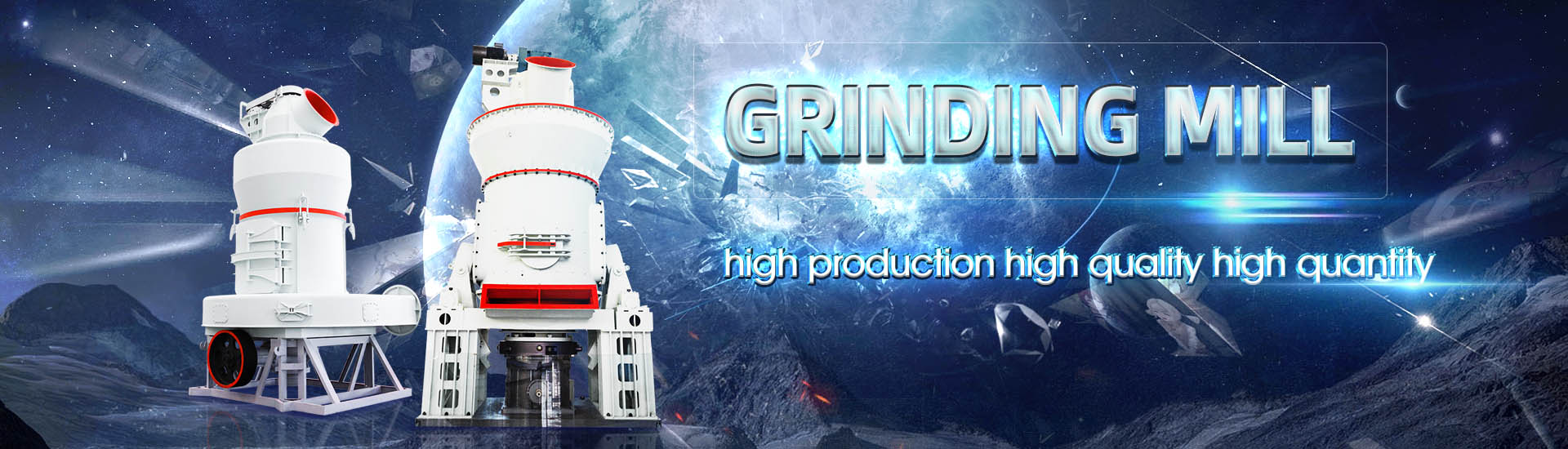
NdFeB waste grinding mill 2000mm
.jpg)
Study of an Impact MillBased Mechanical Method for
2023年6月12日 The scheme represents different steps of the proposed technique: supply of disused hard disks, recovery of NdFeB magnets, crushing with two different impact mills, and recycled powder characterization2023年6月11日 Crushing and milling leads to a fine powder When opening the vibratory mill fast after use, while the powder is still hot, a clear burnoff is observed Hence, to avoid full Development of a Process to Recycle NdFeB Permanent Magnets 2016年9月20日 Firdaus et al indicated a number of challenges for REE recovery from NdFeB magnet scrap: (1) the different mix of wastes produced—the complexity of magnet waste REE Recovery from EndofLife NdFeB Permanent Magnet Scrap2024年4月1日 NdFeB recycling includes direct reuse, wastetoREE, wastetoalloy, and magnettomagnet (MtM) approaches NdFeB magnets were first dismantled and finely An overview of NdFeB magnets recycling technologies
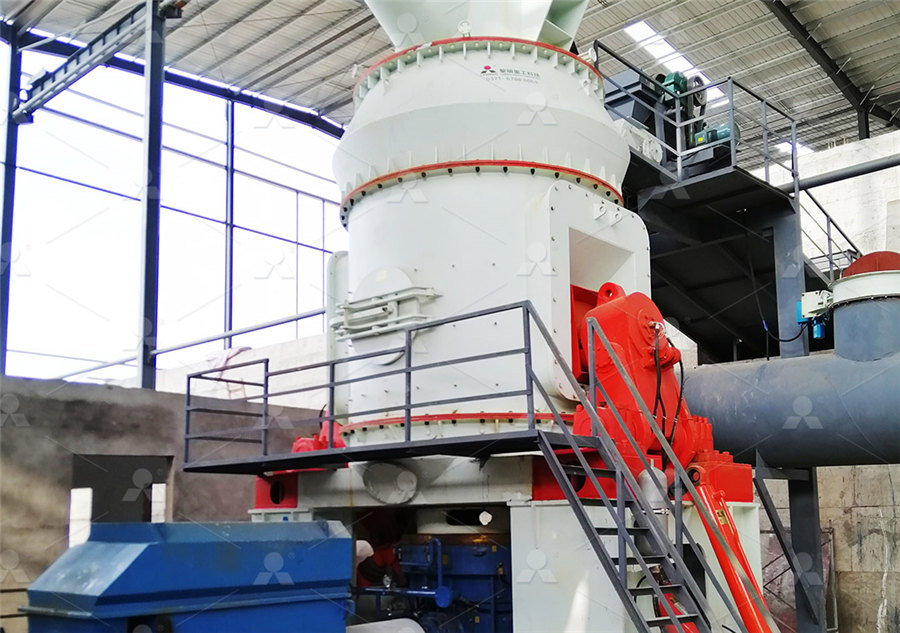
Recycling NdFeB Magnets and Rare Earth Fluorescent Materials
2023年11月13日 Liu 44 proposed a new carbonization/hydrogenation hydrolysis process, using waste sawdust biochar as extraction agent to recover rare earth elements from waste NdFeB At KIGAM, recycling processes from NdFeB waste magnet and scraps to REEs compound were researched and developed The pilot plant scale test demonstrated that high recovery yields of KIGAM Technology for the Recovery of NdFeB Waste Magnet and 2020年1月1日 In this study, an alternative approach to recover valuable metals (REEs and Co) from sintered NdFeB magnets by reaction with a ferric salt is described Sintered, Recovery of valuable metals from NdFeB magnets by 2023年10月1日 The sludge wastes are generated from machining processes such as wirecutting and grinding of NdFeB sintered magnets Different from bulk scraps, the sludge Shortprocess recycling of NdFeB sintered magnet sludge wastes
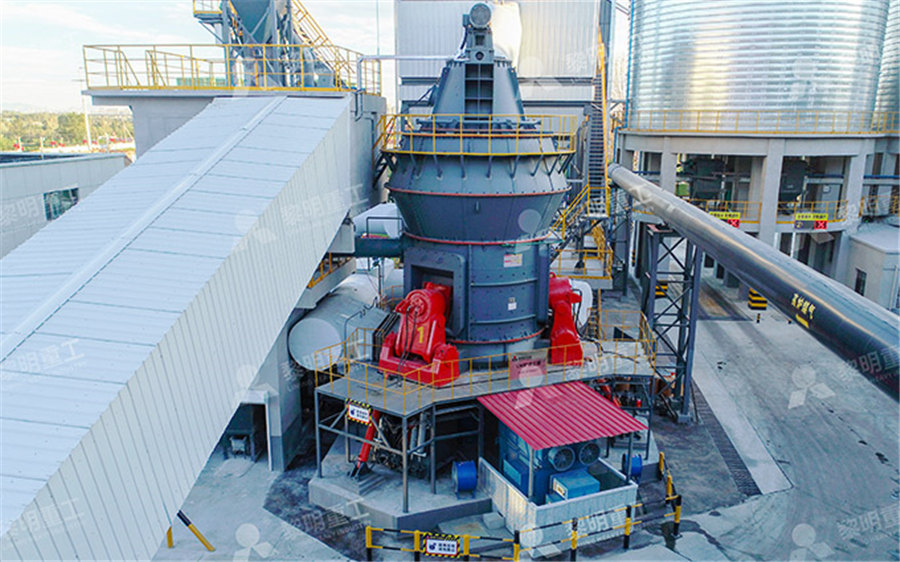
Development of a NearZeroWaste Valorization Concept for
2024年2月2日 In this study, the near zerowaste valorization concept for EoLNdFeB magnets is developed, and highpurity REEs are achieved with a twostep process, including leaching 2023年6月25日 In this method, waste NdFeB magnets were demagnetized by heating above Curie temperature, crushed and ground and additionally roasted in order to transform the Semicontinuous Process of Rare Earths Recovery from EndofLife 2018年8月19日 Rare earth elements (REEs) have been widely used in a number of hightech applications The demands for these elements are growing, especially as the demand for high magnetism neodymiumiron boron (NdFeB) magnets [1,2,3] continues to increaseHowever, with the increasing production of high performance rare earth magnets there is also an increase in Selective Extraction and Recovery of Rare Earth Metals (REMs) 2024年1月1日 Recent advances in electrochemical methods show promise for more sustainable recycling of rare earth elements (REEs) from endoflife NdFeB permanent magnets(PDF) Recent advances in electrochemical recovery of rare earth
.jpg)
KIGAM Technology for the Recovery of NdFeB Waste Magnet and
Figure 1 shows the recycling process for the NdFeB waste magnet consisting of peeling of plating layer, crush and grinding, thermal oxidation, sulfuric acid leaching, precipitation of rare earth double sulfate, conversion of double salt to REEs hydroxide, hydrochloric acid leaching of hydroxide, purification of REEs using solvent extraction, and synthesis of REEs compounds2019年6月30日 In ball mill grinding test, it was found that the grinding process was not performed properly at the early stage of grinding Moreover, waste rare earth magnet showed very low specific rate of breakage(S) and high fraction of fine particle breakage distribution(B) compared to ordinary minerals These results can be used as a basic data for Breakage and Surface Oxidation Characteristics of Waste NdFeB The kinetics and conditions of the acid leaching process of the grinding waste of a heatresistant nickel alloy are studied depending on the composition of the acid solution (H2SO4, HCl, HNO3, and SEMEDS analysis of NdFeB permanent magnets [54]; published 2023年5月27日 The importance of NdFeB magnets is increasing rapidly with the development of electronic technologies Accordingly, the reserves of rare earth elements are decreasing day by day, and their costs are increasing Therefore, effective recovery of waste magnets is critical Within the scope of this study, NdFeB alloys (30 wt% Nd, 69 wt% Fe, and 1 wt% B) without Evolution of the magnetic properties of meltspun NdFeB alloys
.jpg)
ModelBased Comparison of Recycling Processes for Grinding
2016年10月14日 Grinding slurries arise as process waste during the production process of NdFeBmagnets when the magnets are cut to the desired manufacturing dimension According to Rolf Blank (Director RD for permanent magnets at Vacuumschmelze GmbH und Co KG) grinding slurries as process waste can account for up to 30 % of the raw materials input into 2023年9月30日 NdFeB magnet scraps are primarily produced during cutting, grinding, and polishing, accounting for ~30% of raw materials in the product ion of magnets According to variousSeparation and Recovery of Rare Earths and Iron from NdFeB 2017年9月1日 Effect of acid concentration on the leaching yield (%) of (a) REEs and (b) iron from NdFeB magnet waste powder (Stirring rate 550 rpm, T = 25 °C, = C 3 M NH4ClAn environmentally friendly electrooxidative approach to 2023年6月12日 All of the grinding processes in this work were Michailidis, N Sustainable Recovery, Recycle of Critical Metals and Rare Earth Elements from Waste Electric and Electronic Equipment (Circuits, Solar, Wind) and 2023 "Study of an Impact MillBased Mechanical Method for NdFeB Magnet Recycling" Metals 13, no 6: 1103 Study of an Impact MillBased Mechanical Method for NdFeB

New insight into oxidative roasting and leaching for NdFeB waste
2022年12月1日 Reported recycling technology of NdFeB waste: preferential dissolution by HCl [8], oxidation [9], [10], [11], chlorination [12], [13], and electrochemical method [14]Among them, the hydrochloric acid preferential dissolution method is to form Fe 2 O 3 and REO after roasting and to leach RE elements by HCl The method is attributed to its high purity production, 2020年1月1日 The grinding, leaching and the oxalate precipitation steps were optimized as function of the REE recovery A complete recycling flowsheet can be found in Fig 11, based on previous subsections (33–37) Fig 12 shows an overview of the solid materials in and outgoing streams The overall NdFeB recycling process consists of 7 unit operationsRecovery of valuable metals from NdFeB magnets by 2015年9月1日 The pretreatment processes consisting of grinding followed by roasting were investigated to improve the selective leaching of Nd and Dy from neodymiumironboron (NdFeB) magnet scrapsThe Effect of Grinding and Roasting Conditions on the Selective Our Best selling Lab Jet Mill Classifier is use for s uperfine grinding, where material crash into each to smash to avoid contamination This jet mill is specially designed for universities and research institutions This machine can be placed on desk or laboratory bench with its small dimension This machine is effective for Mohs 110 hard materialNdFeB Lab Jet Mill China Manufacturers Suppliers Factory Exporter
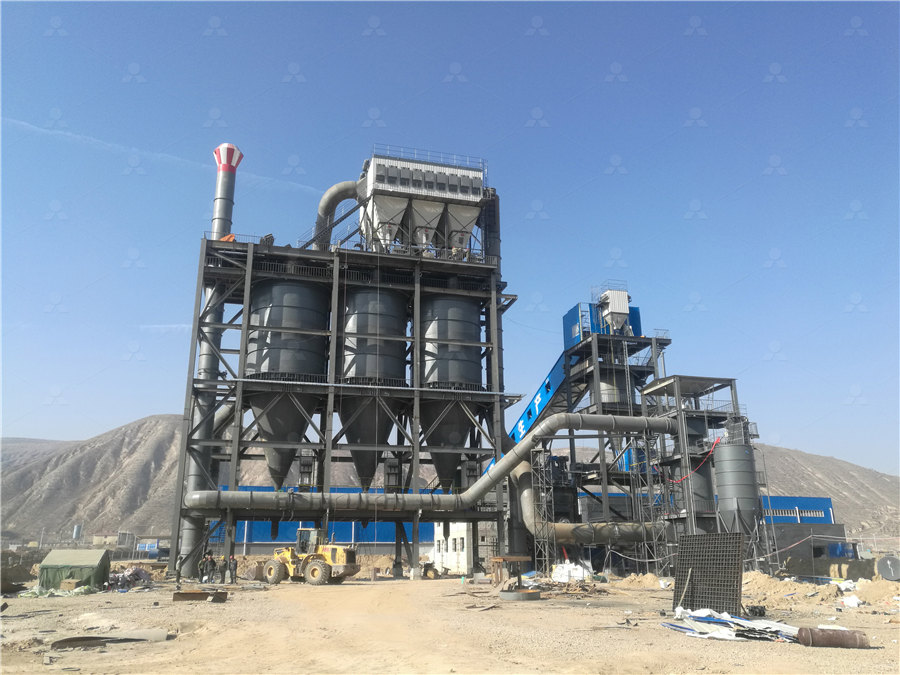
Recovery of rare earth elements from NdFeB magnet by mono
2022年4月1日 Rare earth elements (REEs) such as Nd 3+ and Dy 3+ were recovered from simulated and real leaching solution of the NdFeB magnet via solid phase extraction (SPE) Extraction of REEs from simulated solutions was investigated using silica functionalized with NH 2, EDTA and/or phosphonic groupsThe effects of several experimental factors (pH, efficiency Penurunan Oksalat Tepung Porang Mawarni, dkk Jurnal Pangan dan Agroindustri Vol 3 No 2 p571581, April 2015 PENGGILINGAN METODE BALL MILL DENGAN PEMURNIAN KIMIA TERHADAP PENURUNAN OKSALAT TEPUNG PORANG Grinding By Ball Mill With Chemical Purification on Reducing Oxalate in Porang Flour Rizki Tika Mawarni1*, Simon Bambang PENGGILINGAN METODE BALL MILL DENGAN PEMURNIAN KIMIA 2022年2月28日 An investigation on the dry mechanical activation of mine waste has shown that after 120 min of dry grinding by a planetary mill, a portion of the serpentine present in the waste converts to olivine According to this phenomenon, the authors concluded that, for carbonation purposes, dry mechanical activation is more suitable than wet grinding [ 32 ]Grinding SpringerLinketary mill (Retsch PM 100, RETSCH, Hahn, Dusseldorf, Germany) First of all, 8 g oxidized NdFeB magnet powders were placed in a 50mL stainless steel ball grinding tank, and then 12 stainless steel balls with diameter of 10 mm were added The ball mill was activated at 300, 500, and 650 rpm for 60 min In order to prevent superheated powEfficient recovery of rare earth elements from discarded NdFeB
.jpg)
Hydrometallurgical Recovery of Rare Earth Elements from NdFeB
NdFeB permanent magnet scrap is regarded as an important secondary resource which contains rare earth elements (REEs) such as Nd, Pr and Dy Recovering these valuable REEs from the NdFeB permanent magnet scrap not only increases economic potential, but it also helps to reduce problems relating to disposal and the environment Hydrometallurgical routes are considered 2018年4月6日 Experience the benefits of Zibo Chenze's Metal Hammer Mill Shredder Advanced automation and quality materials for metal recycling Home; About us; 2000mm: 1000hp: 18~25: 1200hp: 25~30: PSX60104: 2600mm: Metal Hammer Mill Shredder2024年9月11日 Liquid nitrogen embrittlement at 77 K is a process applied to make magnets more brittle for easier grinding The Nd 2 Fe 14 B magnet was then ground using a RETSCH PM 400 planetary mill equipped with and Y Yılmaz, Evolution of the Magnetic Properties of MeltSpun NdFeB Alloys with the Addition of Waste NdFeB Magnet, J Mater The Effect of MB40 Addition on the Electrochemical Corrosion2021年2月1日 The weight of NdFeB magnets, which have a life cycle of 1015 years in electric/hybrid cars and 2030 years in wind turbines, can reach 3040 g in electric/hybrid cars and 12 t in wind turbines Energy efficient process for recovery of rare earths from spent NdFeB
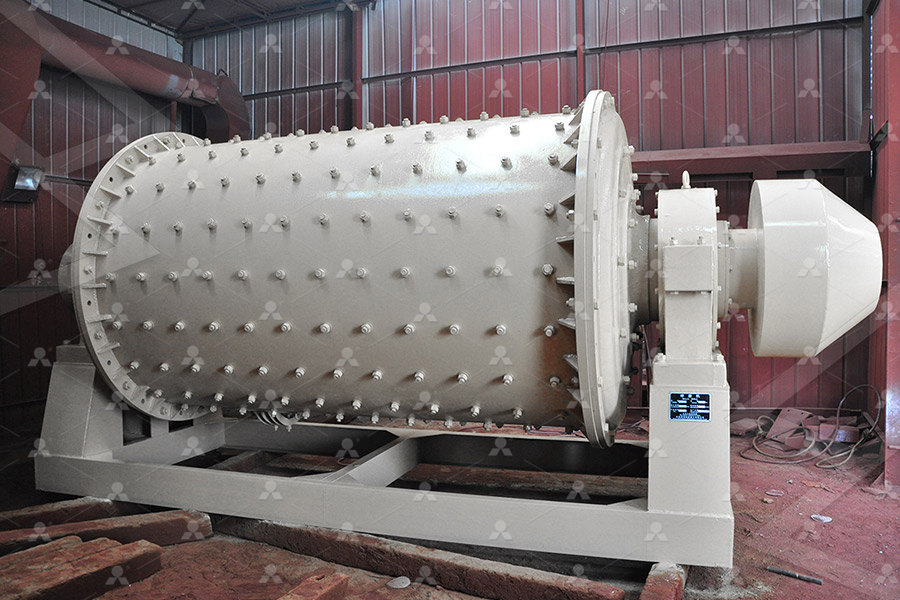
Preparation of highpurity iron oxide from endoflife NdFeB magnet waste
The acidsoluble residue from endoflife NdFeB magnet waste is often introduced into the ferrous metallurgical process to recover iron oxide as a HCl leaching, NaOH precipitation, grinding, calcination Fe 2 O 3 of particle size 02–035 μm Small size of synthesized the mill scale is successfully converted into pigments with 75 % 2018年9月15日 A large number of waste sintered NdFeB magnets are generated in the machining and electroplating process and the waste magnet in the machining process accounts for 35% [1]To deal with the waste magnet, the usual recycling method is to resmelt as raw materials or partially joining the quicksetting flakes into the jet mill [2], and crush it into single Efficient reuse of the waste sintered NdFeB magnet with Dy2O3 2018年8月9日 p>Sintered NdFeB as a thirdgeneration rare earth permanent magnet material, has been in rapid development since 1980’s due to its broad industrial applications and high electromagnetic performanceNew Technology of Making NdFeB by Sintering ResearchGate2018年1月29日 NdFeB magnet waste is one of the important secondary resources from which rareearth elements (REEs) can be recovered Herein we present an electrochemical route to selectively extract REEs from Selective electrochemical extraction of REEs from NdFeB magnet waste
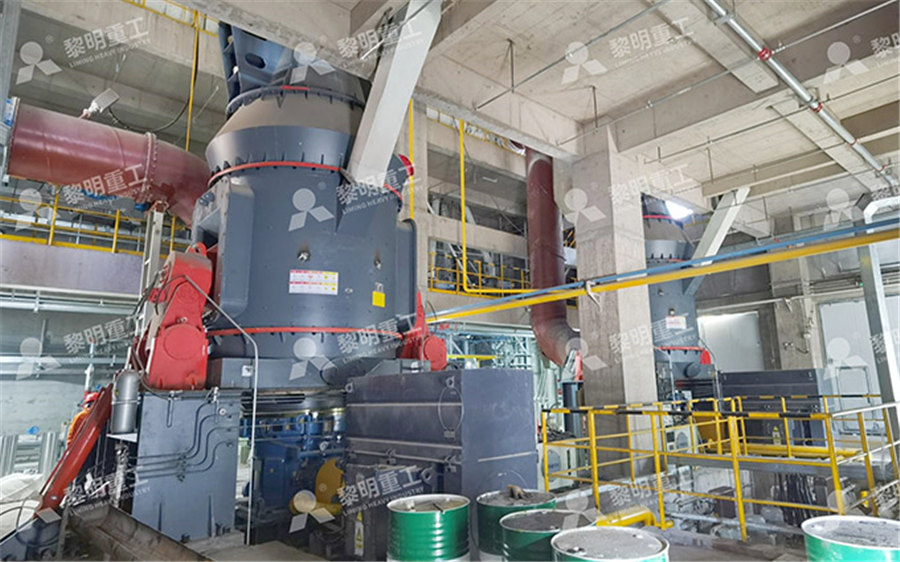
Planetary Ball Mill PM 400 RETSCH powerful and quick grinding
The grinding jars are arranged eccentrically on the sun wheel of the planetary ball mill The direction of movement of the sun wheel is opposite to that of the grinding jars in the ratio 1:2 (or 1:25 or 1:3) The grinding balls in the grinding jars are subjected to superimposed rotational movements, the socalled Coriolis forces2019年12月18日 Oxidative roasting of Nd–Fe‒B permanent magnets prior to leaching improves the selectivity in the recovery of rareearth elements over iron However, the dissolution rate of oxidatively roasted Nd–Fe‒B permanent magnets in acidic solutions is very slow, often longer than 24 h Upon roasting in air at temperatures above 500 °C, the neodymium metal is not Selective Roasting of Nd–Fe‒B Permanent Magnets as a 2024年4月16日 In our last article, we've briefly introduced the Ferrite Magnet, and in this article, we'll give a brief introduction to Neodymium Magnet (NdFeB)The NdFeB magnet is the strongest permanent magnet in the world It is a tetragonal crystal formed of neodymium, iron, and boronThis kind of magnet is the most commonly used rare earth magnet nowadays and is A Brief Introduction to Neodymium Magnets (NdFeB)2021年6月28日 Owusu et al took waste printed circuit boards as the research object, and evaluated the influence of different mill speed, screen size and feed size on its grinding characteristics based on 2 of Grinding characteristics of waste printed circuit boards in hammer mill
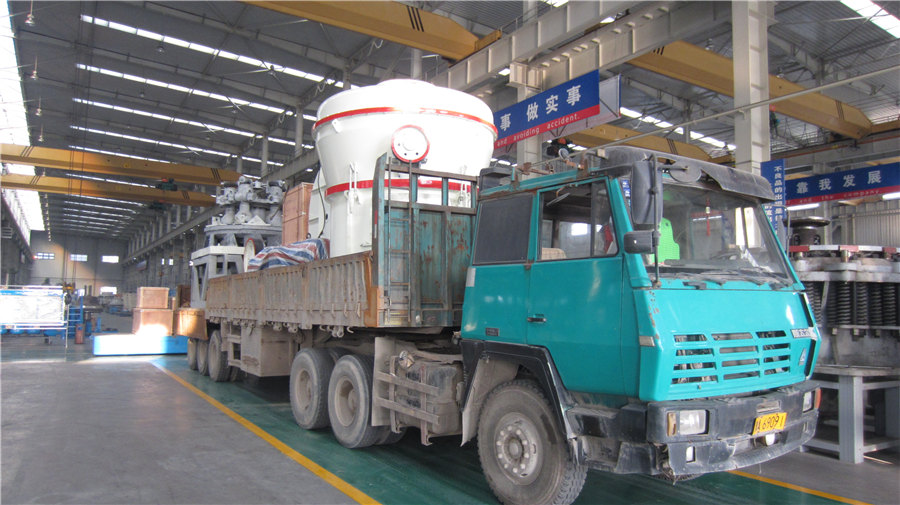
How To Make Neodymium Magnets GTEK Magnet
The sintered NdFeB magnet process is to pulverize the magnetic material into a powder by air flow grinding, and then put it into a smelting furnace to smelt it into a specified overall materialThe coercive force of NdFeB magnets produced 2015年7月17日 The pretreatment processes consisting of grinding followed by roasting were investigated to improve the selective leaching of Nd and Dy from neodymiumironboron (NdFeB) magnet scraps The peaks of Nd(OH)3 and The Effect of Grinding and Roasting Conditions on the 2021年11月29日 Due to the increasing demands and supply shortages for rare earth elements (REEs), the recovery of REEs from discarded NdFeB with high REE content has become extremely important In this paper, a hydrometallurgical coupling process involving mechanical activation and selective acid leaching was proposed for the recovery of REEs from discarded Efficient recovery of rare earth elements from discarded NdFeB 2018年1月31日 In this manuscript, we demonstrate a room temperature electrochemical process for efficiently recycling NdFeB magnet waste First, the magnet waste was completely leached with HCl and then, insitu electrochemical oxidation was performed to selectively oxidize Fe(II) in the leachate to Fe(III) Finally, oxalic acid was added directly to the electrooxidized leachate An environmentally friendly electrooxidative approach to
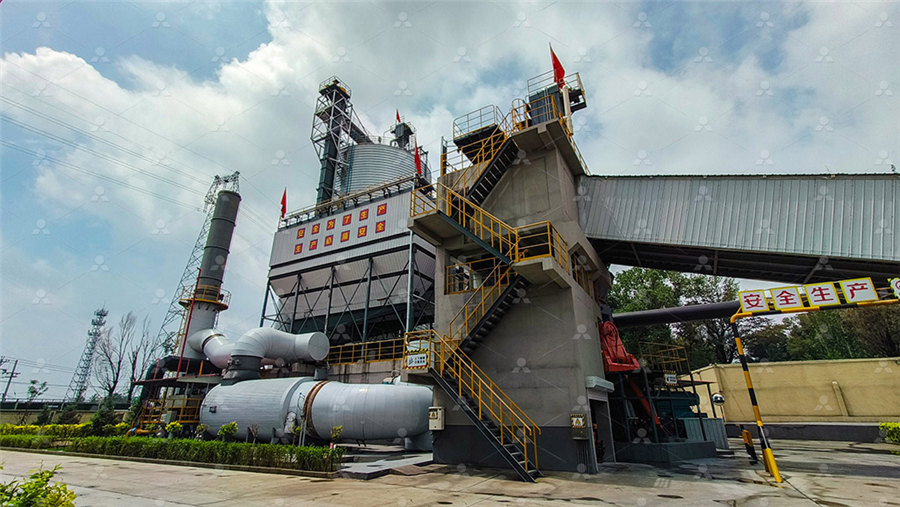
Electrochemical leaching of rareearth elements from spent NdFeB
2020年3月1日 Moreover, during electrolysis, it is possible to add waste from the top of the basket without interrupting the process It has also been discovered recently that materials like NdFeB waste (Venkatesan et al, 2018c), for of which the principal anode reaction is oxygen evolution may continue to function as anodes when placed in a titanium basket2018年10月3日 Vulcanized rubbers are passed though the nip gap of a shear mill or two roll mill at room temperature for reduction of the particle size 12 Ambient grinding does not mean processing at room temperature, the milling temperature may rise up to 130 °C when using this grinding technology 5 The particle size reduces with the increase in the number of passes CHAPTER 1: Grinding of Waste Rubber Royal Society of Chemistry2017年1月3日 NdFeB permanent magnets have different life cycles, depending on the applications: from as short as 2–3 years in consumer electronics to 20–30 years in wind turbines(PDF) REE Recovery from EndofLife NdFeB Permanent2015年7月7日 NdFeB magnets currently dominate the magnet market Supply risks of certain rare earth metals (REMs), eg, Nd and Dy, demand efficient recycling options that are applicable to different types and (PDF) Recycling of NdFeB Magnets Using Sulfation ResearchGate
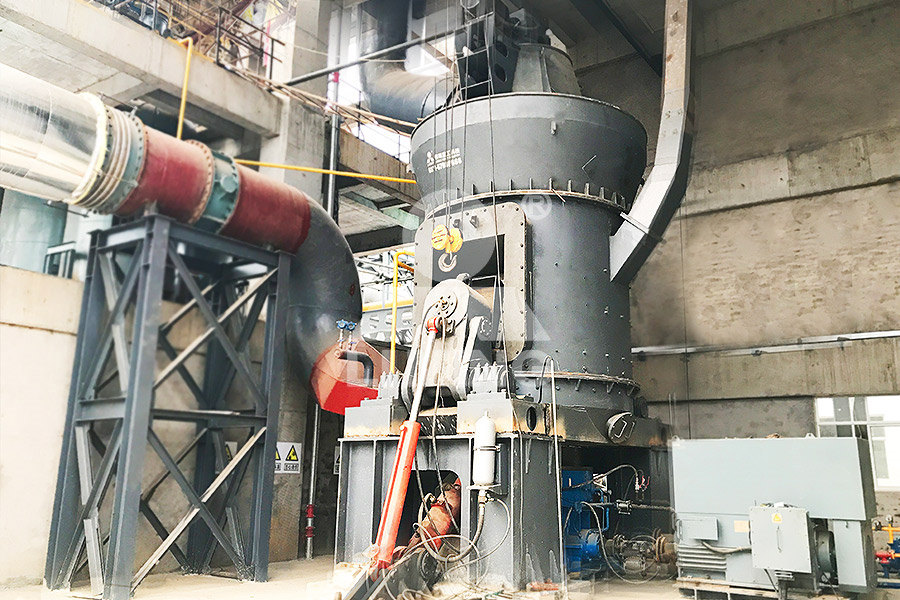
Equipment Sizing: Crusher or Grinding Mill 911Metallurgist
2016年7月8日 The Work Index values listed in Table I and II apply directly to a wet grinding overflow type rod mill 75 feet in diameter in open circuit; and to a wet grinding overflow type ball mill 75 feet in diameter in closed circuit with a rake classifier at 250% circulating load, and with 80% or more of the feed passing 4 mesh