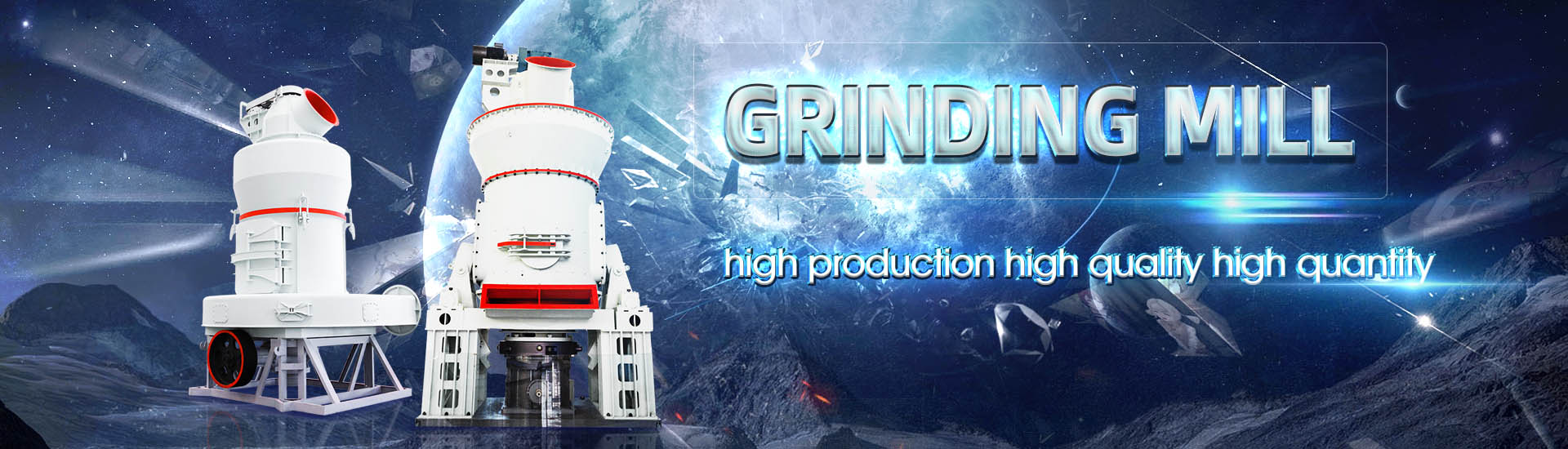
p talcum ore mill, feed size
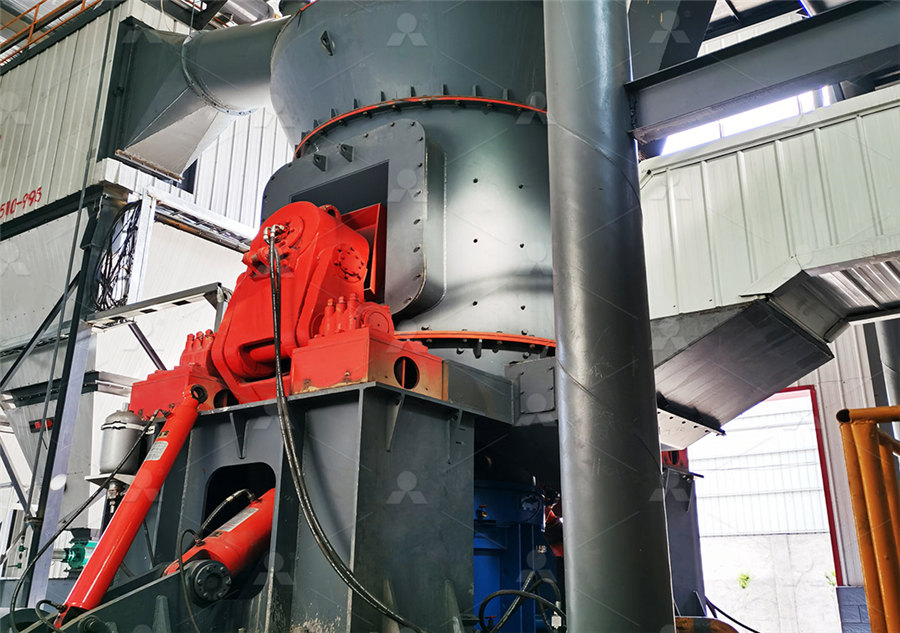
Determination and scaleup of the milling parameters of a high
understand the breakage properties of the ore to be used The kinetics of size reduction in tumbling mills is often determined using two probabilistic functions: selection and breakage functions [3] The knowledge of the Selection and Breakage functions also enables the 2019年9月1日 Narrowsize feeds of the ore were prepared and milled with 20 and 30 mm sets of singlesize balls using the onesize fraction method From the experimental data obtained, milling parameters of the ore were determined, validated and then used in the population balance Tailoring ball mill feed size distribution for the production of a size In this article, alternative forms of optimizing the milling efficiency of a laboratory scale ball mill by varying the grinding media size distribution and the feed material particle size distribution were investigated Silica ore was used as the test material The experimental parameters that were Effect of ball and feed particle size distribution on the milling 2018年6月1日 In this article the effect of grinding media size distribution and feed material particle size distribution (PSD) on the product fineness requirements were investigated A model free approach called the Attainable Region method was then applied in order to optimize the Effect of ball and feed particle size distribution on the milling
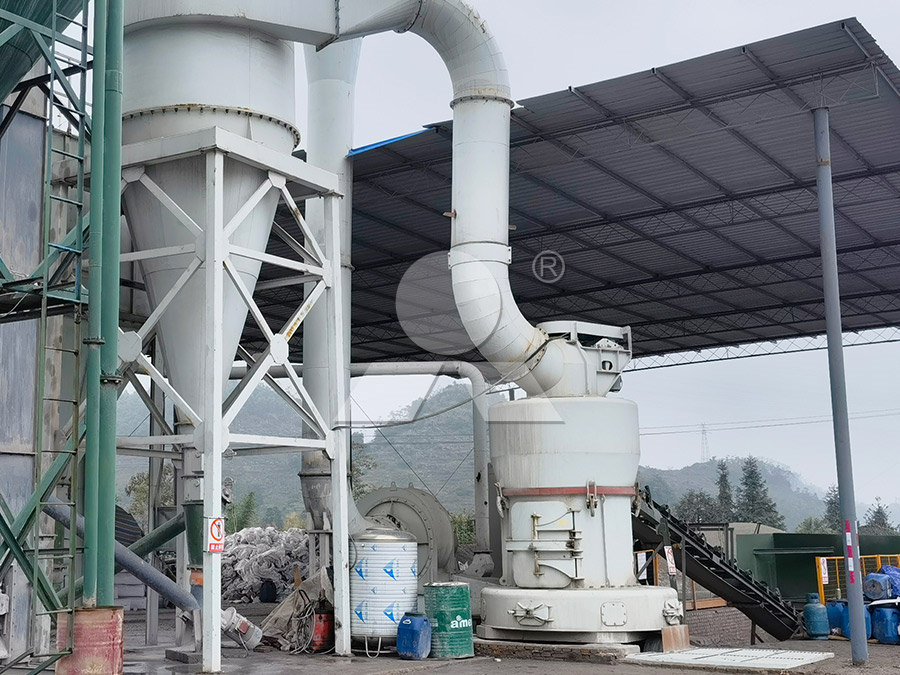
Parameters affecting wet ultrafine grinding of talc ore
Conventional mills require long retention time and tremendous energy input for micron size production This work aims at studying the parameters affecting wet ultrafine grinding of Egyptian talc from Shalatin locality of the Eastern Desert to produce ultrafine product less than 10 2023年10月18日 As a result of study, a final ultrafine talc powder was obtained after 60 minutes grinding time with d50=185 µm particle size and 14058 cm2/g total surface area It has been seen that the conventional ball mill+stirred mill combination effective a process to obtain talc Combination of Conventional Ball Mill and Stirred Mill to Obtain 2022年12月22日 This is a sizebased crushing test using a conical ball mill to establish an energysize reduction relationship [Shi, 2014] Experiments were conducted with five monosized feed samples including 300–600 μm, 600–1180 μm, 1180–2000 μm, 2000–2800 μm, and An Energy T 75 Size Reduction Model for Ball Mills Springer2018年2月1日 It was found that the ball mill consumed 5467 kWh/t energy to reduce the F 80 feed size of 7222 lm to P 80 product size of 2754 lm while stirred mill consumed 3245 kWh/t of energyEffect of ball and feed particle size distribution on the milling
.jpg)
Combination of Conventional Ball Mill and Stirred Mill to
In this study, it was investigated that talc ore could ground to very fine sizes using a combination of conventional ball mill and vertical stirred mill Firstly, the conventional ball mill parameters such as millEffect of ball and feed particle size distribution on the milling efficiency of a ball mill: An attainable region approach N Hlabangana a, G Danha b, *, E Muzenda b a Department of Chemical Engineering, National University of Science and Technology, P O Box AC 939, Ascot Bulawayo, Zimbabwe b Department of Chemical, Materials and Metallurgical Engineering, College of Effect of ball and feed particle size distribution on the milling 2001年1月1日 The efficiency of the mill to break ore is a function of both the feed size distribution and the relative hardness of the ore When the feed size of a SAG mill becomes coarser, ie α r increases Influence of feed size on AG / SAG mill A new method, staged flotation for effectively increasing the recovery of ultrafine copper oxide ore with a new type of collector (ZH1, C35 carbon chain xanthate) is proposed for the first timeParticle size distribution (PSD) of the mill feed
.jpg)
THE APPROPRIATENESS OF THE TRANSFER SIZE IN AG AND SAG MILL
6 0 2 4 6 8 10 12 14 16 18 20 % 6000 T80 (microns) Figure 4 – Histogram of T80 vales from AG/SAG Talcum powder making machine is also called talc industrial ultrafine grinding mill, which can produce 1503000 mesh talcum powder and other nonmetallic ore which can produce 1503000 mesh talcum powder and other nonmetallic ore +17 [ protected] Feed size: 20 mm Output: 0545 T/HTalcum Powder Making Machine2016年7月8日 Sizing a Ball or Rod Mill Sizing a Crusher using >1200 Wi of Ores from Database For your convenience, F the feed size or diameter in microns of the square hole which 80% of the feed passes, P the product size or microns which 80% of the product passes, and Rr the reduction ratio F/P To find the Work Index (IF/) use Equation 1Equipment Sizing: Crusher or Grinding Mill 911Metallurgist2022年10月1日 The relationship between parameters F 80 02 and P 80 06 for ores with different hardness of standard size and coarse and finer samples shows some variation in Fig 1 It was assumed that each ore had its own unique “Hukki exponent”, which means that the empirical exponents differ slightly from the ore’s actual breakage characteristicsA new methodology to obtain a corrected Bond ball mill work
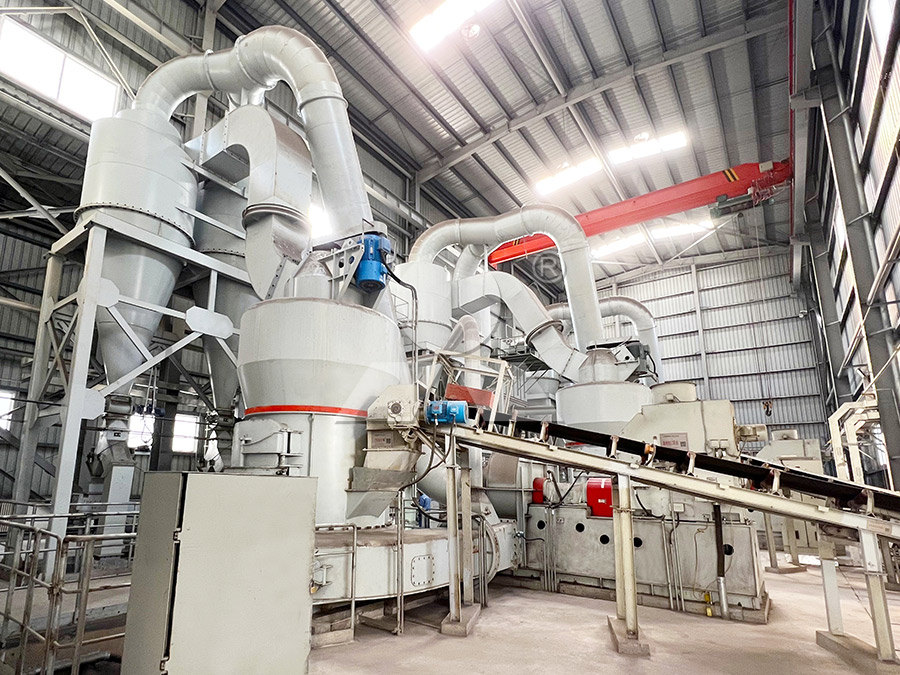
Crushing Plant Flowsheet DesignLayout 911Metallurgist
2016年3月11日 To reduce runofmine to mill feed requires reduction in a series of stages The physical size and power requirements of a crusher capable of reducing hard rock vary depending on the application Extended experience in most crushing plants show that a minus 19MM (¾”) rod mill feed can be and is being produced in three stages of crushingJanuary 2007, two complete grinding circuit surveys were performed followed by a SAG mill crash stop and grindout After stopping the mill, a SAG mill feed sample was also collected from Conveyor parison of SAG mill feed size throughputswill become the predictions In the case of SAB/SABC circuits the transfer size is the product of the SAG mill circuit and the feed of the ball mill circuit Hence if powerbased equations such as eq 1 and eq 2 are to be used to predict the SAG mill circuit and ball mill circuit specific energies it is important to ascertain:THE APPROPRIATENESS OF THE TRANSFER SIZE IN AG AND SAG MILL 2015年4月15日 During grinding tests obtain samples of mill feed for grindability tests so that work indices calculated from the pilot plant data can be compared to grindability test results Operating work indices can be obtained using pilot What Ore Testing is Required For Mill Selection
.jpg)
Talcum powder with different fineness perfoms in filler
Here we take 325 mesh talcum powder and 1250 mesh talcum powder as an example The difference between the talc with these two fineness is mainly reflected in particle size and distribution Among them, 325 mesh talcum selected iron ore samples is shown in Table 2Inthe crushing machine, all the three iron ore samples were crushed to −3 mm and analyzed for the desired P 80 passing (−150 μm) and percentage of hematite liberated in the three feed iron ore samples The – 150μm feed size fractions were selected to determine the nominalEstimation of Grinding Time for Desired Particle Size Distribution2016年2月1日 A case study was undertaken at a gold mine in the Free State on the influence of the fragment size distribution on 'free gold', the effect of ore loss and dilution on the mill efficiency, and time Monitoring ore loss and dilution for minetomill integration in 2011年1月1日 Ball mills in HPGRBall mill circuits tend to have more installed capacity than their counterparts in AG/SAGBall mill circuits This is because the product size distribution from AG/SAG mills (PDF) The appropriateness of the transfer size in AG and SAG Mill
.jpg)
5 Effects of flow rate, slurry solid content, and feed size
Mill feed particle size circuit’s feed size, the ore was passed through screens with 180 aperture of 12, 20, 25, and 30 mm prior to feeding the material to the 2 mm trommel screen2020年10月1日 In most concentrators, the generation of new − 75 μm during the grinding process is commonly used to evaluate the grinding effect of a millEffect of feed size on residence time and energy consumption in a 2018年4月8日 Regrind Ball Mill F = 210 micrometers P = 45 micrometers Wi = 140 W = 10 x 140/√45 – 10 x 140/√210 = 1121 kwh/s ton Efficiency Factors: EF1 does not apply EF2 Many regrind operations are closed circuit, but assume this one is open circuit and 80 percent passing grind will be the controlling point Refer to Table VIII The EF2 How to Size Design a Regrind Ball Mill 911Metallurgist2019年8月15日 In this study eggshells and low density polyethylene plastic (LDPE) wastes were reused to produce tiles The eggshells were ground in a laboratory scale jar mill into the particle size of fine sand(PDF) Effect of interstitial filling, ball and feed size on particle
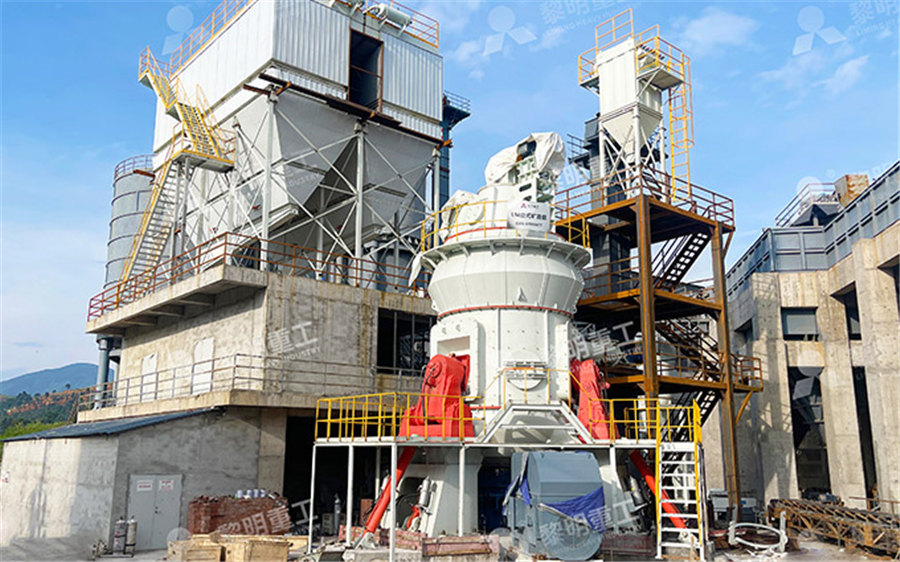
Ore Feed Size * Work Index Hardness: Crushing
2015年7月29日 The coarser ore being drier and having more space in between each piece than is normal, will not slow the flow of fine material towards the discharge points as much This means that when the crushers stop putting ore 2018年1月19日 The key ore related parameters relevant to throughput for the BHX circuit are the size distribution of the feed to the mill and the comminution or mill hardness The feed size is a function of the fragmentation from blasting and primary crushingPredicting Mill Ore Feed Variability Using Integrated Geotechnical 2018年6月1日 A number of researchers (Deniz, 2012; Bwalya et al, 2014; Petrakis et al, 2016) carried out studies about the effect of feed particle size and grinding media size on the grinding kinetics of different oresKhumalo et al, 2006 postulated that generally larger sized grinding media would break larger particles quicker but a finer product would be obtained by use of Effect of ball and feed particle size distribution on the milling Mill Weight Power Top Size Figure 4: Feed Top Size vs SAG Mill Performance 5000 5500 6000 6500 7000 7500 8000 8500 9000 9500 10000 13:00 14:00 15:00 16:00 17:00 kW 00 500 1000 1500 2000 2500 3000 3500 4000 Top size (mm) Top Size Power Mill Weight Figure 5: Feed Top Size vs AG Mill Performance This is not say that ag mill performance I203 I204 INTRODUCTION SMC Testing
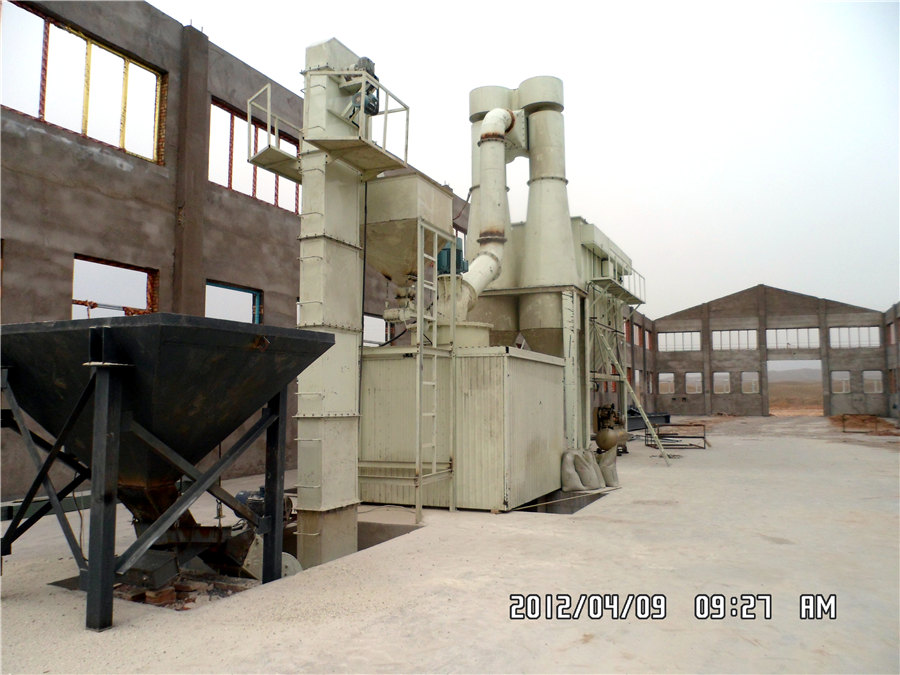
Introduction of talcum powder surface modification
The third part refers to the talcum powder packing machine This machine adopts the technology of electronically automatic measurement, variablefeed and frequencyconverted method Talcum powder grinding machine; Talcum powder packing machine; If you want to get more information in our talcum powder processing plant, please feel free to 2016年6月6日 Criticalsized particles are those where the product of the mill feedsize distribution and the mill breakage rates result in a buildup of a size range of material in the mill load, Four 1067 x 2400 mm vibrating feeders under the coarse ore stockpile feed the SAG mill via a 1067 mm feed belt equipped with a belt scaleSAG Mill Grinding Circuit Design 911Metallurgist2020年7月2日 A comprehensive investigation was conducted to delineate the effect of ball size distribution, mill speed, and their interactions on power draw, charge motion, and balls segregation in a (PDF) Effects of Ball Size Distribution and Mill Speed and Their 2023年3月16日 Feed size was divided into two fractions of (+238 −4) and (+2 −238) millimeters, from which different feeds with different weight and size percent values were fed to mill at three feeds of Fractal approach of particle size distribution description of ball
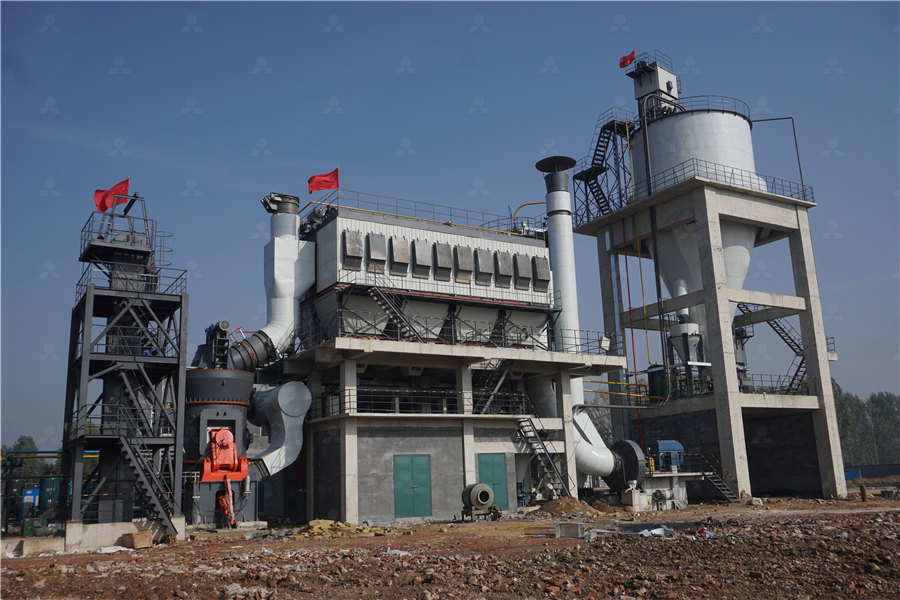
Particle Size Distribution Effects that Should be Considered when
He concluded that the size distribution from a laboratory rod mill gave a similarshaped size distribution to that of a closed circuit laboratory ball mill He also demonstrated how a laboratory rod mill gave a similar shape of size distribution to a 36 inch (08 m) Hardinge ball mill in closed circuit with a rake classifi er treating the same oreTalc is a filler for plastics second only to calcium carbonate, and the number of applications in plastic guessing is more than 200,000 tons per year, and it has been further deepened as some of the physical and chemical characteristics Talcum powderused as an agricultural film insulation 2022年5月23日 Grinding experiments were conducted in a laboratoryscale stirred mill on a lowgrade PGE bearing chromite ore HighPressure Grinding Rolls (HPGR) product of −1 mm was used as feed material to (PDF) Modeling and application of stirred mill for the coarse 2021年9月1日 Recently, acoustic sensor measurements have gained upsurge of interest in the grinding circuit, particularly AG/SAG and ball mill to monitor and optimise charge dynamics such as the toe and shoulder angle, load level estimation, particle size distribution, pulp viscosity, ore breakage rate, charge size distribution and interaction and liner wear rate (Aldrich and Theron, Predicting mill feed grind characteristics through acoustic
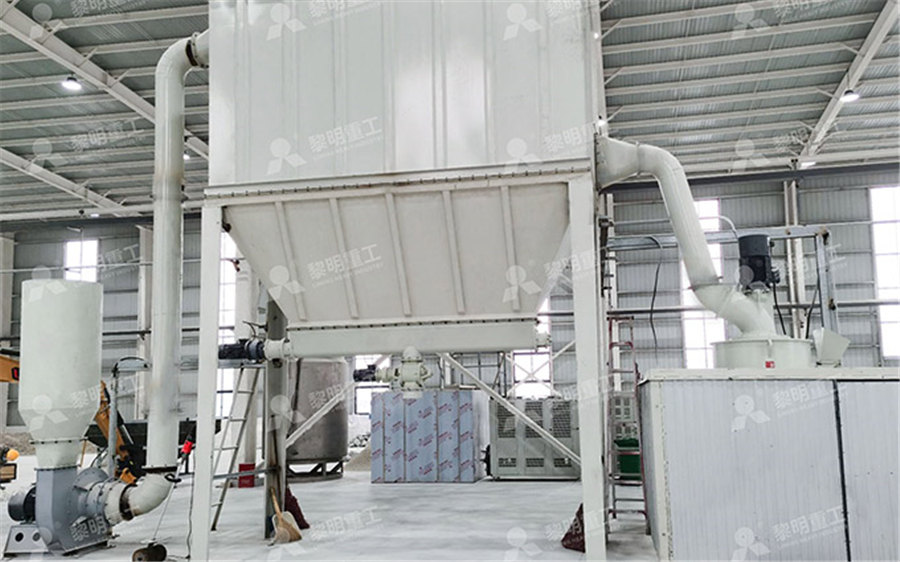
Influence of feed size on AG/SAG mill performance
100 2500 20 18 80 16 14 Mill Throughput 60 40 20 Sieve 1500 12 10 1000 8 6 500 Split 0 01 1 10 Size (mm) 100 1000 4 Specific Power 2 0 0 50 Figure 1: Sag Mill Feed Size Comparison Between Sieving and Image Analysis Using the “Split” Throughput Specific Power Cum% Passing 2000 60 70 80 90 100 110 120 Feed Size F80 (mm)(mm) Figure 2: Correlation Download scientific diagram SAG Mill Feed Size Versus Throughput from publication: Optimisation of the Cadia Hill SAG mill circuit ResearchGate, the professional network for scientistsSAG Mill Feed Size Versus Throughput ResearchGatethe objective of mill feed size optimisation Results Monitoring the mill feed size WipFrag results showed a remarkable correlation between the % fines and mill tonnage for all grinding lines The effect of feed size on one of our autogenous mills is shown in Figure 3 page I193 Even short term changes in % fines (eg peak inThe Importance of Primary Crushing in Mill Feed Size OptimizationDOI: 101016/JSAJCE201802001 Corpus ID: ; Effect of ball and feed particle size distribution on the milling efficiency of a ball mill: An attainable region approachEffect of ball and feed particle size distribution on the milling
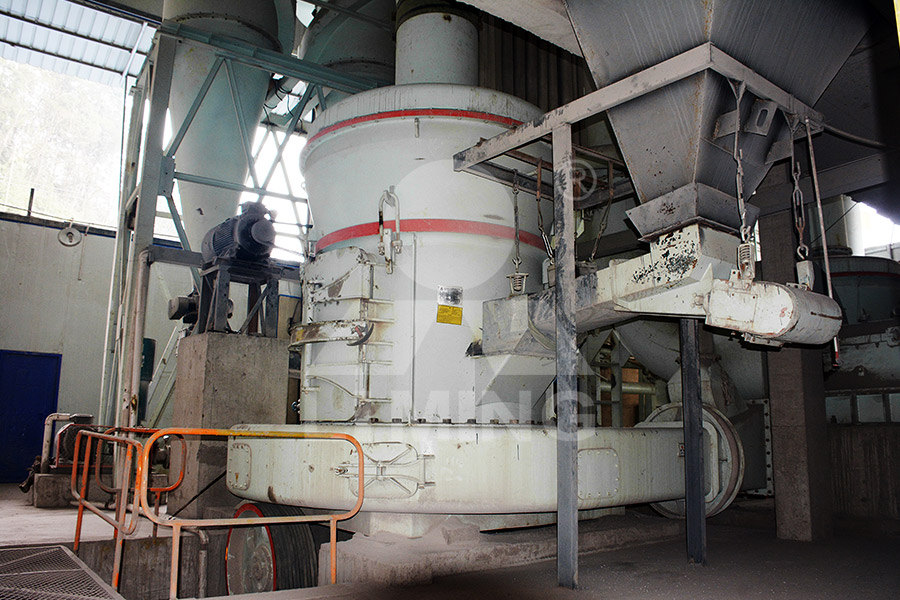
(PDF) Grinding Media in Ball MillsA Review ResearchGate
2023年4月23日 Therefore, it was concluded that the effect of ball size on mill performance depends also on the feed size Another study conducted by Petrakis et al [47] on gr inding ferronickel slag using diff 2018年3月30日 We describe here one of the very first pioneering SAG Mill Feed Particle Size Analysers: A set of preliminary experiments was carried out in order to assess the hardwaresoftware’s behaviourStatic ore was used to obtain the right sequence of image processing algorithms The camera was installed 3 mts away from the commercial sizer over the feed SAG Mill Feed Particle Size Analyser 911Metallurgist2013年8月3日 In Grinding, selecting (calculate) the correct or optimum ball size that allows for the best and optimum/ideal or target grind size to be achieved by your ball mill is an important thing for a Mineral Processing Engineer AKA Metallurgist to do Often, the ball used in ball mills is oversize “just in case” Well, this safety factor can cost you much in recovery and/or mill liner Calculate and Select Ball Mill Ball Size for Optimum Grinding