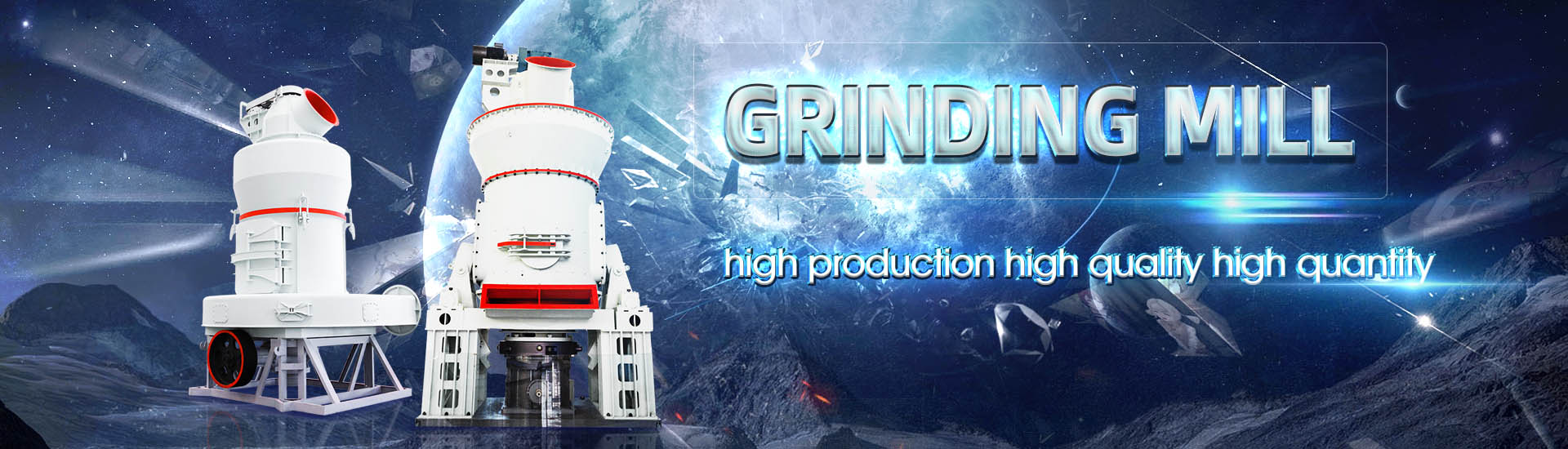
ore powder mill mining and backfilling
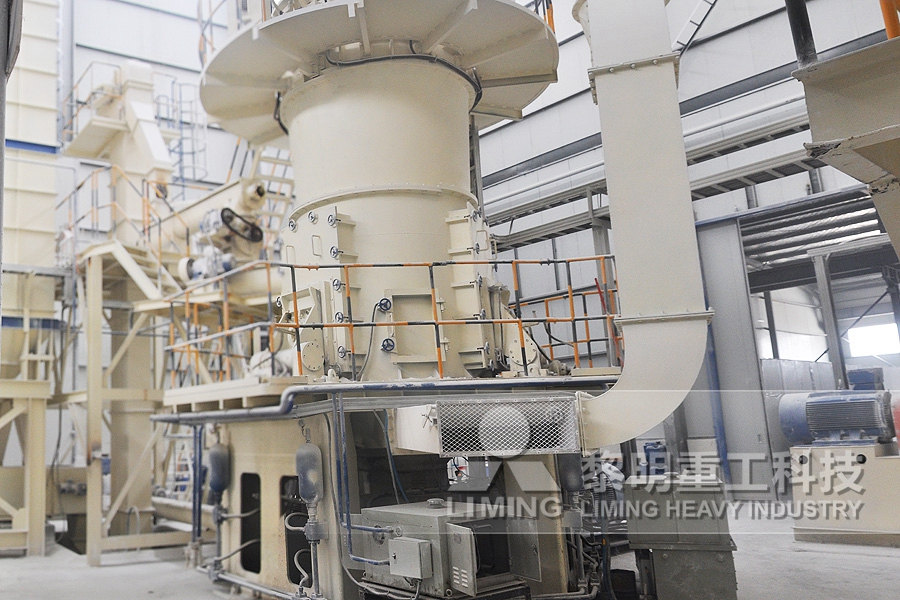
Utilization of mill tailings, fly ash and slag as mine paste backfill
2021年11月22日 Critical review on utilising mill tailings, fly ash and slag in mine paste backfilling Explains strength prediction using statistical and artificial intelligence techniques Economics plays a key role in paste backfill application in underground mines Elucidates 2007年5月1日 Backfilling is required for the continuance and efficiency of mining operations Additional benefits include: improved regional and local rock (PDF) Underground Mining with Backfills ResearchGate2022年8月13日 This paper systematically reviews the recent development of mining with backfill methods, and the new technology application progresses were introduced from three aspects: highefficiency and(PDF) Research Progress on Mining with Backfill 2023年4月26日 This review paper describes the development history of metal mine filling mining in China and the characteristics of each stage The excitation mechanism and current research status ofProgress and prospects of mining with backfill in metal
.jpg)
Innovative mine backfill materials and structures Taylor Francis
2023年12月25日 Capable mining methods with diverse fill types such as cementitious tail/paste backfill (CTB/CPB) in metal mines and cementitious gangue/ash backfill in coal mines can 2024年3月1日 Cemented paste backfill technology plays a pivotal role in promoting green mining within the metal industry The technology allows safely backfilling of surface tailings into Key theory and technology of cemented paste backfill for green 2024年3月13日 Mine backfilling has various benefits, including preventing ore dilution, improving waste utilization, raising output, and enhancing the integrity of subterranean structures A detailed review study on utilization of mine and industrial wastes One of their US mines in Montana, Stillwater Mining Company, owns and operates underground mines for PGM ore and a Concentrator plant The process involves mining, transporting the SIMULATING BACKFILL OPERATIONS FOR UNDERGROUND
.jpg)
Extraction and Backfill Scheduling in a Complex Underground
We solve our integer programming model with a heuristic to produce a schedule that adds value to the mining operation by (1) shifting metal production forward, (2) reducing waste mining and 2023年7月16日 The filling of underground mines with mine tailings allows the return of mining waste material to its origin, considerably reducing the amount of mine tailings deposited on the surface, thus decreasing the number of mining Experiences of Underground Mine Backfilling Using 2023年4月26日 Mining is the foundation of modern industrial development In the context of the “carbon peaking and carbon neutrality” era, countries have put forward the development strategy of “adhering to the harmonious coexistence Progress and prospects of mining with backfill in 2021年11月22日 In mining, the development of the ore deposits generates waste rock Along with the mine development waste, fragmented waste rock and subgrade minerals are also generated [1] The other category of solid waste generated during mineral processing (separation of valuable minerals from the ores) is called mill tailingsUtilization of mill tailings, fly ash and slag as mine paste backfill
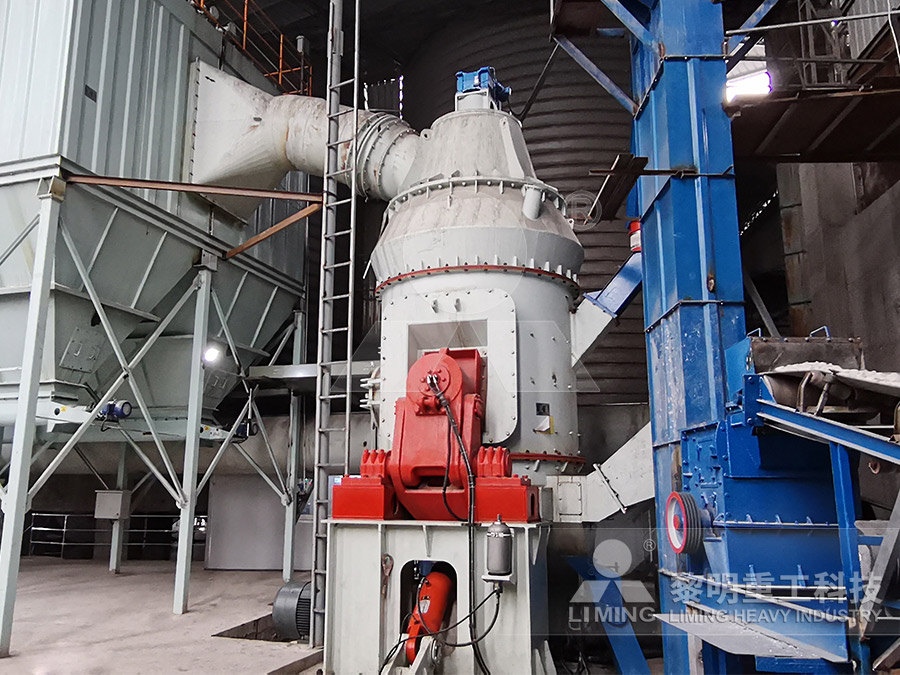
Underground Mine Backfilling Transition in Sukinda, Odisha:
2023年10月26日 23 Water Drainage Characteristics A significant concern for any hydraulic backfill is the liquefaction potential of the backfill mass Liquefaction occurs when the pore pressure increases dramatically, thus reducing the effect stress in the fill mass, to the point where the shear resistance of the fill mass is so low that the mass begins to flow like a liquid2007年5月1日 The change in perception of backfilling from an additional cost to mining operations to one of a preprofit activity will aid the required advancement in technology required for backfills(PDF) Underground Mining with Backfills ResearchGate2022年11月16日 In the mining sector, backfilling can vary, depending on the need In many cases, it’s simply the process of refilling holes that have been dug up or found (mining voids) during the mining process In others, it may involve mixing soil with other products (such as cement or binding agents) to create specific backfilling solutionsWhat is Backfilling? A Guide to Backfill in Mining and ConstructionBackfilling for Safety and Efficiency A large number of mines use backfill for stabilization and safety, as well as for reaching the ore and preserving the environment Used mainly in sublevel open stoping and cut and fill mining, a good knowledge of fill types, preparation methods and how these are applied is decisive for successful resultsBackfilling for Safety and Efficiency Black Diamond Drilling
.jpg)
Iron Ore Processing: From Extraction to Manufacturing Mining
2024年4月26日 In this method, largescale excavation machinery, such as excavators and haul trucks, is used to remove the overburden (surface material) and expose the ore deposit The ore is then extracted and transported to the processing plant b Underground Mining: Underground mining is employed when the iron ore deposit is located at significant depthsmilling ore into powder and backfilling the mined out cavities in the underground with tailings from milling operation The circular dependency between mining and backfilling operations, along with variability for each task, the mill, which in turn depend on rate of mining activities, which depends on how quickly BFO canSIMULATING BACKFILL OPERATIONS FOR UNDERGROUND MINING The rod mill is another type of grinding mill used in the copper ore mining process This machine uses steel rods as the grinding media instead of balls, which are commonly used in ball mills The rods grind the ore by tumbling within the mill, similar to the action of a rotating drumUnderstanding the SAG Mill in Copper Ore Mining Process2023年12月13日 Continuous mining and continuous backfilling (CMCB) is an effective method to control surface subsidence and implement resource utilization of solid waste To address the issue of asymmetric deformation of the surrounding rock, threatening the overall stability of roadways with CMCB, the deformation characteristics of the roadways at the 2112 CMCB Asymmetric Deformation Mechanism of Roadway with Continuous Mining
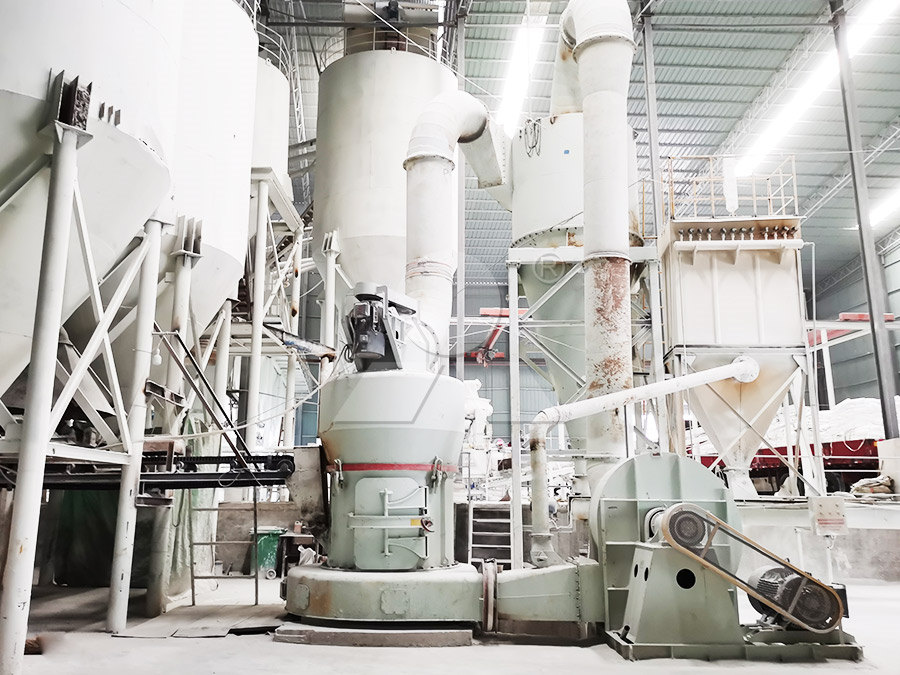
Characterization of lead–zinc mill tailings, fly ash and their
2019年7月10日 Surface disposal of mill tailings and fly ash is a major concern for many countries, as it pollutes the environment including air, water, and soil Paste backfilling is an emerging mine backfilling technique, wherein the industrial wastes such as mill tailings, fly ash and blast furnace slag are backfilled inside the stopes This study examines the physico 2016年3月1日 Valorization of mining waste and tailings through paste backfilling solution, Imiter operation, MoroccoValorization of mining waste and tailings through paste backfilling 2015年5月13日 Underground mine backfilling is a form of ground improvement that has to be carried out in the mine sites The backfilling provides ground support and regional stability, thus facilitating ore removal from nearby Underground Mine Backfilling in Australia Using Backfill (Hydro fill Paste fill) plants commissioned at Mochia and Zawarmala mines, respectively, to improve Mining Ore Recovery and global stability; Obtained Environmental Clearance for 48 Mt of Ore Production Ore Beneficiation for Zawar Group of Mines; Started opening up the New Mining Block “Purvanchal” at Balaria MineMines Performance Overview Hindustan Zinc
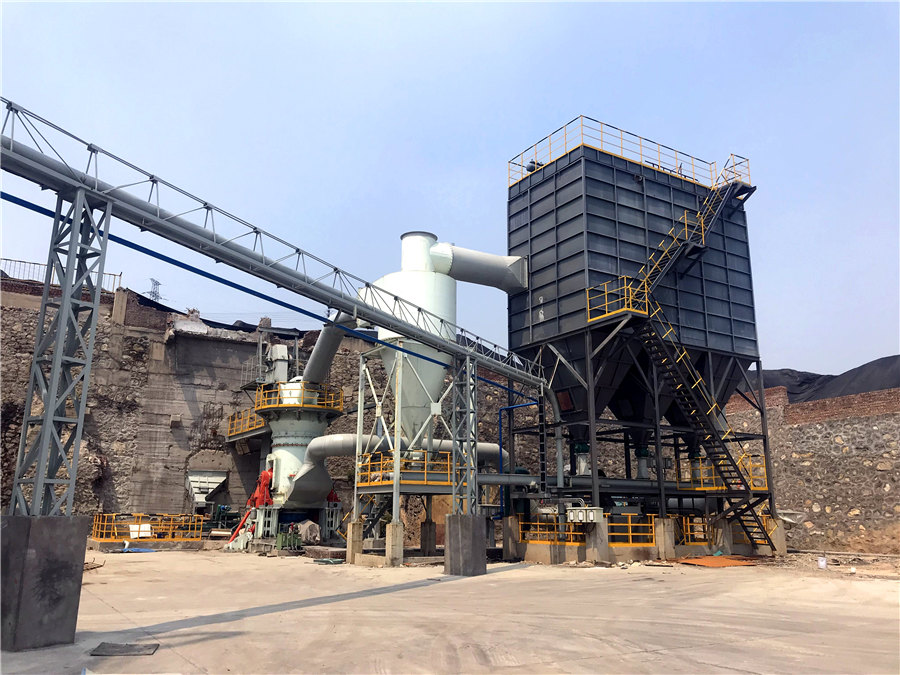
SBM Ore Ultrafine Grinding Mill
HGM ultrafine grinding mill can process nonmetallic ores with Mohs hardness less than 7 The equipment has stable operation, simple operation, long service life, low carbon and environmental protection There are 5 models of HGM ultrafine grinding mill, 2019年7月10日 Let's say, the CSH (calcium silicate hydrate) intensity value of T70S30@75CMF sample at 29 • 2θ angle was measured as roughly 4900 CPS, while the intensity value of T70S30@70 CMF sample Characterization of lead–zinc mill tailings, fly ash and their 2024年10月30日 Ore is a deposit in Earth’s crust of one or more valuable mineralsThe most valuable ore deposits contain metals crucial to industry and trade, like copper, gold, and iron Copper ore is mined for a variety of industrial uses Copper, an excellent conductor of electricity, is used as electrical wire Copper is also used in constructionOre National Geographic SocietyPDF On Jan 1, 2013, Jim Everett published Planning an Iron Ore Mine: From Exploration Data to Informed Mining Decisions Find, read and cite all the research you need on ResearchGatePlanning an Iron Ore Mine: From Exploration Data to Informed Mining
.jpg)
Ore and Backfill Dilution in Underground Hard Rock Mining
Request PDF On Nov 1, 2021, M N Bagde published Ore and Backfill Dilution in Underground Hard Rock Mining Find, read and cite all the research you need on ResearchGate2022年8月13日 PDF Mining with backfill has been used extensively in underground metal mines which is an important way to conduct the green and lowcarbon mining (PDF) Research Progress on Mining with Backfill Technology of 2022年3月15日 Abstract The ore dilution is generally defined as the degradation of economical and valuable ore with the addition of the unwanted host rock, failed backfilled material and or ore material considered below the cutoff the grade The importance of ore dilution on the profitability of a mining operation is very well known and also well documented, since, it adds to the cost Ore and Backfill Dilution in Underground Hard Rock MiningWhen ore enters the plant from underground it first needs to be milled to reduce its size so that the gold is liberated from the host rock South Deep’s milling circuit consists of a singlestage semiautogenous grinding mill (SAG) Creating Gold Fields South Deep Gold Mine How we process
.jpg)
Advanced Analytics for Drilling and Blasting SpringerLink
Under wellcontrolled conditions, Ouchterlony et al [] assessed energy partitioning of limestone production blasts and computed inhole losses, seismic energy, the kinetic energy of throw, and fragmentation energyTheir search revealed the energy partitioning of a blast with bulk emulsion explosive would be []Crushing and other losses in the rock mass; 20–40%2014年4月1日 We use mathematical optimization to determine a production schedule (ie, a schedule of extraction and subsequent filling of the voids) for a complex underground mine in IrelandExtraction and Backfill Scheduling in a Complex Underground MineMining Western Australian iron ore mines are all open cut pits The ore is generally blasted, then trucked to a crusher where it may be separated into lump and fines component products The crushed ore is railed to a port and loaded onto ships, typically of Planning an Iron Ore Mine: From Exploration Data to Informed Mining 2017年3月4日 The type of backfill used by an underground mine operation is dependent on several factors: the configuration of the mining process, the stope sequences, and excavation sizes determined by the mining method, the depth and orientation of the orebody, and the materials available to use as backfill, focusing on tailings management requirements over the Design and Characterization of Underground Paste Backfill
.jpg)
Mining Rock Ore Grinding Ball Mill Powder Grinding Machine
The ball mill is a key equipment to grind the crushed materials after the material were broken , and carrying on the smashing again and the ball mill is widely used in powdermaking production line including cement, silicate, newtype building material, refractory material, fertilizer, ore dressing of ferrous metal and nonferrous metal, glass ceramics, etc,the ball mill carries on the 2022年5月27日 Backfilling of mine openings is typically used in coal mining for pillar replacement to enable secondary recovery, reduce surface waste, limit subsidence and control spontaneous combustionThe potential of foamed backfilling in underground mines2017年4月15日 necessity for mining and ore dressing also Frag mentation helps rapid excavation of resou rces Through a properly designed blasting pattern and safe execution, in a mine, it is possible to achieve(PDF) ROCK BLASTING FOR MINING ResearchGateOR BACKFILLING MINING METHODS by Vladirnir Straskraba President, HydroGeo Consultants, Inc and John F Abel, Jr Prof Emeritus, Colorado School of Mines ABSTRACT Zambia Consolidated Copper Mines Ltd (ZCCM) is planning a substantial increase in ore production in several of their underground mines on the Zambian Copperbelt overThe Differences in Underground Mines Dewatering with the
.jpg)
Open Pit Mining IntechOpen
2021年2月17日 Open pit mining method is one of the surface mining methods that has a traditional coneshaped excavation and is usually employed to exploit a nearsurface, nonselective and lowgrade zones deposits It often results in that adds value to the mining operation by (1) shifting metal production forward, (2) reducing waste mining and backfilling delays, (3) avoiding expensive millhalting drops in ore production, and (4) enabling smoother workforce management Keywords : underground mine production scheduling; integer programming applicationsExtraction and Backfill Scheduling in a Complex Underground Focus on the field of nonmetallic ore ultrafine powder and pursue the ultimate covering 200+ mining equipment SBM's ore grinding equipment sells well all over the world with high quality and high cost performance Grinding Mill Stone Crushing Machine Auxiliary Equipment Feeding Conveyor about Company profileAbout Us SBM Ultrafine Powder Technologymines in Montana, Stillwater Mining Company, owns and operates underground mines for PGM ore and a Concentrator plant The process involves mining, transporting the muck (ore and waste) to the surface, milling ore into powder and backfilling the mined out cavities in the underground with tailings from milling operationSIMULATING BACKFILL OPERATIONS FOR UNDERGROUND MINING
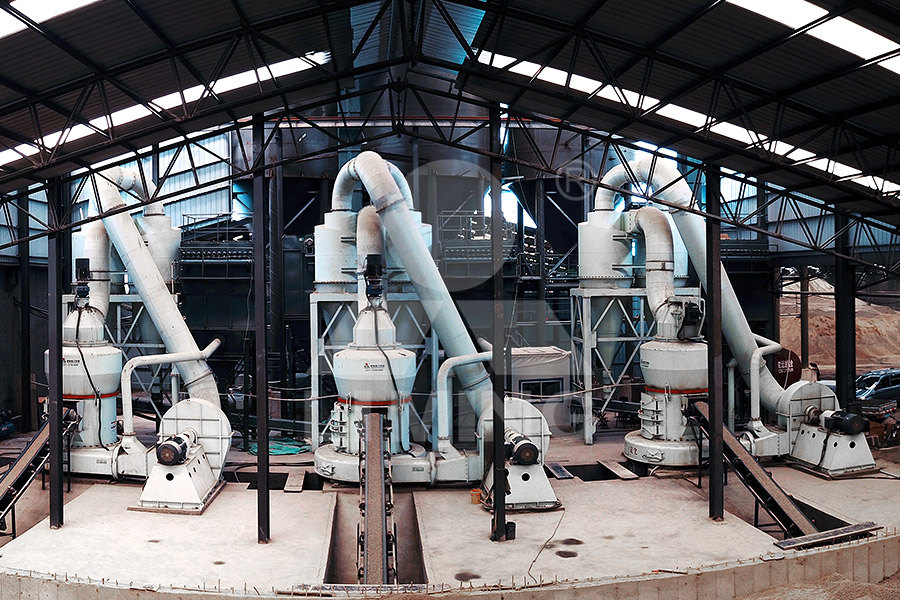
MINING, MILLING, CONVERSION, AND ENRICHMENT OF URANIUM ORES
Background to the Nuclear Fuel Cycle • 1939 – Discovery of fission of uranium by Hahn and Strassman in Germany and extra neutrons released to give possibility of a chain reaction • 1939 –1942 – Concept of an atomic bomb developed in UK U S andConcept of an atomic bomb developed in UK , US, and Germany • 1942 – Start of the Manhattan Project and the need Ore grinding is one of the key stages in the mining process It's where the ore is reduced to a fine powder, which can then be used in other stages of the extraction process Grinding performance is a critical parameter for this stage, as it affects both the speed and quality of the final product The parts of a ball millFactors affecting ores grinding performance in ball mills2021年1月15日 The present paper considers aspects of underground iron ore mining in Ukraine, in particular the level of mine production and reserves of basic ore fields It analyzes and generalizes the practice of using cemented rockfill under difficult mining and hydrogeological conditions of the PivdennoBilozerske highgrade iron ore field The Belozersky iron ore district Sustainable Underground Iron Ore Mining in Ukraine with Backfilling the metal ore and the large mining depths result in a significant increase in mining costs with increasing depth Gelling materials are the key to controlling the filling costs and helping innovate filling mining techniques and technologies [12] The Progress and prospects of mining with backfill in metal mines in
.jpg)
Slump Test:Laboratory and Numerical SimulationBased
2019年7月25日 Iron ore tailings, silica tailings, sulphiderich mill tailings, nickel, goldsilver, coppergold, tungsten mine tailings, red mud, tantalumniobium ore tailings, uranium and leadzinc mill 2021年11月1日 Backfilling mining primarily includes solid backfilling mining, paste backfilling mining, highwater backfilling mining, and separation layer grouting (Zhu et al 2017;Deng et al 2017;Qi and Utilization of mill tailings, fly ash and slag as mine paste backfill