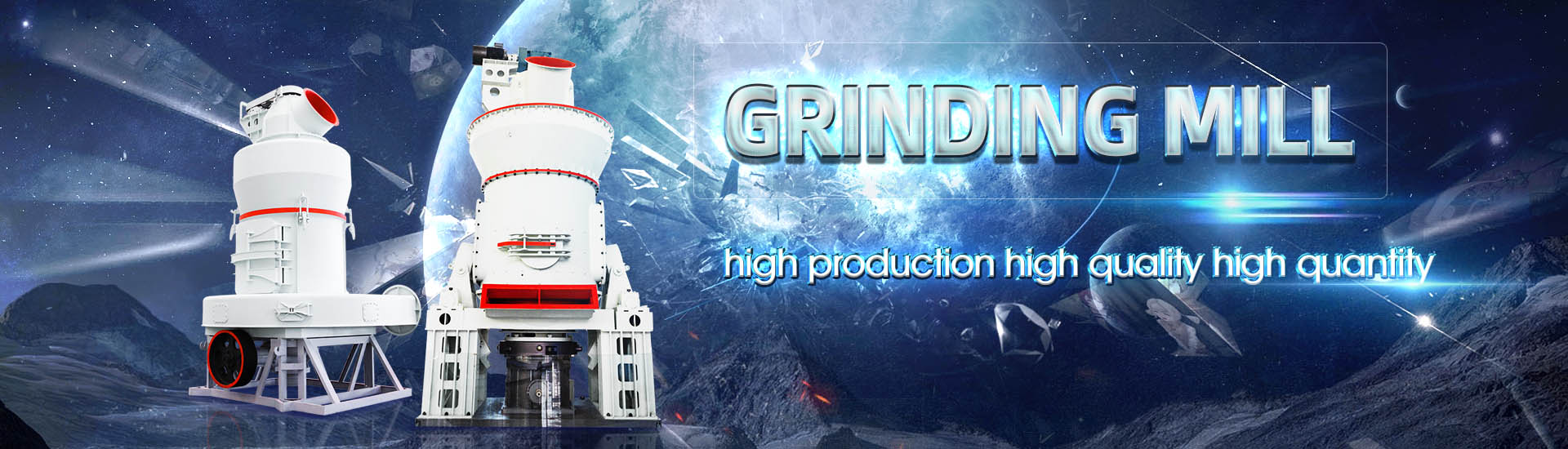
Dry separation process Dry separation process Dry separation process
.jpg)
Industrial separation processes: fundamentals De Gruyter
2013年10月1日 In chapter 7, the separation process of drying is introduced which actually entails the removal of any liquid solvent from a solid by evaporation The definitions of certain We consider drying of solid products here Why dry? Material, when exposed to air with a certain humidity, will reach equilibrium with that air Key point: heat to vapourize the liquid is Separation Processes: DryingAmong the common separation processes are evaporation, distillation, absorption, crystallization, filtration, centrifugation, drying and membrane processes Separation processes are primarily Chapter 3 Separation Processes (Unit operations) The Hong Kong 2021年1月2日 Separation performance is the most important parameter for a continuous gassolid separation fluidized bed In this work, the separation process and its influencing factors in Study on dry separation technology of a continuous gassolid
.jpg)
(PDF) Textbook of Separation Processes ResearchGate
2012年1月1日 Book Contents: Preface; Nomenclature; Dimensions and Units; Various Separation Processes: General IntroductionDefinitions; Absorption/Stripping; Distillation; Liquidliquid Extraction;2014年8月1日 Dry separation methods can basically be broken down into three main types of mechanical separation procedures: air classification, screening and specificgravity separation Dry Separation Methods Chemical Engineering Page 12021年12月1日 During the whole process of coal utilization, coal preparation and separation is an initial and crucial stage for hazards emission control Gravity dry separation technologies, Recent progress and potential challenges in coal upgrading via In order to make the separator produce suitable micropores and reduce the internal stress of the polymer during heat treatment, the stretching process is divided into three steps, which are low Dry Process an overview ScienceDirect Topics
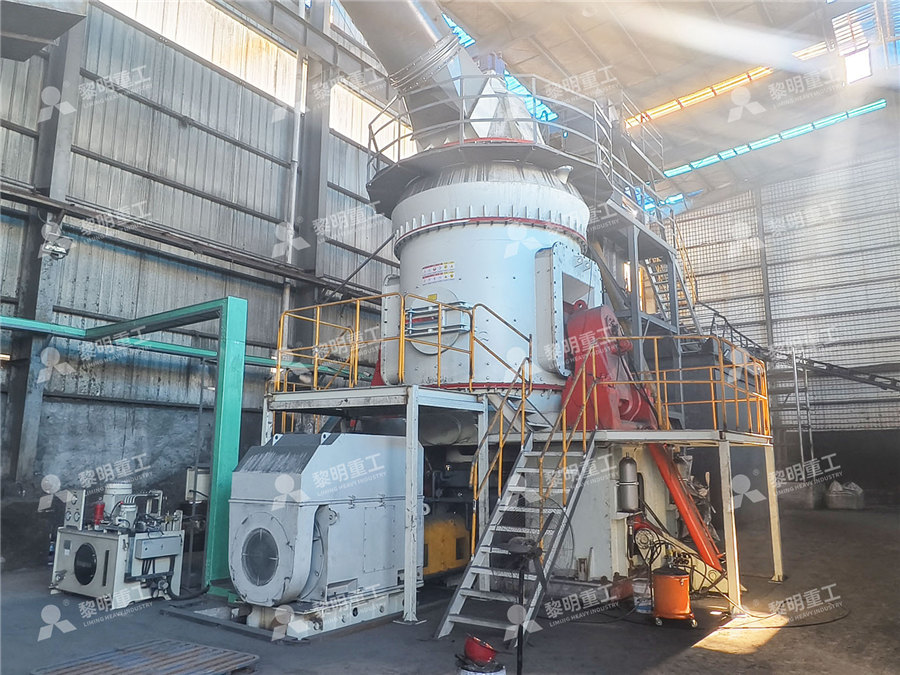
New Highly Efficient Dry Separation Technologies of Fine Materials
2017年12月5日 Medium temperature pyrolysis at t° = 450–600 °C is an effective method of modification of highash coal providing possibility of dry cleaning derived semicoke with the 2016年1月1日 Dry separation method was used at the beginning of 20th century to separate coal separation process First industrial applications of dry separation took place in the middle of 1930sDry Coal Preparation of Fine Particles by KAT Magnetic separation process Magnetic separation technology can roughly be divided into three classes of magnetic intensity ie, low, medium, and high, all depending on the characteristics of the minerals subjected to magnetic processing: • Strong magnetic minerals (ferromagnetic) can be processed by Low Intensity Magnetic Separators (LIMS)For dry and wet processing Low Intensity Magnetic Separators 2019年9月5日 The strengthening method of separation process was put forward, which A largescale compound dry separation machine with the processing capacity of 480600 t/h and quantity efficiency higher than 90% has been developed The largescale dry separation andResearch Progress in Dry Beneficiation University of Pittsburgh
.jpg)
The simplified flowsheet of magnetic separation process: dry
Download scientific diagram The simplified flowsheet of magnetic separation process: dry lowintensity magnetic separation (LIMS) and highintensity magnetic separation (HIMS) from publication 2018年9月26日 Dry separation method was used at the beginning of 20th century to separate coal separation process First industrial applications of dry separation took place in the middle of 1930sDevelopment of dry coal gravity separation techniques2010年7月1日 Having estimated the separation performances of both technologies in this initial study would be able to describe the separation phenomenon and the possible applicability of the dry separation process Furthermore, a micron separator has been utilized to verify the estimated separation performance of the dry separation processRecovery of cenospheres from coal fly ash using a dry separation 2024年4月15日 With an attempt to address this significant problem in the DMS process, the DMS process in centrifugal field was proposed, and a novel centrifugal dry magnetic separator (cDMS) was developed to enhance the separation efficiency for fine particles [23]In this investigation, the mechanical structure and magnetic field characteristics of the separator were Centrifugal dry magnetic separation of fine magnetic minerals
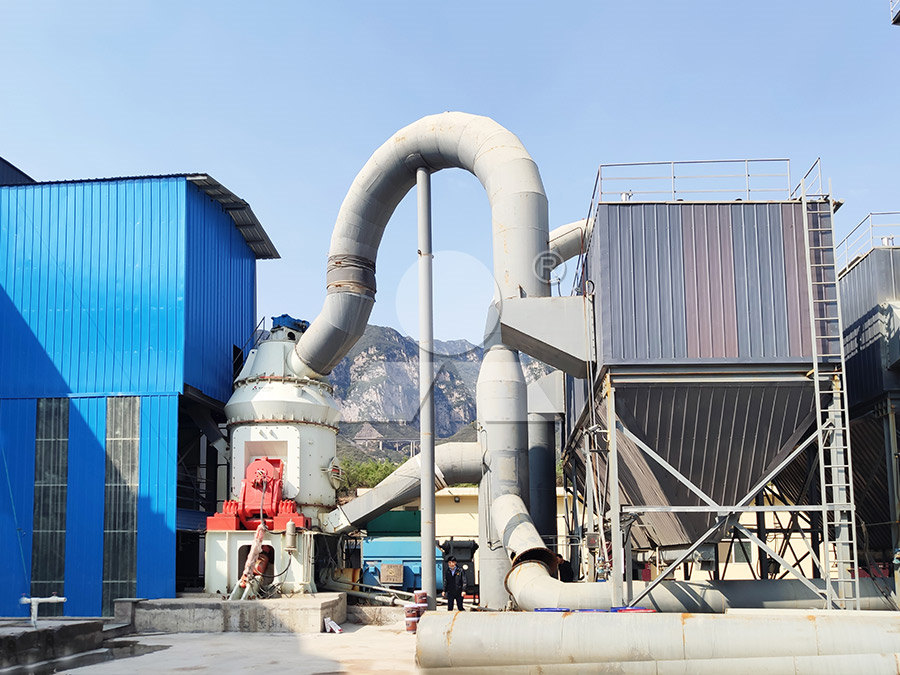
Oil shale separation using a novel combined dry beneficiation process
2016年9月15日 Dry separation processes can therefore be used to separate oil shale across the full particle size range of 0–100 mm In this paper, based on the laboratory experiments, we propose a novel dry beneficiation process combining the compound dry cleaning with VADMFB separation to beneficiate oil shaleThe conventional separation system for the recovery of palm kernel from its palm shell–kernel mixture using water as process media generates a considerable amount of waste effluent that harms the environment The aim of this study is to develop a dry separation process for the recovery of palm kernel by using winnowing columns A commercial system consisting of a Dry Separation of Palm Kernel and Palm Shell Using a Novel Five drycyclone, the use of apex cone in the inlet of dust box is effective to improve particle separation efficiency Because the upward fluid velocity decreases by use of the apex cone, then the number of escaping particles decreases in this case The optimum cone angle of the apex cone is detected The use of the additional air jet flow near the Recent Technology of Dry and Wet Type Particle Separation Process AOGMS process could provide the appropriate competitiveness in the dry separation process, thus, the locked particles and fine nonmagnetic particles can be discarded efficientlyEquipment for magnetic separation in dry process
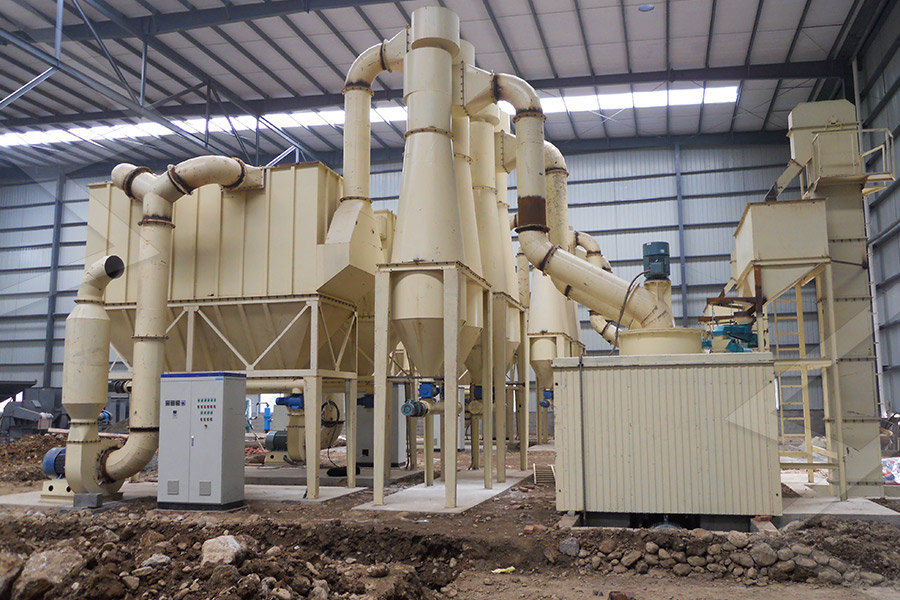
Dry vs Wet Separation Methods in Mineral Processing
2024年2月14日 Learn how to choose the best equipment and process for dry or wet separation methods in mineral processing, based on feed characteristics, product specifications, environmental regulations, and The novel process involved pyrolysis of high sulfur coal at low temperature and then a dry magnetic separation For testing the cleaning coal process, a Chinese high sulfur coal, Baisu coal was pyrolyzed in a fixed bed reactor from 400 to 700°C for 30min, and then separated by a dry magnetic separatorDRY MAGNETIC SEPARATION OF MAGNETITE ORES ScienceGateseparation efficiency reachable; however, the substantial process water constraint proves wet beneficiation impractical and unsustainable in some parts of the world As a result, research into the development of dry methods for effectively beneficiating coal has progressed; especially in the arctic, arid and also coalrich regionsDry processing for coal preparation: a review2024年1月24日 China produces around 80% of the world’s separators Out of these, 70% are wet process separators and 30% are process separators As NMC battery are targeting higher energy density, manufacturers are mostly using wet separators This is due to wet separators are 30%40% thinner than dry separators, it can save more space for other componentsDry vs Wet Separator Technology Battery Design
.jpg)
Performance of dryseparation processes in the recovery of
2011年1月17日 A real sample of cenospheric fly ash with a cenospheres concentration of 028 wt%, supplied by Idemitsu Co Ltd, was chosen for the implementation study of the dryseparation process in a cenospheres recovery unitThe composition of the ash sample was analyzed by means of a fluorescence Xray analyzer2024年3月15日 A novel fullscale centrifugal dry magnetic separator (cDMS) was developed, and in this investigation, it was used to process a fine magnetite ore, which assays 2857% Fe in magnetite The separation results indicate that the cDMS separator is capable of producing a high separation selectivity for magnetite powdersDevelopment of a centrifugal dry magnetic separator for separation 2014年8月1日 (Page 1) The chemical process industries (CPI) have many applications that require classifying or separating solid materials Dry separation methods can basically be broken down into three main types of mechanical separation procedures: air classification, screening and specificgravity separation This article provides background on the different dryseparation Dry Separation Methods Chemical Engineering Page 1PhD 2019 Dry processing for coal preparation: a review N Hughes Addendum A: Performance report on the applicable dry coal processing techniques 4 NWU in association with CoalTech Elutriation or gravity separation Process PSD (mm) Capacity (tph) Efficiency Characteristics Application (P3) All Air Jig + 05 mm 50 mm [7] 50 120 tph [7]Dry processing for coal preparation: a review
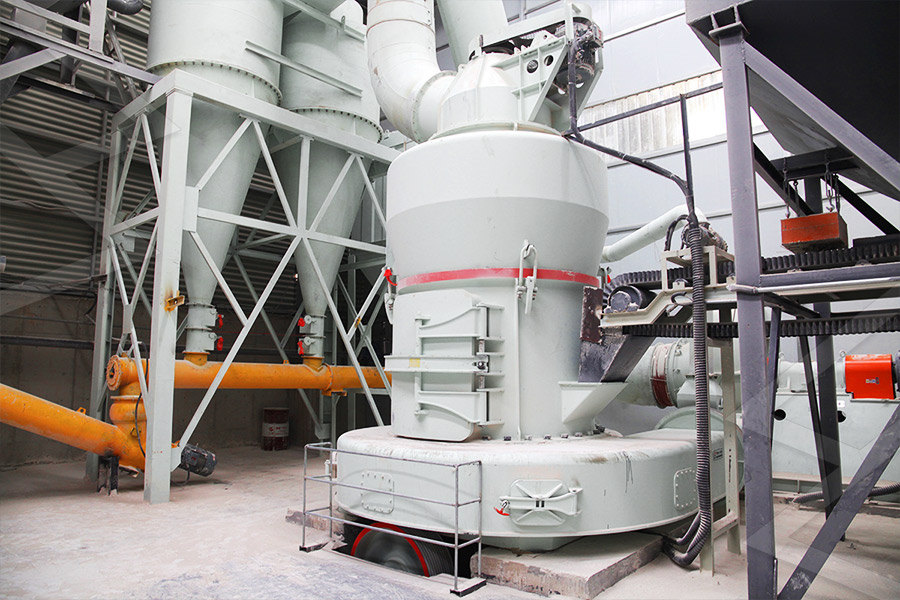
Variables and Applications on Dry Magnetic Separator e3s
process requires subsequent processing The dry separation process has many advantages and disadvantages compared to the wet process In some tests, dry sorting is superior to wet processes such as water consumption, reuse of recycled water, management of tailings ponds, and so on There are different methods for classifying magnetic2023年10月1日 Dry fractionation is an energyefficient and environmentally friendly process for protein separation, preserving protein's native functionality Cereals and pulses are excellent sources of plant proteins as they are widely Dry fractionation process operations in the production DOI: 101016/JMINPRO201701007 Corpus ID: ; Influence of process parameters of dry high intensity magnetic separators on separation of hematite @article{Tripathy2017InfluenceOP, title={Influence of process parameters of dry high intensity magnetic separators on separation of hematite}, author={Sunil Kumar Tripathy and Veerendra Influence of process parameters of dry high intensity magnetic 2020年10月26日 After applying more wet processing technologies like beneficiation processes in jigs or dense medium separators the dry separation process becomes less popular due to less efficiency and lower separation accuracy In Poland last operating air separation systems were applied in “Rozbark” coal mine in Bytom City [1, 3, 4]Modern Methods of Dry Mineral Separation Polish Experience
.jpg)
Development and engineering application of coal dry separation
Diversified separation process Combined with the emergence of new dry separation equipment recently, many new dry separation processes were developed to meet the needs of different customers For example, in the old thermal coal preparation plants without dry separation systems (Zhang, 2019), the calorific value of finalAir classification is the dry separation method that separates fractions based on its size, shape, density and physicochemical nature which is comprised of protein, from heavy particles such as starch The process is highly automated and may be repeated several times until ideal concentration is achieved In some cases, Fractionated Pulses USA Pulses2005年3月1日 The polymeric membrane formation by the drycasting method is a complicated process due to phase separation, and simultaneous heat and mass transfer mechanisms controlled by complex thermodynamic and transport properties of polymer solutionsMembrane formation by drycast process: Model validation to operate with 100% water recycle, requiring disposal of at least of portion of the process water, likely containing trace amounts of chemical reagents Dry methods such as electrostatic separation will eliminate the need for fresh water, and offer the potential to reduce costsExpanding Applications in Dry Triboelectric Separation of Minerals
.jpg)
Economic Advantages of Dry Triboelectric Separation of Minerals
consulting firm of the triboelectrostatic belt separator versus conventional flotation for barite / quartz separation illustrates the advantages of dry processing for minerals Utilizing this dry process results in a simpler process flow sheet with less equipment than flotation with both capital and operating expenses reduced by ≥30% Keywords:2017年3月10日 Rare earth roll magnetic separators (RERMS) and induced roll magnetic separators (IRMS) are the simple and efficient dry highintensity magnetic separators used for upgrading different paramagnetic minerals These are the most popularly adopted units for separation of mineral sands, but its application for processing of other minerals is scantyInfluence of process parameters of dry high intensity magnetic 2015年3月3日 High intensity dry magnetic separators are gaining popularity for the separation of paramagnetic minerals due to the cost economic factor Induced roll magnetic separator is found to be an effective dry separator for the separation of fine particles Separation efficiency of this separator depends on mineral characteristics and the design features of equipment along with Prediction of Separation Performance of Dry High Intensity 2022年9月9日 Dry permanent magnetic separators have been widely used in the mineral and coal processing industries due to their simple operation and high separation efficiency These tools not only discard some amount of bulk Dry Permanent Magnetic Separator: Present Status
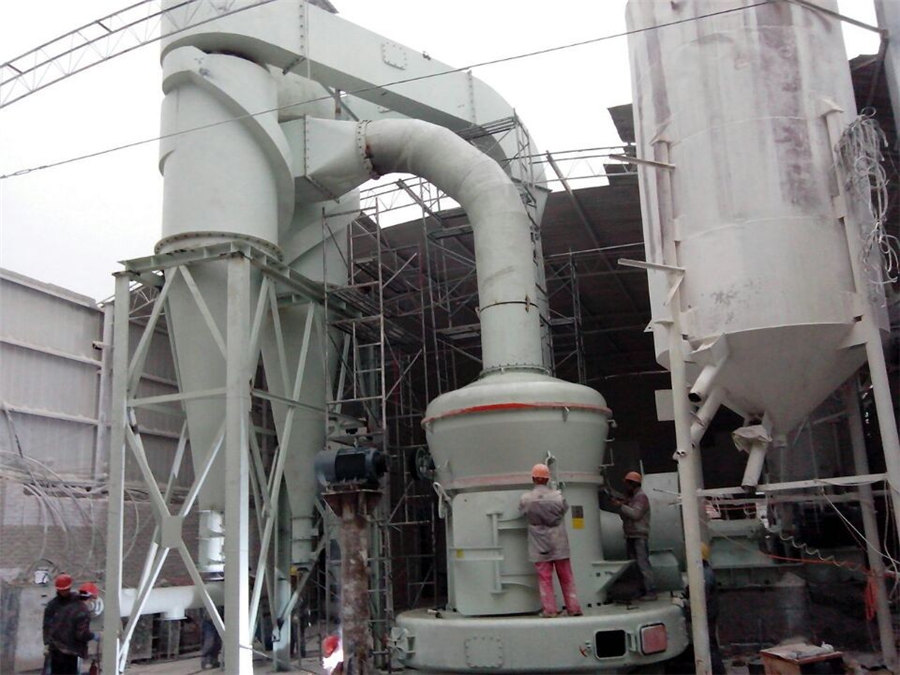
Fine Size Dry Iron Ore Beneficiation Using Thin Bed Air Fluidized Dry
2024年3月13日 Lump iron ores dry separation using dry dense medium gasfluidized bed was reported by Oshitani [4,5,6] Suresh N (2017) Influence of process parameters of dry high intensity magnetic separators on separation of hematite, International Journal of Mineral Processing 160, 1631 Article CAS Google Scholar 2016年9月15日 Dry separation processes can therefore be used to separate oil shale across the full particle size range of 0–100 mm In this paper, based on the laboratory experiments, we propose a novel dry beneficiation process combining the compound dry cleaning with VADMFB separation to beneficiate oil shaleOil shale separation using a novel combined dry beneficiation process Thus, implementing a dryseparation process (micron separator) in the cenospheres recovery unit not only provides high recovery of cenospheres, but also economic, environmental, and ecological benefits Acknowledgements The authors express appreciation for support of this research by the Japan Coal Energy Center (PDF) Performance of dryseparation processes in the recovery of 2016年7月28日 Steelmaking slags are usually processed for iron recovery by dry magnetic separation The recovered ironrich products are recycled back into the ironmaking and steelmaking processes to replace highcost steel scrap and iron ores However, current slag processing is far away from optimum conditions, especially for slag fines with small particle Enhancement of Iron Recovery from Steelmaking Slag Fines by Process
.jpg)
Influence of Separation Angle on the Dry Pneumatic Magnetic Separation
Minerals 2022, 12, 1192 5 of 14 where α, β and θ, respectively, represent the iron grade of feed, concentrate, and tailing, and β max is the theoretical iron grade of magnetite, 6854%When it comes to effective particle separation, gravity separation is traditionally done as a wet process rather than a dry process In fact, wet processing has been the industry standard across the mining industry for centuries, and has recently been adapted into urban mining processes such as incinerator bottom ash separation There is a reason wet processing is the optimal Choosing a Gravity Separation Process: Dry vs Wet Processing2016年6月1日 address this, dry magnetic separation is an alternative approach to separate these ironbearing gangue minerals from the chromite This work investigated on the application of different dry high HighIntensity Magnetic Separation Processing of Ferruginous Chromite 2000年7月25日 Phase separation mechanisms during the membrane formation by drycast process were investigated by light scattering in the cellulose acetate/dimethylformamide (DMF)/2methyl2,4pentanediol system Phase separation occurred by spinodal decomposition (SD) when paths of the composition changes due to the evaporation of DMF were close to the critical Phase separation mechanism during membrane formation by drycast process
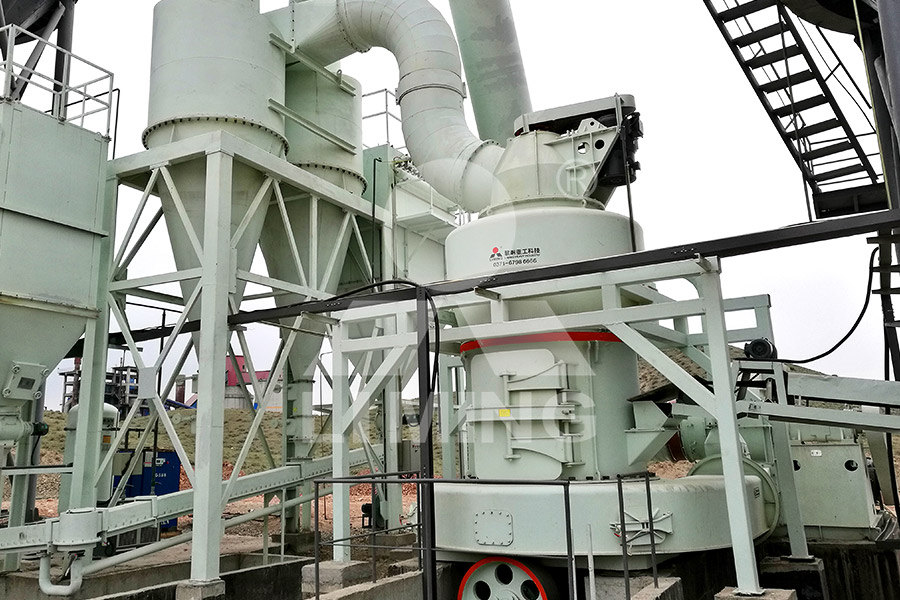
Dry Coal Preparation of Fine Particles by KAT Process
2016年10月22日 In this study, effectiveness of KAT Process, dry coal preparation process developed by KIGAM (Korea Institute of Geoscience and Mineral Resources), Dry separation on coalsilica mixture using rotary triboelectrostatic separator, Fuel Processing Technology131(2015) 317324 Google Scholar