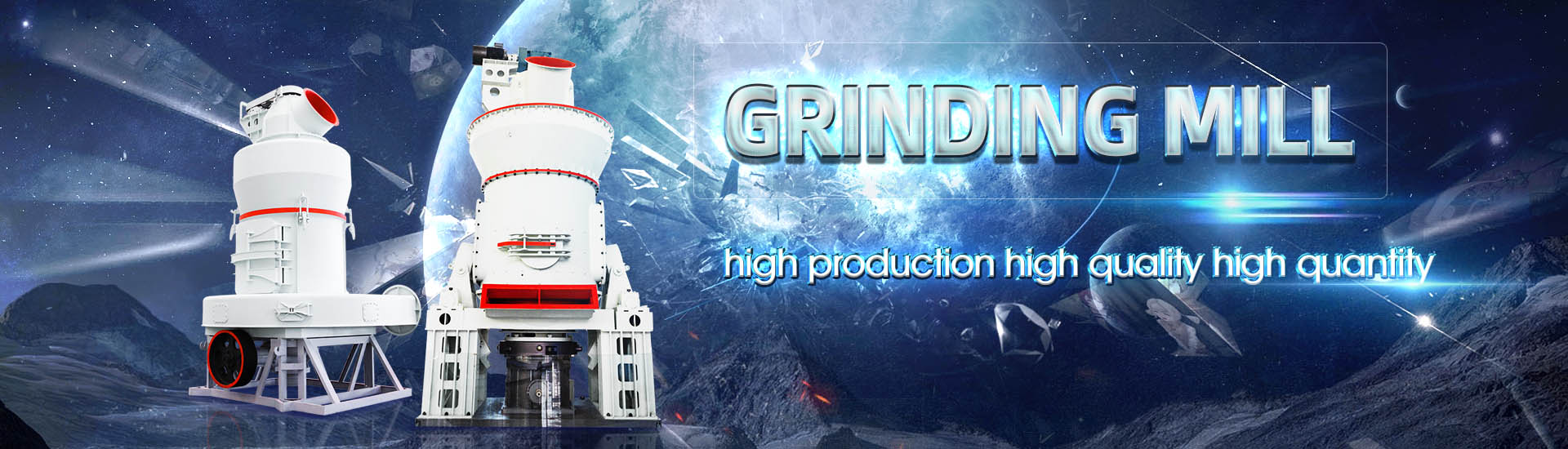
Process flow of iron oxide yellow processing equipment
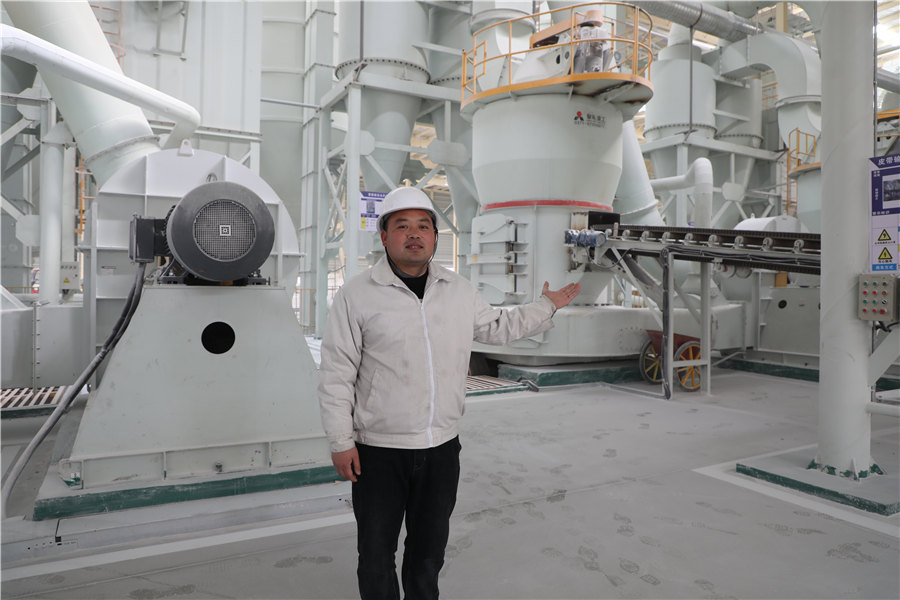
Process for the production of iron oxide yellow pigments
A process for the production of iron oxide yellow pigments by the PennimanZoph process from the raw materials iron (II) sulfate, sodium hydroxide and metallic iron, is disclosed in whichThe present invention relates to a process for the preparation of iron oxide yellow pigments by the PennimanZoph process from the raw materials iron (II) sulfate, sodium hydroxideProcess for preparing yellow iron oxide pigments2021年1月4日 Both of the ferric oxide hydrates and magnetite can be changed into hematite by heating; calcination of yellow αFeOOH is one of the main ways of producing synthetic red iron Iron Oxide Pigments 911MetallurgistThe precipitation and Penniman processes are primarily used to produce yellow iron oxide pigments The three processes for iron oxide production are described in detail below The scholz farbpigmente colourpigments
.jpg)
(PDF) Effective Processing of the Iron Ores
2017年1月1日 Effective technology for a complex wasteless processing of the iron ores has been designed and includes three main components (plats): comminution plant, briquette plant, pigment plant TheThe CTL process contains five major process steps: atmospheric chloride leaching, oxidation, iron solvent extraction/precipitation/calcination, titanium solvent extraction/precipitation/calcination, PilotScale Demonstration of Ilmenite Processing Technology2022年8月23日 The aim of all the processes is to synthesize the best synthetic iron oxide pigments made up of welldefined compounds with known crystal structures (Table 1); Synthesis of Iron Oxide Pigments from Iron Waste (Mill Scale)2024年1月1日 Ironmaking is the process of refining iron oxides in iron ores into metallic iron The earth’s crust is rich in iron, accounting for 42% of the total elements, ranking fourth With no Ironmaking SpringerLink
.jpg)
Iron Ore Processing, General SpringerLink
2022年10月20日 Making iron and steel from iron ore requires a long process of mining, crushing, separating, concentrating, mixing, agglomeration (sintering and pelletizing), and Iron processing, use of a smelting process to turn the ore into a form from which products can be fashioned Included in this article also is a discussion of the mining of iron and of its preparation for smelting Iron (Fe) is a relatively dense Iron processing Definition, History, Steps, Uses,2019年8月23日 Strong magnetic separation Manganese mineral is a weak magnetic mineral ( the specifical magnetization coefficient x=10×106~600×106cm3/g ), and it can be recovered in a strong magnetic field magnetic Manganese Processing Equipment, Process Flow, 2022年4月1日 The iron oxide used was purchased from Tianjin Kermeo Chemical Reagent Co, Ltd Its chemical formula is Fe 2 O 3, and the relative molecular weight of which is 15969 The content of iron oxide is more than or equal to 94%, the water soluble substance is less than or equal to 1%, and the drying weight loss is less than or equal to 1%Microwaveassisted iron oxide process for efficient removal of
.jpg)
Synthesis of Iron Oxide Pigments from Iron Waste (Mill Scale)
2022年8月23日 The aim of all the processes is to synthesize the best synthetic iron oxide pigments made up of welldefined compounds with known crystal structures (Table 1); Goethite (αFeOOH, yellow color, by precipitation), Hematite (α Fe 2 O 3 (red color, by copperas process, calcination between 600 and 900 ℃ for 3 h), Maghemite (γ Fe 2 O 3, brown color, by 2024年10月12日 The study aims to synthesize and homogeneously functionalize iron oxide nanoparticles (IONPs) using a nonthermal atmospheric pressure (NTAP) plasma for biological applications IONPs were synthesized using a new NTAP plasma assisted electrolysis technique The utilization of a unique NTAP plasma rotating reactor allows for a uniform surface Development of Functionalized Iron Oxide Nanoparticles Through 2024年3月12日 Abstract The author investigated the modes of thermal and heatandradiation treatment of ferruginous bauxite from Vezhayu–Vorykva deposit and revealed different mechanisms of mineral transformations Under thermal treatment, oxohydroxides transform into anhydrous iron and aluminum oxides, while under heatandradiation treatment, scattered Process Flow Charts and Recommendations for Processing of Typical Copper Extraction Process Flow Chart (Copper Oxide): Multotec specialises in process equipment used in copper beneficiation, with over 50 years of global experience Our team of metallurgists and engineers will help devise the optimum solutions for your plant Typical Copper Extraction Process Flow Chart (Copper Sulphide):Copper Processing Multotec
.jpg)
Direct Reduced Iron and its Production Processes – IspatGuru
2013年3月16日 Feed material for the DR process is either sized iron ore of size ranging from 10 mm to 30 mm or iron ore pellets of size ranging from 8 mm to 20 mm produced in an iron ore pellet plant The gas based process uses a shaft furnace for the reduction reaction The coal based process uses any one of the four types of reactors for the reduction 2018年7月11日 Iron Ores and Iron Oxide Materials 50 Bentonite, an inorganic binder, has been the main binder used in the iron ore pelletizing process since the beginning of pellet production in the 1950sIron Ore Pelletizing Process: An Overview ResearchGateIron is currently produced by carbothermic reduction of oxide ores This is a multiplestage process that requires largescale equipment and high capital investment, and produces large amounts of CO2 An alternative to carbothermic reduction is reduction using a hydrogen plasma, which comprises vibrationally excited molecular, atomic, and ionic states of hydrogen, all of Hydrogen Plasma Processing of Iron Ore Metallurgical and 2017年6月21日 Iron is currently produced by carbothermic reduction of oxide ores This is a multiplestage process that requires largescale equipment and high capital investment, and produces large amounts of CO2Hydrogen Plasma Processing of Iron Ore
.jpg)
Quartz Processing Equipment, Process Flow, Cases
2019年8月26日 Thinfilm iron or leaching iron on the surface of quartz sand particles by microorganisms is a newly developed iron removal technology According to foreign research results, it is indicated that aflatoxin, penicillium, 2023年4月5日 Recent Trends in the Technologies of the Direct Reduction and Smelting Process of Iron Ore/Iron Oxide in the Extraction of Iron and Steelmaking April 2023 DOI: 105772/intechopen(PDF) Recent Trends in the Technologies of the Direct2021年1月4日 Until the late 19th century iron oxide pigments were obtained wholly from natural materials, generally with little alteration other than physical purification In some cases roasting or calcination was also carried out However, beginning in the first part of the 20th century, chemical methods were developed for synthetic production of commercial iron oxidesIron Oxide Pigments 911Metallurgist2024年3月20日 Electrochemical production of iron metal can support a decarbonized process for steelmaking Here, we report a lowtemperature, electrochemical cell that consumes lowcost and abundant iron oxide, salt, and water, while producing both iron and the alkaline electrolyte needed for efficient operation of the cell Coproduction of iron, lye, and chlorine leads to a process Electrochemical chloriron process for iron production from iron oxide
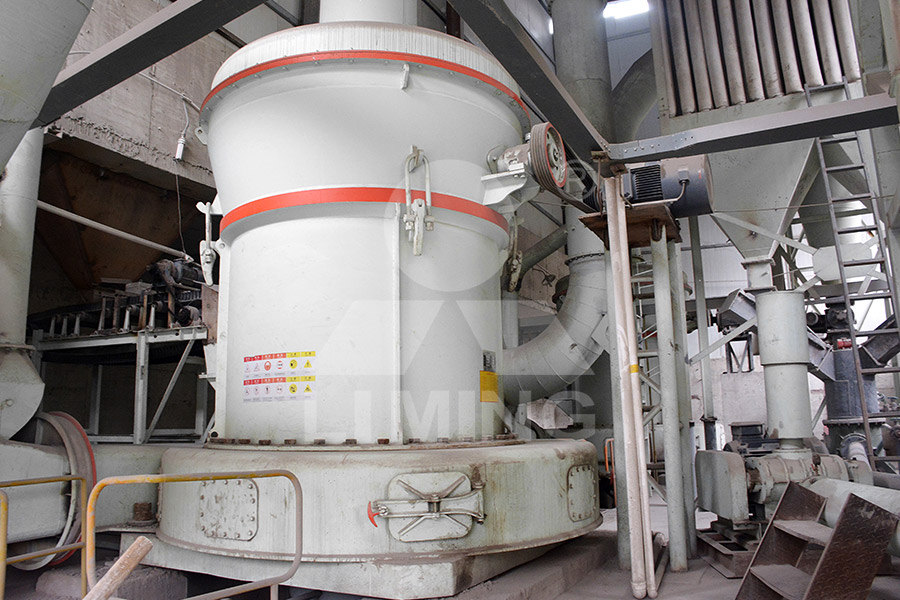
Iron and SteelMaking Process SpringerLink
2020年6月10日 224 Direct Reduction of Iron Oxide by Solid Carbon The direct reduction process of iron oxide by solid carbon is highly endothermic in nature and occurs when the molten slag flows over incandescent coke in the bosh region at a temperature above 1000 °C Therefore, the corresponding reaction can be written as follows:2024年10月15日 The article deals with the H 2 consumption for different processing conditions and the composition of the processed pellets during the direct reduction process The experiments are carried out at 600–1300 °C, with gas pressures of 1–5 bar, gas flow rates of 1–5 L min −1, and basicity indices of 0 to 215Pellets with different compositions of TiO 2, Al 2 O 3, CaO, Optimization of Hydrogen Utilization and Process Efficiency in the 2008年2月1日 PDF ÖzcanTaşkin G, Padron G, Ding, P, Pacek A, Xie L, Rielly, C (2008) Processing of red and yellow iron oxide nanoparticles Find, read and cite Processing of red and yellow iron oxide nanoparticlesproduct The estimated iron oxide production was estimated at 82,088 tpa Fe 2 O 3 The estimated credit for the iron oxide product was approximately $82 per ton of TiO 2 product This byproduct credit has an adjusted production cost of $713 per ton of TiO 2 A production cost of under $1,000 per ton appears favorable compared to other producersPilotScale Demonstration of Ilmenite Processing Technology
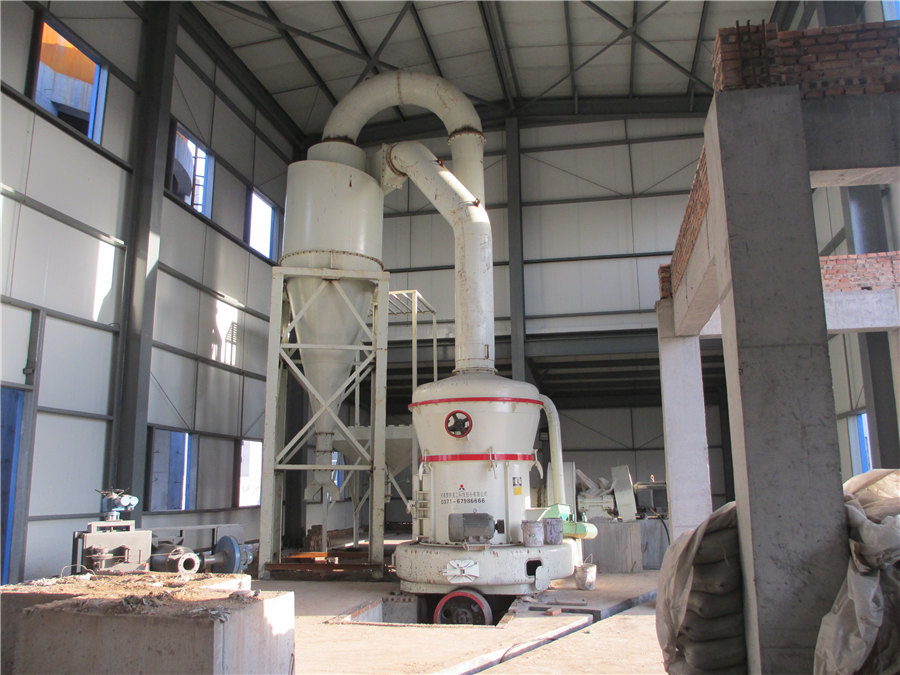
Production of Yellow Iron Oxide Pigments by Integration of the
2014年1月16日 To resolve problems with the traditional air oxidation process for producing yellow iron oxide pigments, an integration of bipolar membrane electrodialysis (BMED) with the air oxidation process was proposed Before the integration, both the individual air oxidation process and the BMED process were investigated The matching conditions for the integration were 2019年11月19日 PDF A tremendous amount of research has been done on refining the flotation process for iron ore and designing the reagents which go into it This Find, read and cite all the research you (PDF) Flotation of Iron Ores: A Review ResearchGate2024年10月15日 The article deals with the H 2 consumption for different processing conditions and the composition of the processed pellets during the direct reduction process The experiments are carried out at 600–1300 °C, with gas pressures of 1–5 bar, gas flow rates of 1–5 L min −1, and basicity indices of 0 to 215Pellets with different compositions of TiO 2, Al 2 O 3, CaO, Optimization of Hydrogen Utilization and Process Efficiency in the 2020年6月10日 Fenton is considered to be one of the most effective advanced treatment processes in the removal of many hazardous organic pollutants from refractory/toxic wastewater It has many advantages, but drawbacks are Advancements in the Fenton Process for
.jpg)
Iron Mining Process Equipment Flow Cases JXSC
3 This iron ore slurry is pumped to the agitation tank This iron ore slurry is finally pumped to the flotation machine with the fine sulfide ore (~0074 mm) going to froth flotation cells for recovery of iron 4 In the magnetite processing plant, the process of flotation separation is replaced by magnetic separation2015年3月1日 This design guideline covers the basic elements of Process Flow Sheets in sufficient detail to allow an engineer to design a flow sheet with the suitable symbols of equipment, line, indicator and PROCESS FLOW SHEET, Kolmetz Handbook of Process Equipment Design2020年3月19日 Production of Iron Oxide Nanoparticles by CoPrecipitation method with Optimization Studies of Processing Temperature, pH and Stirring Rate(PDF) Production of Iron Oxide Nanoparticles by Co2023年9月8日 “Blast Furnace process optimization for sustain able Iron making” 9 Page mathematical flow rate model for burden flow has been successfully developed and thoroughly validated usin g realBlast Furnace process optimization for sustainable Iron making
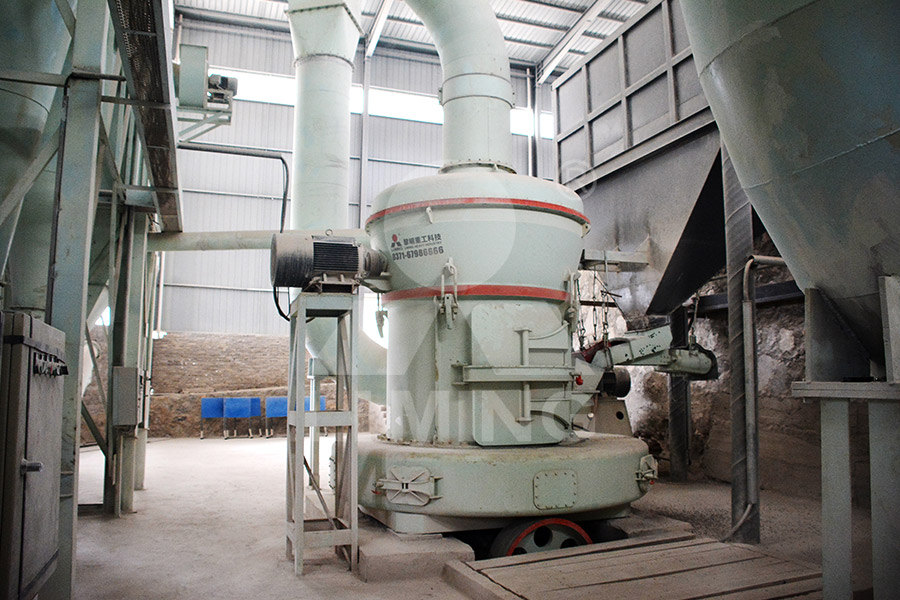
SPECIAL IRON ORE PROCESSING ISSUE Development of a process
the above gravity separation process were subjected to a size reduction process to achieve 80% passing 0150 mm size The 45% hematite and 418% quartz particles fall under the size category below 75µm Thus, the ground product of the gravity separation process and fine material obtained from the original2024年4月25日 Approved by Dr Andrea Middleton Yellow iron oxide is a versatile pigment used across various industries, mostly deemed safe by regulatory standards In cosmetics and pharmaceuticals, strict purity regulations minimize health risks In the food industry, it's a colorant consumed safely within limits Industrially, proper safety protocols can mitigate inhalation or Is Yellow Iron Oxide Bad For You? Here Is Your Answer2020年2月1日 Optimization studies were carried out in the production of γFe2O3 nanoparticles by using coprecipitation method Iron (II) chloride and iron (III) chloride were used as precursors which are dissolved in distilled water followed by centrifugation, drying and grinding process in order to obtain dried dark brown precipitated γFe2O3 powderProduction of Iron Oxide Nanoparticles by CoPrecipitation A concentration of 120 g/L of Fe is achieved by a countercurrent solvent extraction process with controlled O/A ratios, flow rate, temperature, and organics of desired composition The ironcontaining aqueous phase can be converted Innovative Process for the Production of Titanium
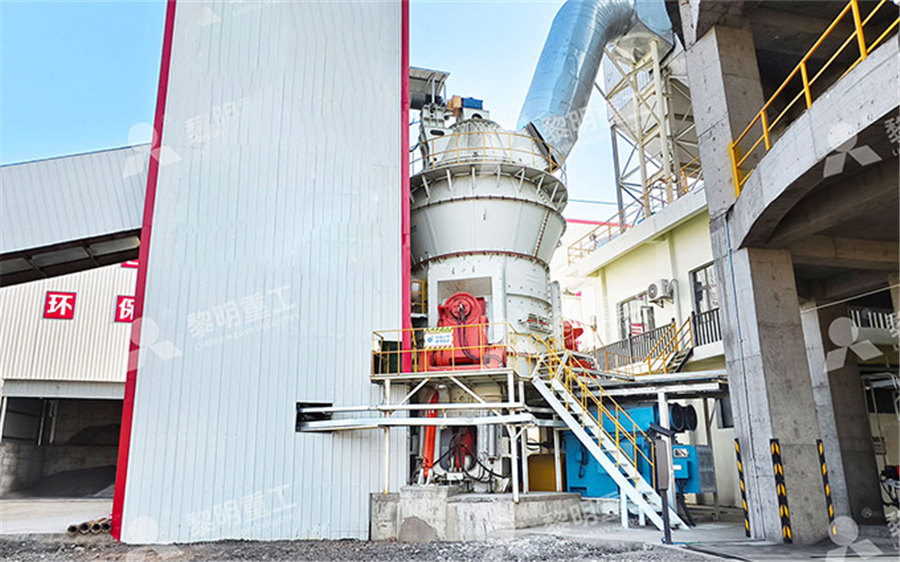
Semiconductor Manufacturing Process: Steps,
2024年10月12日 The photolithography process and the etching process are repeated several times on the wafer layer by layer Here, an insulating film that separates and protects the stacked circuits is required It is called a thin film 2016年2月29日 The smelting process involves several operations, retorting, smelting and refining Gold Alloys The most known gold alloys are made with silver The proportion between gold and silver changes the alloy color In this Gold Smelting Refining Process 911Metallurgist2017年4月9日 The productivity gains of the Midrex process is due to (i) larger capacity shaft furnaces due to scaleup of the process equipment, (ii) continual refinement of the process which includes increased heat recovery, (iii) improved catalysts, (iv) hot briquetting, and (v) incorporation of new technologies such as double bustle, insitu reforming, oxide coating, thin wall Midrex Process for Direct Reduction of Iron Ore – IspatGuru4 天之前 Copper industrial minerals include: natural copper, chalcopyrite, chalcocite, tetrahedrite, azurite, malachite, etc Chalcopyrite (a compound of copper, sulfur, and iron) is mined mainly, followed by chalcocite and bornite If copper ore wants to be fully utilized, it must be processed by flotation Flotation separation is an important copper ore beneficiation process in Copper Ore Processing Plants, Flow And Equipment
.jpg)
(PDF) Iron Ore Sintering: Process ResearchGate
2017年2月16日 Sintering is a thermal agglomeration process that is applied to a mixture of iron ore fines, recycled ironmaking products, fluxes, slagforming agents and solid fuel (coke)2024年4月26日 The final stage in iron ore processing is ironmaking, where the iron ore is transformed into molten iron through a process called reduction The most common method of ironmaking is the blast furnace route In a blast furnace, iron ore, coke (carbon), and fluxes (limestone or dolomite) are loaded into the furnace from the topIron Ore Processing: From Extraction to ManufacturingPDF On Aug 3, 2018, Md Quddus and others published Synthesis and Characterization of Pigment Grade Red Iron Oxide from Mill Scale Find, read and cite all the research you need on ResearchGateSynthesis and Characterization of Pigment Grade Red Iron Oxide Iron sponge is normally sold in the US by the bushel The volume in bushels can be determined from the following equation once the bed dimensions of diameter and height are known: where Bu = volume, bushels The amount of iron oxide that is impregnated on the wood chips is normally specified in units of pounds of iron oxide (Fe2O3) per bushelDesign Procedures For Iron Sponge Unit Oil Gas Process
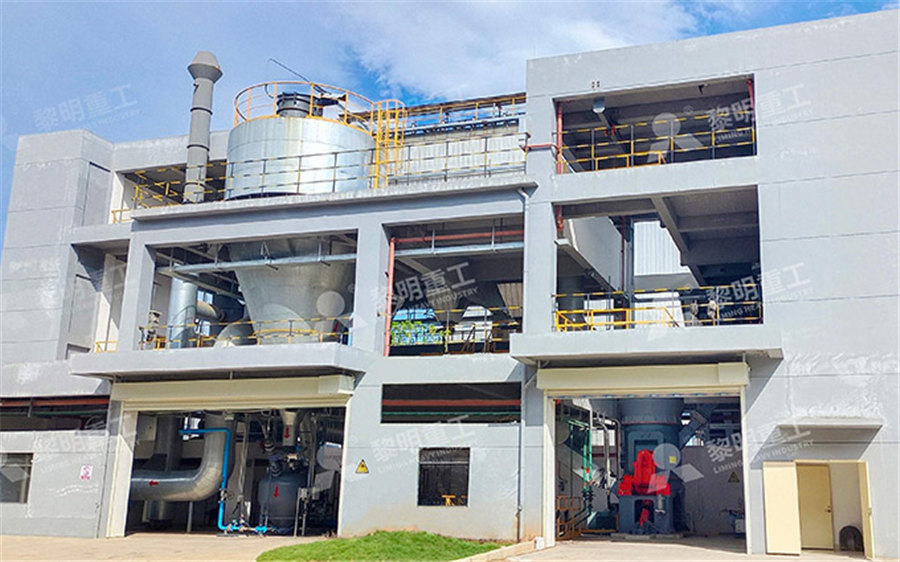
(PDF) Iron oxide red wastewater treatment and recycling of iron
2015年1月15日 The paper presents a wastewater treatment process and recycling of iron sludge from wastewater treatment for iron oxide red production Results show that: (1) Sludge from wastewater treatment