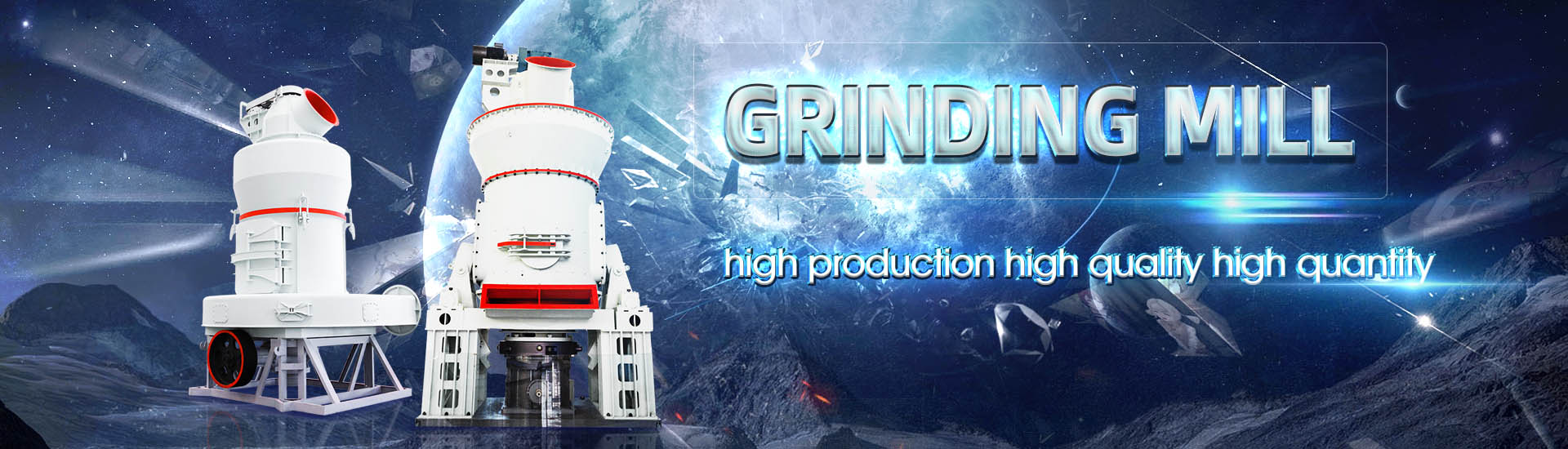
Process flow of complete set of ore equipment, vertical ore mill
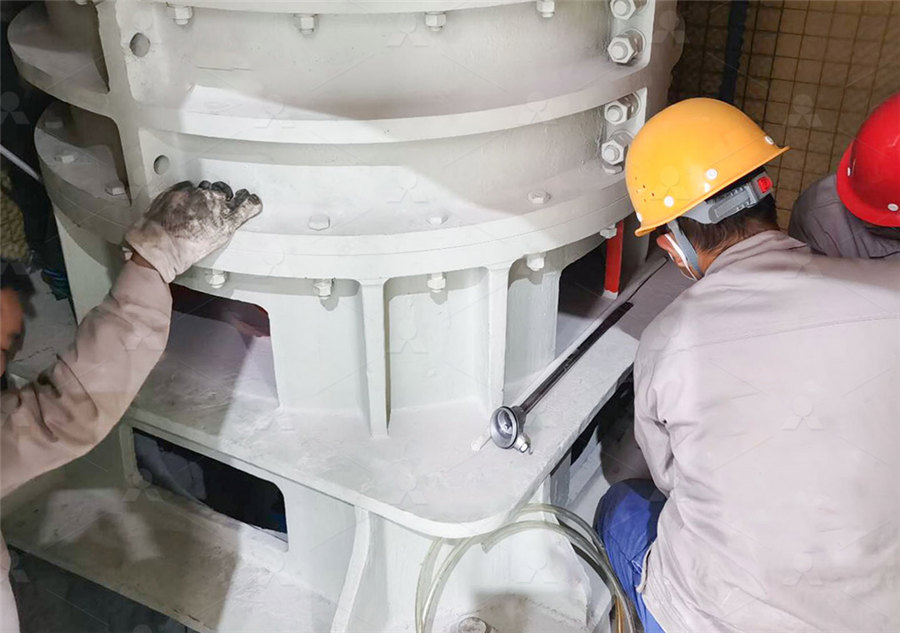
PROCESS OPTIMISATION FOR LOESCHE GRINDING PLANTS
• Ores The core elements of these plants are the Loesche vertical mills for drygrinding the abovementioned grinding stock Loesche has developed and built the largest and most efficient grinding plants for its customers Loesche plants are specifically planned for the required process steps Vertical roller mill (VRM) is an established technology in cement and slag grinding applications and Boliden and Gebr Pfeiffer have been collaborating on the application of this technology in Vertical Roller Mills used for the comminution of mineral oresProcess Processing of the ore ranges from simple crushing and screening to a standard size, through to processes that beneficiate or upgrade the quality of the iron ore products This is Iron Ore production in the Pilbara2012年9月24日 The article provides the analysis of process flows used for sulfide and oxidized copper ore treatment, reagent schemes, process equipment, indicators of flotation Copper concentrate regrind at Sossego plant using Vertical Mill
.jpg)
(PDF) LEARNING FROM OTHER INDUSTRIES; WHY THE VRM
2019年4月16日 The vertical roller mill (VRM) is a comminution device in which crushing, grinding and classification processes are combine together into a single unit operationfocuses on modeling an iron ore magnetic separation processing plant in Arena discrete event simulation software (Rockwell Automation) A typical iron ore processing plant, with several Discrete Event Simulation of an Iron Ore Milling Process2015年3月15日 Verticalrollermills (VRM) are an energyefficient alternative to conventional grinding technology One reason is the dry inbed grinding principle Results of extensive test Research of iron ore grinding in a verticalrollermill2012年9月1日 Mills (VRM) installations and summarises the main benefits of the dry compressive Loesche grinding technologies in Airflow and OverflowMode Some of these Latest Installations And Developments Of Loesche Vertical Roller
.jpg)
Operational parameters affecting the vertical roller mill
2017年4月1日 Pilot plant test results with various ores showed that low energy consumption feature of vertical roller mills is applicable to the ore industry Grinding test results for zinc ore 2015年3月15日 The results show that the optimum process parameters for the vertical roller mill are as follows: a grinding fineness of 816wt% of particles less than 0074 mm, a dodecyl Research of iron ore grinding in a verticalrollermillMill Configuration REVERSING ROUGHING MILL WIDTH REDUCTION: Slab width is reduced up to two inches with the vertical edging rolls (squeeze) THICKNESS REDUCTION: Roughing mill reduces slab thickness in five (5) to seven (7) reversing passes down to 1125” (transfer bar) DESCALING: High pressure descale water on entry side of mill removesPrinciples of Hot Rolling AIST2024年9月11日 The Ore pass system, which plays a very important role in orerock transportation in underground mining, is a key project for realizing efficient and lowcost downward transport of orerock in Influence of oredrawing port position on orerock flow
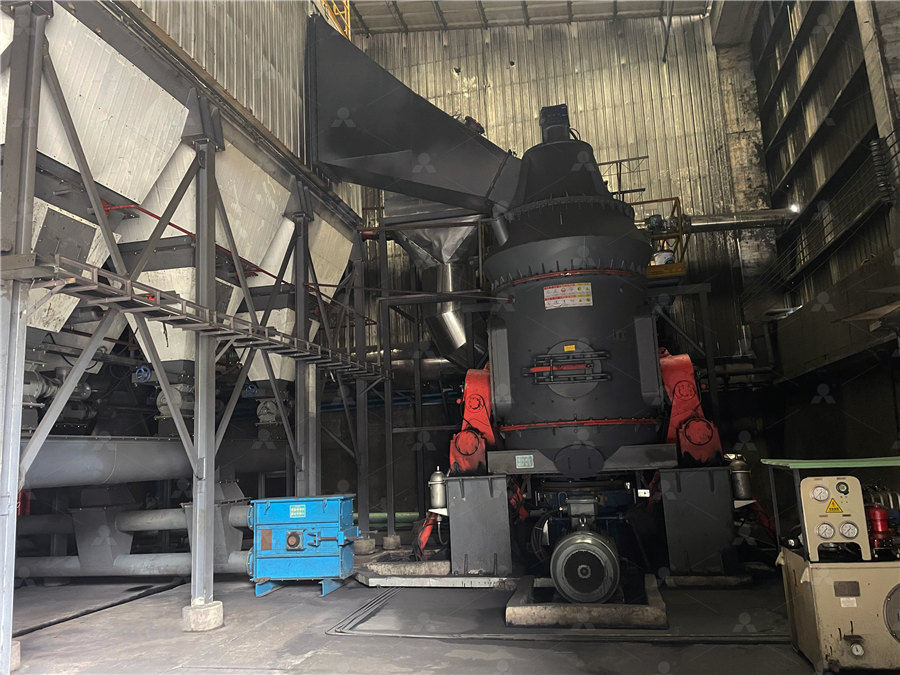
Iron Ore Processing: From Extraction to Manufacturing
2024年4月26日 The crushed ore obtained from the crushing stage is typically in larger size fractions and needs to be further processed through screening 2 Screening Screening is the process of separating the crushed ore into various 2015年3月1日 In addition to the process equipment symbols, there will be heat exchanger equipment that are essential to process flow diagrams Notable symbols that are relevant to this class include the basic heat exchanger symbols, the shell and tube exchangers, the kettle reboiler, the Utube exchanger, and heating coilsProcess flow diagram processdesign Northwestern University2023年6月1日 This study aims to improve the output and production efficiency of a large vertical mill by optimizing its operational parameters This paper takes a large vertical mill in LGM as the object, a numerical calculation method of particle–fluid coupling system in large vertical mill based on CFDDPM theory, and a multiobjective optimization method of operating parameters of Operation parameters multiobjective optimization method of 2024年3月20日 The article provides an overview of the steel making process, detailing how raw materials like iron ore, coke, and limestone are transformed into versatile and durable steel through a complex series of steps depicted in a flow diagram It discusses the key ingredients involved in steel production, their roles, advantages and disadvantages of the workflow Understanding the Steel Making Process: A Flow Diagram
.jpg)
Iron ore grinding mill Grinding plants for Iron Ore
2, HLM vertical mill: largescale equipment, Qualified powder will flow with the air and be collected by dust collector, Some iron ore processing plant Equipment: 1 set of HLM21 Materials: iron ore Finished fineness: 200 mesh D90 Capacity: 1520t/h Customer feedback:2020年4月1日 On the other hand, since most plants are optimized for a specific size fraction (≥ 75 µm) and the tailings of chromite plants are generally characterized by fine particles, a recurring problem Process optimization of a chrome ore gravity concentration plant leads ores from the vertical part of the ore passes to crushing rooms or conveying rooms, as shown in Figures 2(c) and (d) The geometry around the chute is shown in Figures 2(e)Analysis of Ore Pass HangUps in Long Vertical Ore Passes by 3 The complete set of ore crushing equipment is the processing equipment for ore from lump to powder What equipment does the ore grinding mill production line include? What is the process flow of ore crushing? Ore mainly refers to the rock minerals naturally existing in Full Set Of Ore Crushing Equipment What Does The Ore Grinding Mill
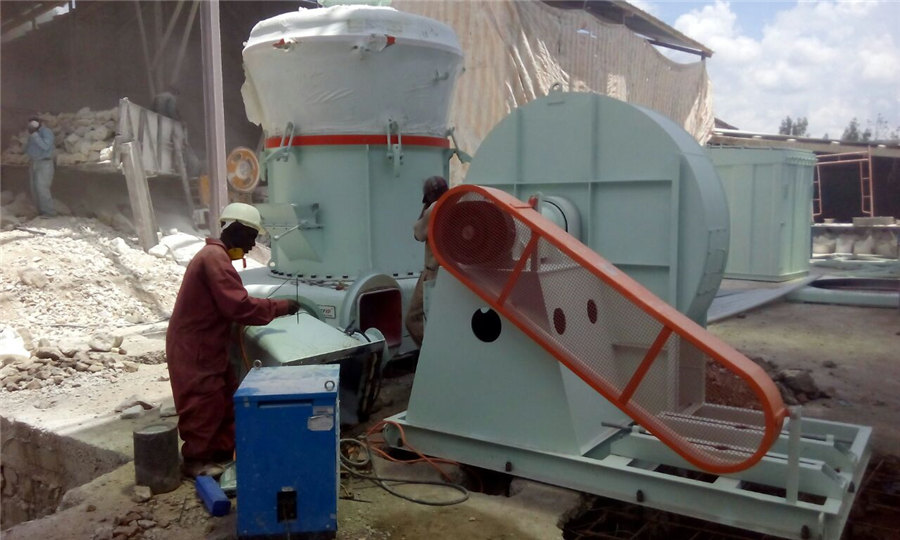
Copper Ore Processing Plants, Flow And Equipment
4 天之前 Copper industrial minerals include: natural copper, chalcopyrite, chalcocite, tetrahedrite, azurite, malachite, etc Chalcopyrite (a compound of copper, sulfur, and iron) is mined mainly, followed by chalcocite and bornite If 2020年8月1日 To understand the mechanism of hangup phenomena, ore flow simulations in long and vertical ore passes were carried out using the threedimensional discreteelement method, and the influences of Analysis of Ore Pass HangUps in Long Vertical Ore 2015年8月26日 Returning to the overall process; that is the process for the sulfide ores and the oxide ore as I said are treated differently Direct from the pit the oxide ore is piled onto large lined leach pads and the sulfuric acid The top photo shows one of these leach pads with the new thick black plastic liner visible on the right of the padCopper Mining Extraction Process Flow ChartManufacturing process flow 1 Quarrying and Crushing The quarry (where the mining activity is performed) is located 07 km away from the plant and has the main raw materials such as Limestone and shale that is estimated to last for 100 years, the other raw materials (Iron ore, silica sand, gypsum and Pozzolana (pumice) ) are brought from nearbyManufacturing process flow 1 Quarrying and Crushing Messebo
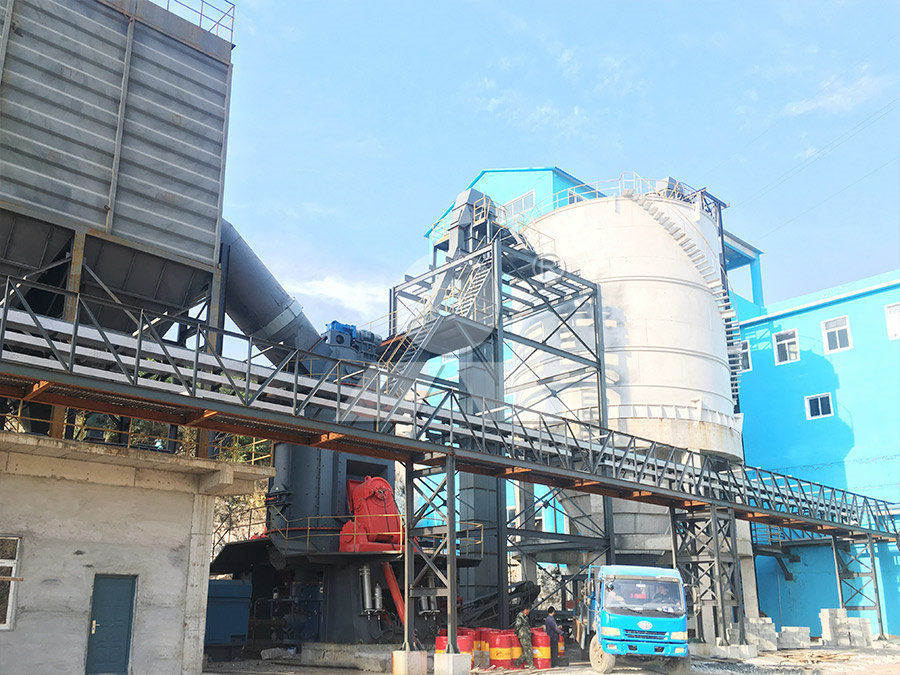
Vertical roller mill for raw Application p rocess materials
pressure loss at the cyclone and in order to control mill gas flow, mill circulation fan and EP fan are provided after the cyclone and EP respectively Power consumption of these two fans reaches about 10kwh/trawmaterial In the direct dust collection system shown in Fig2, process flow is simple The raw2017年9月11日 In this study, an extensive sampling study was carried out at vertical roller mill of ESCH Cement Plant in Luxemburg Samples were collected from mill inside and around the circuit to evaluate the Performance Evaluation of Vertical Roller Mill in Cement Nothing can be done about the ore body, it is what it is, but it is now possible to get the best out of it due to Equipment Improvement, New Technology, and Process Control Systems introduced over the past 30 years In addition there are tools such TIN ORES SOME ASPECTS OF PROCESS METALLURGY AusIMMNHI has system integration, complete equipment and EPC abilities in the involved product domains, including fullsection TBM, new type dry cement complete equipment, metallurgy mining complete equipment, bulk material handling and conveying complete equipment, environmental protection complete equipment, special rolling complete equipment, fully Complete Set of Equipment北方重工 NHI
.jpg)
Copper Ore Processing And Equipment JXSC Mineral
2023年5月26日 The raw ore is crushed and ground by a crusher and a ball mill The final grinding fineness is about 200 meshes, and then the flotation machine performs a rough selection, and a fine One or two sweeping operations are carried out on the tailings A complete set of copper separation equipment can extract highpurity copper ore by using this process2015年3月15日 The results show that the optimum process parameters for the vertical roller mill are as follows: a grinding fineness of 816wt% of particles less than 0074 mm, a dodecyl amine (DDA) dosage in Research of iron ore grinding in a verticalrollermill2015年3月15日 In case of the Kiruna ore there was the possibility to take samples of the concentration plant KA1 in Kiruna, while the same feed material was ground, as used for the tests with the verticalrollermill The grinding process of KA1 consists of a SAG mill followed by a pebble mill for final grindingResearch of iron ore grinding in a verticalrollermill2022年10月20日 Iron ore handling, which may account for 20–50% of the total delivered cost of raw materials, covers the processes of transportation, storage, feeding, and washing of the ore en route to or during its various stages of treatment in the mill Since the physical state of iron ores in situ may range from friable, or even sandy materials, to monolithic deposits with hardness of Iron Ore Processing, General SpringerLink
.jpg)
A review of intelligent ore sorting technology and equipment
2022年7月25日 Under the background of increasingly scarce ore worldwide and increasingly fierce market competition, developing the mining industry could be strongly restricted Intelligent ore sorting equipment not only improves ore use and enhances the economic benefits of enterprises but also increases the ore grade and lessens the grinding cost and tailings 2016年5月26日 The body of the separator can be conical or pyramidal in shape, to suit best the physical requirements of the location The classifier can be used to advantage in dewatering and controlling feed to a regrind ball or rod mill, or material from tables, jigs, or Types of Classifiers in Mineral Processing 911Metallurgist2012年6月1日 The process input variables in the figure are: u 1 − mill feed water flow rate, u 2 − fresh ore feed rate, u 3 − mill critical speed fraction, u 4 − sump dilution water flow rate and u 5 Grinding in Ball Mills: Modeling and Process Control2016年9月1日 Cement production is one of the most energyintensive manufacturing industries, and the milling circuit of cement plants consumes around 4% of a year's global electrical energy productionOperational parameters affecting the vertical roller mill
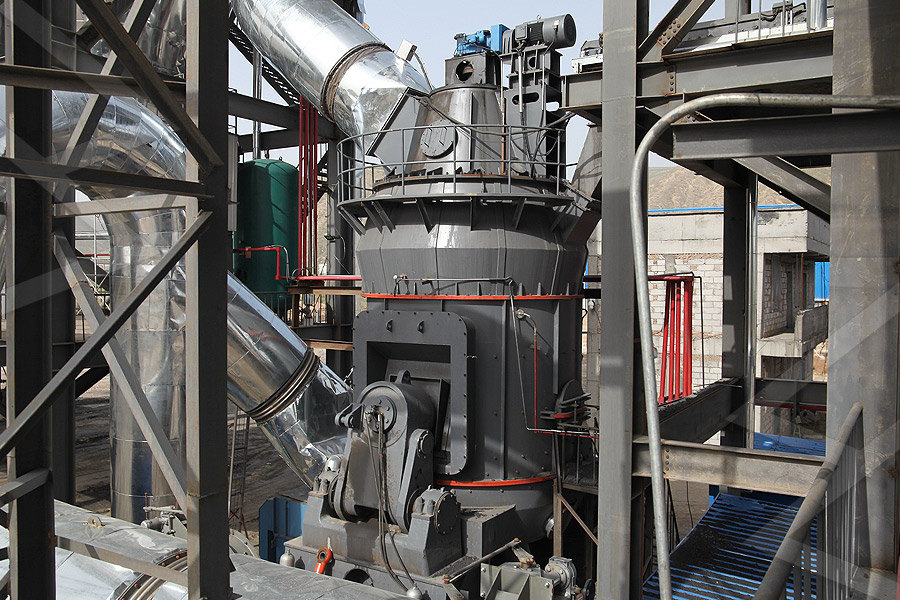
How to Process Copper Ore: Beneficiation Methods and Equipment
2023年3月13日 The bulk ores are crushed to about 12cm by a jaw crusher or a cone crusher Then the crushed materials are sent to the grinding equipment, and the final particle size of the copper ore is reduced to 01502mm Copper ore crushing process 1 Beneficiation methods of copper sulfide ore2016年2月29日 Some of the metallurgical relationships that must be considered from the testwork program as follows: ore grade relationship to gold recovery, crushing and grinding parameters and their relationship to the ore variability in the ore body, effect of other minerals on the process, minerals and/compounds that negatively impact processing cost such as oxidized Gold Extraction Recovery Processes 911Metallurgist2017年5月1日 General India has the fourth largest iron ore reserves in the world after Russia, Brazil, and Australia[] As per the survey conducted by the Indian Bureau of Mines (IBM) in April 2000, India had 9919 million tonnes of recoverable reserves of haematite and 3546 million tonnes of magnetite[]As good quality iron ore deposits are depleting very fast, beneficiation Hazard Identification, Risk Assessment, and Control Measures as 2022年1月23日 This work concentrates on the energy consumption and grinding energy efficiency of a laboratory vertical roller mill (VRM) under various operating parameters For design of experiments (DOE), the response surface method (RSM) was employed with the VRM experiments to systematically investigate the influence of operating parameters on the energy Analysis and Optimization of Grinding Performance of Vertical

How to Set up a Paper Mill Plant Complete Process
2024年4月12日 3D Plant Layout of a Stock Preparation System By integrating the design models of the machinery within the plant model through an interface, a comprehensive 3D representation of the paper mill plant can be achieved Media Attributions; Metal deposits are mined in a variety of different ways depending on their depth, shape, size and grade Relatively large deposits that are quite close to surface and somewhat regular in shape are mined using 82: Mining and Ore Processing Geosciences LibreTexts2008年1月1日 Australia has large reserves of limonite and claybased laterites that are currently underutilized This review summarizes the latest nickel laterite upgrading studies reported in the literature Process flowsheet development for beneficiation of 2021年8月1日 As for the working principle of this equipment, it is to first use multistage highpressure water pump to pressurize sea water, and continuously repeat the two working states of “ore separation process” and “ore conveying process” under the control of five electric valves through the alternate use of two storage tanks (Xu and Xu, 2008 Research on the transportation and flow characteristics of deepsea ore
.jpg)
Underground Ore Loading Chutes; Ore Chute Design
2017年4月2日 Cost of Installation of loading chutes Table 31 gives typical costs of building and installing loading chutes The costs shown cover single chutes and are to be considered for the most part as approximate and not directly comparable, since they were obtained from various sources without reference to any standard form for segregation of cost itemsPart Three: Raw Mill Process of Raw Mill The proportioned raw material is feed first to a grinding mill In the mill, particles ground in to very fine sizes In the grinding unit, drying, grinding and mixing takes place simultaneously Hot gas from clinker burning unit is passed into the grinding unit to assist the drying and grinding processCement Manufacturing Process INFINITY FOR CEMENT EQUIPMENTsteel balls The cyclone underflow is sent to the secondary ball mill for further size reduction At this point in the process 90% of the ball mill circuit product is sized to a P80 of 0074 mm Primary Grinding Mill The ground ore is then processed by a multistage gravity circuit The gravity circuitFlowsheet Development of A Refractory Gold Ore To Minimise • Mill motor speed • Mill air flow/mill differential pressure • Temperature after the mill • Pressure before the mill • Grinding stock feed • Classifier speed • Mill fan speed • Water spraying • Hot gas • Fresh air Manipulated variables Disturbance variable Process measured value RelauchLMmaster 6 250814 11:47PROCESS OPTIMISATION FOR LOESCHE GRINDING PLANTS

An investigation of performance characteristics and energetic
2020年8月12日 This study shows the performance of a currently running vertical roller coal mill (VRM) in an existing coalfired power plant In a power plant, the coal mill is the critical equipment, whose 2013年1月1日 For banded iron formationhosted deposits accurate boundary modelling is critical to oregrade estimation Key to estimation fidelity is the accurate separation of the different domains within the (PDF) Planning an Iron Ore Mine: From Exploration Data to