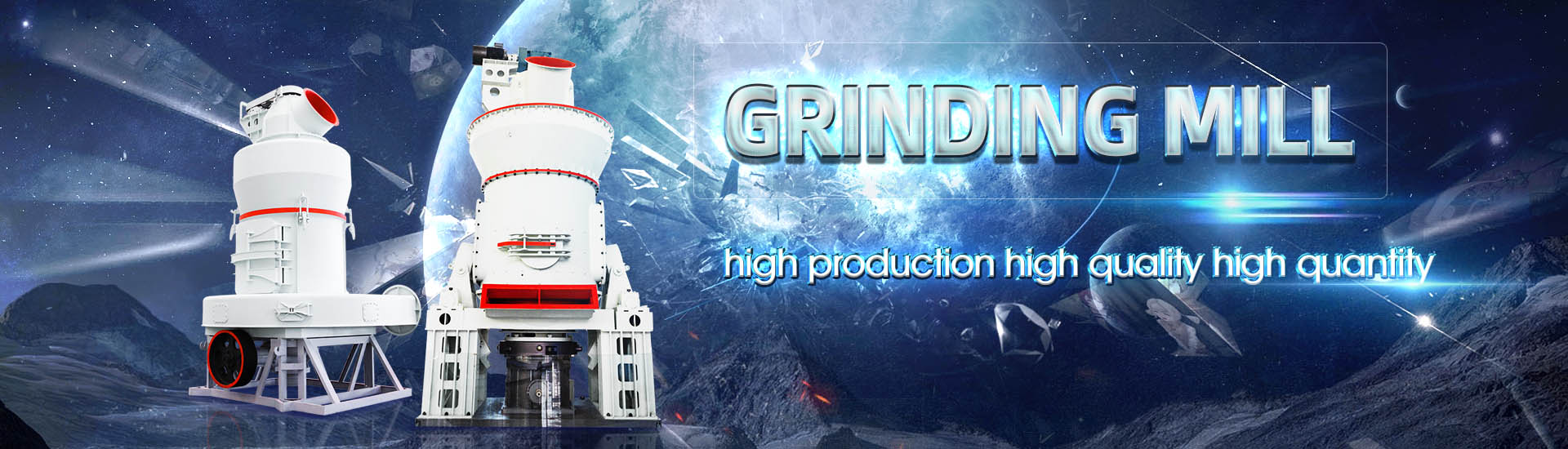
Removing silicon impurities during ironmaking
.jpg)
Removal of Silicon, Aluminum and Phosphorus Impurities from
In this paper, the removal processes for silicon (Si), aluminum (Al) and phosphorus (P) impurities from lowgrade iron ore, in which hematite (Fe2O3), goethite (FeO(OH)), and quartz (SiO2) are the main mineral constituents, have been presented The reverse froth flotation process was 2016年9月1日 In this paper the beneficiation methods for removing SiO2, P and S are presented, including flotation, and the parameters that need to be considered in the design of beneficiation plants are REMOVING IMPURITIES FROM IRON ORES: METHODS 2024年2月1日 This paper studies the removal of impurities in refined silicon through slagmaking experiments with different slag system compositions, different slagtosilicon ratios and refining Removal of impurities from Metallurgical silicon by adding ZnO 2024年7月3日 This study introduces a method for removing iron and aluminum impurities from silicon ore The silicon ore samples were analyzed through Xray diffraction, scanning electron Study on the Purification Mechanism of LowGrade Silicon Ore
.jpg)
Removing Impurities from Iron Ores: Methods and Industrial Cases
2016年1月1日 In this paper the beneficiation methods for removing SiO2, P and S are presented, including flotation, and the parameters that need to be considered in the design of 2021年5月1日 Hydrometallurgy techniques for impurities removal from MGSi are firstly reviewed Various traditional and intensive leaching methods are summarized and compared A review of hydrometallurgy techniques for the removal of 2018年6月1日 In this study, a novel metal assisted chemical leaching (MACL) was proposed to remove impurities from metallurgical grade silicon (MGSi) HF acid leaching, one step MACL Removal of impurities from metallurgical grade silicon with metal 2018年9月10日 Silicon and ironrich phases are two main detrimental impurities in coarse AlSi alloy, and they can be simultaneously removed by adding Mn under the electromagnetic field Simultaneous Removal of Silicon and IronRich Phases from
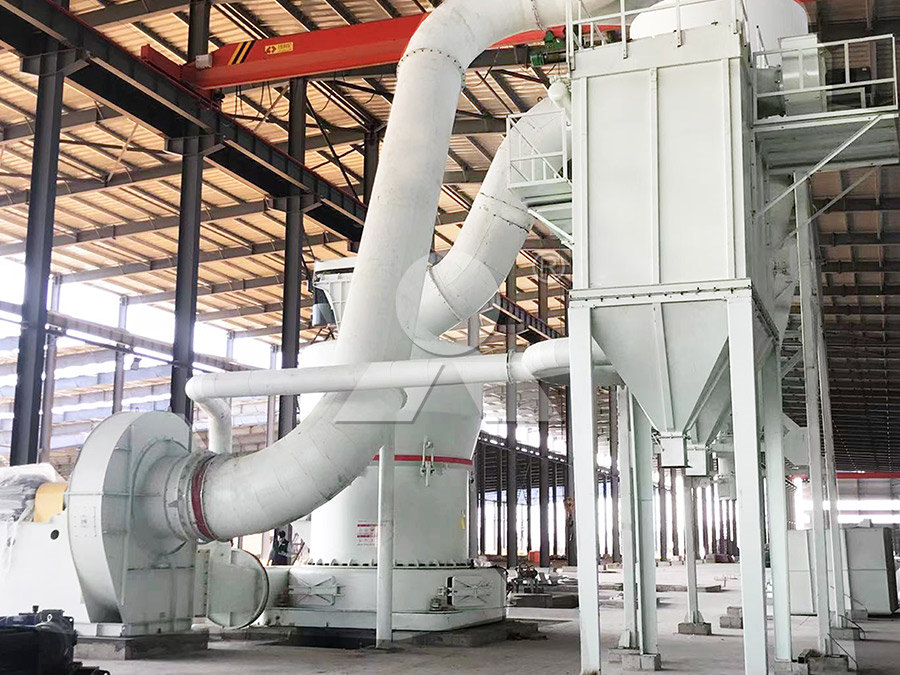
Impurities Removal from MetallurgicalGrade Silicon by Combined
2013年4月26日 The purification of metallurgicalgrade silicon (MGSi) by combined solvent refining processes has been studied The final highpurity silicon was recovered through SnSi 2022年2月13日 Silicon [Si] in hot metal is an impurity acting in the steel shop as an energy source that is released by oxidation during oxygen blowing in the converter Preferred silicon Silicon in hot metal from a blast furnace, the role of FeO: 2017年10月10日 Ironmaking Blast Furnace Iron is made by reacting iron ore (iron oxide and impurities), coke (a reductant) and limestone (CaCO 3) in a blast furnace Iron ores with lower iron content such as taconite are first processed Ironmaking 101 – From Ore to Iron with Blast FurnacesThis page titled 33B: General Procedures for Removing Impurities is shared under a CC BYNCND 40 license and was authored, remixed, and/or curated by Lisa Nichols via source content that was edited to the style and standards of 33B: General Procedures for Removing Impurities
.jpg)
Ironmaking Process an overview ScienceDirect Topics
Using the same steammethane reformer, the 1step ironmaking process was constructed and simulated in the cases in which (1) hydrogen was first produced and (2) syngas from the SMR process was directly fed to the ironmaking process The ironmaking reactor operating at 1500 °C with an excess driving force of 05 was used as the standard caseDeveloped in the mid20th century, the LD process involved blowing oxygen through molten pig iron to reduce impurities and control alloy composition, resulting in highquality steel Contemporary Ironmaking Techniques: As we step into the 21st century, ironmaking continues to evolve with an emphasis on sustainability and technological innovationEvolution of Ironmaking Techniques From Ancient to Modern 2020年7月15日 Currently, approximately 95% of hot metal is produced by the blast furnace ironmaking process, which is also predicted to be the largest single ironmaking process until 2050 because of its advantages in production cost and efficiency Therefore, replacing fossilbased fuels with H 2 as the reductant is expected to relieve environmental concerns and, Blast Furnace Ironmaking an overview ScienceDirect Topicswhere sulphur can be removed: in the blast furnace (BF), during hot metal (HM) pretreatment, in the converter and during the secondary metallurgy (SM) treatment For sulphur removal a low oxygen activity and a basic slag are required In the BF typically 90% of the sulphur is removed; still, the HM contains about 003% of sulphurSulphur removal in ironmaking and oxygen steelmaking
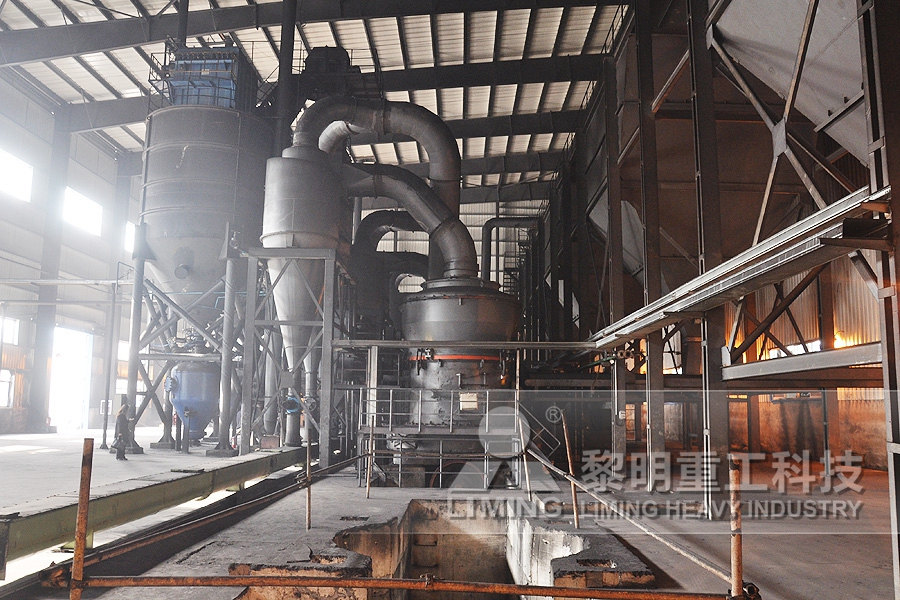
CNA Method for removing iron and silicon impurities during
The invention relates to a method for removing iron and silicon impurities during the regeneration of aluminum scraps, belonging to the field of impurity removal during the regeneration and recovery of nonferrous metals The method comprises the steps of putting 2030% of borax, 2030% of manganese chloride, 1020% of calcium chloride, 1020% of calcium oxide, 510% of 2021年3月2日 This paper reviews the effects of Pb and Zn impurities and their removal in the ironmaking process The phase changes during ironmaking were investigated, along with the removal techniques of such impurities and their environmental impact Results show that distribution of Pb–Zn–Fe in Fe ore is complicated, the particles are fine, and the removal of Effect of Lead and Zinc Impurities in Ironmaking and the MDPIMetals 2024 2 = in Reduction Ironmaking Process ResearchGate2024年1月1日 The iron ore in the mine is processed as the ironmaking raw materials required for blast furnace ironmaking through crushing, sieving, mineral processing, agglomerating, and blending Then, coke, ironmaking raw materials, and flux are loaded into the blast furnace according to a certain proportion, and the hot air is blasted from its lower tuyereIronmaking SpringerLink
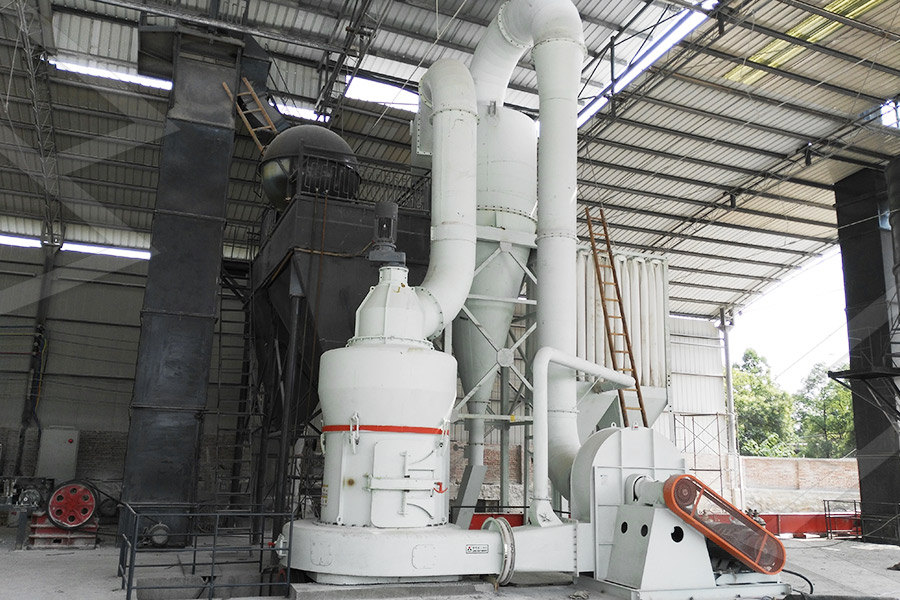
Ironmaking 101 – From Ore to Iron with Smelting and
2017年10月17日 Smelting Reduction Figure 2: The smelt reduction vessel (SRV) is the core technology component of the Hismelt process Source: RioTinto While years of ironmaking technology innovations have optimized blast 2024年11月4日 Limestone (calcium carbonate) is added to the furnace to remove impurities in the ore The calcium carbonate in the limestone thermally decomposes to form calcium oxide calcium carbonate → calcium oxide + Extraction of iron IGCSE Chemistry Revision Notes2021年3月9日 The burden charging operation in blast furnace is one of the most important operations during ironmaking process In this paper, we focus on the study of precise burden charging operation, which (PDF) Precise Burden Charging Operation During Iron The molten iron has a dissolved carbon content of approximately 36% as well as some silicon, manganese, vanadium, and titanium Slag, which floats on top of the iron, has the function of removing impurities from the iron and its chemical composition and temperature to a large extent determine the chemistry and hence quality of the ironThe Ironmaking Process New Zealand Steel
.jpg)
Distribution Behavior of Impurities during the Hydrogen
2024年6月17日 The traditional blast furnace ironmaking process is the most widely used ironmaking process globally, yet it is associated with significant drawbacks, including high energy consumption and carbon emissions To achieve lowcarbon ironmaking, researchers have developed hydrogen ironmaking, which is capable of achieving lower CO2 emissions 2014年1月1日 Silicon is one of the main impurities in the hot metal to be removed in steel converter, which should be controlled at the level of about 05%, but normally in the range of 03–09% in the hot metal Silicon content in the hot metal is used as the measure of thermal state of the hearth, due to the strong endothermic nature of the SiO 2 reductionIronmaking ScienceDirect2024年6月17日 of impurities during the hydrogen ironmaking process and to explore ef fective methods for enhancing iron purity Therefore, based on the optimization of slag properties andDistribution Behavior of Impurities during the Hydrogen 2021年5月1日 Conversely, these impurities replace the silicon atoms and occupy interstitial positions For these reasons, the insoluble impurities cannot be completely exposed during the grinding process Therefore, it is more difficult to remove insoluble impurities from MGSi than segregation impuritiesA review of hydrometallurgy techniques for the removal of impurities
.jpg)
Steelmaking SpringerLink
2024年1月1日 The removal of harmful impurities, such as silicon and phosphorus, is carried out by making basic slag before decarbonization and at a lower molten pool temperature When silicon, phosphorus, carbon, iron, and other elements are oxidized and exothermic, the temperature of the molten pool rises, entering the main decarbonization period2010年11月1日 The FeO content was between 1077 and 39 19 Assis et al [27] proposed, in 2012, the following formula This equation was derived from the revision of the Suito correlation [25] using Thermodynamics of Phosphorus and Sulphur Removal during 2024年4月1日 Carbon mineralization technology has emerged as a promising method for permanently sequestering CO 2 by transforming it into a thermodynamically stable solid carbonate material Recently, alkaline industrial waste, particularly from steel and ironmaking processes, has been identified as a proper feedstock due to its high potential for CO 2 storage and the Carbon mineralization of steel and ironmaking slag: Paving the Abstract This chapter begins our development of an a priori mathematical description of steadystate blast furnace smelting The ultimate objective is to provide equations that can be used to: 1 calculate the quantities of coke and blast air that are required to successfully produce 1500°C molten iron from any given ore;Blast Furnace Ironmaking ScienceDirect
.jpg)
Removal of Impurities from Metallurgical Grade Silicon During
Silicon (2017) 9:77–83 DOI 101007/s1263301492690 ORIGINAL PAPER Removal of Impurities from Metallurgical Grade Silicon During GaSi Solvent Refining Jingwei Li Boyuan Ban Yanlei Li 2022年2月13日 Silicon [Si] in hot metal is an impurity acting in the steel shop as an energy source that is released by oxidation during oxygen blowing in the converter Preferred silicon concentration in hot steel is typically 04 wt% (± 01 wt%), Silicon in hot metal from a blast furnace, the role of FeO: Ironmaking Sulphur removal in the ironmaking and oxygen steelmaking process is reviewed A sulphur balance is made for the steelmaking process of Tata Steel IJmuiden, the Netherlands There are four stages where sulphur can be removed: in the blast furnace (BF), during hot metal (HM) pretreatment, in the converter and during the secondary metallurgy (SM Sulphur removal in ironmaking and oxygen steelmaking2022年4月12日 In this paper, the removal processes for silicon (Si), aluminum (Al) and phosphorus (P) impurities from lowgrade iron ore, in which hematite (Fe2O3), goethite (FeO(OH)), and quartz (SiO2) are the Removal of Silicon, Aluminum and Phosphorus Impurities from
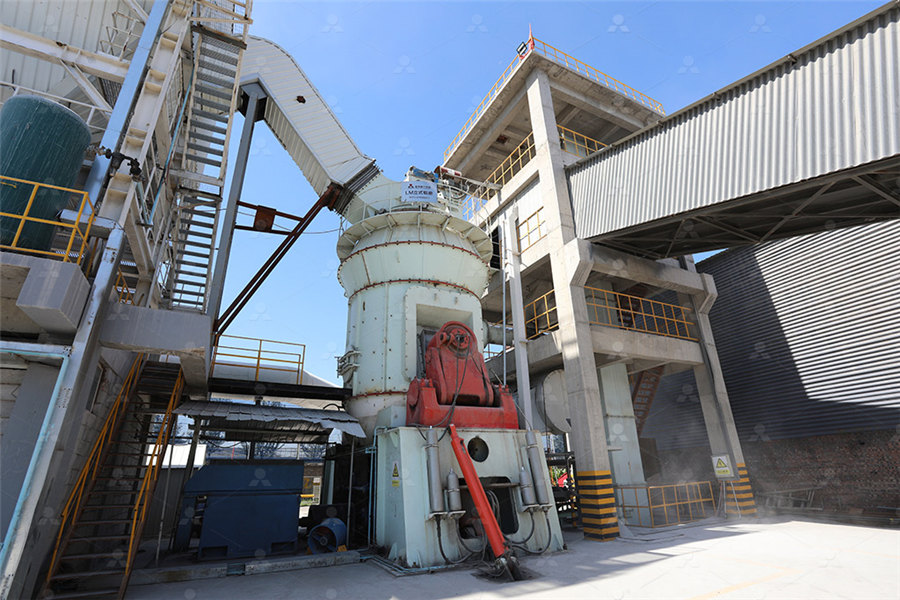
A REVIEW OF IRONMAKING BY DIRECT REDUCTION PROCESSES:
2023年11月10日 During the last four decades, a new route of ironmaking has rapidly developed for Direct Reduction (DR) of iron ore to metallic iron by using noncoking coal/natural gas This product is known as Steel mill with two arc furnaces Steelmaking is the process of producing steel from iron ore and/or scrapIn steelmaking, impurities such as nitrogen, silicon, phosphorus, sulfur, and excess carbon (the most important impurity) are removed from the sourced iron, and alloying elements such as manganese, nickel, chromium, carbon, and vanadium are added to produce different Steelmaking Wikipedia2018年9月10日 Coarse AlSi alloy is produced from bauxite via carbon electrothermal reduction method Silicon and ironrich phases are two main detrimental impurities in coarse AlSi alloy, and they can be simultaneously removed by adding Mn under the electromagnetic field We focus on the influence of different Mn additions, dropping rates, and current intensity on the Simultaneous Removal of Silicon and IronRich Phases fromMines worldwide extract these ores, which are then processed to remove impurities and enhance iron content Advanced beneficiation techniques such as magnetic separation and froth flotation ensure that highgrade iron ore feeds into the ironmaking process, optimizing efficiency and product quality 2From Ore to Alloy: Navigating Ironmaking in Modern Steel
.jpg)
Desphosphorization in ironmaking and oxygen
2018年1月1日 All figure content in this area was uploaded by VilleValtteri Visuri2003年1月1日 As one of sequential purification processes where high purity silicon for solar grade silicon (SOGSi) was manufactured by removing impurities from metallurgical grade silicon (MGSi), a Removal of Metal Impurities in Molten Silicon by Directional 2003年10月1日 An industrialscale pyrometallurgical method of removing metallic impurities from metallurgical grade silicon (MGSi) was developed as an element technology in a sequential purification process for manufacturing highpurity silicon for solar grade silicon (SOGSi) by segregation of metallic impurities during solidification Metallic impurities were removed from Removal of Metal Impurities in Molten Silicon by Directional where sulphur can be removed: in the blast furnace (BF), during hot metal (HM) pretreatment, in the converter and during the secondary metallurgy (SM) treatment For sulphur removal a low oxygen activity and a basic slag are required In the BF typically 90% of the sulphur is removed; still, the HM contains about 003% of sulphurSulphur removal in ironmaking and oxygen steelmaking
.jpg)
Segregation and removal of transition metal impurities during
2019年10月15日 Therefore, it suggests that a combination of aqua regia and HF could be employed to efficiently remove transition metal impurities during Al–Si solvent refining Graphical abstract Download: Download highres image (256KB Effect of Ti addition on B removal during silicon refining in Al30%Si alloy directional solidification 2013年7月9日 The removal of impurities from metallurgical grade silicon using the O2 and H2OO2 gas blowing techniques was firstly studied by thermodynamics The relationships between the boron content in refined silicon and the equilibrium partial pressures of gaseous boride species were established, which shows a theoretical limitation for boron removal from metallurgical Impurities Removal From Metallurgical Grade Silicon Using Gas 2021年8月22日 In the BOF steelmaking process, lime quality and quantity directly affect slag quality, affecting metallurgical results, liquid metal yield, productivity, and therefore the total cost and Value in use of lime in BOF steelmaking process ResearchGate2021年5月1日 Hydrometallurgy is considered a promising method to produce solargrade silicon (SOGSi) from metallurgicalgrade silicon (MGSi) due to its advantages of low cost, simple operation, and easy control Researchers have investigated different hydrometallurgy techniques for impurity removal from MGSi This study systematically reviews hydrometallurgy A review of hydrometallurgy techniques for the removal of impurities
.jpg)
Novelty on deep reduction roasting through removal of lead and
2023年10月1日 Iron ore contains lead and zinc impurities, which combine to form complex ores that are challenging to purge at high temperatures These impurities reduce iron output [2], exerting a considerable effect on the lifespan of BFs and the advantages of ironmaking [8]They are simple to decrease or oxidise and have the potential to generate and produce zinc and