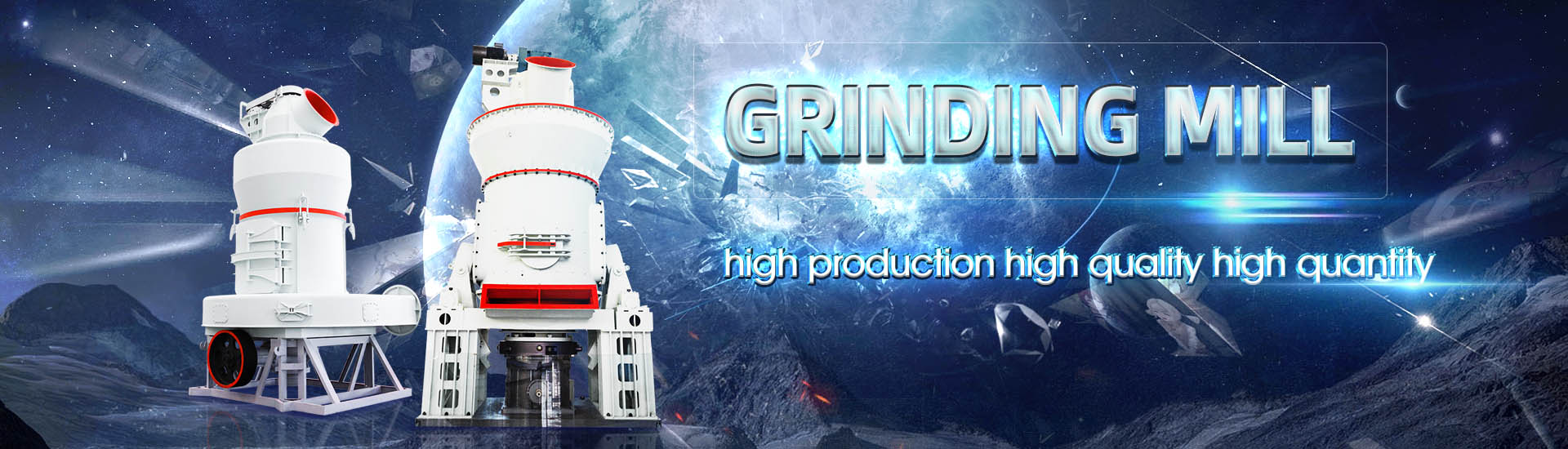
Standard production capacity of cement mills of different specifications
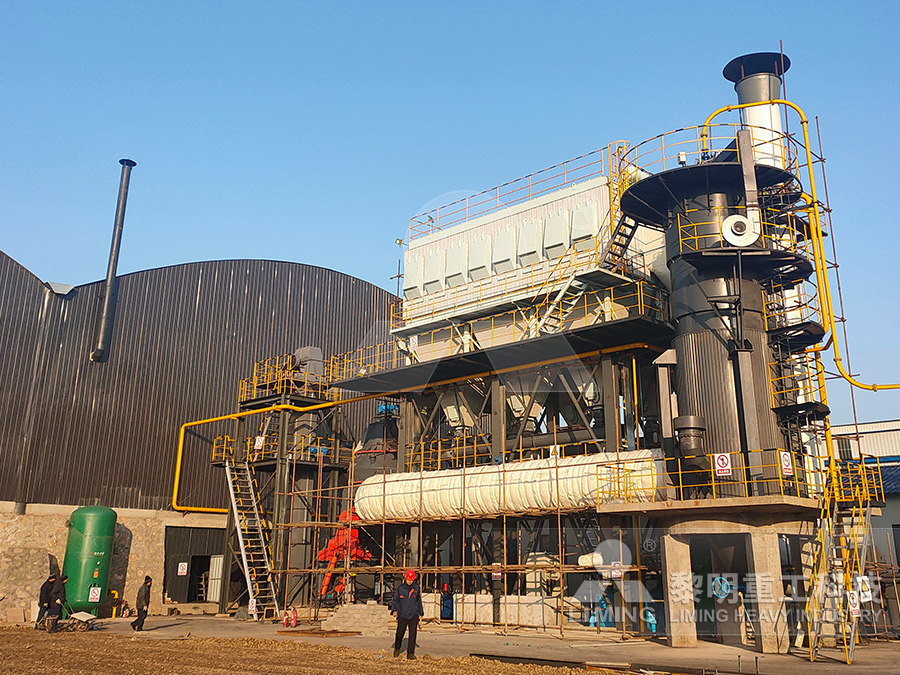
The Cement Plant Operations Handbook International Cement
The Cement Plant Operations Handbook is a concise, practical guide to cement manufacturing and is the standard reference used by plant operations personnel worldwide Providing a comprehensive guide to the entire cement production process from raw materialAssociation of Portland Cement (ABCP), the International Energy Agency (IEA), the Cement Sustainability Initiative (CSI) of the World Business Council for Sustainable Development IMPROVING THERMAL AND ELECTRIC ENERGY EFFICIENCY AT 2 BALL MILLS INTERNATIONAL CEMENT REVIEW FEBRUARY 2021 aim of delivering a target mill discharge size at the end of the chamber, with a maximum residue of five per cent >2mm BALL MILLS Ball mill optimisation Holzinger ConsultingThe cement production is one of the most energy consuming processes, typically accounting for 50 to 60% of the production costs However, there are several ways of heat recovery opportunities to achieve better energetic and exergetic (PDF) Cement plant operation handbook Academia
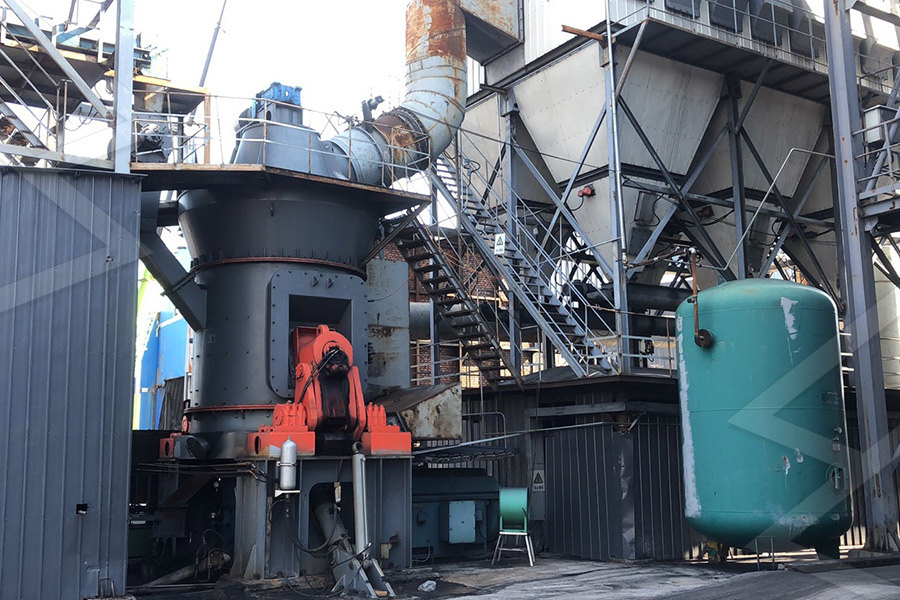
Industrial : Optimization for the Cement Industry ABB
the grinding circuit of a raw mill are an increase in output and a reduction in power consumption Expert Optimizer has been successfully applied in more than 90 mills, to optimize milling Today, our production capacity amounts to over 30 million metric tons As its most important ingredient, cement gives concrete a number of properties, especially its strength It is a fine mineral powder obtained by firing and milling a mixture of Cement: stages of manufacture of artificial cement VicatA 10 MW cement mill, output 270 tonnes per hour A cement mill (or finish mill in North American usage [1]) is the equipment used to grind the hard, nodular clinker from the cement kiln into Cement mill WikipediaEquipment: Ball mills, vertical roller mills Ball Mills: 1030 tons/hour capacity, 5001500 kW motor power Vertical Roller Mills: 2050 tons/hour capacity, 10003000 kW motor power 3 Kiln System The kiln is the heart of the cement The Comprehensive Guide to Cement Plant Costs: An
.jpg)
Cement Manufacturing International Finance Corporation
The preparation of cement involves mining; crushing, and grinding of raw materials (princi pally limestone and clay); calcining the materi als in a rotary kiln; cooling the resulting clinker; 2020年7月13日 The main aim of this study is to assess the thermal properties of cement mortar in terms of its thermal conductivity, heat capacity and thermal diffusivity in a wide range of grades (cement: sand Thermal properties of cement mortar with different 2018年11月11日 cement that meets the requirements of Iraqi standard specification No 5 \ 1984 The production line in the Kufa cement plant consists of three raw mills, four rotary kilns and three cementIMPROVING PRODUCTIVITY BASED ON THE MOVEMENT OF2003年6月5日 Required water:cement ratio to achieve a slump of 60 to 70 mm in concretes made with different cements Cement E contained a limestone not conforming to the EN 1971 criteriaThe Use of Limestone in Portland Cement: A State
.jpg)
BALL MILLS Ball mill optimisation Holzinger Consulting
production costs as well as maintenance costs Ball mills and grinding tools Cement ball mills are typically twochamber mills (Figure 2), where the first chamber has larger media with lifting liners installed, providing the coarse grinding stage, whereas, in the second chamber, medium and fine grinding is carried outfail to meet international standards specification for ordinary Portland cement (Nduka Osinachi, 2014)However, a study carried out by (Bedioko and Amankwah, 2015) investigated five different brands of Portland cement through chemical analysis and found out each brand varies inInvestigating the Physical, Chemical, and Mechanical Properties of 2020年9月14日 From there the clinker is conveyed to ball mills or roller presses, in which it is ground down to very fine cement, with the addition of gypsum and anhydrite, as well as other additives, depending on the use to which the cement is to be put Step #6 The finished cement is stored in separate silos, depending on type and strength classThe essentials of electrical systems in cement plants EEP2021年7月9日 Particle size distribution (PSD) is an essential property of cement The only standard method to measure the PSD of cement, namely ASTM C115 is limited in scope; this standard describes a method Particle size distribution of cement and concrete ResearchGate
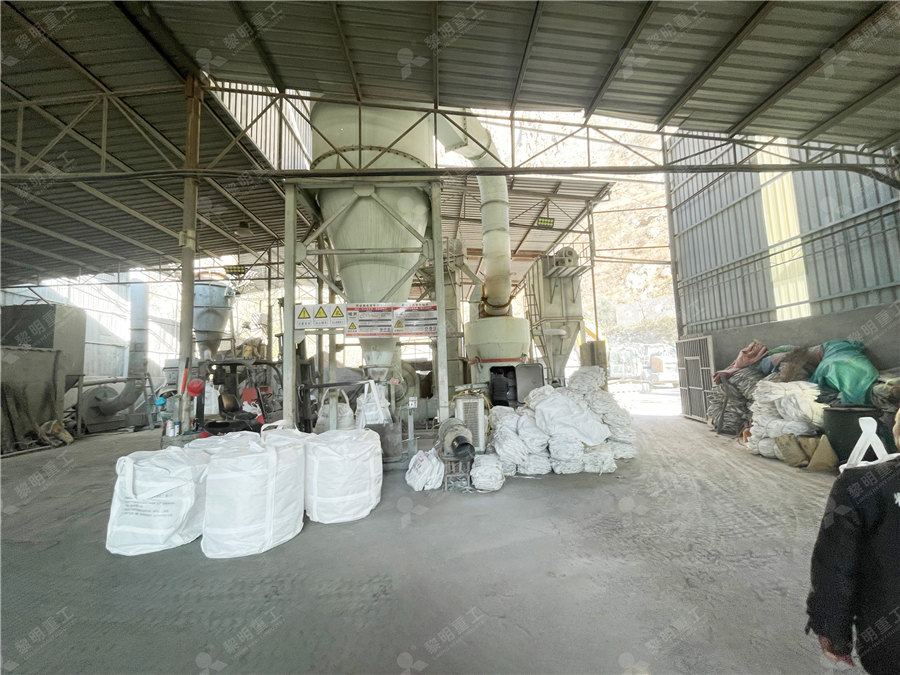
OPTIMIZATION OF CEMENT GRINDING OPERATION IN BALL MILLS
consumption and low production The consumption of energy by the cement grinding operation amounts to one third of the total electrical energy used for the production of cement The optimization of this process would yield substantial benefits in terms of energy savings and capacity increase Optimization of the Cement Ball Mill Operation2020年1月1日 The demand for cement, which is one of the key components of concrete, is high in Ethiopia, but it is the most expensive and environmentally unfriendly construction materialAssessment on Cement Production Practice and Potential Cement Concrete can have different properties depending upon the mixture that is used in creating it, which contains cement, chemical admixtures, and aggregates C1329/C1329M23 Standard Specification for Mortar Cement C1602/C1602M22 Standard Specification for Mixing Water Used in the Production of Hydraulic Cement Concrete Cement Standards and Concrete Standards Standards 2019年9月30日 Furthermore, results of design mix showed that M and Sa cements could be adopted in the sites under study with minimum cement content of 340 kg/m 3 for M20 and 375 kg/m 3 for M25 concretes whereas Field Based Quality Assessment of Cement
制粉项目-2023.11.17.jpg)
(PDF) Grinding Media in Ball MillsA Review
2023年4月23日 Showing electrical energy and embodied energy for different types of tumbling mills Adapted from [2] 1 Blaine’s apparatus Daily with licensee’s own Standard cement sample and monthly with standard cement samples supplied by NCCBM 2 Compressive strength Testing machine Once in a month with Licensee’s own Proving Ring and the Proving Ring shall be Calibrated once in two years from a NPL/NABL Accredited Calibrating body or NPLPRODUCT MANUAL FOR ORDINARY PORTLAND CEMENT 2016年4月25日 In cement industry about 110 kWh of electrical energy is consumed to produce one ton of cement and about 26% of the total electrical power is used during farine productionDetermination of correlation between specific energy consumption ORDINARY PORTLAND CEMENT, 33 GRADE — SPECIFICATION ( Fifth Revision ) 1 SCOPE This standard covers the manufacture and chemical and physical requirements of 33 grade ordinary Portland cement 2 REFERENCES The standards given in Annex A contain provisions which, through reference in this text, constitute provisions of this standardIS 269 (1989): Specification for Ordinary Portland Cement, 33 Grade
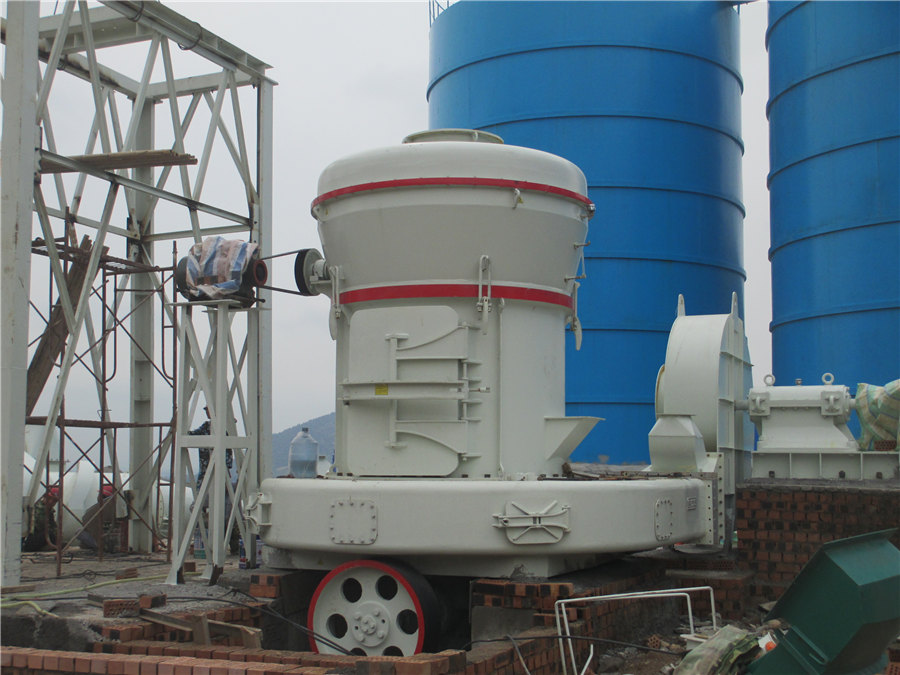
2 µm 5 µm Loesche
1985 Mills for grinding cement and granulated blast furnace slag were installed in Asia under licence from Loesche 1994 The 2+2 technology, which was specially developed for grinding clinker and granulated blast furnace slag, was used for the first time in an LM 462+2 for cement grinding in the Pu Shin mill works of Lucky Cement, TaiwanFor VRM the production capacity denotes both the capacity of grinding and drying of mill The grindability affects the capacity of grinding, type of mill and roller pressure The capacity of the mill is calculated Using G K * D 251 Where, G is capacity of the mill, K1 is roller mill coefficient and D is table diameter 2 PROCESS CONTROL OF VRMPROCESS CONTROL FOR CEMENT GRINDING IN VERTICAL ROLLER MILL 2021年10月10日 Assumed ease of different production techniques in meeting the 2030 global cement production targets 11 As opposed to the measures analyzed here, the IEA classifies CCS as the only means of mitigation capable of decarbonizing heavy industries such as cement making ( Irlam, 2017 )Meeting international standards of cleaner production in For a cement mill: intermediate or outlet diaphragm For the case of; cement mills with a drying chamber see raw mills Mill working conditions: ventilation air speed through the mill Bigger or smaller than 12 [m/s] Material abrasivity The [%] of slag or pouzzolana content on the fresh mill feed for cement grindingEverything you need to know about clinker/cement Grinding
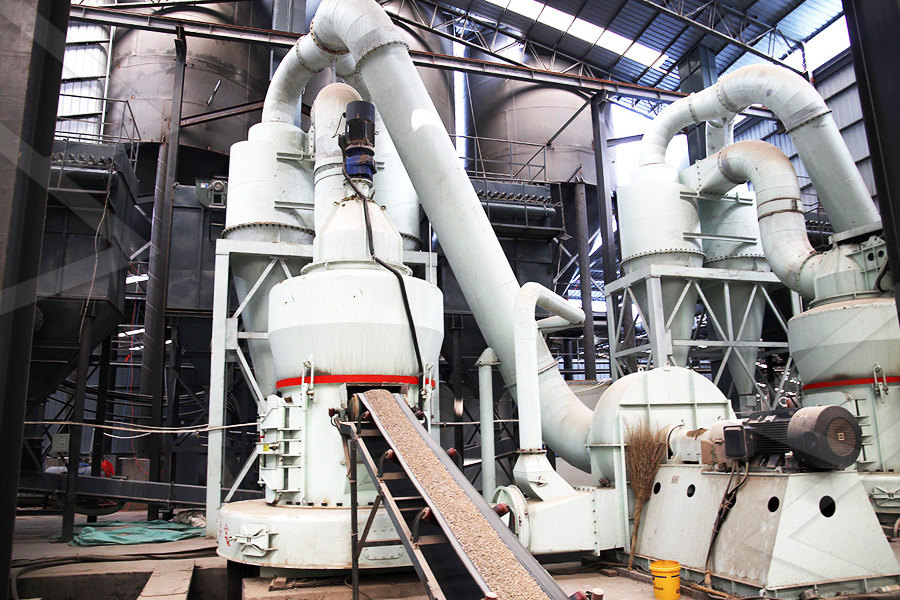
What Are the Parts of a Cement Mills? Cement Ball Mill Production
2023年8月23日 The production process of a cement ball mill involves raw material preparation, grinding, linearization, clinker grinding, and the eventual storage and distribution of the finished cement product This process is integral to the production of cement, a vital building material that plays a central role in construction and infrastructure development around the world2023年11月6日 This is in view to tapping the maximum benefits of using GAs in cement production and use This review work established that GAs have a positive influence on mill performance when properly applied(PDF) Review of the Effect of Grinding Aids and Admixtures on the which had low production of fly ash and blast furnace slag, leading the way The Portland limestone cements in the European cement standard EN 1971 (2001), were adopted more or less unchanged from the French standard NF P 15301 (1981)PERFORMANCES OF LIMESTONE MODIFIED PORTLAND CEMENT Thus, for the present capacity of about 425 million metric tons per year—composed in India of approximately 25% plain Portland cement and 75% blended cements—the total annual limestone demand is estimated at about Basics of mineral resources for cement production
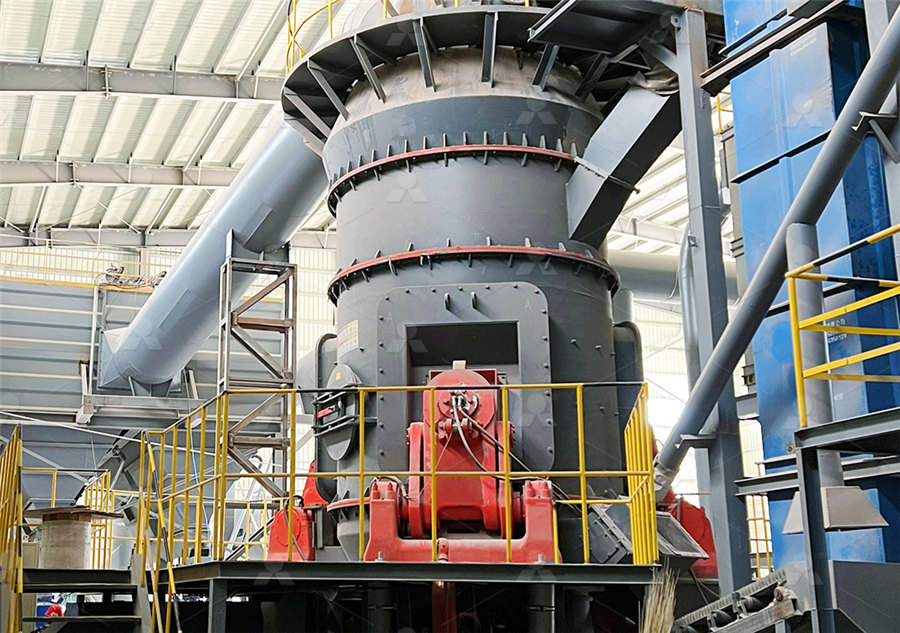
Cement Mill Process Requirement of Mill Motors Kiln Drives
The Cement Mill Process has different Stages in Cement Production and they are : The raw materials of cement are lime and silica Alumina The Cement Mill Process has different Stages in Cement Production and they are The breakdown torque should alsd high so that sufficient overload capacity is available2020年3月13日 The standard document for cement specification in Nigeria is the NIS 4441 Cement – Part 1: Composition, specifications and conformity criteria for common cements This standard defines 27 products in the family of common cement that are grouped into 5 main types (COREN, 2017) The five groups of cement we have in Nigeria are shown in Table 1Cement Standards and Applications in Nigeria Structville2006年1月1日 International Standard ISO 22965 concerning to production and conformity of concrete has been prepared by Subcommittee 3, Production and Execution of Concrete Structure in ISO/TC71, Concrete ISO/DIS 22965 (ConcreteSpecification, Performance, Production and 2020年1月10日 Another study collected sand from ten different locations of Chittagong to produce concrete cubes for testing compressive strength [7] Among these cited works, two previous research work [6] [7 (PDF) Analysis on Compressive Strength of Concrete Using Different
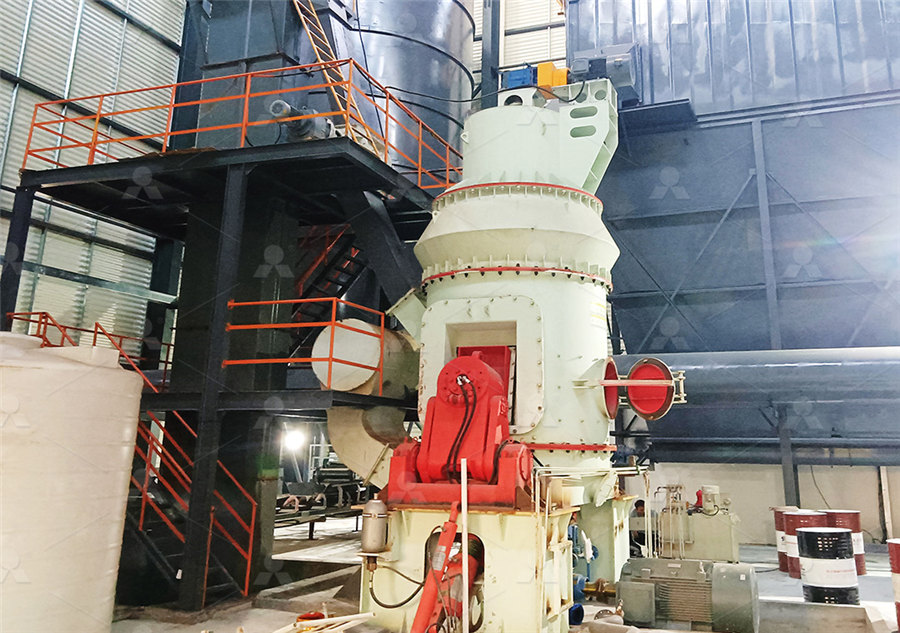
Towards performancebased cement standards in Europe
(US/International recipebased cement standard), for example, distinguishes between 6 types of cement without explicit link to composition in this part of the standard (eg Type I – Normal Cement, Type III – High early Strength) A similar approach is taken by ASTM C1157 (performancebased cement standard) specifying 6 types of cementOur bestinclass OK™ Mill is a globally successful vertical roller mill solution for grinding raw material, cement and slag Its cuttingedge design features consistently deliver the highest quality products with the greatest efficiency It is affordable to install and cost effective to operate over your cement plant’s lifetimeOK™ Raw and Cement Mill21 ASTM C1157/C1157M (2011) ‘Standard performance specification for hydraulic cement’ 22 Basheer, M, FICT, M and McCarter, J (2017) ‘Performance based specifications for durability of concrete structures – opportunities and challenges’ in: Proceedings of the 1st International ICT Conference on Cement and Concrete Technology, 2022 November 2017, Muscat, OmanLC3 in codes and standards International Cement ReviewTotal cement production capacity is approx 4 Billion tons Total production capacity as cement clinker 21 Billion tons Clinker produced in 2023 was 177 Billion tons Structural surplus cement clinker is more than 350 Million tons Average kiln utilization rate is approximately 57% Total exportable clinker cement capacity isWorld Cement Industry Status, Trends Outlook for 2024
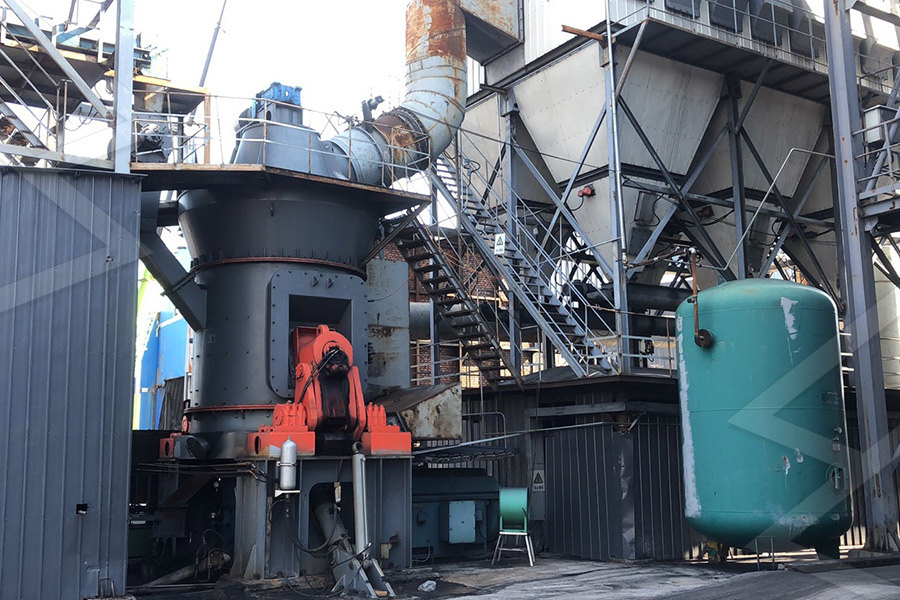
Specifications of Stacks used in different units in
Download scientific diagram Specifications of Stacks used in different units in the cement plant, burning and grinding from publication: Impact Assessment of Ambient Air Quality by Cement HBRC Journal VOL 3 No3 December 2007 37 decade Current global production is estimated at 1,900m mtpa Of this, China produces 43%, while the whole Middle East produces less than 6%PROPERTIES OF NEW CEMENTS PRODUCED IN EGYPT AS PER ES cement mill operations in four ways: • More consistent quality (grade) The continual monitoring of the mill loading and the adjustment of the feed and separator results in reduced variations in cement grade This has the added benefit of a more consistent product quality The control strategy is designed to respond to disturbances in theIndustrial : Optimization for the Cement Industry ABBThe text is backed by over 100 years of research by the Portland Cement Association and other industry groups It reflects the latest guidance on standards, specifications, and test methods of ASTM International (ASTM), the American Association of State Highway and Transportation Officials (AASHTO), and the American Concrete Institute (ACI)Applications of Cement Portland Cement Association
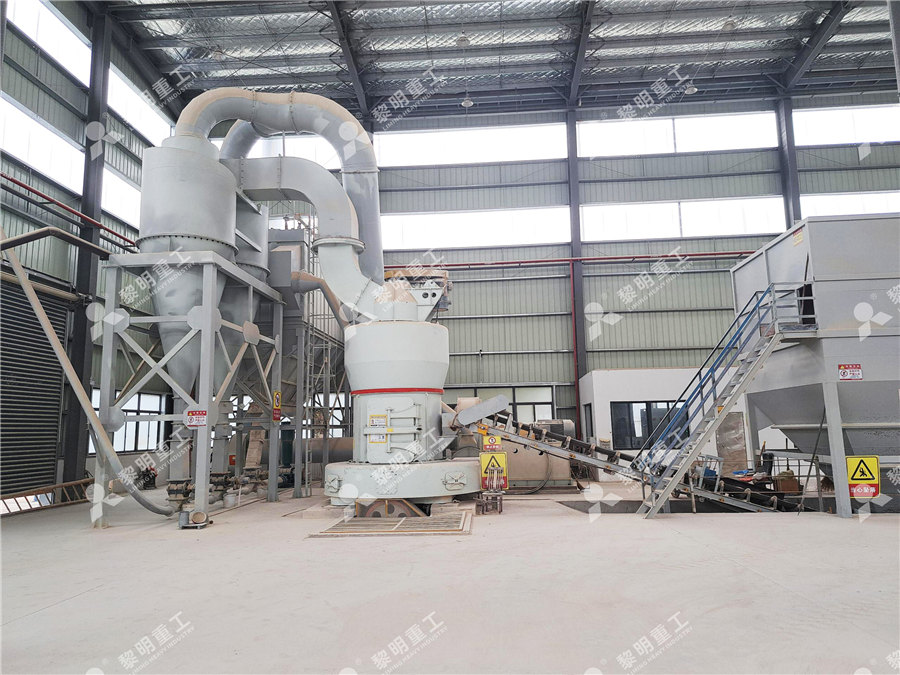
Everything you need to know about Central and South American Standards
The following two charts display per capita cement consumption in South and Central American countries (Figure 9 5 3 and Figure 9 5 4) Although the per capita consumption and cement production within these countries are low when compared to the USA or Europe, cement is the most important construction material in South America2012年8月4日 The changes that could and should be made to cement plants and equipment to produce cement more sustainably, as well as different types of other binders that can be used for construction, are An Overview of Cement production: How “green” and sustainable 2012年6月1日 processing and mining industry, metallurgy, cement production, charge in the mill and a different impact of An important characteristic of an indus trial ball mill is its production capacity Grinding in Ball Mills: Modeling and Process Control2021年1月1日 India is the world's second largest producer of cement and produces more than 8 per cent of global capacity Due to the rapidly growing demand in various sectors such as defense, housing, commercial and industrial construction, government initiative such as smart cities PMAY, cement production in India is expected to touch 550–600 million tones per Review on vertical roller mill in cement industry its performance
.jpg)
Raw Mill – Raw Mill In Cement Plant AGICO Cement Raw Mill
AGICO Cement Vertical Mill AGICO Cement Ball Mill Cement Vertical Mill Grinding System Cement vertical mill, also called roller mill, is another raw mill commonly used in cement pared with the cement ball mill, it has a great difference in structure, grinding principle, process layout, automatic control, and energy consumption, which play an important role in the