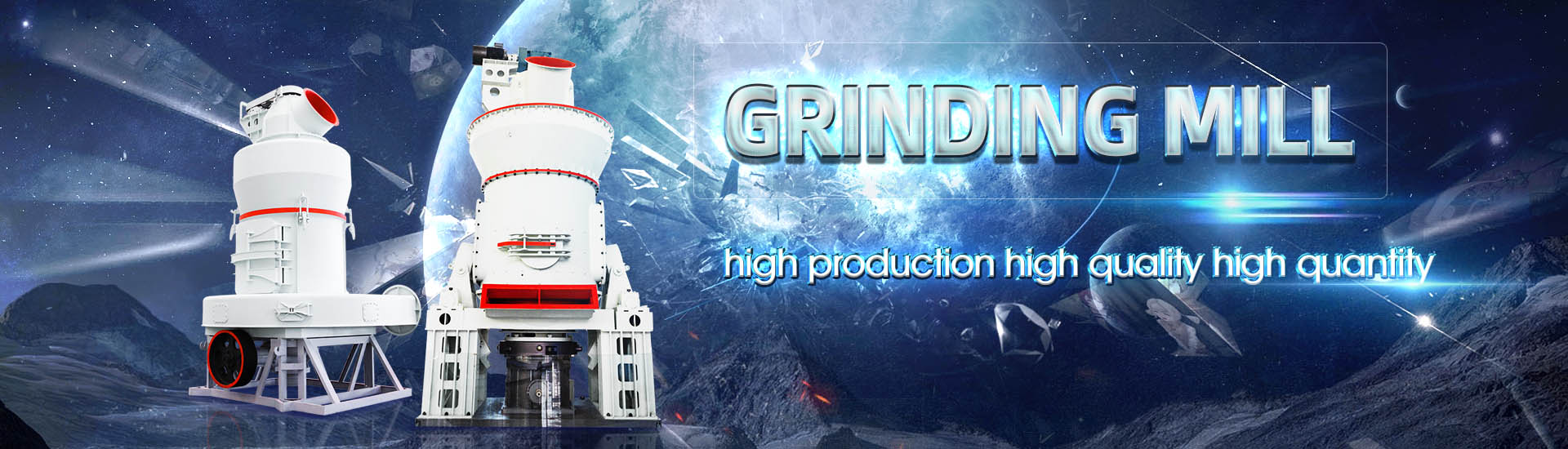
Roller mill discharge end lining structure
.jpg)
Semiautogenous grinding (SAG) mill liner design and development
Mill liners provide the replaceable wearresistant surface within grinding mills; they also impart the grinding action to the mill charge, and at the discharge end, remove the ground contents of highlighted the significance of correct mill liner selection Liners protect the mill shell from wear and transfer energy to the grinding charge, and a careful balance is required to optimise these The Selection and Design of Mill Liners 911 MetallurgistThe working performance of the current SAG mill when the radial structure and arc structure were adopted in the lifting bars of the grate liners and slurry lifters, respectively, was compared to Study on the influence of the discharge end cover structure of Bullnose® discharge cone system reduces the relining times by 50% to maximise mill availability Discharge grate slot analysis is carried out across all grate designs to optimize open area, recycle size and product passing performanceDischarge End Liner System Bradken
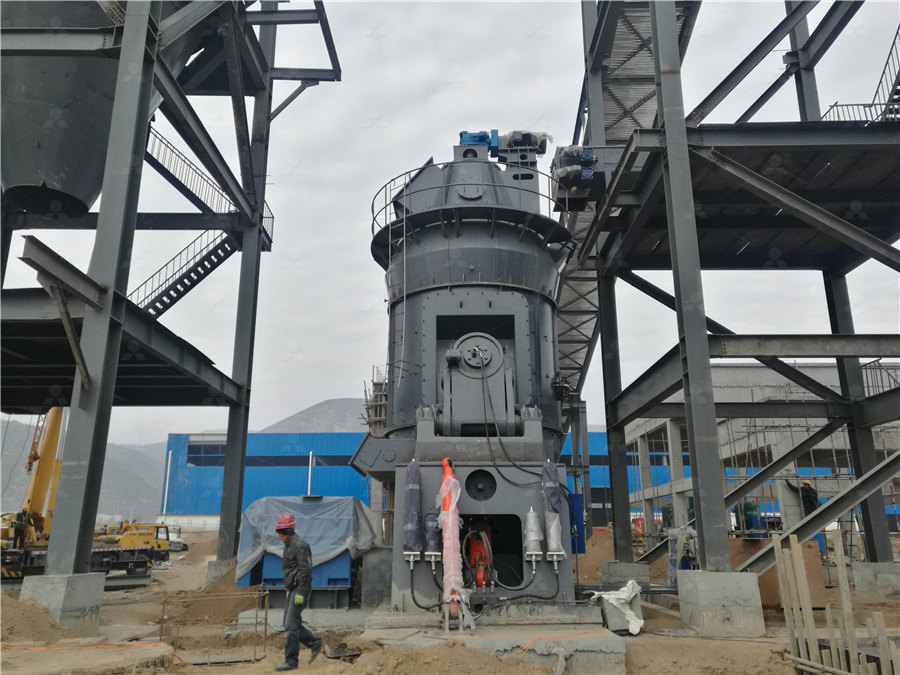
STEP CHANGE IN LINER DESIGN FOR THE KANSANSHI 32FT SAG
The liner configuration of the Feed End of the mill was enhanced with a single one piece composite liner to include a high chrome insert to combat the high wear zone The single one 2006年1月1日 Protection of the mill shell and the end walls from the aggressive impacting and abrasive environment inside a mill is well known as the primary purpose of mill liners (Powell et al,(PDF) Selection and design of mill liners ResearchGateHengin designs the structure of the feeding and discharge mill head liner and SAG mill shell liner of SAG mill liners according to the structure size, critical speed, processing capacity, mineral properties and other parameters of the millSAG Mill Liners Design Hengin Heavy2007年8月1日 A discrete element method (DEM) simulation scheme is conducted to look at how ball size distribution, mill filling, endliner configuration and shape affect the distribution of Semiautogenous grinding (SAG) mill liner design and development
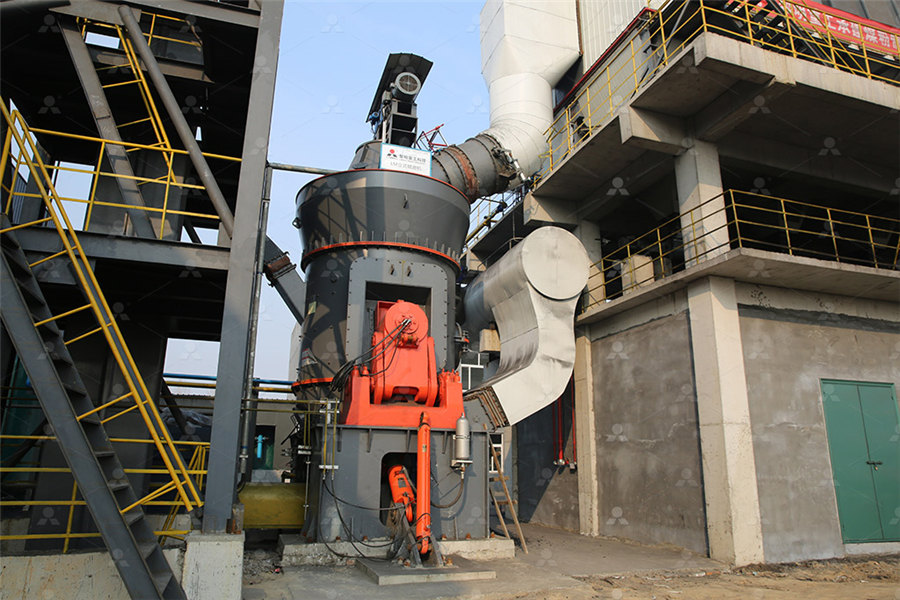
Ball Mills 911Metallurgist
2017年2月13日 Center peripheral discharge Rod Mill for minimal slimes in final product CERAMIC LINED BALL MILL Ball Mills can be supplied with either ceramic or rubber linings for wet or dry grinding, for continuous or batch type Choice of mill lining A mill lining should be optimized to suit each specific mill Choosing an appropriate type of lining and design in terms of lining material, thickness and profile is vital for optimizing mill throughput and total grinding costs Choosing the correct liner material and design ensures that the mill itself is well protectedThree factors that determine the wear life and performance of mill The KMS series mill discharge pump is ideal for semiautogenous and autogenous mill discharge, thickener underflow, tailings, and hydrocyclone feeding +86 186 3393 5649 info@kingdagroupKMS Mill Discharge Pump kingdapumpAbstract Three roller sugar mill is the most vital part of sugar industry sugar roller mill is used for to separate the sucrosecontaining juice from the cane ie extraction of juice consist of three rollers namely Top, Feed and Discharge The extraction of juice in a mill is achieved by squeezing prepared cane between two rollsStatic structural analysis of conventional sugar mill roller shaft for
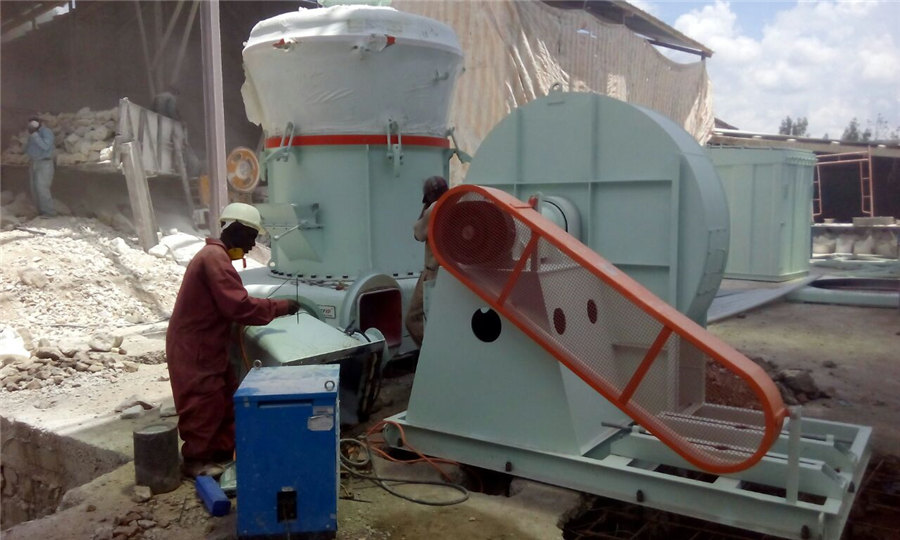
Static Structural Analysis of Crushing Rollers of Three Roller Sugar Mill
2015年1月6日 Results of static analysis for discharge roller:Fig No 10 Maximum Shear Stress in discharge roller Maximum value of shear stress is 75624 MPa which is at bearing position of discharge roller Maximum value of shear stress is within limit so shaft is safe Minimum value of shear stress is 25069e4 MPa at bearing, shell and pinion end2006年1月1日 Protection of the mill shell and the end walls from the aggressive impacting and abrasive environment inside a mill is well known as the primary purpose of mill liners (Powell et al, 2006)(PDF) Selection and design of mill liners ResearchGate2022年6月24日 The grinding roller of CLUM vertical roller mill is made of special alloy steel, which is more wearresistant and has a longer service life The ball mill is more suitable for coarse grinding and fine grinding, and adopts the method of impact crushing, so the consumption of grinding media is very large, which makes the life of the mill lining How to choose between ball mill and vertical roller mill?2007年8月1日 Keywords semiautogenous grinding mill, lining, modeling of lining wear processes, factors of influence on the process of wear of lining 1 Introduction The process of destruction (grinding and Semiautogenous grinding (SAG) mill liner design and development
.jpg)
Static Structural Analysis of Crushing Rollers of Three Roller Sugar Mill
2015年6月1日 Wear is often observed on top roll shaft journal surface Sugar mill roller shafts are made up of carbon steel EN8 The friction and wear behavior of carbon steel EN8 was investigated under dry Mill Lining Discover Element's solutions in mill wear protection crafted for various grinding equipment: from AG to MCM Element develops mill lining from a wide array of materials and creates comprehensive design and production documentation Our collaboration with advanced manufacturing facilities enables us to craft mill linings of any type,Mill Lining Element Mining and Construction Oy2022年5月31日 Mineral crushing is the main source of energy consumption in mineral processing According to statistics, this consumption accounts for about 35–50% of the total cost of the mine (Curry et al, 2014), or even higherIt may also account for 18% of the global electrical energy consumption (NapierMunn, 2015)More efficient crushing equipment needs to be Analysis of vertical roller mill performance with changes in 2016年6月6日 Discharge End Mechanical Considerations In the feed end and the cylinder of the mill, the active liners are bolted directly to the end or shell However, in the discharge end, the active liners must be bolted on top of the SAG Mill Liner Design 911Metallurgist
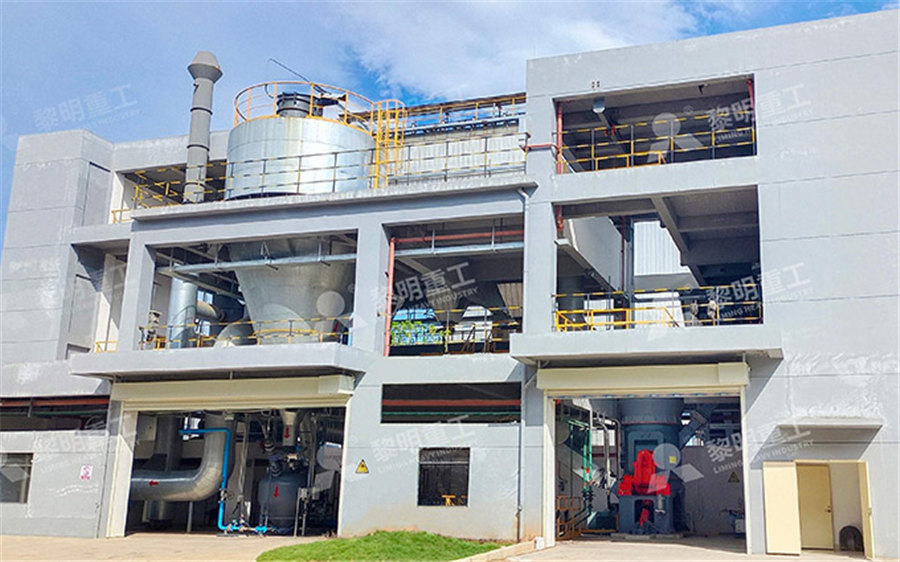
LOWSTRESS Trommel and Screen Media Lower costs, easy and
Key benefits Designed to increase structural life Improved screening efficiency and availability One partner for trommel, media and mill Easy and safe to install and maintan Lowest total cost of operation FLS —Trommel frames and screen media 3 Marketleading design backed by superior support Our new range of LOWSTRESS trommel frames and screen2023年6月7日 Wet autogenous mill is also called cascading autogenous mill Its structure is shown in Fig 3 Characteristics: (1) The cylinder has large diameter and short length, but its lengthdiameter ratio is greater than that of dry autogenous mill and usually 03–05 (2) The end cover is conical, with cone angle 150 °Autogenous Mill SpringerLink2019年8月3日 Internal Cracks and NonMetallic Inclusions as Root Causes of Casting Failure in Sugar Mill Roller Shafts(PDF) Internal Cracks and NonMetallic Inclusions asFig No 1– Three roller sugar mill [7] roller The rollers are arranged in an isosceles triangle with a top angle of 720 The feed and discharge rollers are placed at an angle of 35 37 respectively from the vertical below the top roller The crushing of cane takes place first in topfeed roller and then in topdischarge roller The shaftStatic Structural Analysis of Crushing Rollers of Three Roller Sugar Mill
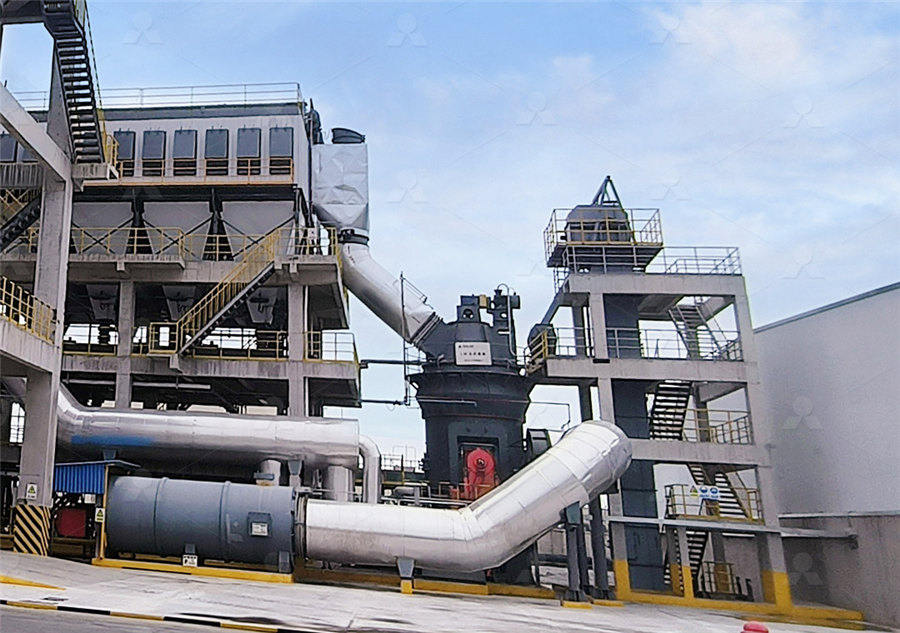
Overflow Ball Mill Wet Ball Mill Shanghai YingYong Machinery
The overflowtype ball mill is a wet grinding machine used as the key equipment for secondary grinding It is named after its feature of an overflow discharge, and it offers several advantages, like a high crushing ratio, strong adaptability, and large capacityThe correct choice of the discharge equipment is a major issue for the design of the wagon tipping station Hopper discharge with rotary discharge machine,type RDM Rotary discharge machine,type RDM Hopper discharge with deep drawn pan conveyor,type KZB 250S Hopper with deep drawn pan conveyor,type KZB 250SHopper Discharge Systems ZAS AgenciesThe mill structure, scraper, hydraulic system, material, and pressure difference will all affect the grinding efficiency of the vertical mill The hardness, composition, viscosity, moisture, and particle size of the grinding material will all affect the output, so the appropriate grinding machine should be selected according to the nature of the grinding materialUltrafine Vertical Mill2023年1月2日 As shown in Figure 11, under the lining plate height height arrangement, according to practical experience, the height of the lifting strip of the cylinder lining plate at the feed end is Structure optimization and application of shell liner of large SAG mill
.jpg)
STEP CHANGE IN LINER DESIGN FOR THE KANSANSHI 32FT SAG MILL
The discharge end of the SAG mill was originally fitted with straight radial grates and pulp lifters, which were replaced by a Bradken Vortex discharge design as shown in Figure 7 The Vortex discharge end encourages early discharge of coarse product and improves pulp movement down the pulp chamber per2) Three high roller mill 3) Four high roller mill 4) Six high roller mill Usually three roller mills setup is used nowadays to extract of juice form sugarcane in sugar industry It consists of three rollers that is top, feed and discharge rollers The processed Sugarcane is being feed in between top, feed and discharge rollers as well as the Design of Three Roller Shafts of Sugar Mill Using Static Structural mm (8 in) and water enter the feed end of a SAG mill through a feed chute; the ore is milled in the shell and milled product exits through grates and pulp lifters at the discharge end (Fig 1) The discharge is screened and the undersize, typically less than 12 mm (05 in), provides ball mill feed and the oversize is returned for further millingSemiautogenous grinding (SAG) mill liner design and development2024年9月12日 Friction and wear test equipment, scanning electron microscope, abrasion balls made of CGr15 high carbon chromium bearing steel, and liners made of NM500 steel were used for wear simulation and friction–wear experiments The variation trends of friction coefficient, wear amount, and subsurface characteristics under dry friction and slurry conditions were studied Friction and wear characteristics and simulation study of NM500 lining
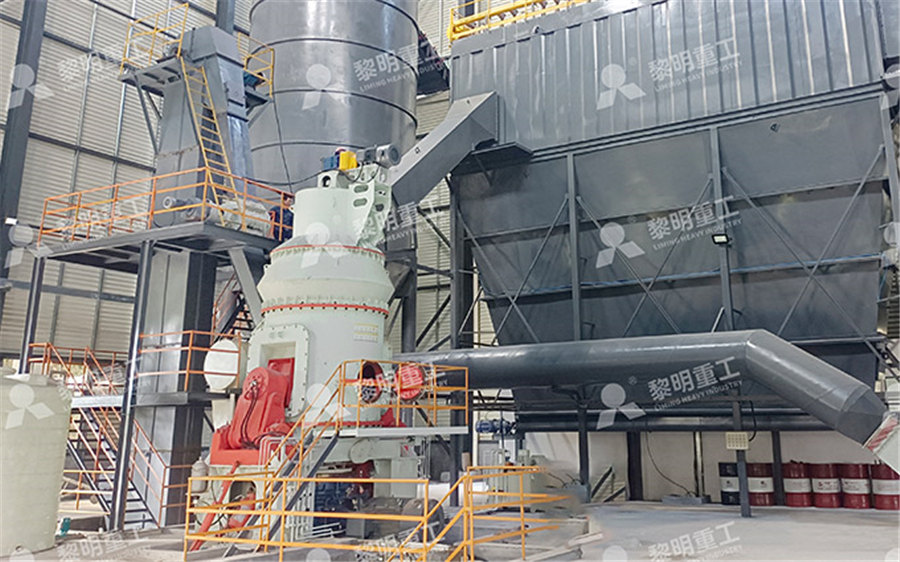
Superhigh Manganese Steel Ball Mill Lining Plate Liners
Roller; Conveyor Belt; ’ processes through customized designs The use of internationally recognized advanced specialized software simulation mill liners for lining structure, • Single wave liners • Modified single wave liners • Double wave liners • Shell liners • Feed head liners • Discharge end liners Rod Mill Liners RENN Mill Center Inc Tel: 4037843518 Fax: 4037842060 : sales@rennmill RR#4 Lacombe, AB T4L 2N4 rennmill Authorized Dealership Roller Mill Specifications and Configurations Model Roll DxW (in) Shaft Dia (in) Min Elec HP*** Min PTO HP*** PTO Std* Auger Discharge Elevator Discharge Blower Discharge Conveyor Roller MillDownload scientific diagram Drawing of the basic structure of a roller mill with two rotating/counterrotating rollers (crosssection) from publication: A study of operating parameters of a Drawing of the basic structure of a roller mill with two rotating Table Energy saving effect of the vertical roller mill Ball mill Specific power Cost estimation About 14million US$ [Newlybuilt] and about 230 million US$ [retrofitted], including the cost of supplemental facilities [200tRM/h] [1US$=¥110] Related matters References Fig1 Vertical roller mill Vertical roller mill Effect(%)Vertical roller mill for raw Application p rocess materials
.jpg)
Vertical roller mill Hengtu Machinery
The roller hydraulic system has an adjustable spring rate that is applied to the bed through a hydraulic pull rod The designed vertical roller can be easily flipped over the casing and the roller lining is easy to maintain The material of the roller and the grinding plate are made of alloy wearresistant linings with long service lifeMinimum value of deformation is 0 mm which is at bearing position Maximum value of total deformation is 024424 mm at pinion end of discharge roller B Static Analysis of Discharge Roller: C Static Analysis of Feed Roller: CAD model, meshing, material, boundary conditions are same as that of top rollerStatic Structural Analysis of Crushing Rollers of Three Roller Sugar MillThree types of grooves are commonly manufactured into finished sugar mill roller shafts; • • • Fine grooves, containing 5–20 mm of pitch Medium grooves, containing 20–50 mm of pitch Coarse grooves, containing >50 mm of pitch Tribochemistry of Sugar Mill Roller Shaft MaterialsFocus Minerals hit us up for a top job – reverse engineering the pipe spools and rubber lining for their mill discharge pumps We kicked things off with a laser scan, gathering all the data in e57 format That got chucked into our Reverse Engineering Software, where we cleaned it up and made sure everything lined upFocus Minerals – Mill Discharge Pumps Reverse Engineering of
46.jpg)
Rod Mill SpringerLink
2023年5月3日 End Peripheral Discharging Rod Mill The end peripheral discharging rod mill feeds the material from one end through the mill journal, and discharges the grinding products from the other end of the mill to the adjacent ring groove with the help of a number of circumference holes (Fig 2)The structure of end peripheral discharging rod mill is basically AG MillDischarge Filler Ring, The filling strip is used between the lining plate of the feed end and the lining plate of the cylinder body Roller Liner Mill Parts Liner AG Mill Liner Bulkbuy More Less Hot Products China Products Chinese Manufacturers/Suppliers China AG MillDischarge Filler Ring AG Mill Liner and Filler Ring2023年3月16日 Dry ball mill: uniform discharge, low failure rate, no paste grinding, swelling, and other phenomena, no need to add water, saving costs, but sometimes in the grinding processing will form a dead corner, and the materials entering the dead corner are difficult to grind Wet ball mill: because there is liquid involved in the grinding process, there is no existing material What Is Ball Mill? Eastman Rock CrusherIn addition, the processing capacity of the rod mill is larger than that of the ball mill of the same specification The overflow, end peripheral discharge and center peripheral discharge are the three main types of rod mill, while only the wet overflow type rod mill is usually used as the pregrinding equipment in the cement plantRod Mill Ball Mill Cement Milll AGICO Cement Equipment
.jpg)
Titanium Alloy is Best Material for Roller Shaft in Sugar Mill IJITEE
Fig 1 Conventional 3 Roller Mill Arrangement A fourth pressroller ie toothed roller pressure feeder is employed in industry, which can be accustomed to fed sugarcane to top and feed rollers to facilitate extraction The top roller, feed roller and discharge roller shaft had shared about 50%, 15% and 35% torque These all rollers have amaterials Article Internal Cracks and NonMetallic Inclusions as Root Causes of Casting Failure in Sugar Mill Roller Shafts Muhammad Jamil 1,2, Aqib Mashood Khan 1,2, Hussien Hegab 3, Shoaib Sarfraz 4, Neeraj Sharma 5, Mozammel Mia 6, Munish Kumar Gupta 7, GuLong Zhao 2, H Moustabchir 8 and Catalin I Pruncu 9,10,* 1 Department of Industrial Engineering, University Internal Cracks and NonMetallic Inclusions as Root Causes of 2007年8月1日 SAG mill liner development draws primarily on practical experience from SAG milling operations supported by computerbased modeling of charge motion in SAG mills and on established good design practice Liner design needs to respond to the process aspects of mill liner action that are critical to good SAG mill performance, ie, the impact of shell liners on the Semiautogenous grinding (SAG) mill liner design and developmentof total hydraulic load, 15% hydraulic load is shared by feed roller and 35% is shared by discharge roller These all rollers have high coefficient of friction and these rollers rotated with the help of steam turbine In three roller mill, three rollers are arranged in isosceles triangle arrangement which help to removing sucrose up to 9697 % maxTo identify best material for roller shafts using static structural