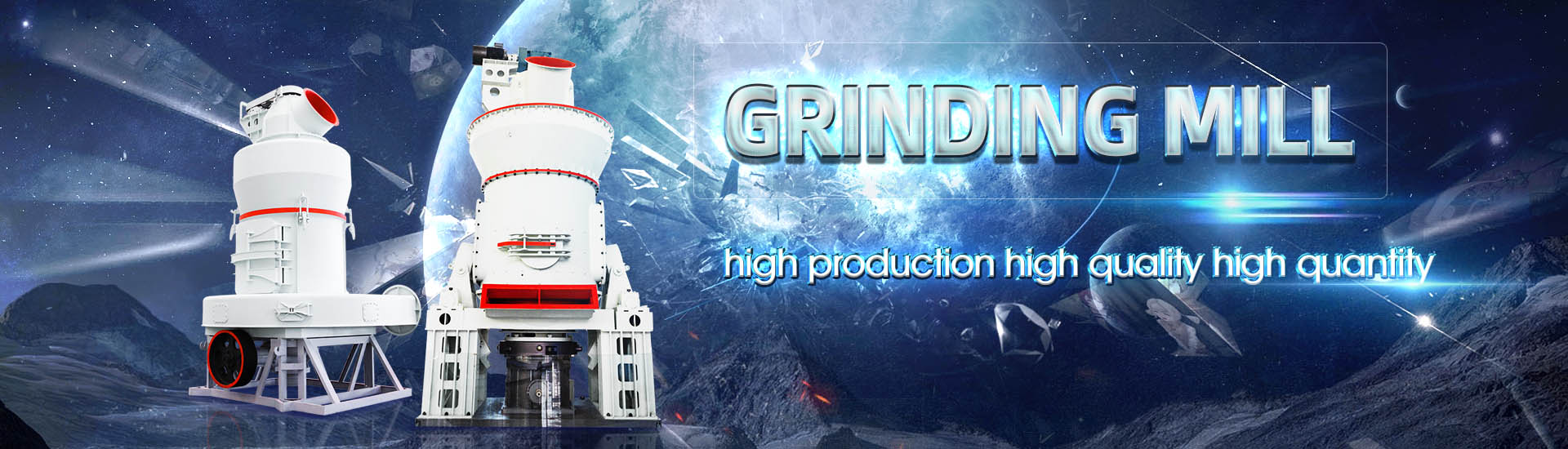
Coal mill monitoring io point
.jpg)
Instrumentation and control in coalfired power plant
2018年1月28日 this review Automation and control in coal preparation will not be addressed in this report but is discussed in detail in a previous Clean Coal Centre publication by Couch (1996) This report will discuss instrumentation and control (IC) in conventional, pulverised coal (pc) 2024年5月1日 To avoid abnormal operating conditions of coal mills in time and effectively, a dual fault warning method for coal mill is proposed Three typical faults of coal mill plugging, coal Dual fault warning method for coal mill based on2021年6月10日 Safe coal handling practices are designed to ensure that the fuel remains intact throughout its journey from the mine until the point at which it is ignited in the boiler Risks of COAL MILL Land Instruments International2010年3月1日 By adopting this multisegment coal mill model in power plants, the power plant engineers will be offered a nonstop model for monitoring the coal mill system The model can estimate the(PDF) Condition Monitoring of Power Plant

Monitoring Model of Coal Mill in Power Plant Based on Big
Abstract: In order to monitor the wear condition of grinding roller of coal mill in power plant and improve the reliability of production equipment, it is necessary to establish a state monitoring 2022年5月31日 In this paper, a brannew GAIFCMIDHGF assessment method is proposed Genetic algorithm (GA) is first applied to optimize initial parameters, which is fundamental and A brannew performance evaluation model of coal mill2014年4月1日 The online model is used for mill condition monitoring in two ways: (i) to compare the predicted and measured mill output pressure and temperatures and to raise alarms if there A new modelbased approach for power plant Tubeball mill 2023年8月13日 Outlet temperature and CO are established methods of detecting fires in mills, but at present they are not very effective for detecting small fires The CO detection system Condition Monitoring of Power Plant Milling Process
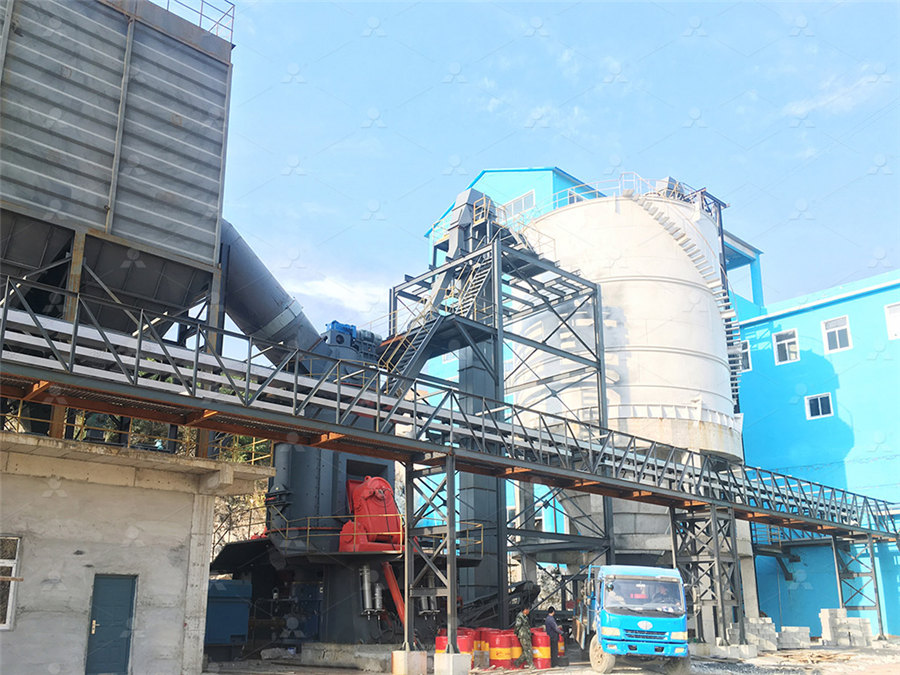
COALFIRED POWER PLANTS Land Instruments
2021年2月12日 From coal stockpile through to boiler, there are many transfer points and storage areas that must be monitored for the onset of spontaneous combustion If these areas are not Abstract: Coal mill is the main equipment in the industrial pulverizing system It is the key to ensure the stable and efficient operation of the pulverizing system to effectively use the Process monitoring and abnormal reason tracing of coal mill 2021年8月1日 The MHQI monitoring and prediction model assesses the working zone's air health status in an underground coal mine Finally, the toxic gas concentration monitoring and prediction module have a forecasting mechanism for predicting different gas concentrations, like CO 2, CH 4, CO, NO 2, SO 2, and H 2 S in the working face and goaf area inside a Hybrid CNNLSTM and IoTbased coal mine hazards monitoring 3 天之前 CODEL’s products for coal mill monitoring offer advanced technology and reliable performance to meet the stringent demands of coalfired power plants With continuous CO monitoring, CODEL’s systems provide realtime Coal Mill Monitoring CODEL International LTD
.jpg)
An investigation of performance characteristics
2020年8月12日 This study shows the performance of a currently running vertical roller coal mill (VRM) in an existing coalfired power plant In a power plant, the coal mill is the critical equipment, whose 2019年12月11日 CPT crossing point temperature CSIT critical selfignition temperature DNRM Department of Natural Resources and Mines, (Queensland) Australia 312 Models to predict coal behaviour 19 32 Monitoring as a preventative measure 21 321 Gas monitoring 22 322 Heat/light monitoring 27Assessing and managing spontaneous combustion of 2019年11月21日 coal and the high temperature inside the mill lead to rapid oxidation of the coal This results in further heat buildup and the potential for a ire If the mill is restarted without irst removing the hot coal, an explosion can occur when particles are suspended and exposed to the inrushing combustion air Even in routine mill shutdowns, there isSTRENGTHENING PLANT SAFETY IN COAL GRINDING 6 天之前 CO Mill Fire Monitoring, getting the design right for a reliable CO measurement for the early detection of fires Single Point Flow Monitors TunnelTech 305 Air Flow Monitor; Single Multi Gas Electrochemical Cell Spontaneous combustion of coal in a coal handling system (coal conveyors, coal mills, coal silos, coal bunkers) has long CO Mill Fire Monitoring Systems CODEL International LTD
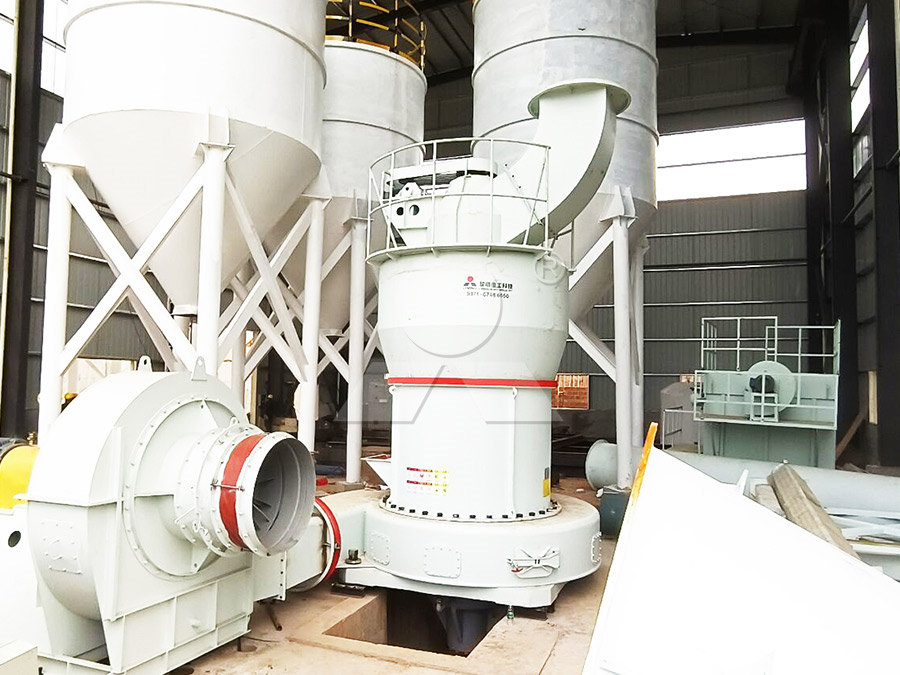
In discussion: Coal Mill Safety Coal Mill Safety, Explosion
2024年10月31日 In discussion: Coal Mill Safety At best, coal mill safety is not well understood and, at worst, it is ignored When it comes to coal mill systems, most cement plant operators just presume that the supplier of the equipment knows all of the standards and rules and is 100% capable of making a system that conforms to these and is therefore safe2020年6月19日 Safe coal handling practices are designed to ensure that the fuel remains intact throughout its journey from the mine until the point at which it is ignited in the boiler It takes as little as 14 kg (3 lbs) of pulverised coal in 28 m 3 (1,000 ft3) of air to form an explosiveCOAL HANDLING SAFETY2015年8月1日 Mill problems originate mainly due to poor controls or faults occurring within the milling system As discussed by GQ Fan and NW Rees [3], the control of mills remains very simple in most of the power plants due to the fact that the mill system is highly nonlinear with strong coupling among the variables and it is very difficult to measure some important Review of control and fault diagnosis methods applied to coal mills2020年3月19日 ONLINE COAL FLOW MEASURING AND BALANCING (CONTROL) AND ONLINE COAL FINENESS MEASURING SYSTEM FOR COMBUSTION OPTIMISATION IN A THERMAL BOILER Suresh G Chandwani1, Dr Francesco Turoni2, Reinhardt Kock2, Dr Michael Haug2, Dr Michael Schreiber2 1NSGuzder Company Pty Ltd, Neville House, Currimbhoy CPRI Online Coal Flow Balancing and Fineness
.jpg)
A unified thermomechanical model for coal mill operation
2015年11月1日 As presented by Andersen et al (2009) and Odgaard, Stoustrup, and Mataji (2007), coal moisture imposes limit on the maximum load at which a coal mill can be operated and the load gradient (how fast the mill may change its operating point), if it is desired that the pulverized coal entering the furnace has moisture content less than or equal to 2010年7月14日 the coal If the coal mill heating process is treated as happening in an isolated environment as shown in Figure 3, the heat input into the coal mill and the heat output from the coal mill complies with the heat balance rule The heat into the coal mill Q in includes the heat from raw coal Q coal, the heat from the hot air Q airMathematic Modeling and Condition Monitoring of Download Citation On Nov 1, 2019, Yanping Li and others published Monitoring Model of Coal Mill in Power Plant Based on Big Data and BP Neural Network Find, read and cite all the research you Monitoring Model of Coal Mill in Power Plant Based on2023年6月18日 Underground coal mine environment is hazardous and accident prone The present work proposes an internet of things (IoT) based smart under ground mine monitoring system at the excavation site The developed system establishes a communication link to enable data transmission between underground smart devices and above the ground monitoring IoT and LoRa based smart underground coal mine monitoring
.jpg)
A brannew performance evaluation model of coal mill
2022年5月31日 There are two points to explain On the one hand, the relationship between input variables and output variables of mechanism models so complicated that it is extremely difficult to find an accurate function Abnormal condition monitoring and diagnosis for coal mills based on support vector regression IEEE Access, 7 (2019), pp 2010年3月1日 By adopting this multisegment coal mill model in power plants, the power plant engineers will be offered a nonstop model for monitoring the coal mill system The model can estimate the (PDF) Condition Monitoring of Power Plant Milling Process 2021年2月12日 • Monitoring coal transport, storage and preparation • Maximising efficiency of coalfired furnaces and boilers • Ensuring emissions compliance This application note aims to provide an overview of the many technologies available for monitoring essential operations in coalfired power generation and their respective limitations and COALFIRED POWER PLANTS Land Instruments In order to monitor the wear condition of grinding roller of coal mill in power plant and improve the reliability of production equipment, it is necessary to establish a state monitoring model with high accuracy and good prediction effect It has been shown that the power of coal mill can reflect the wear degree of grinding roller If the voltage and power factor of coal mill are constant Monitoring Model of Coal Mill in Power Plant Based on Big
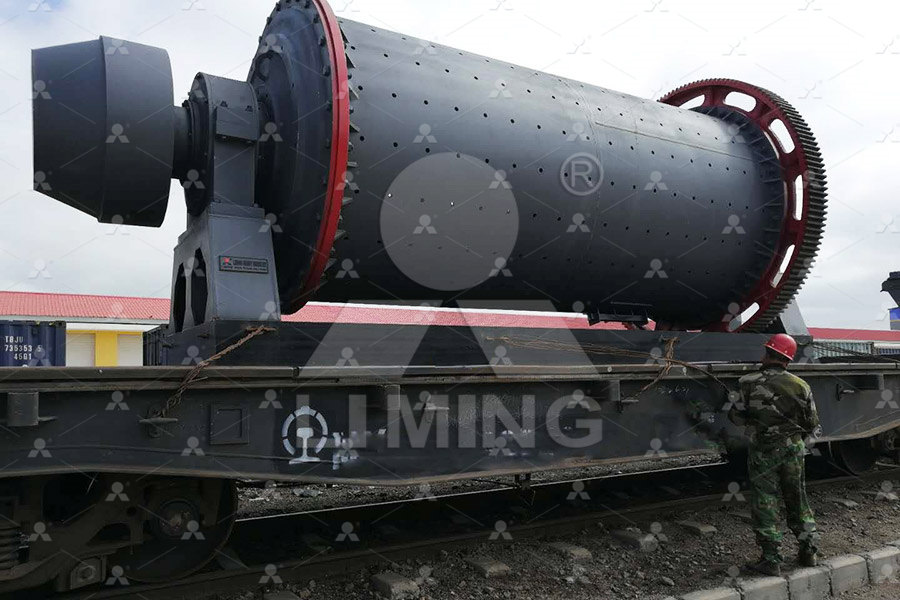
Decision Support System for Coal Mill Fault Diagnosis in
The coal mill under study is a vertical roller type, such as the one available at the PLTU (coalfired steam power plant) Rembang unit, which has two boilers with a steam generator capacity of 513 t/h The schematic of a coal pulverizer mill is provided in Fig 12011年4月30日 The application of MPC to coal mills can b e considered in tw o di eren t lev els of complexit y The rst lev el comprises the con trol tasks related to the op eration of individual coal mills A typical con trol strategy for a coal mill is based on receiving a coal feeder reference The con trol loop for theCoal Mill Modeling for Monitoring and Control NTNU2019年1月1日 The work in this part is based on a ZGM113N medium speed coal mill equipped in a subcritical 600MW unit Combined with existing research [1, 53] and relevant theoretical knowledge [54], 15 Abnormal Condition Monitoring and Diagnosis 2024年5月1日 Taking the selected important monitoring parameters of coal mills as an example Using the actual operation data of a mediumspeed coal mill in a power plant in eastern China on April 30, 2022, a multioutput regression predictive condition monitoring fault early warning model for coal mills based on Autoformer WaveBound is establishedDual fault warning method for coal mill based on
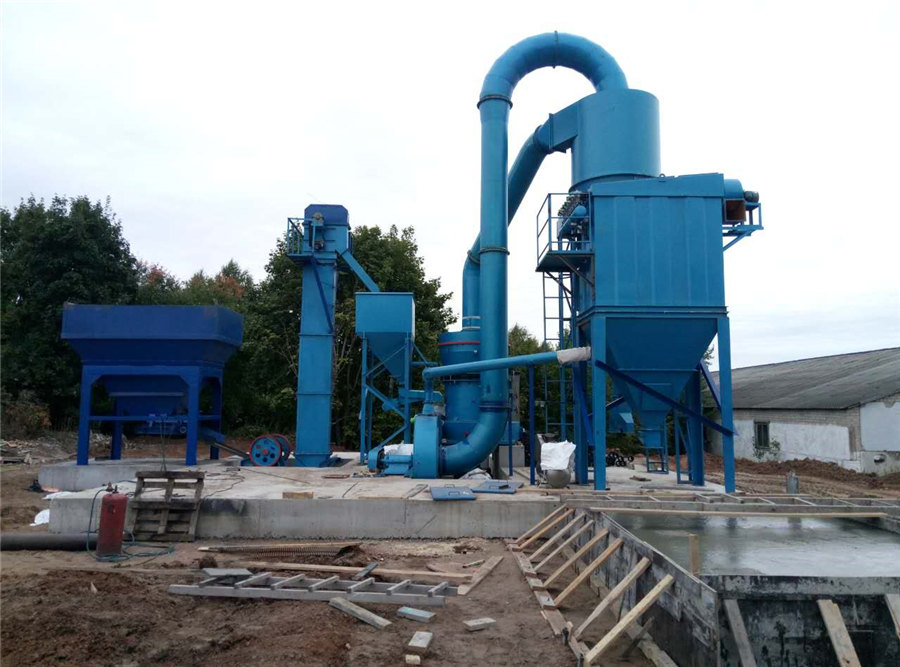
Advanced CGA Solutions ACX Analyzer Systems for
2024年3月13日 – Emission monitoring using performancetested analyzers – Process control in cement rotary kilns and calciners – Process control in rotary kilns with wet process – CO monitoring and emission monitoring in cement plants – Coal bin and coal mill monitoring in cement plants – Process measurement of nontoxic and nonflammable gasesDownload Citation On Oct 14, 2020, Yanping Li and others published A Wear Condition Monitoring Model of Coal Mill Grinding Roller Based on LSTM Find, read and cite all the research you need on A Wear Condition Monitoring Model of Coal Mill Grinding2021年5月1日 The key abstract is to use IoT to incorporate a coal mine safety monitoring system The extraction of coal from the field is known as coal mining Coal is used as a fuel in the steel and cement industry to extract iron from ore and to manufacture cement Every parameter in the underground mining industry must be controlled on a regular basis Safety Monitoring System in Coal Mine Using IoT IOPscience2010年11月1日 Inside pulverizing coal mills and silos, carbon moNO X ide (CO) monitoring provides earlier detection of combustion to prevent mill firesThese detection systems are specifically designed to Measurement Solutions in Coalfired Power Plants
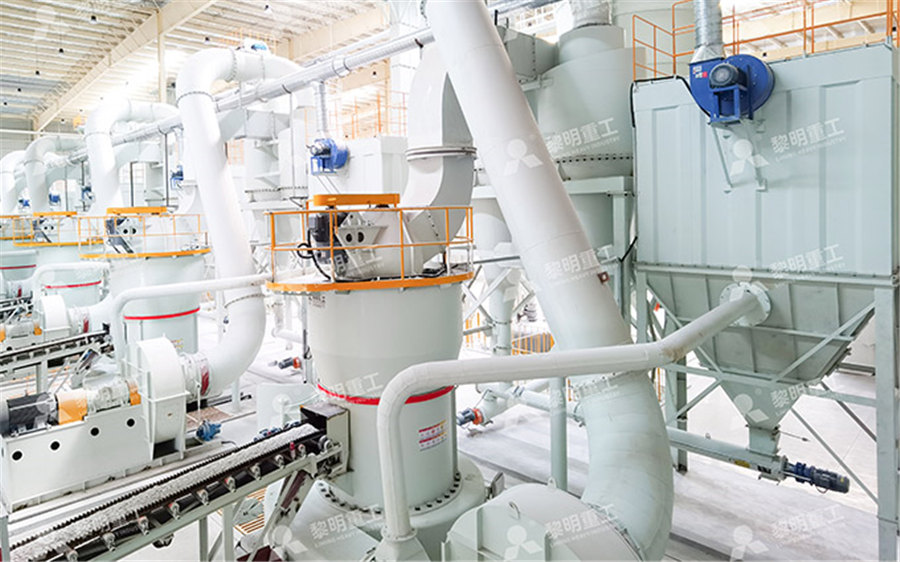
IOT Based Coal Mine Safety Monitoring and Alerting System
2021年6月17日 The Coal Mine Safety and Monitoring Project revolutionizes safety practices in coal mining through its innovative approach, leveraging modern technology for realtime monitoring and cloudbased 2013年6月4日 Collura et al [13] utilized model identification and signal processing techniques to develop a coal mill performance monitoring tool based on realtime detection of the fineness of pulverized Coal mill performances optimization through noninvasive online coal 2021年5月13日 A coal mine safety monitoring and alerting system using IoT can help improve safety in coal mines by providing realtime monitoring and alerting of hazardous conditions(PDF) IoT Based Coal Mine Safety and Health Monitoring2021年8月1日 The MHQI monitoring and prediction model assesses the working zone's air health status in an underground coal mine Finally, the toxic gas concentration monitoring and prediction module have a forecasting mechanism for predicting different gas concentrations, like CO 2, CH 4, CO, NO 2, SO 2, and H 2 S in the working face and goaf area inside a Hybrid CNNLSTM and IoTbased coal mine hazards monitoring
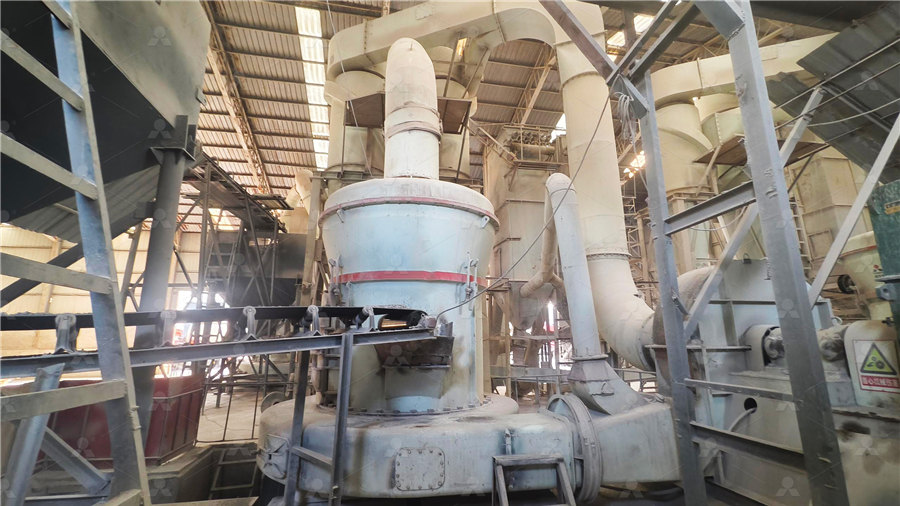
Coal Mill Monitoring CODEL International LTD
3 天之前 CODEL’s products for coal mill monitoring offer advanced technology and reliable performance to meet the stringent demands of coalfired power plants With continuous CO monitoring, CODEL’s systems provide realtime 2020年8月12日 This study shows the performance of a currently running vertical roller coal mill (VRM) in an existing coalfired power plant In a power plant, the coal mill is the critical equipment, whose An investigation of performance characteristics 2019年12月11日 CPT crossing point temperature CSIT critical selfignition temperature DNRM Department of Natural Resources and Mines, (Queensland) Australia 312 Models to predict coal behaviour 19 32 Monitoring as a preventative measure 21 321 Gas monitoring 22 322 Heat/light monitoring 27Assessing and managing spontaneous combustion of 2019年11月21日 coal and the high temperature inside the mill lead to rapid oxidation of the coal This results in further heat buildup and the potential for a ire If the mill is restarted without irst removing the hot coal, an explosion can occur when particles are suspended and exposed to the inrushing combustion air Even in routine mill shutdowns, there isSTRENGTHENING PLANT SAFETY IN COAL GRINDING
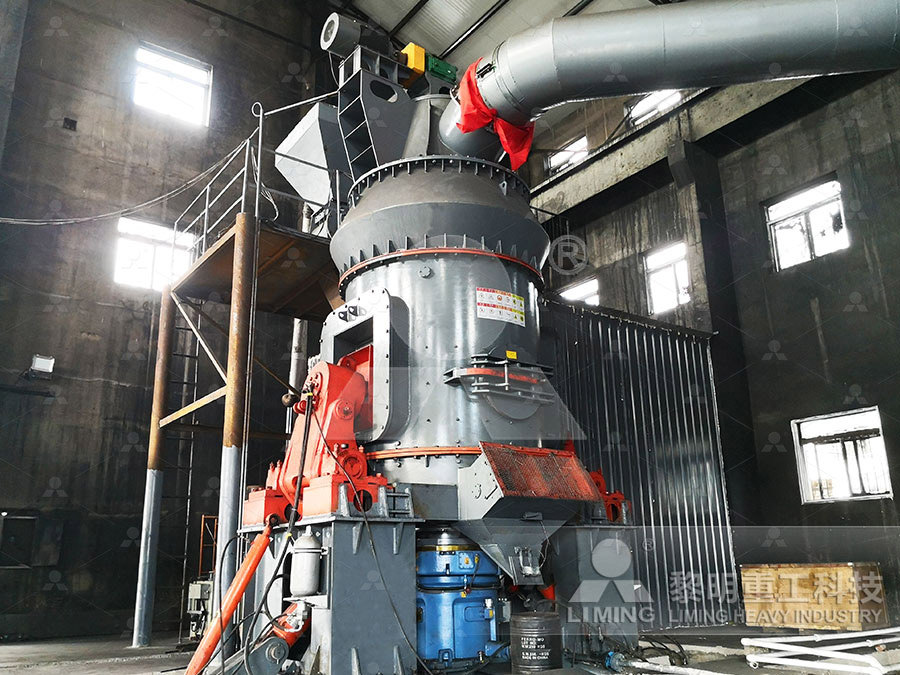
CO Mill Fire Monitoring Systems CODEL International LTD
6 天之前 CO Mill Fire Monitoring, getting the design right for a reliable CO measurement for the early detection of fires Single Point Flow Monitors TunnelTech 305 Air Flow Monitor; Single Multi Gas Electrochemical Cell Spontaneous combustion of coal in a coal handling system (coal conveyors, coal mills, coal silos, coal bunkers) has long 2024年10月31日 In discussion: Coal Mill Safety At best, coal mill safety is not well understood and, at worst, it is ignored When it comes to coal mill systems, most cement plant operators just presume that the supplier of the equipment knows all of the standards and rules and is 100% capable of making a system that conforms to these and is therefore safeIn discussion: Coal Mill Safety Coal Mill Safety, Explosion 2020年6月19日 Safe coal handling practices are designed to ensure that the fuel remains intact throughout its journey from the mine until the point at which it is ignited in the boiler It takes as little as 14 kg (3 lbs) of pulverised coal in 28 m 3 (1,000 ft3) of air to form an explosiveCOAL HANDLING SAFETY2015年8月1日 Mill problems originate mainly due to poor controls or faults occurring within the milling system As discussed by GQ Fan and NW Rees [3], the control of mills remains very simple in most of the power plants due to the fact that the mill system is highly nonlinear with strong coupling among the variables and it is very difficult to measure some important Review of control and fault diagnosis methods applied to coal mills
.jpg)
CPRI Online Coal Flow Balancing and Fineness
2020年3月19日 ONLINE COAL FLOW MEASURING AND BALANCING (CONTROL) AND ONLINE COAL FINENESS MEASURING SYSTEM FOR COMBUSTION OPTIMISATION IN A THERMAL BOILER Suresh G Chandwani1, Dr Francesco Turoni2, Reinhardt Kock2, Dr Michael Haug2, Dr Michael Schreiber2 1NSGuzder Company Pty Ltd, Neville House, Currimbhoy