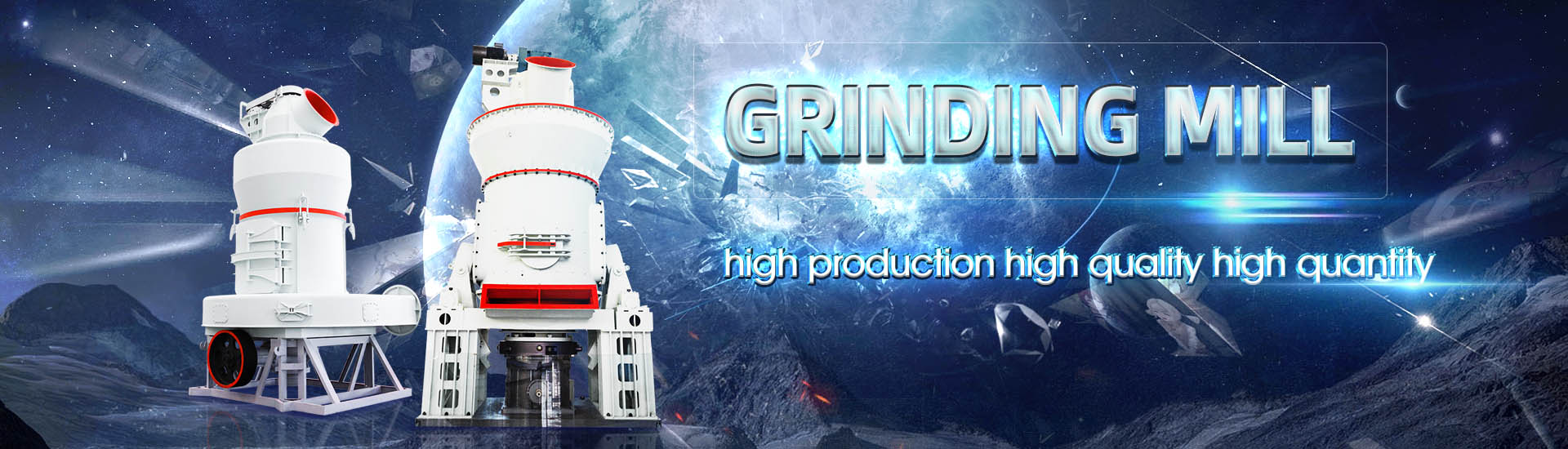
Highefficiency grinding mill for thermal power plant
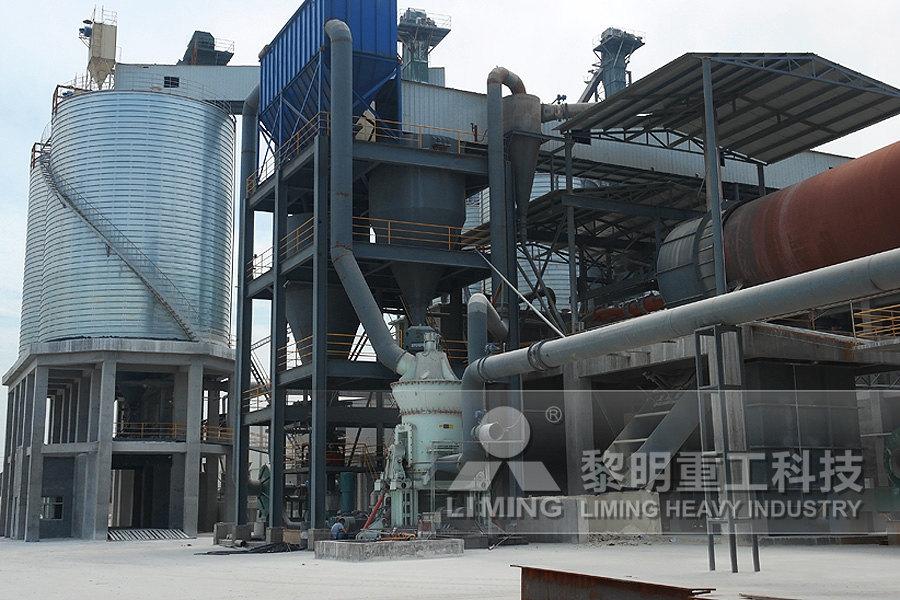
IMPROVING THERMAL AND ELECTRIC ENERGY EFFICIENCY AT
Improving Thermal and Electric Energy Efficiency at Cement Plants: International Best Practice v This report was produced in cooperation between IFC, SNIC (Sindicato Nacional da Indústria do Cimento), ABCP (Associação Brasileira de Cimento Portland), and INT (Brazil’s National The Metso HIGmill™ is an advanced, energyefficient fine and ultrafine grinding solution that utilizes proven technology With the tall, narrow, vertical body arrangement, grinding media is evenly distributed and mineral particles remain HIGmill high intensity grinding mill MetsoThis paper will focus on the ball mill grinding process, its tools and optimisation possibilities (see Figure 1) The ball mill comminution process has a high electrical energy consumption, BALL MILLS Ball mill optimisation Holzinger Consulting2022年5月1日 Scientists have proposed a scheme to increase the efficiency of a thermal plant by studying the impact of temperature and flow rate of cooling water on the performance of Improvement in efficiency of thermal power plant using
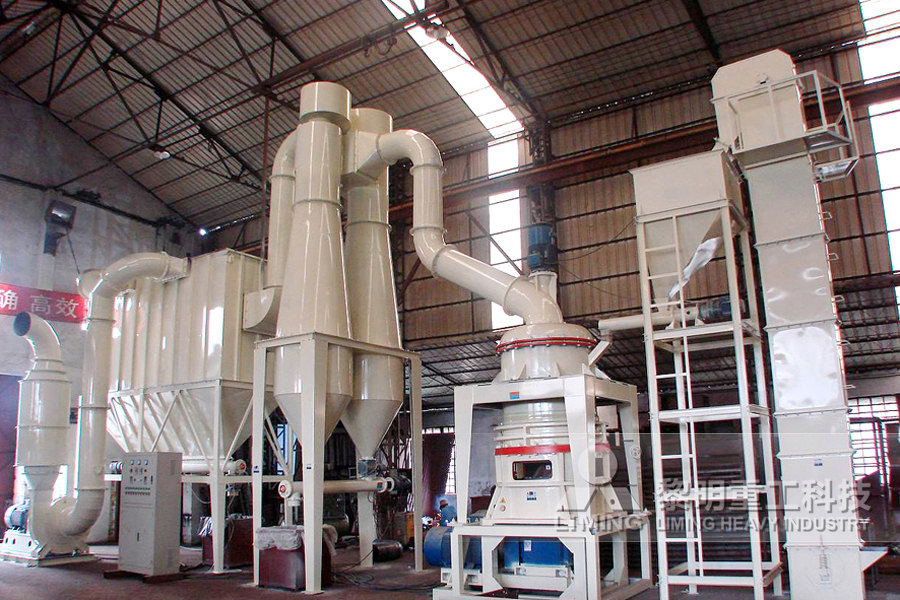
Practical assessment of grinding capacity and power
2019年1月1日 This paper analyzes the effects of coal grindability and its characteristics on the grinding capacity and power consumption for beater wheel mill during exploitation in thermal power2022年2月24日 The study reveals that the lowest specific energy consumption is achieved when the relative rotational speed of the mill is between 081 and 087; the weighted average Improving the efficiency of the coal grinding process in ball drum 2022年2月24日 The proposed methodology allows adjustment of the operating parameters of the grinding process to achieve the lowest energy consumption The power consumption for Improving the Efficiency of the Coal Grinding Process in Ball Drum 2022年1月1日 A pilotscale study of highefficiency and energysaving grinding technology using a special stirred mill with the ceramic medium was proposed in this studyHighefficiency and energyconservation grinding technology
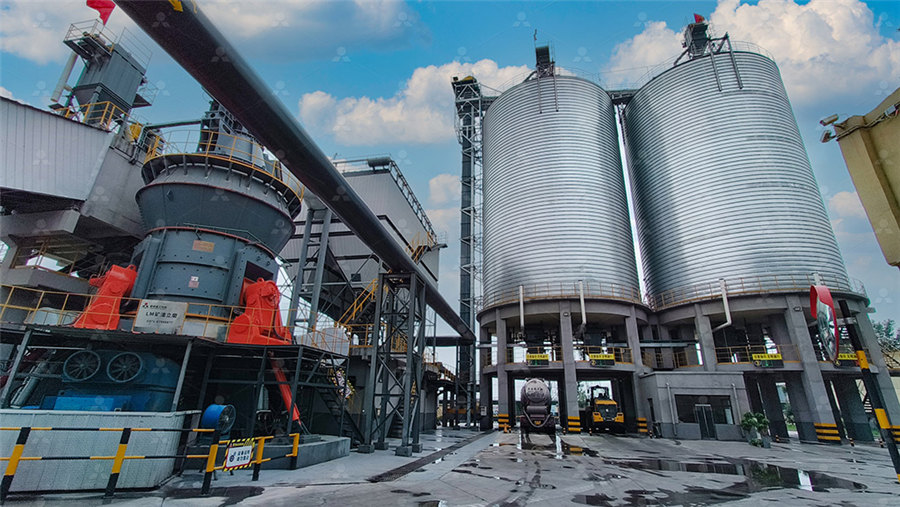
Improving the efficiency of the coal grinding process in ball drum
2022年2月24日 The study reveals that the lowest specific energy consumption is achieved when the relative rotational speed of the mill is between 081 and 087; the weighted average 2023年7月10日 The review concludes that stirred mills have significant potential for achieving the energyefficient ultrafine grinding of particles Stirred mills have unique designs and operations, which provide higher grinding efficiency, lower EnergyEfficient Advanced Ultrafine Grinding of Indian coals used for power generation are lowgrade high ash coals having a GCV of about 2600 kcal/kg with ash content as high as 45 to 50% with Pyrites of about 12% and alpha quartz to an extent of about 8 to 18% Bowl Mills are one of the major components of a coalfired thermal power station These are used for grindingISSN (Print) : 09730338 Central Power Research Institute DOI : 10 This study shows the performance of a currently running vertical roller coal mill (VRM) in an existing coalfired power plant In a power plant, the coal mill is the critical equipment, whose The layout of the coal mill with a rotary classifier
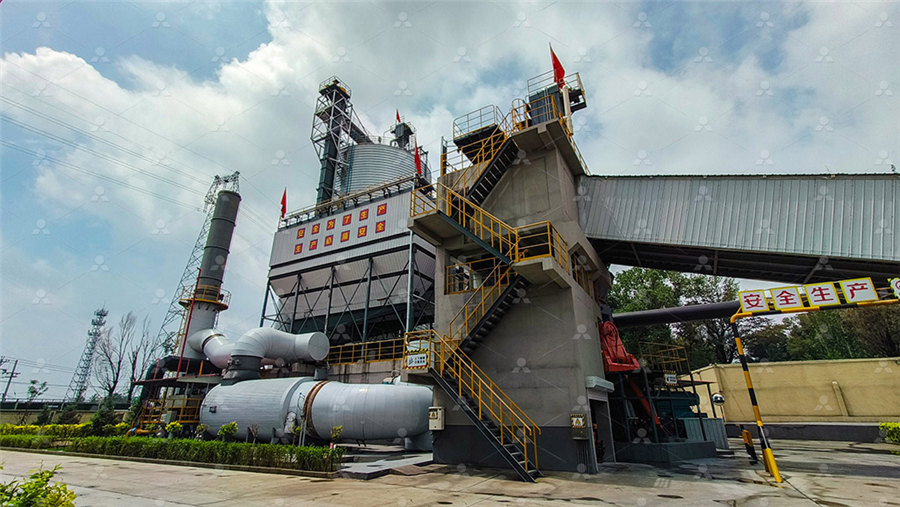
Coal Mill in Thermal Power Plant PDF Mill
Coal Mill in Thermal Power Plant Free download as Word Doc (doc / docx), PDF File (pdf), Text File (txt) or read online for free This document discusses coal pulverizers/mills which are critical components that convert the stored 2024年11月19日 The Open Circuit Grinding Mill is a product of Technomart Engineers, a prominent manufacturer of industrial equipment, and is aimed at offering highefficiency grinding solutions for a variety of sectors, including mineral processing and cement production Applications, where sophisticated milling circuits are not required due to material qualities and Grinding Mill Continuous Grinding Mill, Open Circuit Grinding Mill In addition to the vertical slag mill, other types of cement mill that can grind slag powder include: cement ball mill, pregrinding cement roller press, and cement roller press for final grinding For slag grinding plant, ball mill generally causes problems of dust accumulation, low grinding efficiency and high grinding temperatureSlag Grinding Plant GGBS Plant Slag Mill, Slag Grinding Mill2016年11月22日 By monitoring the thermal acoustic emission, the grinding efficiency can be judged in relation to grinding thermal behaviour To achieve this, the key issue of the thermal acoustic emission monitoring method is to identify the thermal AE signatures in relation to different grinding temperatures without involving any mechanically induced stressesEffect of different parameters on grinding efficiency and its

How to Calculate Grinding Mill Operating Efficiency
2017年9月13日 When accurate mill ore feed rate in dry tons per hour, mill power draw in kilowatts, and mill feed and product size analyses in microns are available the Bond Equation can be used to measure the operation of comminution machines, reporting it as operating work index1992 Central coal grinding plant (LM 263 D) for the production of lignite (brown) coal dust 1985 Delivery of first selfinerting coal grinding plant (LM 212 D) for the steel industry 1980 Delivery of first modular coal mill (LM 263 D) 1965 Construction of first pressure mill (LM 122 D) 1961 Introduction of hydraulic spring assembly system Loesche Grinding Technology for the Power IndustryThe utility model discloses a load soft measurement method for a coal grinding machine in the thermal power plant, the unit powder process dimension ball loss of selecting mill load to be under basic, normal, high three kinds of situations is w1=240 gram/ton SVRbased coal mill efficiency abnormity detection and diagnosis method CNA Thermal power plant ball mill load soft equipped with spring load system, the grinding force is overloaded at reduced mill load This will result in additional wear on roller and table segments and will produce excessive mill vibration While at high mill load operation, the grinding force is insufficient to meet the requirement for mill load increase o 180 160 140 120 100Coal Pulverizer Design Upgrades to Meet the Demands of Babcock Power

CEMENT GRINDING UNIT (20 MTPA) JP Power Ventures
Cement Grinding Unit named ‘Jaypee Nigrie Cement Grinding Unit’ at Nigrie (MP) with a capacity of 2 MTPA, which commenced its operations wef 9th October, 2014 and utilizing generated Fly Ash from Jaypee Nigrie Super Thermal Power Plant Jaypee Nigrie Super Thermal Power Project is a Coal Based Super Critical Thermal Power Plant ofDownload scientific diagram Thermal power plant's coal grinding and transport system to the burner from publication: The Characterization of PulverizedCoal Pneumatic Transport Using an Array Thermal power plant's coal grinding and transport Introduction The main Function of the Pulveriser in thermal power plant is to crush/grinding the raw coal coming from coal handling system through coal feeder into a predetermined size in order to increase the surface area of the coal If Pulveriser in Thermal Power Plant Bowl Mill Ball Mill2023年3月15日 Coal mills in thermal power plants are used to grind and dry the coal before it is fed Coal preparation plant crusher and grinding mill; Application of HFV3000 highpower highvoltage coal mill for thermal power plant LinkedIn
.jpg)
Performance Evaluation of Vertical Roller Mill in Cement Grinding
FIGURE 4 Particle size distributions of collected samples (Survey 2) Bond work indices and breakage characteristics under compression were determinedSo, due to the number of energy conversions, the efficiency of thermal power plants is very low around 2029% The efficiency of a thermal power plant is also depending on the size of the plant and the quality of coal In a thermal power plant, the heat energy is lost in the condenser There are two types of efficiency in thermal power plantsThermal Power Plant Components, Working and Site Selectionthe greater is the efficiency of the thermal power plant the efficiency of a power plant can be defined as “the percentage of energy contained in the fuel that is converted into electricity The rest is lost through conversion or in the form of exhaust heat The greater the Improving Thermal Power Plant Efficiency International Journal 2015年2月1日 Advanced coal plant emissions controls are the norm, and PRB coal is in use to some extent at most power plants in the US, and the Environmental Protection Agency (EPA) has proposed standards Understanding Coal Power Plant Heat Rate and Efficiency

Improving the Efficiency of the Coal Grinding Process in Ball
2022年2月24日 Keywords: drum ball mill, coal grinding, efficiency improvement, thermal power plant, regression analysis Suggested Citation: Suggested Citation Kamarova, Saule and Abildinova, Saule and Terziev, Angel and Baydusenov, Galym, Improving the Efficiency of the Coal Grinding Process in Ball Drum Mills at Thermal Power Plants (February 24, 2022)HIGmill high intensity grinding mill is an advanced and energyefficient fine and ultrafine grinding solution that relies on proven technology significantly increasing grinding efficiency and the mill itself The benefit of high power intensity and vertical installation is a very small footprintHIGmill high intensity grinding mill Metso2022年1月1日 A pilotscale grinding technology of ceramic medium stirred mill was proposed in this study Based on the specific productivity and grinding efficiency, the appropriate grinding parameters were ascertained as follows: material ball ratio of 07, ceramic ball medium size ratio (10 mm: 15 mm: 20 mm = 3:2:5), stirring speed of 110 rpm, grinding concentration of 50%, Highefficiency and energyconservation grinding technology using 大量翻译例句关于"high efficiency grinding" typical Thermal Design Power the Cemotec™ Mill for grinding solid samples without moisture loss; the Cyclotec™ Mill for uniform grinding of dry samples and the Knifetec™ Mill for the preparation of highfat, highmoisture and fibrous [] samples fosshigh efficiency grinding 英中 – Linguee词典
.jpg)
Cement Grinding Unit Clinker Grinder AGICO Cement
Cement grinding unit is also called the cement grinding plant It consists of cement ball mill, dust collector, belt conveyor, bucket elevator, cement silo, powder concentrator, etc AGICO provides highquality clinker grinders and 2023年5月19日 Did you know that 29% of plants spend 5 to 10% of their annual budget on maintenance, and 44% spend more than 40 hours a week performing maintenance? Considering this, crusher and mill efficiency must be one of the focal points of your business Crusher and mill efficiency measures the ability to crush, grind, and convert raw material into a finished productTactics for Optimizing Crusher and Mill Efficiency: A Guide for Plant 2024年3月1日 Thermal power plant operators have implemented various measures to deal with power grid load regulation requirements, such as reducing the low load and offdesign operating time [11] Steam temperatures can fluctuate when the generation load of a CFPP changes rapidly under grid demandDynamic characteristics and economic analysis of a coalfired power Download scientific diagram Gearless motor for a highpower mill from publication: Technical Evaluation and Practical Experience of HighPower Grinding Mill Drives in Mining Applications Gearless motor for a highpower mill ResearchGate
.jpg)
Optimizing Electrical Energy Consumption In Cement Process Plants
Roller Mill Ball Mills Limestone grinding 175 1750 3400 Limestone grinding 125 1300 2600 Coal grinding 25 310 730 High pressure grinding rolls High pressure grinding rolls can be used as premill in open circuit or as a finish mill in a close circuit mode The comminution of the material to be ground in the high pressure grinding roll takes Kamarova, Saule, et al "Improving the Efficiency of the Coal Grinding Process in Ball Drum Mills at Thermal Power Plants" EasternEuropean Journal of Enterprise Technologies , vol 1, no 1, 2022, pp 93105, doi: 1015587/172940612022 Improving the Efficiency of the Coal Grinding Process in Ball 2017年10月26日 The following are factors that have been investigated and applied in conventional ball milling in order to maximize grinding efficiency: a) Mill Geometry and Speed – Bond (1954) observed grinding efficiency to be a function of ball mill diameter, and established empirical relationships for recommended media size and mill speed that take this factor into Factors Affecting Ball Mill Grinding EfficiencyAirswept Coal Mill is the key equipment of rotary kiln cement clinker production system, also used in thermal power plant, metallurgy, chemical sugar industry Features: The airswept coal mill produce by our company has the following features: Production continuously, high output Fineness adjustableHigh Efficiency Coal Ball Mill for Grinding Coal with Different
.jpg)
Coal Mills in Thermal Power Plant PDF Mill
This document discusses coal pulverization in power plants It covers various topics related to coal pulverizers including: Types of coal and reasons for pulverizing coal like improved efficiency and combustion control Two types With the help of reheatregenerative cycle the efficiency of a plant can be enhanced substantially Other cycles of interest are the Kalina cycle, higher efficiency of steam generators It is predominantly adopted in large coalfired utility boilers The finer the grinding of coal, the more efficient its Thermal Power Plant: Thermal Power Plant ScienceDirectNowadays, in the field of cement grinding system of the world cement industry, the major cement grinding equipments include loop flow ball mill, roller press, ball mill semifinishing system, and vertical mill system, in which ball mill and Power Consumption of Cement Manufacturing PlantImproving Thermal and Electric Energy Efficiency at Cement Plants: International Best Practice iii LIST OF FIGURES Figure 1: Cement Production Process Flow Schematic and Typical Energy Efficiency Measures 2 Figure 2: Rotary Cement Kiln (Dry Process with Cyclonic Preheaters) 4 Figure 3: Schematic Depiction of Control Points and Parameters in a Kiln System Control IMPROVING THERMAL AND ELECTRIC ENERGY EFFICIENCY AT CEMENT PLANTS
.jpg)
Thermal Power Plant PDF Boiler Mill (Grinding)
Thermal Power Plant Free download as PDF File (pdf), Text File (txt) or view presentation slides online This document provides information about coal analysis, coal handling and storage, and coal firing systems used in thermal power plants It discusses the key components of coal analysis including proximate analysis, ultimate analysis, ash analysis, and calorific value2019年1月1日 This paper analyzes the effects of coal grindability and its characteristics on the grinding capacity and power consumption for beater wheel mill during exploitation in thermal power plant TENT B Practical assessment of grinding capacity and power 2016年10月5日 In this chapter an introduction of widely applied energyefficient grinding technologies in cement grinding and description of the operating principles of the related equipments and comparisons over each other in terms of grinding efficiency, specific energy consumption, production capacity and cement quality are given A case study performed on a EnergyEfficient Technologies in Cement Grinding IntechOpenHighefficiency, low emissions (HELE) technologies in operation already reach a thermal efficiency of 45%, and technologies in development promise even higher values A successful outcome to ongoing RDD could see units with efficiencies approaching 50% or even higher demonstrated within the next decadeTechnology Roadmap HighEfficiency, LowEmissions CoalFired Power
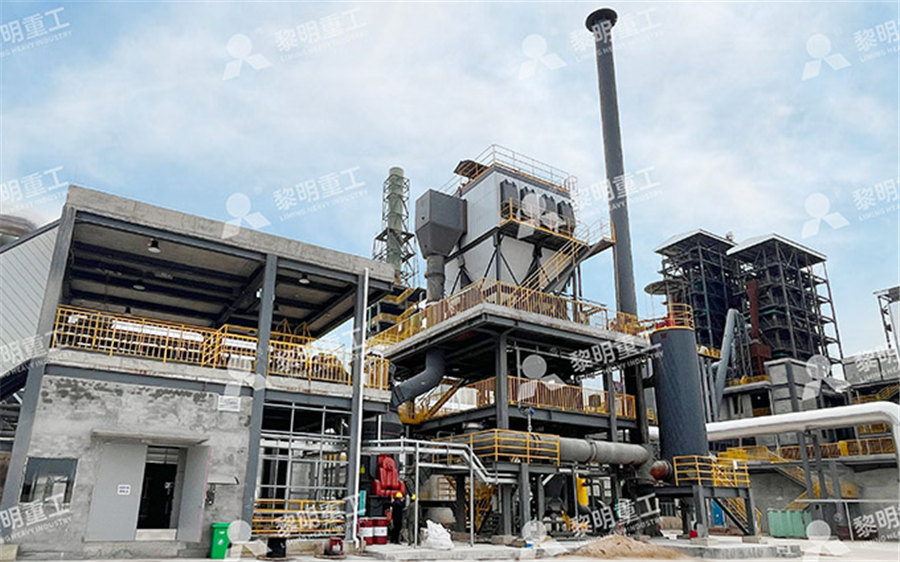
Variables Affecting Grinding Mill Power 911Metallurgist
2017年7月3日 In this paper it is paramount and is expressed as horsepower Power is one of the most enlightening single factors in the study of grinding In plant operations gross power input to the ballmill unit is the quantity of economic interest to the operator, but from the scientific aspect the study must be made of the net power expended within the Hefei Hengcheng Industrial Equipment Technology Co, Ltd hcverticalrollermill@outlook 86 HomeVertical Powder Gypsum Grinding Mill Production Line In Thermal Power Plant