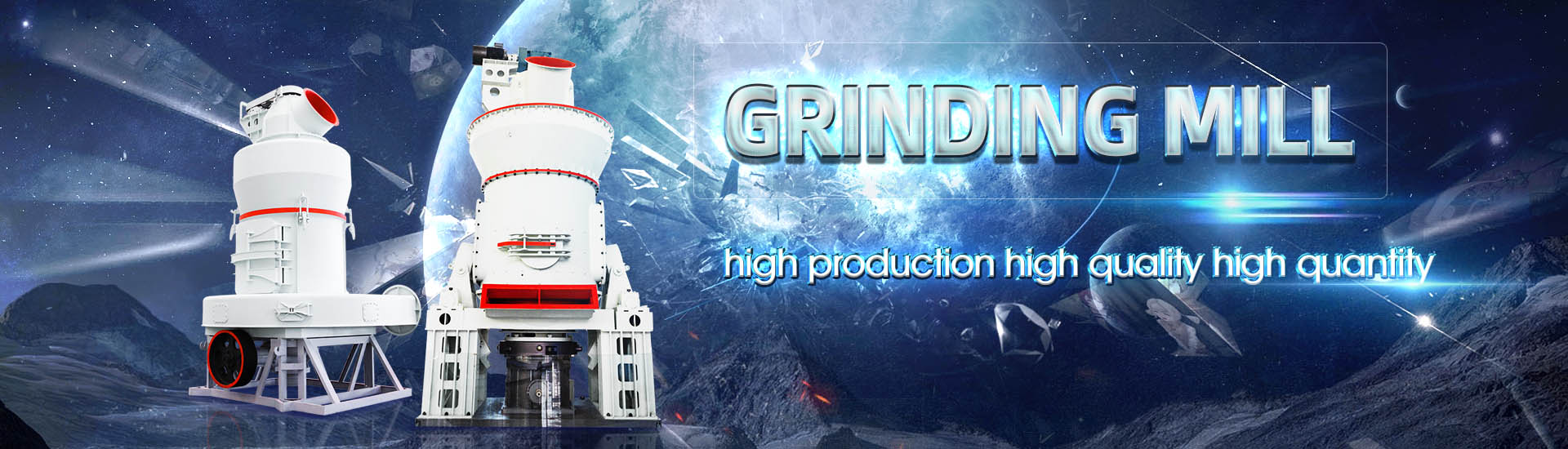
HOME→RZ8O is the raw material vertical mill main oil reduction station what kind of limestone is used
RZ8O is the raw material vertical mill main oil reduction station what kind of limestone is used
.png)
Vertical roller mill for raw Application p rocess materials
Vertical roller mills are adopted in 20 cement plants (44 mills) in Japan In the vertical roller mill which is widely used in the raw material grinding process, raw materials input grinding table are crushed and pulverized on it and transported to separator by kiln exit gas introduced into the 2021年1月1日 For the past three decades the vertical roller mill has emerged to be the preferred choice for grinding raw materials With the grinding capacity of a vertical roller mill and the Review on vertical roller mill in cement industry its performance Vertical raw mill is an ideal grinding mill that crushing, drying, grinding, grading transfer set in one It can be widely used in cement, electric power, metallurgy, chemical industry, nonmetallic Vertical raw mill Cement PlantVertical roller mills are used in cement industries for grinding clinker, coal, raw materials, and cement They comprise 24 conical rollers that are hydraulically pressed onto a horizontal VRM Operation and Optimization PDF Mill (Grinding) Scribd
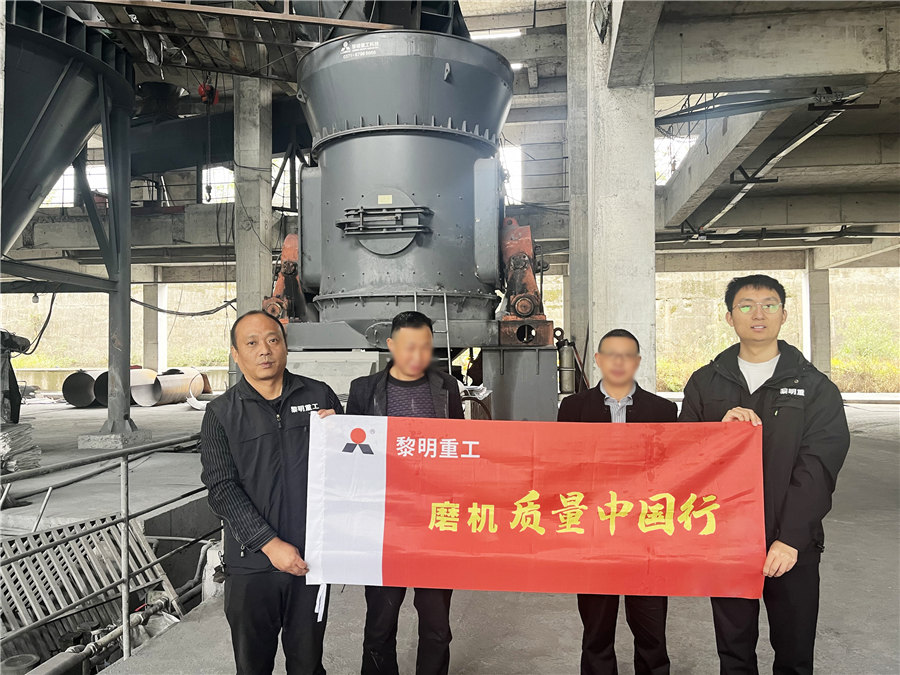
VRM Operation and Optimization PDF Mill (Grinding)
Process parameters like feed size, moisture content, product fineness, and material properties affect mill operation and performance Common issues and corrective actions are also The core elements of these plants are the Loesche vertical mills for drygrinding the abovementioned grinding stock Loesche has developed and built the largest and most efficient PROCESS OPTIMISATION FOR LOESCHE GRINDING PLANTSDrying of moisture in raw materials is required for effective grinding and subsequent handling of raw meal This is achieved normally by ducting part of the kiln exhaust gas through the mill Raw Material DryingGrinding Cement Plant OptimizationIn the 1970s, Vertical Roller Mills (VRMs) became increasingly dominant for grinding raw materials, mainly for the cement and power industries, due to their high energy efficiency and Key Industry Program Castolin Eutectic
.jpg)
quadropol® thyssenkrupp Polysius Grinding Technologies
Compact plant arrangement with service tower, quadropol® vertical roller mill and main filter are part of the supply Optimized mill operation will be supported by a digitalization package incl 2022年5月31日 The vertical roller mill (VRM) is commonly used for secondary and tertiary crushing processes in numerous industries In this study, the discrete element method (DEM) Analysis of vertical roller mill performance with changes in material 2016年9月1日 Vertical roller mills, VRMs, are widely used for grinding raw materials in factories engaged in the extraction and processing of minerals Any machine used for grinding or crushing consumes around Operational parameters affecting the vertical roller mill The main raw materials are limestone, basalt, sand stone, pumice, gypsum Raw material Proportion Station: Raw material proportion station is the place where the raw materials like limestone, This temperature is used to drying Cement Manufacturing Process INFINITY FOR
.jpg)
VRM Operation and Optimization PDF Mill
The document discusses vertical mills used for grinding clinker, raw materials, coal, and cement Vertical mills can be used for both pregrinding and finish grinding They comprise rollers that are hydraulically pressed onto a rotating 2022年10月3日 Raw materials grinding process is a first step of cement production which is has an important role in the first grinding step Vertical Raw Mill is a main equipment that is used in grinding or (PDF) ANALISA KINERJA ALAT VERTICAL RAW MILL PABRIK II PT 2023年8月8日 Grinding: The raw materials, such as limestone, clay, shale, etc, are fed into the vertical mill and ground to a fine powder known as raw mealWhat is the separation process in a vertical raw mill? LinkedIn2022年1月10日 The required pace of transition means that the availability of certain raw materials will need to be scaled up within a relatively short time scale—and, in certain cases, at volumes ten times or more than the current market size—to prevent shortages and keep newtechnology costs competitive (see sidebar “Rareearth metals”)The rawmaterials challenge: How the metals and mining sector
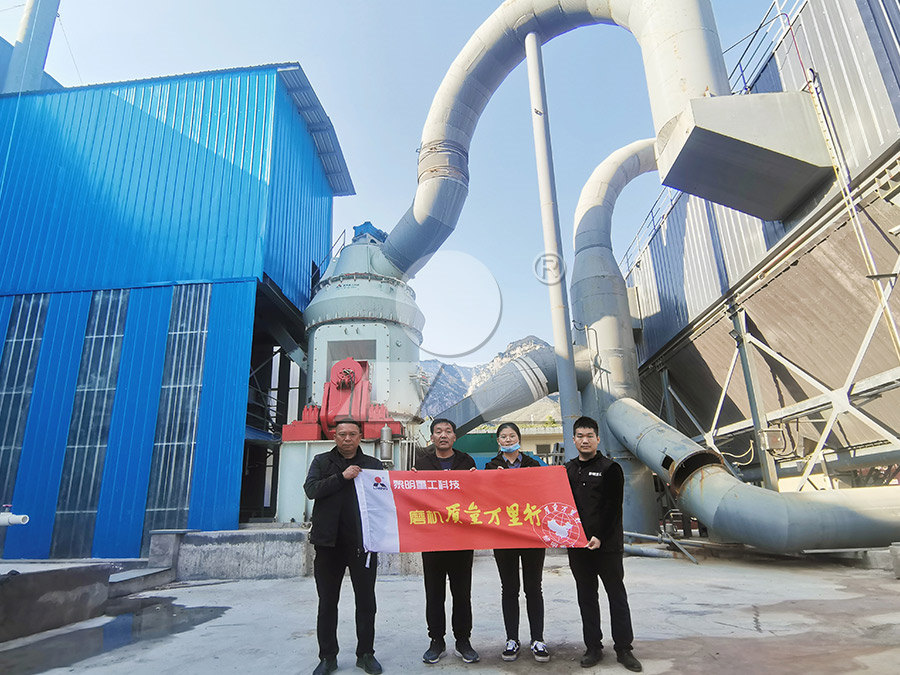
Vertical Raw Mill CHAENG
The GRMR Vertical Raw Mill of CHAENG is a kind of high efficiency, energy saving and environment friendly grinding equipment specially for cement raw material grinding system in cement plant It has the advantages of high grinding efficiency, low power consumption, low noise, and little dust pollution, can meet the requirements of 30010,000 TPD cement production lineAGICO Cement Vertical Mill AGICO Cement Ball Mill Cement Vertical Mill Grinding System Cement vertical mill, also called roller mill, is another raw mill commonly used in cement pared with the cement ball mill, it has a great difference in structure, grinding principle, process layout, automatic control, and energy consumption, which play an important role in the Raw Mill – Raw Mill In Cement Plant AGICO Cement Raw Mill2021年1月22日 In the whole process of cement production, the electricity consumption of a raw material mill accounts for about 24% of the total Based on the statistics of the electricity consumption of the raw A Survey and Analysis on Electricity Consumption of Raw Material Mill There are two main layouts for a vertical roller mill (VRM) system, with product collection in cyclones or a filter The power consumption of a VRM is calculated using factors like the specific grinding pressure, roller dimensions, grinding Vertical Mill Calculations PDF Mill (Grinding) Nozzle
.jpg)
(PDF) Drives for large vertical roller mills ResearchGate
PDF On Jan 1, 2017, J Harder published Drives for large vertical roller mills Find, read and cite all the research you need on ResearchGateThe OK™ Mill was originally designed for cement grinding In 2017 we released the OK™ vertical roller mill for raw materials grinding The OK™ Mill’s modular design comes with unique flexibility, showcasing parts commonality, where OK™ Raw and Cement MillRaw material, cement slag, gypsum and coal ash grinding, as well as pregrinding, in building material industries; coal and limestone mill in power and metallurgical industries and grinding systems in calcite, ceramic powder and mine industries Vertical Mill Gearboxes MFY and MFYT central drive gearboxes are a new series of low01 NGC GearsDry Grinding: Open circuit Ball mill, closed circuit Ball mill, vertical roller mill, Roll Press or Roll press in circuit with ball mill However, it would be seen that the most significant process and types used for raw material grinding operations in modern cement industry are: Process: Dry Closed circuit drygrinding Type of mill: Ball and Raw Material DryingGrinding Cement Plant Optimization
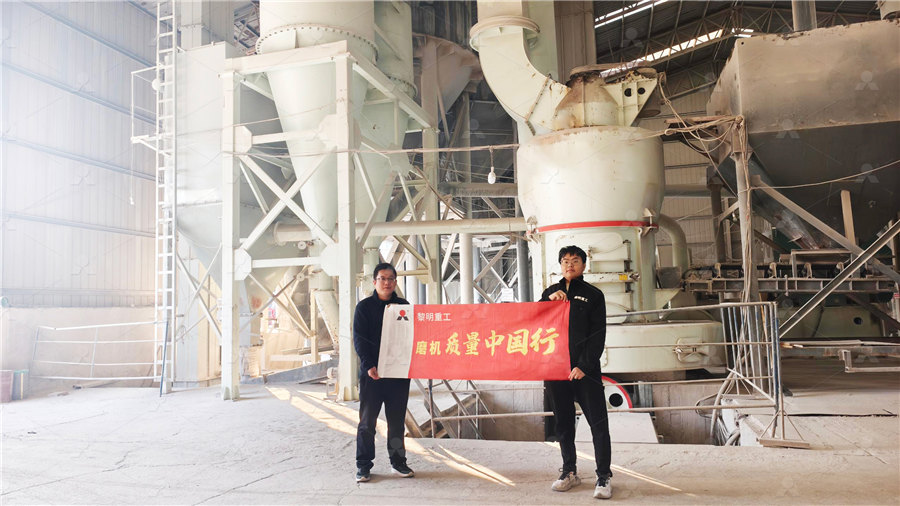
Design and Realization Of Roller Mill Control System ResearchGate
438 QianHong Wang et al / Physics Procedia 33 ( 2012 ) 437 – 443 Among the rest, stable operation of the vertical mill vertical means that to ensure the material layer thickness of the disc 2013年3月1日 This is referred to as the classifier cut size Generally, the plant operator can control the classifier cut size, and thus the comminuted product fineness by adjusting the classifier rotor speed Cements ground in the vertical roller mill fulfil the quality 2020年3月3日 Because the preliminary processing of raw materials is eliminated, the construction of the FINEX plant will cost 8% less to build than a blast furnace facility of the same scale Furthermore, a 17% reduction in production costs is expected since lowerpriced raw materials can be used in the FINEX processSmelting Reduction Processes SpringerLink2017年9月11日 Due to the compact design and material transportation system of vertical roller mills (VRM), some important streams (total mill feed and discharge, dynamic separator feed and reject) remain in the (PDF) Performance Evaluation of Vertical Roller Mill in
.jpg)
VRM Operation and Optimization PDF Mill (Grinding) Scribd
Vertical roller mills are used in cement industries for grinding clinker, coal, raw materials, and cement They comprise 24 conical rollers that are hydraulically pressed onto a horizontal rotating grinding table Material is fed onto the center of the table and thrown outward under the rollers where it is ground into a fine powder by both rolling and sliding motion Fine material is carried Vertical Roller SINOMALY produces cement raw material grinding mills in various specifications These machines are suitable for grinding mill production lines with an output of 2500t/d, 3200t/d, 4000t/d, 5000t/d, 6000t/d and 8000t/d Vertical Roller Mill for Cement Raw Material2018年12月18日 Main components of cement are all minerals provided in clinker and raw materials These experiments were carried out in the Holding Company Cement Plant in Lukavac, Bosnia and Herzegovina Mineral Characterization of raw materials and final product Fig2 Schematic process flow of vertical roller mill for grinding of raw materials Vertical roller mills are adopted in 20 cement plants (44 mills) in Japan (Reduction) Mill and Separator 89 77 Mill Fan 105 57 50% (Reduction) Limestone Clay Silica Iron raw material CFW CFW CFW CFW 72 7 Item Optimization of raw materialVertical roller mill for raw Application p rocess materials
.jpg)
Raw Material Production For The Oil Gas Industry
Anglo Carbon manufactures a diverse range of materials components for use in Valves including: Valve Seats, Seals and Bearings (+44) Raw Material Production For The Oil Gas Industry Waterloo Mills Waterloo Road Pudsey LS28 8DQ t: (+44) 0113 256 4664 info@anglocarbon Markets Industry;7 // Almost any plant for the grinding of cement raw material is a combination of machines specially adapted to the particular physical properties of the material to be ground As a result, our plants work efficiently without any trouble » Highly efficient grinding, drying, and separating in one unit » Outstanding production capacities exceeding 1,400 t/h in one single millPFEIFFER MILLS FOR THE CEMENT INDUSTRYThe document discusses maintenance and repair of an ATOX Vertical Mill It describes systematic and conditionbased maintenance approaches Systematic maintenance consists of regular cleaning, lubrication and visual inspections Conditionbased maintenance monitors factors like vibration levels and temperatures during operation and performs more thorough inspections Atox Vertical Roller Mill, Maintenance and Repair2012年12月31日 Report system used to show our main work pa ram eters roller mill, limestone, pul verized coal and accumulativ e total parameters, the time of history and can be used for roller mill work Design and Realization Of Roller Mill Control System
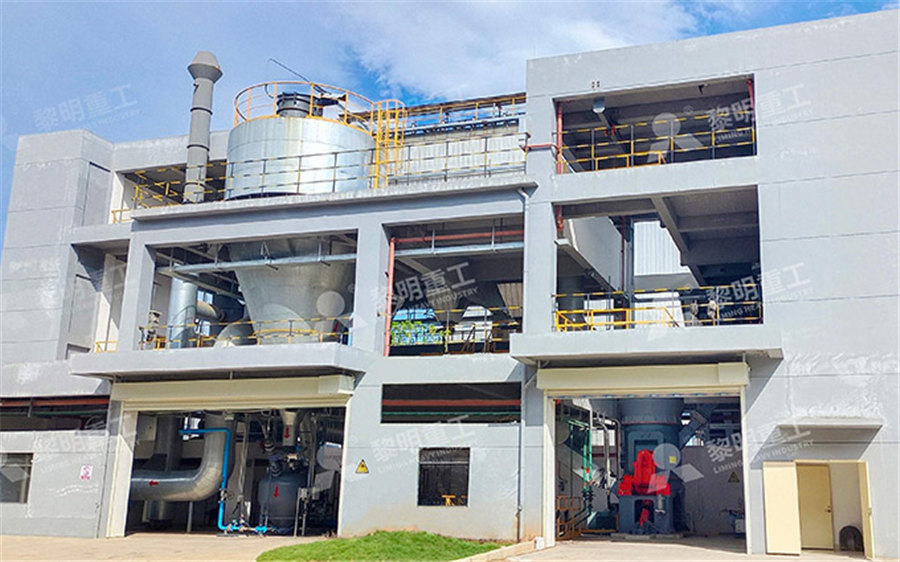
A Survey and Analysis on Electricity Consumption of Raw Material Mill
vertical mill raw material final grinding system, and roller press raw material final grinding system This paper compares the characteristics of several grinding systems and summarizes their The document discusses optimization and operation of vertical roller mills (VRMs) Key points include: 1) Continuously monitor and adjust process parameters to find the optimum operating conditions of highest capacity and lowest power consumption 2) Relevant process parameters to monitor include product rate, fineness, classifier speed, grinding force, power consumption, air Optimization of Vertical Raw Mill Operation PDF2023年12月4日 A vertical roller mill (VRM) is a grinding equipment used for the size reduction of minerals, cement, and ceramics The capacity of the VRM depends not only on the grinding material properties but also on the operational parameters of the VRM This study investigatedNumerical Investigation of Vertical Roller Mill Operation Using HRM Limestone vertical HRM vertical mill can be used to grind materials with a diameter less than 44mm on the rotary disc by rollers with certain pressure It has advantages of high grinding efficiency, strong dry capacity, easily adjustable grinding size, low noise, low power consumption, simple process flow, low wear rate, low operation costs, etcHRM Limestone verticalHefei ZhongYa Building Material
.jpg)
Hammer Mill: components, operating principles,
2022年11月30日 2 Not suitable for lowmelting sticky or plasticlike material due to heat generation in the mill head as a result of mill fouling 3 The mill may be choked if the feed rate is not controlled, leading to damage 4 Presence of The Vertical Mill, also known as a Vertical Milling Machine or Vertical Roller Mill, is a crucial equipment used in various industries for grinding and processing materialsBellian Mining Machinery offers a wide range of Vertical Mills with advanced technology and reliable performance to meet the diverse needs of our customersVertical Roller Mill, Vertical Raw Mill, Vertical Cement MillA vertical roller mill, also known as a vertical grinding mill or vertical mill, is a comprehensive grinding equipment integrating crushing, drying, grinding, grading, and conveying Vertical grinding mills can be widely used in electric power, metallurgy, construction, chemical industry, and other industries to make powder, especially for materials such as cement clinker, coal Energysaving and Efficient Vertical Roller Mill Fote MachineryLimestone is not only the main component in cement raw material Owing to its particular characteristics, the separate grinding of limestone in our Pfeiffer machines has been a routine practice for well over 100 yearsLimestone mills for all requirements Gebr Pfeiffer
.jpg)
Vertical Grinding Mill: How it Works, Application And Advantages
Vertical Grinding Mill’s are used to grind various insulation materials, phosphate rocks, cement, activated clay or carbon, limestone, marble, glass, plaster, etc It enables the grinding and processing of more than 280 kinds of nonflammable and nonexplosive materials with a hardness lesser than 7 and humidity less than 6%According to a report from the National Renewable Energy Laboratory (Table 30), depending on make and model wind turbines are predominantly made of steel (6679% of total turbine mass); fiberglass, resin or plastic (1116%); iron or cast iron (517%); copper (1%); and aluminum (02%) Many turbine components are domestically sourced and manufactured in the United StatesWhat materials are used to make wind turbines?We hope this guide has helped you understand what a raw mill is, how it works, and its benefits If you have any further questions, feel free to ask us in the comments section below FAQs What raw materials are used in a raw mill in a cement plant? The raw materials used in a raw mill in a cement plant include limestone, clay, shale, and iron oreWhat does a Raw Mill do in Cement Plant? ball mills supplier2020年3月3日 The raw materials of the blast furnace are (i) solids (ore, coke, flux) which are charged from the top of the furnace and (ii) preheated air (ie hot blast) which is passed through tuyeres near the bottom of the furnace Metallurgical coke supplies most of the reducing gas and heat for ore reduction and smelting operationBlast Furnace Process SpringerLink
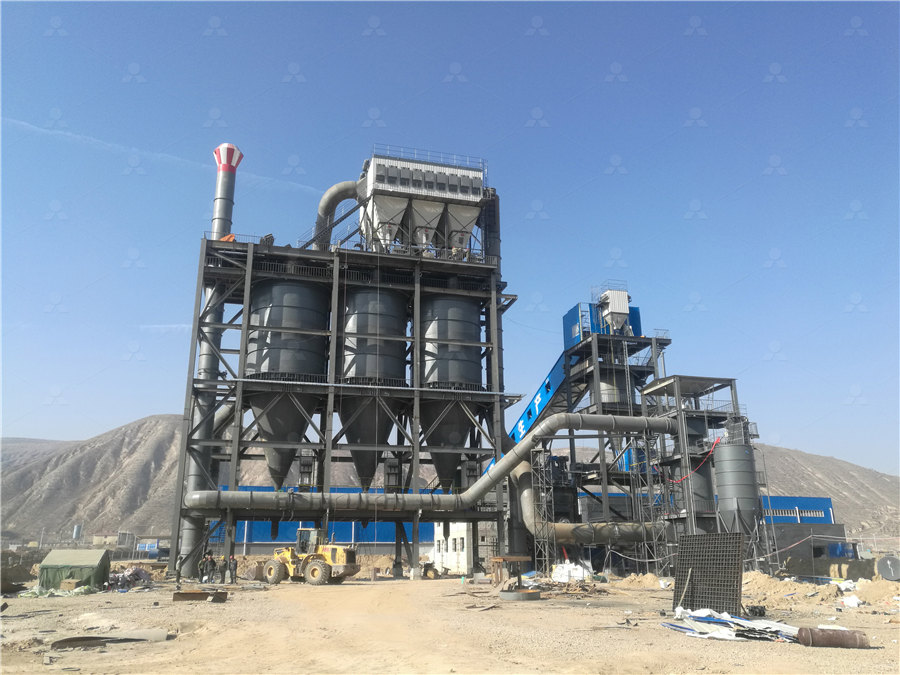
What is a vertical roller mill (VRM)? A Comprehensive Guide to
2023年10月3日 Unveiling the Vertical Roller Mill In the everevolving world of industrial machinery, vertical roller mills (VRMs) have gained immense popularity for their efficiency and versatility This powerful milling machine is used across various industries, including cement, mining, and chemicals, to grind raw materials and achieve finely ground products