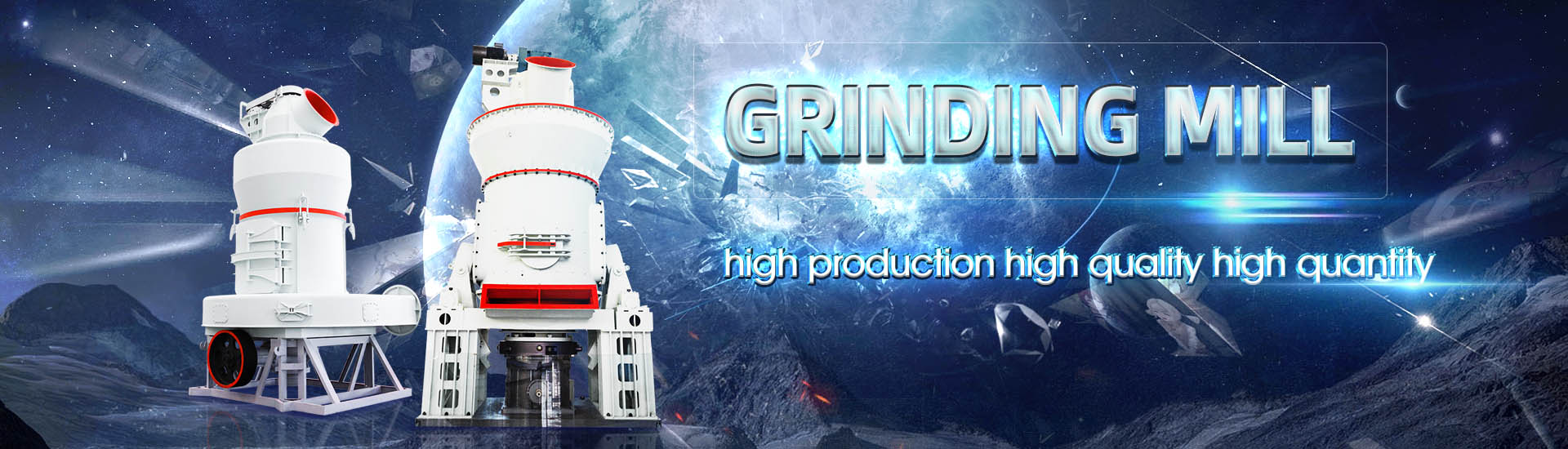
Raw and clinker mill
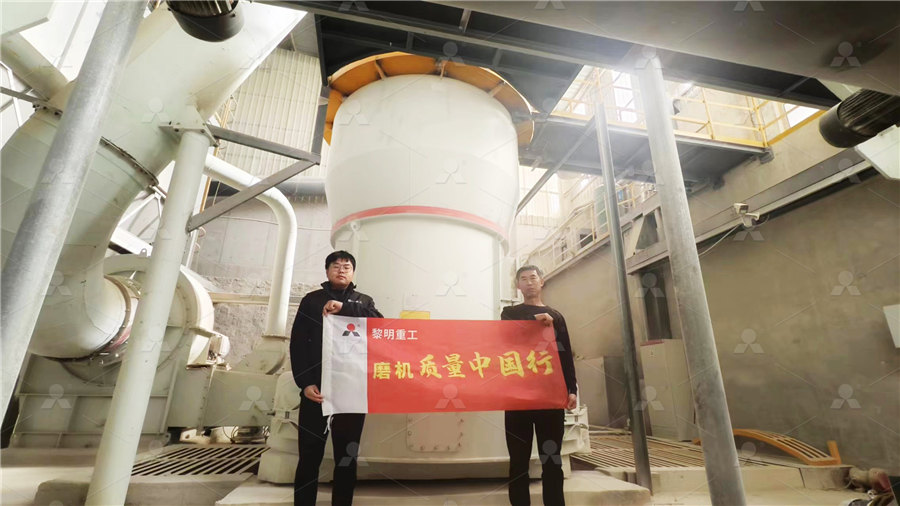
Clinker Production an overview ScienceDirect Topics
Raw materials for clinker production are for good reasons primarily based on limestone, clay or its natural mixture, marl In many cases, alternative raw materials are used mostly as corrective 2014年6月1日 Raw clinker breakage functions were established using the data reduction technique proposed by Narayanan [11] which uses tfamily curves Proposed empirical Analysis of single particle impact breakage characteristics of raw 2012年11月8日 Raw materials crushing and grinding seeks to reduce materials from roughly one meter cubes of blasted stone to a size where at least 80 percent of the raw material is less Breakthrough in Clinker Grinding Massachusetts Institute of 2023年1月7日 The typical cement manufacturing process involves the following steps: limestone quarrying, raw material preparations by crushing and milling, preheating, precalcining, kiln Emission reduction through process integration and exploration of
.jpg)
Process characteristics of clinker and cement production SINTEF
Cooling gas recirculation contributed to a phenomenon of moisture enrichment The clinker microstructure of the clinker samples indicate fast cooling the extraction of finer clinker The raw materials, now known as kiln feed, enter a raw mill that consists of a drying chamber and a grinding chamber The kiln feed is then fed into a rotary kiln, a large chemical reaction A practical guide to improving cement manufacturing processes 2020年9月29日 Portland cement clinker is manufactured by defined raw materials containing CaO, SiO 2, Al 2 O 3, Fe 2 O 3, MgO, K 2 O, Na 2 O, etc Homogenous mixtures of raw materials are developed for firing in the kiln The An overview of alternative raw materials used in 2002年5月9日 Abstract: A comprehensive understanding of the chemical and physical aspects of raw material transformation into clinker is an important foundation to increasing production, Solving raw material challenges [cement industry] IEEE Xplore
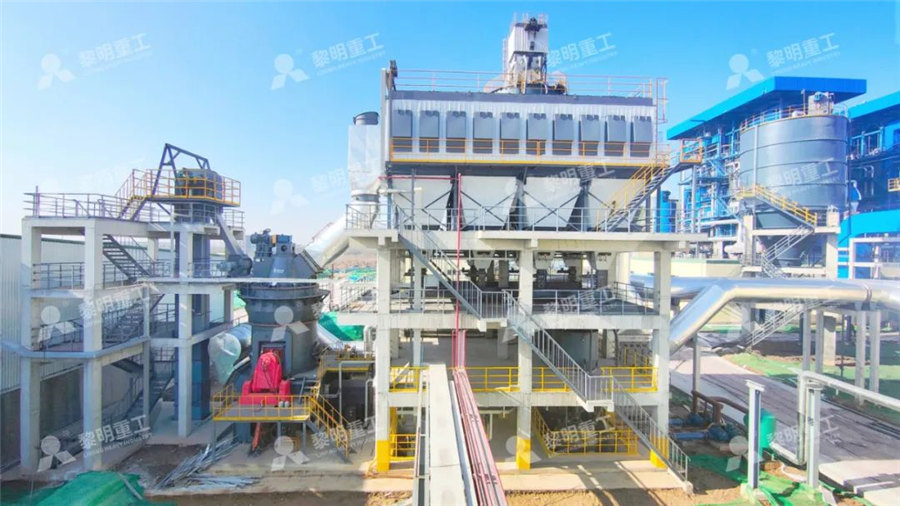
OK RAW AND CEMENT MILL
available for raw grinding, ensure the ability to meet all possible capacity requirements in a single mill even for the hardest materials The wellknown reputation of the OK mill as a reliable machine that is easy to operate and maintain continues with the OK raw mill In addition to the roller design features, the OK mill retains the abilityLearn about the raw mill in cement plants and the basic raw materials used in cement manufacturing Discover our efficient cement manufacturing process Physical and chemical analysis of clinker cement and fly ash with Bureau of Raw Mill in Cement Plant Cement Manufacturing 2022年5月15日 Mercury pollution has attracted worldwide attention due to its toxicity, bioaccumulation and persistence Cement clinker production is the top emitter of atmospheric mercury in China and the emissions from raw mill systems account for about 85% of all emissions However, the mercury emission characteristics and mechanisms as a function of Mercury emission characteristics and mechanism in the raw mill The OK™ Mill was originally designed for cement grinding In 2017 we released the OK™ vertical roller mill for raw materials grinding The OK™ Mill’s modular design comes with unique flexibility, showcasing parts commonality, where spare parts can be shared between vertical roller mills regardless of size and applicationOK™ Raw and Cement Mill
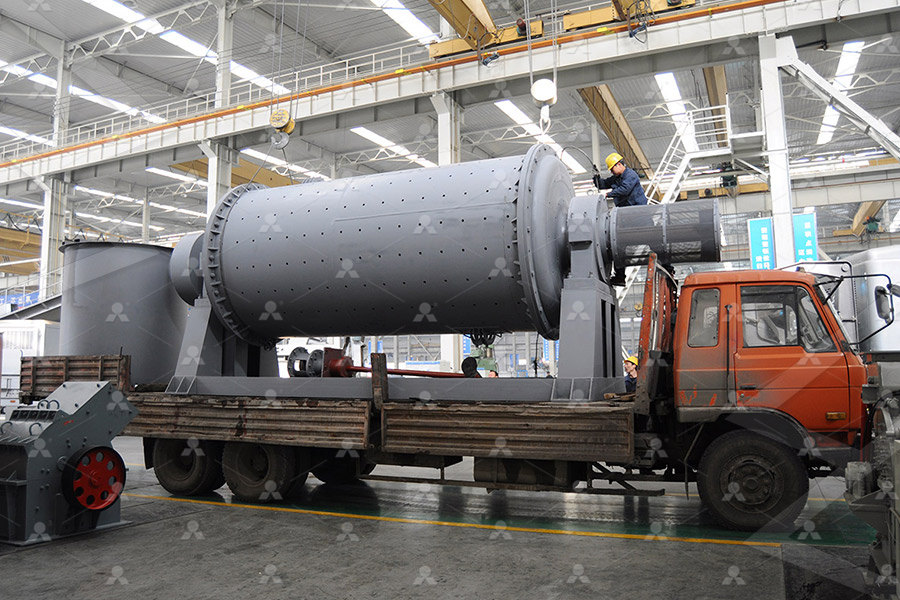
Cement Manufacturing Process INFINITY FOR CEMENT EQUIPMENT
Form Dark in color of clinker Part Three: Raw Mill Process of Raw Mill The proportioned raw material is feed first to a grinding mill In the mill, particles ground in to very fine sizes In the grinding unit, drying, grinding and mixing takes place simultaneouslyFasil A and Omprakash S [16] studies the mixing of raw materials process and composition of raw mill feed, kiln feed as well as formed clinker to reduce the variation in clinker qualityEffect of raw mill on LSF with time Download Scientific DiagramRaw Mill Optimization Module The Raw Mill Optimization option controls both the temperature, the feed rate to the mill and the separator speed in order to achieve the required throughput for kiln Where starting the mill requires dampers to be moved, to change gas flow paths, the module will also respond to these effects to keep the system stableRaw Mix Preparation ABB2020年8月25日 A full cement production process includes the cement crushing process, raw mill process, clinker process, and cement grinding process, cement packing process, and related process Find more! Skip to content +86 s about blog contact EN ES Menu Menu Home;Cement Production Process Cement Manufacturing Process
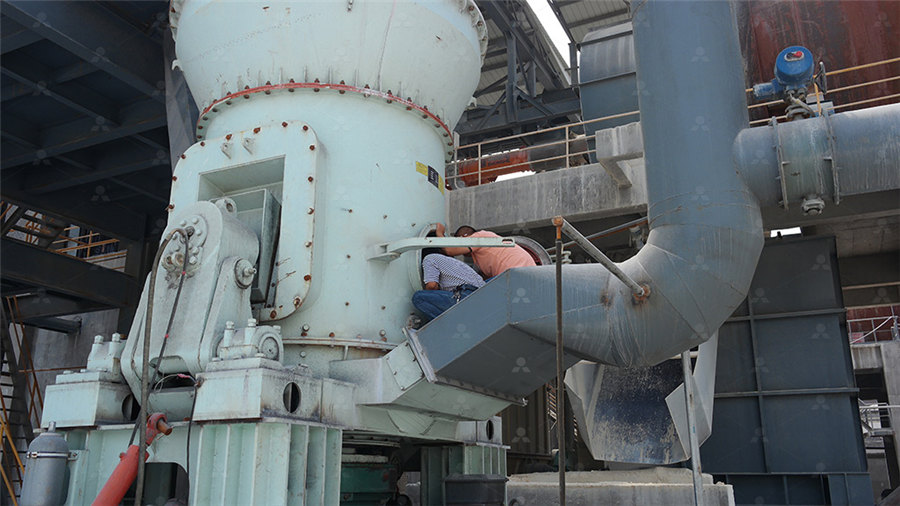
Understanding the Difference Between Raw Mill and Cement Mill
A: Cement mill is generally more energyefficient than raw mill because the clinker particles in the cement mill are already in a fine powder form, and less grinding is required The main difference between raw mill and cement mill lies in the raw materials and Raw Mill The clinker production process involves much equipment and material flow; thus, an operating system is needed to regulate and manage the production processOptimizing the clinker production by using an automation model in raw A mill of this type would be driven by a 1200 hp motor, but the mills can vary in size from 500 hp to 6000 hp with cement outlets that can vary from 10 to 140 tons per hour As with the grinding of raw materials, both the open circuit mill and An Introduction to Clinker Grinding and Cement Storage2021年4月1日 The raw meals were determined for the second clinker using different lime saturation factors from 089 to 095, while in the first clinker, lime saturation was 089(PDF) Influence of raw meal composition on clinker reactivity and
.jpg)
Vertical raw mill Cement Plant
Vertical raw mill for sale! AGICO CEMENT is a cement equipment manufacturer offers raw mill used in cement plant, it has a good development prospect in the pregrinding of slag powder and cement clinker Advantages of vertical raw 2019年6月22日 For Example: Using the Bond formula, the increase in raw mill output was predicted to be only 35% for a recent modern VSM raw mill for a reduction in feed size from 70 mm to 30 mmOptimizing Raw Mills Performance ; the Materials WAYThe LOESCHE scope of delivery includes a raw material mill with a capacity of 540 t/h of cement raw meal, a cement mill with an output of 350 t/h of clinker as well as a coal mill with an output of 45 t/h VIEW MORE Cement Raw MaterialsCement Raw Material LoescheThe Horomill used as a raw mill is claimed to combine the effectiveness of the vertical roller mill and the roller press with a very low pressure drop “Loesche mills for clinker grinding,” Asian Cement and Construction Materials Magazine, September 1998, pages 5257 Brunkick, Horst, and Schafer, Heinz U, “Grinding advances Everything you need to know about cement Materials Preparation and Raw
.jpg)
EVERYTHING YOU NEED TO KNOW ABOUT THE CHEMISTRY OF KILN FEED AND CLINKER
RAW MATERIALS The basic ingredients for portland cement consist of limestone, sea shells, marl, or chalk, that provide the calcareous components; clay, shale, slate, or sand, to provide the silica and alumina; and iron ore, mill scale, or similar material to provide the iron components2021年1月1日 Raw mix, high grade limestone, sand and iron ore are transported from their bins to raw mills for drying and further fine grinding The raw mill is either a Ball mill with two chambers or Vertical roller mill with inbuilt classifier The hot gases from the pre heater enter the mill and are used for drying material in the millsReview on vertical roller mill in cement industry its performance refractories – 9 Clinker cooling – 10 Kiln mechanical – 11 Emergency power – 12 Plant control systems 6 Cement milling process summary data – 8 Typical equipment downtime 110 1 Storage of clinker and other components – 2 Cement milling – 3 Separators (classifiers) – 4 Ball mill circuit control – 5 Cement storage – 6The Cement Plant Operations Handbook International Cement 2024年11月23日 The clinker and the required amount of gypsum are ground to a fine powder in horizontal mills similar to those used for grinding the raw materials The material may pass straight through the mill (opencircuit grinding), or coarser material may be separated from the ground product and returned to the mill for further grinding (closedcircuit grinding)Cement Extraction, Processing, Manufacturing Britannica

Preparation Of Cement Raw Material Cement Mill,
AGICO Cement supplies cement equipment for cement raw material production as you need, such as cement mill, cement crusher, onestop turnkey project, welcome to contact! Skip to content +86 2023年12月20日 In this process, the chemical bonds of the raw materials are broken down and then they are recombined into new compounds The result is called clinker, which are rounded nodules between 1mm and 25mm across The Cement Manufacturing Process Thermo Fisher This document summarizes a study that investigated the effects of raw material fineness and lime saturation factor (LSF) on clinker grindability, energy efficiency, and cement quality in a cement plant in Gabes, Tunisia Various clinker Effect of Raw Meal Fineness On Quality of Clinkerstudy, the second production line was surveyed The cement raw materials (lime, silica and iron ore) enter the circuit through two apron feeders The raw materials are crushed in a hammer crusher to D 95 of 80mm The raw materials are mixed in a certain proportion and fed into a vertical roller mill (LOESCHE mill)Modeling and simulation of vertical roller mill using population
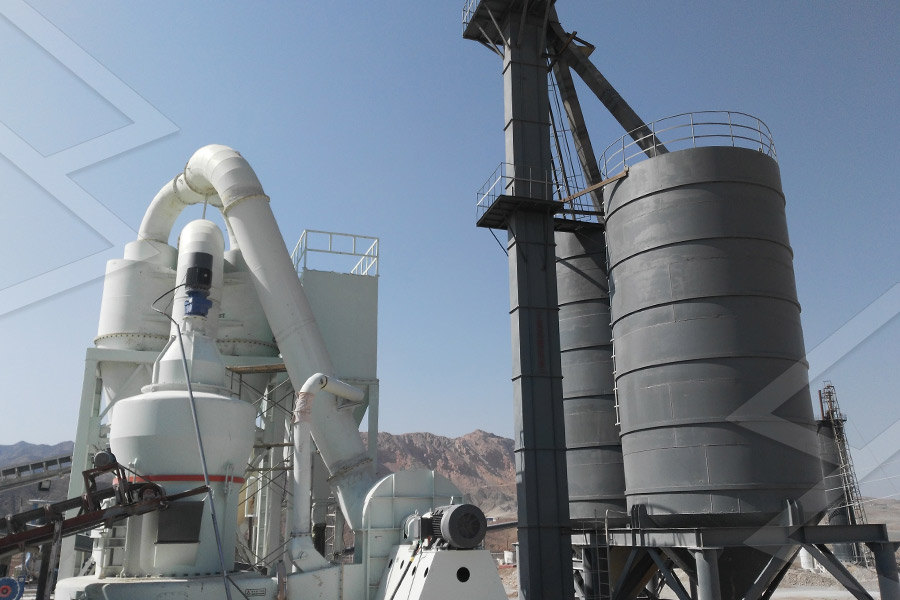
Better and cheaper cement: Optimising raw material properties
2021年6月24日 Cement performance is intially set by targeting a clinker lime saturation factor (LSF) This gives the required product strength but also provides good clinker burnability and reasonable economy of operation The LSF level is often around 95 or 96, although the optimum LSF will vary depending on the raw material properties and other factors2021年7月28日 Raw Mill Ball Mill: 2390: Coal Mill Vertical Roller Mill: 1628: Five Stage Preheater Clinkerisation: 17 05: Six+ Stage Preheater Clinkerisation: 4538: Five Stage Preheater Upto Clinkerisation: 4332: Six+ Stage Preheater Upto Clinkerisation: 2192: Cement Mill Vertical Roller Mill: 2707: Cement Mill Ball Mill Closed Circuit Indian Cement Sector CMARAW MEAL TO CLINKER RATIO Raw meal to clinker ratio is the amount of raw meal required to produce 1 kg of clinker operaion and maintenance You can lso calculate the mill, VRM, pyroprocess, kiln, cooler, and raw mix calculation with our online calculator You May Also Like: Theory By Cement Technology atRAW MEAL TO CLINKER RATIO THEORY CALCULATION2022年11月20日 Raw Mix Design for Raw Mill and Kiln Cement Operation English VersionThe first goal in preparing raw materials is a thorough understanding of the raw materRaw Mix Design for Raw Mill and Kiln Cement Operation
.jpg)
How Does a Raw Mill Work in a Cement Industry
2024年2月23日 The operation of the cement raw mill is a critical step in cement production By grinding the raw materials into a fine powder, these powders can be more easily mixed with other cement ingredients and burn more evenly during the cement clinker process Therefore, the efficient operation of the cement raw mill directly impacts the production efficiency and quality 2020年11月5日 As you all know, the process of a cement manufacturing plant can be divided into several steps, including crushing, raw milling, clinker calcining, cement milling (or cement grinding), packing and etc In the complete cement production line, the cement mill process plays a very important role The design of cement milling and cement mill process will produce a 3 Necessary Cement Milling Comparison Ball Mill, Vertical Roller Mill2021年11月17日 Raw Materials necessary for cement manufacture include materials containing Calcium, Silica, Alumina, and Iron These raw materials are mixed in certain proportions and burnt at 1400 to 1450 °C in a rotary kiln to form a clinker which is subsequently ground to powder and mixed with 2 to 8% gypsum This is called as ordinary Portland cement (OPC)Fundamentals of Cement Chemistry, Operations, and Quality Control2016年12月23日 An empirical expression has been developed, in which the content of uncombined lime of a cement raw mix, heated at 1400°C for 30 minutes, is correlated with the lime saturation factor, the silica (PDF) PROCESS CONTROL CLINKER QUALITY
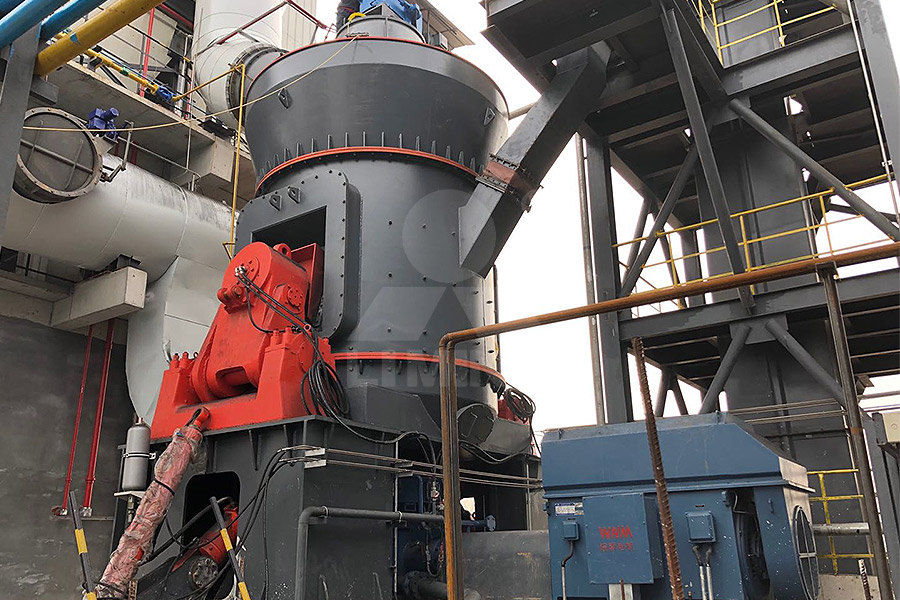
VRM Operation and Optimization PDF Mill
VRM operation and optimizationppt Free download as Powerpoint Presentation (ppt / pptx), PDF File (pdf), Text File (txt) or view presentation slides online The document discusses vertical mills used for grinding clinker, raw materials, A 10 MW cement mill, output 270 tonnes per hour A cement mill (or finish mill in North American usage [1]) is the equipment used to grind the hard, nodular clinker from the cement kiln into the fine grey powder that is cementMost cement is currently ground in ball mills and also vertical roller mills which are more effective than ball millsCement mill WikipediaThe natural variation in the composition of the raw materials is dynamically adjusted for, resulting in a more accurate prediction and control of resulting chemistry The RMCS utilizes high frequency analyses from premill crossbelt analyzers, and lower frequency postmill xray fluorescence (XRF) analyzersRaw Mix Control System PSCL2023年1月18日 The study comprised the preparation of several cement raw mixes using both the currently used and the proposed alternative cement raw materials in Yemen These alternatives were assessed to be substituted materials for the currently used sandclay that mostly excavated from the valuable cultivated lands Also, this study evaluated the effects of some Influence of Corrective and Additive Raw Materials on Clinker
.jpg)
BALL MILLS Ball mill optimisation Holzinger Consulting
the mill liner It also needs to optimise the grinding process Clinker grain sizes depend on precrusher settings but are in some cases still up to 50mm when fed to the ball mill and therefore, it is necessary to adjust the grinding tools accordingly The more that alternative fuels are used in the clinker production process, the finer and hence2016年10月5日 The moisture of the mill feed (cement raw material) can amount to 15–18 % The fineness of the mill product can be adjusted in the range between 94 and 70 % passing 170 mesh Tiggesbaumker P Trends and developments in dry raw material and clinker grinding Ciments, Betons, Platres, Chaux 1982; No 7445/83: 272284 11EnergyEfficient Technologies in Cement Grinding IntechOpen2021年1月22日 Based on the statistics of the electricity consumption of the raw material mill system of 1005 production lines in China between 2014 and 2019, it is found that the average electricity consumption A Survey and Analysis on Electricity Consumption of Raw Material Mill They were regarded as suitable for dry raw materials and soft clinker In the case of dry process rawmilling, early plants preceded the raw mill with separate driers With the arrival of the new dry process in the 1950s, it was desirable to combine the drying and grinding processesCement Kilns: Size Reduction and Grinding