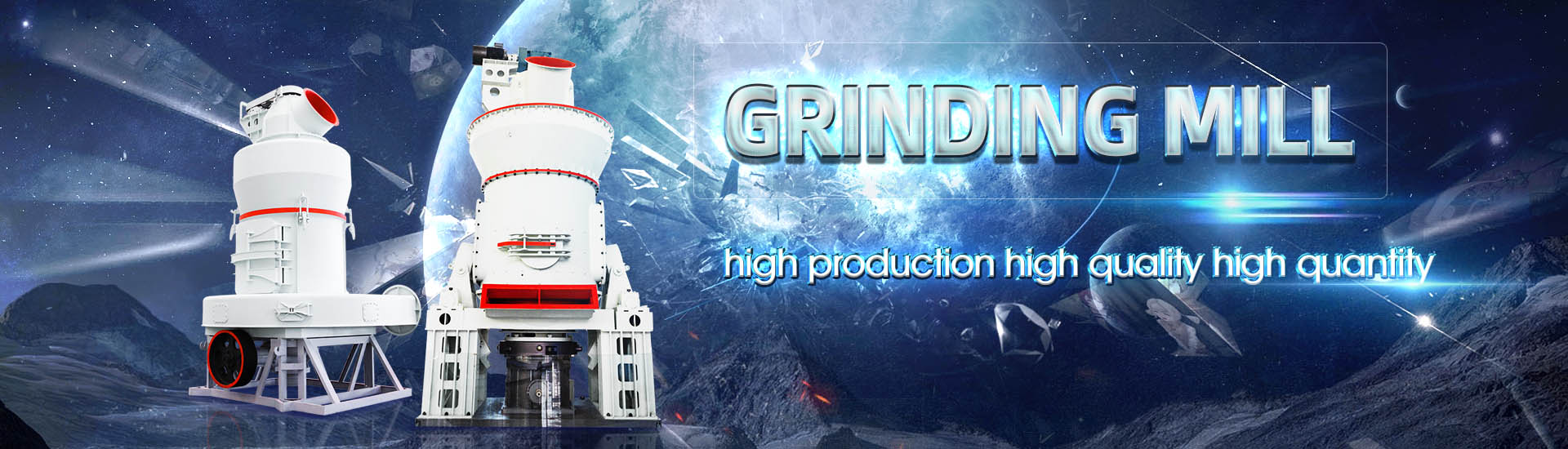
Cement mill with a lot of return
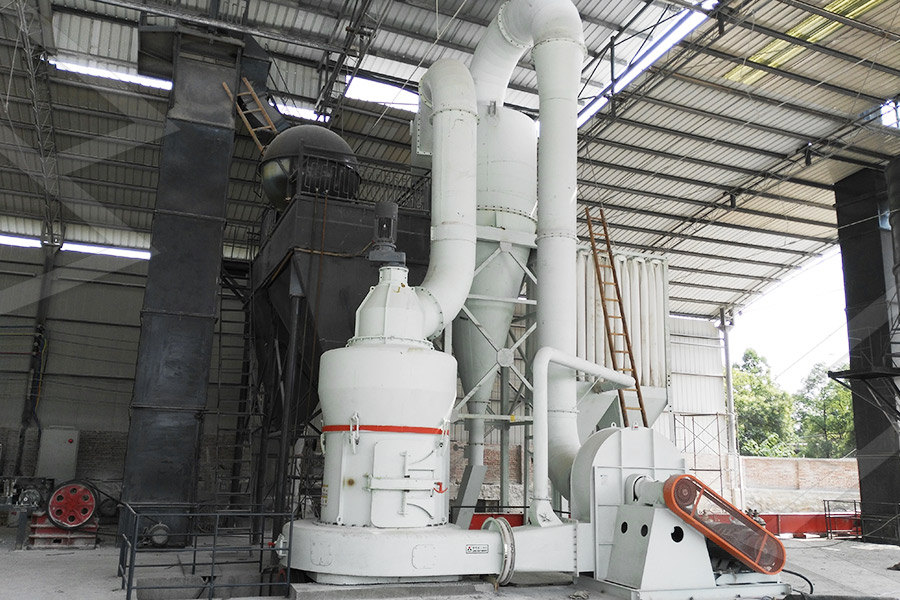
OPTIMIZATION OF CEMENT GRINDING OPERATION IN BALL MILLS
Several energy efficient options for cement grinding are available today such as vertical roller mills, roller presses (typically in combination with a ball mill), and clinker pregrinder s with ballCement milling is usually carried out using ball mills with two or more separate chambers containing different sizes of grinding media (steel balls) Grinding clinker requires a lot of energy How easy a particular clinker is to grind Cement MillingSeveral energy efficient options for cement grinding are available today such as vertical roller mills, roller presses (typically in combination with a ball mill), and clinker pregrinders with ball millsOptimization of Cement Grinding Operation in Ball We master the construction and design schemes of various cement grinding plant systems such as vertical mill system, combined system, and ball mill system No matter what type and strength of cement you want to produce, and what Cement Grinding Plant Expert Cement Grinding
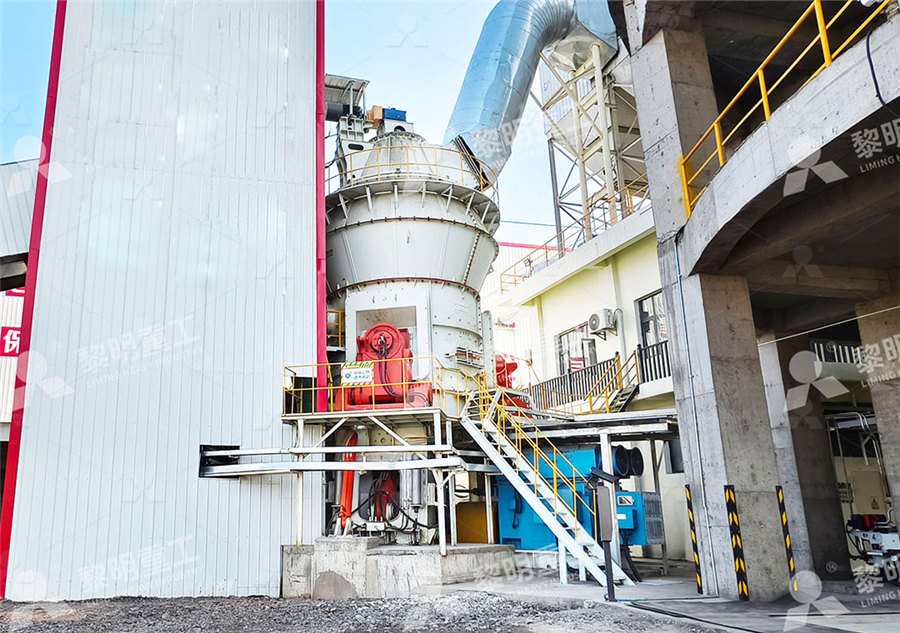
OPTIMIZING THE CONTROL SYSTEM OF CEMENT MILLING:
Abstract Based on a dynamical model of the grinding process in closed circuit mills, efficient efforts have been made to optimize PID controllers of cement milling The process simulation There are basically 4 types of cement mills in use today: Ball Mill (BM): predominant despite higher energy consumption partly because of historical reason but partly also because it still offers considerable advantages over Improvements in New Existing Cement Grinding As grinding accounts for a sizeable share in a cement plant’s power consumption, optimisation of grinding equipment such as ball mills can provide significant cost and CO 2BALL MILLS Ball mill optimisation Holzinger ConsultingOptimizing the operation of cement mills is essential to maximize productivity, reduce energy consumption, and improve the quality of the final cement product In this article, we will delve into practical strategies for cement mill Cement Mill Optimization: Practical Strategies for
.jpg)
Analysis of the efficiency of the process in closed circuit ball mills
Ball mills for fine grinding cement clinker and additives are widely used around the world To improve the efficiency of a ball grinding the ball mills are transferred in closed circuit with air The Cement Plant Operations Handbook is a concise, practical guide to cement manufacturing and is the standard reference used by plant operations personnel worldwide Providing a The Cement Plant Operations Handbook International Cement GLOBAL CEMENT: PLANT REPORT Global Cement Magazine January 2021 51 Left: Construction of the ready2grind mill at the BIGBOSS Cement plant in Porac in mid November 2020 Left: Map of the Philippines, with Manila, Batangas and BIGBOSS Cement plant shown Pampanga Province is highlighted • BIGBOSS CEMENT • BATANGAS LUZON VISAYAS Plant report: BIGBOSS Cement, Philippines Gebr Pfeiffer2022年3月16日 Cement ball mill is a kind of equipment for further fine grinding of materials, with high fineness It is widely used in industry, metallurgy, chemical industry, cement and other industries TheWhat is a Cement Ball Mill? How to Use It? by
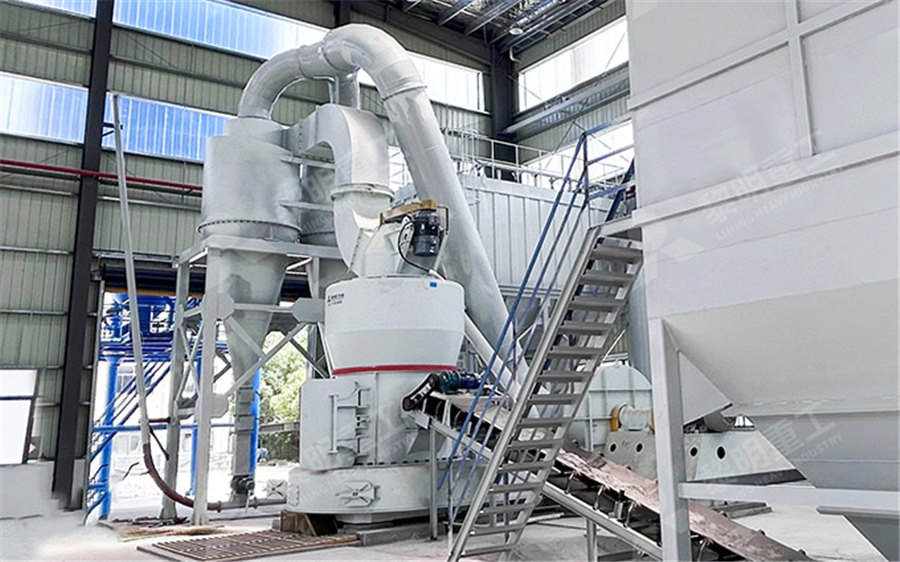
Cement Grinding Plant Expert Cement Grinding
Part of the materials return to the roller press for regrinding, and the qualified materials enter the cement mill for further grinding Compared with the first two grinding systems, although the grinding process of the combined grinding 2018年10月10日 Heat transfer in cement production with raw mill considering the minimum temperature difference 1Hot composite curve; 2cold composite curve, 3heat exchangers (developed after [30])Heat Integration in a Cement Production ResearchGate2020年12月21日 Construction of the ready2grind mill at the BIGBOSS Cement plant in Porac in mid November 2020 Map of Online meetings have been a big help in this regard A lot of pictures were sent back and forth to Germany In late which have enabled a return to some kind of normality Construction workers are now tested for Covid Plant report: BIGBOSS Cement, Philippines2020年12月15日 A lot of studies have indicated that the amount of free quartz in clay should be kept Terembula J Operational experience from the United States' first vertical roller mill for cement grinding Capacity of roller mill for cement grinding ResearchGate
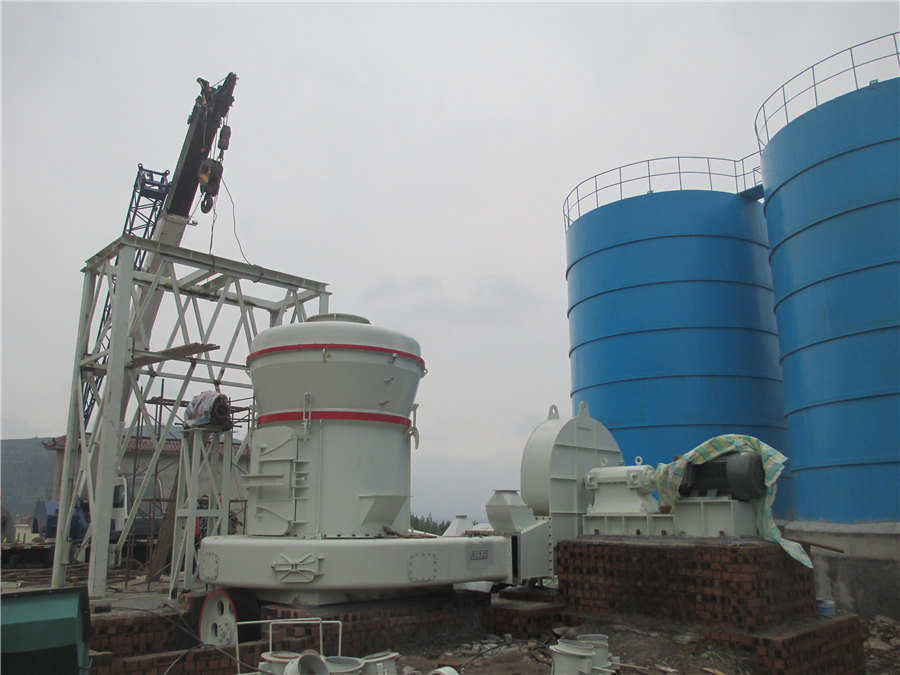
INCREASING OUTPUT OF CEMENT GRINDING IN BALL MILL
increases production of cement mill To seal air leakage in SKS Separator with uniform air gap increases output of cement mill Proper distribution of grinding media with appropriate sizes also enhanced productivity of cement mill Target To increase the TPH from 190 to 220 TPH (PPC) with maintaining quality parameter ie 8% residue on +45 micronDownload scientific diagram A schematic of a closedloop cement grinding control system Adapted from [6] from publication: Coarse Return Prediction in a Cement Industry’s Closed Grinding A schematic of a closedloop cement grinding control system2012年6月12日 About three and a half miles upstream on the CO Canal towpath from Hancock, Maryland are the ruins of the Round Top Cement Mill, one of the more interesting features on the canalI parked in the lot by the boat ramp, just east of the Route 522 bridge and rode my bicycle up to the ruinsRound Top Cement Mill Light, Shadow, Form, and Texture2017年4月3日 Above Table 1: Cement capacity added in Iran, 2005 2015 1 The most recent data from the Ministry of Industries, Mining and Trade, released in January 2017, shows that Iran’s cement production fell by 14% yearonyear to 427Mt in the first nine months of the Iranian calendar year that started on 21 March 2016 2 Cement industry ExportsThe cement sector of Iran
.jpg)
Predictive Control of a Closed Grinding Circuit
2017年10月12日 The resultant control strategy has enabled the operators to take corrective actions before the coarse return clink cooler, and cement mill are determined to be 3669%, 3424%, 3924 While this is not standard practice in cement production, cement plants in countries like India are often located far away from energy sources, so they rely on their own sources Power generation typically involves direct firing Coal Mill Safety In Cement Production IndustriesAnother comparative closed circuit grinding of clinker to high early strength cement of 4000 cm2/g Blaine, showed a 14% better grinding economy com pared to grinding of the same mill feed in a conven tional mill Besides, F L Smidth Grinding in closed circuit INFINITY FOR CEMENT Ball mill is the cement crushing equipment in the cement plant Compared with open circuit ball mill, the closedcircuit ball mill has high efficiency, Only when these conditions are met can we produce highquality cement At present, there are a lot of enterprises whose cement production can meet the above requirements, and the quality, Ball Mill In Cement Plant Cement Ball Mill AGICO Cement
.jpg)
BALL MILLS Ball mill optimisation Holzinger Consulting
and cement Roller presses are used mainly in combination with a ball mill for cement grinding applications and as finished product grinding units, as well as raw ingredient grinding equipment in mineral applications This paper will focus on the ball mill grinding process, its tools and optimisation possibilities (see Figure 1) The ball mill2015年2月14日 However, the measurement of material flow rates was not easier Costea et al [13] developeda fuzzy logicbased control architecture in which the ball mill grinding process was considered as a Control System Architecture for a Cement Mill Based on Fuzzy 1995年10月29日 In this paper we develop a Model Predictive Controller (MPC) for regulation of a cement mill circuit The MPC uses soft constraints (soft MPC) to robustly address the large uncertainties present (PDF) Cement mill optimization: Design parameters7 // Almost any plant for the grinding of cement raw material is a combination of machines specially adapted to the particular physical properties of the material to be ground As a result, our plants work efficiently without any trouble » Highly efficient grinding, drying, and separating in one unit » Outstanding production capacities exceeding 1,400 t/h in one single millPFEIFFER MILLS FOR THE CEMENT INDUSTRY
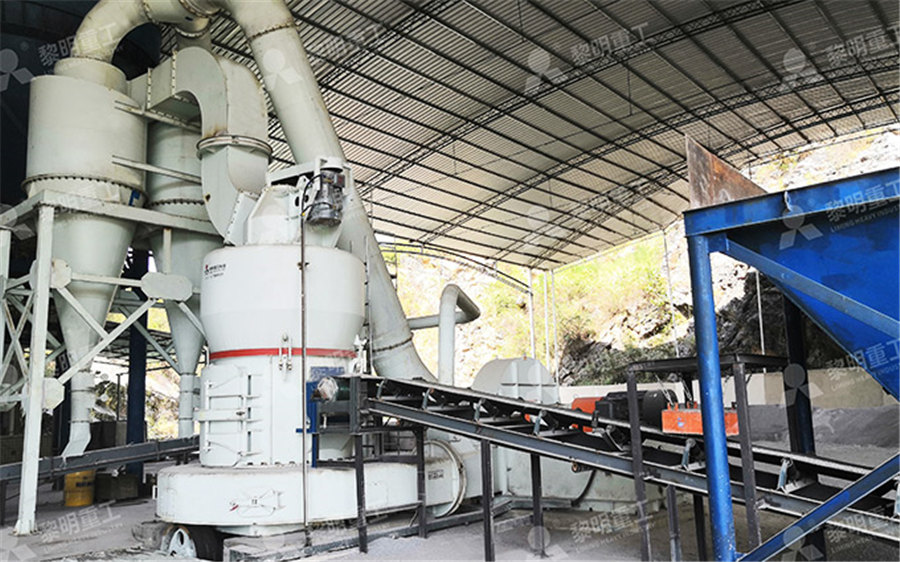
Cement grinding Vertical roller mills VS ball mills
Vertical roller mills and ball mills represent two clearly distinct technologies However, with proper adjustments to the operational parameters of the vertical roller mill almost identical cement properties can be achieved by the two mills that satisfy the cement user’s demandsNevertheless, the two types of mills have their distinctive meritsOptimal values for clinker level inside cement mill is 50% (30% are grinding media, for example steel balls and 20% are gas) Therefore, clinker level inside the mill is approximative 70% from mill capacity, excluding grinding media percentage For coarse return a value of 20% can be considered optimalControl System Architecture for a Cement Mill Based on Fuzzy GLOBAL CEMENT: GRINDING 42 Global Cement Magazine December 2016 GlobalCement Contents Subscribe Ad Index Field report of a cement plant modernisation with the compact 2Stage Koesep air classifier During 2015 the Austrian cement manufacturer Schretter Cie GmbH Co KG modernised its grinding processField report of a cement plant modernisation with the7 // Almost any plant for the grinding of cement raw material is a combination of machines specially adapted to the particular physical properties of the material to be ground As a result, our plants work efficiently without any trouble » Highly efficient grinding, drying, and separating in one unit » Outstanding production capacities exceeding 1,400 t/h in one single millPFEIFFER MILLS FOR THE CEMENT INDUSTRY
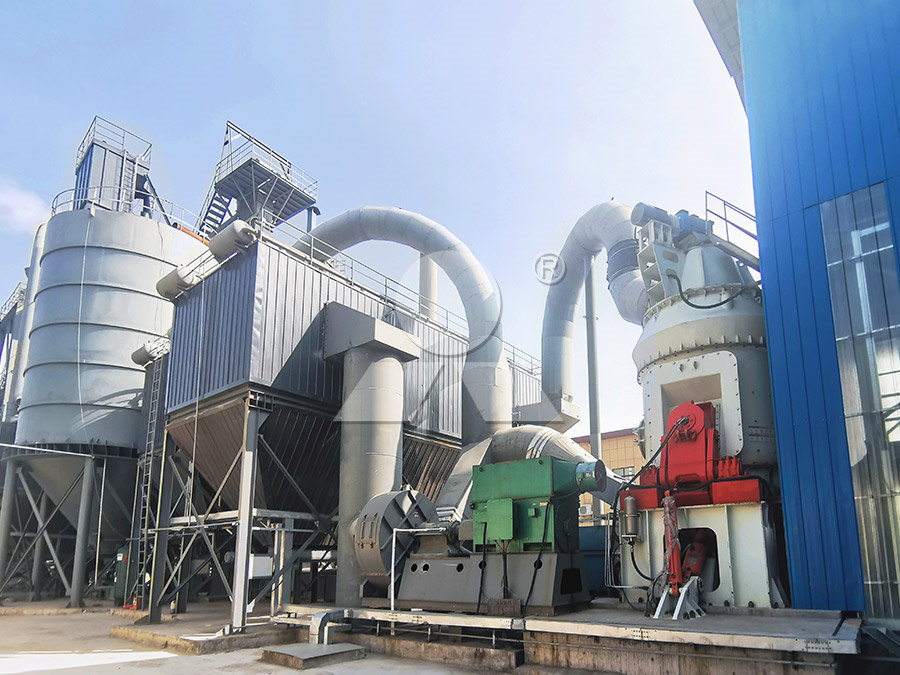
(PDF) Thermodynamic Analysis of Raw Mill in
2018年9月10日 The simulator was used for the thermodynamic performance of a raw mill (RM) and raw materials preparation unit in a cement plant in Nigeria using actual operating data The raw mill has a capacity 2016 Abstract—Fuzzy logic is a new and innovative technology that was used in order to develop a realization of engineering control In recent years, fuzzy logic proved its great potential especially applied to automatization of industrial process control, where it enables the control design to be formed based on experience of experts and results of experimentsControl System Architecture for a Cement Mill Based on Fuzzy LogicDownload scientific diagram The use of electrical energy in cement production from publication: Determination of correlation between specific energy consumption and vibration of a raw mill in The use of electrical energy in cement productionEVERY COMPONENT OF BALL MILL DETAILED EXPLAINED To Download this post + all manuals and books and Excel sheets and all notes I collected over my 23 years of experiance in Cement industry click here now A lot of individual rotating masses risk of resonance vicinitiesEVERY COMPONENT OF BALL MILL DETAILED EXPLAINED INFINITY FOR CEMENT
.jpg)
(PDF) Review of the Effect of Grinding Aids and Admixtures on the
2023年11月6日 PDF Grinding aids (GAs) are polar chemicals introduced in cement mills in either liquid or powder form to improve on mill grindability efficiency Find, read and cite all the research you Cement mill A cement mill (or finish mill in North American usage[1]) is the equipment used to grind the hard, nodular clinker from the cement kiln into My in return for favourable prices Clearly, plenty of excess cement milling capacity is needed in Cement mill2022年9月28日 With a grinding table diameter of 808 metres and roller diameter of 264 metres, Shah Cement Industries’ vertical roller cement mill isn’t your runofthemill piece of equipment In fact, so unique is this towering machine, which was first put into operation in 2018, that it has its very own entry in The Guinness Book of Records as the Largest Vertical Cement Mill, with a Hafiz Sikander, Operations Director of Shah Cement IndustriesDifferences between Cement Ball Mill and Vertical Cement Mill Grinding Mechanism The grinding mechanism of a ball mill is a series of impact and attrition events that occur inside a large rotating drum The grinding media collide with each other and the material being ground in the drum, creating a large amount of heatDifference between a Cement Ball Mill and Vertical Cement Mill
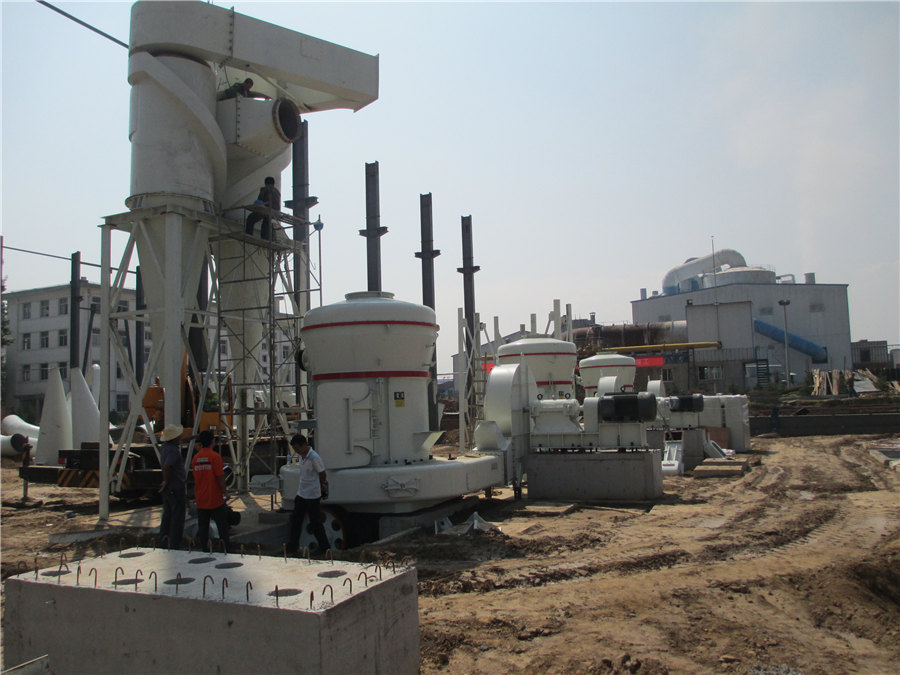
Process Training Ball Mill INFINITY FOR CEMENT
Most cement plants have restrictions with regards to their finish cement temperature, which should in a lot of cases not exceed 160 F (71 DEG C) Since in most cases the feed temperature of clinker is higher than 220 F (104 DEG 2014年3月1日 For each cement type a PID set is selected and put in o peration in a closed circuit cement mill The power of the recycle elevator or return flow rate, Q 0Optimizing the control system of cement milling: Repair of two cement mill gear units at a Belgian cement plant 1 » return to plant and reinstallation » recommissioning Insitu repair was not possible within the time available, That would have necessitated a lot of complicated cement mill gear unit BRAUER Maschinentechnik AGFKPumps and airlifts use compressed air thus consuming major share of power Replacing FKPumps and air lifts with bucket elevator for blending silo / Cement Silo, Kiln feed can make substantial saving in power This can be made possible by locating the blending silo and Cement Silos near the Raw Mill and Cement Mill building respectivelyModern Processing Techniques to minimize cost in Cement
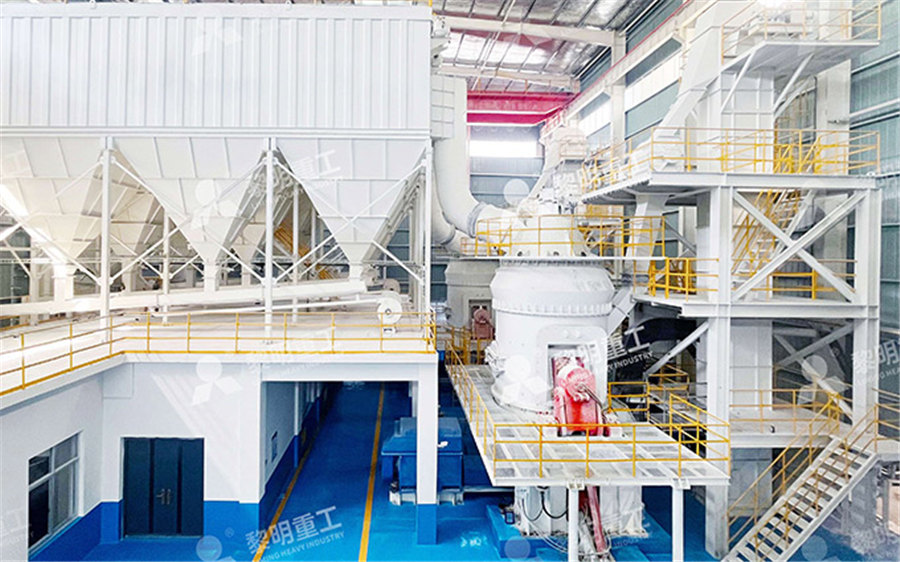
Cement ball mill Xinxiang Great Wall Machinery Co, Ltd PDF
The cement ball mill can perform dry process production and also wet process production, moreover it can do grinding and drying at the same time CHAENG cement ball mill has features of small investment, high rate of return, simple process and easy operation Advantages of CHAENG cement ball mill: 1Material Mill System in China Cement Industry between 2014 and 2019 Ruonan Meng 1,2, Qinglin Zhao 1,2,* , Miaomiao Wu 1,2, The disadvantage is consuming a lot of electricity, A Survey and Analysis on Electricity Consumption of Raw Material Mill 2023年1月30日 CalPortland Cement (CPC) is subsidiary of Japan’s Taiehiyo Cement and renowned for its commitment to energy efficiency The Mojave K6 line was built in the early 1980s and has been upgraded a number of times since then, but it was still operating the original raw mill – a nonFLSmidth brand VRM rated for about 250 stphNew OK raw mill increases productivity and efficiency at World Cement2018年1月27日 A cement plant in Gujarat (India), partnered with Ecomak Systems to improve production capacity by 1 Million TPA by implementing the Reverse Air Baghouse design by Ecomak by Ecomak Systems Introduction Gujarat is a state in the western part of India with beautiful coastal beaches, as well as good quality of limestone reserves A reputedEcomak enhances cement kiln output with Baghouse retrofit
.jpg)
INVT VFDs Applied to Fans in the Cement Plant
2020年4月4日 There are many kinds of fans in the cement plant For example, Raw material mill ID fan/ Coal mill ID fan/ Cement mill ID fan/ Preheater hightemperature fan/ Kiln end fan / Kiln head fan/ the grate cooler/ separated fan and transport power fan Optimization of a Fully Airswept Dry Grinding Cement Raw Meal Ball Mill Closed Circuit Capacity With the Aid Free download as PDF File (pdf), Text File (txt) or read online for free This document discusses optimizing the production capacity of a fully airswept industrial scale twocompartment cement ball mill through simulation The mill has two compartments, with the first Optimization of A Fully AirSwept Dry Grinding Cement Raw Meal