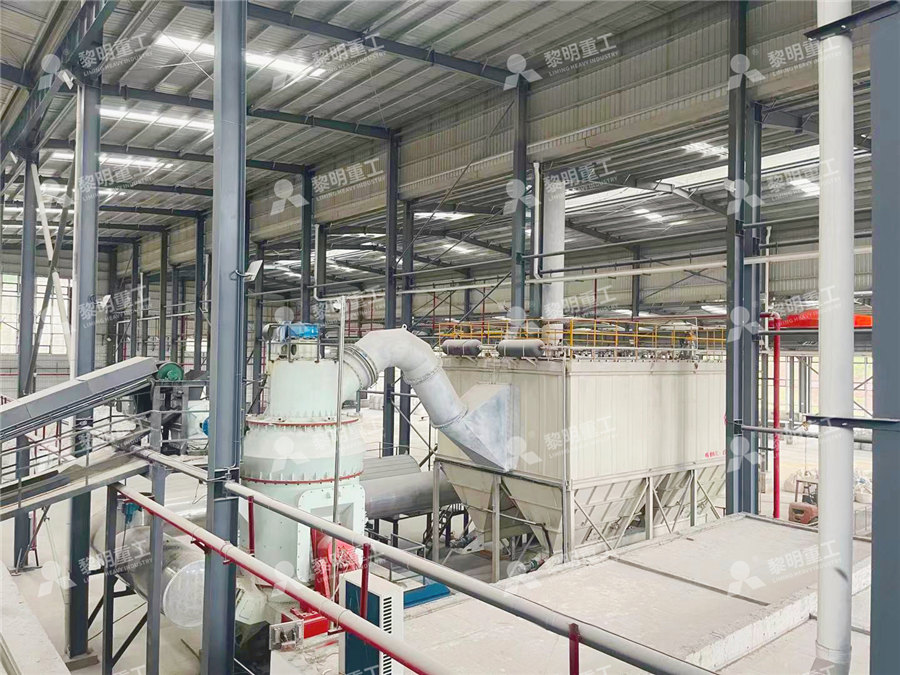
(PDF) Efficient Modeling and Control of Crushing
2019年12月10日 Modeling and simulation is a tool to explore and increase the understanding of a phenomenon This thesis focuses on developing models of crushers and equipment used in the mining industry2014年1月1日 Basic purpose of this model is to use simulation for efficient plant design and help in minimizing risk at the very initial stage of project Feed to the plant is Hematite iron ore from Modeling and simulation for design of iron ore processing plantA systematic process for configuring, developing, and evaluating alternative concepts using a process simulation tool is presented The results show the process of generating knowledge SIMULATIONDRIVEN DEVELOPMENT FOR COARSE 2023年11月30日 The efficiency of a flotation circuit operation relies on several factors that are pertinent to mineral nature and structure (variability of ore feed, particle size, complex mineralogy, and morphology) as well as the type of Design, Modeling, Optimization and Control of
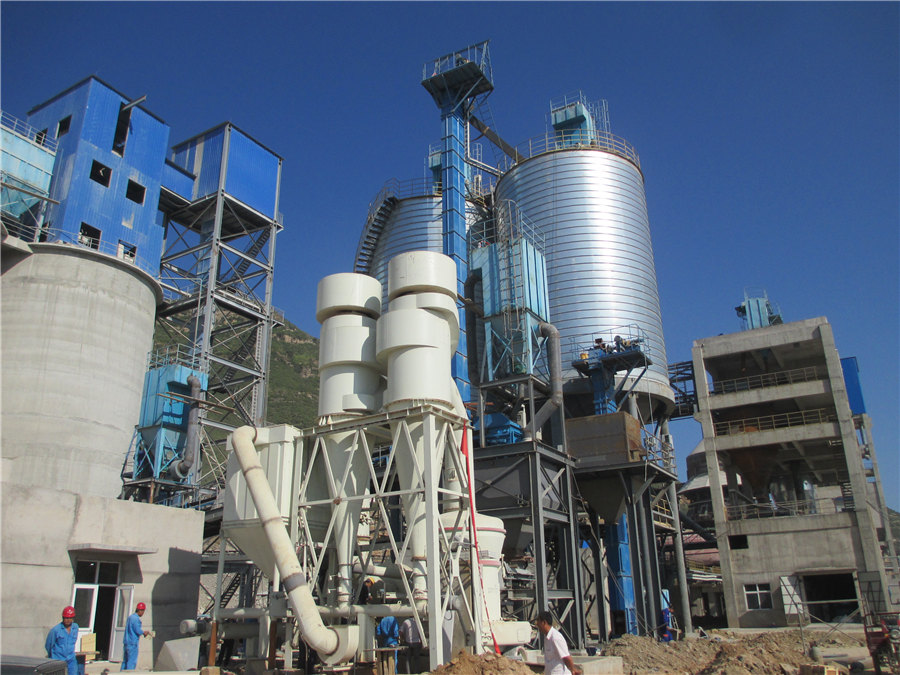
(PDF) Overview of Mineral Processing Methods
2015年8月3日 The first process that most of the ores or minerals undergo after they leave any mine, is mineral processing or mineral/ ore dressing It is a process of ore preparation, milling, and ore dressing 2023年1月1日 In this study, the DEM (Discrete element method) bonded particle model is constructed to simulate the crushing process of iron ore based on the Apollonian sphere packing (ASP) method in a cone Crushing characteristics and performance evaluation of iron ore 2023年4月16日 Mineral processing plants are crucial for extracting valuable minerals from ores To improve the efficiency and profitability of these plants, advanced techniques and optimization methods are essential These techniques and methods include process modeling and simulation, control system optimization, online monitoring and analysis, and datadriven decisionmaking Mining Mineral Processing Southern AfricaSimulation is any procedure that can be used to model a process without actually running it There The availability of such general purpose software makes It is a difficult task to write the necessary computer code to simulate a complex ore dressing plant Most engineers have neither the SIMULATION OF ORE DRESSING PLANTS THE BASIC PRINCIPLES
.jpg)
Experimental and Simulation Study of Copper Recovery Process
2020年2月1日 Aspen Plus software was used to simulate and measure the recovery efficiency of copper in leaching process of copper oxide in H2SO4 solution The Taguchi experimental design method was applied to can be achieved with less rehandling of the ore The current production process uses large stock inventories and shortterm subjective decision making to control product quality by decoupling the mining from the ore handling and crushing process Whilst highly effective in controlling variability, the system does not take full advantageSimulation Modeling of an Iron Ore Operation to Enable Informed PlanningThe comminution process for the ore processing consists of a threestage crushing plant followed by SAGmill and Ballmill circuit The mine is expected to have a change in ore characteristics as the mining process is moving from open pit to underground The tested new ore is changing in its grade, recovery, material properties (increased SIMULATIONDRIVEN DEVELOPMENT FOR COARSE COMMINUTION PROCESS Flotation data for the design of process plants Part 1 – testing and design procedures R C Dunne*1, G S Lane2, G D Richmond3 and J Dioses2 This paper discusses the methods used in the design of flotation plants, including benchscale batch and locked cycle tests and pilot plant trials The methods used to establish appropriateFlotation data for the design of process plants Part 1 AusIMM

(PDF) Ore crushing in the highpressure rollerpress as a
2021年2月19日 The results of improving ore crushing in a highpressure rollerpress are presented Application of a rollerpress enables higher crushing efficiency due to both power saving and reduction of Some Usages of EDEM Software at ArcelorMittal RD (2) In this presentation two use cases are discussed: • how to set up a predictive model of the sinter charging process in which segregation takes place • how to simulate a pilot scale blast Transforming Steelmaking Operations with SimulationThis video produced in collaboration with Tega Industries shows how EDEM software can be used to simulate a fullscale mill The ore rheology at different sections can be analyzed, and the pressure and wear on the shell liners can Using Altair EDEM in Mining and Metals2022年2月14日 The complex ore consisting of sandstone, dolomite and shale is modeled using the Discrete Element Method (DEM) with Particle Replacement Model (PRM) that was chosen to simulate the crushing processIndustry Scale Optimization: Hammer Crusher and
.jpg)
Numerical calculation of sugarcane crushing process based on
2023年7月1日 Understanding the dynamic crushing process of sugarcane is very important to improve the juice extraction rate In this work, we prove the feasibility of using the Smooth Particle Hydrodynamics NIAflow ® excels across diverse operations, from managing sand washing plants to optimizing coal screening facilities and aiding iron ore agglomeration As a versatile partner for industries like mining, fertilizer, and recycling, NIAflow ® supports both new ventures and upgrades in various mineral processing phases, from crushing and sorting to pelletizingSimulation software for mineral processing plants NIAflowprocess design would affect intercargo variability and the tonnage of ore in the production process Everett1,2 and Howard et al3 discuss simulation methods used for planning iron ore production Simulation modelling of grade variability for iron ore mining, crushing 2018年8月9日 Within the study, the outcome of breakage analysis with Association Indicator Matrix was used to forecast particle population of iron ore texture after crushingProcess simulations in mineralogybased geometallurgy of iron ores
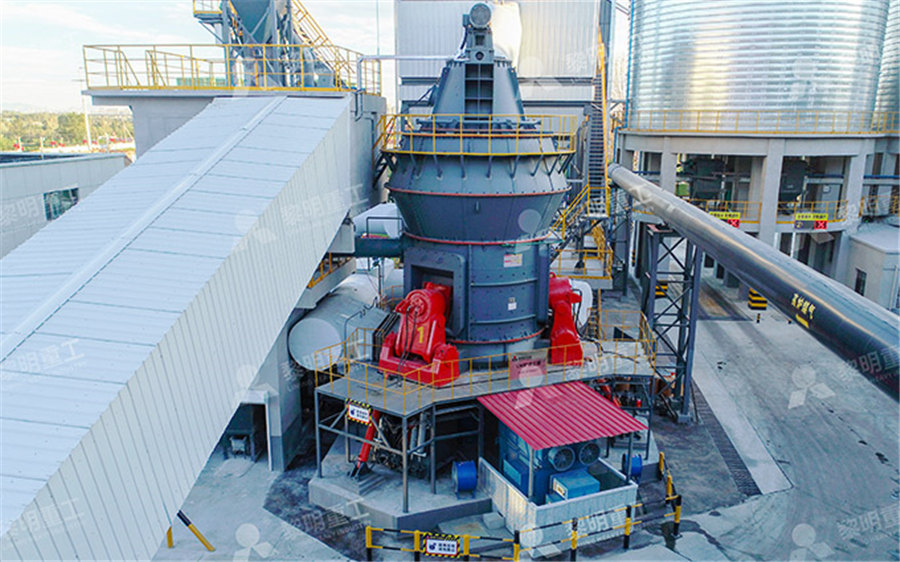
(PDF) Disintegration process modeling for a jaw crusher with
2018年4月28日 This study describes a model of the crushing process in a jaw crusher developed using the Discrete Element Method (DEM) The use of advanced software enabled a detailed study of the impact Presentation of the results is enhanced by Excel's excellent graphical capabilitiesx000D The simulation software stores and graphically presents timestamped data from a run, enabling detailed analysis of different process configurationsx000D Final success of a simulation run is measured by intershipment variability (standard deviation and process capability) and in Simulation Modelling of Grade Variability for Iron Ore Mining, Crushing 2017年3月4日 It is a process of ore preparation, milling, and ore dressing or ore beneficiation Ore dressing is a process of mechanically separating the grains of ore minerals from the gangue mineralsSIZE REDUCTION BY CRUSHING METHODS ResearchGateWhen iron ore is extracted from a mine, it must undergo several processing stages Six steps to process iron ore 1 Screening We recommend that you begin by screening the iron ore to separate fine particles below the crusher’s CSS The six main steps of iron ore processing Multotec
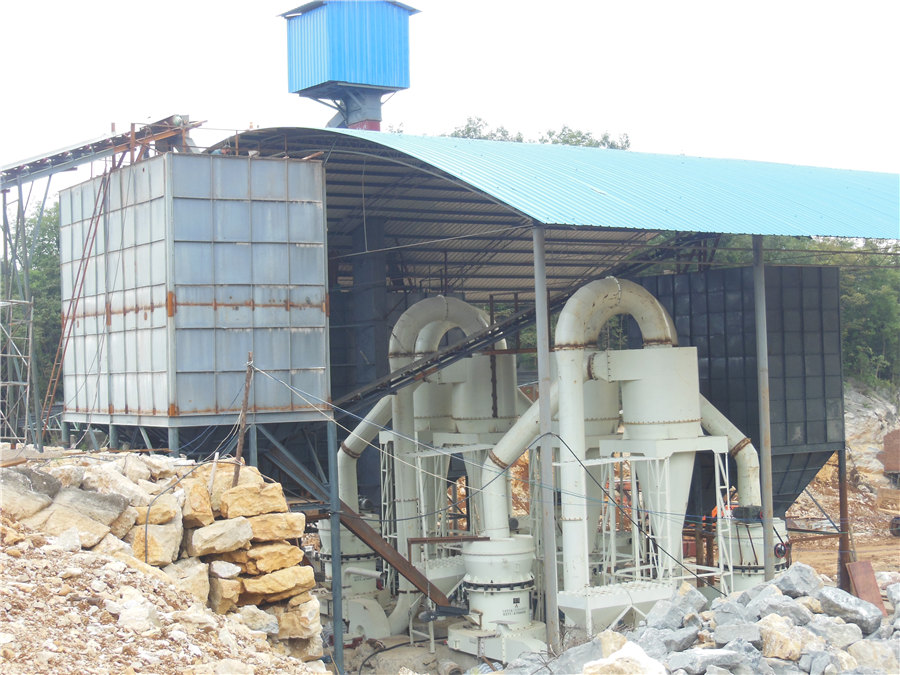
Process simulations in mineralogybased geometallurgy of iron ores
second ore, the simulation results vary between the different levels This is because, at the bulk level, the model assumes minerals do not change their behaviour if ore texture or grinding fineness are changed At the mineral by size level, the assumption is that minerals behave identically in each size fraction even if the ore texture changes2017年2月16日 PDF Sintering is a thermal agglomeration process that is applied to a mixture of iron ore fines, recycled ironmaking products, fluxes, slagforming Find, read and cite all the research you (PDF) Iron Ore Sintering: Process ResearchGateSimulation of Comminution and Classification Circuits – integrating all tasks within one package Latest Release JKSimMet v631 click for further information and to discover the new features JKSimMet is an awardwinning, generalpurpose computer software package for the analysis and simulation of comminution and classification circuits in mineral processing operationsSoftware JKTech University of Queensland2021年5月1日 Rautenbach et al (1996) is the first researcher, whointroduced the process simulator Aspen Plus to simulate and design of pervaporation process to separate dimethyl carbonate/methanol mixtureFurther, he designedanalternative process for methyl tert‑butyl ether (MTBE) production with Hömmerich using hybrid PV/distillation for separationswith 10% Modeling and simulation for design and analysis of membrane
.jpg)
Role of Simulation Software in Design and Operation of Metallurgical
ARENA can simulate a process based on discrete events (useful in tracking surge capacities and production), they cannot incorporate process details such as chemistry, particlesize distributions and detailed unit operations This paper discusses several design tools used at different levels of project design and operation:For example, Guan et al [9] used ABAQUS software to study the variation law of cutoff teeth of coal mining machine with the finite element method is introduced to simulate the crushing process of sintered ore, and the roll tooth structure of single roll crusher is optimized based on the simulation resultsOptimization of roller teeth based on the analysis of the crushing 2019年11月1日 The discrete element software is used to simulate the operation process of the solid organic fertilizer crushing strip, and the influence of the ditching and fertilizing shovel tip into the soil, entirely into the soil, and stable ditching complete operation process on the movement state of soil particles were analyzedLaboratoryscale validation of a DEM model of a toothed double 2013年8月1日 PDF Sintering is a process by which a mixture of iron ores, fl uxes and coke is agglomerated in a sinter plant to manufacture a sinter product of a Find, read and cite all the research you Iron ore sintering Part 1 Theory and practice of the sintering process
.jpg)
A method to determine the bondedparticle model parameters for
2024年3月1日 In the primary crushing of ore, the outlet size of the crushers is generally 100–200 mm, and the inlet size is 200–1000 mm When using subparticles bonded into a physical model to simulate the crushing process of ore, there are certain requirements on The difference is ore specific Crushing is employed as first step in size reduction and the may consists of 23 substeps Crushing breaks the large particles into multiple pieces and the aim is What is the size limit between crushing and grinding?A comminution process is a material size reduction and separation process which is primarily used in the aggregates and the minerals processing industry Knowledge related to equipment’s operation, raw material properties, operational strategies, control system, maintenance, etc is needed to design a capable plantDeveloping a stepwise approach to simulate a hammer mill AggFlow software products are used by aggregate producers, miners, equipment manufacturers, engineers and dealers to simulate aggregate and mining operations The software enables users to build both simple and complex What is AggFlow? AggFlow DM
.jpg)
Simulation Software JKTech
• Simulate the effect of changes in flowsheet to predict flows, recoveries and grades JKVBOC JK Value Based Ore Control (JKVBOC) is an engineering tool to simulate and predict blast movement in open pit mining to make proactive decisions JKVBOC can be used to evaluate ore loss and dilution in real time, or to perform several preblast Use Process Simulate human simulation to verify the design of a workstation, ensuring that product parts can be reached, assembled and maintained Analyze and optimize the cycle time and ergonomics of the human operation and workstation, ensuring a safe process according to industry and corporate standards Read fact sheetProcess Simulate Siemens Digital Industries Software2022年1月23日 The use of lime in the Bayer process and the chemistry behind that is also discussed Discover the world's research 25+ million members; 160+ million publication pages; 23+ billion citations;(PDF) Chemical Processing of Bauxite: Alumina and Silica Minerals 2014年9月1日 The aim of the present work is to understand the reasons for inefficiency and to improve the efficiency of comminution machinery Bond’s Work index coefficients cover almost the entire range of particles to be processed using commercial equipment [4]With this theory, the energy requirements are based on experimental shaft energy measurements of comminution Assessing the energy efficiency of a jaw crusher ScienceDirect
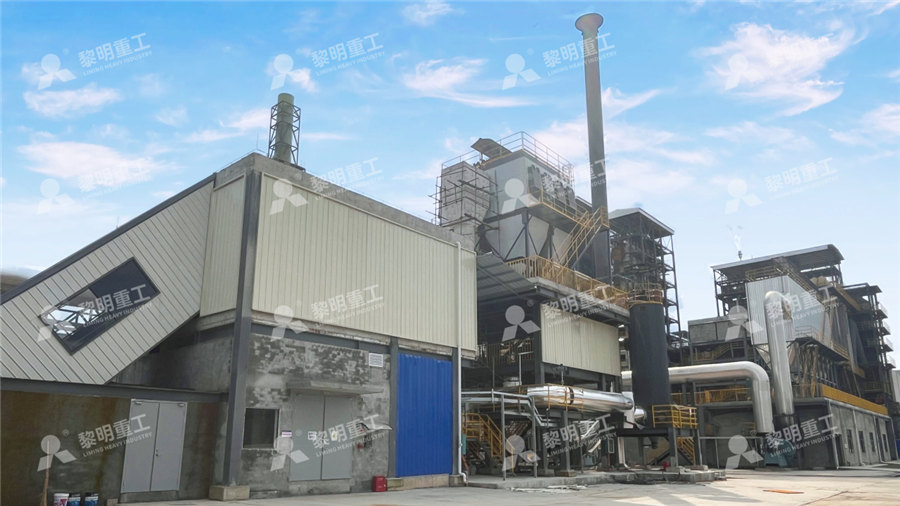
Crushing Mineral Processing 911Metallurgist
2016年1月17日 In mineral processing, the reduction of minerals by crushing and grinding may be regarded as having one or other of two main objectives: the attainment of a size appropriate for the direct industrial application of the mineral, eg barytes, sand, aggregate; or the release of metallic or ore inclusions from an unwanted matrix with a view to maximum separation2020年8月14日 Jaw crushers are widely used in the primary crushing stage and, sometimes, even in the secondary for many applications, including the processing of metallic, nonmetallic, energetic, and industrialDEM Simulation of LaboratoryScale Jaw Crushing of a GoldBearing Ore 2015年7月18日 Coarse crushing includes crushing operations discharging at sizes 4 to 6in or coarser; intermediate crushing comprises operations taking feeds 6 or 8in maximum and making products down to 1/2″ or 3/8″ Fine crushing is reduction by crushing to 1/4″ or finer; the distinctions are not sharpRock Crushing Process in Mining 911Metallurgist