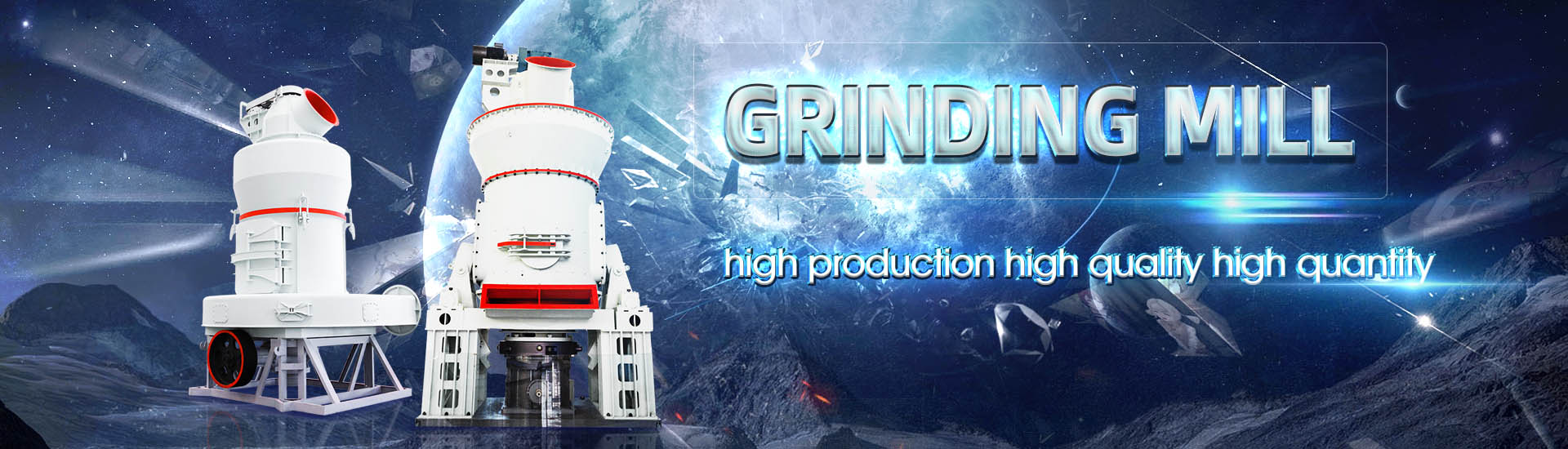
Electrolytic aluminum waste slag grinding machine transmission principle
.jpg)
Efficient lithium recovery from electrolytic aluminum slag via an
2024年2月1日 The electrolytic aluminum industry generates a large amount lithium (Li)containing electrolytic aluminum slag (EAS) annually, and this can result in severe 2020年8月1日 Here, we discuss the influence of different processing parameters on electrolytic refining of aluminum alloy and investigate the mechanism of extracting Al from coarse AlSi Recovery of aluminum from waste aluminum alloy by low 2022年4月13日 Here we propose a solidstate electrolysis (SSE) process using molten salts for upcycling aluminium scrap The SSE produces aluminium with a purity comparable to that of A solidstate electrolysis process for upcycling aluminium scrap2023年10月1日 In this paper, a “sulfated roasting–calcine water leaching–aluminum precipitation–lithium precipitation” process is proposed for the disposal of waste aluminum Efficient extraction and recovery of lithium from waste aluminum
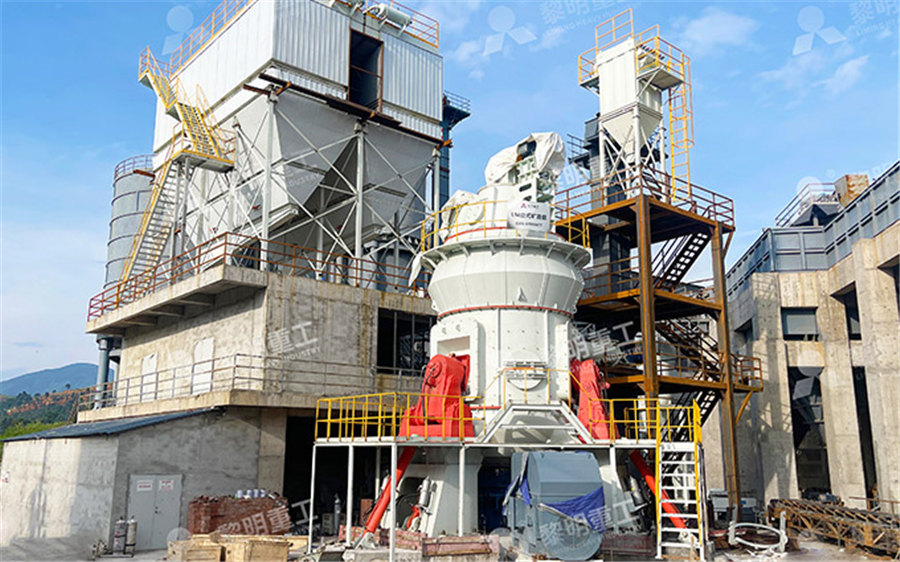
Research Progress of Electrolytic Aluminum Overhaul Slag Disposal
2023年4月25日 This article analyzes and summarizes the composition and hazards of the overhaul slag and the current development status of domestic and international electrolytic 2016年10月24日 In this paper, the development of aluminum electrolysis control systems is reviewed, followed by a discussion of the progress made since 2000, which mainly consists of Progress in Aluminum Electrolysis Control and Future Direction for 2022年10月10日 In this work, electrolytic aluminum carbon anode slag was separated by flotation Using the selectivity index ( SI ) as an indicator, the influencing factors of the carbon Recovery of carbon and cryolite from spent carbon anode slag of 2024年7月24日 The lithium was selectively recovered and enriched from spent aluminum electrolyte slag by using calcium salt roasting transformation followed by HBL121solvent Cleaner Process for the Selective Extraction of Lithium from Spent
.jpg)
Recycling and Utilization of the Electrolytic Aluminium Ash and Slag
Aluminum ash is a kind of industrial solid waste Original aluminum ash (OAA) can be prepared into original aluminum ash spray powder (OAASP) through hydrolysis treatment, and the 2024年1月1日 A novel approach for lithium recovery from waste lithiumcontaining aluminum electrolyte by a roastingleaching process Anode carbon residue is produced in the production Efficient lithium recovery from electrolytic aluminum slag via an 2021年5月5日 Grinding Machine Working Principle: In brief, we can say the working of the Grinding Machine is the Workpiece is fed against the rotating abrasive wheel The action of rubbing or friction generates between wok price Grinding Machine: Definition, Parts, Working 2024年2月2日 Calcium carbide slag is a difficult industrial waste to treat Millions of tons of calcium carbide slag are piled up in China yearly, occupying a large amount of land and easily causing secondary pollution []The main component of calcium carbide slag is Ca(OH) 2, with 71–95% content []Therefore, the current recycling methods of calcium carbide slag mainly Research on Using Carbide Slag to Mineralize the Carbon Dioxide
.jpg)
Electrochemical Grinding: Definition, Parts or
2021年8月27日 The grinding wheel is the most important and unique part of the electrochemical grinding machine It is connected to the negative terminal of the power supply and acts as the cathode The grinding wheel is made of 2020年4月7日 ZG35Cr25Ni20 electrolytic aluminum slag grab, with its excellent high temperature resistance and corrosion resistance, is unique in the electrolytic aluminum industry The grapple is made of highquality 310S heatresistant steel castings, which maintain excellent stability in hightemperature environments, ensuring that the grapple can operate stably in Electrolytic Aluminum Slag Grab Sino Machine2023年3月12日 The aluminum electrolysis industry continually and unavoidably produces hazardous solid waste in the form of carbon anode slag Carbon anode slag poses a serious environmental pollution risk, and (PDF) Recovery of Carbon and Cryolite from Spent Carbon Anode Slag waste generated in the aluminum electrolysis process Li et al [33] explored a plan for recovering the waste lining of electrolytic cells by optimizing flotation conditions, includThe Study of Carbon Recovery from Electrolysis Aluminum
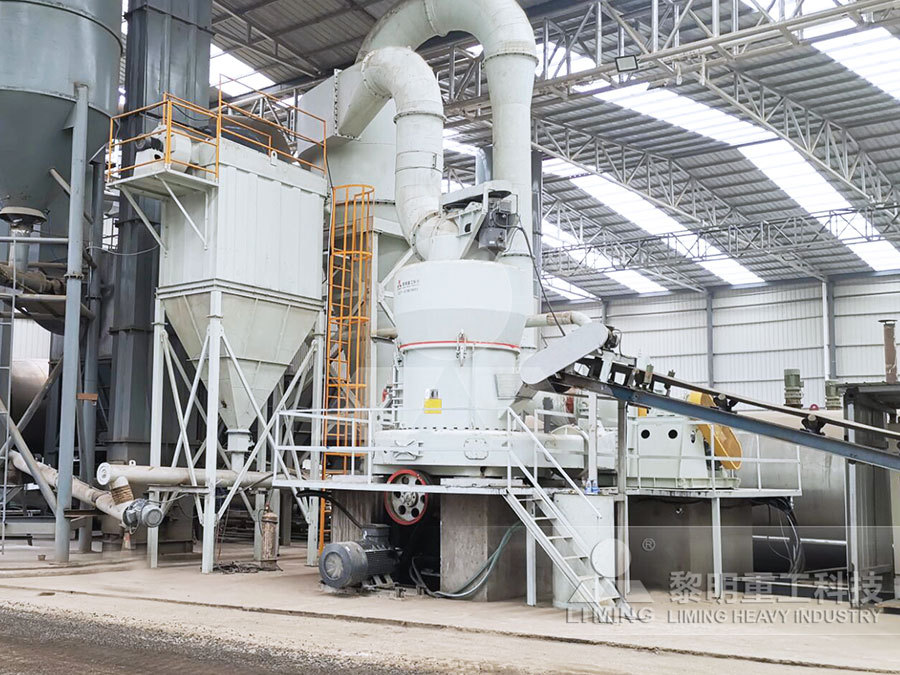
Thermodynamic analysis of waste heat recovery of aluminum
Thermodynamic analysis of waste heat recovery of aluminum dross in electrolytic aluminum industry, Energy Sources, Part A: Recovery, Utilization, and Environmental Effects, DOI: 101080/ The aluminum dross skimming from the smelting furnace is called primary aluminum dross, which is graywhite in appearance, mainly composed of a mixture of metallic aluminum and aluminum oxide, and the aluminum content can reach 15%~ 70%, also known as “white aluminum dross”; secondary aluminum dross is the waste after the primary aluminum dross is extracted from Aluminium dross processing/Brightstar Aluminum Machinery2021年1月12日 At present, the treatment methods of carbon anode slag from electrolytic aluminum mainly include flotation [8, 9], vacuum smelting [10], physical activation, roasting, alkali fusion, bubbling (PDF) The Study of Carbon Recovery from Electrolysis Aluminum Carbon 2024年2月1日 The electrolytic aluminum industry generates a large amount lithium (Li)containing electrolytic aluminum slag (EAS) annually, and this can result in severe environmental pollution and wasting of Li resources This paper proposes a method for recovering Li from the slag using AlCl 3 as the leaching agent The effects of the leaching temperature, AlCl 3 Efficient lithium recovery from electrolytic aluminum slag via an
.jpg)
Aluminum dross: aluminum metal recovery and emerging
2024年4月17日 Recycling plays an important role in today's world due to its considerable contributions to mitigating energy concerns and environmental challenges One of them is dross recycling from aluminum (Al) cast houses Unlike other recyclable materials, dross has an abundance of components, including rare earth elements, heavy metals, ferrous, and recycled What Is Grinding Slag Removal? Slag is a specific type of sand that’s traditionally made from steel It often forms as a coarse waste product resulting from deburring or smelting processes To remove slag, metal processing facilities require grinding and slag removal Slag grinding processes efficiently remove all of the heavy slag produced Grinding Slag Removal Apex Machine Group2021年11月22日 The secondary aluminum ash of electrolytic aluminum is a hazardous waste containing a large amount of toxic and hazardous substances such as fluoride, cyanide, aluminum carbide dies, and aluminum nitride, and The Utilization Technology Analysis Of Secondary 2024年2月21日 2 Grinding The crushed small pieces are sent to the cryolite mill and ground into powder 3 Stir The powdery electrolytic slag is fed into the mixer and stirred evenly 4 Flotation The uniformly stirred electrolytic slag is sent to the flotation machine and undergoes three steps: rough selection, primary selection, and secondary selection 5Aluminum slag recycled cryolite powder production line
.jpg)
The recycling of carbonrich solid wastes from aluminum electrolytic
2024年5月23日 The aluminum electrolysis industry continually and unavoidably produces hazardous solid waste in the form of carbon anode slag Carbon anode slag poses a serious environmental pollution risk, and 2023年8月12日 Disadvantages of Electrochemical Grinding Electrochemical Grinding comes with some drawbacks or disadvantages These include: Low Metal Removal Rate: The rate at which material is removed during the process is relatively slow, typically around 15mm/s, which can impact productivity for highvolume production requirements; High Power Consumption: Electrochemical Grinding: Learn Components, Working Principle 2019年7月8日 The electrolytic aluminum waste, which would inevitably be produced from the electrolytic process in the aluminum industry, is harmful to environment and human bodyThermodynamic analysis of waste heat recovery of aluminum 2022年10月10日 The comprehensive recovery and utilization of electrolytic aluminum spent carbon anode slag (Hereinafter simplified as “carbon anode slag”) are therefore necessary Flotation is a physical separation method used to separate particles by using the difference in surface property of particles ( Chen et al, 2022 ; Ni et al, 2022 )Recovery of carbon and cryolite from spent carbon anode slag of
.jpg)
Enhanced flotation separation of aluminum electrolysis anode slag
2024年3月1日 One of the main electrolytic aluminum production costs is the consumption of carbon anodes, and carbon anode slag is a common hazardous waste in the aluminum industry2021年1月12日 A large amount of carbon dust is generated in the process of aluminum smelting by molten salt electrolysis The carbon dust is solid hazardous waste but contains a large quantity of recyclable components such as carbon and fluoride How to recycle carbon dust more effectively is a challenge in the aluminum electrolysis field In this study, Xray diffraction, The Study of Carbon Recovery from Electrolysis Aluminum for electrolytic aluminum waste is proposed This mode is to pulverize the electrolytic aluminum waste, and then mix the crushed electrolytic aluminum waste with the raw coal of the circulating fluidized bed boiler [6], then send it to the circulating fluidized bed boiler for combustion In this study, a mixed combustion experiment ofResearch on the Coprocessing of Mixed Electrolytic Aluminum Waste 2023年4月13日 This paper proposes a technical viewpoint for the recovery of waste heat in aluminum electrolysis The idea of combining heatgenerating electrolysis process and the heatconsuming alumina tube A comprehensive review of aluminium electrolysis and the waste
.jpg)
Efficient extraction and recovery of lithium from waste aluminum
2023年10月1日 Cryolitealumina (Na 3 AlF 6Al 2 O 3) molten salt electrolysis is the only modern method for the industrial production of metallic aluminum (Ishak et al, 2017)Under the influence of direct current, Al 2 O 3 dissolved in the molten salt is reduced to monolithic aluminum at the cathode (Haraldsson and Johansson, 2020)As the blood of the electrolytic cell, the electrolyte 2022年9月1日 To better solve the waste pollution problem generated by the electrolytic manganese industry, electrolytic manganese slag as the main raw material, chromium iron slag, and pure chemical reagents (PDF) A study of the solidification and stability mechanisms of 2016年10月24日 The industrial aluminum reduction cell is an electrochemistry reactor that operates under high temperatures and highly corrosive conditions However, these conditions have restricted the measurement of key control parameters, making the control of aluminum reduction cells a difficult problem in the industry Because aluminum electrolysis control Progress in Aluminum Electrolysis Control and Future Direction Aluminum ash is the slag produced in the production process of electrolytic aluminum or cast aluminum, which is a hazardous solid waste Aluminum ash contains aluminum element, aluminum oxide, aluminum carbide, silicon, fluoride, chloride and other components Among them, alumina accounts for more than 70%, which has a high recycling valueAluminum Ash Processing Aluminum Ash Recovery Aluminum
.jpg)
Preparation of Recycled Ceramic Tiles by Using Electrolytic
WANG Gongxun;LI Zhi;ZHU Mingqiao Preparation of Recycled Ceramic Tiles by Using Electrolytic Manganese SlagWaste Ceramic Grinding Fine Powder[J] BULLETIN OF THE CHINESE CERAMIC SOCIETY, 2013, 32(8): 149615012014年2月19日 Slags are byproducts of the metallurgical industry It is of importance to recycle materials and recover heat from metallurgical slags to reduce the energy consumption and environmental impact of steel industry China is the largest iron and steelmaking slag producer in the world, and intensive efforts have been made during last decades for slag valorisation, Current Development of Slag Valorisation in China Waste2023年10月1日 The electrolytic aluminum waste, which would inevitably be produced from the electrolytic process in the aluminum industry, is harmful to environment and human bodyHarmless recovery and utilization of electrolytic aluminum spent 2012年6月1日 As the cylinder starts to rotate, the grinding balls inside the cylinder crush and grind the feed material, generating mechanical energy that aids in breaking bonds, activating the catalyst, and Grinding in Ball Mills: Modeling and Process Control
.jpg)
Harmless recovery and utilization of electrolytic aluminum spent
2023年12月1日 However, the amount of solid waste generated in electrolysis process continues to accumulate due to the confinements of the process With the growth of solid waste emissions, environmental and ecological issues have ended up one of the major bottlenecks limiting the sustainable development of aluminum enterprises (Liao et al, 2018; Ishak et al, 2017)On August 2nd, China Nonferrous Metals Industry Association organized an expert meeting on scientific and technological achievements in Kunming, Yunnan Province, and completed the "electrolytic aluminum overhaul slag" jointly Electrolytic aluminum overhaul slag harmless 2013年1月1日 PDF Principles of Modern Grinding Technology explains the principles that led to rapid improvements in modern grinding technology over recent decades Find, read and cite all the research Principles of Modern Grinding Technology2021年10月31日 Introduction Hall–Heroult method is currently used to produce aluminum Highpurity primary aluminum is produced by electrolysis with aluminum electrolysis cell as the carrier, cryolite (Na 3 AlF 6) as the reaction solvent, and alumina (Al 2 O 3) as the raw materialAs a core component, prebaked anode drives the electric current into the electrolytic cell and participates Advances in the Safe Disposal and Comprehensive Utilization of
.jpg)
An electrolytic grinding machine IOPscience
2020年4月7日 structed a special electrolytic grinding machine for the second stage It has definite advantages over conventional techniques: thinning is more uniform and absolutely deforma tionfree Fiere 1 (h) schematic drawing of the grinding machine (a) General view of the grinding machine;2022年2月19日 Recycling waste containing rare earth has always been a research hotspot The molten salt electrolysis process of rareearth metals and alloys generates a large amount of waste slag, which contains high rareearth content and, thus, has very considerable recovery value However, the high content of fluorine in rareearth molten salt slag brings challenges to the Recovery of RareEarth Elements from Molten Salt Electrolytic Slag 2022年10月1日 Request PDF Cocombustion characteristics of electrolytic aluminum waste and coal The electrolytic aluminum waste, which would inevitably be produced from the electrolytic process in the Cocombustion characteristics of electrolytic aluminum waste 2024年6月6日 These protruding abrasive particles also remove the unactive layers formed on the work by abrasion to make the surface more receptive It can be seen that the process is similar to conventional grindingIn that, an abrasive grinding wheel is used and the work is fed against the rotating wheel 10% of the work metal is removed by abrasive cutting, and 90% by Electrochemical Grinding: Parts, Working, Application, Advantages
.jpg)
Aluminium salt slag characterization and utilization – A review
2012年5月30日 Aluminium salt slag is toxic/hazardous waste (production: 200–500 kg/Al tonne) Chemical and mineralogical characteristics are presented Various processes for Al metal recovery and recycling of KCl/NaCl to smelting process are reported Preparation of value added products from the final NMR is discussed2021年8月5日 EMR is waste residue generated during the production of electrolytic manganese after leaching with concentrated sulfuric acid, neutralization with ammonia, and filtration by plate filter pressing (Wang et al, 2019, Zhang et al, 2020)Due to historical and technical reasons, the existing open storage EMR in China is as high as 80 million tons; thus (Tian et al, 2019, Ayala Selective recovery of manganese from electrolytic manganese residue