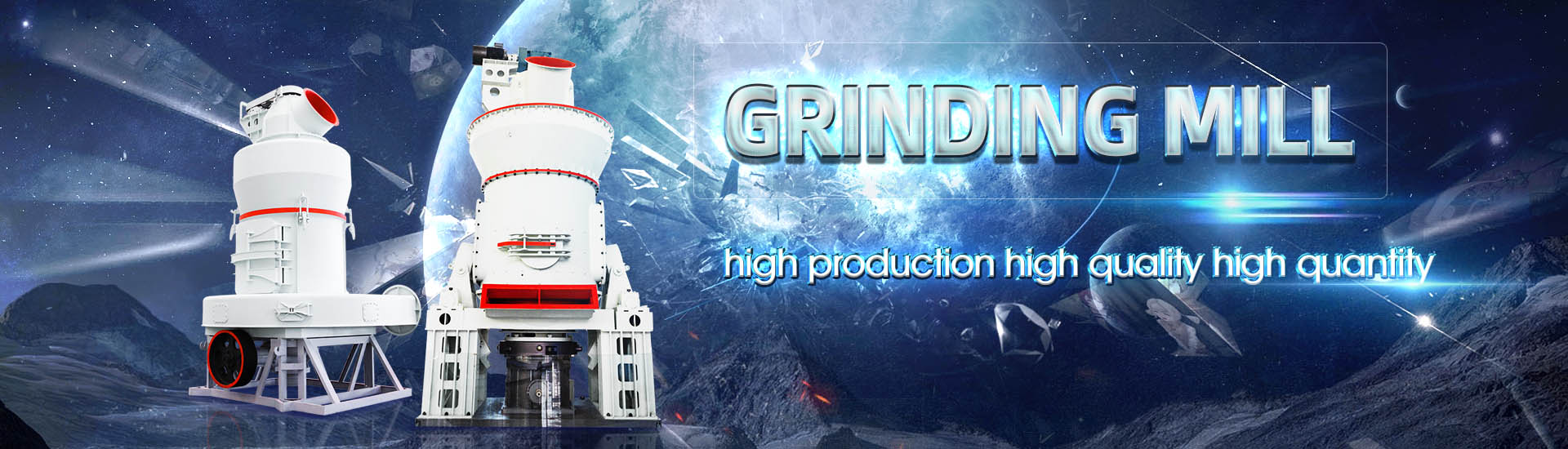
The principle of highefficiency bentonite mill
.jpg)
Optimization of bentonite clay mechanochemical activation using
2017年2月1日 Principal component analysis and analysis of variance were used in the observation of the influence of input variables (bentonite chemical composition) and process parameters (milling duration, rotor velocity) on the product characteristics: density, specific 2023年11月30日 This paper aims to provide an overview of the several organic modification methods of bentonite for drilling fluids It also evaluates the characteristics and application impacts of bentonite(PDF) Modification Method of HighEfficiency Organic The typical Raymond roller mill system is designed to dry, pulverize, classify and deliver a number of different products COST EFFICIENCY The Raymond roller mill provides efficient control of RAYMOND® ROLLER MILLS Thomasnet2023年7月4日 The highpressure roller mill, also called the roller presser or the extrusion mill, is a grinding equipment based on the principle of material layer crushingRoller Mill SpringerLink
.jpg)
Modification Method of HighEfficiency Organic
2023年11月30日 Organically modified bentonites effectively reduce the consumption of drilling fluids, conserve resources, and lessen environmental effects This paper aims to provide an overview of the several organic Ultrafine Vertical Mill is a highperformance grinding mill that can produce bentonite powder with a fineness of 3252500 mesh It has the advantages of low energy consumption, high efficiency, Types of Grinding Mills for Bentonite Processing PlantThe preparation of high quality bentonite, efficient milling equipment is an inevitable choice Guilin Hong Cheng has accumulated rich manufacturing experience in bentonite processing field, Working principle of drilling grade bentonite Vertical grinding mill2021年12月30日 In this study, a pintype vertical stirred media mill was used to perform the dry grinding of bentonite Grinding time and stirring speed were investigated for effect on the particle sizeDry Grinding of Bentonite by Stirred Media Mill
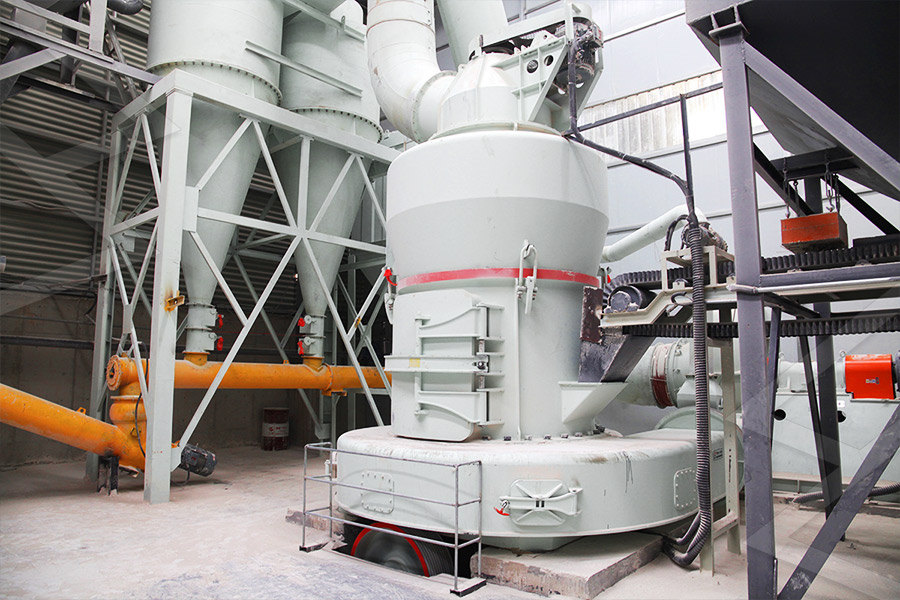
Roller mills: Precisely reducing particle size with greater efficiency
This article introduces roller mills and explains how they efficiently grind friable materials to a uniform final particle size while using relatively little energy2023年9月12日 The properties of the material being milled can impact the performance of the hammer mill Properties such as moisture content, density, and hardness can affect milling Materials with high moisture content can The Principle of Hammer Mill SinofudeBentonite has many advantages when used in coating, it is required to be ground by bentonite powder grinding mill into powders for diverse applications If you need bentonite mill, please let us know your requirements: News The Advantages of Bentonite in Coating IndustryWe take pleasure in an extremely fantastic standing among the our prospects for our great product top quality, competitive cost and the finest support for Gfg High Efficiency Fluidized Bed Dryer for Bentonite We adopt the business philosophy of quality, innovation, integrity and winwin For even more data, please do not be reluctant to call usGfg High Efficiency Fluidized Bed Dryer for Bentonite
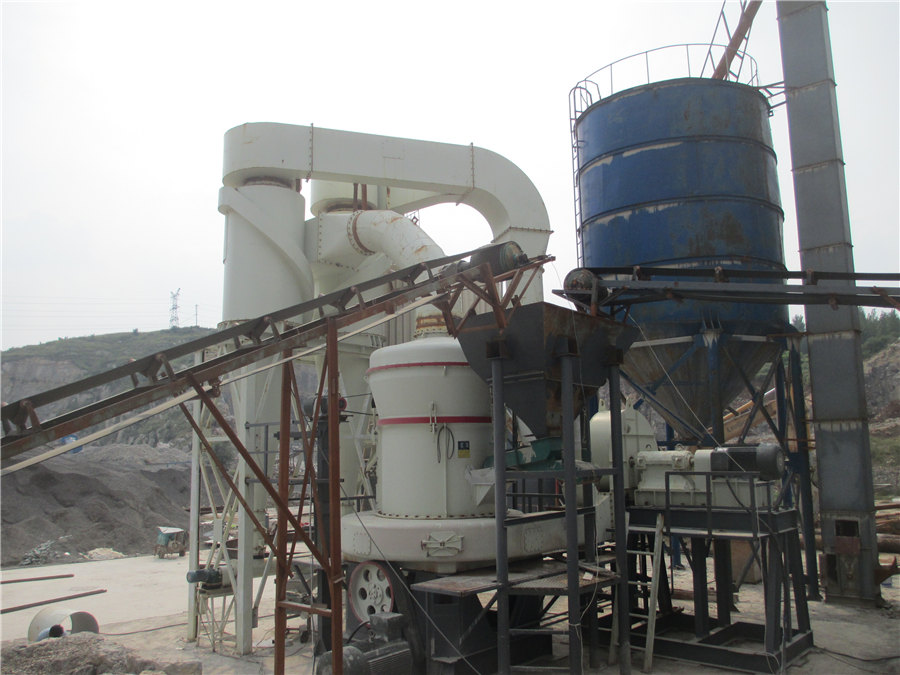
(PDF) Modification Method of HighEfficiency Organic Bentonite
2023年11月30日 Modification Method of HighEfficiency Organic Bentonite for Drilling Fluids: A Review November 2023; Molecules 28(23):7866; The reaction principle is as follows: Under the action of the 2024年4月22日 The equipment is developed for the properties of bentonite, with strong processing capacity and high powder production efficiency The vulnerable parts are cast with strong wearresistant materials, resulting in low wear during powdermaking operations, long service life of the entire machine, and low costBentonite Processing Plant And Grinding MachineStructure and Principle HC1700 pendulum grinding mill consists of main mill, constraint turbine classifier, pipe system, high pressure blower, double cyclone collector system, pulse air collector, feeder, electronic control motor, jaw crusher, pan elevator The main mill consists pedestal, return air box, shovel, roller, ring, hood cover and HC1700 Pendulum Grinding Mill HongCheng2013年1月1日 The return of 100400% of the ore mass to the mill typically reduces the retention time of the material inside the mill increasing the grinding capacity, improving the energy efficiency, resulting THE BENEFITS OF HIGH CLASSIFICATION EFFICIENCY IN CLOSED BALL MILL
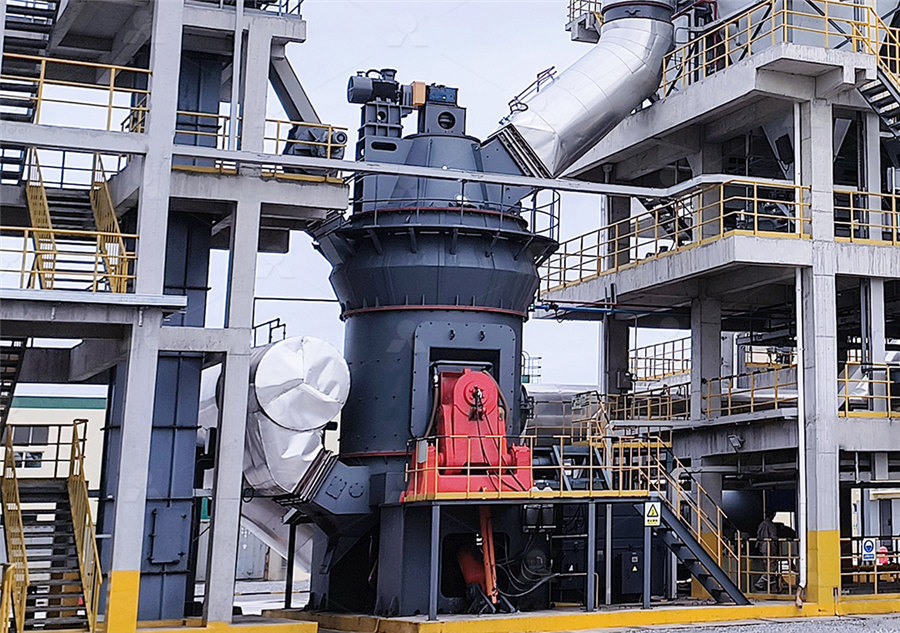
The working principle of ball mill Meetyou Carbide
2019年5月22日 When the rotation speed is high and the ball loading amount is large, the ball forms a drop type under the action of centrifugal force and starts rolling grinding b At this time, there is both a turning action and a mutual friction between the ball and the material (grinding action), so the mixing and grinding efficiency is highThe FDS60 nano sand mill features a new pintype grinding component design, ensuring high efficiency, substantial output, and low energy consumption Its compact length/diameter ratio and elevated energy density set it apart The incorporation of a highflux static centrifugal separation sieve with a sizable discharge area ensures that the grinding medium doesn't contact the High efficiency super fineness sand mill FDS60Download scientific diagram Working principle of the highefficiency rotor classifier from publication: CFDBased Structural Optimization of Rotor Cage for HighEfficiency Rotor Classifier Working principle of the highefficiency rotor classifier2017年10月26日 The same source of synergy found in Turner’s “optimized load” principle can also be applied to ball milling through suitable application of grinding mechanisms in conjunction with the other previously described factors that Factors Affecting Ball Mill Grinding Efficiency
.jpg)
What is Fluid Energy Mill? Working Principle,
Working Principle of Fluid Energy Mill Fluid energy mill is also known as jet mill It works on the principle of impact and interparticle attrition to achieve the desired particle size Construction of Fluid Energy Mill It consists of a grinding The operating principle of the colloid mill is that the fluid or semifluid material passes between the fixed teeth and the movable teeth that move relatively at high speed so that the material is subjected to a strong shearing force, friction What is the Principle of Colloid mills? Inox millWorking Principle of Raymond Mill(https://tinyurl/yyfurvvh) The Raymond mill is a threedimensional structure, which occupies a small area; The fineness Working Principle of Raymond MillXinhai Mineral Processing 2016年10月5日 In this chapter an introduction of widely applied energyefficient grinding technologies in cement grinding and description of the operating principles of the related equip‐ ments and comparisons over each other in terms of grinding efficiency, specific energy consumption, production capacity and cement quality are given A case study per‐ formed on a EnergyEfficient Technologies in Cement Grinding
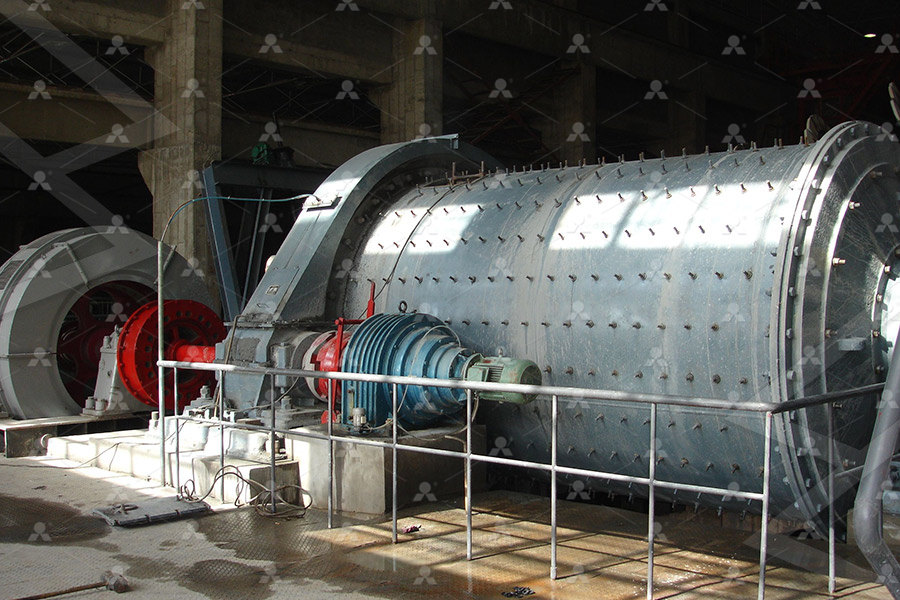
Types of Grinding Mills for Bentonite Processing Plant
Ultrafine Vertical Mill is a highperformance grinding mill that can produce bentonite powder with a fineness of 3252500 mesh It has the advantages of low energy consumption, high efficiency, and large capacity Ball Mill Ball Mill is a traditional grinding mill that can grind bentonite into powder with a wide range of particle sizes2023年10月26日 A review of HighPerformance Liquid Chromatography included an introduction, chromatographic terms, different classes, and types of HPLC techniquesReview of High Performance Liquid Chromatography and Its 2023年8月29日 The grinding media’s movement within the sand mill is attributed to the principle of centrifugal motion and shear Enhanced Dispersion Efficiency: Sand mills excel in achieving efficient particle dispersion due to the intense agitation and grinding action they Sand mill is a kind of highefficiency grinding equipment, Sand Mill: Enhancing the Efficiency of Grinding Dispersion2023年9月28日 A jet mill is a milling machine that uses highspeed compressed air or gas jets to impact particles and reduce their size It is commonly used in the pharmaceutical, chemical, and food industries for particle size reduction The purpose of a jet mill in particle size reduction is to finely grind and disperse solid materials into smaller particlesWorking principle of jet mill
.jpg)
Performance Benefits of Colloidally Mixed Two Component Grouts
The colloidal mill is capable of generating a maximum discharge pressure of 200 kPa Depending on the batch size of the mixer, there may be up to 4 of these mills operating in unison each with a throughput of up to 750 l/min (200 USgpm) It is possible to increase the mills efficiency as a pump (thus giving it a higher pressure capacity) butAGICO Cement provides vertical cement mill, vertical roller mill used for cement manufacturing, powerful grinding and homogenization, customdesign cement mill, onschedule delivery Skip to content +86 Vertical Cement Mill, Vertical Roller Mill Buy Cement 2015年10月23日 In this chapter an introduction of widely applied energyefficient grinding technologies in cement grinding and description of the operating principles of the related equipments and comparisons over each other in EnergyEfficient Technologies in Cement Grinding2024年9月4日 Phosphorus (P) discharge from anthropogenic sources, notably sewage effluent and agricultural runoff, significantly contributes to eutrophication in aquatic environments Stringent regulations have heightened the need for effective P removal technologies in wastewater treatment processes This paper provides a comprehensive review of current P A Review of the Efficiency of Phosphorus Removal and Recovery
.jpg)
Ball Mill Grinding Machines: Working Principle, Types, Parts
High Grinding Efficiency: The grinding mechanism of ball mills ensures effective comminution, resulting in high grinding efficiency and reduced processing time Easy Maintenance: Ball mills are relatively simple machines with fewer moving parts, making maintenance and Materials: Raymond mill grinds minerals like gypsum and limestone, while ball mill processes metal ores and cement clinker b Output: Raymond mill produces less than ball mill but uses less power c Dust pollution: Raymond mill has cleaner dust control, whereas ball mill is larger, harder to manage, and causes more dust pollution dHighefficient Raymond Mill Fote Machinery2017年1月18日 The osmotic, hydraulic and selfhealing efficiency of bentonite based barriers (eg geosynthetic clay liners) for containment of polluting solutes are governed by both the chemicophysical intrinsic parameters of the bentonite, ie the solid density (ρ sk), the total specific surface (S), the fixed negative electric surface charge (σ), the Stern fraction (f Stern), Intrinsic and State Parameters Governing the Efficiency of Bentonite 2023年11月30日 The requirements for drilling bentonites are tightening due to everincreasing demands for petroleum resources, coupled with cost and reaction technology constraints In addition to raising the risk of drilling, bentonite’s poor performance also raises the possibility of safety incidents and significant financial losses Organically modified bentonites effectively Modification Method of HighEfficiency Organic Bentonite for
.jpg)
The Pelleting Process CPM
California Pellet Mill Co 3 Terms Used in Pelleting The following terms are often used to measure the efficiency and quality of pellet mill operation Friction is the difference in temperature of the feed entering the pellet mill die and the pellet being discharged from the die The difference reflects the mechanical energy required to2021年12月30日 In this study, a pintype vertical stirred media mill was used to perform the dry grinding of bentonite Grinding time and stirring speed were investigated for effect on the particle size Dry Grinding of Bentonite by Stirred Media Mill ResearchGateThe newly upgraded 300 mesh environmentfriendly Raymond mill has outstanding competitive advantages, high powder yield, stable performance and high cost performance You are welcome to negotiate with HCM factory at any time, and come to the factory to investigate the bentonite grinding mill production line cases and equipment petitive Advantages Of Raymond Mill For Grinding 300 Mesh BentoniteGuilin Hongcheng recommends HC series highpressure suspension Bentonite Powder Roller Mill for grinding bentonite HC1700 Grinding Mill Max feeding size: ≤ 30mm Capacity: 625t/h Fineness: 0180038mm (80400mesh) Bentonite News Bentonite HighPressure Suspension Roller Mill
.jpg)
Exploring the working principle of ball mills
A ball mill is a type of grinder used to grind and blend materials for use in mineral dressing processes It is a cylindrical device filled with balls, which rotate on a horizontal axis to pulverize the material The working principle of a ball mill is based on the impact and friction between the balls and the powder material 1 Ball Mill 2023年11月8日 Hammer mills can effectively deagglomerate these materials, ensuring they are suitable for further processing Principles of Hammer mill The principle of a hammer mill in pharmaceuticals, as in other industries, is based Hammer mill Principle, Construction, WorkingThe shift towards highpressure boilers in sugarcane mills has been driven by a number of factors, including the need to reduce greenhouse gas emissions, improve energy efficiency, and reduce Efficiency Improvement in Sugar Mills; The Role of HighPressure 2021年11月10日 Bentonite clay is one of the oldest clays that humankind has been using from ancient times as traditional habits and remedies In recent years researchers have found many applications of bentonite Modification of bentonite clay its applications: a review
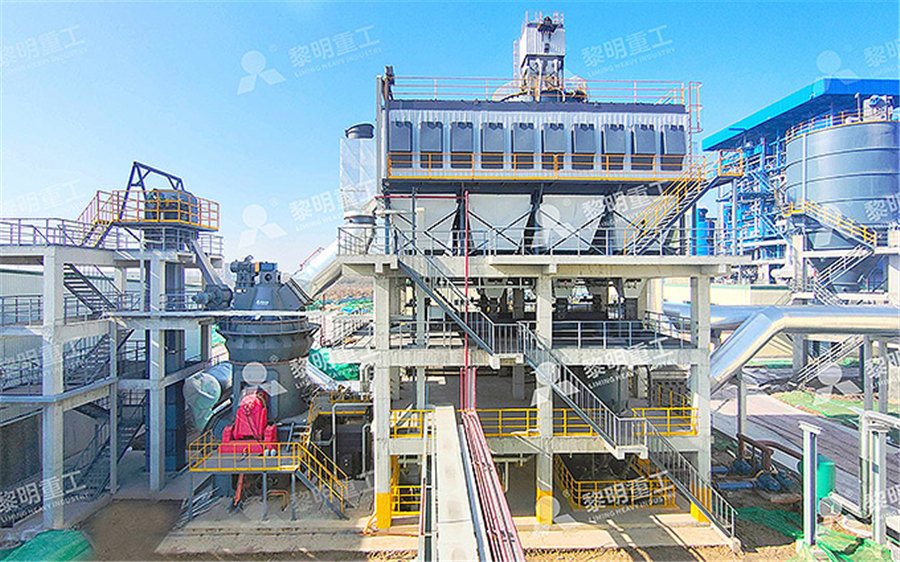
Modelling of the HighEnergy Ball Milling Process
2021年1月1日 PDF In this paper, the milling parameters of high energy ball mill (Fritsch Pulverisette 7) like vial The balls made of stainlesssteel have a positive effect on the milling efficiency2016年3月1日 Request PDF Application of modified bentonite granulated electrodes for advanced treatment of pulp and paper mill wastewater in threedimensional electrode system Two types of granular Application of modified bentonite granulated electrodes for 2015年6月24日 HMS and DMS are acronyms for Heavy (Dense) Medium Separation and is applied to the process of preconcentration of minerals – mainly the production of a high weight, low assay product, which may be rejected as waste In principle it is the simplest of all gravity processes and is a standard laboratory method for separating minerals of different specific DenseHeavy Medium Separation HMS / DMS ProcessDownload scientific diagram Types of mills for highenergy milling: Aball mill, Bplanetary mill, Cvibration mill, Dattritor (stirring ball mill), Epin mill, Frolling mill 4k Modified from Types of mills for highenergy milling: Aball mill, Bplanetary mill
.jpg)
Increase productivity of vertical roller mill using seven QC tools
2021年1月29日 Too high negative pressure before the mill increases the energy consumption of the mill system fan However too low negative inlet pressure influen ces the steady gas flow within the system and lead s