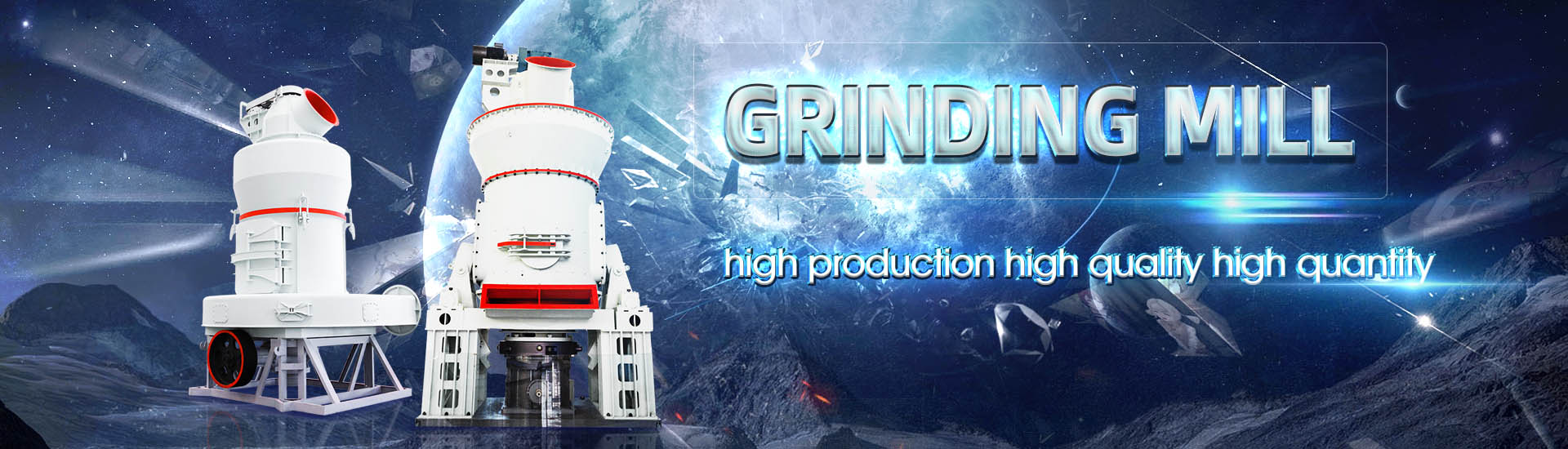
Ore powder making plant operation method

Development and Problems of Fluidized Bed Ironmaking Process:
2023年10月9日 Fluidized bed technology has become a crucial method used to process iron ore powder in nonblast furnace ironmaking, such as smelting reduction and direct reduction This paper introduces the working principle and several typical working states of fluidized bed (FB) 2017年2月16日 Sintering is a thermal agglomeration process that is applied to a mixture of iron ore fines, recycled ironmaking products, fluxes, slagforming (PDF) Iron Ore Sintering: Process ResearchGate2024年8月15日 Mineral processing, also known as ore dressing or mineral beneficiation, typically consists of four key unit operations: comminution, sizing, concentration, and dewatering 1 Comminution involves both crushing and Mineral Processing Plants: What You Need to Know2017年10月17日 In the smelting reduction process, pelletized iron oxide ore or fine ore powders are prereduced in a fluidized bed or reduction shaft The reduced iron along with coal and lime is fed to a gasifiermelter, which From Ore to Iron with Smelting and Direct Iron
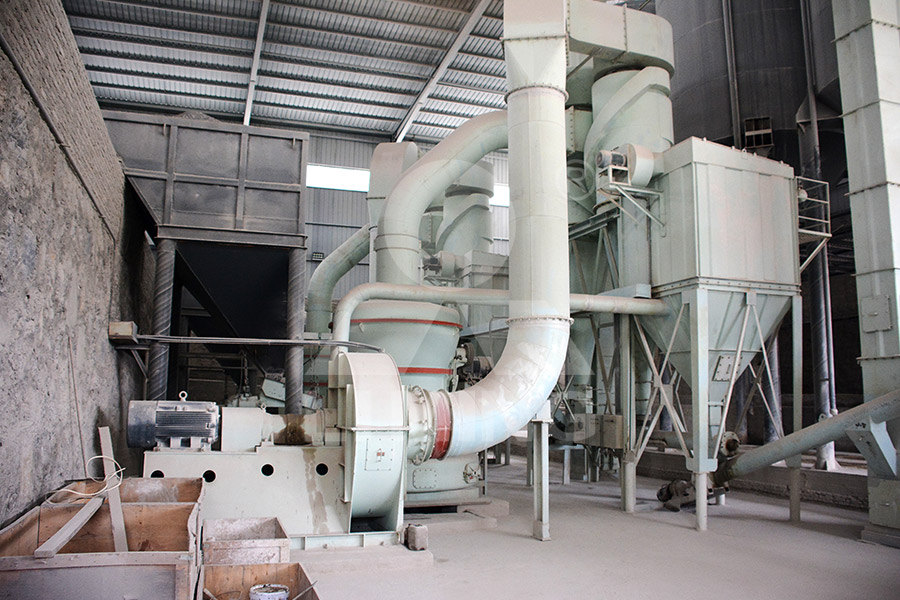
Iron Manufacturing process related to the specified manufacture(s)
The Höganäs process is a direct reduction method for production of sponge iron powder using magnetite ore (Fe3O4) and carbon as raw materials The reduction process takes place in a 2017年8月24日 The runofmine extracted from the ground requires further processing in order to make a marketable product This preparation is called mineral processing Thus, ores must Mineral Processing SpringerLinkThe first step in the overall powder metallurgy (PM) process is making metal powders There are four main processes used in powder production: solidstate reduction, atomization, electrolysis, and chemical In solidstate reduction, Making Metal Powder MPIFThe iron ore pelletizing process consists of three main steps: 1 Pelletizing feed preparation and mixing: the raw material (iron ore concentrate, additives anthracite, dolomite and binders are Iron Ore Pelletizing Process: An Overview IntechOpen
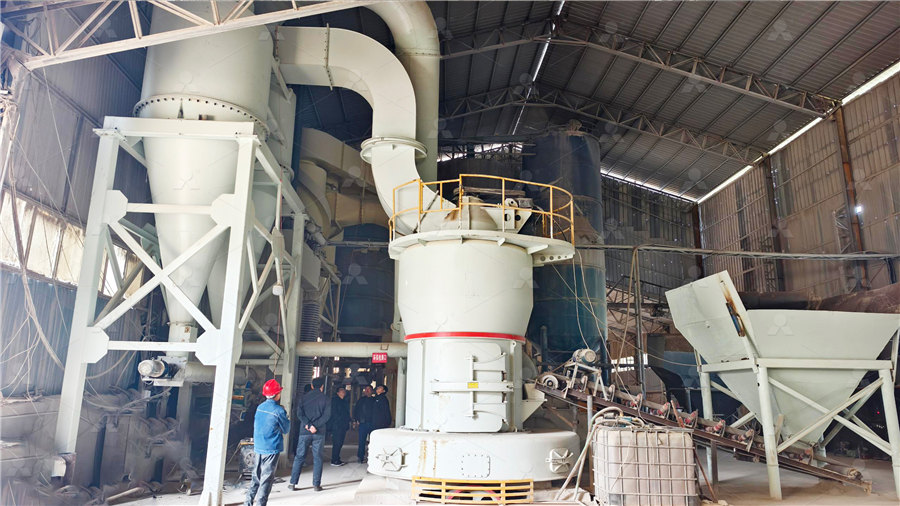
Micronsized ore powder production by propulsion and rapid
2021年9月6日 A pulverization method for micronsized ore powder production by propulsion and rapid unloading of highpressure air is introduced This approach is different from the 2015年8月3日 Ore dressing is a process of mechanically separating the grains of ore minerals from the gangue minerals It is done in order to produce a concentrate containing most of the ore minerals(PDF) Overview of Mineral Processing Methods2023年9月4日 Iron ore is an essential ironmaking material with a wide application The iron ore processing plant usually adopts the magnetic separation method The iron ore magnetic separation production line consists of iron ore Iron Ore Beneficiation Plant Equipment For Mining Media Attributions; Metal deposits are mined in a variety of different ways depending on their depth, shape, size and grade Relatively large deposits that are quite close to surface and somewhat regular in shape are mined using 82: Mining and Ore Processing Geosciences LibreTexts
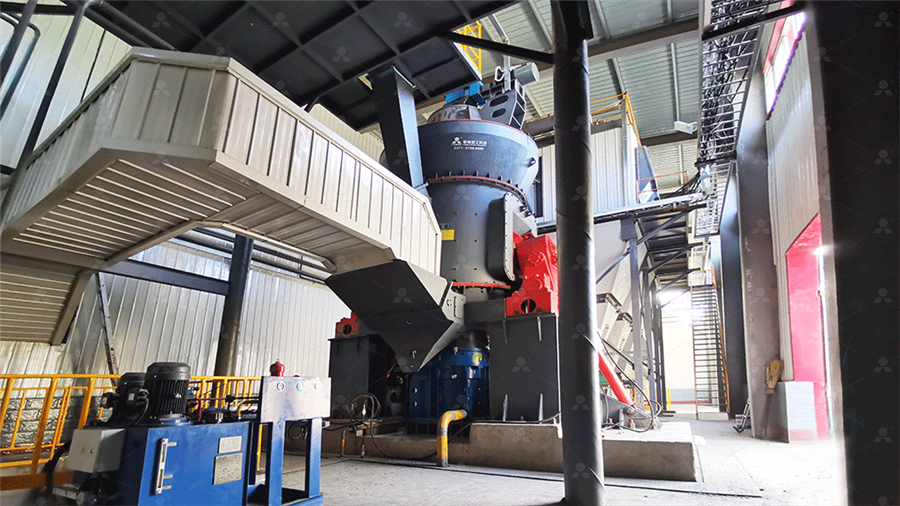
Iron Ore Pelletizing Process: An Overview ResearchGate
PDF On Jul 11, 2018, Sandra Lúcia de Moraes and others published Iron Ore Pelletizing Process: An Overview Find, read and cite all the research you need on ResearchGate2023年2月15日 If it is difficult to recover fine ore particles smaller than 10μm by other methods, the flotation separation method can be adopted At present, froth flotation is commonly used Its principle is to grind the hematite ore into a slurry by adding water to the flotation machine, and then stir and aerate to produce a large number of dispersed bubblesHow to Extract Iron from Hematite: Methods and PlantsThe iron ore production has significantly expanded in recent years, owing to increasing steel demands in developing countries However, the content of iron in ore deposits has deteriorated and lowgrade iron ore has been processed The fines resulting from the concentration process must be agglomerated for use in iron and steelmaking This chapter shows the status of the Iron Ore Pelletizing Process: An Overview IntechOpen2016年2月29日 When a pilot scale testing is possible, we can confirm many design parameters and flowsheet options A big plant will determine the effect of a gravity circuit on the plant gold distribution In this way, the gravity circuit must improve the plant payment for gold The method of handling gravity concentrate is plant dependentGold Extraction Recovery Processes 911Metallurgist
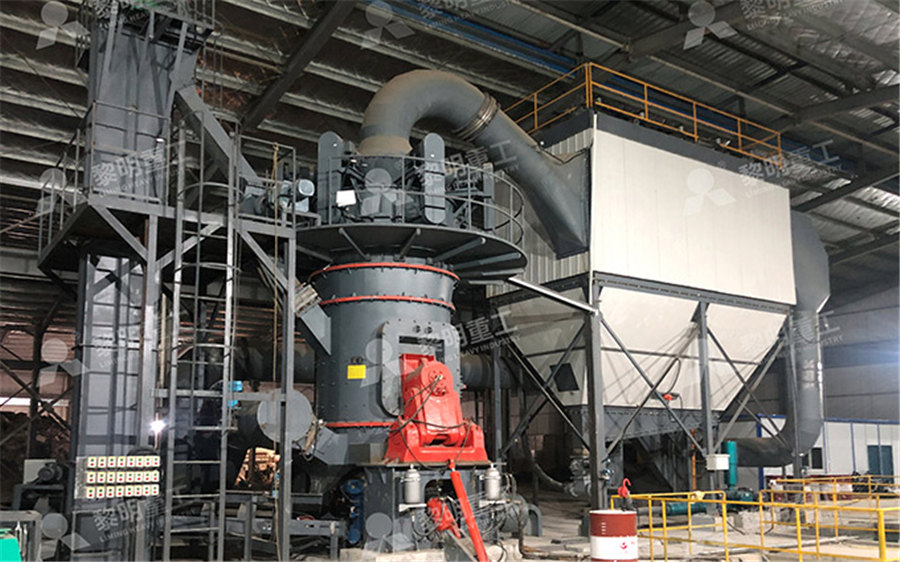
Mineral processing plant design and optimisation PPT SlideShare
2012年10月26日 7 Process Design • Process design criteria • A statement of what the plant will be required to do and the framework in which it will have to accomplish it It includes: • The capacity of the plant, • Material to be treated, • The sources of feed, • The product, • Time schedule for the commissioning of the various stages, • General information regarding the 2023年3月15日 The pellet making method was studied for production of iron ore pellets with a carbon core The pellets are to be fired in a sintering machine to produce sintered ores containing carbonaceous (PDF) Method of Making Iron Ore Pellets with a Carbon2023年9月5日 2 Preparation Methods of Metal Powder: 21 Physicochemical Methods 211 Reduction Method The reduction of metal oxides and salts is a widely used method for powder preparation Solid carbon can be used to reduce iron and tungsten powder, while hydrogen or decomposed ammonia is used to produce tungsten, molybdenum, iron, copper, cobalt Metal Powder Preparation Methods and Principles: A 2023年3月13日 For example, the ore in the Nchanga processing plant in Zambia contains 47% copper The copper content achieved to 50% ~ 55% through flotation by adding 500g/t of lime (pH 9 ~ 95), 10g/t of cresol (foaming agent), How to Process Copper Ore: Beneficiation Methods
.jpg)
Copper Mining and Processing: Processing Copper Ores
Copper processing is a complicated process that begins with mining of the ore (less than 1% copper) and ends with sheets of 9999% pure copper called cathodes, which will ultimately be made into products for everyday useThe 2024年3月16日 The sintering process is an intricate system with a protracted process flow The steps in the manufacturing line are primarily composed of the ingredients and mixing process, the sintering operation process, and the treatment of the sintered ore [39, 40]22 Important parameters and characteristics of sintering process As shown in Fig 2, all variables affecting Application of deep learning in iron ore sintering process: a reviewThe pellet making method was studied for production of iron ore pellets with a carbon core The pellets are to be fired in a sintering machine to produce sintered ores containing carbonaceous Method of Making Iron Ore Pellets with a Carbon Core by Disc 2024年11月21日 Manganese ore processing plants typically include crushers, ball mills, screens, and magnetic separators to increase the productivity of mining operations Skip to content JXSC Machinery Us +86 where the manganese ore is refined into a fine powder using specialized equipment such as ball mills or vertical roller Equipment Required To Build A Manganese Ore Processing Plant
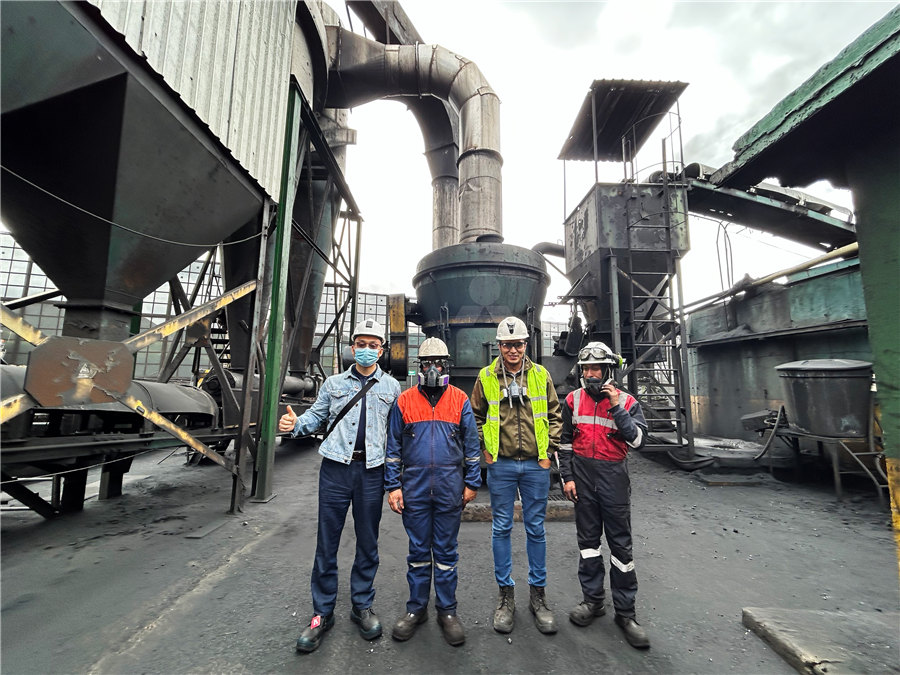
Understanding Gold Processing Techniques MINERALS BASE
As the quest for efficient gold extraction methods continues, flotation gold processing emerges as a forwardthinking technique dedicated to optimizing sulfide ore separation This advanced method plays on minerals’ natural hydrophobicity to achieve unparalleled segregation, carving a niche for itself in the modern gold processing landscape2022年9月16日 Numerical Simulation of the Operating Conditions for the Reduction of Iron Ore Powder in a Fluidized Bed Based on the CPFD Method September 2022 Processes 10(9):1870Numerical Simulation of the Operating Conditions for the 2023年10月9日 Fluidized bed technology has become a crucial method used to process iron ore powder in nonblast furnace And the use of highpressure operation has high requirements for equipment and operation, making the further promotion of the (2000) Status of Finmet plant operations at BHP DRI and Orinoco Iron AISE Steel Development and Problems of Fluidized Bed Ironmaking Process: 2015年3月15日 Understanding Sinter and Sinter Plant Operations satyendra; March 15, 2015; 8 Comments ; fluxes, Iron ore fines, SCFA, sinter, sinter plant basic sinter, sintering machine,; Understanding Sinter and Sinter Plant Operations Sintering is a process of agglomeration of fine mineral particles into a porous and lumpy mass by incipient fusion caused by heat produced Understanding Sinter and Sinter Plant Operations IspatGuru
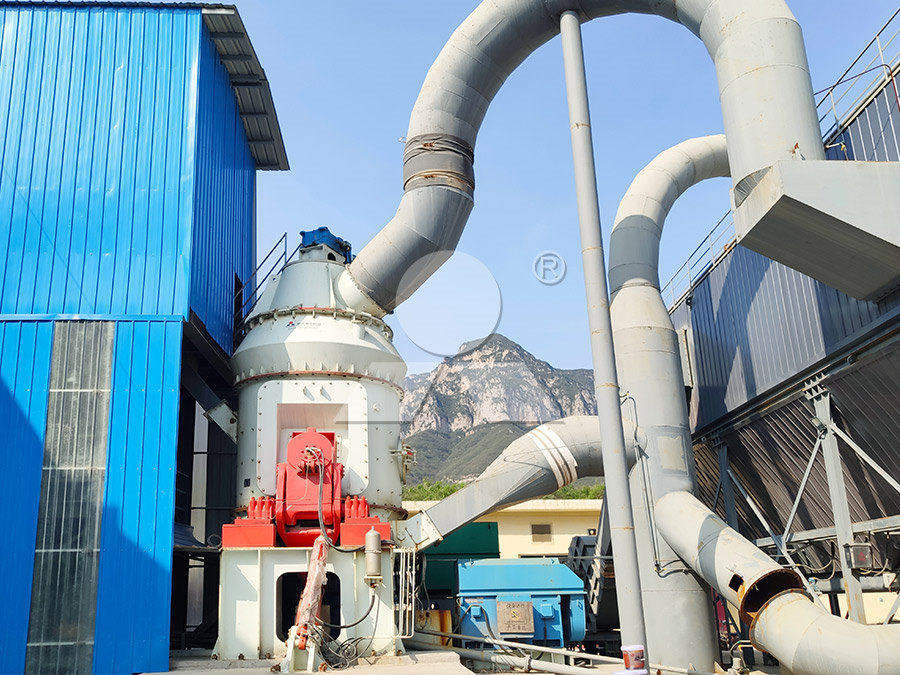
(PDF) i) Direct Reduced Iron: Production ResearchGate
2016年3月30日 In book: Encyclopedia of Iron, Steel, and Their Alloys (pppp 10821108) Chapter: i) Direct Reduced Iron: Production; Publisher: CRC Press, Taylor and Francis Group, New York2022年3月1日 Copper Flotation is a beneficiation method based on the hydrophobicity difference of the mineral surface — CHEMICALS MIX WITH SLURRY —FROTH FLOTATION —COLLECT CONCENTRATE — COPPER FLOTATION PLANT Pineer Mining Machinerypoint The test method of assimilation property is to (1) press the ground iron ore powder and CaO into a cake with 8 and 20 mm in diameter, respectively, and then, the iron ore cake is placed on the CaO cake, as shown in Figure 3, (2) the samples were calcined in a sintering characteristic tester, (3) the beginning melting temperOptimizing Iron Ore Proportion Aimed for Low Cost by Linear It is suitable for grinding ore such as iron ore, gold ore, copper ore and leadzinc ore and other metal beneficiation, used to grind the ore to below 0075mm for subsequent beneficiation process According to the different discharge methods, it can be Crushing and grinding process of copper oreIndustry Newsstone
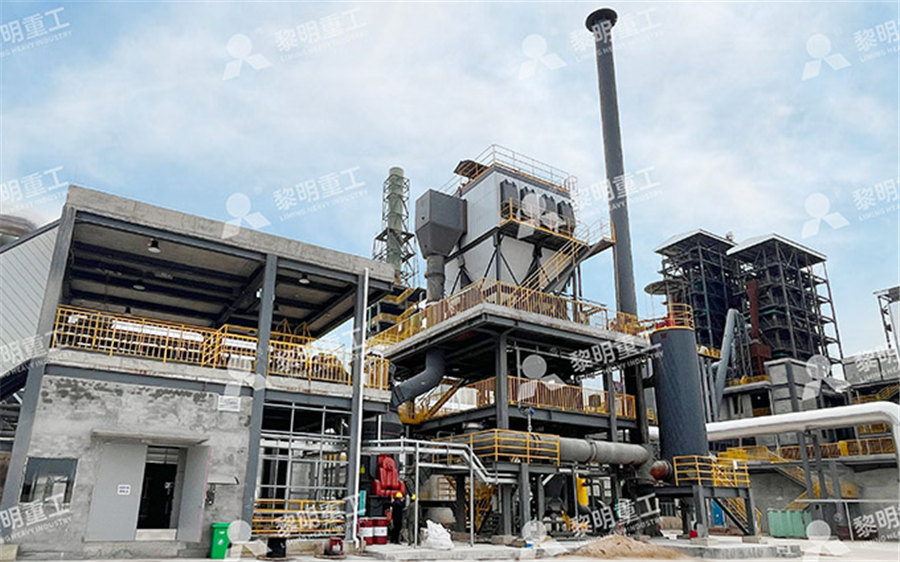
Copper Ore Processing Plant Fote Machinery
Send ore powder to concentrator to get rough copper concentrate, and finally transport concentrate to the magnetic separator for rough and fine selection Copper mine: magnetic separation method Copper Ore Processing Plant in Zimbabwe: 6 Enrichment and recovery of copper by solution extraction — electrolytic operationWhen iron ore is extracted from a mine, it must undergo several processing stages Six steps to process iron ore 1 Screening We recommend that you begin by screening the iron ore to separate fine particles below the crusher’s CSS before the crushing stage A static screen is used to divert the fine particles for crushingThe six main steps of iron ore processing Multotec2017年2月9日 The cohering behavior of iron ore pellet powder in kiln cannot be reflected entirely has been extensively used to produce oxidized pellets in China due to a series of advantages including simplified operation, easy control and large production etc, their contents in powder B and C were higher than in powder A MethodsCohering Behavior of Iron Ore Pellet Powder in Kiln by a Novel 2021年12月16日 For several decades, the metallurgical industry and the research community worldwide have been challenged to develop energyefficient and lowcost titanium production processes The expensive and energyconsuming Kroll process produces titanium metal commercially, which is highly matured and optimized Titanium’s strong affinity for oxygen Titanium: An Overview of Resources and Production Methods
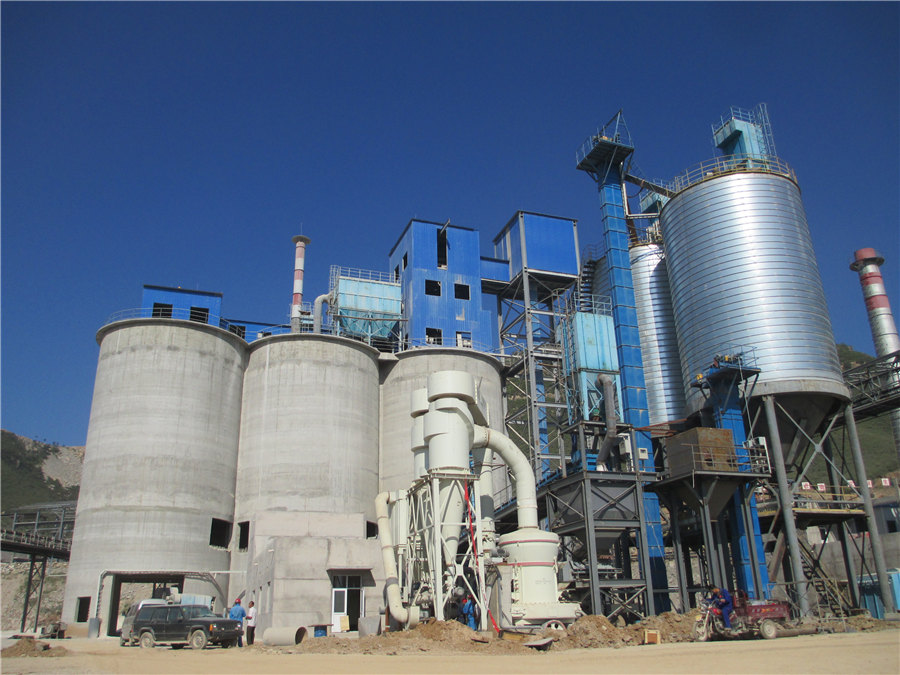
Iron ore pellets for blast furnace a technical guide MAXTON
2023年1月28日 What is iron ore pellet Iron ore pellets are made by adding a small amount of additives to the fine ore powder (200 mesh, that is, the ore powder with a particle size of less than 0074mm accounts for more than 80%, and the specific surface area is more than 1500cm2/g), adding water to the pelletizer, relying on capillary force and mechanical force of 2015年8月3日 Compared to existing ore sensing methods, MWI has the potential to penetrate deeper into rock particles and to be used as a supplementary method for analyzing those ores with high contrast in Overview of Mineral Processing Methods ResearchGate2016年9月1日 However, the phosphorus removal from iron ores other than igneous formations has been a challenge for most of the iron ore operations This research aims to make a preliminary study of wavellite REMOVING IMPURITIES FROM IRON ORES: METHODS AND 4 天之前 (1) Grinding It involves reducing the size of tin ore particles It is usually accomplished through crushing and grinding stages using various types of equipment, such as jaw crushers and ball mills The purpose is to obtain a The Importance Of Two Treatment Methods When Tin
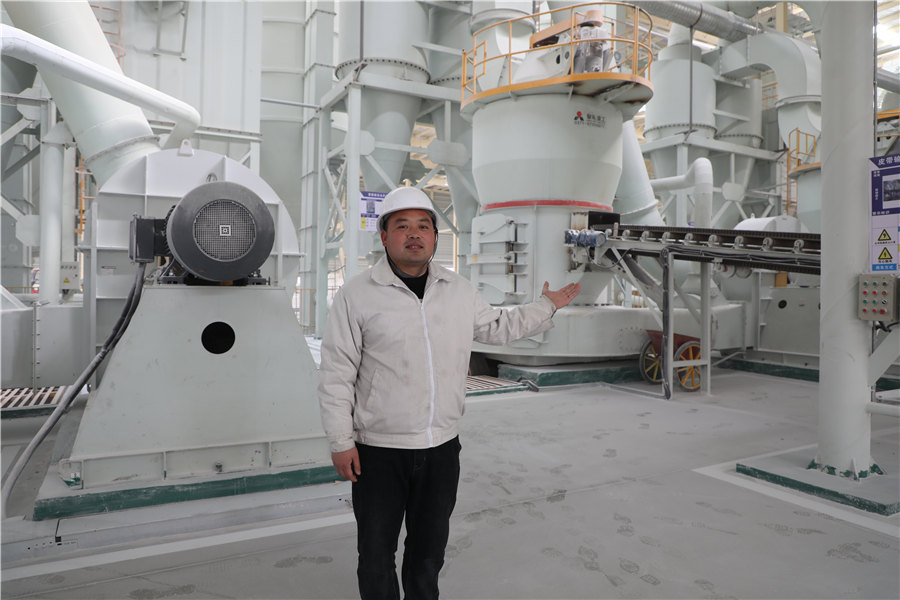
Ore Sampling Methods: Good Proper 911Metallurgist
2017年2月21日 Table VIII gives a comparison of assays and total ounces of gold contained in four lots of Engineers’ Lease ore from the property of the FlorenceGoldfield Mining Co, in Goldfield, Nev, sampled at the Columbia plant and afterwards screened through 3/8in punched screen at the Hazen plant, and the coarse and fines sampled separately after screening2021年3月18日 This article will introduce the flow of a CIP gold processing plant: from raw gold ore to gold bar step by step The main process of the CIP gold processing plant to extract gold from ore and convert it into pure metal How Does A CIP Gold Processing Plant Work?2024年6月18日 Input parameters such as powder specifications, pellet characteristics and operating conditions could be altered to study the process in detail In this regard, reference settings similar to the industrial operation were used in a base test to make the results more comparable These parameters are represented in Table 6Experimental and numerical investigation of iron ore pellet firing 2019年1月1日 Blast furnace ironmaking requires separate coke making and sintering plants and often has reduced operating flexibility (Lu, Pan and Zhu, 2015) Coking coal is regarded as premium quality coal that attracts relatively higher cost and there are concerns over the limited reserves (Chukwuleke, Iiuju and Chukwujekwu, 2009)A review of ironmaking by direct reduction processes: Quality
.jpg)
Specifications of iron ores required by steel plants for ironmaking
Download Table Specifications of iron ores required by steel plants for ironmaking from publication: Current strategies and future challenges on exploration, beneficiation and value addition of 2023年7月6日 Alluvial tin ore is separated by the gravity separation method For alluvial tin ore with a high degree of monomer dissociation, the final concentrate is obtained by the 6S shaker tables at one timeThe concentrate grade is above 60% For alluvial tin ore with a low monomer dissociation degree, use a jig machine for primary selection, then concentrate enters 6s TIN ORE PROCESSING PLANT Pineer Mining Machinery2024年1月23日 The unqualified gypsum powder goes back to the Raymond mill for secondary grinding Step 4: Calcination of stone powder Gypsum powder meets the fineness requirement and enters a fluidized bed furnace for calcination treatment After calcination, the gypsum powder goes to a storage bin to complete the grinding operation of the gypsumGypsum Powder Grinding And Processing Plant EquipmentAn exception to the above discussion of mineral processing arises when the valuable component of the ore is extracted directly by chemical methods The flowsheet in Figure 1 shows diagrammatically the typical sequence of operations in the process plant The various unit operations used for liberation and separation will be discussed in the Introduction to Mineral Processing or Beneficiation
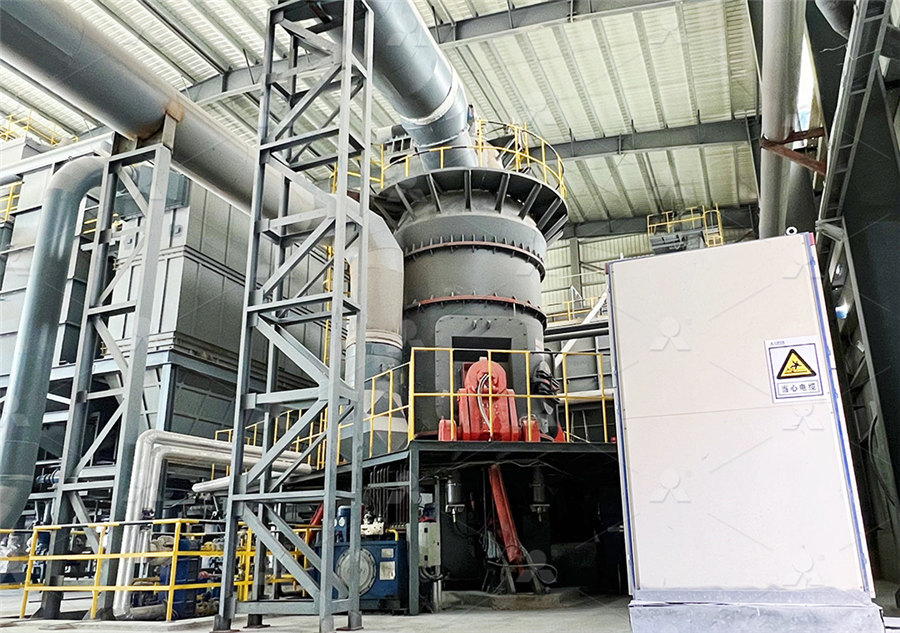
Effective Methods to Reduce Grade Variability in Iron Ore Mine
2019年11月30日 This paper explores possible strategies to meet iron ore customer requirements (reduce variability and keep Fe% and contaminants such as Al 2 O 3 % and P% within the acceptable tolerance) by optimizing the mine plan and scheduling strategy in the rehandling process The paper aims to obtain more homogenous iron ore grade by