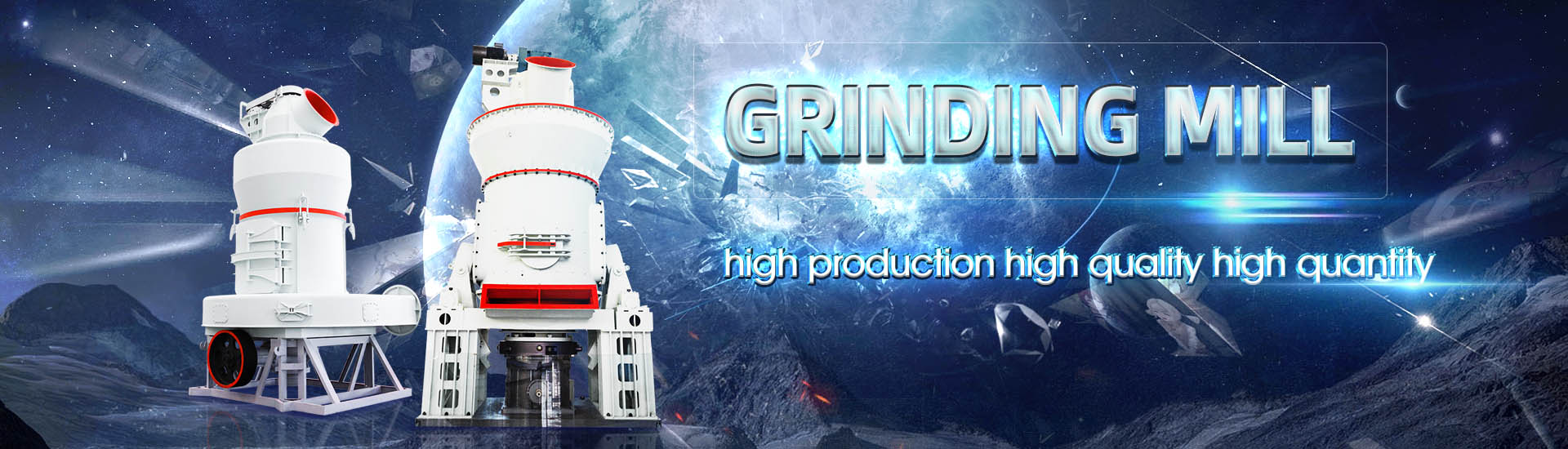
Sponge iron oxide crushing equipment
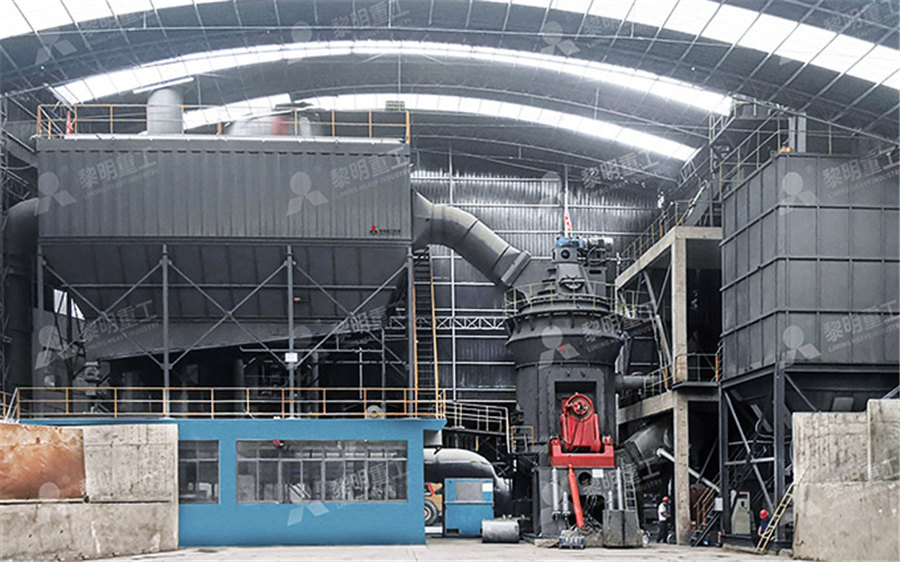
Sponge Iron Plant(DRI)Henan Dajia Mining Machinery Co, Ltd
Sponge iron is a metallic product produced through direct reduction of iron ore in the solid state It is a substitute for scrap and is mainly used in making steel through the secondary route The DRI, also known as Sponge Iron, is the product of the direct reduction of iron ore or other ironbearing materials while in the solid state, ie without melting, using “reducing agents” carbon Hot Briquetted Iron (HBI): A Guide to Shipping, Handling StorageIndia is the largest producer of direct reduction of iron (DRI), popularly known as sponge iron and accounted for about 393% of the global production in 2020 India’s growing economy will ENERGYEFFICIENT TECHNOLOGY OPTIONS FOR DIRECT DRI, also known as sponge iron, is the product of reducing iron oxide in the form of iron ore and steel plant wastes into metallic iron, below the melting point of iron and typically in the range of Sponge Iron an overview ScienceDirect Topics
.jpg)
Iron Ore Pelletizing Process: An Overview IntechOpen
The iron ore pelletizing process consists of three main steps: 1 Pelletizing feed preparation and mixing: the raw material (iron ore concentrate, additives anthracite, dolomite and binders are Iron Sponge is most frequently supplied with 15 pounds of iron oxide per bushel of product Iron Sponge, which has been used for many years to treat other gas streams, is a very simple way to remove the corrosive, bad smelling H2S It Iron Sponge Connelly GPM IncDirect reduction refers to solidstate processes which reduce iron oxides to metallic iron at temperatures below the melting point of iron Reduced iron derives its name from these processes, one example being heating iron ore in a Direct reduced iron WikipediaThe H2SPlus™ System approach to dryscrubbing uses longproven, lowcost iron oxide coated media (iron sponge) that MV Technologies has enriched with select bacteria and complemented with a system designed to extend media H2SPlusTM Systems MV Technologies
.jpg)
Sponge Iron (DRI) Rotary KilnCalcining EquipmentHenan
Sponge Iron (DRI) Rotary Kiln Specification: Φ14×33Φ60×95 Processing capacity: 1002000TPD Applied material: Iron Ore, Mill Scale, Concentrated Iron Powder Application: Steel industry, chemical industry, mining industryDRI, also known as Sponge Iron, is the product of the direct redu or other ironction of iron orebearing materials while in the solid state, ie without melting, using “reducing agents” carbon monoxide and hydrogen, derived from reformed natural gas, syngas or coal It is a porous iron material which, due to itsHot Briquetted Iron (HBI): A Guide to Shipping, Handling StorageThe major Raw Materials required for production of Sponge Iron by the rotary kiln process are: sized graded Iron Ore and NonCoking coal The carbon monoxide (co) produced as above reduces iron oxide to metallic iron Fe2o3 + 3 CO > 2Fe + 3 Co2 However, Iron ore crushing is not required since sized material has to beSPONGE IRON PLANT2013年3月16日 One is in metallic form which is known as metallic iron, Fe (M), and the second form of iron which is present in residual iron oxides, Fe (O) The total iron, Fe (T), in DRI is the sum of these two iron components Metallic iron is the aggregate quantity of iron, either free or combined with carbon (as cementite) present in DRIDirect Reduced Iron and its Production Processes – IspatGuru
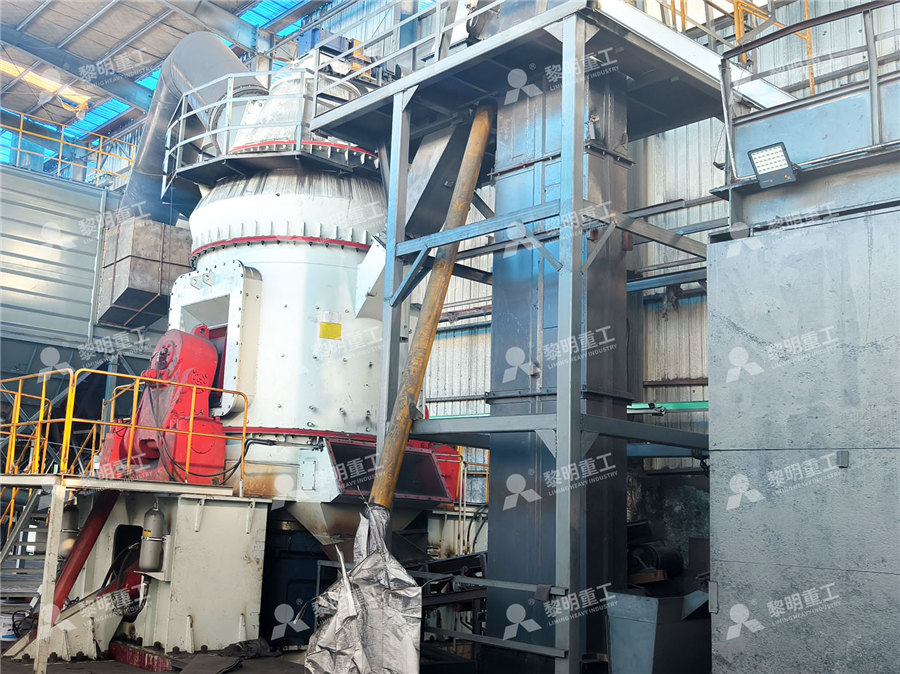
(PDF) Environmental performance evaluation of sponge iron
2016年10月1日 The direct reduced iron (DRI) production in India deserves special attention not only because the country is the largest producer of direct reduced iron but also because production is primarily Direct reduction refers to solidstate processes which reduce iron oxides to metallic iron at temperatures below the melting point of iron Reduced iron derives its name from these processes, one example being heating iron ore in a furnace at a high temperature of 800 to 1,200 °C (1,470 to 2,190 °F) in the presence of the reducing gas syngas , a mixture of hydrogen and Direct reduced iron WikipediaSPONGE IRON PLANT Iron ore crushing is not required since sized material has to be purchased Iron ore of size 5 mm to 20 mm is being used for the production of Sponge iron Iron ore is being fed to the Ground hopper, from where it conveyed to the Screen with the help of Vibro Feeder, where Oversize ie + 20 mm and Undersize ie – 5 Read Moreyield calculation of iron ore for sponge iron2020年3月3日 Sponge iron means porous iron produced by direct reduction processDirect reduction (DR) process is a solidstate reaction process (ie solid–solid or solid–gas reaction) by which removable oxygen is removed from the iron ore, using coal or reformed natural gas as reductants, below the melting and fusion point of the lump ore or agglomerates of fine ore []Sponge Iron SpringerLink

Iron Sponge Process Oil and Gas Separator
Several grades of treated wood chips are available, based on iron oxide content The most common grades are 65, 90, 150, and 20lb iron oxide/bushel The chips are contained in a vessel, and sour gas flows through the bed and reacts with the ferric oxide Figure 73 shows a typical vessel for the iron sponge processscales, etc) → Drying → Magnetic Separation → Crushing → Sieving → Canning → Entering Primary Reduction Furnace → Sponge Iron The secondary procedure includes: Sponge Iron→ Brushing → Magnetic Separation → Entering Secondary reduction furnace → becoming powder lump → crushing → magnetic separationReduced Iron Powder Sponge Iron Powder CNPC Powder2018年6月22日 Iron sponge (iron oxidized onto wood shavings) uses a simple packed tower (3) on a flowthrough support (4) After liquid separation (1), the deflected (2) sour gas flows down to contact with the reactive iron oxide, IRON SPONGE Process by ConnellyGPMVandana Global is a leading sponge iron manufacturer that empowering India since 1996, registered in Mumbai and working from Raipur, Chhattisgarh Sponge iron is the product of reducing iron oxide in the form of iron ore and steel plant Sponge Iron Manufacturer in India Vandana Global
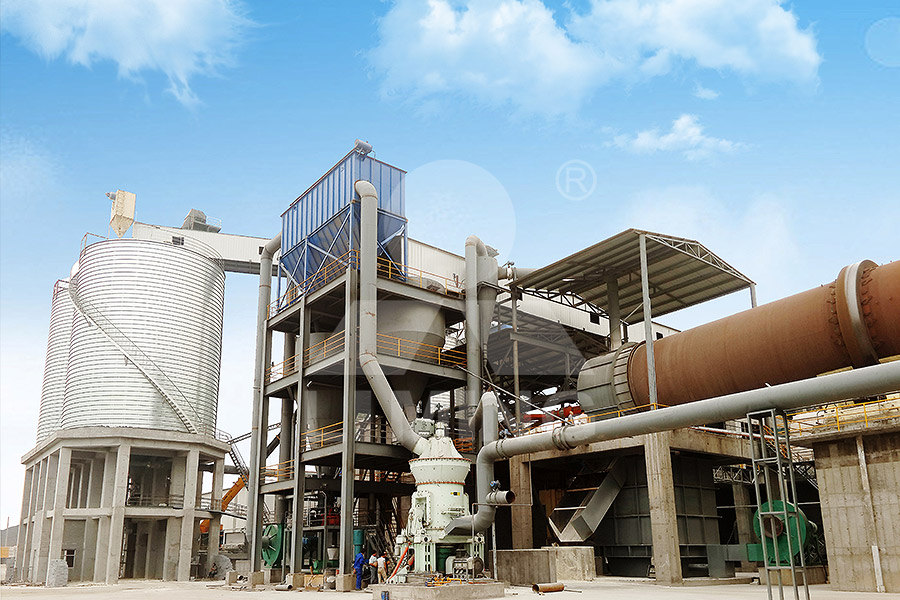
LECTURE NOTES ON Sponge Iron Ferro Alloys KIIT Polytechnic
Sponge Iron Ferro Alloys 2 CONTENTS SlNo Chapter Name Page No 1 Review of sponge iron making process 313 2 Thermodynamics of Sponge Iron making 1418 3 Parameters of Sponge Iron making 1925 4 Plant operating parameter 2630 5 Environmental management in DRI 31年4月7日 5 5 Iron ore crushing is not required since sized material has to be purchased Iron ore of size 5 mm to 20 mm is being used for the production of Sponge iron Iron ore is being fed to the Ground hopper, from where it conveyed to the Screen with the help of Vibro Feeder, where Oversize ie + 20 mm and Undersize ie – 5 mm is being removed by screeningSponge Iron Plantpdf Free Download SlideShareSponge Iron Free download as PDF File (pdf), Text File (txt) or read online for free The document discusses reoxidation of sponge iron, which is an exothermic process caused by the removal of hydrogen from sponge iron Sponge iron is produced through the direct reduction of iron ore using reducing gases like carbon monoxide and hydrogenSponge Iron PDF Iron Ore Scribd2020年1月1日 The sponge market did not expand as much as some producers had expected While the production of aerospacegrade sponge is secure in the US, lower grade materials can still be used for alloying work in stainless steels and nonaerospace markets; this has suppressed the price margins that US producers can achieve, resulting in the closing of all US producers The Kroll process and production of titanium sponge
.jpg)
Crushing and Screening Plant for Activated Carbon Plant AGICO
The crushing and screening plant is designed to remove impurities and select qualified sizes and improve the quality of activated carbon, it is generally set after carbonization section or activation section of activated carbon plant The activated carbon crushing and screening equipment is a set of product grading equipment that crushes and grades activated carbon particles based on Calcining Equipment Drying Equipment Grinding Equipment Crushing Equipment Beneficiation Equipment Rotary Kiln Case Rotary Dryer Case Ball Mill Case Hongke News Industry News Tel:+86 Email: chinarotarykiln@163Rotary Kiln, Rotary Dryer, Ball Mill, Stone CrusherHenan Hongke 2012年4月1日 At present, the process of deoiling, drying and crushing is needed when iron oxide scale is used for dephosphorization of molten iron 4) , and the cost will increase when the dosage is high Production of sponge iron powder by reduction of rolling mill scale2023年10月31日 Turkey’s iron ores may be used to manufacture sponge iron, and the country’s coal resources, which are plentiful despite being of poor quality, can be used as a reducing agentOptimization of sponge iron (direct reduced iron) production
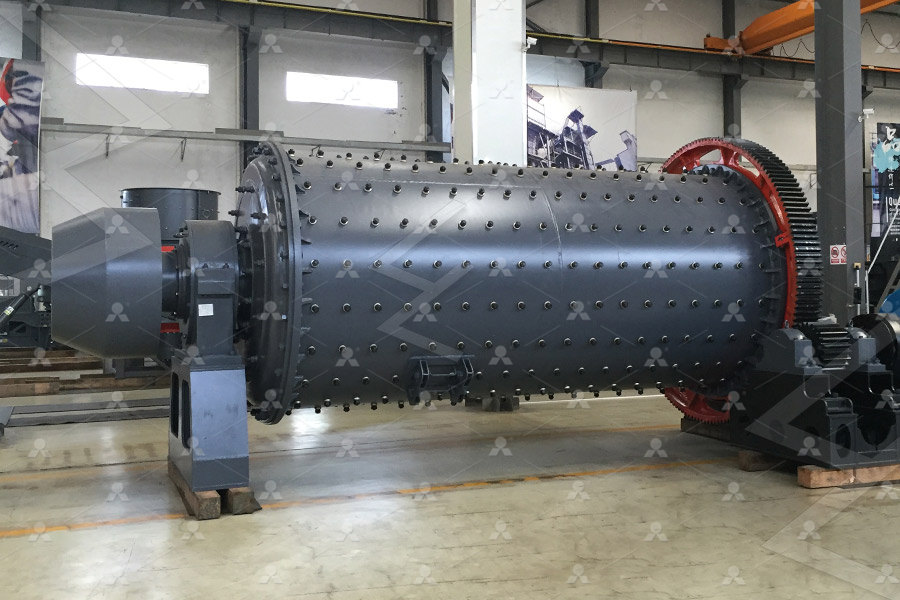
Sponge Iron aramico
Although iron powder could be produced in sponge iron tunnel kiln production line and it is the main raw material for powder metallurgy production lines Process In sponge iron production plant by tunnel kiln method, after crushing and 2016年3月30日 In book: Encyclopedia of Iron, Steel, and Their Alloys (pppp 10821108) Chapter: i) Direct Reduced Iron: Production; Publisher: CRC Press, Taylor and Francis Group, New York(PDF) i) Direct Reduced Iron: Production2023年10月31日 Amount of Reduced Oxide Iron in Sponge Iron Amount of Oxide iron in Feed Pellets * 100 [13] The reduction (sponge iron production) experiments carried out within the scope of the study by using BoxWilson experimental design Proper optimization was made for the parameters effective in the reduction In this context, independent parameOptimization of sponge iron (direct reduced iron) production42 Iron Ores and Iron Oxide Materials ISO 4700 Determination of the crushing strength The balling equipment that can be either a disc or a drum produces green pellets in a variable size distribution 31 Balling disc or disc pelletizer Figure 3 schematically shows a Iron Ore Pelletizing Process: An Overview IntechOpen
.jpg)
New Sponge Iron Rotary Kiln Design In Sponge Iron
Sponge iron rotary kiln is professional equipment for smelting sponge iron 1 Sponge iron rotary kiln 2 Central burner system 3 Cooling rotary kiln 4 Crushing magnetic separation system 5 Warehouse 6 Metering pneumatic conveying device 7 Mingled storehouse 8 Air supply Rotary Kiln For Magnesium Oxide Bauxite Rotary Kiln41 Direct Reduction of Iron Production Using Solid Coal 39 42 Direct Reduction of Iron Production Using Coal Gasification 43 43 Direct Reduction of Iron Production Using Gas Route 49 44 Hydrogen Use in Indian Iron and Steel Sector 54 50 Conclusion 57 Technology Vendors – Energyefficient Equipment and Systems 60 References 65ENERGYEFFICIENT TECHNOLOGY OPTIONS FOR DIRECT REDUCTION OF IRON 1994年9月1日 The iron sponge technique originated in Europe more than 100 years ago, and the earliest operators used a naturally occurring form of hydrated iron oxide known as bog iron or bog ore As refinements were made in the process, it was found that more efficient sulfur removal could be attained by uniformly distributing the iron oxide hydrate across a substrate, and that After more than a century, iron sponge still soaks up hydrogen Ore Dressing Equipment; Calcining Equipment; Crushing Screening Equipment; Construction Machinery Equipment; Ball Mill Capacity: Zinc Oxide Rotary Kiln Model: Ø25×30mØ30×60m Capacity: 160850TPD Dri Sponge Iron Rotary Kiln Model: Φ22x38m Crushing Screening Equipment Zoomjo Group
.jpg)
Iron Processing Equipment, Process Flow, Cases JXSC Machine
2019年8月23日 Jaw crusher reduces the hard iron ore into a smaller size, it has a high iron crushing ratio, feeding and crushing capacity, uniform texture, good grain shape Ball mill is the key equipment for grinding iron ore particles after crushing The purpose is to achieve sufficient dissociation of useful minerals to achieve a better beneficiation effectDirect reduction iron or sponge iron is an old method for producing hydrogen (Milne et al, 2006; Peña et al, 2010; Biljetina and Tarman, 1981) that was replaced by more efficient and economic processesRecently, the interest in sponge iron as a hydrogen production process has grown again, although the technology still has some major technical and economic challenges to Sponge Iron an overview ScienceDirect TopicsIs Maintenance Necessary With a BAM Iron Sponge System or Solution? At times, routine maintenance may be necessary to preserve and extend the lifespan of your BAM iron sponge system Ongoing maintenance can help H2S Removal Media MV Technologiesmm (for sponge iron) and fines (10/6 mm) products • It involves multistage crushing and screening operation using Gyratory and/or cone crusher as prime equipmentCURRENT PRACTICES IN INDIAN IRON ORE BENEFICIATION
.jpg)
Chapter 1 Review of Sponge Iron Making Process Historical
associated with iron ore as oxide removed from the particle is known as percentage reduction whereas the percent of iron as part of whole iron existing as metallic iron is called as degree of metallization in sponge iron technology Sponge Iron Making Process(Coal Based) KruppRenn Process : The KruppRenn process was developed in 1930exposed to heat and reducing atmosphere The reduction from iron oxide to iron occurs by a gradual removal of oxygen at various temperatures under the controlled reducing atmosphere giving rise to various intermediate oxides Hot sponge iron is discharged from the kilndischarge end and taken into the rotary cooler The sponge iron after EIA/EMP Report of M/s Bravo Sponge Iron Pvt Ltd At: Mahuda, 2023年10月9日 A gas is used as reductant to reduce iron oxides into iron metal in certain temperature or experiences passivation If sponge iron is used in steelmaking, low energy consumption (105 GJ per ton of sponge iron), high yield, high quality, and serialized equipment The maximum output of single plant is 2,750,000 t/a nowDirect Reduction Ironmaking SpringerLink2019年6月4日 Data1 includes temperatures profiles and air inlet at positions, AT1 to AT3 and MF1 and MF2, inside the kiln whereas, flow rates of iron ore, feed coal, slinger coal and sponge iron is (PDF) Operation of CoalBased Sponge Iron Rotary Kiln to Reduce
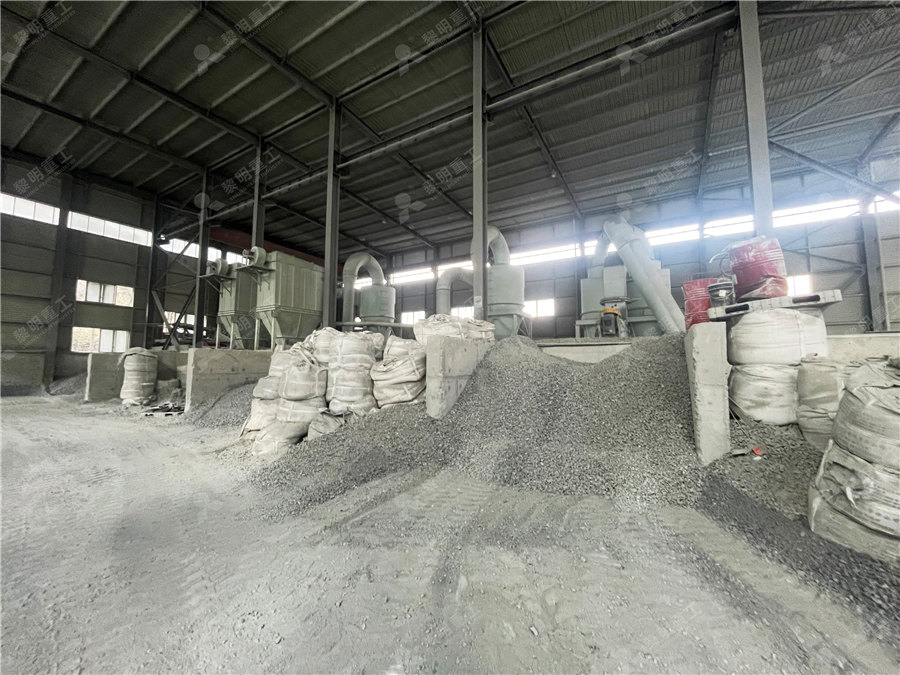
MV Technologies Iron Sponge H2S Scrubber Newtrient
Their systems minimize maintenance costs for downstream equipment; help prepare gas utilization for renewable energy; enable air emissions compliance and eliminate odor MV Technologies designs both iron sponge based (H2SPlus™ Systems) and granular iron oxide based (SulfAx® Systems) for removal of hydrogen sulfide (H 2 S) from biogasSponge iron and critical minerals are future products we are developing in the transformation towards carbon free production Iron ore The iron ore we extract is our main raw material and consists of magnetite, a greyblack iron oxide, We are a leading supplier in sustainable and qualityconscious concrete production, rock work and crushingOur products and services LKAB2013年2月23日 Recrystallization of iron oxides is essentially a physical process in which smaller particles consolidate into larger ones with the loss of surface energy During the recrystallization of iron oxides, continued growth of iron oxide crystals imparts sufficient strength During the process, the grain growth for hematite starts at around 1100 deg CIntroduction to Iron ore Pellets and Pelletizing processes2024年10月4日 Further, it is melted at 1100° C which produces sponge iron Let’s understand indepth the uses and applications of sponge iron, the production process, plants and more Sponge iron plants in India Since the year 2002, India has become the largest producer of sponge iron worldwide and 20% of the sponge iron is produced by India itselfSponge iron: Uses, process formula, iron plant, and more Tata