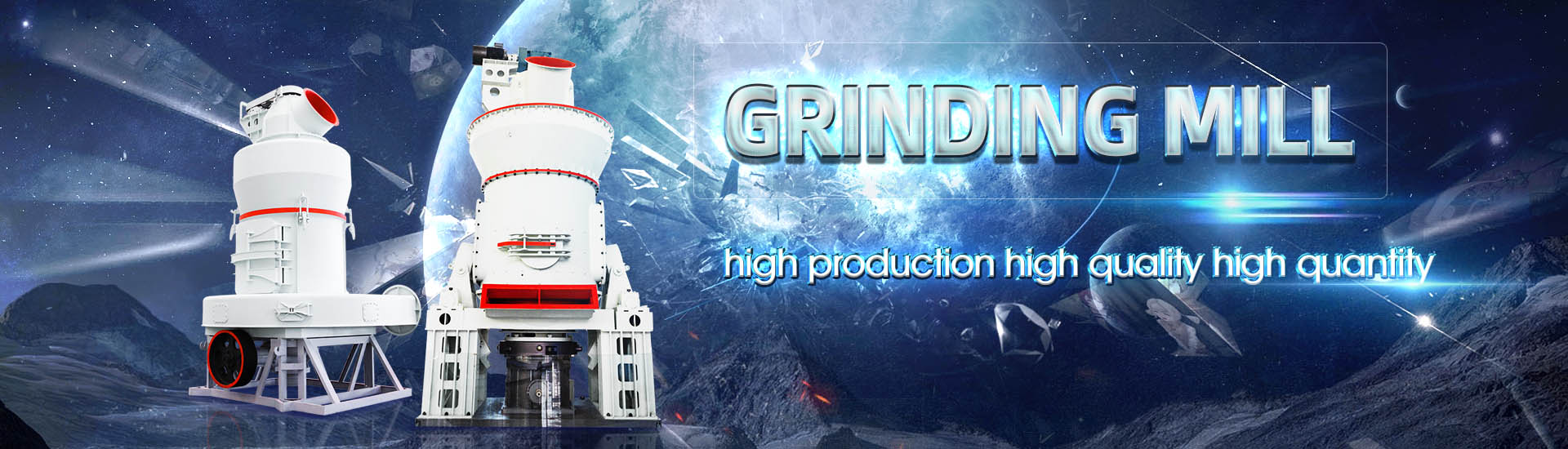
GP11 barite grinding machine fault analysis
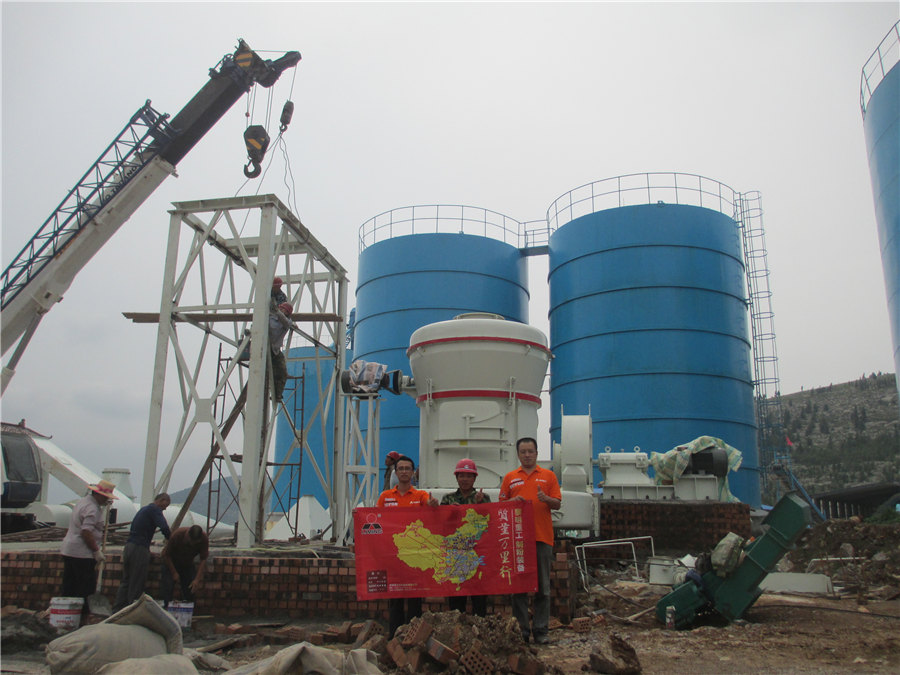
Reliability Analysis of Centerless Grinding Machine Using Fault
The centerless grinding machine consists of a large number of components, assemblies, and components and several failure causes (failure events), the occurrence of which results in the failure of the whole centerless grinding machine or stops functioning or will not give the required output The required failure 展开Abstract: This article explores the corresponding relationship between the equipment fault and grinding quality in a robotic grinding system (RGS), and establishes a unified and lightweight Unified Diagnostic and Matching Framework of Fault and Quality 2021年2月1日 This paper gives an overview of the most important approaches for bearingfault analysis in grinding machines There are two main parts of the analysis presented in this paperA survey of machinelearning techniques for condition monitoring Fault Tree is a graphical representation of major faults or critical failures associated with a system It uses Boolean logic and lowlevel event methods to analyze the possible mechanisms of Reliability Analysis of Centerless Grinding Machine Using Fault Tree
.jpg)
Vibration Analysis for Machine Monitoring and Diagnosis: A
The simplest vibration analysis for machine diagnosis is used to analyze the measured vibration signal in the time domain Vibration signals obtained are a series of values representing A Monte Carlo simulation method based on multisource bayes is proposed to improve the reliability of motorized spindles in cycloid gear grinding machines and reduce their failure rate Fault analysis and reliability evaluation for motorized spindle of 2022年7月1日 This paper proposed a vibrationbased process monitoring method to classify faults generated during grinding processes Gear grinding measurements have been Vibrationbased gear continuous generating grinding fault 2021年9月5日 In order to explore the factors affecting the reliability of the CNC grinding machine spindle system and find out measures to improve the reliability of the CNC grinding machine, Reliability analysis of spindle system of CNC grinder based on fault
.jpg)
Vibration Analysis for Machinery Health Diagnosis Emerson
Vibration analysis can often pinpoint a failing element of a rotating machine in time to avoid catastrophic failure and costly replacement of machinery as well as lengthy2024年5月26日 The integration of ultrasonic signal processing with various machine learning (ML) models can significantly enhance the efficiency of industrial fault diagnosis In this paper, Advanced Industrial Fault Detection: A Comparative Analysis of2023年7月19日 The operation of belt grinding machines is usually accompanied by a significant level of noise and vibration, which adversely affect the health of operators and the accuracy of processing the Theoretical studies of vibrations and noise of grinding belt machines2022年9月9日 Reliability analysis plays a crucial role in the design and operational process Fault Tree Analysis (FTA), one of the reliability evaluation techniques, plays a crucial role in the design processReliability Analysis of Centerless Grinding Machine Using Fault
.jpg)
(PDF) Machine Fault Signature Analysis ResearchGate
2008年2月6日 Vibration analysis is often used to detect localized faults in REB [5,6] The periodic force effects caused by impulsivity at a particular frequency in the presence of a defect are computed using 2023年4月30日 Bearing Fault Detection Scheme Using Machine Grinding Burn F ault in The average accuracies for the five classifiers are 909% for discriminant analysis, 925% for support vector machines, (PDF) Bearing Fault Detection Scheme Using Machine Learning 2021年9月5日 The spindle system is the key component of the CNC (computer numerical control) grinding machine In order to explore the factors affecting the reliability of the CNC grinding machine spindle system and find out measures to improve the reliability of the CNC grinding machine, this paper proposed a reliability evaluation algorithm based on fault data Reliability analysis of spindle system of CNC grinder based on fault The Williams Patent Crusher General Purpose (Type GP) Hammer Mill is a simple, rugged answer to many small and medium capacity particle size reduction jobs The Type GP Hammer Mill can be used in a variety of applications from coal and limestone to salt cake, sawdust, and wood chipsIt’s a versatile machine that can perform efficient particle size reductionType GP Hammer Mills Grinding Machine Williams Crusher
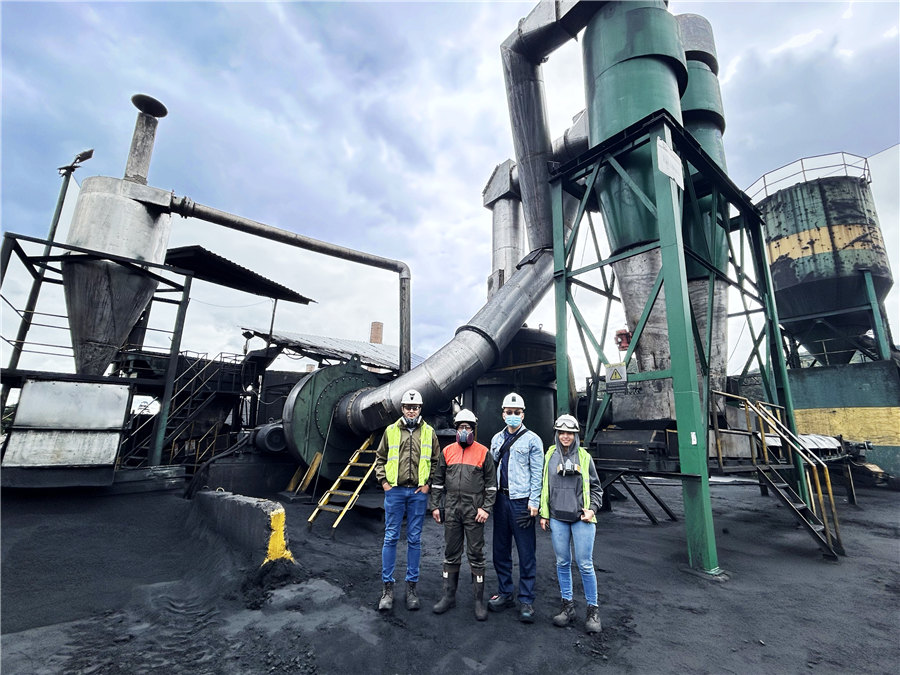
ANALYSIS AND CONTROL OF VIBRATION IN GRINDING MACHINES
2014年6月25日 Download Citation ANALYSIS AND CONTROL OF VIBRATION IN GRINDING MACHINES Vibration in grinding machine is hard to measure It is witnessed from the formation of waviness on the work piece and 2023年5月10日 to enhance the fault data set with an insufficient number of fault samples and applies it to fault diagnosis The effectiveness of the method is verified by an example(PDF) Bearing Fault Diagnosis Using ACWGANGP Enhanced by 2018年12月7日 To effectively extract the fault feature information of rolling bearings and improve the performance of fault diagnosis, a fault diagnosis method based on principal component analysis and support vector machine was presented, and the rolling bearings signals with different fault states were collected To address the limitation on effectively dealing with the raw Fault diagnosis method of rolling bearing using principal 2020年3月17日 The horizontal axis represents the rotor speed, at the vertical axis is the vibration deflection SS follows approximately the centrifugal force 312 Flexible Rotors Also, here we might notice this “basic curve” as well (dependent on the unbalance amount and distribution), but as soon as the rotor passed its 1st critical speed, it changes from a “solid Fault Analysis: Vibration Causes and Case Studies
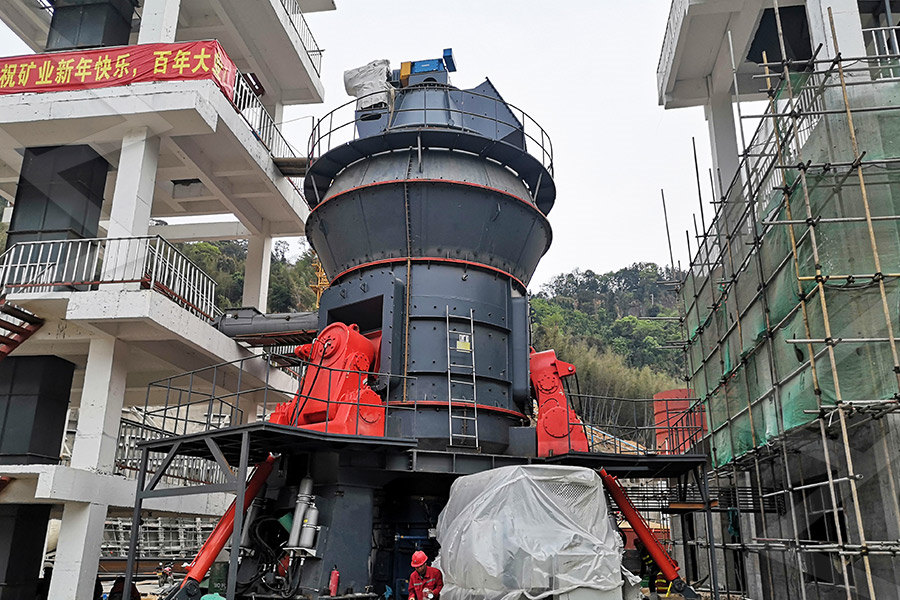
(PDF) Machining Processes and Machines: Fundamentals, Analysis
2020年12月15日 Machining is one of the eight basic manufacturing processes This textbook covers the fundamentals and engineering analysis of both conventional and advanced/nontraditional material removal 2023年6月2日 To increase the reliability of cycloidal wheel grinding machines, reduce the failure rate of machine tools, and shorten maintenance times, a reliability modeling method for smallsample fault data Reliability modeling and analysis of cycloid gear 2021年8月2日 Barite is mainly used in petroleum, chemical, paint, filler and other industrial sectors after barite grinding machine powder, of which 80 to 90% is used as a mud weighting agent in petroleum drilling The blower blows air from the splitter disk into the grinding chamber, and sends the crushed powder to the analysis chamberBarite Ore Grinding MillCLIRIK Machinery2023年6月1日 Thus, fault analysis has recently received increasing attention worldwide due to its extensive applications and has become a field of research increasingly hot and popular In the forthcoming years, machine learning will become even more significant due to the presence of a huge volume of fault analysisrelated dataMachine learning for fault analysis in rotating machinery: A
.jpg)
(PDF) Reliability analysis of cooling system of CNC grinding machine
2019年10月19日 Fault Tree Analysis (FTA) is a systematic approach that identifies weaknesses, evaluates possible upgrades, and monitors and predicts behavior and has been used in various areas [8][9][10][11 The barite grinding production line is a production line specially used to process barite raw ore into fine barite powder; it has the advantages of simple configuration, stable operation, high output, low energy consumption, and the fineness of the finished product meets the requirements Barite is a pure natural stone with high practical value in mining, machinery, metallurgy, Barite Grinding Production Line TAYMACHINERY2024年4月17日 The fineness of barite powder is one of the crucial factors to consider when selecting a barite milling machine Barite powder grinding is generally classified into three fineness levels: coarse powder processing (≤ 100 mesh), fine powder processing (120 mesh–325 mesh), and ultrafine powder processing (400 mesh–800 mesh)Quick Pick: Compare 4 Top Barite Grinding Mills for Your NeedsDownload scientific diagram Gear grinding machine fault frequency table from publication: Reliability modeling and analysis of cycloid gear grinding machines based on the bootstrapbayes method Gear grinding machine fault frequency table ResearchGate
.jpg)
Analysis of faults in machine and transformer windings EEP
2019年1月2日 Effective impedance under fault The analysis of faults in the synchronous machine and transformer windings presents a special difficulty because the effective impedances of the affected windings under internal fault conditions are not normally Synchronous machine with fault position F, a perunit distance x from the neutral point2019年9月20日 Mishra AKDA (2015) Computation effort and effect of signal processing techniques in condition monitoring and fault diagnosis of machine Int J Adv Res Electr Electron Instr Eng 4:7 Google Scholar Xue S, Howard I (2018) Torsional vibration signal analysis as a diagnostic tool for planetary gear fault detectionVibration Analysis Methods for Misalignment and ToleranceThe crushed barite small pieces are sent to the silo by elevator and then evenly and quantitatively sent to the grinding chamber of the mill by the vibrating feeder for grinding Stage 3: Grading The powder classifier classifies the ground Barite Aggregate Processing JXSC Machine2024年7月1日 Qin et al [19] present a fault diagnosis method based on ML algorithms such as principal component analysis (PCA) and a support vector machine This work’s proposed system also develops a fault detection model using current signals from grinding machines with feature extraction methods and ML algorithmsDeveloping a datadriven system for grinding process parameter
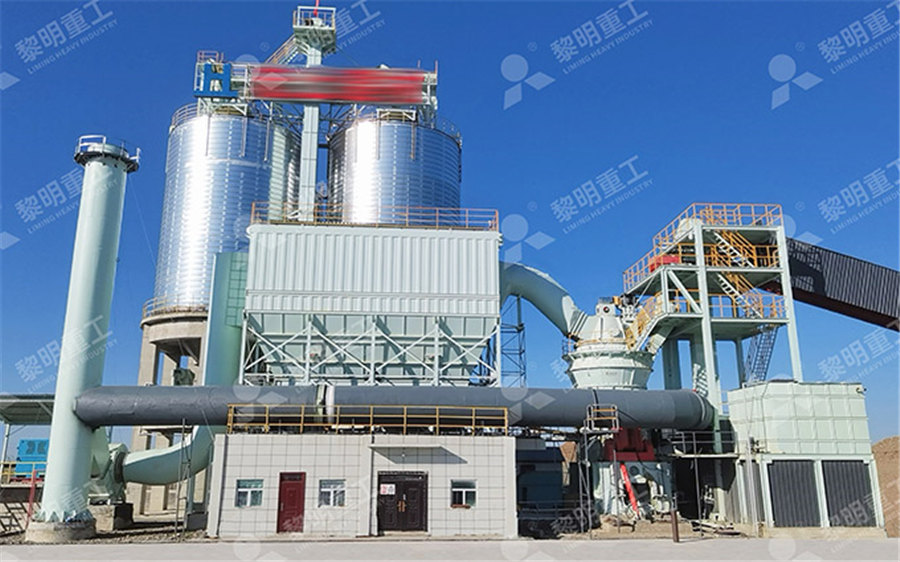
Gear Profile Grinding GP 500 H EMAG SU
Internal Grinding through Twin Spindle Principle The EMAG SU GP 500 H gear profile grinding machine features an array of innovations and establishes at the same time the new improved base for all machines of the horizontal profile 2018年1月1日 Fault tree of a hydraulic system: subtree VIII Deposition of contaminants in filter Z 57 Pipe joint leakage Z 6 Filter not replaced or cleaned Z 58 Pipe leakage Z 7 Filter element damage Z 59 Fault Tree Analysis: A Case Study from Machine Tool IndustryWith barite being used for a multitude of industries, our Sales Managers and Agents will help find you the barite grinding machine that will be most suitable for your application Learn more about our barite grinding mills below or contact us today to discuss your project in detailBarite Grinding Mills Barite Crushers Williams Crusher2023年11月21日 For instance, Qi et al presented a machinelearningbased faultdiagnosis system for reciprocating compressors, utilizing denoised data and support vector machine (SVM) for fault recognition 42 Huang et al introduced a cloudbased intelligent fault diagnosis (IFD) method for planetary gearboxes using deep residual networks by leveraging the computational Advances in vibration analysis and modeling of large rotating
.jpg)
Comprehensive Diagnosis of Localized Rolling Bearing Faults
2024年1月16日 The analysis of electrical machine faults during startup, and variable speed and load conditions offers numerous advantages for fault detection and diagnosis In this context, diagnosing localized bearing faults through vibration signals remains challenging, particularly in developing physically meaningful, simple, and resamplingfree techniques to monitor fault 2024年11月4日 Accurate and timely fault detection is crucial for ensuring the smooth operation and longevity of rotating machinery This study explores the effectiveness of imagebased approaches for machine fault diagnosis using data from a 6DOF IMU (Inertial Measurement Unit) sensor Three novel methods are proposedPredictive Analytics and Fault Diagnosis of Machines with Machine Sustainability 2023 gp: gp= E 2 (7) gp = EBearing Fault Diagnosis Using ACWGANGP Enhanced byBarite Grinding Mill 989 likes Shanghai Clirik Machinery Co,Ltd is the professional barite grinding mill manufacturer, devoted to the barite powder grinding process more than 10 yearsBarite Grinding Mill Facebook
.jpg)
Vibration Analysis for Machinery Health Diagnosis Emerson
Each machine fault generates a specific vibration pattern The frequency of the vibration is determined by the machine geometry and operating speed A single vibration measurement provides information about multiple components When evaluating any machine’s health, the analyst should: 12024年5月26日 Modern condition monitoring and industrial fault prediction have advanced to include intelligent techniques, aiming to improve reliability, productivity, and safety The integration of ultrasonic signal processing with Advanced Industrial Fault Detection: A Comparative 2021年9月23日 Recommended barite grinding mill: In the barite processing line, the grinding mill is a very important and indispensable part Barite industrial ultrafine grinding mill machine can grind barite into a fine powder, the highest Barite Industrial Ultrafine Grinding Mill SBM 2021年6月1日 The success of the manufacturing process which involves grinding as one of the stages depends solely on the accuracy of the grinding process Being the last stage of the manufacturing path, it is mostly done to provide the desired surface finish to the product This makes the stage very crucial To prevent the ruining of all the previous stages and efforts, the Development of Realtime Grinding Process Monitoring and Analysis
.jpg)
(PDF) AN OVERVIEW OF FAULT TREE ANALYSIS (FTA) METHOD
2013年3月1日 Based on the conducted analysis, proposals were made to improve the printing process with UV inks A fault tree as a tool of the Fault Tree Analysis FTA method (Patil, 2013) was used to analyse 2022年8月29日 ANN is widely used in reliability and fault analysis of mining machines Several literature works can be found using ANN for analysis ANN h as been used in mining since the early 2000s(PDF) A Review of Reliability and Fault Analysis Methods for 2023年12月13日 Fault diagnosis using vibration analysis can be used for crack detection in a rotor system Crack detection of cracked rotor [AS Sekhar and BS Prabhu] can be analyzed using vibration analysisFAULT DIAGNOSIS IN ROTATING MACHINES USING VIBRATION ANALYSISBarite grinding is generally divided into four types, namely, coarse powder processing (≤80 mesh), fine powder processing (80 mesh400 mesh), ultrafine powder processing (200 mesh2500mesh), and micro powder processing (400mesh3000 mesh)Which Should You Choose Barite Grinding Mills?
.jpg)
A review on fault detection and diagnosis techniques: basics
2020年11月10日 Statistical approaches are very effective for quick fault detection but generally not suited for classification and diagnosis purposes On the other hand, nonstatistical analysis of measured signal is often carried out by using machine learning and pattern recognition techniques (Soualhi et al 2013; Malhi and Gao 2004)2021年11月15日 Accurate and early detection of machine faults is an important step in the preventive maintenance of industrial enterprises It is essential to avoid unexpected downtime as well as to ensure the reliability of equipment and safety of humans In the case of rotating machines, significant information about machine’s health and condition is present in the An Expert System for Rotating Machine Fault Detection Using