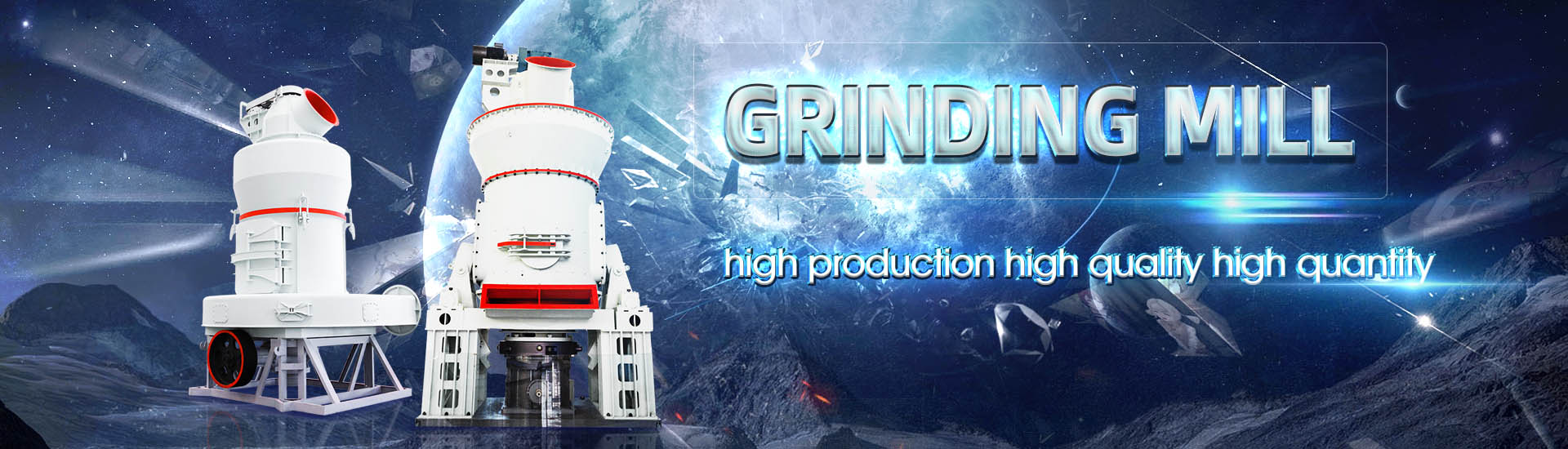
Performance introduction of coal mill roller sleeve
.jpg)
Optimisation of the performance of a new vertical roller mill by
2024年1月15日 This study is concerned with evaluating the performance of a novel roller mill, in which the crushing platen is a vertical wall over which cylindrical rollers rotate, thereby 2020年8月12日 This study shows the performance of a currently running vertical roller coal mill (VRM) in an existing coalfired power plant In a power plant, the coal mill is the critical An investigation of performance characteristics and energetic Technical specifications of vertical roller coal mill This study shows the performance of a currently running vertical roller coal mill (VRM) in an existing coalfired power plantTechnical specifications of vertical roller coal mill2020年8月12日 To understand the performance of a vertical roller coal mill, the real operational tests have been performed considering three different coal sources Obtained results indicate An investigation of performance characteristics and energetic
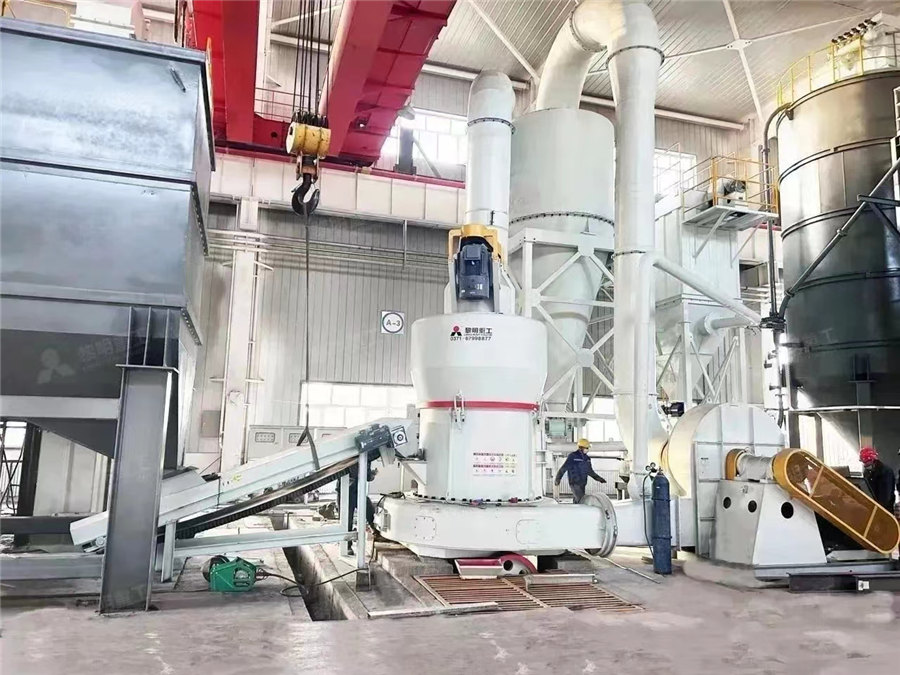
Operational parameters affecting the vertical roller mill
2017年4月1日 Vertical roller mills (VRM) have found applications mostly in cement grinding operations where they were used in raw meal and finish grinding stages and in power plants 2024年11月1日 Particle discharge from Raw Coal VRMs was improved In order to improve the motion characteristics of particles in vertical roller mills (VRMs), the assumption that different Numerical Study of Flow Field and Particle Motion Characteristics the milling performance of coal and torrefied wood pellets (TPs), various blend ratios were tested using a benchscale roller mill Neutral sugar analysis was performed to evaluate the biomass Kiyoshi Sakuragi and Maromu Otaka ACS PublicationsThe effect of low calorific value coal was observed on mill’s response to match the boiler energy requirements Evaluation of the current operating pulveriser data enabled the determination of Performance optimisation of vertical spindle coal pulverisers
.jpg)
PROCESS OPTIMISATION FOR LOESCHE GRINDING PLANTS
vertical roller grinding mills for grinding: • Coal • Cement raw material • Clinker / granulated slag • Industrial minerals, and • Ores The core elements of these plants are the Loesche vertical DOI: 101080/2020 Corpus ID: ; An investigation of performance characteristics and energetic efficiency of vertical roller coal mill @article{Tontu2020AnIO, title={An investigation of performance characteristics and energetic efficiency of vertical roller coal mill}, author={Mehmet Tontu}, journal={International Journal of Coal Preparation and An investigation of performance characteristics and energetic in coal, as a tracer in a roller mill20 In that study, the WPs were selectively accumulated inside the roller mill and discharged with a particle size larger than that of the coal particlesMilling Characteristics of Coal and Torrefied Biomass Blends in a 2021年10月28日 To ensure stable operation of the roller mill and an effective reduction in the size of the coal–TP blend, the selection and use of uniformly and sufficiently torrefied wood pellets are importantMilling Characteristics of Coal and Torrefied Biomass
.jpg)
SHPHGLXPVSHHGFRDOPLOO IOPscience
longer service life and more convenient maintenance Hp1103 coal mill is a kind of HP coal mill Compared with similar coal mills, it has stronger adaptability to raw coal and is more suitable for large unit thermal power plants Taking hp1103 medium speed roller disc coal mill as the carrier, this paper mainly describes theJournal of Physics: Conference Series PAPER OPEN ACCESS)DXOWDQDO\VLVDQGRSWLPL]DWLRQWHFKQRORJ\RI+3ERZOW\SHPHGLXP VSHHGFRDOPLOO To cite this article: Dou Jie 2021 J Phys: Conf Ser 2005 SHPHGLXP VSHHGFRDOPLOO ResearchGate2021年11月4日 including the dropweight test machine, the roller test machine, and the Hardgrove mill Using the attrition test machine, presented in Figure 2 , is the only integrated testing methodTechnique to Investigate Pulverizing and Abrasive Performance of Coals Vertical roller coal mill; energetic performance; coal fired power plant; classifier speed; mill outlet temperature; coal feeding mass flow rate Introduction In the An investigation of performance characteristics and energetic
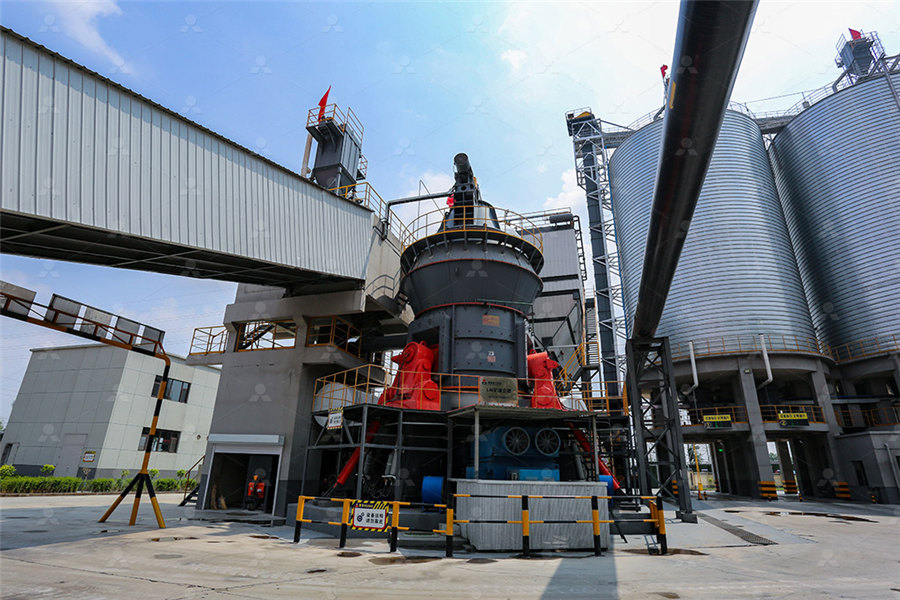
Analysis and Optimization of Grinding Performance of Vertical Roller
2022年1月23日 mill, coal mill, Clinker Mill and cement mill, and the vertical mill occupies a large energy consumption unit Therefore, it is necessary to optimize the multiobjective parameters of2017年9月11日 PDF In this study, an extensive sampling study was carried out at vertical roller mill of ESCH Cement Plant in Luxemburg Samples were collected from Find, read and cite all the research (PDF) Performance Evaluation of Vertical Roller Mill in Cement Vertical Roller Mill The vertical roller mill (VRM) shown in Figure 4 is an air swept, mediumspeed, vertical pulverizer with integral classifier It pulverizes coal by applying hydraulicallyloaded grinding pressure through three grin ding rollers onto a rotating bed of coal Grinding pressure can be adjusted to account for variations in coalA Comparison of Three Types of Coal Pulverizers Babcock Powermill's unique roller loading arrangement as a modification to its MB mill predecessor Shortly thereafter, DBW became the first licensee of Gebruder Pfeiffer in Europe for coal applications This particular mill was chosen because of DBW's successful track record not only in their worldwide installation of 6 to 100 TPHWorldProven Coal Pulverizer Technology Debuts in the US
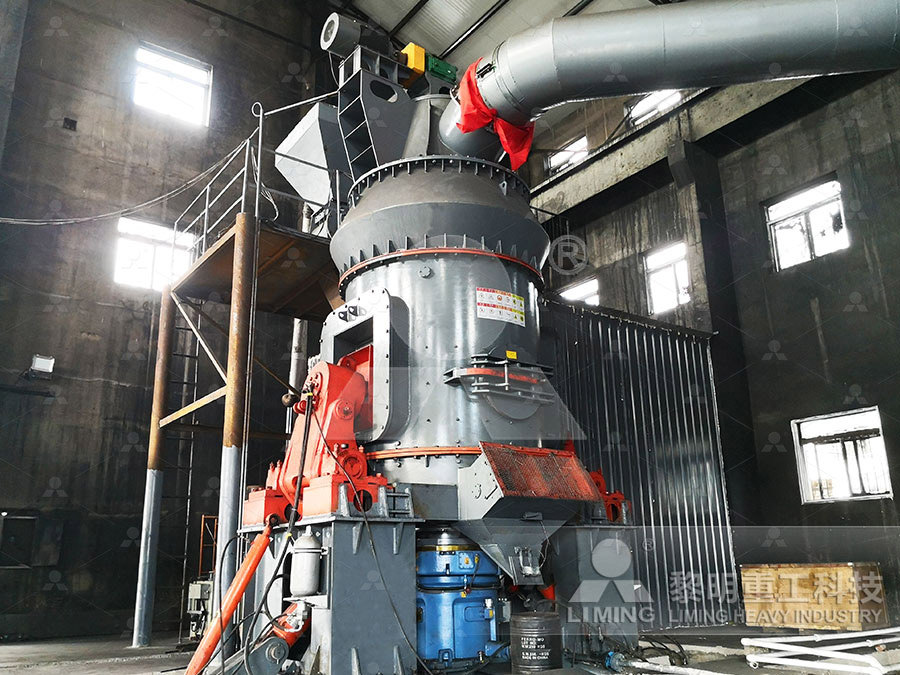
An investigation of performance characteristics and energetic
2020年9月25日 energetic efficiency of coal mill has been investigated and performance value has been found to be a maximum value of 962% ARTICLE HISTORY Received 17 June 2020 Accepted 18 July 2020 KEYWORDS Vertical roller coal mill; energetic performance; coal fired power plant; classifier speed; mill outletThe ball mill is a traditional coal pulverizer machine, which has been widely used since it was invented In the cement plant, the new dry process cement manufacturing requires the moisture content of coal powder to be 05% ~ Coal Mill in Cement Plant Vertical Roller Mill Air Introduction UBE Machinery Corporation Ltd (UBE) Coal, Clinker and Slag Reliable Performance performs drying grinding classification and pneumatic transportation simultaneously Vertical Roller Mill 1 Rotary Lock 2 Separator 3 Chute 4 Roller 5 Swing Lever 6 Table 7VERTICAL ROLLER MILLS AMCL2021年8月1日 A root cause failure analysis of coal mill vertical shaft used in thermal power plant has been carried out The failed parts of the shaft showed the signature of fatigue failures(PDF) Fault analysis and optimization technology of HP
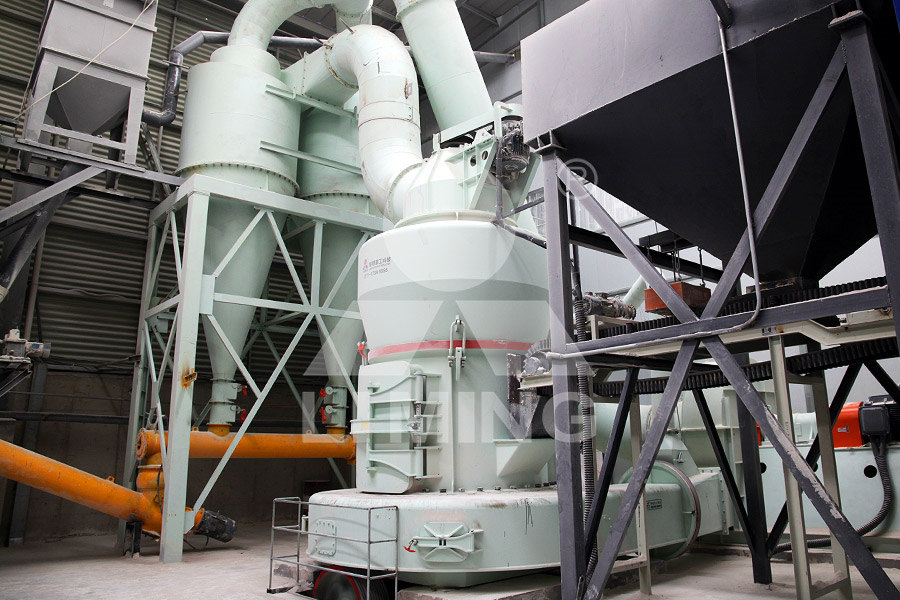
Coal mill pulverizer in thermal power plants PPT SlideShare
2012年11月17日 20 131Fineness Fineness is an indicator of the quality of the pulverizer action Specifically, fineness is a measurement of the percentage of a coal sample that passes through a set of test sieves usually designated at 50, 100, and 200 mesh A 70% coal sample passing through a 200 mesh screen indicates optimum mill performance The mill wear and Introduction MPStype mills, with a roll wheel pulverizer, are widely used in the power generation industry to crush, dry and separate the fine coal particles towards combustion in the furnaceCFD Modeling of MPS Coal Mill for Improved Performance and HRM1700MVRM Free download as PDF File (pdf), Text File (txt) or read online for free The document provides installation and operation instructions for the HRM1700M Vertical Roller Coal Mill It describes the mill's technical parameters, components, structure, working principles, and installation process Key aspects include grinding rollers that can be removed for Operation Manual: HRM1700M Vertical Roller Coal Mill2009年9月20日 A control oriented model was then developed by Fan (1994) and Fan and Rees (1994) In 2009, coal flow and outlet temperature of mill were modelled using mass and heat balance equations for startup Modeling and Parameter Identification of Coal Mill
.jpg)
Performance of the static air classifier in a Vertical Spindle Mill
2016年8月1日 Bhasker has investigated flow paths in the classifier of a roller mill, and trajectories of 25 μm coal particles were obtained by applying computational fluid dynamics (CFD) [12] And for a simplified industrial pulverizer, Vuthaluru et al have conducted numerical simulation to compare the motion of air and 100 μm and 500 μm coal particlesIntroduction As a result of the worldwide attention in recent years to energy efficiency improvement and CO 2 In March 2013 mill performance acceptance was completed Table 2 shows an actual operation data comparison 1 set of coal mills Figure 4 Roller mill design From left to right: raw mill, cement mill 10% downsizing 20% downsizingYasuhiro Shigemoto, Hirofumi Kasai and Tatsuya Hinauchi,2024年1月15日 Bhambare et al [12] carried out multiphase CFD modelling of an MPS roller mill, considering drying of coal particles in the mill By analysing the CFD modelling results, it was found that a nonuniform air distribution at the inlet section was mainly responsible for nonuniformity in the flow of particles at the outletOptimisation of the performance of a new vertical roller mill by Energies 2021, 14, 7300 3 of 15 A = f2(G, B) (2) where G is the coal grindability within the specified system, M means the mechanical properties of the coal, r is the coal porosity, q determines the hard particles mechanical and geometrical characteristics, w is the moisture, T is the temperature, h is the overall efficiency of the grinding system, A is the coal abrasiveness, of Coals in Mineral Processing Systems
.jpg)
Effect of mill outlet temperature on the coal moisture content
This study shows the performance of a currently running vertical roller coal mill (VRM) in an existing coalfired power plant In a power plant, the coal mill is the critical equipment, whose 2022年5月31日 Mineral crushing is the main source of energy consumption in mineral processing According to statistics, this consumption accounts for about 35–50% of the total cost of the mine (Curry et al, 2014), or even higherIt may also account for 18% of the global electrical energy consumption (NapierMunn, 2015)More efficient crushing equipment needs to be Analysis of vertical roller mill performance with changes in 2022年5月31日 Introduction; Section snippets; Minerals Engineering Volume 182, 31 May 2022, Analysis of vertical roller mill performance with changes in material properties and operating conditions using DEM Author links Numerical Study of Flow Field and Particle Motion Characteristics on Raw Coal Vertical Roller Mill Circuits Analysis of vertical roller mill performance with changes in INTRODUCTION As part of the continuing effort to improve combustion performance commensurate with reduced emissions in coalfired power plants, Riley Power Inc (RPI), a Babcock Power Inc (BPI) company has been actively developing mill system technology to achieve better coal fineness, increased capacity, greater reliability, and longer wear lifeCOAL PULVERIZER DESIGN UPGRADES TO MEET THE DEMANDS
.jpg)
Coal mill model considering heat transfer effect on mass
2021年8月1日 Yukio et al [7] proposed a model consisting of blending, grinding and classifying processes for pulverizer control Agarawal et al [8] differentiated coal powder into ten size groups, divided the bowl mill into four zones, and developed a unified model Palizban et al [9] derived nonlinear differential mass equations of raw coal, recirculation coal and suspension coal in 520 P Niemczyk et al / Control Engineering Practice 20 (2012) 519–530 Nomenclature Dpmill mc mpc mcair mass of unground coal on the table (kg) mass of pulverized coal on the table (kg) mass of pulverized coal carried by primary air (kg) wc wpc wout wret mass mass mass mass flow flow flow flow of of of of the dry raw coal to the mill (kg Derivation and validation of a coal mill model for control2023年8月5日 The main bearing of the highpressure roller mill uses double row spherical roller bearings with selfaligning function The bearing has the characteristics of large carrying capacity and long service life It is concentrated with dry oil to ensure good lubricationIntroduction to the structure of high pressure roller mill2021年1月1日 Grinding Mill Vertical Roller Mill or Ball Mill: The reclaimed raw mix fed to Raw Mills, for drying and fine grinding of Raw meal for kiln feed: 4: Coal Grinding: Grinding Mill Vertical Roller Mill or Ball Mill: Coal is ground in Coal mill, which is a fuel for use in Kiln firing: 5: Pyro Section, Clikerization: In line calciner six stage Review on vertical roller mill in cement industry its performance
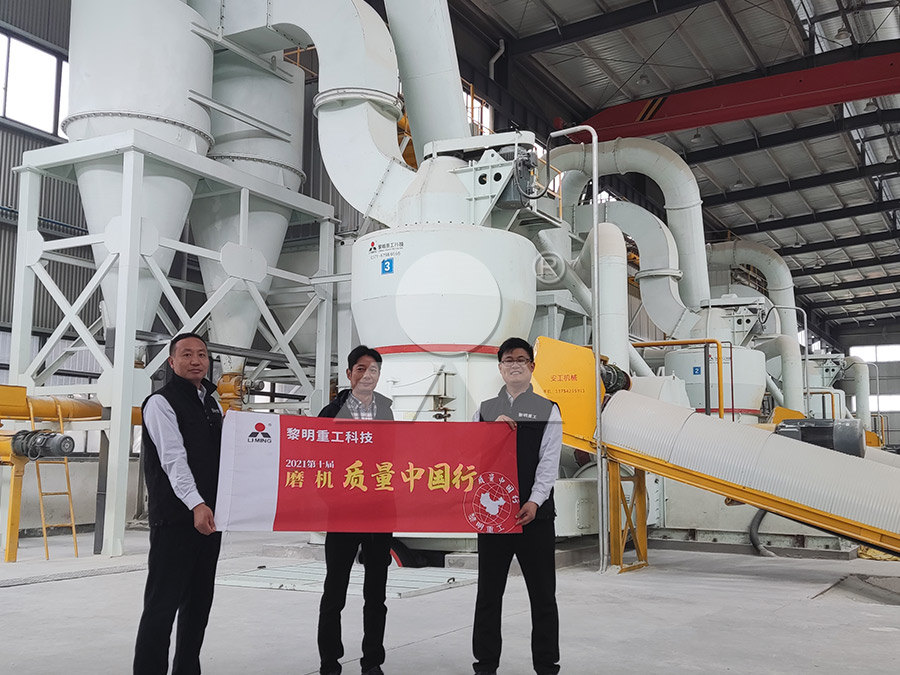
Milling Characteristics of Coal and Torrefied Biomass Blends in a
2021年11月9日 Introduction Replacing some of the coal by biomass is an effective way to reduce CO 2 emissions from pulverizedcoalfired power plants and integrated coal gasificationcombined cycle power plants However, compared with coal, biomass has lower grindability in the existing roller mills 1 and a lower calorific value per weight 2,3 The maximum biomass co 2019年12月1日 The classification performance of model coal mill classifiers with different bottom incoming flow inlets was experimentally and numerically studiedClassification performance of model coal mill classifiers with 2016年8月1日 In coal power plants, classification of coal particles in a classifier after the pulverization process is important A highquality classification can guarantee the delivery of standard PF efficiently, which results in not only primarily reducing the loss of unburned carbon, but also decreasing the slagging potential in the furnace [1]Performance of the static air classifier in a Vertical Spindle MillINTRODUCTION As part of the continuing effort to improve combustion performance commensurate with reduced emissions in coalfired power plants, Riley Power Inc (RPI), a Babcock Power Inc (BPI) company has been actively developing mill system technology to achieve better coal fineness, increased capacity, greater reliability, and longer wear lifeCoal Pulverizer Design Upgrades to Meet the Demands of Low
.jpg)
Classification performance of model coal mill classifiers with
2020年3月1日 The classification performance of model coal mill classifiers with different bottom incoming flow inlets was experimentally and numerically studied The flow field adjacent to two neighboring impeller blades was measured using the particle image velocimetry technique The results showed that the flow field adjacent to two neighboring blades with the swirling inlet was 2016年9月1日 To understand the performance of a vertical roller coal mill, the real operational tests have been performed considering three different coal sourcesOperational parameters affecting the vertical roller mill performance 2012年5月1日 Coal fired power plants are heavily used due to large and long lasting coal resources compared with oil or natural gas An important bottleneck in the operation of this particular kind of plants, however, is the coal pulverization process, which gives rise to slow takeup rates and frequent plant shutdowns (Rees Fan, 2003)In typical coal fired power plants, Derivation and validation of a coal mill model for control700 Journal of Power Electronics, Vol 9, No 5, September 2009 JPE 954 Modeling and Parameter Identification of Coal Mill HwiBeom Shin *, Xinlan Li , InYoung Jeong **, JongMan Park **, and Soonyoung Lee † †*Department of Electrical Engineering, Gyeongsang National University, Korea ** Korea Western Power Co, Ltd, KoreaModeling and Parameter Identification of Coal Mill
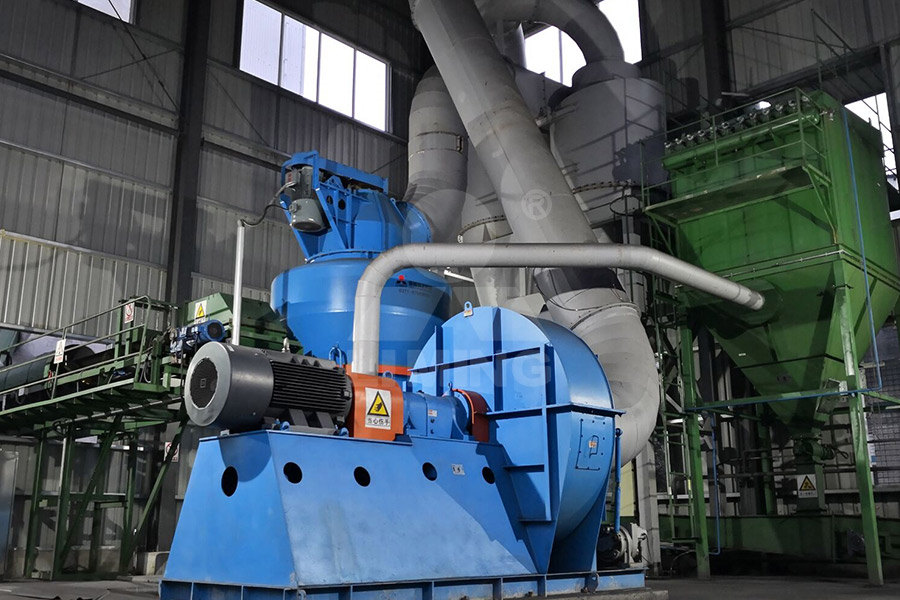
(PDF) Modeling and Control of Coal Mill Academia
Finally, the temperature equation is based on heat balance equation of the coal millThe significant heat contribution comes from the primary air flow , moisture of the incoming coal particles, coal flow into the mill (1) and from grinding the moisture coal particles and temperature depends on the The mass of pulverised coal on the table grinding rate and the amount of coal