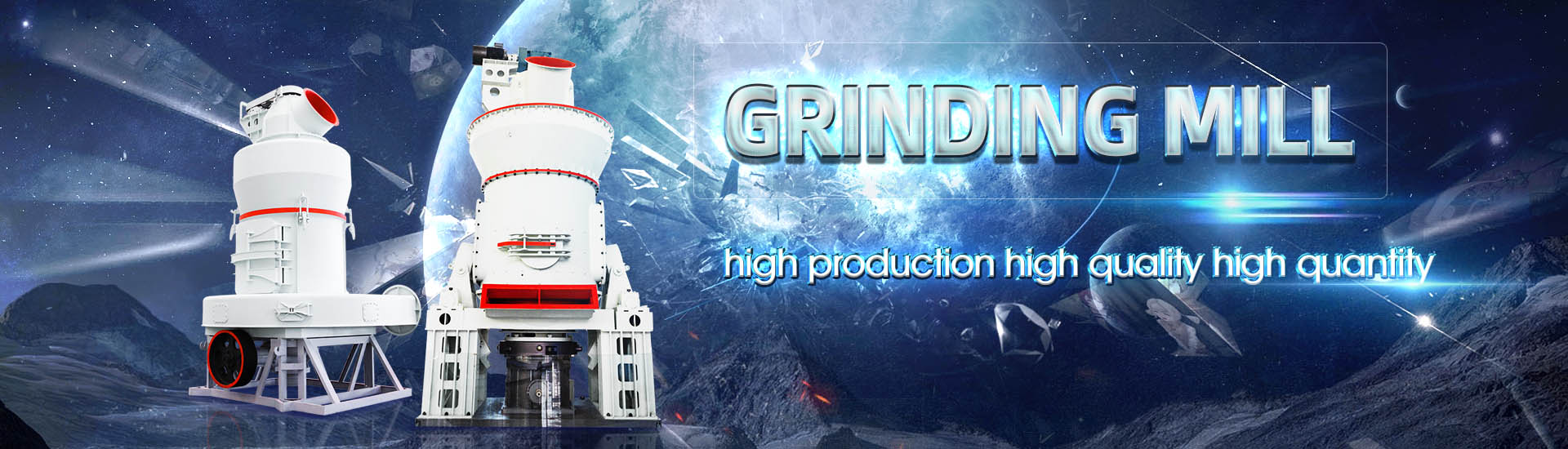
The cost of concrete ore grinding mill
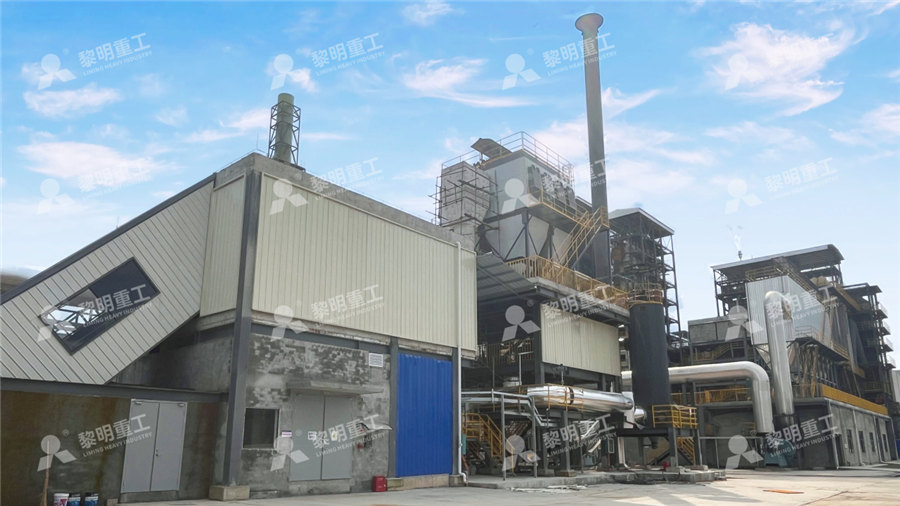
Crushing Plant Design and Layout Considerations 911 Metallurgist
crushing plant costs can be as high as $18 million It’s necessary therefore to estimate crusher installation costs based on equipment costs plus the following direct costs, including construction contractor indirects: • Earthworks • Mechanical • Concrete • Electrical • Structural steel • 2014年2月1日 Energy costs typically comprise one of the largest ongoing costs of mining operations, of which 70% is devoted to the comminution of the ore (Norgate and Jahanshahi, Mine operating costs and the potential impacts of energy and 2014年1月31日 Grinding is one of the most important operations in mineral processing plants and assumes a substantial share of the total milling costs The objective of this work was to develop a set ofA parametric cost model for mineral grinding millsSuitible for concrete crushing, scrap and demolition applications, cutting and lifting Output: 150 kg/h 200,000 kg/h The POITTEMILL pendulum roller mill is a vertical mill that works by Concrete mill, Concrete grinding mill All industrial manufacturers
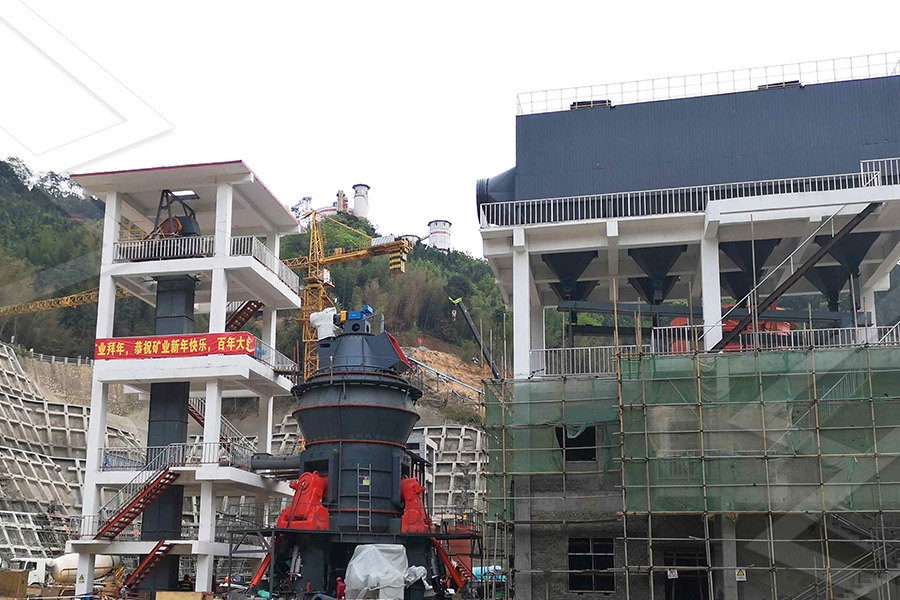
A parametric cost model for mineral grinding mills
2014年1月1日 The objective of this work was to develop a set of cost functions for major grinding mill equipment These cost models were developed using two relatively different Using this table, the capital (US$) and operating costs (US$/h) of mills with a certain power (variable P in the model) can be estimated in the preliminary stages of feasibility studies orOperating and capital costs vs power for SAG mill2022年10月4日 Optimum rock fragmentation from mining to mineral processing must meet the following conditions (Zhang 2016a): (1) minimum cost in the size reduction chain: Reduction of Fragment Size from Mining to Mineral Processing: A 2021年1月1日 With the grinding capacity of a vertical roller mill and the ability to dry, grind and sort in a single unit, the vertical roller mill offers a definite advantage over the ball mill system Review on vertical roller mill in cement industry its performance
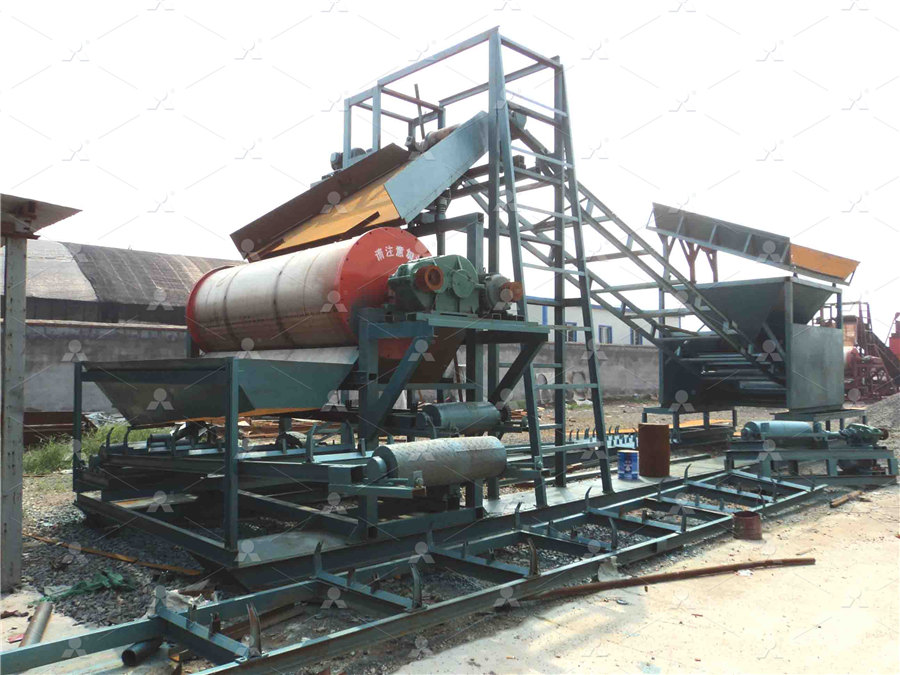
Ore Grinding SpringerLink
2023年7月20日 Ore grinding is a process to further reduce and disperse the ore particle size In the mineral processing industry, ore grinding is the particle size preparation before the The Autogenous Mill, also known as AG Mill, is a type of grinding mill used in the mining industry This machine uses ore and rock itself as grinding media to perform its job Unlike other types of mills that use steel balls or rods for Understanding the SAG Mill in Copper Ore Mining 1 Grindability: The grindability of the ore affects the efficiency of the grinding mill Harder ores require more energy and longer grinding times, which can impact the mill's performance and operational costs 2 Media andliner Wear: The condition of the grinding media and liners affects the mill's efficiencyUnderstanding the operation of grinding mills in the mining and 2015年4月9日 Grinding Mills and Their Types satyendra; April 9, 2015; 12 Comments ; autogenous grinding, ball mill, grinding mills, hammer mill, rod mill, roller mill, SAG,; Grinding Mills and Their Types In various fields of the Grinding Mills and Their Types – IspatGuru
.jpg)
Raymond Grinding Mill: The Ultimate Guide From SMAT Machinery
2023年9月18日 The Raymond mill has several advantages over other traditional Raymond mills in terms of size, cost, operation, and performance It is much more efficient than traditional Raymond mills due to its advanced structure, which provides more 2016年6月3日 The Tower mill can be installed for a fraction of the cost of an equivalent kilowatt (horsepower) ball mill The Tower mill develops very little dynamic forces Therefore, its foundation can be a concrete floor slab designed for dead load only, whereas a cylindrical ball mill requires a reinforced concrete submat with a minimum of two times the mass of the rotating Tower Mill Operating Work Index 911Metallurgist2020年2月26日 Regardless of the grinding wheel, though, all grinding processes use abrasive particles to “grind” away material from a workpiece’s surface When a workpiece is exposed to a grinding wheel, some of its material will rub off With that said, grinding is often used to both remove material from workpieces as well as polish workpiecesMilling vs Grinding: What's the Difference? OneMonroeBall mill optimisation As grinding accounts for a sizeable share in a cement plant’s power consumption, optimisation of grinding equipment such as ball mills can provide significant cost and CO 2 emission benefits to the cement producer n by Thomas Holzinger, Holzinger Consulting, SwitzerlandBALL MILLS Ball mill optimisation Holzinger Consulting
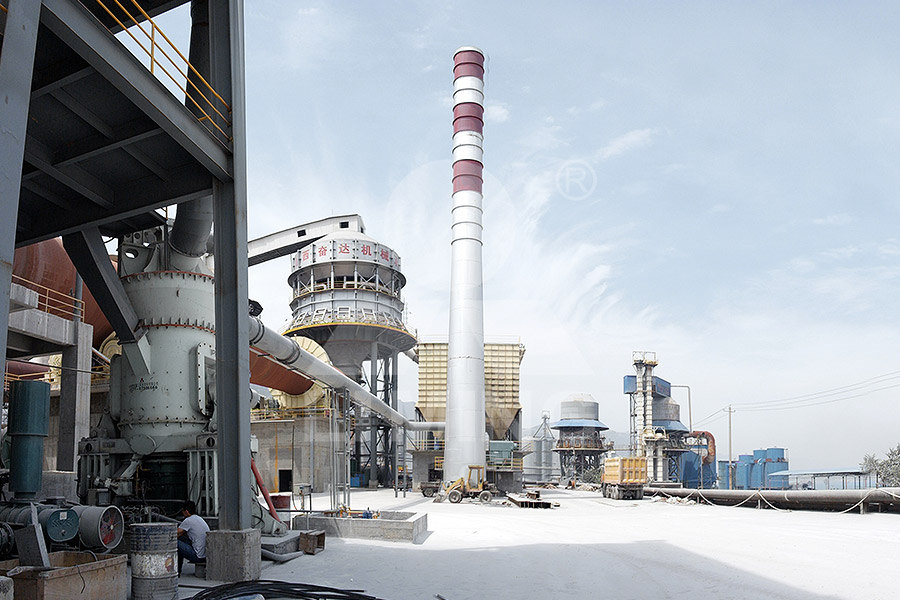
Iron Ore Processing: From Extraction to Manufacturing
2024年4月26日 These mills utilize the ore itself as the grinding media, reducing the need for additional grinding media AG/SAG mills are typically used for coarse grinding, where large pieces of ore are efficiently broken down The grinding process reduces the ore size, which enhances the efficiency of subsequent beneficiation processes by increasing the 2023年10月17日 Ultrafine powder mill (threering / fourring mediumspeed micropowder mill) feed particle size ≤25 mm, production capacity 0545 t/h, production fineness 1503500 mesh,it is a highefficiency and lowconsumption ultrafine powder processing equipment that successfully replaces the traditional jet mill and complex process ball mill grinding and powder selection, How to choose a suitable ore powder grinding mill?2020年5月21日 Diamond grinding is used to carry out concrete restorations by repairing cracks, grooves and joints in concrete Milling helps in smoothing the surface It removes upper coats of heavy floor tiles mastic, epoxy materials and other industrially used flooring Concrete roads are safer and more driver friendly after millingConcrete Milling: Why, What and How to Mill [Tips]Reducing Grinding Energy and Cost Magnetite Iron Ore Design Case Study A Jankovic and W Valery Metso Process Technology Innovation, PO Box 1028, Eagle Farm Qld, 4009, AustraliaReducing Grinding Energy and Cost Magnetite Iron Ore
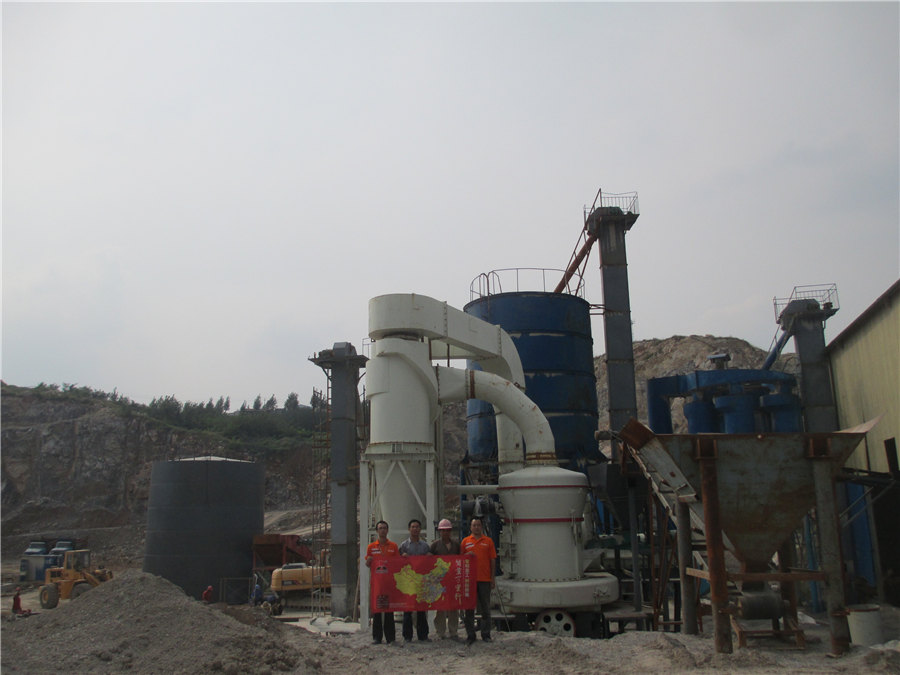
DYNAMIC DESIGN FOR GRINDING MILL
2019年1月30日 The weight of mill and charge (ore and grinding media) The concrete mill foundation is modelled using solid element with dimension of 091 x 091 and the construction cost should be Cold Milling – Efficient Removal Granulation of Road Pavements Working widths from 35 cm – 440 m Working depth 35 cm Find out more!Cold Milling Removal of Road Pavements WirtgenGrinding mediatoore ratio of 3:05kg gave 2100% fines, 7900% coarse and mill filling is 3kg:1kg of media and iron ore liberating 1500% fines and 8500% coarse KEYWORDS: Critical speed, Communition, Mill Filling, Grinding Media, Mill Speed, BeneficiationProcessing of Magnetite Iron Ores–Comparing Grinding Options2022年10月4日 21 Energy Rock drilling, blasting, and comminution (crushing and grinding) consume a vast amount of energy in hard rock mines As mentioned in Sect 1, statistics from hard rock mines indicates that drilling and blasting consumes 2% and comminution does 53% of the total energy input in the whole production chain from mining to mineral processing (Spathis Reduction of Fragment Size from Mining to Mineral Processing: A
.jpg)
Concrete Grinders, Planers and Scarifiers for Rent United Rentals
Uses: Ideal for grinding and polishing concrete or hardwoods; Add this concrete grinder and polisher to your cart now; Cat Class Code 2202322 WalkBehind Concrete Grinder, 2022 in, Propane Power Triple grinding head; 2022 in working width 2023年7月20日 Therefore, the rod mill is mostly used for coarse grinding of the previous period of ball mill, or grinding of brittle materials and materials against overcrushing, such as tungsten and tin ore before gravity separation; and (3) autogenous mill – it refers to the materials which themselves are collided and ground mutually to be crushed when the grinding mill rotates, and Ore Grinding SpringerLink2009年1月1日 Also, equipment like ball mill is used at the final stages of grinding Among the comminution and grinding equipment, HPGR is increasingly utilized as tertiary crusher or primary mill because of Processing of Magnetite Iron Ores–Comparing Grinding Options2015年10月23日 1 Introduction Cement is an energyintensive industry in which the grinding circuits use more than 60 % of the total electrical energy consumed and account for most of the manufacturing cost []The requirements for the cement industry in the future are to reduce the use of energy in grinding and the emission of CO 2 from the kilns In recent years, the production EnergyEfficient Technologies in Cement Grinding IntechOpen
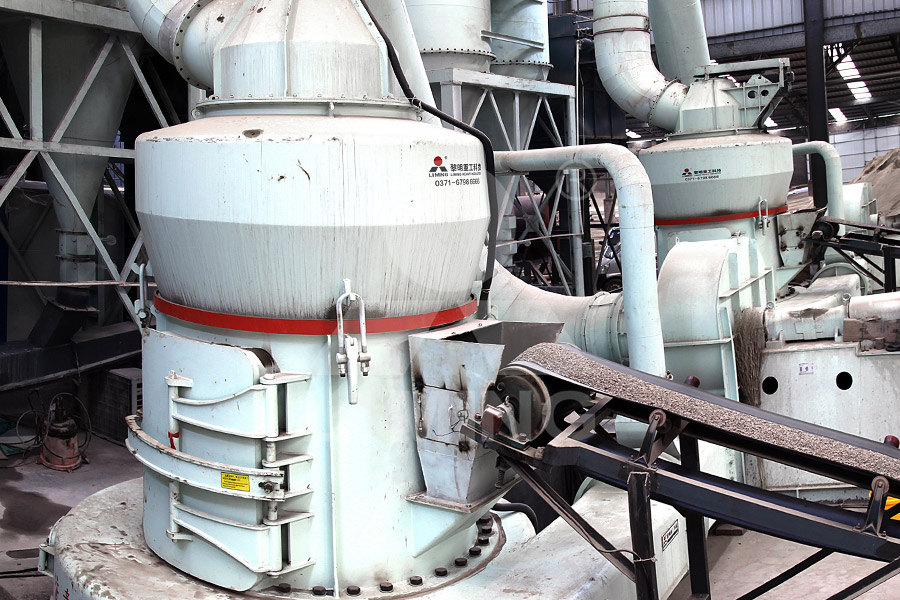
Fine Grinding as Enabling Technology – The IsaMill
Table 1: Power Intensity of Different Grinding Devices Ball Mill is a 56m D x 64m L @ 26MW Tower Mill is a 25m D x 25m L @ 520KW Table 2: Mill Comparison of Media Size, Power Intensity, number of grinding media The ability to use smaller media is probably the dominant impact on grinding efficiency It2023年10月27日 The ball mill is a rotating cylindrical vessel with grinding media inside, which is responsible for breaking the ore particles Grinding media play an important role in the comminution of mineral ores in these mills This work reviews the application of balls in mineral processing as a function of the materials used to manufacture them and the mass loss, as A Review of the Grinding Media in Ball Mills for Mineral 2023年5月12日 In position a (Fig 1a) the length l 1 of the lower part of the chamber 1 is minimal, the grinding bodies 2 in it are located at the maximum level h 1Center of masses (CM 1) of grinding bodies (GB) in chamber 1 is located at the minimum distance a 1 from the filling bottom and at the distance b 1 from the crushing cylinder body The length l 2 of the lower part of the Power Calculation of BallTube Mill Drives in the Construction 2020年6月3日 Effect of OEM mergers on grinding mill design A wave of grinding mill OEM mergers took place in the 70’s and 80’s During those years, only a handful of OEM’s were competing with one another, and no more than How grinding mill design changed over the last 30 years
.jpg)
Overview of cement grinding: fundamentals, additives, technologies
2017年5月19日 Cement industry is characterized by sizeable energy demand which accounts for about 110kWh (375 thm) per ton of cement in modern plants Industry impacts heavily also on CO2 emissions2016年1月11日 Spending a little extra on drilling and blasting to increase fragmentation will same you multiples ore loading and hauling, then finally crushing The Experts: SandVik Mining + Metso and Quarry Academy = all agree The approximate running costs for crushing plants of different capacities up to 4,000 tons per day on the basis of an eighthour crushing day are Crusher Operating Costs: How to Optimize and ReduceClay body being extruded from a deairing pug A pugmill, pug mill, or commonly just pug, is a machine in which clay or other materials are extruded in a plastic state or a similar machine for the trituration of ore [1] Industrial applications are found in pottery, bricks, cement and some parts of the concrete and asphalt mixing processes A pugmill may be a fast continuous mixerPugmill Wikipedia2021年1月8日 peak performance and balancing the power available in the SAG mill and ball mill, the transfer size must be measured and controlled • The transfer size will be 500 microns using a 12mm opening trommel This can be true under special conditions of operation when treating fine ore at high mill density, but in general the transfer size forA CRITICAL REVIEW OF GRINDING DESIGN PROCEDURES FOR THE
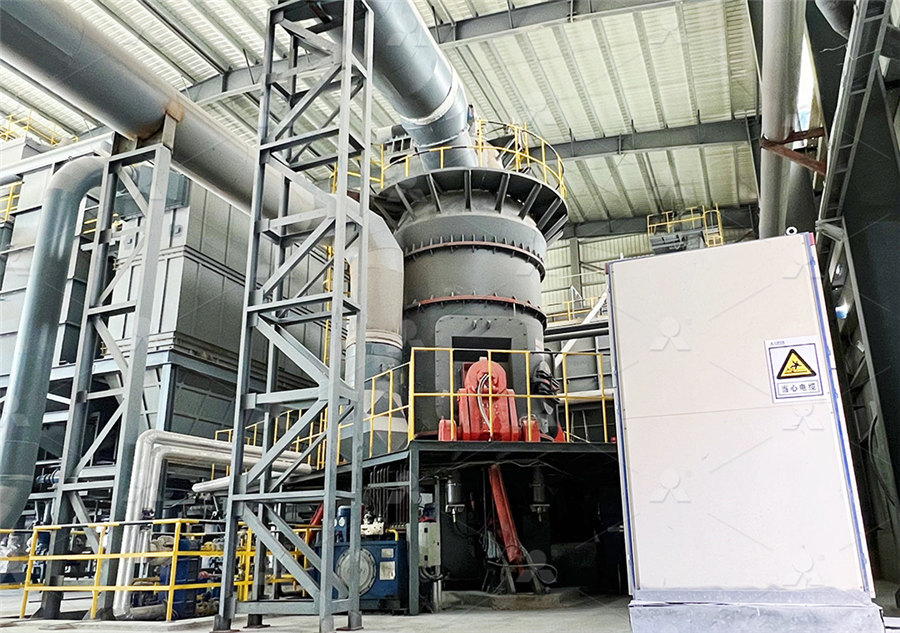
NCLUDES Concrete Pavement Surface Restoration: Diamond Grinding
For more information on diamond grinding or carbide milling, contact your local concrete paving representative (187PAVEMENT), the American Concrete Pavement Association, or the International Grooving and Grinding Association References 1 The Concrete Pavement Restoration Guide, TB020P, American Concrete Pavement Association, Skokie, IL 200 tph 3 stage skid mounted aggregate crushing plant AGGREGATE Crushing Process Planning; Stone Crushing crusher and grinding mill have the high cost mobilecrushing silver phosphate crushing process; Cost Estimate For Aggregate Crushing Grindingvent air requirement when grinding slag separately is around 15 per cent less than when grinding clinker or clinker and slag together, because the mill has to be set up for the lowest common denominator (which is clinker when it comes to early strength) Separate grinding typically requires two mills, or if one bigger vertical mill isSEPARATE OR INTERGRINDING? Loesche2024年5月17日 A SAG (SemiAutogenous Grinding) mill is a giant rotating cylinder filled with grinding media and the ore being reduced As the mill rotates, the grinding media lifts and the impact crushes the feed material SAG mill control refers to the practice of managing the mill load, which is the amount of material inside the mill at any given timeA guide to SAG Mill management
.jpg)
(PDF) The Effects of Blasting on Crushing and Grinding
2003年1月1日 Modeling indicates that the ranges of cost increases are within the range of 24 hours variations in mill throughput Clearly, there are many other factors that impact mill throughput Read moreSpeed also plays a role in ore grinding; too high of a speed can cause damage to the mill gears and other components, while too low of a speed can cause excessive wear on these same components It is important to find a balance between these two variables in order to achieve optimal grinding performanceFactors affecting ores grinding performance in ball mills2019年12月15日 429 VertiMills Vertical mills were first designed in the 1950s for applications in fine and ultrafine grinding in Japan Lately, the vertical mill is making progress toward primary grind application and shown promise in energy reduction relative to ball mills, typical to what is normally seen in regrinding applications (Mazzinghy et al 2014)Beneficiation of Gold and Silver Ores SpringerLink2021年1月14日 was surprising that the Bond Rod Mill Wi average was 113 kWh/t Since the ore is unusually soft, the Rod Mill Wi is probably irrelevant in determining required power for the SAG mill Drop Weight Tests Drop Weight tests were done at Hazen and analyzed by Contract Support Services, Inc Table 4: Summary of 6 JKTech Drop Weight TestsComparison of Ore Hardness Measurements for Grinding Mill
.jpg)
Mill Grinding Machines in Nigeria for sale Price on Jijing
Jijing More than 30 Mill Grinding Machines for sale Price starting from ₦ 130,000 in Nigeria choose and buy today! Concrete Batch Plants • 19 ads Concrete Block Machines • 179 ads Containers • 168 ads Dehydrators • 70 2022年5月23日 Grinding experiments were conducted in a laboratoryscale stirred mill on a lowgrade PGE bearing chromite ore HighPressure Grinding Rolls (HPGR) product of −1 mm was used as feed material to Modeling and application of stirred mill for the coarse grinding 2016年3月19日 These are namely a simple crushing, grinding, concentrating, and flotation circuit without frill or fancy theories, but with a constant supply of ore through the mill at a nominal profit per ton, operating continually 24 hours per dayOperating Costs of Gold Processing Plant 911Metallurgist2022年8月10日 ICR gets Vimal Jain, Director – Technical, HeidelbergCement India, to share his views about the innovations in technology of the grinding process and grinding aids as well as his understanding on how the entire process can be made more energyefficient and costeffective Explain the grinding process in cement manufacturingThe grinding process is needed to Efficient grinding unit selection impacts profitability
.jpg)
Ore Grinding Mill
Rod Mill The rod mill is loaded with steel bars as grinding media and comprises five parts: cylinder shell, feeding system, discharge system, main bearing, and transmission system It is suitable for both dry and wet grinding to meet customer needs Materials with a Moh's Hardness of 5512 can all be handled by our mill