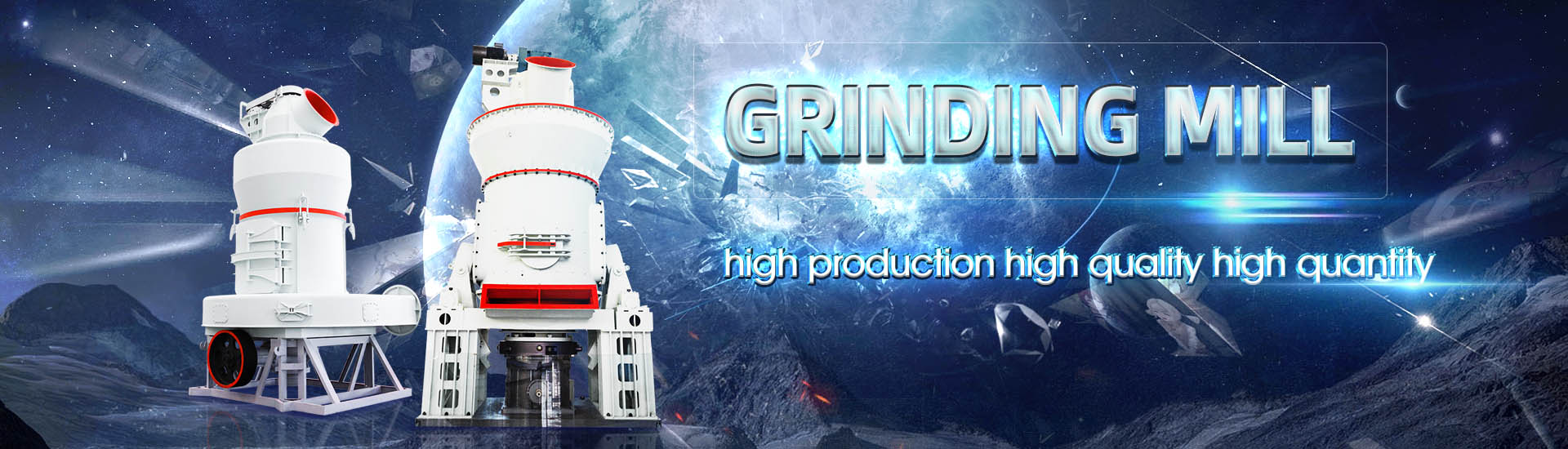
Cement mill grinding ball size
.jpg)
OPTIMIZATION OF CEMENT GRINDING OPERATION IN BALL MILLS
Operation and Elements of a ClosedCircuit Ball Mill System Cement ball mills typically have two grinding chambers The first chamber is filled with larger diameter grinding media andlined with lifting liners The first chamber coarsegrinds the feed material and prepares it for the second online live calculators for grinding calculations, Ball mill, tube mill, critical speed, Degree of filling balls, Arm of gravity, mill net and gross powerball mill calculations, grinding media filling degree, ball size, mill online live calculators for grinding calculations, Ball mill, tube mill, critical speed, Degree of filling balls, Arm of gravity, mill net and gross powerball mill calculations, grinding media filling degree, ball size, mill A 10 MW cement mill, output 270 tonnes per hour A cement mill (or finish mill in North American usage [1]) is the equipment used to grind the hard, nodular clinker from the cement kiln into the fine grey powder that is cementMost cement is currently ground in ball mills and also vertical roller mills which are more effective than ball millsCement mill Wikipedia
.jpg)
Everything you need to know about clinker/cement
Ball Mill Cement Lafarge max R5% >25mm, Holcim 30mm; Raw Meal max R1% > 30 mm (Lafarge) Using a pre grinding circuit the maximum ball size could be as low as 60 mm Ball mills and grinding tools Cement ball mills are typically twochamber mills (Figure 2), where the first chamber has larger media with lifting liners installed, providing the coarse grinding stage, whereas, in the second chamber, medium and fine grinding is carried out with smaller media and classifying linersBALL MILLS Ball mill optimisation Holzinger Consulting2013年8月3日 In Grinding, selecting (calculate) the correct or optimum ball size that allows for the best and optimum/ideal or target grind size to be achieved by your ball mill is an important thing for a Mineral Processing Engineer AKA Metallurgist to do Often, the ball used in ball mills is oversize “just in case” Well, this safety factor can cost you much in recovery and/or mill liner Calculate and Select Ball Mill Ball Size for Optimum Grindingwhat we offer The ultimate ball mill – with flexibility built in You can’t optimise cement grinding with a onesizefitsall solution That’s why our ball mills are designed to adapt to your requirements, with a high degree of flexibility built inBall mill for cement grinding
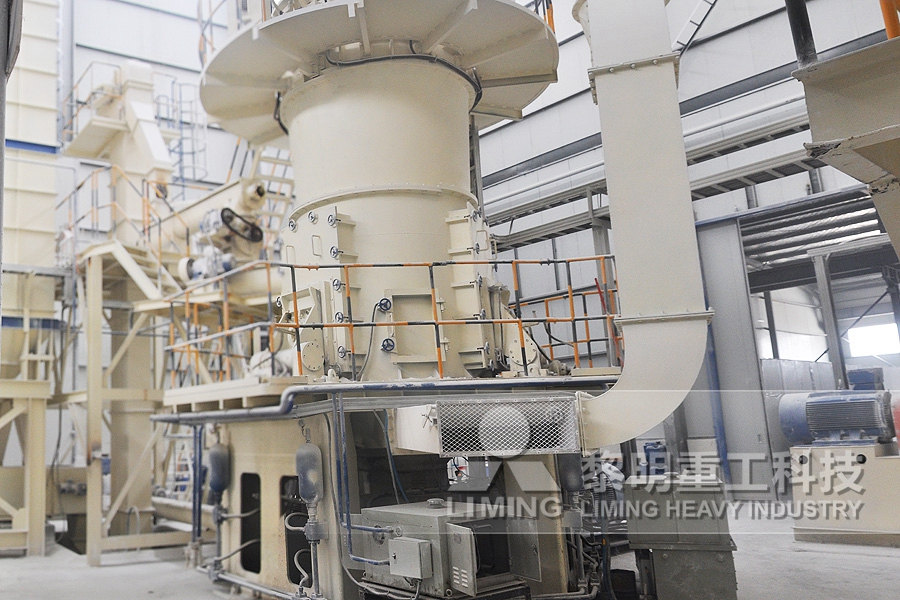
Ball mill CEMENTL
Ball mills control particle grading (such as the size and proportion of steel balls) by reasonably adjusting the grinding media to achieve a more uniform grinding effect 2 Ball mills are also used in the grinding stage of iron ore beneficiation processes, which can achieve 80% of 200 mesh fineness and improve beneficiation efficiencyCement ball mills typically have two grinding chambers The first chamber is filled with larger diameter grinding media and lined with lifting liners The separator’s efficiency is determined by drawing a Tromp curve based on particle size distribution analysisOptimization of Cement Grinding Operation in Ball Mills PEC Types of Mills Used in Grinding 1 Ball Mills Ball mills are one of the most commonly used types of equipment for cement grinding They utilize steel balls as grinding media to crush and grind the raw materials into fine powder The process operates in a continuous cycle: Material Feeding: The raw materials are fed into the millGrinding in Cement Manufacturing: Key Process, Types of Mills, Roller press with Ball mill Ball Mill Ball mills with high efficiency separators have been used for cement grinding in cement plants all these years Ball mill is a cylinder rotating at about 7080% of critical speed on two trunnions in white metal bearings or Cement Grinding Cement Plant Optimization

Grinding Ball Ball Mill Balls For Sale Ball Mill
Ball mill balls supplier – AGICO CEMENT Ball mill ball is a hotsale product of our company, we also supply other ball mill parts including ball mill girth gear, ball mill pinion, ball mill trunnion, and ball mill bearing house according to the 2023年4月23日 A comparison of the grinding media is given together with the knowledge gaps that still need to be bridged to improve the quality and performance of grinding media used in ball mills(PDF) Grinding Media in Ball MillsA ReviewCement Industry: Ball mills are extensively used in the cement industry for grinding raw materials, clinker, and additives to produce cement The ability to finely grind materials and control the grinding process makes ball mills crucial Ball Mill Grinding Machines: Working Principle, Types, As one of the Chinese ball mill manufacturers, AGICO offers energysaving cement ball mills and other cement grinding machines Skip to content Blog Contact About Cases Factory CONTACT US info@cementplantequipment CALL US +86 REQUEST A QUOTE Just ask! As the particle size of the material is greatly reduced, Ball Mill For Cement Grinding – Cement Ball Mill Ball Mill

Grinding in Ball Mills: Modeling and Process Control
2012年6月1日 Besides particle size reduction, ball mills are also widely used for mixing, blending and dispersing, amorphisation of materials and mechanical alloying [1, 49, 51]The benefit of the OK mill is in particular pronounced when grinding to a high fineness and/or when slag is included in the cement Grinding aid For ball mills grinding OPC to a fineness of up to around 3600 cm2/g (Blaine) grinding aid is usually not required; it may not even be feasible considering the cost of grinding aidCement grinding Vertical roller mills VS ball millsThe OK™ Mill was originally designed for cement grinding In 2017 we released the OK™ vertical roller mill for raw materials grinding The OK™ Mill’s modular design comes with unique flexibility, showcasing parts commonality, where spare parts can be shared between vertical roller mills regardless of size and applicationOK™ Raw and Cement MillVertical roller mill vs ball mill for cement grinding: Comparison the advantages and disadvantages of these two types of mills TO Download this post and all the books and excel sheets and my personal notes and presentations I collected about cement industry in the last 30 years click the below paypal linkVertical roller mill vs ball mill for cement grinding: Comparison
.jpg)
Impact of ball size distribution, compartment configuration, and
2022年11月1日 In the context of fullscale continuous cement ball milling, there is no exact rule for ball selection; rather, the cement industry designs the mixture of ball sizes and BSD on the basis of their experience along with recommendations from the mill machine suppliers (eg, FLSmidth, 2012, FLSmidth, 2014) and (empirical) Bond’s approach (Bond, 1958), in which top Cement ball mill is a cement grinding machine used in the cement production line for cement clinker grinding AGICO supplies the cement ball mills for processing limestone, cement clinker, gypsum, slag, ore, etc Feed size(mm) Rotated speed(r/min) Largest ball charge(t) Rotor power(kW) Weight (t) φ12×45: opencircuit: 15~17: ≤25: 34 Cement Ball Mill Cement Grinding Machine Cement Mill2024年8月8日 Unlock the secrets to ball mill efficiency with our comprehensive guide on choosing the right grinding media Learn how material composition, size, shape, hardness, and cost impact your milling process and outcomes Perfect Ball Mill Success: A StepbyStep Guide to Choosing Types of cement mills There are basically 4 types of cement mills in use today: Ball Mill (BM) Ball Mill (BM): predominant despite higher energy consumption partly because of historical reason but partly also because it still offers Improvements in New Existing Cement Grinding
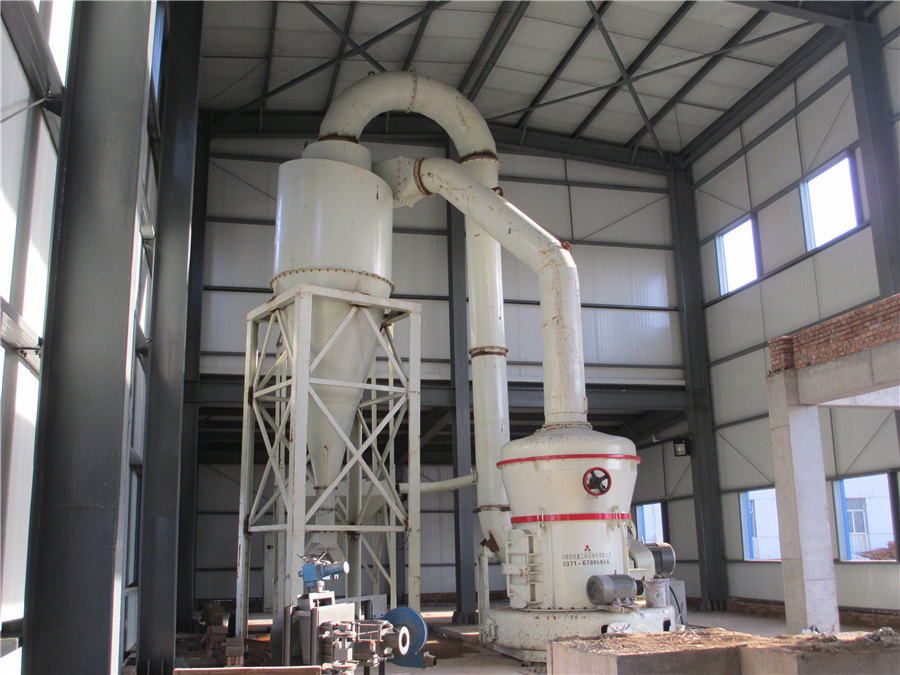
Effect of Grinding Conditions on Clinker Grinding
2024年7月31日 The production of cement, an essential material in civil engineering, requires a substantial energy input, with a significant portion of this energy consumed during the grinding stage This study addresses the gap in By this means, a regular gradation of ball size and of size reduction is produced Figure 722 Hardinge mill There are also nonspherical shapes of grinding media such as Doering Cylpebs Usually, for large scale operations, as in the case of rawmeal grinding mills or cement mills, only continuous mills are usedBall Mill an overview ScienceDirect TopicsPrevious Post Next Post Contents1 Ball charge optimization2 1 How to use the BP21 2 Description of the main indicators used in this BP2101 The residue on 2mm/4mm before partition wall2102 Material filling level and ball charge expansion211 Cement mill specific power 1st compartment 212 Raw mill specific power 1st compartment Ball charge Ball charge optimization INFINITY FOR CEMENT EQUIPMENTCement Ball Mill Feeding Size: ≤25 mm Milling Capacity: 20 – 130 t/h Gross Weight: 106 – 310 t Application: grinding and milling of cement clinker, raw meal, etc Grinding Compartment A cement ball mill is generally divided into two or three grinding compartmentsCement Ball Mill Cost Effective Cement Grinding Mill from
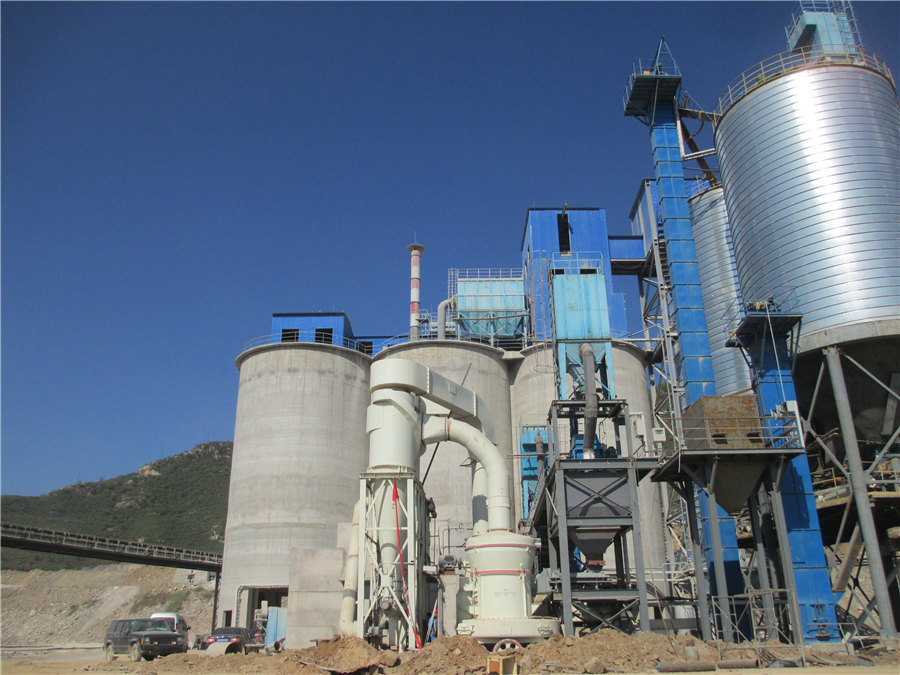
Ball charges calculators
Ball top size (bond formula): calculation of the top size grinding media (balls or cylpebs):Modification of the Ball Charge: This calculator analyses the granulometry of the material inside the mill and proposes a modification of the ball charge in order to improve the mill efficiency:2015年10月23日 Multicompartment ball mills are relatively inefficient at size reduction and have high specific energy consumption (kWh/t) Typical specific energy consumption is 30 kWh/t in grinding of cement A comparison between the grinding systems and conventional ball mills applied in cement grinding circuits is given in Table 5EnergyEfficient Technologies in Cement Grinding IntechOpenThis table shows the range of FLSmidth ball mills for cement grinding, with capacities up to ~10 000 kW in an array of mill diameters and lengths Mill Motor * Size (D x L)(m) Speed (rpm) Installed motor Power (kW) 38 x 13 1686 2570 42 x 125 1603 3130 42 x 145 1603 3660BALL MILL FLSmidth CementBall mill is the cement crushing equipment in the cement plant materials mixed in a certain proportion will firstly enter the cement ball mill for grinding and then be sent to the powder concentrator by bucket the output of the closedcircuit ball mill is 15% ~ 25% higher than that of the opencircuit ball mill with the same sizeBall Mill In Cement Plant Cement Ball Mill AGICO Cement
.jpg)
An Introduction to Clinker Grinding and Cement Storage
The specific energy consumption of a ball mill is greater than that of a vertical mill (VRM) that performs the same operations by a factor of between 15 and 2, depending on the degree of optimization of the ball mill Today, cement Cement Services Solutions Contact us now Ball Mill Overview the grinding balls that move inside the mill and the material ensure the material is ground down to the desired size Grinding balls are used to grind materials into fine Grinding ball Magotteaux2024年7月31日 PDF The production of cement, Effect of Grinding Conditions on Clinker Grinding Efficiency: Ball Size, Mill Rotation Speed, and Feed Rate July 2024; Buildings 14(8):2356;Effect of Grinding Conditions on Clinker Grinding Efficiency: Ball Size 2004年12月1日 During the last decade, semifinishgrinding plants have been used more and more for the energy efficient grinding of highquality cement In 1999, it was found that by decreasing the ball charge Optimization of continuous ball mills used for finishgrinding
.jpg)
The cement mill
Cement manufacturing brief description of a cement mill Cement clinker is usually ground using a ball mill This is essentially a large rotating drum containing grinding media normally steel balls As the drum rotates, the motion of the balls crushes the clinker The drum rotates approximately once every couple of secondsThe proven classical option for cement grinding Whether employed as a twocompartment separator mill in an independent grinding system, or in combination with a high pressure grinding roll, the Ball Mill is a robust and reliable alternative for cement and granulated blast furnace slag grinding Used in combination with the sepol® highefficiency separator, ball mills can reliably Ball Mill thyssenkrupp PolysiusThis document discusses optimizing cement separator and ball mill systems through periodic testing and evaluation It provides guidance on when and why to conduct optimization, including abnormal operations, poor performance, or high costs Conventional grinding systems and their main components are described The document then covers ball charge optimization factors Cement Separator Ball Mill Optimization PDF Mill (Grinding Ball Mill Grinding Media Max Ball Size Calculation Free download as Excel Spreadsheet (xls), PDF File (pdf), Text File (txt) or read online for free The document contains data on the relationship between feed size (F80), drum diameter (De), and maximum ball size for different cement production parameters It shows that as feed size increases from 2 to 30 mm, the Ball Mill Grinding Media Max Ball Size Calculation
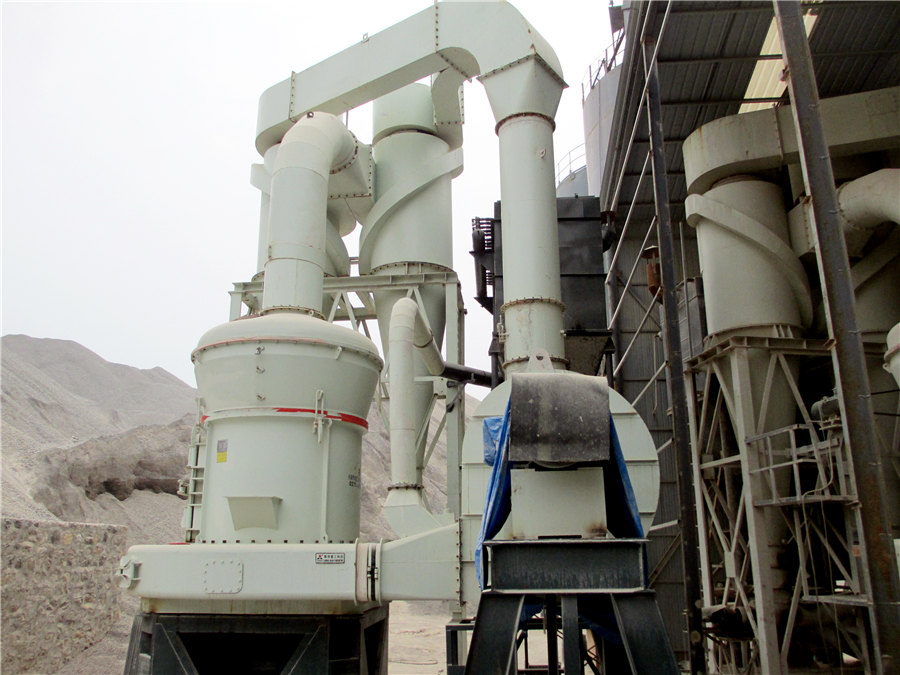
Ball mills FLSmidth Cement
Ball mill for cement grinding An inefficient ball mill is a major expense and could even cost you product quality The best ball mills enable you to achieve the desired fineness quickly and efficiently, with minimum energy expenditure and low maintenanceCement Vertical Mill vs Ball Mill Free download as PDF File (pdf), Text File (txt) or read online for free This document compares vertical roller mills to ball mills for cement grinding It discusses that while vertical roller mills have advantages over ball mills for raw material grinding, ball mills remain more commonly used for cement grindingCement Vertical Mill Vs Ball Mill PDF Mill (Grinding) Scribd