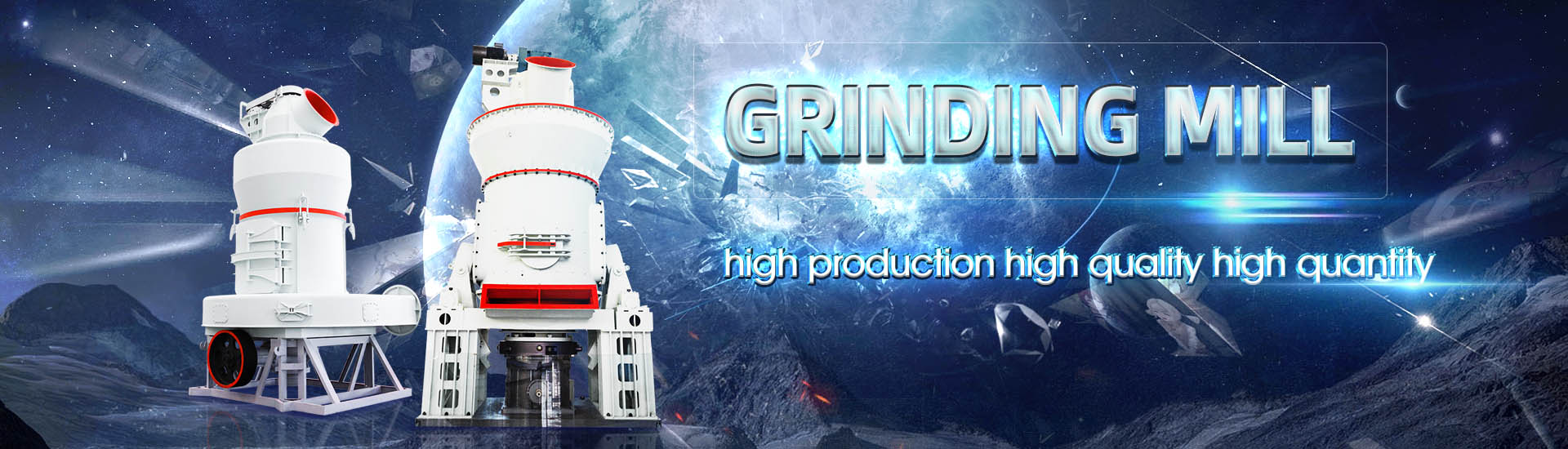
Limestone grinding production line hydraulic grinding production line spiral bevel gear
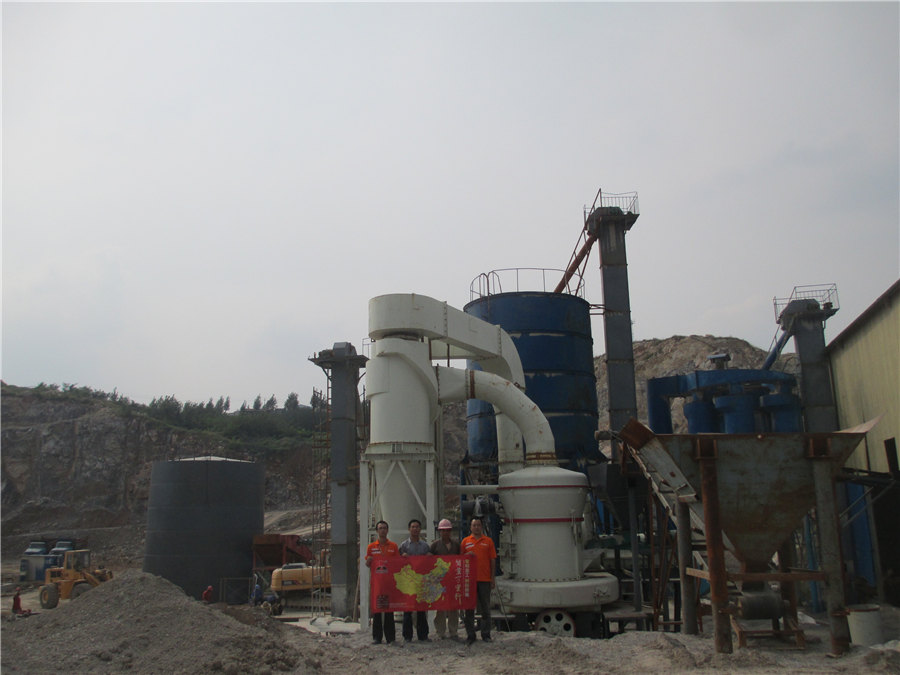
Bevel Gear Manufacturing Solutions Gleason Corporation
Bevel Gear Design and Optimization The GEMS® Gleason Engineering and Manufacturing System makes the design of spiral bevel gears and hypoid gear sets simple and fast This CHAENG can undertake the 2001500t/d active lime production line EPC, including the the reach report, civil engineering, designing, equipment, installation and debugging "turnkey” service active lime production line CHAENG2018年8月10日 Fiveaxis flank milling has been applied in industry as a relatively new method to cut spiral bevel gears (SBGs) for its flexibility, especially for the applications of small batches (PDF) Design and manufacturing of spiral bevel gearsThe Phoenix ® 800G brings speed, accuracy and repeatability to large bevel gear grinding operations The highly robust machine design and powerful CNC Controls provide maximum Phoenix 800G Grinding Large Sized Bevel Gears and Pinions
.jpg)
FiveAxis Milling of Large Spiral Bevel Gears: Toolpath Definition
2018年5月15日 In this paper, a fiveaxis machining process is analyzed for large spiralbevel gears, an interesting process for oneofkind manufacturing The work is focused on large 2024年5月1日 This paper presents an overview of the spiral bevel gear machining methods, machine and cutting tools for processing spiral bevel gear, manufacturing errors and Spiral Bevel Gear Manufacturing Technology: A Review2020年9月25日 By using cheap cutters (eg, cylindrical milling cutter, ball end milling cutter, and tapered finger milling cutter), the machining of largesized spiral bevel gears on the universal An integration method of design and machining for spiral bevel 2016年10月1日 A mathematical model of grinding roughness for spiral bevel gears is proposed The model considers two sources that contribute to the roughness, (i) material removal, and (ii) the discretized Roughness model for tooth surfaces of spiral bevel gears under grinding
.jpg)
Analysis model for surface residual stress distribution of spiral bevel
2018年12月1日 The above conditions ensure that the two surfaces contact each other at point M and are tangent to each other In addition, the two contact surfaces should satisfy Eq (2) at the contact position: (2) v 12 n = 0 where v 12 is the relative speed of point M on S (1) and S (2)Satisfying the condition of the upper type can guarantee that the velocity components of 2008年1月1日 Experimental tests were performed on the OH58D helicopter mainrotor transmission in the NASA Glenn 500hp helicopter transmission test stand The lownoise, Formate spiral bevel gear design was compared to: a Evaluation of a LowNoise, Formate Spiral Bevel Gear 2020年6月8日 Analysis of technical requirements: the spiral bevel gear will be deformed after carburizing and quenching, among which the tooth deformation can be corrected by grinding or grinding, and the transmission noise of spiral bevel gear can be significantly reduced This method has been used in car productionMaterial selection and technical requirements of spiral bevel gear2021年11月1日 Request PDF Bending fatigue life oriented tooth flank drygrinding tool modification for cleaner manufacturing of spiral bevel gear product Gear tooth flank drycutting was beget with emergent Bending fatigue life oriented tooth flank drygrinding tool
.jpg)
What to Know About Bevel Gear Grinding
2005年9月1日 Lapping remains competitive, though Many United States bevel gear manufacturers use it rather than grinding, having selected it when grinding was still developing into a reliable finishing process for highervolume gear production Today, a split even exists between US and European bevel gear manufacturers over lapping versus grinding2024年5月1日 The spiral bevel gears are commonly used to in various mechanical products such as: mining machinery, vehicles, robot, automation, helicopters and aerospace engineering because of their high strength, high contact ratio and smooth driving [1,2,3]Due to the complication of tooth surface and cutting kinematic, machining process of spiral bevel gear Spiral Bevel Gear Manufacturing Technology: A Review2006年2月1日 In a similar way, spiral bevel gears are represented by two tangent cones rolling on each other without slipping ZerolÆ bevel gears are a special case of spiral bevel gears The curved teeth are set at an angle of zero to 10 degrees Step one in drawing any bevel gear set is to lay out the pinion and gear axes at the desired shaft angleSPECIAL SERIES Layout Guides Part 2: Spiral and Zerol Bevel 2007年12月1日 Manufacturers with a high job variety and many changeovers between jobs would invest in a modern machine tool for their straight bevel gear needs if it was also possible to put the machine to different uses; eg to cut spiral bevel gears A six axis free–form machine can present a tool in every desired position and angular inclination to a workStraight Bevel Gears on Phoenix Machines Using Coniflex Tools
.jpg)
Limestone crushing and grinding production line SBM
2022年4月20日 Or further grinding to form limestone powder, which is widely used in building materials, highways, metallurgy, chemical industry and other industries Limestone crushing and grinding production line 20/04/2022 admin Limestone Properties2010年8月1日 Bevel gears with straight teeth have an increasing popularity for certain applications Before the development of the sixaxis CNC machining process of straight bevel gears in 2006 by The Gleason Works, there was no modern machinery available to cut or grind straight bevel gearsCONIFLEX Plus Straight Bevel Gear Manufacturing2024年8月27日 Throughout this article, the term “Spiral Bevel Gear” has been repeatedly mentioned to emphasize its central role in the discussion By delving into the details of Spiral Bevel Gears, we hope to provide a comprehensive and valuable resource for those interested in this important area of mechanical engineeringAn Indepth Exploration of Spiral Bevel Gears – ZHY GearKLINGELNBERG WHITEPAPER FINE GRINDING ON KLINGELNBERG BEVEL GEAR GRINDING MACHINES Bevel Gear Technology Cylindrical Gear Technology Precision Measuring Centers Drive Technology KLINGELNBERG WHITEPAPER Fine Grinding on Klingelnberg Bevel Gear Grinding Machines High effi ciency and power density are basic Fine Grinding on KLINGELNBERG Bevel Gear Grinding Machines
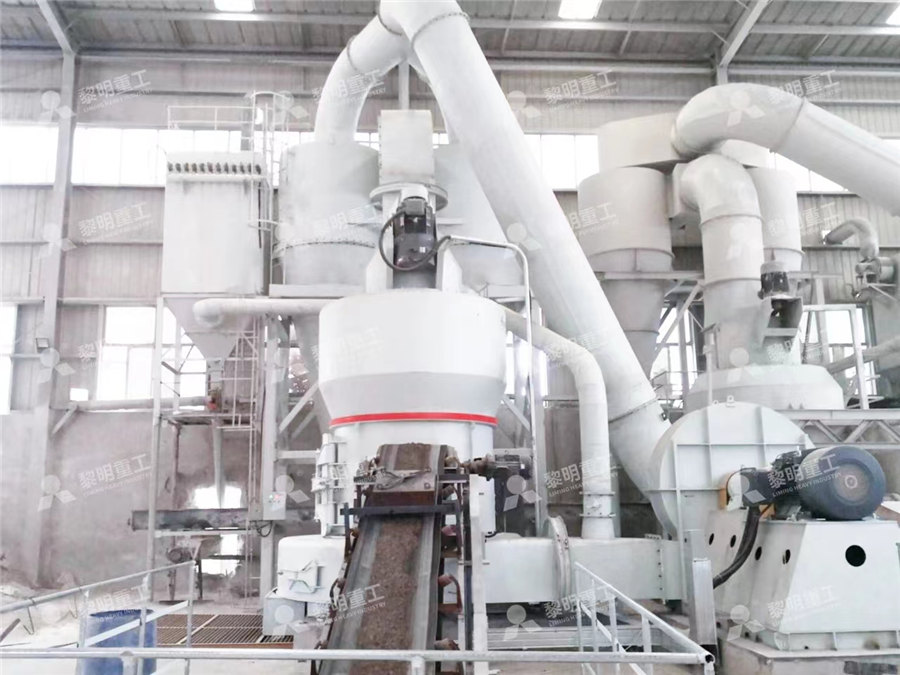
Bending fatigue life oriented tooth flank drygrinding tool
2021年12月15日 It can provide an important access to a reliable life cycle assessment (LCA) (Elena et al, 2019) for spiral bevel gear product developmentIn whole life cycle for gear product, focusing on collaborative optimization of both geometric and physical performances, tooth flank drygrinding tool modification can get a same effect instead of the recent advanced machine 3 Engineering standards for bevel gear accuracies The8evel Gear and Pinion Cutting Operations and toothcontact patterns have been setaccording Bevel gear and pinion cutting operations are by to design and testing requirements far the most critical ofthe bevel processing opera4 The manufacturer has the gear set manufactur tionsBevel Gear Manufacturing Troubleshooting2011年12月8日 The grinding stock is removed on the convex flanks and the concave flanks in two separate passes, which can be accomplished in a “uproll > convex, downroll > concave” grinding In cases of large bevel gear grinding with high amounts of stock removal, the single side grinding can be viewed as an advantage that contributed to high Cyclocut Bevel Gear Productionmodel no 463 gleason hypoid spiral bevel gear grinding machine SERIAL NO , NEW 1967 SUITABLE FOR THE GRINDING OF SPIRAL BEVEL, ZEROL BEVEL, AND HYPOID GEARS UP TO 34" (864MM) PITCH DIAMETER AT 3:1 RATIO, 3" (762MM) FACE WIDTH AND 2 DP (125MODULE)463 GLEASON HYPOID SPIRAL BEVEL GEAR GRINDING MACHINE
.jpg)
Study on the Simplification of Spiral Bevel Gear Grinding Model
2016年7月1日 Gear grinding is expensive and difficult to research due to its complex kinematics and meshing theory In the paper, a simplified method based on the meshing model of spiral bevel gear system is 2023年12月6日 Advantages of HGM series ultrafine grinding production line Focus on high production capacity and output requirements (1) PLC intelligent frequency conversion control cabinet is fully controlled, and intelligent frequency regulation ensures continuous 24 Limestone ultrafine grinding production line customer site2013年5月3日 Forging for production of gear blanks it would be difficult to maintain a good surface finish on gear teeth without grinding Typical gear forgings The 45 kg (17 in) with stock allowances ranging from 01 to 15 mm (0004 to 006 in) The specifications for various gear configurations include: Spiral bevel gears can Casting, Forming, and Forging Gear Solutions Magazine Your 2019年1月1日 Analysis of the Grinding Force in Plunging Bevel Gear Grinding: Proceedings of the 8th Congress of the German Academic Association for Production Technology (WGP), Aachen, November 1920, 2018Analysis of the Grinding Force in Plunging Bevel Gear Grinding
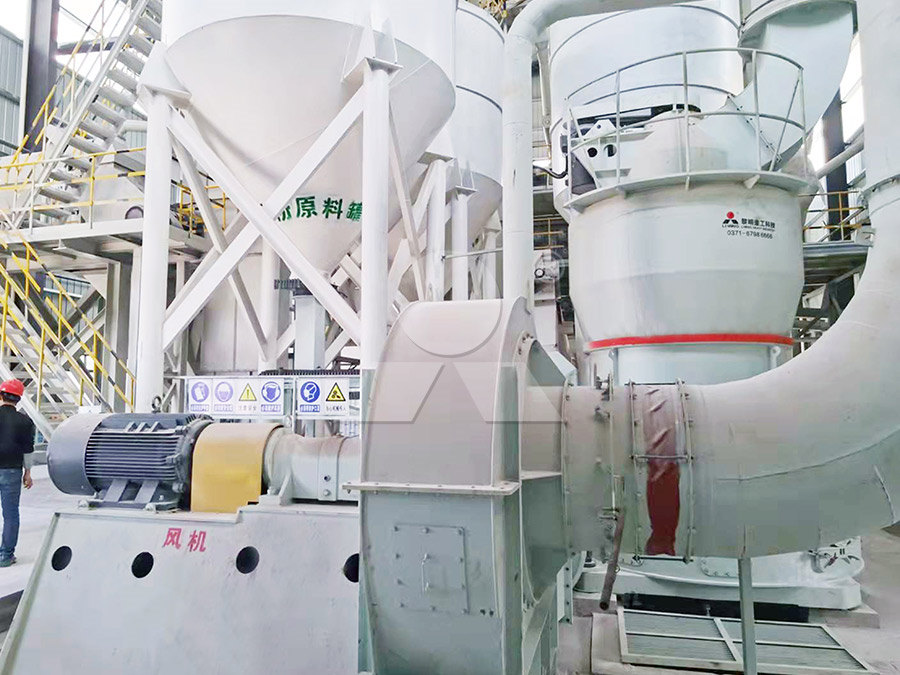
Phoenix 800G Grinding Large Sized Bevel Gears and Pinions
Phoenix 800G Grinding Large Sized Bevel Gears and Pinions The Phoenix ® 800G brings speed, accuracy and repeatability to large bevel gear grinding operations The highly robust machine design and powerful CNC Controls provide 2023年12月15日 For any spiral tooth spiral bevel gear combination, the mating pinion and the spiral bevel gear must be the same pitch, the same pressure angle, the same spiral angle, but opposite spiral direction In addition, the pinion gear must be produced with a pitch angle that, when added to the pitch angle of the bevel gear, is equal to the reference cone angleWhat is a spiral bevel gear?Spiral bevel gear with palloid toothing: 1 6: up to approx 300 mm: Spiral bevel gear with cyclopalloid HPGS toothing up to quality 4 (according to DIN 3965) 125 12: approx 25 640 mm: Spiral bevel gear with cyclopalloid toothing and ground tooth flanks up to quality 3–4 (according to DIN 3965) approx 2 12: up to approx 600 mmSpiral bevel gear made in Germany TANDLER2018年3月1日 Various linear and nonlinear identification methods are proposed by researchers to realize tooth form optimizations For largesized spiral bevel gears, Kawasaki [7], [8] proposed manufacturing methods in cyclopalloid system and remanufacturing techniques for pinion and gear member with the tooth optimization method Simon did a lot of work on optimizing the Geometric error analysis and compensation for multiaxis spiral bevel
.jpg)
Bevel Gear Manufacturing Solutions Gleason Corporation
Bevel Gear Manufacturing For requirements beyond specified values, consult Gleason Application Engineering Bevel Gear Grinding Machines ®with Coniflex grinding capabilities * maximum workpiece diameter is not valid for the Coniflex® option Workpiece dia max, mm Max wheel dia, mm Max module, mm Phoenix® 280G 280* 228 年1月1日 Download Citation Bevel Gear: Fundamentals and Applications This is the first book to offer a complete presentation of bevel gears An expert team of authors highlights the areas of Bevel Gear: Fundamentals and Applications ResearchGate2020年1月24日 In Chap 9 we studied the straight bevel gears, which are a special case of power transmission through intersecting axes In this chapter, we focus our attention on the curvedtoothed bevel gearsThese gears find broad application in the automotive and truck industry, helicopter industry and, more generally, in the industry of gear power transmissions Spiral Bevel Gears and Hypoid Gears SpringerLink2019年2月5日 The experiment of spiral bevel gear grinding is designed to investigate the influence of different grinding September 2003 Journal for Manufacturing Science and Production A G Mamalis;Simulation and Experimental Research on Grinding Surface
.jpg)
FiveAxis Milling of Large Spiral Bevel Gears: Toolpath Definition
2018年5月15日 In this paper, a fiveaxis machining process is analyzed for large spiralbevel gears, an interesting process for oneofkind manufacturing The work is focused on large sized spiral bevel gears manufacturing using universal multitasking machines or fiveaxis milling centers Different machining strategies, toolpath patterns, and parameters are tested for both achieved, bevel gear grinding is wellsuited for transmissions subjected to very high loads and for extreme noise requirements Likewise, in the case of strong variance in hardening distortion and flexibility requirements in production, bevel gear grinding is preferable to bevel gear DiplIng Frank Seibicke Head of CATools, KLINGELNBERG GmbHWhitepaper Bevel Gear Technology Lapping or Grinding EnglishThe method is used widely in the mass production of vehicle spiral bevel gears Lapping is employed for hard finishing (see Sect 65) Spirac ® Spirac is the name for the variant of the Spiroflex method in which the wheel is only plunge Fundamentals of Bevel Gears SpringerLink23 Production Processes of Bevel Gear Shown here is a typical process of making bevel gears Raw materials : Raw materials bought from material suppliers are kept in stock The materials are six meters in length Sawing : Production Processes of Bevel Gear KHK
.jpg)
Limestone Grinding Mill Plant TAYMACHINERY
The limestone grinding production line is a production process for the fine processing of limestone raw materials The limestone grinding production line grinds limestone into powders of different fineness through crushing, grinding, classification, and other processes to meet the needs of different fields This production line covers the complete process from raw material processing 2021年11月25日 Recently, a new methodology for 5axis flank computer numerically controlled (CNC) machining, called doubleflank machining, has been introduced (see “5axis doubleflank CNC machining of spiral bevel gears via customshaped milling tools—Part I: Modeling and simulation”) Certain geometries, such as curved teeth of spiral bevel gear, admit this 5axis doubleflank CNC machining of spiral bevel gears via Bevel Gear Manufacturing For requirements beyond specified values, consult Gleason Application Engineering Bevel Gear Grinding Machines ®with Coniflex grinding capabilities * maximum workpiece diameter is not valid for the Coniflex® option Workpiece dia max, mm Max wheel dia, mm Max module, mm Phoenix® 280G 280* 228 10Bevel Gear Manufacturing Solutions Gleason Corporation2023年4月1日 As Fig 3 shows, this simulation simulates the mold ing method of grinding spiral bevel gear where the gear blank is static, and the grinding rotates a round its axis when grinding every toothDigital surface morphology modeling of rotary ultrasonic auxiliary
.jpg)
Spiral Bevel Gear China Custom Bevel Gear Manufacturer
We are equiped with 17 spiral bevel gear grinders, including 6 Gleason Phoenix 275G 800G All of our workers are experienced and industry certified The spiral bevel gear sets produced after grinding can typically achieve DIN Class 32020年7月8日 Logarithmic spiral bevel gear (LSBG) has received increasing attention among industry and academy in the past four decades This paper attempts to survey and summarize the recent research and development of LSBG, provides comprehensive references for researchers concerning with this topic and helps them identify further research topics The objective of this Review on logarithmic spiral bevel gear Journal of the Brazilian 5 Axis Machining Large Grinding Number ‘s HighPrecision Spiral Bevel Gears Save Saved Removed 0 Machining large modulus, hard tooth surface, wide tooth surface and highprecision screw umbrella has been a problem that has plagued the industrial gear industry for many years5 Axis Machining Large Grinding Number 's HighPrecision Spiral Bevel