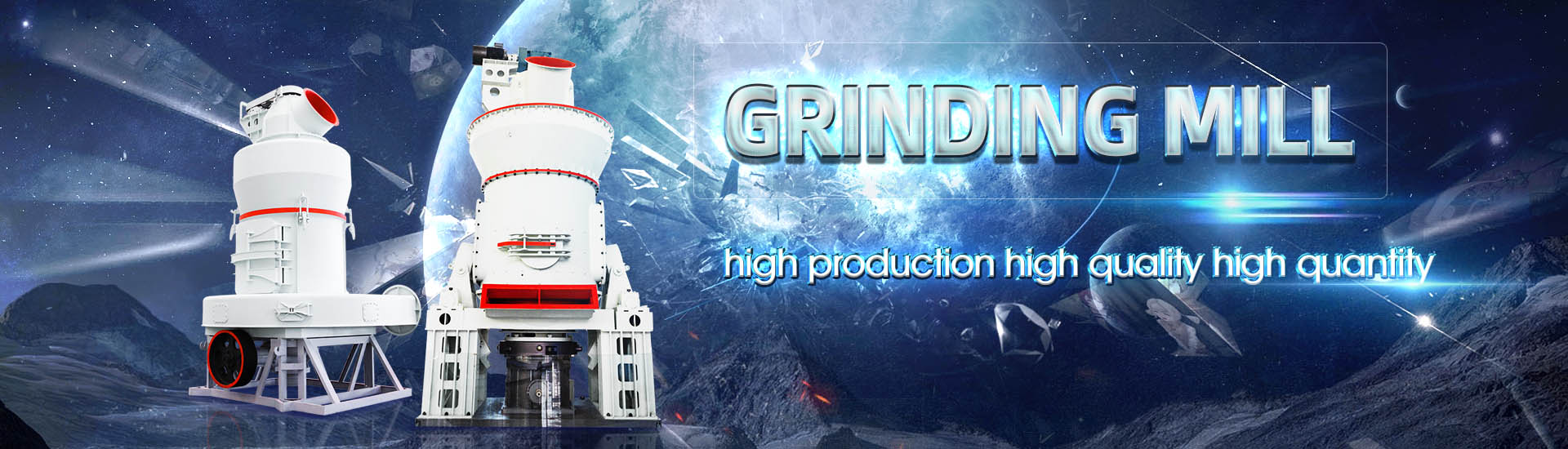
Industrial mill, how small is the discharge port of the ore mill
.jpg)
AMIT 135: Lesson 7 Ball Mills Circuits – Mining Mill Operator
Size rated as diameter x length Feed System 1 One hopper feed 2 Diameter 40 – 100 cm at 30 ° to 60 ° 3 Top of feed hopper at least 15 meter 展开2016年6月1日 The Steel Head Rod Mill is available with five types of discharge trunnions and each type trunnion is available in small, medium, or large Rod Mills: Efficient Grinding Solutions for Mining2023年5月3日 In accordance with different ore discharging ways, rod mill can be divided into center discharge (overflow type) and peripheral discharge (open type), and the latter is further Rod Mill SpringerLink2024年11月1日 The ore discharge rate of the slurry lifter with the radial pattern structure increased gradually during the discharge process and then tended to stabilize The steady Study on the influence of the discharge end cover structure of
.jpg)
ISAMILL FINE GRINDING TECHNOLOGY AND ITS INDUSTRIAL
The IsaMill is a horizontal stirred mill with sizes up to 3 m3 chamber net volume and 1120 kW installed motor It was jointly invented by Mount Isa Mines of Australia and Netzsch 2012年6月1日 Several types of ball mills are distinguished discharge mill, eg see [23] In industrial applications, the inner surface of the mill and cascades down [36] • ceramic balls Grinding in Ball Mills: Modeling and Process Control ResearchGate2020年1月1日 Discharge of desired particle size is directly related to critical speed of the mill Mill with lifters has maximum discharge of desired particle size Mill with lifters has minimum A comparative study on a newly designed ball mill and the Smaller scrubbers 13×33 ft (500–700 kW) are suited to small scale soft ore (100400 t/h) operations Larger scrubbers up to 2,500 kW have the capability of very high throughput in THE MODELLING OF SCRUBBERS AND AG MILLS, WHEN TO USE
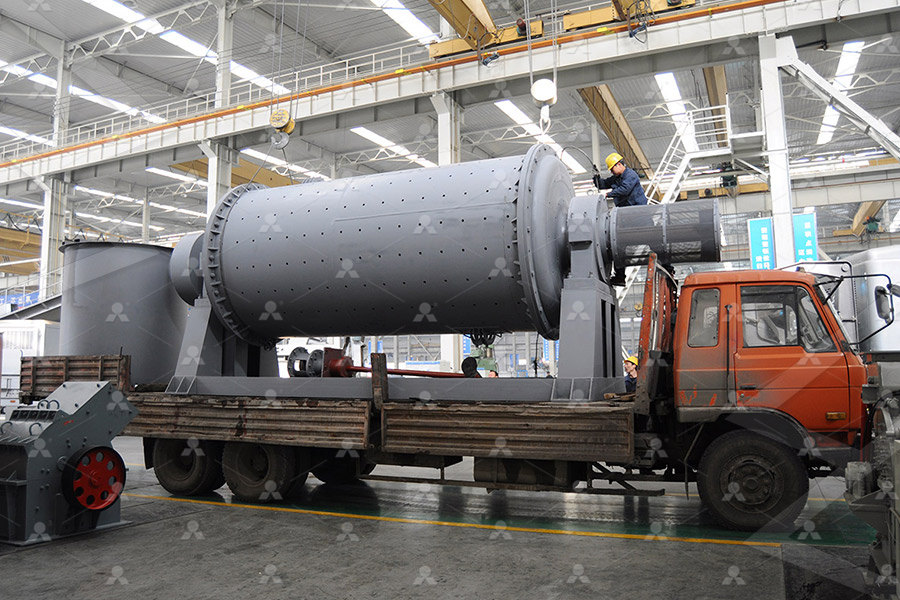
TECHNICAL NOTES 8 GRINDING R P King
t varies with the type of discharge For overflow mills = 798 and for grate mills K = 910 This difference is ascribed to the presence of a pool of slurry that is present on the bottom of 2024年1月1日 Peripheral discharge ball mill, and the products are discharged through the discharge port around the cylinder According to the ratio of cylinder length ( L ) to diameter ( Ball Mill SpringerLink2015年4月9日 This type of mill is only suited for those kinds of ores which are of a fairly coarse nature but once they are broken, disintegrate readily into small size Typically this type of mill can deliver a product with a fineness of less Grinding Mills and Their Types – IspatGuruMILL POWER DRAW Charge Motion Modelling of the charge motion is based on the approach adopted by Morrell (1996a and 1996b) for predicting the power draw of wet tumbling millsTHE MODELLING OF SCRUBBERS AND AG MILLS, WHEN TO USE
.jpg)
(PDF) The appropriateness of the transfer size in AG
2011年1月1日 The AG/SAG circuit discharge P80 is now increasingly referred to as the “Transfer Size” or T80 for short From the literature it is apparent that in circuit design some approaches to the Ball Mill Introduction There are three main stages to mineral processing in the mining industryThese are: Comminution (crushing and grinding); Beneficiation (separation and concentration); Smelting and refining; Ball mills are employed in the comminution stage as grinding machines (size reduction)The purpose of grinders in the mining industry is to reduce Ball Mill (Ball Mills Explained) saVRee saVRee2015年9月1日 Discharge of pebbles, finer rock, ball scats and slurry from mills and its flow through trommels, and into other processing operations has strong impacts on overflow ball mill performanceSimulation of overflow ball mill discharge and trommel flow using Mill Type Overview Three types of mill design are common The Overflow Discharge mill is best suited for fine grinding to 75 – 106 microns; The Diaphram or Grate Discharge mill keeps coarse particles within the mill for additional grinding and typically used for grinds to 150 – 250 microns; The CenterPeriphery Discharge mill has feed reporting from both ends and the product AMIT 135: Lesson 7 Ball Mills Circuits – Mining Mill Operator
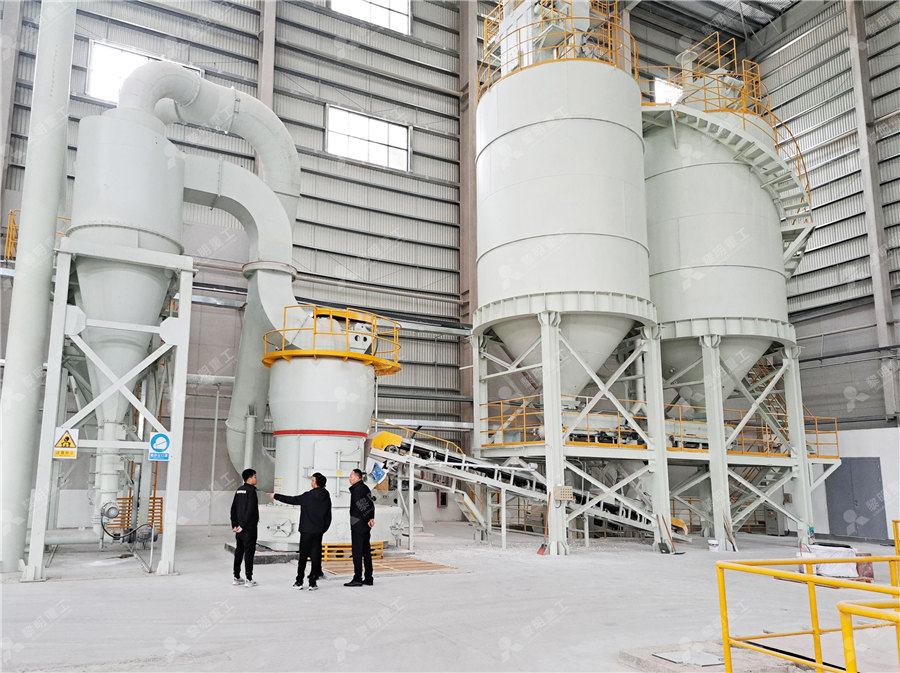
2020 Technology and Operation of a Hot Rolling Mill
2020年1月3日 Transfer bar cooling system installed at the hot strip mill of Tata Steel´s Port Talbot [2] Scale breaking in the roll bite, simulation of 45% reduction Rolling Forces with and without separated Or, in the case of industrial minerals, used as is Grinding is often done in steps: a primary mill grinds the largesized ore and then a secondary mill grinds the ore from a small size to the desired size The breakage mechanisms that mills use are impact (for coarse grinding), and attrition and abrasion (for finer sizes)Three factors that determine the wear life and performance of mill 2016年3月14日 It is useless to expect a large capacity from a mill operated with balls of a size too small to crush the ore, or when the balls are of a composition that will not withstand the shock of impact and shatter themselves to fragments Hard ores, when fed direct from a crusher, require a proper percentage of 5in steel balls to do effective workPeripheral Discharge Ball Mills Theory and PracticeThe basic design of the industrial hammer mill is really quite simple: A steel chamber containing a shaft to which rectangular steel hammers are affixed Replaceable plates lining the mill's interior to reduce wear caused from grinding abrasive materials Steel screens or bar grates cover the mill's discharge opening hammermills 3The Industrial Hammer Mill: A Versatile Workhorse
.jpg)
Calculate Ball Mill Grinding Capacity 911Metallurgist
2015年10月15日 Grate Discharge mills will not face this issue C) This value represents the Volumetric Fractional Filling of the Voids in between the balls by the retained slurry in the mill charge As defined, this value should never 2014年1月1日 The sample of coarse iron ore was characterized in laboratory tests carried out in a small batch ball mill Selection and breakage function parameters were determined from the laboratory testsPopulation balance model approach to ball mill 2023年5月27日 Industrial development has begun to have a negative impact on the entire environment The constant need and agreed of humans has resulted in the formation of massive polluting industries(PDF) Causes and Impact of Industrial Effluents on 2024年11月1日 The small ore particles that fit the size requirements need to enter the the lifting bars raise the ore particles to a height where they can slide down and exit through the discharge port resulting in a smaller relative equilibrium angle and facilitating easier discharge of ore particles from the SAG mill’s outlet as Study on the influence of the discharge end cover structure of SAG mill
.jpg)
SAG Mill Liner Design 911Metallurgist
2016年6月6日 If the discharge diaphragm does not have a large enough capacity the mill will display all the outward appearances of being too small (or a given capacity The charge and slurry level will rise, the grind will get coarser, and slurry will leak from the feed chute seals2024年11月1日 The grate liners and slurry lifter, separated into two stages, finish the discharging process of the SAG mill First, the ore slurry is released through the grate liners; and being released from the discharge port 3D liner wear profile measurement and analysis in industrial SAG mills Miner Eng (2007)Study on the influence of the discharge end cover structure of SAG mill mill specific power, pilot plant ball mill specific power, pilot plant product size distributions and Bondtype calculations (as reported by Rowland (Rowland, 1982) and modified by Minproc) SAG Mill Dimensions: The SAG mill was designed for monzonite ore, with allowance in the mine schedule for reduced throughput when treating the harder Design of the 40 foot SAG Mill Installed at the Cadia Gold Copper 2023年2月15日 It is better to select a grate discharge ball mill when the required discharge size is 02 ~ 03 mm b Overflow discharge ball mill The overflow discharge ball mill is designed with no sieve plate so that the ore pulp can be discharged directly without filtration It is very simple in structure and convenient for maintenanceWhat Are the Differences between Ball Mill and Rod Mill?
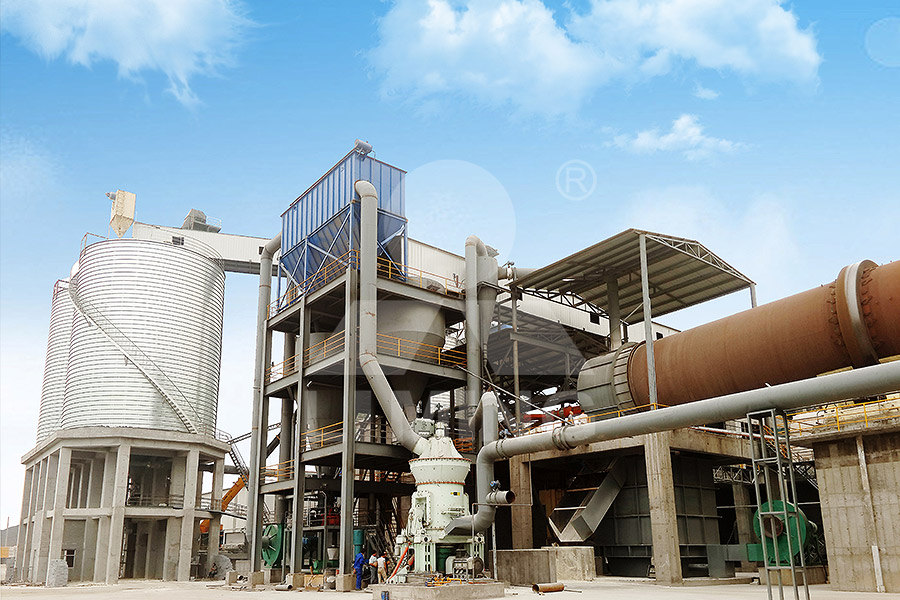
Closed circuit ball mill – Basics revisited Request PDF
2013年4月1日 Industrial application results show that after the abrasion of the secondary ball mill for grinding magnetite was enhanced, the circulating load of the grindingclassification system dropped by 29 2024年5月27日 Grated / Diaphragm Ball Mill: Designed to discharge material through slots or grates, providing efficient grinding and separation Peripheral Discharge Ball Mill: This mill features discharge ports around its periphery, allowing quick removal of the ground material Rod Mill: Uses long rods for grinding media, ideal for coarse grinding Ball Mills in the Mineral Processing Industry MechProTechoverflow discharge mill, diaphragm or grate discharge mill and centreperiphery discharge mill, eg see [23] In industrial applications, the inner surface of the mill is lined with mill liners protecting the steel body of the mill and incorporating mill lifters which help to raise the content of the mill to greater heights before it dropsGrinding in Ball Mills: Modeling and Process Control Sciendo2015年8月13日 Tramp metal in the ore such as scaling bars and rock bolts cut the rubber and can become lodged in the grate openings This puts an excessive strain on the grates When the mill rotates the metal is pushed and twisted by the ore This stretches the rubber and can cause severe damage to the face and the back of the grateHow a Grate Discharge Ball Mill Works 911Metallurgist
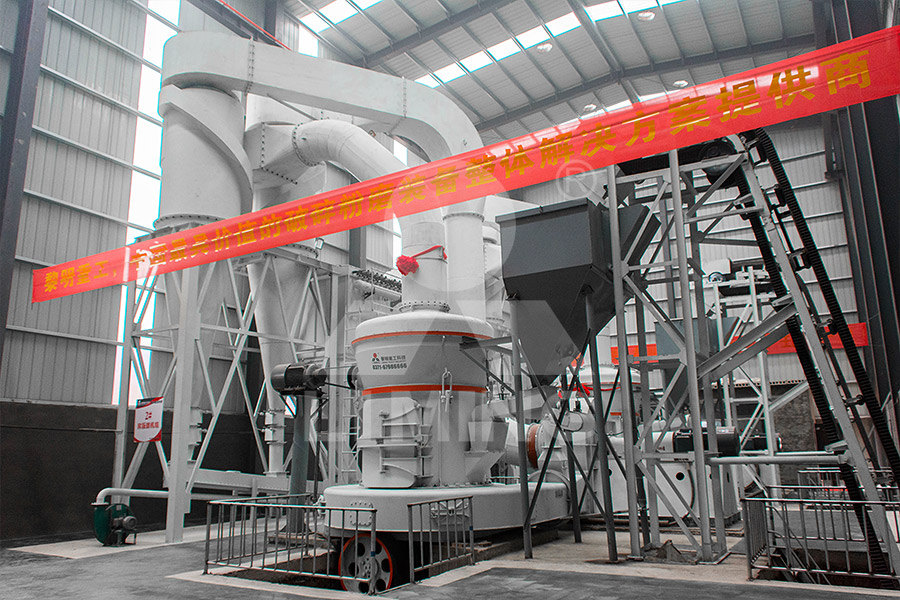
Impact of industrial effluents on the environment and human
2022年11月1日 Rapid industrialization and urbanization are becoming the new fulcrum for a nation's economic growth and a critical area for human wellbeing But, it is also becoming an emerging pointsource of water pollution and a decisive, inescapable, threat to disturb the ecosystem and homeostasis of the environment (Gaur et al, 2020)As a direct impact analysis 2007年7月1日 Silica and Fe presence, however, are almost universal and, together with oxygen, are usually the most abundant elements, with Al, Ca, K, Mg, Mn, Na, P, Ti and S also major components (Table 1)Methods for the disposal and storage of mine tailings2016年6月6日 The ability to mill a broad range of ore types in various circuit configurations, Circuits producing a coarser grinds often classify mill discharge with screens the design stress levels at the trunnion/head transition in the case of the SAG Mill Grinding Circuit Design 911Metallurgist2024年7月12日 The ball mill discharge system can be enhanced with the use of Mineral Jigs or Unit Flotation Cells to immediately remove free minerals Types of Grinding Media Grinding media, also known as grinding medium, are essential in ball mills, as they help to reduce the size of the ore particles through both attrition and impactWhat Is a Ball Mill and How Does It Work? Certified MTP Blog
.jpg)
The Selection and Design of Mill Liners 911 Metallurgist
Mill linings, Weir Rubber Engineering, Salt Lake City, UT 84126, United States of America ABSTRACT Dramatic shortcomings of mill liner designs, especially of large SAG mills, such as rapid failure and even mill shell damage arising from 2023年6月19日 2 Different discharge way The gridtype ball mill discharges the material through the sieve plate under pressure, which is a forced ore discharge This is also the reason for the name grid ball mill The overflowtype ball mill overflows from the discharge pipe when the pulp in the cylinder reaches a certain height, which is a passive ore Battle of the Mill Grid Ball Mill VS Overflow Ball Mill2024年1月31日 It can be seen that the discharge yield of −0075 mm was close to that of the ceramic ball mill ore and the steel ball mill ore, 2458% and 2581%, respectively However, the ceramic ball ground product +03 mm yield is about 13 percentage points higher than that of Enhancing the Grinding Efficiency of a Magnetite SecondStage Mill 2016年11月7日 In Fig 13 is shown a large ball mill, designed for the dry grinding of limestone, dolomite, quartz, refractory and similar materials; this type of mill being made in a series of sizes having diameters ranging from about 26 in to 108 in, with the corresponding lengths of drum ranging from about 15 in to 55 inGrinding Mills Common Types 911Metallurgist
.jpg)
Ball Mill SpringerLink
2023年4月30日 Peripheral discharge ball mill, and the products are discharged through the discharge port around the cylinder According to the ratio of cylinder length ( L ) to diameter ( D ), the ball mill can be divided into short cylinder ball mill, L/D ≤ 1; long barrel ball mill, L/D ≥ 1–15 or even 2–3; and tube mill, L/D ≥ 3–5PDF On Apr 8, 2019, Azam Akhbari and others published A study of palm oil mill processing and environmental assessment of palm oil mill effluent treatment Find, read and cite all the research (PDF) A study of palm oil mill processing andWith the continuous feeding of materials, the generated pressure forces the materials that are fed first and have reached the qualified particle size to move to the discharge port of the wet grinding mill The discharge port of the wet Wet Ball Mill for Metal Ores and Nonferrous Metals 2023年10月27日 The ball mill is a rotating cylindrical vessel with grinding media inside, which is responsible for breaking the ore particles Grinding media play an important role in the comminution of mineral ores in these mills This work reviews the application of balls in mineral processing as a function of the materials used to manufacture them and the mass loss, as A Review of the Grinding Media in Ball Mills for Mineral Processing
.jpg)
Five essentials for optimizing hammermill operations
The resulting inconsistent feed rate to the mill creates unwanted deviations in the milling process This is especially significant when a mill is used with varying materials and can result in wide deviations in performance The optimal material feeding method for a mill provides a reliable and consistent mass feed rate to the mill inlet2015年8月7日 This is done by guiding the slurry to the underflow at the same time presenting a smooth surface that will not restrict the generation of the CENTRIFUGAL FORCE that makes classification possible Connected to the lower cone is the APEX The apex is the discharge point of the cyclone, this discharge is referred to as the UNDERFLOWHydrocyclone Working Principle 911Metallurgist2019年11月26日 The ball mill adopts a discharge screen similar to the ball mill, and the function of blocking the internal medium of the overflow ball mill is accomplished inside the rotary part of the ball mill The discharge screen is only responsible for forcing out a small amount of the medium that overflows into the discharge screen through the internal What’s the Difference Between SAG Mill and Ball Mill2020年6月23日 Converting a mill from an overflow to a grate discharge arrangement leads to an increased power draw This happens because the installation of the grate discharge arrangement enables the mill to run with a lower level of slurry due to it being no longer necessary for the slurry to build up inside the mill until it overflows from the mill dischargeConverting a ball mill from overflow to grate discharge Metso
.jpg)
Understanding the SAG Mill in Copper Ore Mining Process
The rod mill is another type of grinding mill used in the copper ore mining process This machine uses steel rods as the grinding media instead of balls, which are commonly used in ball mills The rods grind the ore by tumbling within the mill, similar to the action of a rotating drumOur ball mills are industrial grade and designed for continuous operation, equipped with oversize roller bearings and a complete drive system All wear parts are highly abrasion resistant and replaceable The capacity, or throughput, of a ball mill is Ball Mills Mt Baker Mining and Metals