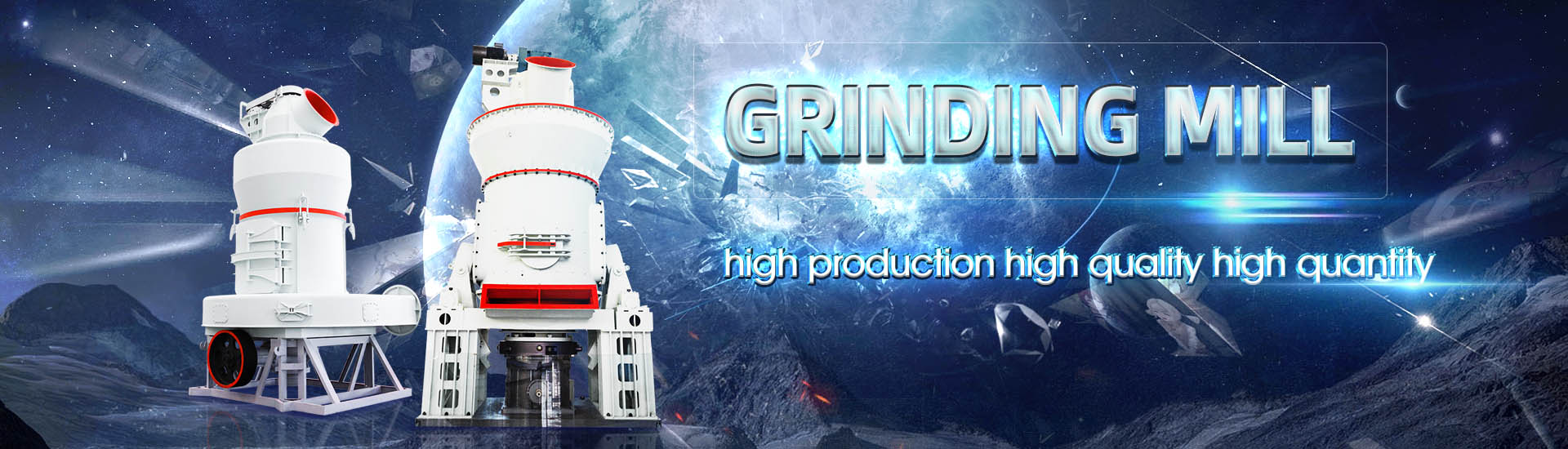
How much is the mill used to produce cement
.jpg)
The Comprehensive Guide to Cement Plant Costs: An
The cement mill grinds the clinker to a fine powder, which is then mixed with gypsum to form cement Equipment: Ball mills, vertical roller mills Technical Specifications: Ball Mills: 1030 tons/hour capacity, 5001500 kW motor The use of a ball mill is common in the cement production process, as it is efficient, costeffective, and able to produce a consistent product size The production of clinker in a kiln is a key Cement Production Demystified: StepbyStep Process and Carbon The cement mill grinds the clinker to a fine powder A small amount of gypsum a form of calcium sulfate is normally ground up with the clinker The gypsum controls the setting properties of the cement when water is addedCement manufacturing: components of a cement plant There are six main stages of the cement manufacturing process The raw cement ingredients needed for cement production are limestone (calcium), sand and clay (silicon, aluminum, iron), How Cement is Made Cement Manufacturing Process
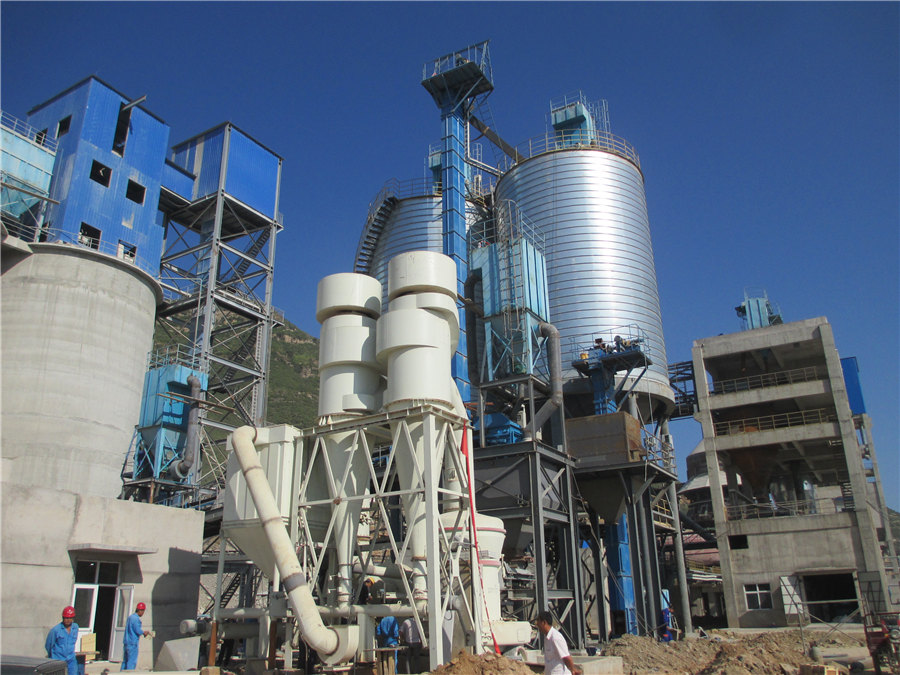
The cement mill
Cement clinker is usually ground using a ball mill This is essentially a large rotating drum containing grinding media normally steel balls As the drum rotates, the motion of the balls crushes the clinker The drum rotates The clinker keeps cooling and a ball mill grinds it with gypsum or other ingredients into fine cement—about 150 billion grains per pound Blending in higher ratios of limestone or SCMs can reduce a plant’s carbon footprint by up to 10% The How Cement is Made Portland Cement AssociationRaw material mill This takes places in vertical steel mill, which grinds the material through the pressure exerted by three conical rollers Which roll over a turning milling table Horizontal Cement Production: How Cement Is Manufactured CEMEX UK2021年8月29日 A year, factories usually have to produce about 800,000 tons of clinker, if in the past they had to use more than 136,000 tons of 4A bran coal, now thanks to the application of the solution of using coal oxide in the production of Coal and its application in the cement production
.jpg)
How Cement is Made Cement Manufacturing Process
Stage of Cement Manufacture There are six main stages of the cement manufacturing process Stage 1: Raw Material Extraction/Quarry The raw cement ingredients needed for cement production are limestone (calcium), sand and clay (silicon, aluminum, iron), shale, fly ash, mill scale, and bauxite The ore rocks are quarried and crushed into smaller pieces of about 6 inches2023年7月10日 The clinker is finely ground with gypsum and other additives to produce cement This process consumes substantial amounts of energy, primarily in the form of fossil fuels, leading to significant Cement Manufacturing Process and Its Environmental 2020年3月1日 Manufacturing cement requires energy intensive processes; and consumes almost 15% of the total demand for energy in industry [3]On average, to produce one ton of cement, 34 GJ of thermal energy (in dry process) and 110 kWh of electrical energy are needed [4, 5]Furthermore, manufacturing a ton of cement releases 073–099 tons of CO2 [6] which A decision support tool for cement industry to select energy 2003年6月5日 Required water:cement ratio to achieve a slump of 60 to 70 mm in concretes made with different cements Cement E contained a limestone not conforming to the EN 1971 criteriaThe Use of Limestone in Portland Cement: A StateoftheArt
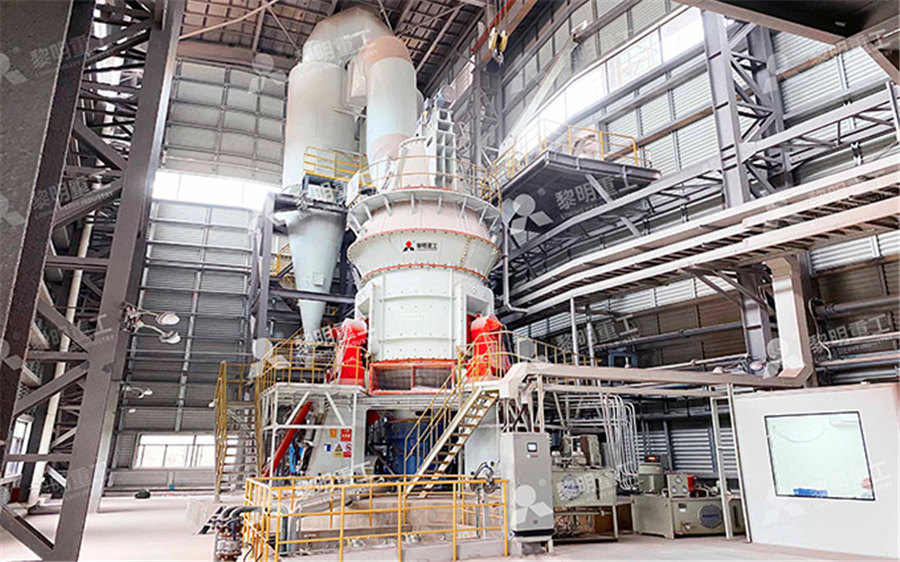
How much energy is used to produce 400 cement?
The energy consumption for cement production varies significantly depending on the specific processes involved On average, the cement industry consumes about 4 GJ/ton of cement, with 75% of this energy attributed to thermal energy for clinker production Additionally, approximately 110 kWh of electrical energy is used to produce one ton of cement, with 26% of this electricity would be a length of 135 m and a diameter of 25 m, with a speed of approximately 20 revolutions per minute Such a mill would normally have a load of approximately 90 tons of grinding media, graduated from 90 mm to 60 mm in the first chamber, 50 mm to 15 mm in the second chamber and 15 mm down in the final chamberAn Introduction to Clinker Grinding and Cement Storage2023年12月20日 The result is called clinker, which are rounded nodules between 1mm and 25mm across The clinker is ground to a fine powder in a cement mill and mixed with gypsum to create cement The powdered cement is then mixed with water and aggregates to form concrete that is used in constructionThe Cement Manufacturing Process Thermo Fisher Scientific2023年5月27日 The use of limestone powder to replace part of the cement clinker to produce Portland limestone cement (PLC) has become increasingly popular Portland limestone cement is popular for three reasons 1) When burning to form cement clinker, it consumes a lot of energy and releases a lot of carbon dioxide2 Major Roles of Limestone in Cement Manufacturing
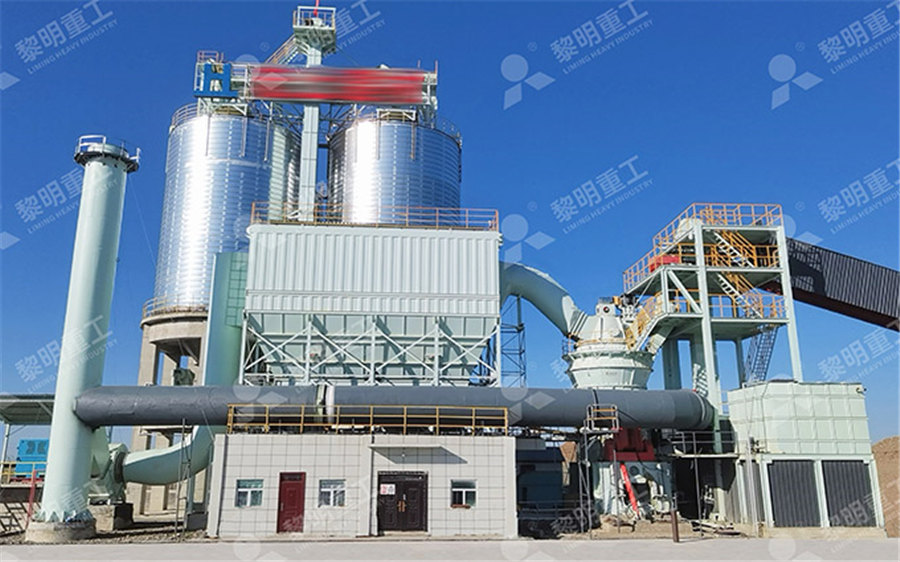
How to Start a Cement Factory
The first thing to do when you are planning to start a cement factory is to determine which type of cement you are going to produce and how many tons you are going to produce per day The most widely used cement for concrete works is ordinary portland cement (OPC), apart from that, there is also pozzolana portland cement (PPC), white portland cement , quicksetting cement , This reduces the capital costs of a new cement plant A dry process kiln might be only 70m long and 6m wide but produce a similar quantity of clinker it is beneficial to minimise clinker temperature as it enters the cement mill The Manufacturing the cement kiln Understanding 2021年7月28日 Cement Mill Ball Mill Closed Circuit: 2320: Cement Mill Ball Mill with HPRG: 065: Packing Plant: 067: Compressor upto clinkerisation: 089: Compressor Cement Griding and Packing: Source: Confederation of Indian Indian Cement Sector CMAThe aim of this work was to evaluate the effect of different inorganic compounds as electron donors for the capture of CO2 from a model cement flue gas CO2/O2/N2 (42:135:823 % v/v) using a non Cement plant flue gas characteristics Download
.jpg)
Cement Euipment Overview Cement Making Machines Cement
2019年9月27日 AGICO offers cement making machines including cement mill, rotary kiln, cement crusher, cyclone preheater, cement dryer, clinker cooler etc any need? Skip to content +86 s about blog contact EN ES Menu Menu Home; Cement Equipment Raw Material processing Stacker And Reclaimer;A typical ball mill can produce 3500 tons of cement per hour Clinker is cooled down in a rotary cooler where steam is used for heating up to 150°C before entering the kiln Grinding begins when raw mix moves towards the mill through either flue gases or airHow is Cement Made? EcoSpecifierAfter cooling, the clinker may be stored temporarily in a clinker store, or it may pass directly to the cement mill The cement mill grinds the clinker to a fine powder A small amount of gypsum a form of calcium sulfate is normally ground up with the clinker The gypsum controls the setting properties of the cement when water is addedCement manufacturing components of a cement plant Understanding CementThe cement industry in the United States produced 828 million tonnes (81,500,000 long tons; 91,300,000 short tons) of cement in 2015, worth US$98 billion, and was used to manufacture concrete worth about US$50 billion The US was the world's thirdlargest producer of cement, after China and IndiaThe US cement industry includes 99 cement mills in 34 states, plus two Cement industry in the United States Wikipedia
.jpg)
Production – Cement
Cement production was 960 million tonnes in 202021, down 1 per cent yearonyear 202021 production was slightly higher than 201516 and 9 per cent higher over the decade Cement imports (including nonCIF members imports) were 057 million tonnes, down 19 per cent yearonyear and 29 per cent higher than in 201011 Overall Australian total cement production (from In both these formulas, the restriction applies that the MgO content is limited to a maximum of 2% In other words, a value of not more than 2% MgO can be used in these formulas Most portland cement clinkers show a liquid content of 25275% Higher liquids produce stickier burningzone clinkerbed appearancesEVERYTHING YOU NEED TO KNOW ABOUT THE CHEMISTRY OF 6 Cement Mill The cement mill grinds the clinker to a fine powder, which is then mixed with gypsum to form cement Equipment: Ball mills, vertical roller mills Technical Specifications: Ball Mills: 1030 tons/hour capacity, 5001500 kW motor power Vertical Roller Mills: 2050 tons/hour capacity, 10003000 kW motor power Example Brands:The Comprehensive Guide to Cement Plant Costs: An InDepth 2021年5月24日 The recirculated dust also shifts burning zone heat toward the kiln inlet, making backend rings and buildups more likely It also contributes to larger, less reactive clinker minerals When clinker cooler air is used for coal mill heating, the fine carryover dust can add large amounts of inert ‘ash’ to the ground coalBetter and cheaper cement: Optimising the right clinker properties
.jpg)
Fact sheet Energy use in the steel industry
energy management systems ensure efficient use and recovery of energy throughout the steelmaking process for use within the steelworks boundary or exported from the site Improvements in energy efficiency have led to reductions of about 60% in energy required to produce a tonne of crude steel since 1960, as demonstrated in Figure 112020年6月24日 The kiln used in the cement industries has a lifetime of 30–50 years The few kilns have been rebuilt to meet the needs of The consumption of the energy in the cement plant is mainly due to raw mill, cooler, preheater and rotary kiln The total energy loss of the plant is generally accounted for about 35–39% of Thermal energy consumption and its conservation for a cement Clinker Grinding: The main process in cement grinding units involves grinding the clinker into a fine powder using a cement ball mill or vertical roller mill This step is crucial as the fineness of the cement determines the rate of hydration and, consequently, the development of strengthStepbyStep Guide to the Manufacturing of Cement PRACTICAL Hydration products The products of the reaction between cement and water are termed "hydration products" In concrete (or mortar or other cementitious materials) there are typically four main types: Calcium silicate hydrate: this is the main reaction product and is the main source of concrete strength It is often abbreviated, using cement chemists' notation, to "CSH," the Cement hydration

Everything you need to know about Kiln System Operations in Cement
Figure 332 Relationship between liquid phase and temperature as a function of A/F ratio A 100% LSF value expresses the theoretical limit to the amount of lime (CaO) that can be added to a mix until all of the calcium would be combined into clinker compounds, with no C2S remaining2020年8月25日 How much do you know about cement production process? A full cement production process includes the cement crushing process, raw mill process, clinker process, and cement grinding process, cement packing process, and related process Find more! Skip to content +86 Cement Production Process Cement Manufacturing Process AGICO CEMENT2022年2月22日 Furthermore, several machines or instruments are required for the production of cement To produce cement, you’ll need a few basic substances in addition to the tools the rock is crushed to a maximum size of about 6 inches In secondary crushers or hammer mills, the rock is crushed to roughly 3 inches or smaller Step 3 How Cement is Made? A Step by Step Process Cement ShopPortland cement clinker overview Portland cement clinker is a dark grey nodular material made by heating ground limestone and clay at a temperature of about 1400 °C 1500 °C The nodules are ground up to a fine powder to produce cement, with a small amount of gypsum added to control the setting properties This page gives a thumbnail sketchPortland cement clinker overview Understanding Cement
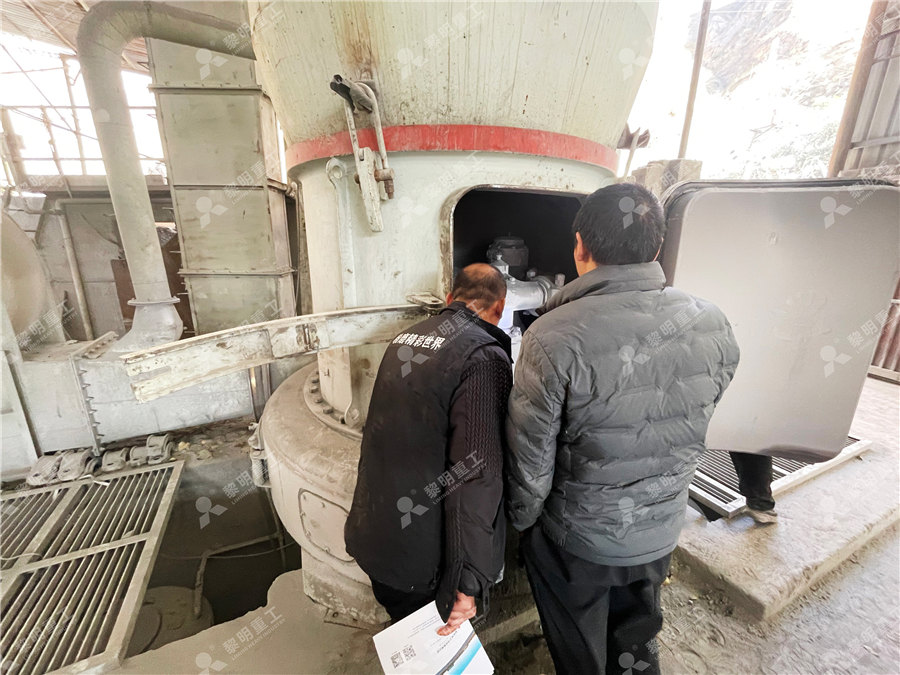
The essentials of electrical systems in cement plants EEP
2020年9月14日 From there the clinker is conveyed to ball mills or roller presses, in which it is ground down to very fine cement, with the addition of gypsum and anhydrite, as well as other additives, depending on the use to which the cement is to be put Step #6 The finished cement is stored in separate silos, depending on type and strength classRoller grinding mills and ball mills grind the mixture to a fine powder at the same time as drying it, before it is conveyed to the raw meal silos for further homogenisation Burning The burning of the raw meal at approx 1,450°C is How cement is made Heidelberg Materials2015年6月30日 The raw material processing consumes about 28 % of the total electricity used in cement production and limestone is the highest proportion of raw material used [Afkhami et al, 2015; Meng et al Energy consumption assessment in a cement production plant1971年8月17日 116 Portland Cement Manufacturing 1161 Process Description17 Portland cement is a fine powder, gray or white in color, that consists of a mixture of hydraulic cement materials comprising primarily calcium silicates, aluminates and aluminoferrites More than 30 raw materials are known to be used in the manufacture of portland cement, and these116 Portland Cement Manufacturing US EPA
.jpg)
Production Process CEMEX Philippines
In the kiln, the raw materials are processed at a very high temperature to produce clinker Clinker is the intermediate product used in the manufacturing of cement There are two primary processes used to manufacture clinker: the dry process and the wet process Our plants use the dry process, which is more energy efficientLearn how vertical roller mill technology is transforming the cement industry Explore its benefits, efficiency, and ecofriendly features VRMs are used to grind and crush the clinker and gypsum used to produce cement Similar to the raw material grinding process, Application of Vertical Roller Mill in Cement Production2011年5月1日 In another study [16], it was found that cement mill, raw mill, crusher and heater consume approximately 38%, 35%, 3% and 24% of total energy, respectively Download: Download fullsize image; Cement kilns use different sources of energy to produce the high temperatures necessary for the clinker formationA critical review on energy use and savings in the cement industriesTo Download Everything About Cement crushers , Kilns , Vertical mill , Cement mill , ETC kindly click here now Preamble It is said that cement manufacture begins in the quarry (Figure 11), which is the commonly used term for opencast mining of minerals and rocks including limestone, the primary raw material for cement productionBasics of mineral resources for cement production
.jpg)
Petroleum Coke in the Cement Industry
Raw material is processed through a mill and fed counterflow into the cement kiln which operates at 1500°C melting the rock to produce clinker This clinker is then further ground to a fine cement powder "Alternative Fuel Use in Cement Manufacturing," Cement Association of Canada and Holcim (Canada) Inc, 2018年10月25日 Here's my full answer for the process diagram task below The diagrams below show the stages and equipment used in the cementmaking process, and how cement is used to produce concrete for building purposes (This task comes from Cambridge IELTS book 8) The first diagram illustrates the process of cement manufacture, and the second diagram shows the IELTS Writing Task 1: process diagram answer IELTS SimonCement is often referred to as Portland cement, a generic term used for nearly all cement It is the mixture from which many types of concrete are made and is called such due to its resemblance to a type of building stone quarried in the early part of the 19th century This stone came from the Isle of Portland, located off the southern coast of EnglandWhat Equipment is Used for Cement Manufacturing?