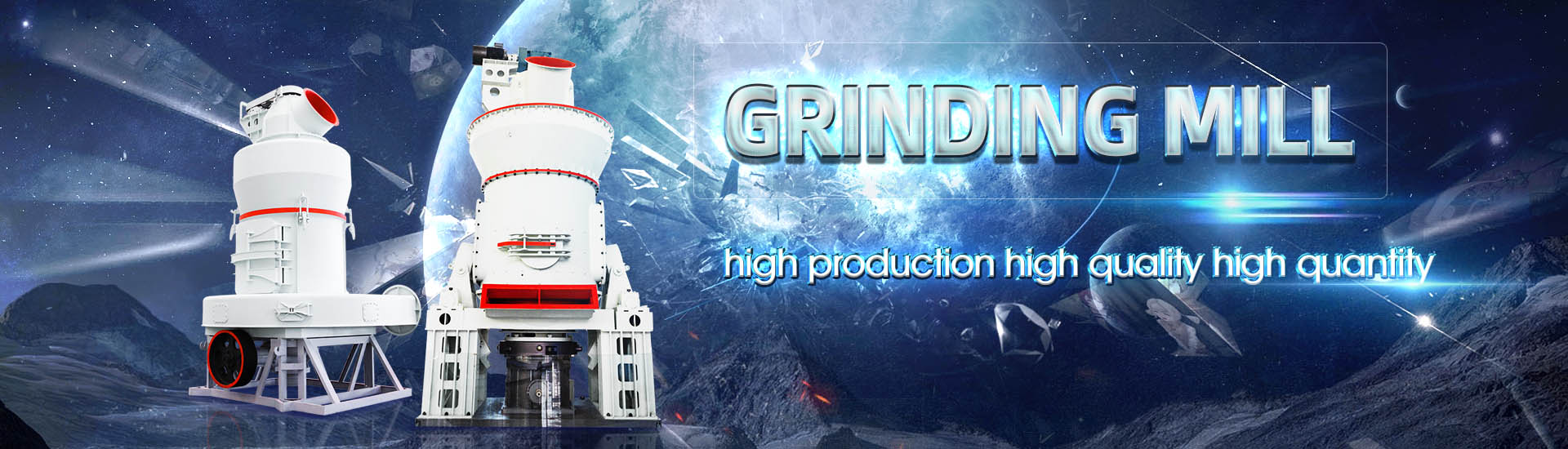
Cement plant clinker processing
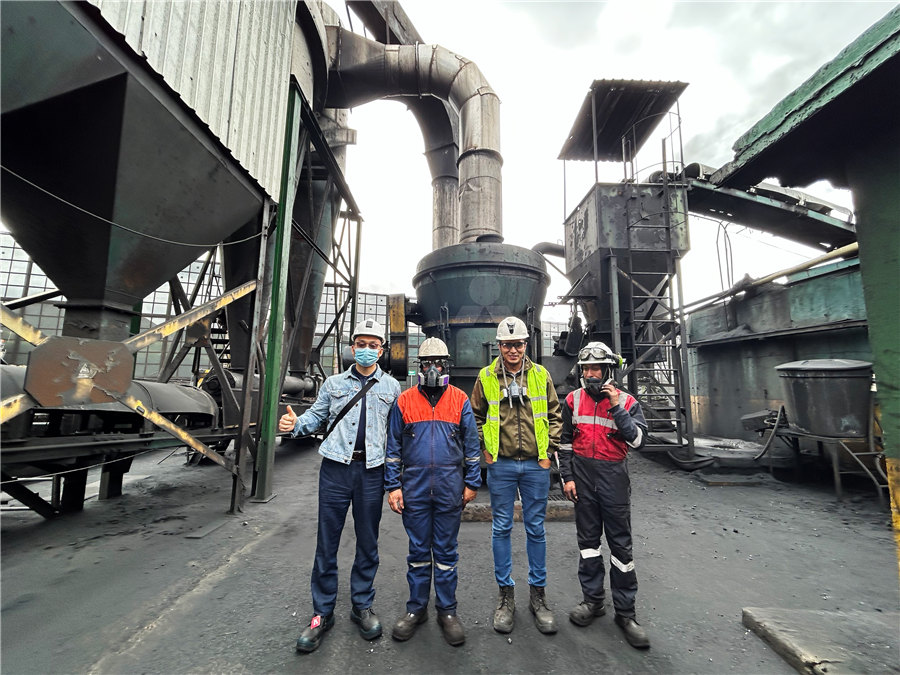
Process characteristics of clinker and cement production SINTEF
• ETHZ has simulated and adapted the CAP system to different cementplant flue gases; • New ratebased model was developed and used to validate fullscale CAP simulations for cement plants Upcoming work: CAP optimization • The Absorber and Direct Contact Cooler (DCC) The process of clinkerization signifies conversion of raw meal into clinker minerals mainly consisting of C4AF (Aluminoferite), C3A (Aluminite), C2S (Belite) and Clinkerization Cement Plant OptimizationClinker production is the most energyintensive stage in cement production, accounting for more than 90% of total industry energy use and virtually all the fuel use The main kiln type used Clinker Production an overview ScienceDirect TopicsThe clinker keeps cooling and a ball mill grinds it with gypsum or other ingredients into fine cement—about 150 billion grains per pound Blending in higher ratios of limestone or SCMs can reduce a plant’s carbon footprint by up to 10%How Cement is Made Portland Cement Association
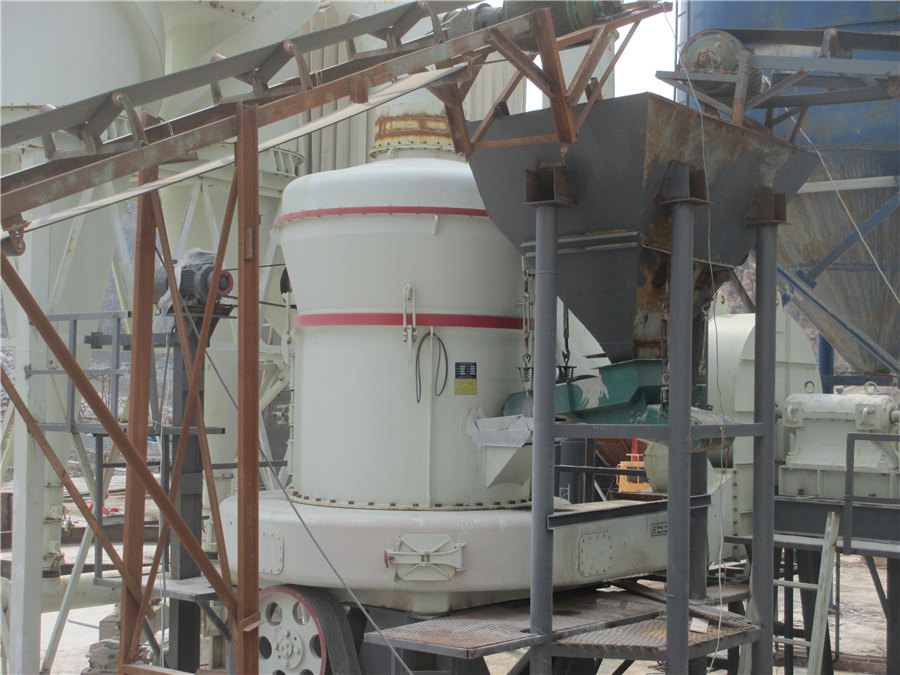
Cement Clinker Manufacturing Process with Reactions
The main part of the manufacturing process of clinker takes place in the kiln The stages in the kiln phase are as follows: Evaporation of free water: A pressure above atmospheric is required The Cement Plant Operations Handbook is a concise, practical guide to cement manufacturing and is the standard reference used by plant operations personnel worldwide Providing a The Cement Plant Operations Handbook International Cement The clinkerization reactions, as we all know, take place at the pyroprocessing stage in a plant, which extends from the extraction of the kiln feed (or the raw meal) from the post Clinkerization an overview ScienceDirect TopicsClinker, and clinker substitutes, are the active components that confer cement its binding properties Producing traditional cement clinker is an extremely energy and CO 2 intensive process In the EU, 90% of clinker is now made via the more energy efficient dry clinkermaking process (2) Older, less efficient wetDeep decarbonisation of industry: The cement sector Europa
.jpg)
Cement Clinker Calcination in Cement Production
The cement clinker calcination is an important step in the cement production process It mainly occurs in cement kiln and can be roughly divided into six reaction stages, namely drying, preheating, chemical decomposition, AGICO Cement has large manufacture workshops and professional processing equipment to ensure the fast and highquality production of related equipment in this fly ash processing plant In addition, we have more than 20 years of Fly Ash Processing Plant Cement Equipment Continuous high temperature process in the cement industry: Calcination and cement clinker burning Calcination of raw material CaCO 3 => CaO + CO 2 Process emissions of raw material: = 054 t CO 2 /t clinker Endotherm reaction at 950 °C ca 1700 MJ/t clinker ≈ 50% of energy Cement clinker burning at 1450 °C formation of hydraulicProcess characteristics of clinker and cement production SINTEFThe Cement Plant Operations Handbook is a concise, practical guide to cement manufacturing Storage of clinker and other components – 2 Cement milling – 3 Separators (classifiers) – 4 Ball mill circuit control – 5 Cement storage – 6 Cement dispatch – 7The Cement Plant Operations Handbook International Cement
.jpg)
Cement Production Process Cement Manufacturing Process AGICO CEMENT
2020年8月25日 A full cement production process includes the cement crushing process, raw mill process, clinker process, and cement grinding process, cement packing process, and related process Find more! Skip to content +86 info@cement Fly Ash Processing Plant Biochar production plant applications Portland cement manufacture Cement Kiln In Cement Plant AGICO offers different types of cement kilns from 105000t/d with steady running, high efficiency and large output We adopt the most advanced calcination technology so that the production investment of clinker is small and the income is highClinker Production Clinker Manufacturing Cement 2023年12月20日 The result is called clinker, which are rounded nodules between 1mm and 25mm across The clinker is ground to a fine powder in a cement mill and mixed with gypsum to create cement The powdered cement is then mixed with water and aggregates to form concrete that is used in constructionThe Cement Manufacturing Process Thermo Fisher Scientific2019年1月3日 Clinker grinding technology is the most energyintensive process in cement manufacturing Traditionally, it was treated as "low on technology" and "high on energy" as grinding circuits use more than 60 per cent of total energy consumed and account for most of the manufacturing cost Since the increasing energy cost started burning the benefits significantly, Clinker grinding technology in cement manufacturing
.jpg)
The cement plant of tomorrow ScienceDirect
2023年11月1日 Cement plants of tomorrow will have to implement all CO 2 abatement and saving measures to the best extent possible Reducing the clinker factor, optimising the reactivity of the clinker, substituting fossil fuels by alternative fuels and using alternative raw materials are pathways which will still play a growing role in future cement productionCement manufacturing: components of a cement plant This page and the linked pages below summarize the cement manufacturing process from the perspective of the individual components of a cement plant the kiln, the cement mill etc Cement manufacturing components of a cement Rotary cooler is one kind of cement cooler applied for cement manufacturing plantsAs an essential part of the cement kiln system, a rotary cooler is used to cool the clinker discharged from the cement rotary kilnThe rotary cooler also Rotary Cooler Clinker Cooler In Cement Plant2024年3月1日 The previous section demonstrates that thermodynamic simulation is a reliable tool for reproducing the phase assemblages of cement clinker at different processing temperatures Building on these simulated results, this section examines the impact of LSF on C 3 S and C 2 S phases across a wide range of cement clinker compositions (shown in Table 2)Toward smart and sustainable cement manufacturing process:
.jpg)
Grate Cooler In Cement Plant Clinker Cooler, Cement Cooler
The grate cooler is a quenching type cement cooler applied for the cement manufacturing plant According to the movement mode of the grate, the grate cooler can be divided into three types, rotary type, vibrating type, and pushtype grate cooler, with the development of cooler technology, pushtype grate cooler is considered the most common clinker cooler in the cement production Cement plant is necessary for cement production, and mainly consists of a series of cement equipment apply for the preparation of cement raw materials, clinker production, and finished cement production, such as a cement mill, cement crusher, rotary kiln, cement roller press, cement dryer, clinker cooler, cement silo, and related cement plant equipmentCement Plant, Cement Equipment Cement Plant ManufacturerAGICO Cement supplies cement preheater, preheater in cement plant as you need! Skip to content +86 s about Concrete Batching Plant; Fly Ash Processing Plant; Cement Plant Upgrade; Lime Production Line; Hydrated Lime and prepare for the clinker production Why cement preheater is necessary for rotary Cyclone Preheater Cement Plant2023年4月19日 Lowcarbon cements The average clinkertocement ratio in the EU in 2017 was 75% (2) The European Standards differentiates five main categories of cements based on their clinker composition The most used cements, Portland and Portlandcomposite cements, have clinker contents over 95% and 65% respectivelyDeep decarbonisation of industry: The cement sector
.jpg)
Comparison of energy consumption and carbon emissions from clinker
2021年7月15日 The high carbon emissions from cement production result from the combination of two of the three main sources of anthropogenic emissions of CO 2 to the atmosphere: i) carbonate decomposition; and ii) oxidation of fossil fuels With roughly 60% of the raw material comprising of carbonates (mostly limestone, CaCO 3), the production of the main component 2019年9月27日 AGICO offers cement making machines including cement mill, rotary kiln, cement crusher, cyclone preheater, cement dryer, clinker cooler etc any need? Skip to content +86 s about blog contact EN ES Menu Menu Fly Ash Processing Plant Biochar production plant applications Portland cement Cement Euipment Overview Cement Making Machines Cement PlantSummary: The coprocessing of Solid Recovered Fuel (SRF) in cement plants offers an efficient alternative to landfilling, particularly for unsorted waste The Robilante Buzzi Unicem cement plant uses SRF, comprising 40%50% carbonneutral biomass, reducing both CoProcessing CEMBUREAUThe clinker cooler, also known as grate cooler or cement cooler, it is a necessary equipment of cement clinker productionThe clinker cooler is mainly used to cool and transport the cement clinker At the same time, cement cooler also Clinker Cooler Cement Plant
.jpg)
8 Tips For Cement Plant Design
2023年11月1日 The selection of cement production line site must be reliable, that is, the supply of raw materials should be reliable, the market sales should be reliable, and the past will be a complete cement production line in the same This method is advantageous due to its lower fuel consumption and reduced time of processing, Clinker Grinding: The main process in cement grinding units involves grinding the clinker into a fine powder using a cement ball mill or StepbyStep Guide to the Manufacturing of CementCement manufacturing process The cement manufacturing plant can be divided into five steps: Crushing prehomogenization: cement crusher crush limestone and other materials and stacker and reclaimer homogenize them; Raw material preparation: use cement mill to process materials into required sizes for cement clinker production; Clinker production: In the cyclone preheater Cement Plant Cement Manufacturing Plant EPC Project2022年4月5日 Worldwide, in the rotary kilns of cement plants, various amounts of combustible waste are burned, which would otherwise end up in municipal landfills The paper first analyzes the literature on the coprocessing of waste in cement manufacture and its influence on the environment and human health Then, it shows how the combustion components of co Assessment of Environmental Pollution in Cement Plant Areas in
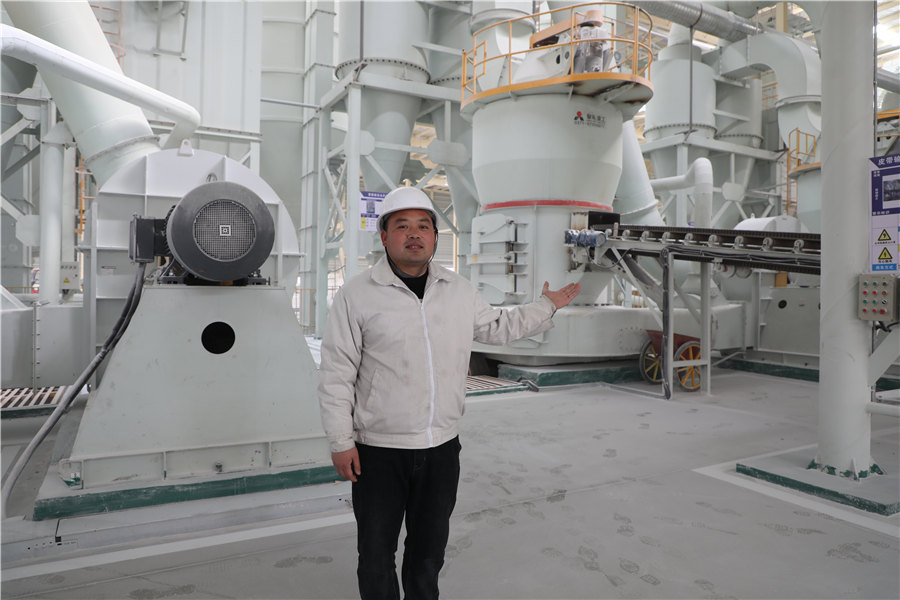
Cement mill Wikipedia
Portland clinker is the main constituent of most cements In Portland cement, a little calcium sulfate (typically 310%) is added in order to retard the hydration of tricalcium aluminateThe calcium sulfate may consist of natural gypsum, anhydrite, or synthetic wastes such as fluegas desulfurization gypsum In addition, up to 5% calcium carbonate and up to 1% of other It is mainly used in the raw material crushing and clinker production systems of cement plant to collect and remove the dust generated during the crushing and clinkerization Industrial cyclone dust collectors are suitable for various industries such as mechanical processing, petrochemicals, metallurgy, power generation, and building Cyclone Dust Collector For Cement Plant Industrial Cyclone Most new cement plant is of this type The principle is similar to that of the dry process preheater system but with the major addition of another burner, or precalciner With the additional heat, about 85%95% of the meal is decarbonated before it enters the kilnManufacturing the cement kiln Understanding Cement2020年9月22日 In this Review, we first examine the environmental impacts of cement and concrete production, use and disposal We then look at potential areas for improvement, investigating what can be Environmental impacts and decarbonization strategies in the cement
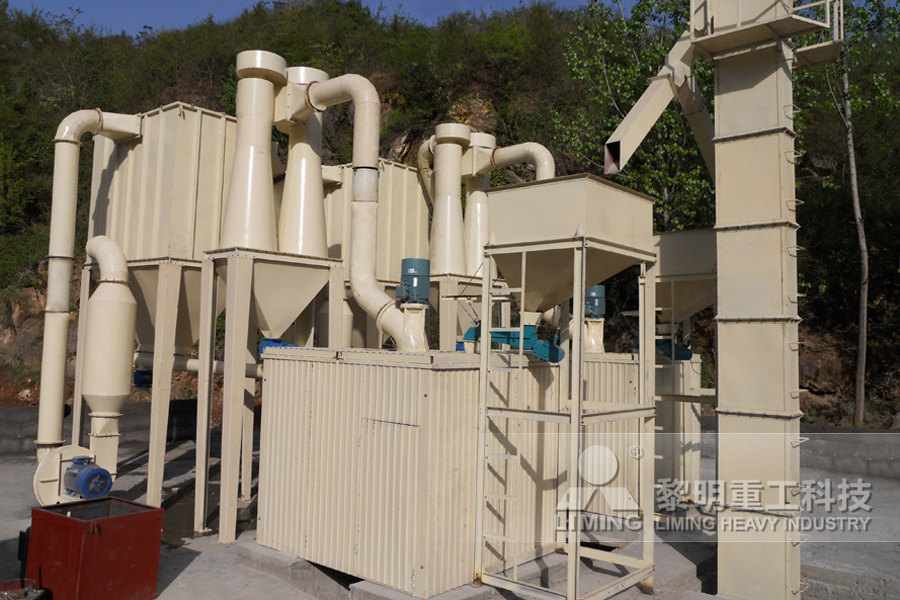
Modular Mobile Grinding Plant, Portable Grinding Plant Cement
Modular Mobile Grinding Plant To meet the small and mediumsized clinker grinding demand of cement producers, AGICO CEMENT develops a modular mobile grinding plant (MMGP in short) to achieve goals of quick return with minimal capital investment The modular mobile grinding plant developed by AGICO CEMENT is a highly flexible system capable of producing any 31 Energy demand of the clinker production process 9 32 Energy balance of the clinker production process 13 321 Energy balance of a clinker production line 13 322 Extended balancing area for a cement plant including the use of further drying processes and externally recovered heat 16European Cement Research European Cement Research Academy2023年4月1日 The global cement industry has the secondlargest share of the direct industrial CO 2 emission, emitting around 26 Gt of CO 2 in 2020 [1]Further, cement production is expected to grow by 12–23% by 2050 due to the rising world population and urbanization [2]The European Union (EU) aims to reduce greenhouse gas emissions by 80–95% by 2050 relative to 1990 [3]Electrified calciner concept for CO2 capture in pyroprocessing of Clinker is a nodular material produced in the kilning stage during the production of cement and is used as the binder in many cement products The lumps or nodules of clinker are usually of diameter 325 mm and dark grey in color It is produced by heating limestone and clay to the point of liquefaction at about 1400°C1500°C in the rotary kiln What is Cement Clinker? Composition, Types Uses

CoProcessing procedure cement plant Shakti Sustainable
5 The cement plant, which got approval for trial run should inform CPCB, about the date of the trial run 15 days in advance 6 A detailed protocol to be followed while conducting trial run in cement plant for co processing hazardous waste has been attached as annexure 2 7Cement kilns are an essential component of the cement manufacturing process, playing a crucial role in producing the clinker that is ground into cement These massive, rotating cylindrical vessels are designed to withstand extreme temperatures and chemical reactions that transform raw materials into prehensive Guide to Cement Kilns: Processes, Types, 2022年4月5日 PDF Worldwide, in the rotary kilns of cement plants, various amounts of combustible waste are burned, In the cement industry, in the manufacture of Portland clinker, the coprocessing(PDF) Assessment of Environmental Pollution in Cement Plant As a cement equipment supplier and cement plant manufacturer, AGICO offers quality cement kiln, cement vertical mill cement ball mill, hammer crusher, etc It replaces clay as the raw material for producing cement clinker We offer fly ash processing plants with different capacities VSK Cement Plant >>Cement Equipment In Cement Plant AGICO Cement Plant

Cement Clinker: Types and Uses of Cement Clinker JK Cement
How Is Cement Clinker Formed? Here is a stepbystep process of how cement clinker is produced: Sourcing Raw Materials The primary raw materials used in the production of cement clinker are limestone and clay These materials are typically sourced from quarries and then transported to the cement plant Crushing and Grinding2023年12月26日 As we all know, the dryprocess cement production line is commonly used in the cement industry The new type of dryprocess cement production process includes four main sections: Prehomogenization of raw materials, homogenization of raw materials, clinker firing, cement grinding, etc Raw material conveying system The raw material, including limestone, 6 Cement Equipment For Dryprocess Cement Production Line2023年5月22日 The cement plant has a rated capacity of ~ 15 tpd clinker and producing approx 1450 tpd There were reducing conditions prevailing at kiln inlet Specific heat consumption works out to 960 kcal/kg clinker based upon the heat balance, operating parameters and plant data for entire pyro processing sectionRefuse Derived Fuel (RDF) Coprocessing in Kiln Main Burner in a Cement