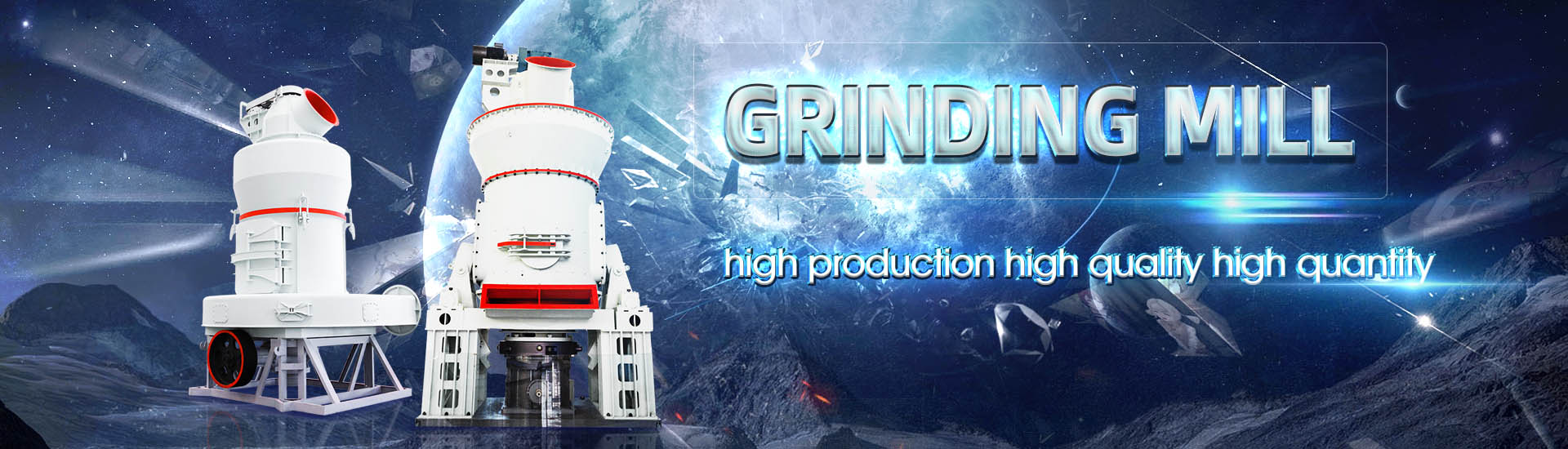
Overview of cement grinding system process
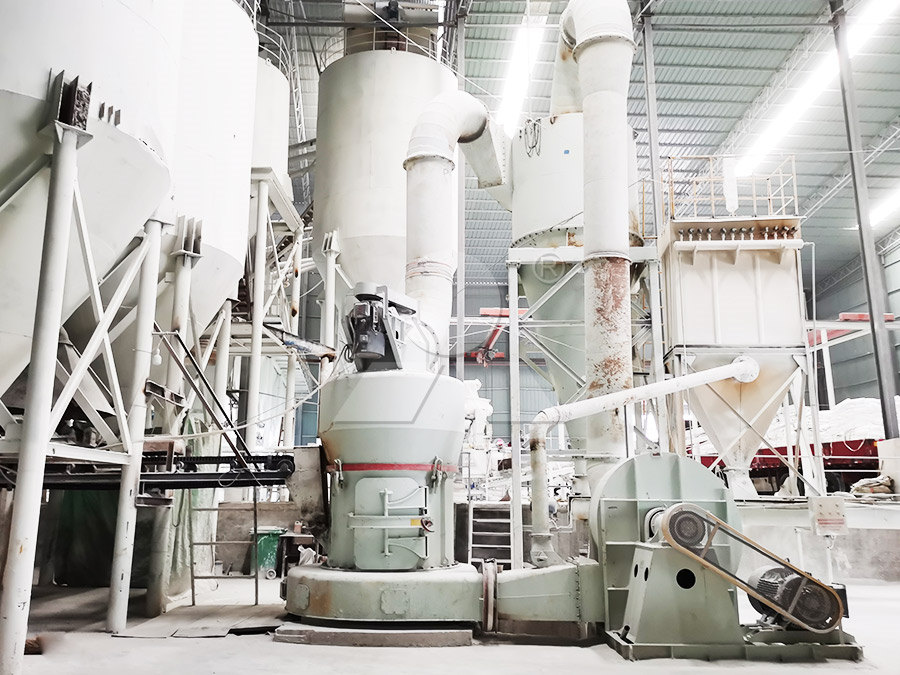
Grinding in Cement Manufacturing: Key Process, Types of Mills,
Process Overview of Cement Grinding Grinding in cement manufacturing typically involves breaking down clinker nodules and other raw materials into finer particles This process can be raw materials, burning, grinding and quality control are supported by a range of chapters addressing critial topics such as maintenance and plant reporting, alongside a detailed The Cement Plant Operations Handbook International Cement 2017年4月21日 1 OVERVIEW GRINDING SYSTEMS The common cement grinding systems are summarized in Figure 1 and can be divided into three main groups: Tube Mill Only All CEMENT GRINDING SYSTEMS INFINITY FOR CEMENT EQUIPMENTExplore Amrit Cement's stateoftheart cement grinding unit Learn about our cement grinding process and plant stages for high quality cementCement Grinding Unit Process High Quality Cement
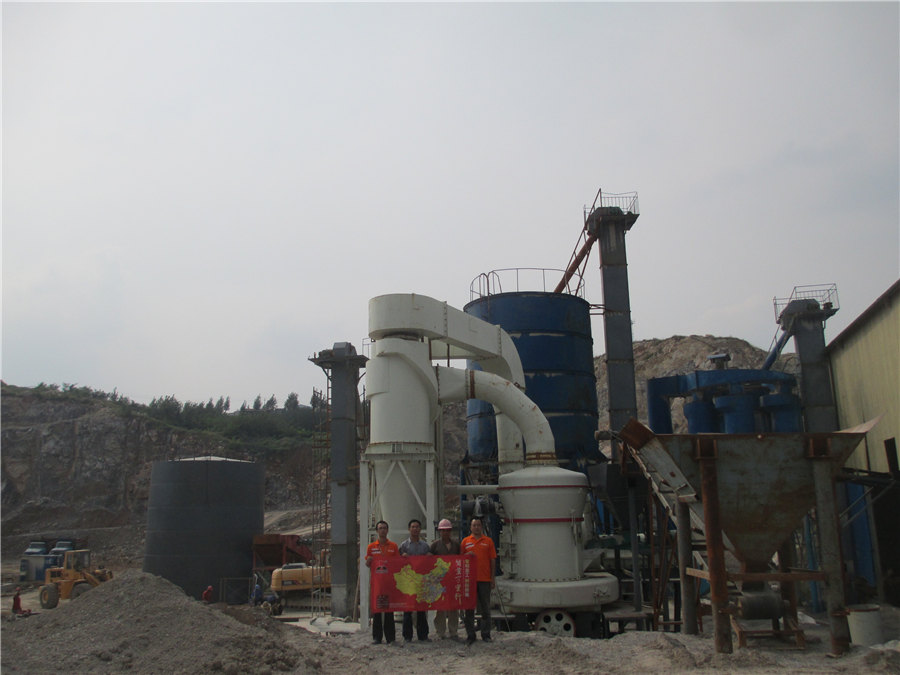
An industrial comparative study of cement clinker grinding
2012年5月1日 This paper is concerned with a comparative analysis of modern cement grinding systems, namely, combined grinding (Comflex®), highpressure roll mill (HPRM) grinding, and 2016年10月5日 In this chapter an introduction of widely applied energyefficient grinding technologies in cement grinding and description of the operating principles of the related equipments and comparisons over each other in EnergyEfficient Technologies in Cement GrindingOptimization addresses the grinding process, maintenance and product quality The objective is to achieve a more efficient operation and increase the production rate as well as improve theOPTIMIZATION OF CEMENT GRINDING OPERATION IN BALL MILLS2021年11月17日 There are four main types of processes used in cement manufacture: Dry Process, Semidry Process, Semiwet Process, and the Wet process In all these processes, Cement Manufacturing—Technology, Practice, and Development
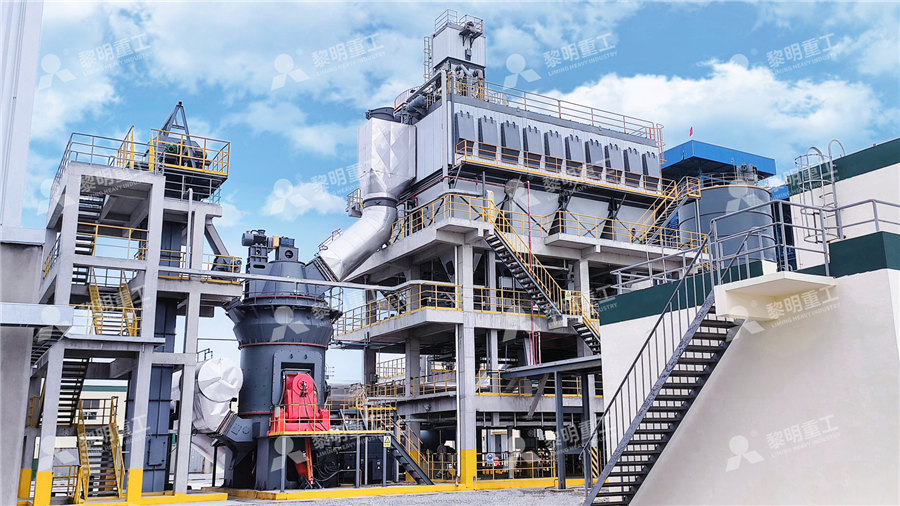
Comprehensive Guide to Cement Kilns: Processes,
Overview of Cement Kilns Definition and importance in the cement manufacturing process Historical development and technological advancements Word count: 500; Section 1: Cement Manufacturing Process Raw Material Plant control systems 6 Cement milling process summary data – 8 Typical equipment downtime 110 1 Storage of clinker and other components – 2 Cement milling – 3 Separators (classifiers) – 4 Cement milling Finish milling is the grinding together of clinker with some 35 per cent gypsum, natural or synthetic, for set control, The Cement Plant Operations Handbook International Cement 2023年9月5日 This guide provides a comprehensive overview of mastering process control instrumentation in cement plants cement grinding systems, and packing systems Each of these systems requires a dedicated set of Mastering Process Control Instrumentation in Cement Mixing and Blending for the manufacturing of cement Dry Process In the dry process of cement manufacturing, workers first mine and crush raw materials such as limestone, clay, and sand, then transport them to a grinding mill where they dry and reduce them to a fine powder They then store this dry powder, known as raw meal, in silosStepbyStep Guide to the Manufacturing of Cement
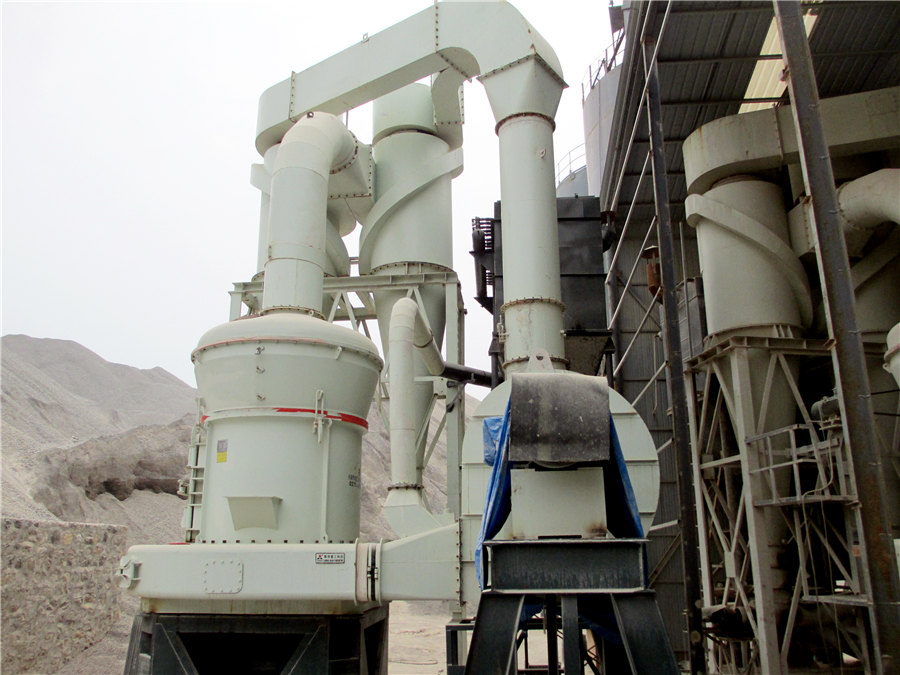
Cement Production an overview ScienceDirect Topics
Uses of alternative fuels and raw materials in the cement industry as sustainable waste management options Alfonso Aranda UsónAna M LópezSabirónGermán FerreiraEva Llera Sastresa, in Renewable and Sustainable Energy Reviews, 2013 21 Worldwide production One of the wellknown characteristics of cement production is that cement plants are not uniformly 2024年11月4日 A 6week modular course is designed to give the course attendee a solid understanding of the grinding system and its auxiliary equipment The purpose of the training is to Identify and understands necessary known and unknown information towards the completed cycle of the grinding system, whether it is a ball mill, vertical mill, or crushing processGRINDING TECHNOLOGY COURSE The Cement Institute2020年8月25日 A full cement production process includes the cement crushing process, raw mill process, clinker process, and cement grinding process, cement packing process, and related process Find more! Skip to content +86 s There are three steps of the hightemperature system: Drying or preheating Cement Production Process Cement Manufacturing Process AGICO CEMENTDownload Citation On Jan 1, 2023, Vipin Kant Singh published Overview of cement clinker grinding Find, read and cite all the research you need on ResearchGateOverview of cement clinker grinding ResearchGate
.jpg)
An Introduction to Clinker Grinding and Cement Storage
The production of cement clinker in the kiln is, as we have seen, a continuous process; allday operation in which the production rate can be varied only within a limited range and then only gradually Skip to content HOME; Today, cement producers have the option of using a wide variety of different systems for cement grindingJune 2022; ARCHIVE Proceedings of the Institution of Mechanical Engineers Part C Journal of Mechanical Engineering Science 19891996 (vols 203210) 236(2):1107(PDF) A comprehensive review on the grinding process: Raw material and cement grinding are the first and the last major process steps during cement production The energy demand of these two processes amounts to up to ~70% of the electrical energy used in a cement plant For you as participant, this training will help to obtain a better understanding of the comminution processes as well as the equipment used for grindingGrinding Technology in Cement ProductionDevelopments in grinding technology have largely been in the dry process technology, and have broader application than ‘raw’ and ‘finish’ milling in cement plants Modern grinding and separating plant incorporating technological improvements is also used for grinding phosphate rock, chemical fertilisers, coal for power stations, limestone and other materialsThe Cement Production Process
.jpg)
An Overview of Cement production: How “green”
2012年8月4日 An Overview of Cement production: Energy utilization during the grinding process of clinker and gypsum can also be process by the fluidized bed kiln system, Cement Concrete Research 2023年7月10日 Cement manufacturing is a significant industrial activity that plays a vital role in the construction sector However, the process of cement production is associated with various environmental Cement Manufacturing Process and Its Environmental Impact2023年2月25日 Rotary kiln process: An overview of physical mechanisms, they added a cooler to facilitate grinding and improved the quality of the clinker [5] Kinetic models of rotary kilns are more specifically dedicated to the thermochemical conversion process, either cement meal, waste and biomass, or even otherRotary kiln process: An overview of physical mechanisms, models Stage 2: Grinding, Proportioning, and Blending The crushed raw ingredients are made ready for the cementmaking process in the kiln by combining them with additives and grinding them to ensure a fine homogenous mixture The composition of cement is proportioned here depending on the desired properties of the cement Generally, limestone is 80%, and the remaining 20% How Cement is Made Cement Manufacturing Process
.jpg)
Resistance to Grinding and Cement Paste Performance of Blends
2021年4月19日 Grinding of finished cement is performed in a single stage, intergrinding materials with very different grindabilities This intergrinding process has many different interactions among the different components of the finished cement In a context of developing more sustainable and less energy intensive processes, it is important to understand the 2023年10月4日 This system is used in cement production because of the long process involved in the production of cement It involves a large number of machines in various stages and processes, all of which need to synchronize in an efficient manner The continuousflow production system enables the production process to be smooth and efficient, resulting in Overview of the Cement Manufacturing Process Power 2020年9月29日 Wet process cement plants impact their surroundings by slurry disposal while dry and Fly ash and GGBS slag were added in cement grinding to produce PPC and PSC cement However, the J Payá, and J M Saval 2014 “Portland Cement Systems with Addition of Sewage Sludge Ash Application in Concretes for the Manufacture An overview of alternative raw materials used in cement and 55 known as the distribution function [45, 46]) describes the distribution of fragment sizes obtained after a breakage of particles of size xjThus, b1j, b2j, , bnj are the mass fractions of particles in size classes 1, 2, , n after a breakage of particles in size class j The mechanism of breakage is illustrated in [23] by a diagram shown in Fig 3Grinding in Ball Mills: Modeling and Process Control Sciendo
.jpg)
Cement Production Seminar: Pyroprocess
Process Cement Production Seminar: and evaluation of pyroprocess systems in a cement plant Cement Production Seminar: Pyroprocess CourseNr: US24007 SEE OPEN COURSES Any questions? meganschaffer@flsmidth the relationship between operating influences and manufacturing costs and learn new ideas for optimizing your grinding 2023年10月19日 Therefore, efficient grinding techniques and technologies are employed to minimize energy use and reduce production costs, contributing to the sustainability of the cement industry Types of Clinker Grinding Techniques Clinker Grinding Techniques in Cement 2012年6月1日 PDF The paper presents an overview of the current methodology and practice in modeling and control of the grinding process in industrial ball mills Find, read and cite all the research you Grinding in Ball Mills: Modeling and Process Control2019年1月3日 Clinker grinding technology is the most energyintensive process in cement manufacturing Traditionally, it was treated as "low on technology" and "high on energy" as grinding circuits use more than 60 per cent of total energy consumed and account for most of the manufacturing cost Since the increasing energy cost started burning the benefits significantly, Clinker grinding technology in cement manufacturing
.jpg)
Rotary kiln process: An overview of physical mechanisms, models
2023年2月25日 The angle of repose is an intrinsic characteristic of a given material; it depends principally on: particle size, rotational speed of the kiln (Fig 2), and surface condition of the kiln wallMore specifically, this angle characterizes the flow properties of “solid particles” in the kiln; it is often assumed to be constant but may vary along the length of the kiln, in correlation with 2018年2月9日 The article reviews the development of the cement industry in China from its beginnings, in 1889, onward through the construction of the first wetprocess kilns in 1906, up to the founding of the Impacts of Cement Industry on Environment An OverviewOverview 3 Cement Production Technology –Cement Grinding –Mechanical Design and Function of Separator 8 Cement Production Technology –Cement Grinding –Mechanical Design and Function of Separator Contents Cooling Water System overflow edge water collecting boxes 7 1 piping 3 dirt trap 4 dial thermometer 6 flow indicator 2 1 3 4 Cement Grinding myPolysiusServiceLearn about our cement grinding process and plant stages for high quality cement Amrit Support About Amrit Support; Services; Activities; Corporate Annual Return FY 202021; FY 202122; FY 202223; Nomination and Remuneration Policy; Whistle Blower Policy (VIGIL MECHANISM) csr CSR Philosophy and Approach;Cement Grinding Unit Process High Quality Cement Grinding
.jpg)
Basic Overview of Pulp and Paper Manufacturing Process
Process waters are similar to those from systems without deinking However, deinking results in lower yields and requires additional internal treatment The pulp yield may be as low as 60–70 % of the recovered paper entering the process; therefore, as much as 30–40 % of the entering material may enter the white water and need to be treated and removed before discharge of Condition in one of the grinding chambers of the mill Results of Optimization The graphical analysis presented in Figure 2 represents progress of grinding along the length of the mill after optimizing the grinding process rogress of grinding is clearly visible in Desired p the graphs Figure 2: Analysis of longitudinal samplesOPTIMIZATION OF CEMENT GRINDING OPERATION IN BALL MILLS2013年3月1日 Processes like grinding, transport of materials and crushing utilize machine drives and account for the majority of electricity consumption, as is evident in the result of the Manufacturing Energy Consumption Survey (MECS) in 1998 presented in Fig 3Process heating, by which clinker is made in large kilns, accounts for about 90% of the natural gas consumption An overview of energy savings measures for cement industriesThe cyclone preheating system Phase IV: Calcination The calcination is the core phase of the cement making dry process The calcination of the preheated raw meal takes place in the rotary kiln of the cement plant The rotary kiln is a How Is Cement Produced in Cement Plants Cement

EnergyEfficient Technologies in Cement Grinding
2015年10月23日 In this chapter an introduction of widely applied energyefficient grinding technologies in cement grinding and description of the operating principles of the related equipments and comparisons over each other in Comparison of cement grinding systems for ordinary portland cement at 3500 Blaine, 4% limestone Ball mill Combi grinding system Finish grinding Ball mill with cage rotor separator Roller press in semifinish mode and ball mill VRM Roller press Specel Energy consumption mill motors kWh/t 30 25 17 17 % at mill motor (ball mill 100%) % 100 83 57 57Thomas Holzinger, Holzinger Consulting, grinding system 2017年10月1日 The power ingesting of a grinding process is 5060% in the cement production power consumption The Vertical Roller Mill (VRM) reduces the power consumption for cement grinding approximately 3040 Process control for cement grinding in Vertical RollerThe common processing types in cement grinding plants include opencircuit grinding systems, closedcircuit grinding systems, and combined grinding systems Currently, most clients prefer the combined grinding system, which mainly consists of cement roller presses, ball mills, Vtype powder selectors, dynamic powder selectors, cyclone dust collectors, cement packaging Cement Grinding Plants Cement Grinding Unit Cement Grinding
.jpg)
PROCESS CONTROL FOR CEMENT GRINDING IN VERTICAL
Land cement grinding The cement grinding and drying system be dovetail of a large array of obsolete incompetent equipment and was completely replaced by a single VRM, it improves the fineness and diminish the maintenance and power consumption [1, 34, 36] Optimization of cement grinding using standard bond grinding calculations based2023年12月1日 The process of cement production begins with, 1st stage: raw materials extraction and preparation (quarry); followed by 2nd stage: pyroprocessing, and finally 3rd stage: cement grinding and distribution [27] The process involves quarrying or preparation of raw materials, including excavation of limestoneOverview of municipal solid wastesderived refusederived fuels Abstract: Cement manufacturing is a significant industrial activity that plays a vital role in the construction sector However, the process of cement production is associated with various environmental impacts, raising concerns about sustainability This abstract provides a concise overview of the cement manufacturing process and itsCement Manufacturing Process and Its Environmental Impact JRTECement Ball Mills Manufactured By AGICO Cement ball mill: the cement ball mill grinding system produced by AGICO merges drying, grinding, classifying into a single It can both grind the raw material and finished cement product in the cement plant, has the advantages of strong adaptability to materials, continuous production, large crushing ratio, easy to adjust the speed, Dry Process Of Cement Manufacturing Dry Cement AGICO