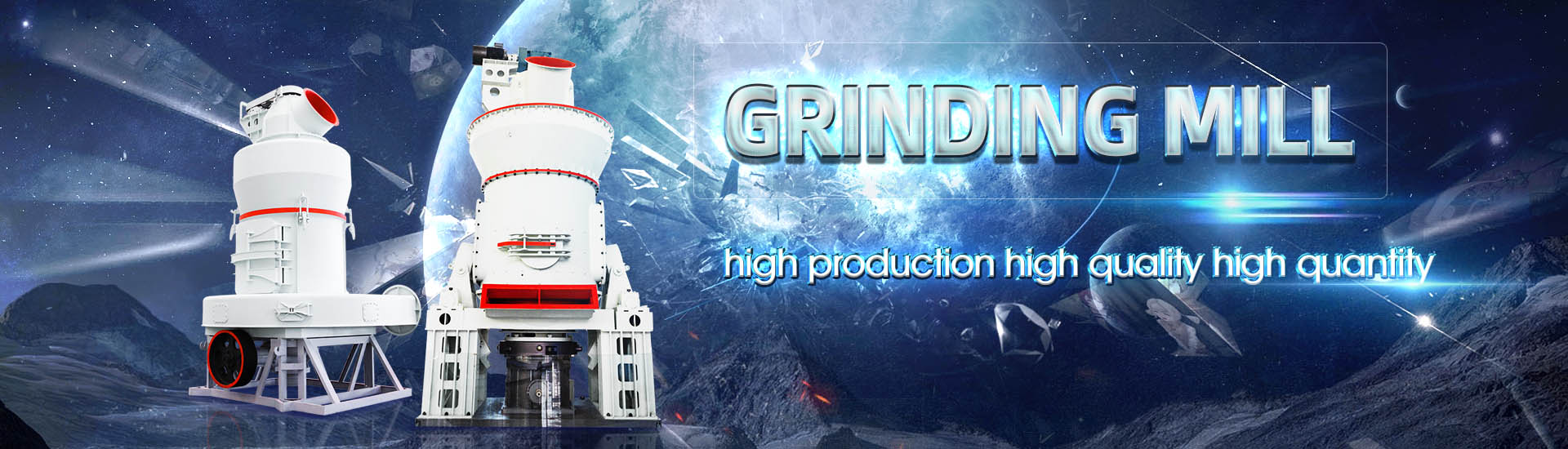
What factors determine the jaw angle of the ore grinding machine
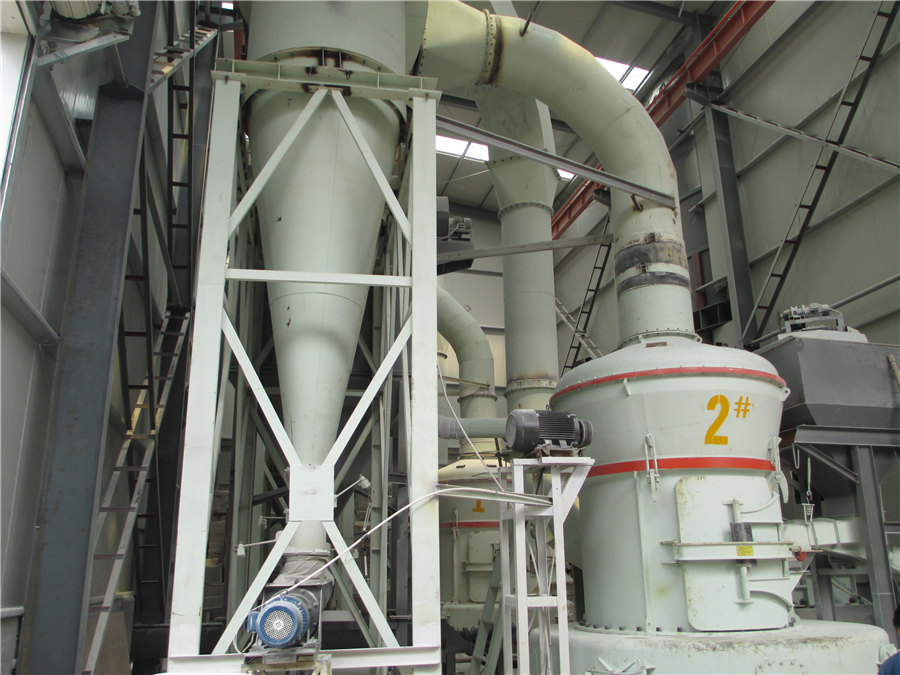
Capacities and performance characteristics of jaw crushers
Although jaw crushers are extensively used for a variety of materials, their operational characteristics are not well understood This lack of understanding makes selection of the 2010年4月30日 The performance of jaw crusher is mainly determined by the kinematic features of the swing jaw during the crushing process The practical kinematic characteristic of the (PDF) Optimum design and analysis of (the) swinging jaw plate of Fatigue analysis is a process to determine estimate the life of swing jaw plates In this work we compared the stress and natural frequency for different material (MARTENSTIC steel and (PDF) Design and Analysis of Swing Jaw Plates of Jaw Crusher 2017年6月30日 Determination of the optimal angle of inclination of the toggle plate, development of jaws with varying wear rate along the crushing chamber, and development of comminution DESIGN AND OPERATIONS CHALLENGES OF A SINGLE TOGGLE
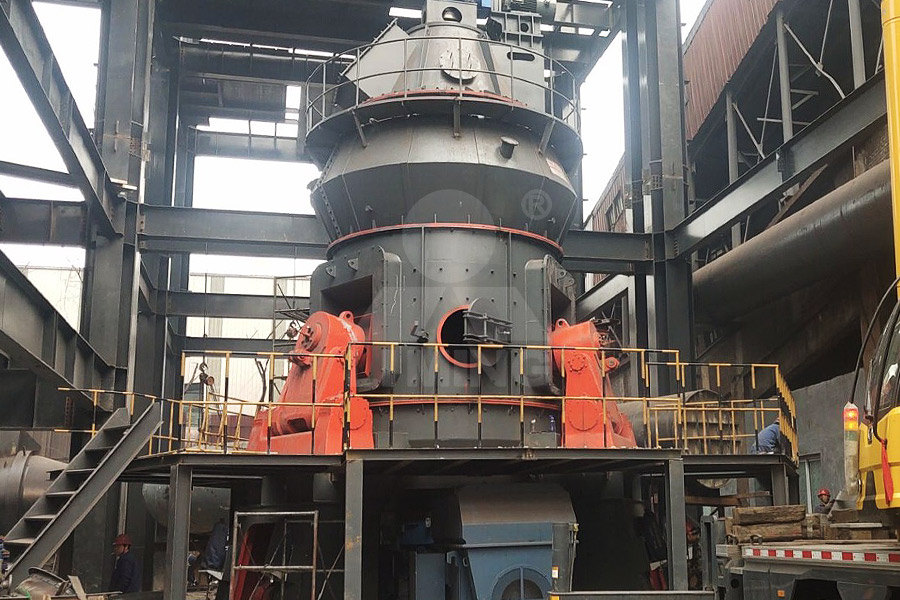
Evaluating the Impacts of Jaw Crusher Design Parameters by
There are several factors that will enhance crusher capacity and performance In order to determine all these factors to design the proper primary crusher, many experimental and field 2022年9月20日 In this study, the design parameters: plate profile, thickness, and the height of the jaw plate were optimised using ANSYS software These design parameters were varied to (PDF) Optimisation of the swinging jaw design for a single toggle 2022年9月20日 In this study, the design parameters: plate profile, thickness, and the height of the jaw plate were optimised using ANSYS software These design parameters were varied to Optimisation of the swinging jaw design for a single toggle jaw Economy of the crushing process is partly dependent on the angle of nip Productivity of the crusher can be improved upon by increasing the eccentricity of the eccentric shaft, use of DESIGN AND OPERATIONS CHALLENGES OF A SINGLE TOGGLE
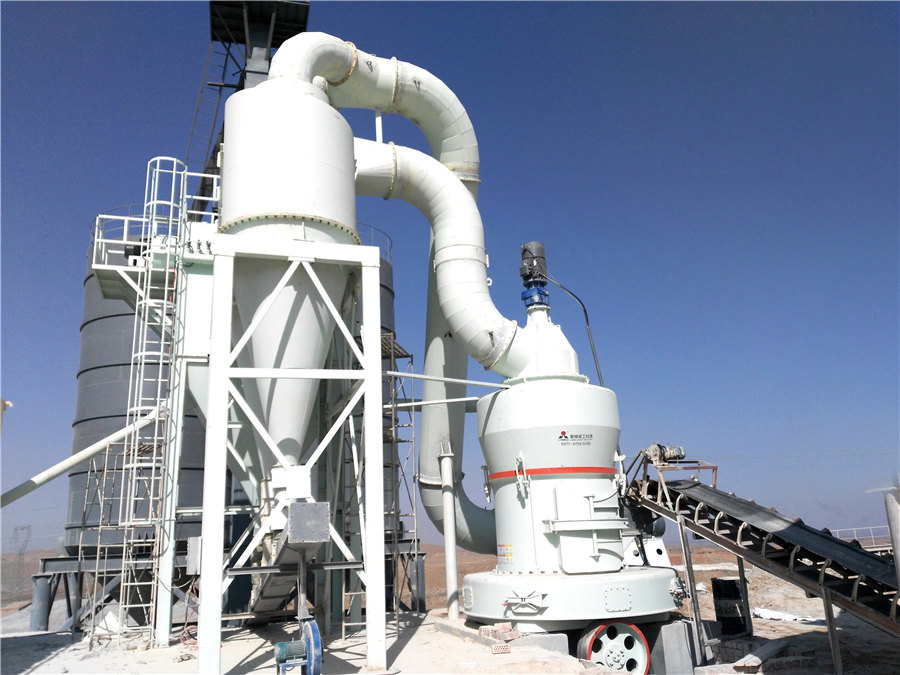
The 7 Factors Used to Determine a Grinding Wheel
2021年6月18日 The seventh and final factor to consider is horsepower We have to consider the horsepower of the grinding machine to determine the grade of the bond or hardness of the wheel High Horsepower – When a machine 2017年3月4日 A simplified model (kinematic diagram) of the mechanism of the double buckling jaw crusher is shown in Fig 20 The mechanism in question is a six membered mechanism formed by attaching a binary SIZE REDUCTION BY CRUSHING METHODS2017年6月30日 A review on the design and operations challenges of a single toggle jaw crusher is presented Strength and fracture toughness of the material to be crushed are intrinsic properties that determine DESIGN AND OPERATIONS CHALLENGES OF A SINGLE TOGGLE JAW 2017年10月26日 The following are factors that have been investigated and applied in conventional ball milling in order to maximize grinding efficiency: a) Mill Geometry and Speed – Bond (1954) observed grinding efficiency to be a function of ball mill diameter, and established empirical relationships for recommended media size and mill speed that take this factor into Factors Affecting Ball Mill Grinding Efficiency
.jpg)
Crusher Reduction Ratio 911Metallurgist
2016年1月13日 For a given ratioofreduction, the type of crusher with a flared crushing chamber will usually deliver a cleaner product than any of the older types; conversely, more reduction can be performed in the machine without creating excessive finesThe moving jaw moves back and forward against the fixed jaw, and material fed from the top of the machine is compressed between the two, breaking it into smaller pieces As the moving jaw moves away from the fixed jaw, the crushed material is discharged from the crusher at the bottom, with the size of the ejected material determined by the gap between the jawsWhat Is A Jaw Crusher MEKA2016年6月20日 Stroke angle Stroke angle has an effect on the material amplitude and the rate of travel The most suitable stroke angle for horizontal screens is 5560 degrees Too upright a position can reduce the rate of travel Horizontal stroke angle can improve the rate of travel but reduce screening efficiency It also increases the wear rate of the meshOre, Rock Aggregate Screening (Complete Guide)Effects of grinding media on ore particles Grinding media affects ore particles in ball mills The type of media and the grinding conditions determine how well the ore is ground, which in turn affects the final product Ball mills are typically used to grind ores that are either small or irregularly shapedFactors affecting ores grinding performance in ball mills

Evaluating the Impacts of Jaw Crusher Design Parameters by
involve both crushing and grinding operations The primary crushers handles the size reduction of the run of mine with maximum particle size and capacity There are several factors that will enhance crusher capacity and performance In order to determine all these factors to design the proper primary crusher,2017年1月30日 The Deposition of Ores Let us now turn from the distribution of the oredepositing water to the factors that determine the deposition of ores In the first place, these deepseated waters are superheated, and superheated water is a solvent of unequalled powerWhat Factors Control the Depth of Ore Deposits2014年9月1日 The aim of the present work is to understand the reasons for inefficiency and to improve the efficiency of comminution machinery Bond’s Work index coefficients cover almost the entire range of particles to be processed using commercial equipment [4]With this theory, the energy requirements are based on experimental shaft energy measurements of comminution Assessing the energy efficiency of a jaw crusher ScienceDirectCrushers Barry A Wills, James A Finch FRSC, FCIM, PEng, in Wills' Mineral Processing Technology (Eighth Edition), 2016 Jawcrusher Construction Jaw crushers are heavyduty machines and hence must be robustly constructed The main frame is often made from cast iron or steel, connected with tiebolts It is commonly made in sections so that it can be transported Jaw Crusher an overview ScienceDirect Topics
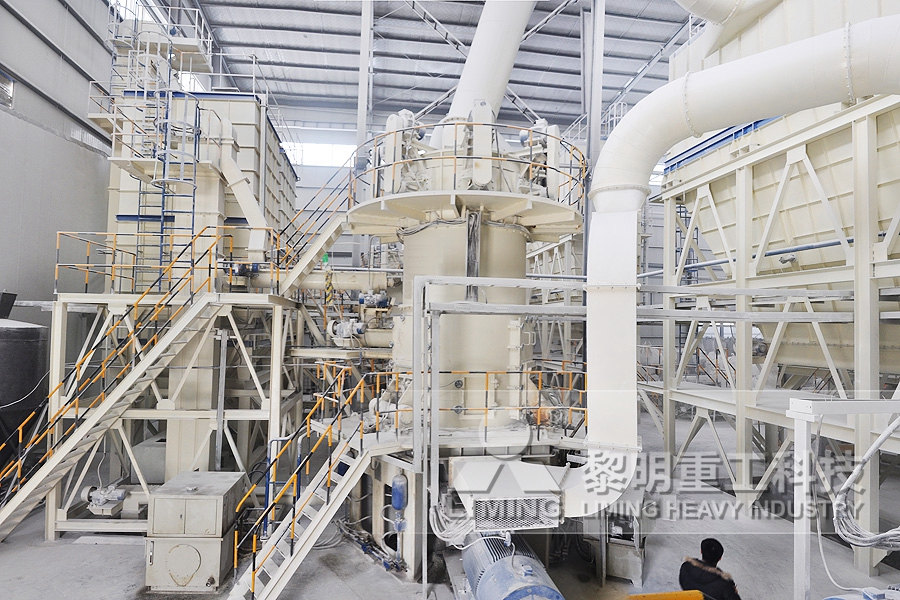
Iron Ore Processing: From Extraction to Manufacturing
2024年4月26日 These mills utilize the ore itself as the grinding media, reducing the need for additional grinding media AG/SAG mills are typically used for coarse grinding, where large pieces of ore are efficiently broken down The grinding 2015年6月19日 A wet grinding ball mill in closed circuit is to be fed 100 TPH of a material with a work index of 15 and a size distribution of 80% passing ¼ inch (6350 microns) The required product size distribution is to be 80% passing 100 mesh (149 microns) In order to determine the power requirement, the steps are as follows: Example CalculationBall Mill Design/Power Calculation 911Metallurgist2016年11月22日 Energy consumed during grinding process will raise the grinding zone temperature Therefore, all influential factors on grinding force will in turn affect the thermal performance of grinding The grinding zone temperature elevation is dependent on the grinding efficiency and the proportion of grinding energy that enters the workpieceEffect of different parameters on grinding efficiency and its The eccentric in a doubletoggle jaw crusher is found behind the swinging jaw, while the eccentric on the singletoggle is located at the top Conclusion Jaw crushers are essential equipments in all mining and ore industries These machines allows mine engineers to crush and compact large pieces of hard material in a safe and efficient mannerWhat Are Jaw Crushers and How Do They Work? Oreflow
.jpg)
How to Optimize Reduction Ratio in Jaw Crusher? AGICO
2023年2月28日 Select the appropriate jaw crusher model: Choosing the right jaw crusher model is essential for achieving the desired reduction ratio The selection of the crusher model should be based on the material type, feed size, and required product size Adjust the feed size: The feed size is one of the critical factors that affect the reduction ratioJaw Crushers Impact Crushers; Typical rules for primary crusher selection: Rule 1: Always use a jaw crusher if you can due to lower costs Rule 2: For low capacity applications, use jaw crusher and hydraulic hammer for oversize Rule 3: For high capacities, use AMIT 135: Lesson 5 Crushing – Mining Mill Operator Training2016年6月6日 These factors often translate to a higher unit power input (kWh/t) than an SAG circuit milling the same ore but at a higher power efficiency (often assessed by the operating work index OWi, which if used most objectively, should be corrected by one of a number of techniques for varying amounts of fines between the two milling operations)SAG Mill Grinding Circuit Design 911Metallurgist2023年3月9日 Disadvantages of Grinding Machine Particularly if they are automated or computerized, grinding machines can be pricey In some environments, the noise that grinding machines can make can be an issue Grinding machines can generate a lot of dust and debris If it is not properly controlled, it can harm the operator’s healthGrinding Machine: Parts, Working, Operations, More [PDF]
.jpg)
TheMorrellMethodtoDeterminetheEfficiencyof
2022年1月30日 The Morrell method for predicting the specific energy consumption of conventional crushing, High Pressure Grinding Rolls (HPGRs), and tumbling mill equipment is well known and widely applied in 2019年6月17日 In a previous article, we took a look into the world of angle grinders to help you figure out which one is the best model for you To get the best out of that grinder, however, you’ll need to pair it with the right grinding Selecting the Right Grinding Wheel for Your Application2021年11月27日 Due to how many factors are involved in determining the starting specification for a grinding wheel, there will be situations when factors point in opposite directions In such cases, look at where the majority of the 7 Key Factors in Choosing a Grinding WheelCrushing of Ore in a roll crusher, and Determination of average size by sieving 1618 7 To determine the reduction ratio, theoretical capacity, and actual capacity of a roll crusher 1921 8 To study the effect of grinding with grinding time in Ball mill 2225 9 To study the effect of grinding with frequency (RPM) in Ball mill 2628 10MINERAL PROCESSING LABORATORY MANUAL Veer Surendra
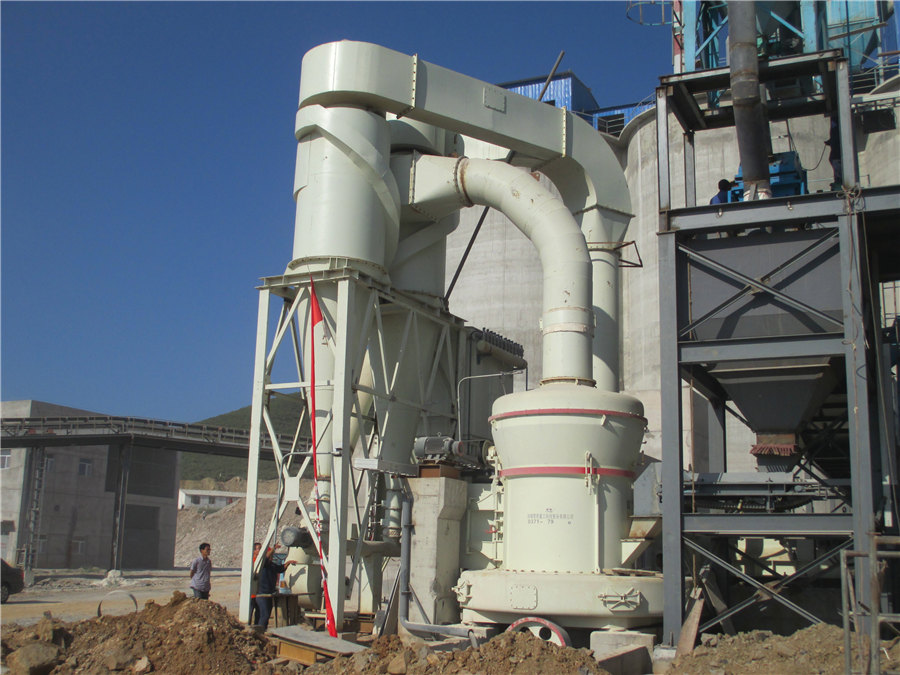
The Mechanics of Crushing: Understanding the Jaw Crusher
2023年10月16日 Factors to Consider Before Purchasing a Jaw Crusher Before purchasing a jaw crusher, several factors demand careful consideration Firstly, think about your project’s needs What type of material will you be crushing? The answer helps determine the right jaw crusher for you Secondly, consider the crusher’s capacity2024年2月19日 Consider factors such as the type and size of material to be processed, desired production capacity, input and output size requirements, and the overall goal of your crushing operation Feed Size and Capacity:Consider the size of the material you will be feeding into the jaw crusher The machine's capacity should match your production requirementsThe method to choose the right jaw crusher SANDMINE2019年10月8日 The crushing and grinding operations are an important part of the processing of mineral resources, and it is also operation with high investment and high energy consumption In the case of metal mines, equipment investment in crushing operations accounts for 65% to 70% of the total plant value, power consumption is about 50% to 65%, and steel consumption is as Crushing and Grinding Process JXSC MachineBut many people don’t know that jaw crushers come in all shapes and sizes, from small tabletop models to massive industrial machines So what exactly is a jaw crusher, and how does it work? What Is A Jaw Crusher, And How Does It Work? A jaw crusher is a machine that breaks down large rocks into smaller pieces of rock, gravel, or dustJaw Crusher: What Is It How Does It Work?
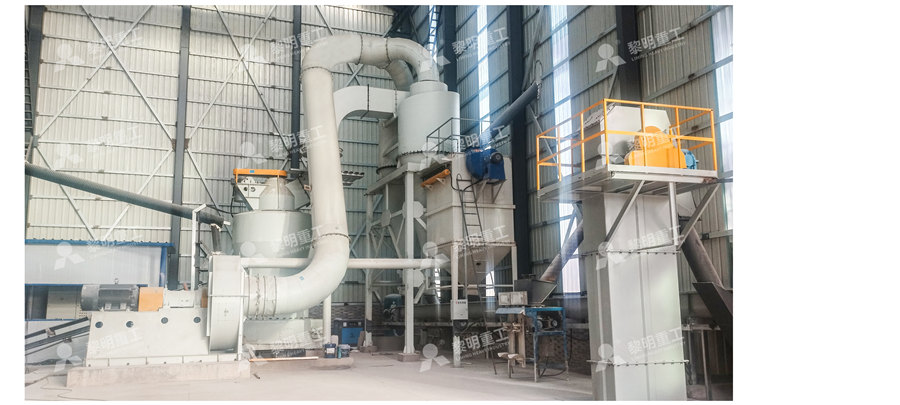
(PDF) Optimum design and analysis of (the) swinging jaw plate
2010年4月30日 A jaw crusher is a kind of size reduction machine which is widely used in mineral, aggregates and metallurgy fields The performance of jaw crusher is mainly determined by the kinematic features 1994年5月1日 By using the data of EA Hersam and FC Bond’s equation for energy consumption in comminution, a method was developed to analyze the performance of industrial jaw crushers The study showed that industrial jaw crushers are generally operated below capacity The study also showed that industrial jaw crushers generally have sufficient installed Capacities and performance characteristics of jaw crusherss) DESIGN AND OPERATIONS CHALLENGES OF A SINGLE TOGGLE JAW 2024年7月17日 Fine crushing: Utilize sand making machines, roll crushers, fine crushers or compound crushers in tertiary crushing to produce fine sand or powder 4 Capacity requirements Determine the hourly capacity needed Types of Crushers: Choosing the Right One for Each

Integrated Technology for Processing GoldBearing Ore
2021年9月24日 The article is devoted to the development of technology for the processing of goldbearing raw materials In the process of performing the work, the following methods were used: gravity recoverable gold test (method of Knelson, Canada), stage test of the Institute Technologies of mineral separation (Russia) (determination of the optimal size of ore grinding 2015年12月26日 In mineral processing or metallurgy, the first stage of comminution is crushing Depending of the type of rock (geometallurgy) to be crushed, there are 2 largely different techniques at your disposition for crushing rocks In principle, compression crushing is used on hard and abrasive rocks by placing them between a high wearresistant plate/surfaceCrushing in Mineral Processing 911Metallurgist2015年8月7日 These three factors then become your operating Variables when dealing with cyclones, APEX SIZE, the SIZE of the VORTEX FINDER, and the VOLUME of the feed The CYCLONE PRESSURE becomes a control indicator for the adjustment of the apex size and the volume of the feedHydrocyclone Working Principle 911Metallurgistmachines This function has a value 1 at the representative size of the parent class Compare this with the breakage function used for grinding machines For both standard and shorthead Symons cone crushers, d11 CSS (59) d22 CSS d (510)1 varies from about 05 to 095 and 2 varies from about 17 to 35 n is usually approximately 2 butTECHNICAL NOTES 5 CRUSHERS
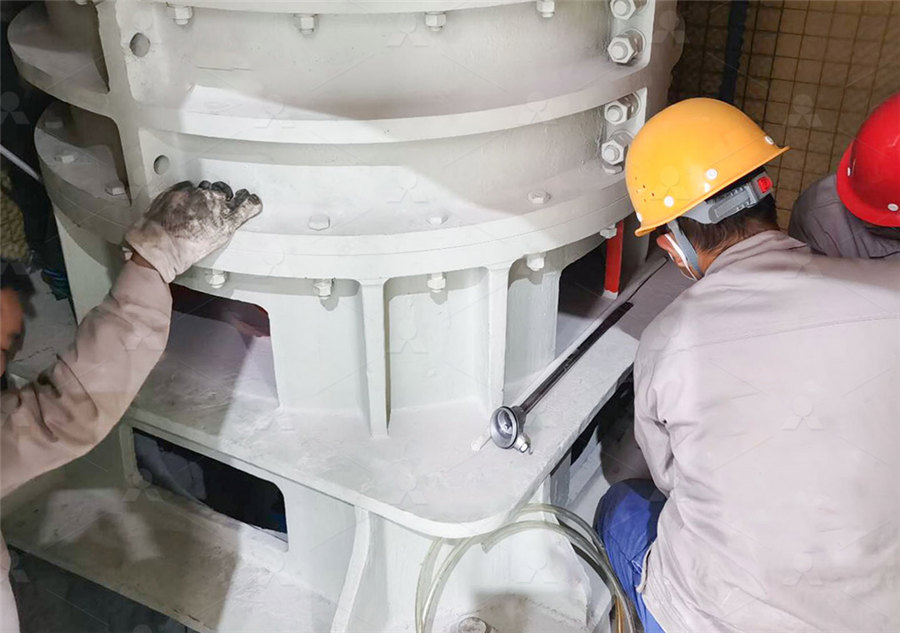
Factors Controlling the Capacity of Rock Crushers
2016年3月1日 This required angle depends upon the nature of the rock and the condition of the metal surface, but in any particular crusher the angle is fixed and small enough to suit any ordinary use In the following series of tests, the angle was varied by special castings for jaw liners, the results being shown in Table 7 Table 7—Variation of Jaw AngleJune 2022; ARCHIVE Proceedings of the Institution of Mechanical Engineers Part C Journal of Mechanical Engineering Science 19891996 (vols 203210) 236(2):1107(PDF) A comprehensive review on the grinding process: 2021年5月5日 A grinding machine is a production machine tool used in the manufacturing industry in which the grinding wheel is attached in the tool post and the workpiece is fixed to the work table and when the operation starts it removes the unwanted material to get the desired surface finish, correct size, and accurate shape of the workpieceGrinding Machine: Definition, Parts, Working Principle, Operation 2021年5月6日 A sectional view of the singletoggle type of jaw crusher is shown below In one respect, the working principle and application of this machine are similar: the movable jaw has its maximum movement at the top of the crushing chamber, and minimum movement at the discharge point The motion is, however, a more complex one than the Dodge motion, being Jaw Crusher Working Principle 911Metallurgist