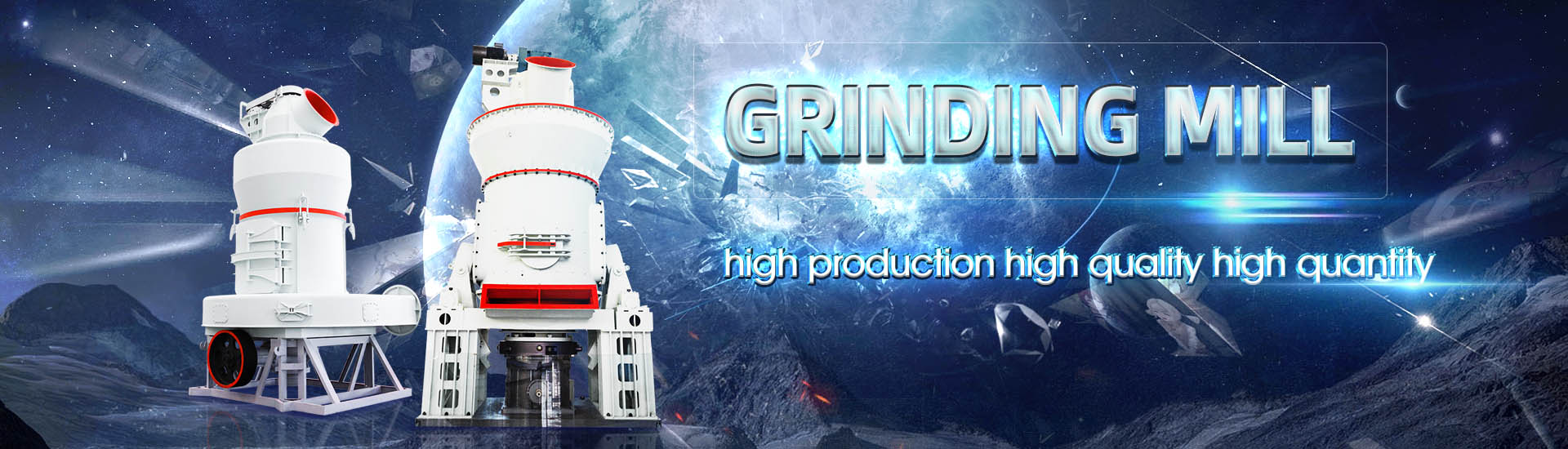
Cement brick production licensing procedures
.jpg)
Soil cement brick production process: literature review MedCrave
article presents a literature review based on research in the production of soilcement bricks Materials and research methods used in the process of making soilcement bricks, as well as various properties, are discussed The most common results are grouped The literaturepresents fundamental procedures for the manufacture of clay brick The types of clay used, the three principal processes for forming brick and the various phases of manufacturing, from Manufacturing of Brick Brick Industry AssociationIMARC Group’s report, titled “Cement Bricks Manufacturing Plant Project Report 2024: Industry Trends, Plant Setup, Machinery, Raw Materials, Investment Opportunities, Cost and Revenue” Cement Bricks Manufacturing Plant Report: Setup Cost IMARC How to start cement brick manufacturing with minimum hassle? Read how you can complete the whole setup and how the entire cement bricks business worksHow to Start a Cement Brick Manufacturing Business? Khatabook
.jpg)
Forms Checklists for Concrete Block and Brick Manufacturing
From production protocols to quality control measures, these forms and checklists play a crucial role in mitigating risks, reducing errors, and fostering a systematic approach2022年5月6日 Cement bricks are now extensively used in hilly areas because they can repel water for a prolonged period In this writeup, we will explore the setup and legal requirements for establishing a cement brick manufacturing Cement Brick manufacturing plant: Setup and Legal For shaping or forming the brick, the clay feed must be consistent in content, grading, plasticity and water content and three principal processes are used soft mud moulding; Brick and block production Mortar2018年3月20日 Researchers have mixed cement with copper mine tailings for the production of bricks and have concluded that by adopting cement content of 959–126%, good quality Towards sustainable bricks production: An overview
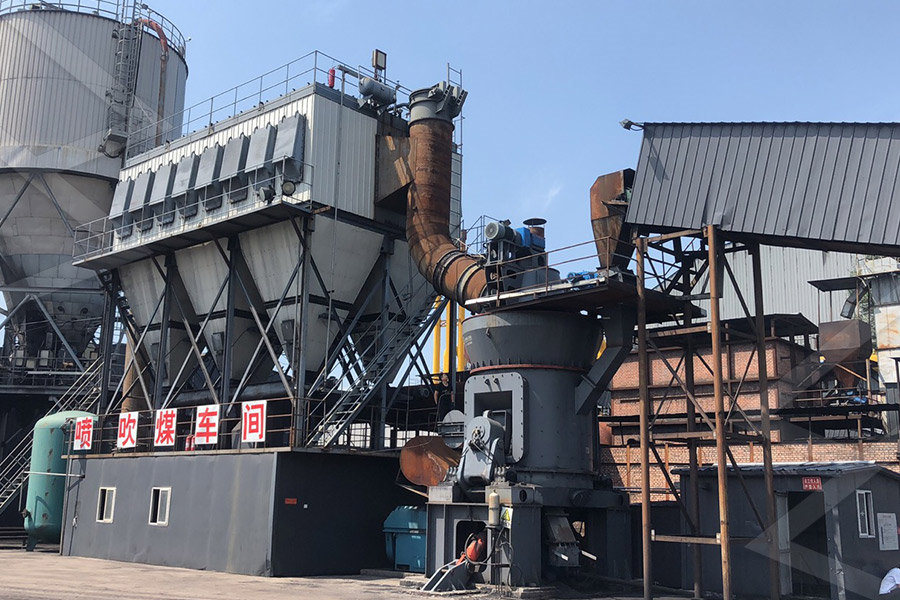
Manufacturing of Bricks for Masonry Construction –
The process of manufacturing of bricks from clay involves preparation of clay, molding and then drying and burning of bricks The bricks are building materials which are generally available as rectangular blocks The bricks do not require The smallscale manufacture of concrete bricks and blocks for masonry is well suited to small businesses Production can be done in the open, the process is simple and the equipment is Your Guide to Concrete Brick and Block Making 2021 Cbmeans it has sufficient characteristics to be used in soilcement brick manufacturing B Liquid Limit The liquid limit test followed the Brazilian Standard [1], as well as its specificities The Brazilian Standard for soilcement brick manufacturing requires a liquid limit lower than or equal to 45% The average of theVol 4 Issue 09, September2015 Manufacturing Soil Cement Brick2024年9月1日 Another example from cement production highlights limits for using different construction and demolition wastes as raw materials in cement production [81] Table 7 Summary of the main challenges for current closedloop recycling of CEM I, Reinforcement bars, flat glass, brick, glass wool, and sawn woodsMapping circular economy practices for steel, cement, glass, brick
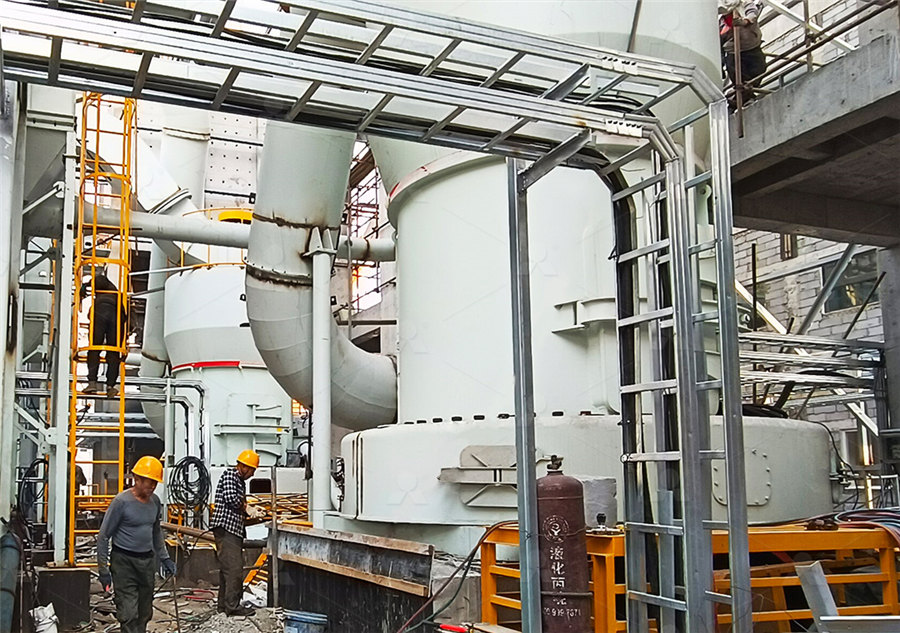
A Rational Approach to Estimating the Cost of LateriteCement
estimate using the three (3) procedures, compare with sandcrete block production and develop predictive equations for cost of lateritecement bricks production 2 Use of Statistical Mixture Experimental Design In using this procedure, experimental design points are used and material variables are fitted to the designated pointsTHE CEMENT MANUFACTURING PROCESS Prof Dr Elshafie Ahmed Gad Faculty of Applied Science Chemistry Dept Portland Cement Portland cement is made by mixing substances containing CaCO3 with substances containing SiO2, Al2O3, Fe2O3 and heating them to a clinker which is subsequently ground to powder and mixed with 26 % gypsum Raw Materials (PDF) THE CEMENT MANUFACTURING PROCESS Academia2022年5月31日 The cement brick reinforced with coconut fiber achieves the expected results in the compressive strength test and thermal conductivity test but underperformed when comparing masses and water Cement and Clay Bricks Reinforced with Coconut Fiber and Fiber I am Chao Zhang, I have been working in the brick making industry for over 10 years I have a deep understanding and research on various models of block making machines, especially automatic brick machines, concrete block machines, compressed earth block machines, clay brick machines, cement brick machinesThe Brick Making Process How Bricks Are Made Block Machine
.jpg)
The use of laterites for production of soilcement blocks
2014年4月1日 Cement, clay and laterite [10][11][12] has been used in the production of blocks for building materials till this present time Cement used for building blocks has some advantages such as high 45 The distance between two brick kilns shall not be less than 500 m to avoid clustering of brick kilns in an area if a new brick kiln is being installed 46 Brick kiln should be constructed at least 500 meters away from path of any natural water flow as well as from River bank water front of beels, lakes etc More over noGUIDELINES ON BRICK MANUFACTURING UNIT2022年2月24日 To reduce the carbon footprint in the brick production industry, Find, read and cite all the research you need on ResearchGate Article PDF Available A Sustainable Reuse of AgroIndustrial A Sustainable Reuse of AgroIndustrial Wastes into Green Cement 2020年12月1日 Owing to the soilcement brick shape, building a soilcement brick wall, as shown on Fig 1 (b), is simple and highly skilled labors are generally not required Because firing is not required after brick forming, the production of soilcement bricks significantly reduces energy costs compared to fired clay brick productionSoilcement bricks produced from local clay brick waste and
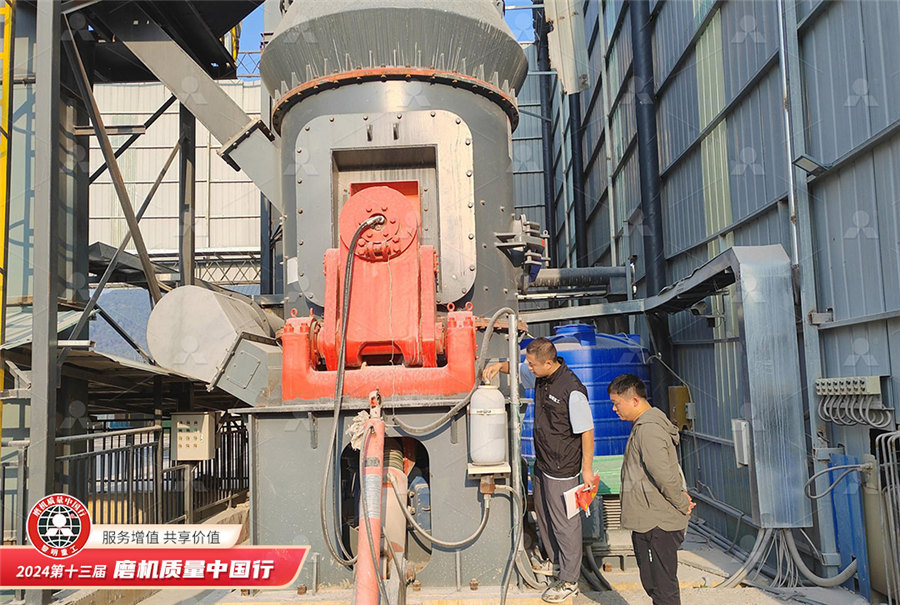
(PDF) Soilcement bricks produced from local clay
2020年11月25日 Soilcement bricks produced from local clay brick waste and soft sludge from fiber cement production November 2020 Case Studies in Construction Materials 13:e年10月1日 This study explored the influence of using copper slag as an alternative sand for producing cement mortar bricks and its effect on γray attenuation property, strength, and consistency of mortar The linear attenuation coefficients and mass attenuation coefficients were experimentally determined for mortar mixtures using the 60 Co and 137 Cs gammaray Incorporation of copper slag in cement brick production as a 2018年9月2日 2 1 Abstract Cement and clay bricks are extensively used construction material in Sri Lanka In Sri Lanka, the demands for both are high in building and infrastructure construction sector The purpose of this this study Sri Lanka’s cement manufacturing and bricks 2023年8月16日 Request PDF Soil cement brick production process: literature review Soilcement brick is one of the most common building materials for masonry construction, although it is not the oldest As Soil cement brick production process: literature review
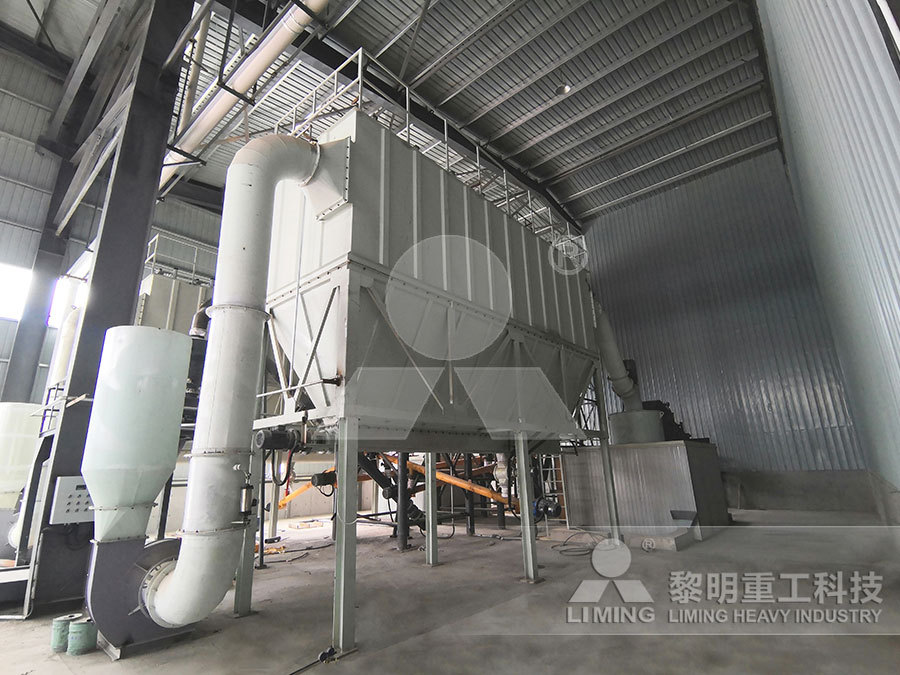
Your Guide to Concrete Brick and Block Making 2021 Cb
Your Guide to Concrete Brick and Block Making 2021 Cbdd 14 2021/09/30 15:11 The maximum jointing space depends on the thickness of the slab The site should be big enough for aggregate stockpiles, cement storage, production, block stacking, staff facilities, offices and onsite access The details are as below:2015年1月1日 Cement, as a binder, is the most expensive input in to the production of sandcrete SANDCRETE BLOCK AND BRICK PRODUCTION IN NIGERIA PROSPECTS the procedure for molding is as follows:SANDCRETE BLOCK AND BRICK PRODUCTION IN NIGERIA2008年6月1日 For soilcement brick containing no sand, the compressive strength has been reported as a maximum of 204 MPa, 349 MPa, 28 MPa, and 355 MPa for zero to five percent cement content, six to ten Use of CementSand Admixture in Laterite Brick Production for Low SOP1073014: Standard Operating Procedure for Brick Cutting and Trimming SOP1073015: Standard Operating Procedure for Concrete Block Stacking Protocol Production Process: Portland cement, water, sand, and gravel are act as a major raw material for manufacturing concrete blocks and bricksSOP Manual for Concrete Block and Brick Manufacturing SOP
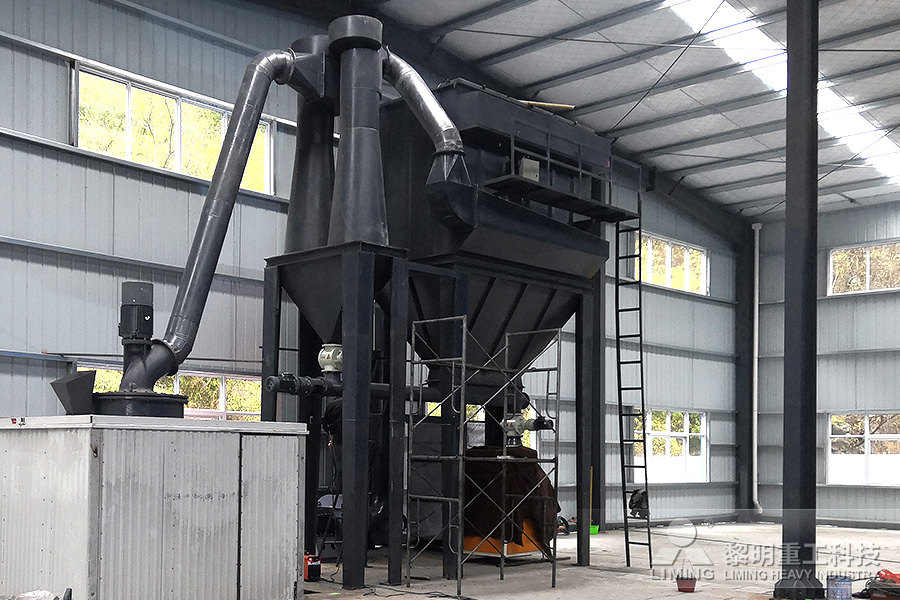
How to Start a Cement Brick Manufacturing Business?
Business Plan for Manufacturing Cement Bricks Business Plan The first stage is to develop an outline of your cement brick business plan When you're sure you'd like to start cement brick factories, it is essential to implement your plan first When drafting an enterprise plan, you must determine the business's strategy2021年10月1日 Incorporation of copper slag in cement brick production as a radiation shielding material Author links open overlay panel Sungwon Sim a, EPA Method 1311toxicity Characteristic Leaching Procedure The United States Environmental Protection Agency, Washington, DC (1992) the Creative Commons licensing terms apply Incorporation of copper slag in cement brick production as a 2023年12月20日 Blog article: PGNAA Improves Process and Quality Control in Cement Production to learn what makes PGNAA particularly suited for cement analysis Editor’s Note: This article was originally published 8/20/15 under the The Cement Manufacturing Process Thermo Fisher were followed for soil–cementparticle bricks production The specimens were produced at 20 × 95 × 5 cm (length, width, and thickness) dimensions Figure 1 demonstrates the materials used and the brick production After their production, the soil–cement bricks were packed in a box at 98% humidity level and stored in aLignocellulosic materials as soil–cement brick reinforcement
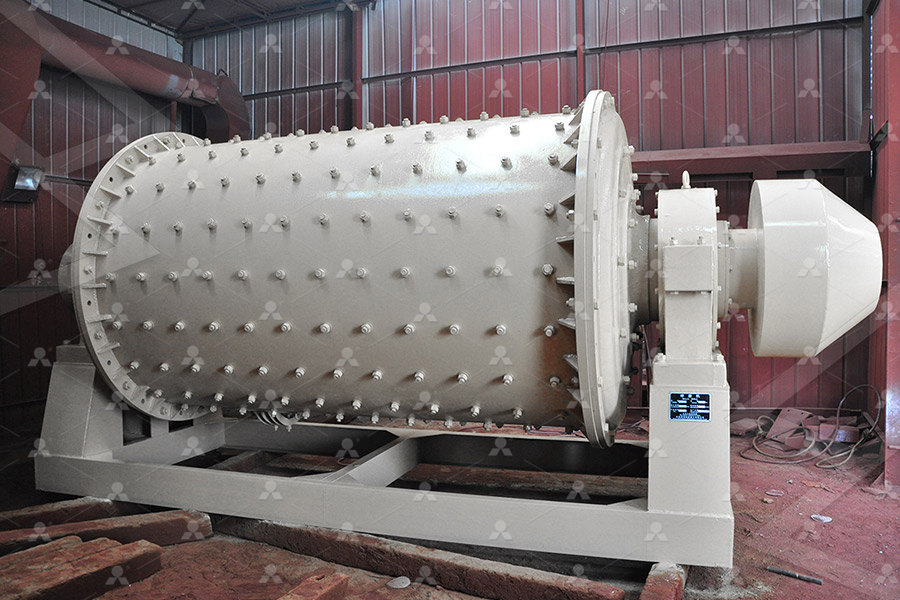
Effectiveness of replacing cement partially with waste brick
2024年11月1日 The chemical compositions of both cement and brick powder are listed in Table 1, and the particle distribution of cement and waste brick powder is in Fig 2The fine aggregate that was used has a maximum particle size of 425 mm, fineness modulus of 318, and a SG of 26, which is within the limits of the Iraqi Specification No45 (1984)2020年11月30日 Soilcement bricks have been gaining prominence in terms of sustainability since it does not use burning process in its manufacturing It uses less than 10% of the energy required to make burnt clay bricks and concrete masonry units, however modern production and construction methods using soil are required [10], [11]Soil masonry commercial brick making Technological properties of soilcement bricks produced with 2024年7月1日 Utilizing Sludges from Tanneries, Water Treatment Plants and Textile Industries in Cement, Concrete and Brick Production: A Review July 2024 Journal of Environmental Nanotechnology 13(2):135143(PDF) Utilizing Sludges from Tanneries, Water Treatment Plants 2023年3月15日 This paper aims to fabricate and optimize ecosustainable cement brick using different sizes of clay brick waste (CBW) The prime input factors of mixtures were clay brick powder (CBP) as a binder, fineclay brick (FCB) as a fine aggregate, and coarseclay brick (CCB) as a coarse aggregate, whereas the compressive strength was the main response of the Production and optimization of sustainable cement brick
.jpg)
KILN STARTUP PROCEDURES INFINITY FOR CEMENT EQUIPMENT
Previous Post Next Post Contents1 KILN STARTUP PROCEDURES11 KILN STARTUP PROCEDURES2 11 Parameters to be tracked during preheat3 111 Preheater/Precalciner4 112 Long Wet/Long Dry Kilns5 ¨ Thermal expansion of the kiln6 12 Tyre Creep601 Turning Schedule: Too Slow602 Too Fast KILN STARTUP PROCEDURES Scope of Work and 2023年4月28日 Sisal fibers have been employed in several reinforcing experiments [18]The compressive and tensile strengths of CSEBs reinforced with sisal fibers were the primary focus of the studies [19]The authors are unaware of any studies that specifically examine mechanical metrics associated with energy dissipation, such as toughness and ductility, for sisal fiber Compressed earth block reinforced with sisal fiber and stabilized 2021年4月1日 Characterization and recycling of textile sludge for energyefficient brick production in Ethiopia(PDF) Characterization and recycling of textile sludge for energy Report Overview: IMARC Group’s report, titled “Cement Bricks Manufacturing Plant Project Report 2024: Industry Trends, Plant Setup, Machinery, Raw Materials, Investment Opportunities, Cost and Revenue” provides a complete roadmap for setting up a cement bricks manufacturing plant It covers a comprehensive market overview to microlevel information such as unit Cement Bricks Manufacturing Plant Report: Setup Cost IMARC
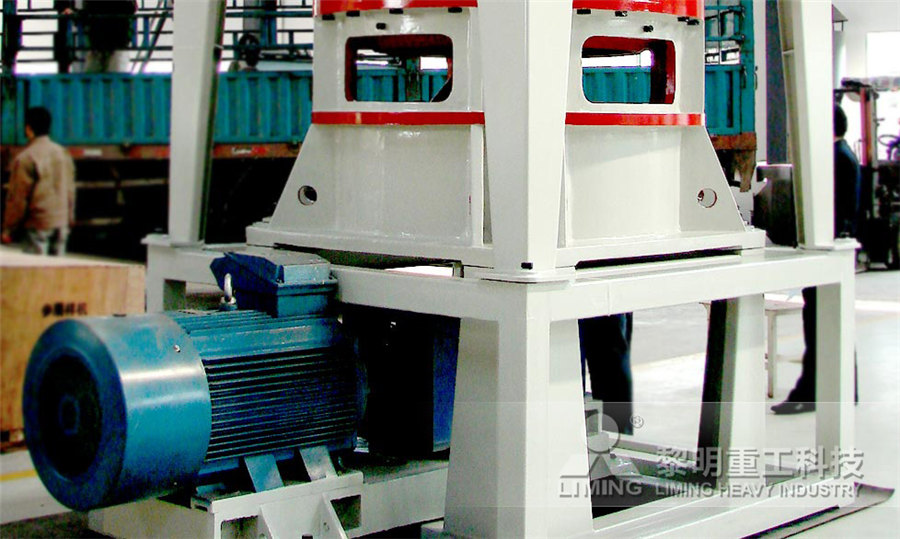
Soilcement brick with granite cutting residue reuse
2021年10月25日 The granite cutting residue (GCR) was supplied by Marmoraria Santana, located in Estância, State of SergipeThe residue used in this work was first dried in an oven, 105 ± 5 °C (ABNT, 2012a), later stored in plastic sealed containers, where they remained protected from the weatherAs shown in Fig 1, to replace the cement, the soil, and the sand, the residue 2006年7月1日 A study was conducted between October 2004 and April 2005 in Kampala District, with the objective of investigating the feasibility of making sawdustcement composites using saw dustProduction of composite bricks from sawdust using 2024年11月23日 Cement Extraction, Processing, Manufacturing: Raw materials employed in the manufacture of cement are extracted by quarrying in the case of hard rocks such as limestones, slates, and some shales, with the Cement Extraction, Processing, Manufacturing2018年3月20日 Manufacturing of bricks being an essential part of construction industry, contributes heavily to environmental degradation A brick kiln emits about 70–282 g of carbon dioxide, 0001–029 g of black carbon, 029–578 g of carbon monoxide (CO) and 015–156 g of particulate matter per kilogram of brick fired, depending on the type of kiln and fuel used for Towards sustainable bricks production: An overview
.jpg)
Soilcement brick with granite cutting residue reuse
2021年10月25日 This research aimed at the production of soilcement brick with the incorporation of granite cutting residue, from partial substitutions of the soil and cement, and the verification of the influence on this incorporation in the brick properties (specific gravity, water absorption, compressive strength, and durability)2023年10月15日 For centuries, soil has been used as a construction material [[1], [2], [3]]When the earthen building material is stabilized with agents like cement or lime in specific proportions, utilizing mechanical compaction to form a compressed earthen unit of specific regular shape and size, it is referred to as a compressed stabilized earthen block/brick [4, 5]Engineering properties of cementstabilized compressed earth 2017年12月31日 However, studies exploring the direct application of raw rice husk in civil engineering contexts remain scarce A majority of these studies are confined to areas such as lightweight concrete and (PDF) Effect of Treatments on Properties of Cementfiber Bricks Since then, a lot of modifications have been done in the composition of bricks and in brick making procedures As a result, in today’s world, brick is considered as one of the most sought after mate Similarly, cement production emits about Towards sustainable bricks production: An overview دانشیاری

Cement Production an overview ScienceDirect Topics
343 Cement production Cement production is one of the largest CO 2emitting industries globally, with the US contributing 643 MMT of CO 2 in 2014 [38] In 2014, the US produced 826 MMT of cement while the world produced a total of 4180 MMT China accounts for the majority of production, claiming 596% of global cement productionMachine Selection: Select a machine that aligns with the production requirements, allowing adjustments for different mold sizes and shapes of the brick, and excels in highvolume production Tabrick offers a range of brick making machines tailored to match the texture and consistency of various brick mixturesBrick Making Machine Manufacturer Tabrick