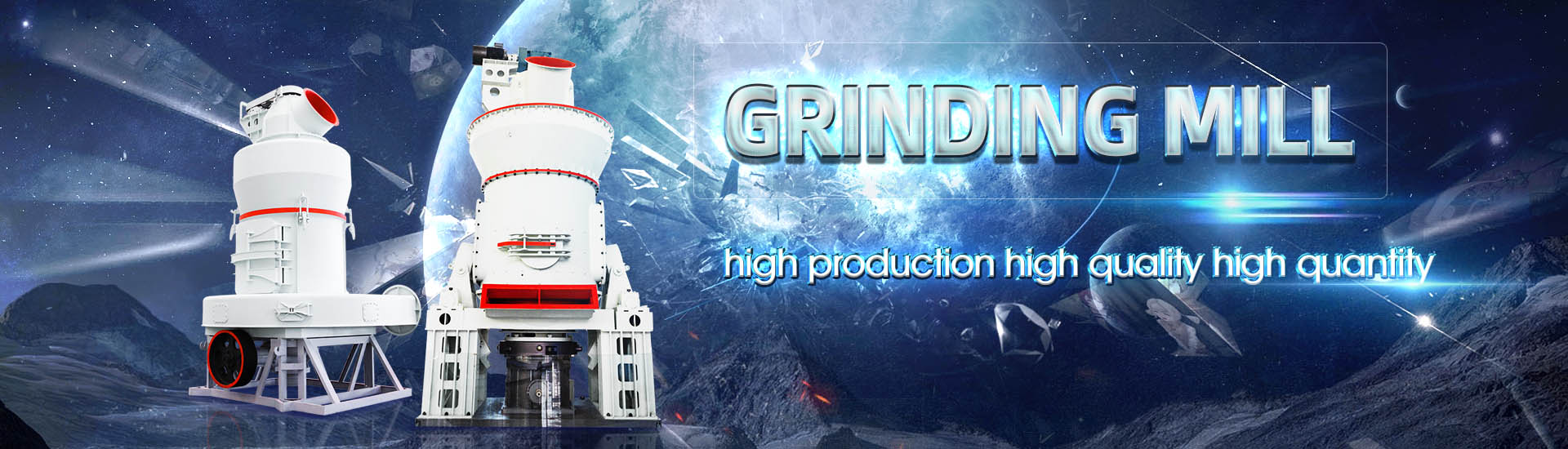
Equipment for producing slag iron
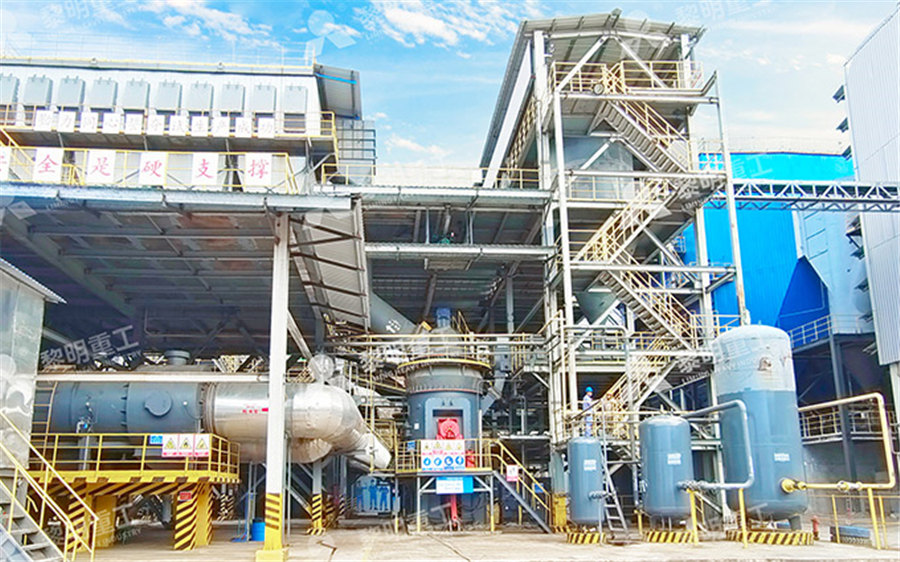
Products › Ironmaking and steelmaking › Slag
Slag granulation using water sprays is now an established technology that not only simplifies blast furnace casting floor operations but also provides an economical route for producing of a valuable raw material for a host of magnetic separation treatment of the slag to recover the metal iron, ③ crushing and classification of the slag for grain size adjustment to manufacture the slag product, and ④ aging treatment Processing and Reusing Technologies for Steelmaking Slag2024年4月1日 Natural minerals such as wollastonite, olivine, serpentine, and alkaline industrial waste, including steel and ironmaking slag, coal fly ash, and mining waste, can serve as Carbon mineralization of steel and ironmaking slag: Paving the 2021年11月3日 A system analysis of advantages and features of the semiindustrial pilot HVGplant showed that its operation for granulation of slag melts of ferrous metallurgy in enterprises A new technological approach to the granulation of slag melts of
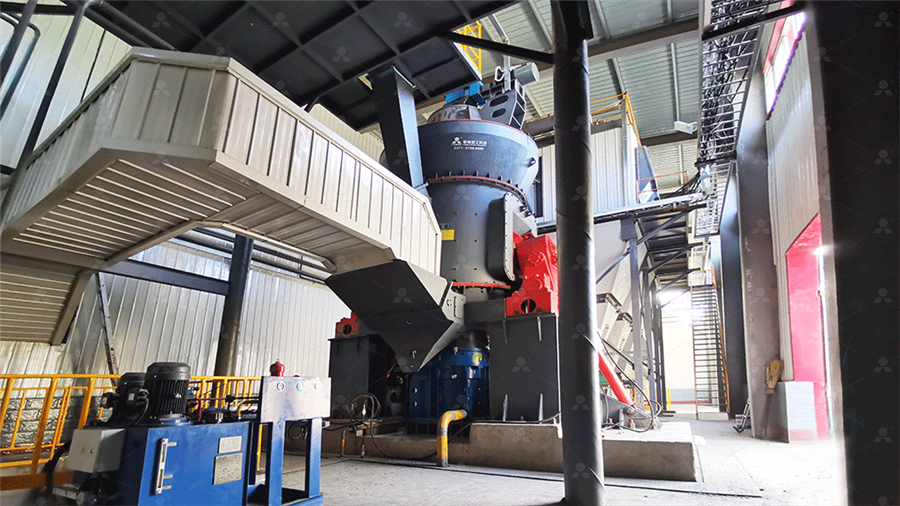
Critical review of applications of iron and steel slags for carbon
2019年1月8日 Iron slag is generated upon treating the iron ores with flux containing limestone to produce pig iron (called ironmaking) Steel slag is generated upon further refining of the 2016年11月20日 In the electric arc furnace process, the electric arc furnace oxidizing slag (EAFOS) is firstly produced when iron scrap is melted and refined into steel, and then the Integrated and innovative steel slag utilization for iron reclamation 2005年2月1日 Environmental concerns and economic realities demand that slag production in iron and steelmaking processes can be reduced and that slag can be effectively utilized Discover the world's(PDF) Industrial uses of slag The use and reuse of iron 2024年6月12日 SS comprises various slags, including basic oxygen furnace slag (BOFS) (or converter slag), electric arc furnace slag (EAFS), ladle furnace slag (LFS), and argonoxygen Recycling of iron and steel slag for carbon reduction and low
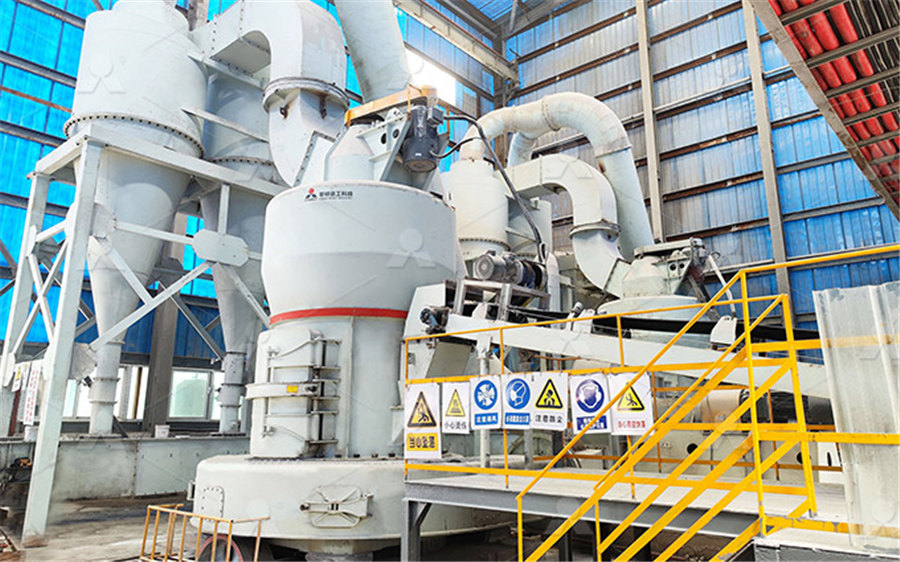
Basics of slag production Article on the slag industry from Global Slag
2011年10月27日 Slags from the Iron and Steel Industry Background With world steel production now well over a billion tonnes per year, the slag that arises from some of the processes involved is a major resource Traditionally it has been used mainly as an aggregate but for some types there are other applications, such as a raw material for cement or as a known as steel slag Slag output obtained during pig iron and steel production is variable and depends mainly on composition of raw materials and type of furnace Typically, for ore feed containing 60 to 65% iron, blast furnace (BF) slag production ranges from about 300 to 540 kg per tonne of pig or crude iron producedSlaglIron and Steel IBM2018年11月7日 Steelmaking plants continuously strive to reduce the environmental load in the steelmaking process, resulting in the recycling of energy, water, and other byproducts In this chapter, techniques for the Treatments and Recycling of Metallurgical SlagsMolten iron is then allowed to run out the bottom of the furnace, leaving the slag behind Originally, the iron was collected in pools called pigs, which is the origin of the name pig iron Figure \(\PageIndex{1}\): A Blast Furnace for Converting Iron Oxides to Iron Metal233: Metallurgy of Iron and Steel Chemistry LibreTexts
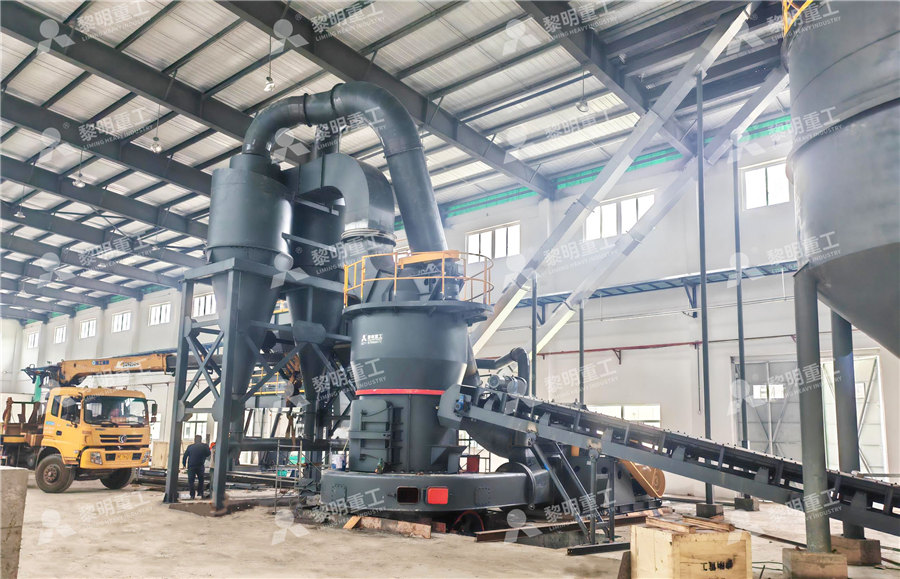
Rock wool : Iron and steel slag products : NIPPON SLAG
HOME > About Iron and Steel Slag > Iron and steel slag products > Rock wool Blast furnace slag and other materials are either heated and remelted in a cupola or electric arc furnace at 1,500 1,600℃ , or else after being removed from the blast furnace the molten slag is kept at approximately the same high temperature and is allowed to flow out from the bottom of the Titanium dioxide slag is the principal product, with pig iron being a coproduct Titanium dioxide slag is largely used as a raw material for producing white pigment, mostly for the paint and plastics industries Richards Bay Minerals Process Flow Basic reactions in ilmenite smelting are: Reduction of FeO from slag FeO + C → Fe + COPig iron Ilmenite route International Iron Metallics AssociationThe invention relates to a method for producing titanium oxidecontaining slag and pig iron from ilmenite The method is characterized in that it comprises the steps: a) prereducing ilmenite in the presence of reductant in a prereduction reactor to metallize at least part of iron in the ilmenite; b) optionally removing unreacted reductant and gangue from the prereduced ilmenite; and c Method for producing titanium oxidecontaining slag and pig iron 2021年11月3日 Pilot scale research demonstrated that the designed equipment for the HVG technology allows sustainable control of the quality of granules, (blast furnace and electrocarbothermic production of pig iron and ferroalloys), slag melts generated as byproducts during metal/alloy smelting rank first by their scale and ecological hazardA new technological approach to the granulation of slag melts of
.jpg)
Steel slag recycling crushing and grinding production line
The magnetic steel slag water washing, ball mill, magnetic separation, purification process and comprehensive slag recycling technology and complete sets of equipment developed and developed by CM Mining Machinery can not only realize water recycling, but also have high purification grade of slag steel (TFe>90%), iron content The grade of slag powder reaches 55%Slag) and GGBFS (Ground Granulated Blast Furnace Slag) as stabilising binders in recent years has significantly increased the area of usage The types of slag covered in this guide are: 1 Blast Furnace Slag — known as BF Slag or BFS or Rock Slag (iron process) 2 Basic Oxygen Steel Slag — known as BOS Slag or BOS (steel process) 1 guide to the use of iron and steel slag in roadsContinuous smelting of ilmenite feed in a DC open arc furnace has become the benchmark technology for the efficient production of TiO₂ slag and saleable pig iron as byproduct Tenova Pyromet’s DC arc furnace technology allows our DC Arc Furnace for smelting Ilmenite and producing 2024年6月12日 1 INTRODUCTION Blast furnace slag (BFS) and steel slag (SS), as industrial solid wastes produced in the process of steelmaking, account for 80%–90% of the total smelting slag [] BFS accounts for about 30% of pig iron output, [] while SS accounts for 10%–15% of the crude steel output [] SS comprises various slags, including basic oxygen furnace slag (BOFS) Recycling of iron and steel slag for carbon reduction and low
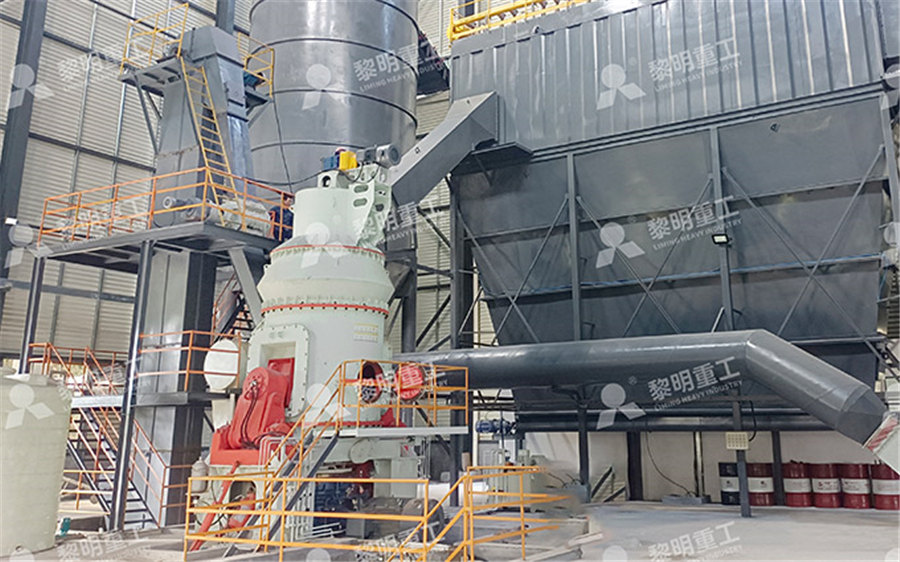
Carbon mineralization of steel and ironmaking slag: Paving the
2024年4月1日 Carbon mineralization technology has emerged as a promising method for permanently sequestering CO 2 by transforming it into a thermodynamically stable solid carbonate material Recently, alkaline industrial waste, particularly from steel and ironmaking processes, has been identified as a proper feedstock due to its high potential for CO 2 storage and the smelt so that the slag could run out (Figure 1) The resulting tap slag has a flowed appearance, like lava (Figure 2) From the Iron Age and Saxon periods, ‘slagpit’ or ‘nontapping’ furnaces are known, such as the probable PreRoman example from Levisham Moor, North Yorkshire During the smelt, the slagHistoric England – Preindustial Ironworks – Introductions to 2024年4月26日 If you want to know more details about equipment, solutions, etc, The limestone or dolomite reacts with impurities, forming a slag that floats on top of the molten iron The molten iron, known as hot metal, each stage plays a crucial role in producing highquality iron ore productsIron Ore Processing: From Extraction to Manufacturing2024年5月26日 Mineral carbonation is one of the known methods for carbon capture, utilization, and storage (CCUS) Slag from the steel industry is studied as a common source of CaCO3 via mineral carbonation owing to its high Ca content Despite numerous preliminary studies, the optimal factors governing the mineral carbonation of steelmaking slag, such as extraction and Experimental study on indirect mineral carbonation using five
.jpg)
Vanadium extraction from steel slag: Generation, recycling and
2024年2月15日 The problem of steel slag could be solved by expanding the utilization ways of steel slag At present, steel slag has been used in the production of cement, the construction of urban roads and the production of fertilizer (Fronek et al, 2012; Jiang et al, 2018b; Shi and Qian, 2000; Wang and Cai, 2006)In developed countries, the utilization rate of steel slag is close to 2018年5月5日 PDF Refractory materials are essential for the production of iron and steel Fig 2 Layout of equipment for recycling of steel and slag in the EAF at Ferri ere Nord [5]A review on recycling of refractories for the iron and steel 2018年1月11日 The submerged electric arc furnace (SAF) has proven a versatile unit in numerous metallurgical applications for more than a century Countless innovations have made this furnace type become the most commonly used furnace for increased metal recoveries and slagcleaning operations In many applications, SAFs are also employed as primary melting The Submerged Arc Furnace (SAF): StateoftheArt Metal2023年10月6日 The smelting process of blast furnace is carried out in the shaft furnace of a closed countercurrent reactor and heat exchanger The complex physical changes and chemical reactions are completed in the process of the countercurrent movement of the charge and gas in which the raw materials containing iron oxide (sinter, pellets, etc), coke, slag flux (limestone) Blast Furnace Ironmaking SpringerLink
.jpg)
Gasshielded metal cored wire developed for
Gasshielded metal cored wire developed for producing antiwear coatings (tungsten carbides in an iron base matrix) on parts subject Features and benefits High density and regular distribution of carbide phases in martensitic matrix Industrial byproduct utilization in concrete has been an important choice of researchers over the years (Khan et al, 2016; Qasrawi, 2014)Steel slag has been utilized as aggregate/cementing material in concrete by various researchers over the years (Faraone et al, 2009)Recycling of metallurgical byproducts will ensure the sustainable industrial production and greener Recent applications of steel slag in construction industry2024年1月26日 All primary equipment and a significant part of auxiliary equipment must be continuously operated without failures or accidents throughout the entire blast furnace campaign, ie, for 20 – 25 years Blast Furnace Blast Furnace Equipment: A Comprehensive Overview2020年8月19日 Pig iron Slag Blast furnace gas Energy entrance: Hot blast Chemical energy of both the coke and pulverized coal Energy associated with the dissolution of elements in the liquid iron Energy associated with the formation of chemical phases in the slag Energy exit: Pig iron Slag Reduction reactions Blast furnace gas Heat lossesProduction of Iron in the Blast Furnace SpringerLink
.jpg)
slag production equipment KOOKS
mineral processing ore slag production equipment production In the production of iron, iron ore, iron scrap, and fluxes limestone and/or gradation requirements using conventional aggregate processing equipment process or by adding the slag to known as steel slag Slag output obtained during pig iron and steel production is variable and depends mainly on composition of raw materials and type of furnace Typically, for ore feed containing 60 to 65% iron, blast furnace (BF) slag production ranges from about 300 to 540 kg per tonne of pig or crude iron producedSlaglIron and Steel2021年9月27日 Application of electromotive force between molten iron–carbon and slag is shown to decarburize iron Electrorefining decarburizes by direct interfacial electrochemical reaction, resulting in low Electrorefining for direct decarburization of molten iron2024年11月4日 Use our notes to revise the extraction of iron from hematite for IGCSE Chemistry Learn the reactions that occur in the Blast Furnace This melts and collects as a molten slag floating on top of the molten iron, which is tapped off separately IBO was not involved in the production of, Extraction of iron IGCSE Chemistry Revision Notes Save My
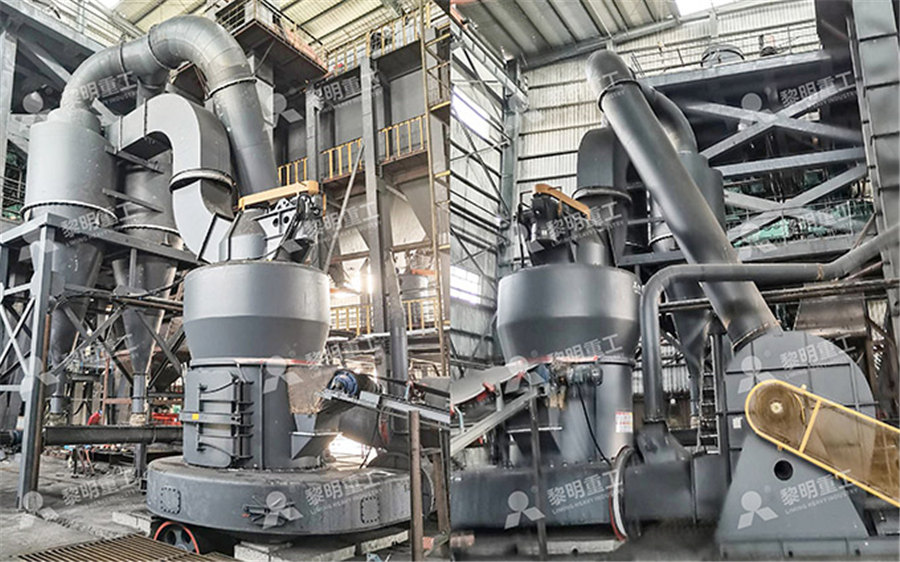
RECOMMENDED GUIDELINE FOR IRON STEEL SECTOR
This entire process of production of hot metal is associated with various safety hazards like hit / entanglement with mobile equipment, burns, fire, slip fall, exposure to dust, smoke, noise, heat gas etc 2 SCOPE This placed on the iron slag side respectively of the Furnace iii) 2017年10月17日 Figure 1: Steelmaking byproducts for blast furnace (BF), basic oxygen furnace (BOF) and electric arc furnace (EAF) processes Source: World Steel Association (worldsteel) The first step in the production of steel or cast iron alloys is the reduction of iron ore—which contains iron oxide and gangue or mineral impurities—to unrefined, reduced iron formFrom Ore to Iron with Smelting and Direct Iron ReductionThe production of iron from its ore involves an oxidationreduction reaction carried out in a blast furnace Iron ore is usually a mixture of iron and vast quantities of impurities such as sand and clay referred to as gangue The iron found in iron ores are found in the form of iron oxidesIron Production Chemistry LibreTexts2023年11月20日 Mineral process wastes, such as metallurgical slags nowadays, are of significant metals and materials resources in the circular economy The usability of ironmaking slag is well established; however, steel A Review on Environmental Concerns and
.jpg)
Gold Smelting Refining Process 911Metallurgist
2016年2月29日 Gold Smelting Equipment Although slag production weight is variable, a typical operation can generate 10 kilos of slag per 1000 oz of gold The presence of manganese minerals is note for a lavender color slag Green slag Slag output obtained during pig iron and steel production is variable and depends mainly on composition of raw materials and type of furnace Typically, for ore feed containing 60 to 65% iron, blast furnace (BF) slag production ranges from SLAG IRON AND STEEL Indian Minerals Yearbook 2017 IBMMolten iron and slag collect in the furnace hearth Being less dense, the slag floats on top of the iron Slag and iron are tapped at regular intervals through separate tap holes For merchant pig iron production, the iron is cast into ingots; in integrated steel mills, the molten iron or hot metal is transferred in torpedo ladle cars to the Pig iron blast furnace route International Iron MetallicsThe utility model is suitable for a slag powder edulcoration field provides a deironing equipment that slag powder production used, and the cooling box up end both sides all are equipped with the guide rail, and the guide rail upper end is equipped with cooling sprinkler, and cooling sprinkler bottom surface is close to both sides position and is equipped with two electronic sliders, and CNU Iron removal equipment for producing steel slag
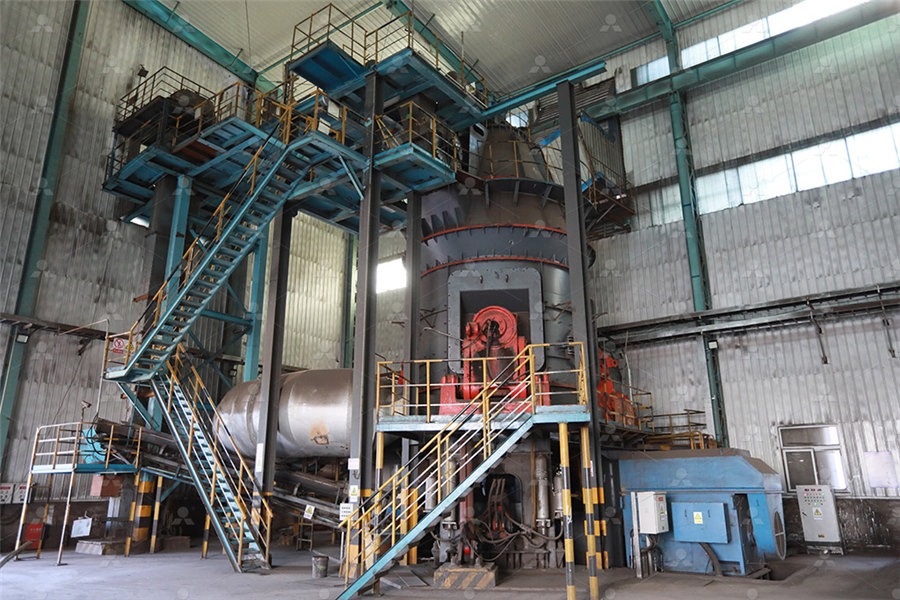
Slag recycling recovery
The data for the EU28 are derived from the reports published by the 19 most important countries and data from the World Steel Association for pig iron production The result for 2018 comes to 207 Mta of blast furnace slag and 163 Mta of steelworks slag or By converting low value aircooled blast furnace slag into a high value material for the cement/construction industry, this process turns a waste product into wealth We are partnering with Beijing MCC Equipment Research Design Corporation (MCCE) to commercialise the dry slag granulation technologyDry slag granulation: producing valuable byproducts from waste2017年10月10日 Ironmaking Blast Furnace Iron is made by reacting iron ore (iron oxide and impurities), coke (a reductant) and limestone (CaCO 3) in a blast furnace Iron ores with lower iron content such as taconite are first processed to Ironmaking 101 – From Ore to Iron with Blast Furnaces23 25 5 2012, Brno, Czech Republic, EU Table 1 Slag production in the Czech Republic (2006 year) Literature presents oneyear worldwide production approximately 50,000 kt steel slags and from SLAG FROM PRODUCTION OF PIG IRON AND STEEL MAKING