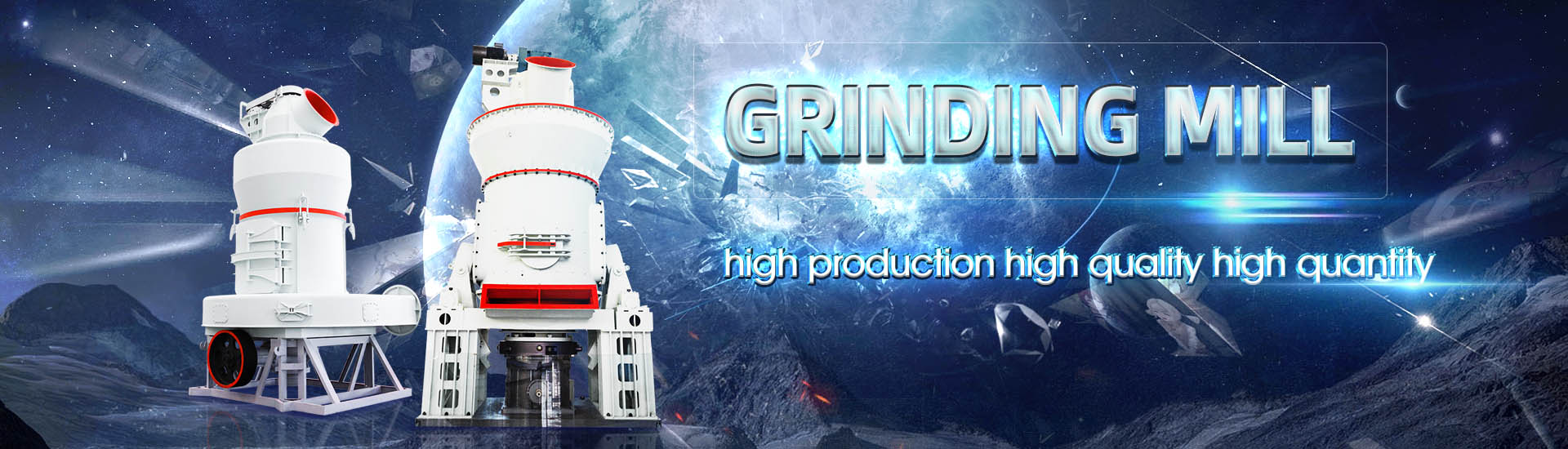
HOME→Crushing energy consumption, and the energy consumption of grinding operations accounted for the crushing energy consumption, and the energy consumption of grinding operations accounted for
Crushing energy consumption, and the energy consumption of grinding operations accounted for the crushing energy consumption, and the energy consumption of grinding operations accounted for
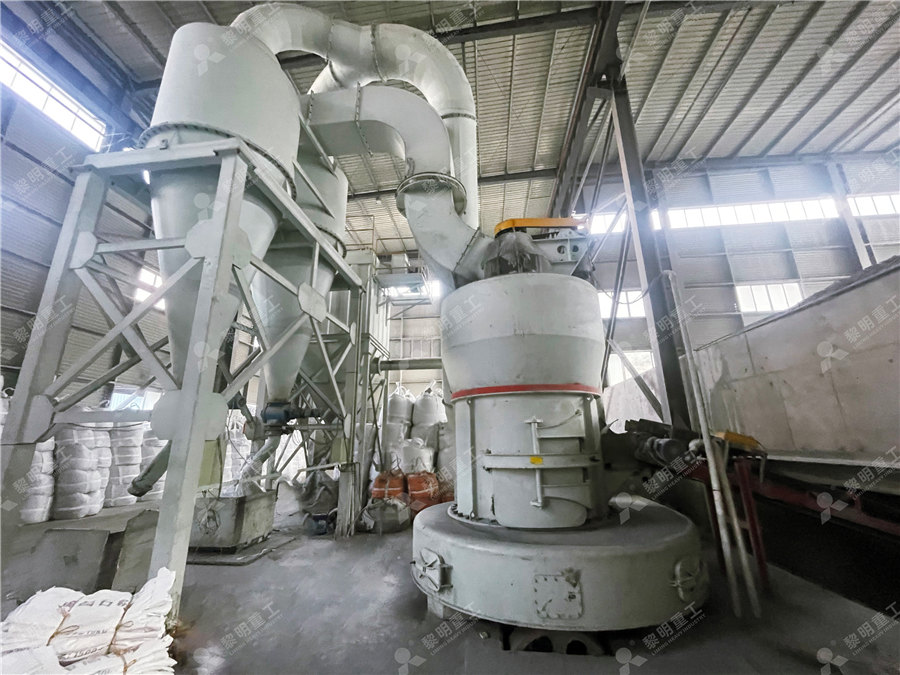
The Effects of Blasting on Crushing and Grinding Efficiency and
This paper examines the role blasting plays in optimum crushing and grinding with the emphasis on energy reduction The role of different blasting energy input on fragmentation is studied, and related to needs at the plant The effect of different feed sizes on energy consumption in 2023年11月1日 This paper demonstrates the feasibility of using a ceramic medium stirring mill to reduce the energy consumption of grinding operations through an industrial verification Energy conservation and consumption reduction in grinding 2003年1月1日 This paper examines the role blasting plays in optimum crushing and grinding with the emphasis on energy reduction The role of different blasting energy input on fragmentation is studied,The Effects of Blasting on Crushing and Grinding 2024年9月1日 Energy consumption in highpressure grinding shows exponential relationship to the moisture and Fsp Lowest values of Wi were achieved for moisture between 2 and 4 Impact of HPGR operational pressing force and material moisture
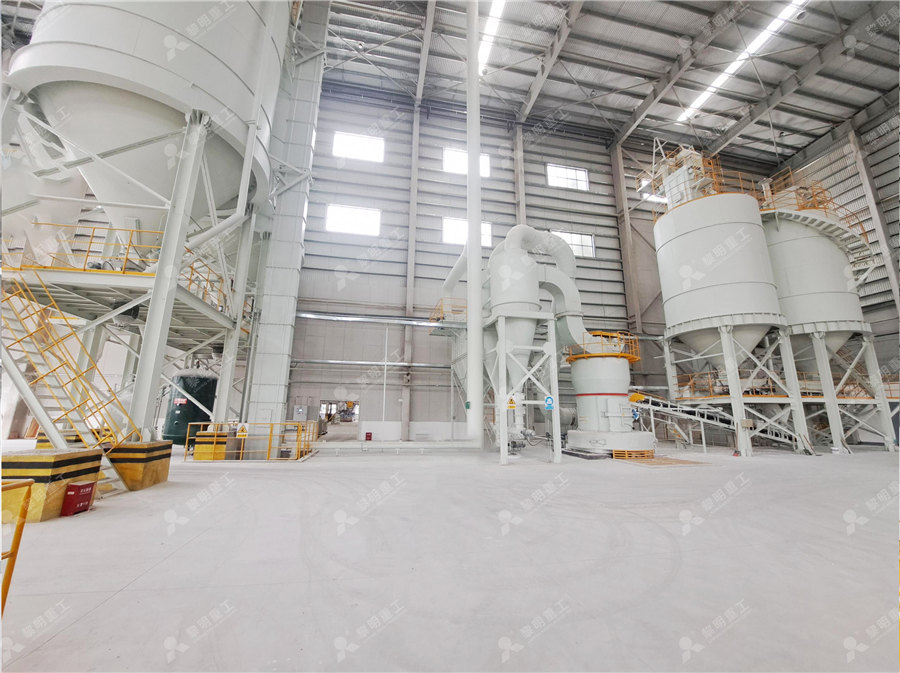
ANALYSIS OF ENERGY CONSUMPTION OF CRUSHING PROCESSES
This paper presents experimental comparison of two machine crushing technologies: onestage and twostage The study was carried on a m del doubletoggle jaw crusher which allows 2014年1月17日 Nielsen and Kristiansen investigated the effect of size distribution on crushinggrinding by examining site blasting operations and laboratoryscale blasting operations They Development of a model estimating energy consumption values The effect of different feed sizes on energy consumption in crushing and grinding is studied The role of microfracturing in this process is examined In the current environment, a policy of The Effects of Blasting on Crushing and Grinding Efficiency and 2017年1月27日 This paper presents experimental comparison of two machine crushing technologies: onestage and twostage The study was carried on a model doubletoggle jaw (PDF) Analysis of Energy Consumption of Crushing Processes
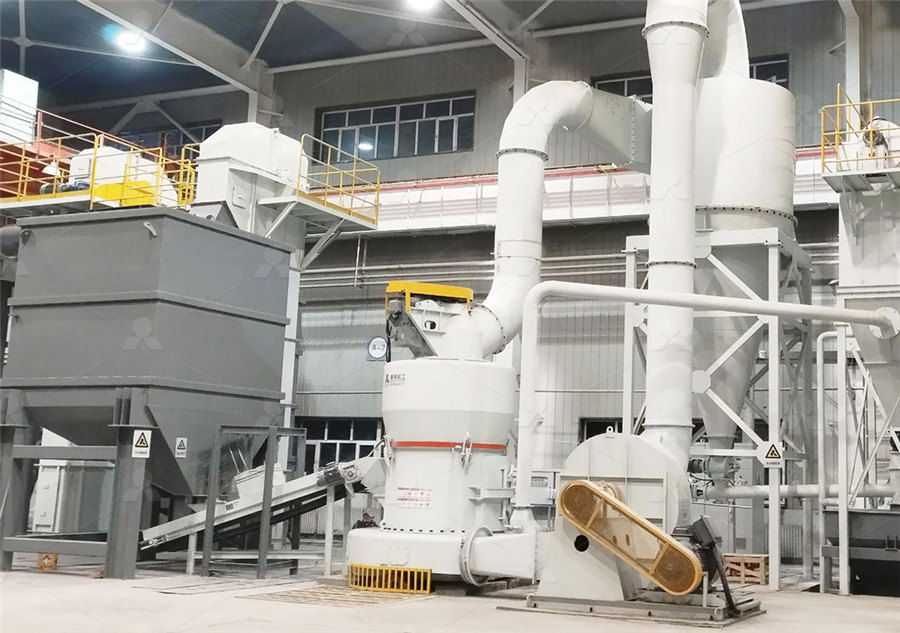
Energy consumption in fine crushing and dry rod grinding
Fine crushing and rod grinding have been investigated using a laboratoryscale jaw crusher and a rod mill The net energy consumption in both crushing and grinding was evaluated from torque Blasting has an important impact on mining and milling well beyond the necessary ability to dig and load the ore efficiently There is an increasing body of blasting research indicating The Effects of Blasting on Crushing and Grinding Efficiency and 2019年6月21日 Vertimills can operate with a minimum energy consumption of 20%, making them useful for regrinding and other applications with variable flows and, on average, they offer a 2530% reduction in Grinding down energy consumption in 2014年10月1日 This comminution process (Ballantyne and Powell, 2014; involves crushing and grinding to reduce fragment size This ore breakage process is energy intensive (Ballantyne and Powell, 2014) and also Benchmarking comminution energy consumption
.jpg)
Modeling and Improving the Efficiency of Crushing
2023年6月30日 energy consumption in order to cut the cost of the final product [3] The crushing process is widely used in the metallurgical, construction, and mining industries2013年12月18日 Fine grinding, to P80 sizes as low as 7 μm, is becoming increasingly important as mines treat ores with smaller liberation sizes This grinding is typically done using stirred mills such as the Isamill or Stirred Media Detritor While fine grinding consumes less energy than primary grinding, it can still account for a substantial part of a mill’s energy budget Overall Energy Use of Fine Grinding in Mineral Processing2021年6月10日 Indeed, innovation to reduce energy consumption in comminution is considered significant enough to be the focus of Natural Resources Canada’s Crush It! Challenge, which boasts a top prize of CA$5 million for the team that demonstrates the best energy breakthrough in crushing and grindingCrushing Energy Efficiency North American Mining Magazine2014年1月1日 The total specific grinding energy of crushed kernels (the sum of crushing energy and grinding energy) ranged from 476 to 1005 kJkg−1 and from 446 to 853 kJkg−1 for hard and soft wheat SOME PHYSICAL PROPERTIES OF CEREAL GRAIN AND ENERGY CONSUMPTION OF GRINDING
.jpg)
Crushing and Grinding Process JXSC Machine
2019年10月8日 The crushing and grinding operations are an important part of the processing of mineral resources, and it is also operation with high investment and high energy consumption In the case of metal mines, equipment investment in crushing operations accounts for 65% to 70% of the total plant value, power consumption is about 50% to 65%, and steel consumption is as 2019年11月14日 With the modern manufacturing industry evolving and advancing and amid a more energy conscious society, high energy demand in manufacturing—particularly in machining—has drawn more and more attention Accurate energy consumption modelling is critical to the improvement of energy efficiency in machining In the existing energy models of Energy consumption model for milling processes considering From the breakdown of energy consumption, it was found that comminution accounts for 25% of final energy consumption of an “average” mine site Diesel in mobile equipment accounts for 46%, electricity in mining (ventilation) 15% and other electricity 14% These are averages based on the different splits of energy consumption that wereMINING ENERGY CONSUMPTION 年1月1日 In times of unstable market development due to the energy system transformation and legislative measures concerning the reduction of CO 2 emissions, the manufacturing industry is increasingly aware of the ecological and economical importance of the factor energy A considerable share of industrial energy and resource consumption can be attributed to Energy efficiency of stateoftheart grinding processes
.jpg)
Impact of HPGR operational pressing force and material moisture
2024年9月1日 Crushing and grinding operations are the basis of raw materials processing and can be characterized with very high energy consumption at relatively low breakage effectiveness It is estimated that approximately 10 % of energy input in comminution equipment is consumed on size reduction (Legendre, 2014), while the remaining part is dissipated and lost or converted to 2013年1月1日 The impact of feeding rate on specific energy consumption of grinding hybrid willow with 115% of moisture content and grinder screen of 4 mm Figures uploaded by Ladan J Naimi Author contentDevelopment of Size Reduction Equations for 2022年6月1日 Ajwain (Trachyspermum ammi L) is an Ayurvedic and medicinal spiceAjwain possesses ample therapeutic constituents along with its exceptionally good qualities such as its strong aroma and pungent taste [1]Ajwain is one of the principal components in pharmaceuticals, functional foods, nutraceutical beverages and cosmetics [2]Ajwain has various food, Grinding characteristics and energy consumption in cryogenic 2023年5月16日 Over the last few decades, the demand for energyefficient mineralprocessing methods has continued The necessity to develop energyefficient technologies for the mineral industry will increase in the future, considering the exhaustion of highquality resources and severe environmental limitations The subject of this study is crushing equipment It is a Modeling and Improving the Efficiency of Crushing Equipment
.jpg)
Assessing the energy efficiency of a jaw crusher ScienceDirect
2014年9月1日 The aim of the present work is to understand the reasons for inefficiency and to improve the efficiency of comminution machinery Bond’s Work index coefficients cover almost the entire range of particles to be processed using commercial equipment [4]With this theory, the energy requirements are based on experimental shaft energy measurements of comminution accounted for approximately two per cent of the total US electricity consumption The specific energy requirements (in kWh/t) were supplied by Battelle Columbus Laboratories (1976) throughTitle: Benchmarking comminution energy consumption for theEnergy Consumption in Crushing and Grinding The energy input to size ore fragments is large Overall reduction, performed in a series of stages may be from an eighty percent feed size passing of 40 cm (158 inches) to a final product size of 270 to 325 mesh (053 to 045 mm)The Effects of Blasting on Crushing and Grinding Efficiency and Energy 2014年10月1日 There are some researches on energy consumption of crusher In terms of disc crusher, JM Zuñiga 3 calculates the total energy consumption of disc crusher by studying the dynamics of parts In terms of cone crusher, Liu 4 puts forward an energy consumption model, which shows the influence of working conditions and structural parameters of crushing Establishment of energy consumption model and multiobjective
.jpg)
Development of a model estimating energy consumption values
2014年1月17日 Most of the costs in open pit quarry operations occur in crushing and grinding processes Therefore, the management of crushing–grinding processes is very important Many researchers investigated the effects of pile size distribution and specific charge values occurring as a result of blasting on crusher energy consumptions and provided some cost reductions in analysis of the results shows that taking into account energy consumption, it is better to use twostage crushing process For given materials energy consumption in the twostage crushing process was reduced by 30% Key words: rock crushing, jaw crusher, crushing efficiency, two stage crushing process 1 INTRODUCTIONANALYSIS OF ENERGY CONSUMPTION OF CRUSHING energy consumption, and in [10], in the context of process kinematics Work [11] proposes a fundamental model that serves as a universal tool for modeling jaw crushersModeling and Improving the Efficiency of Crushing Equipmentminimum to be twothirds of the way from the best practice energy consumption to the theoretical minimum energy consumption3 To reflect more inclusive energy savings, the bandwidth analysis used tacit energy values of electrical energy consumption (ie, generation and distribution losses are factored in addition toUS Mining Industry Energy Bandwidth Study
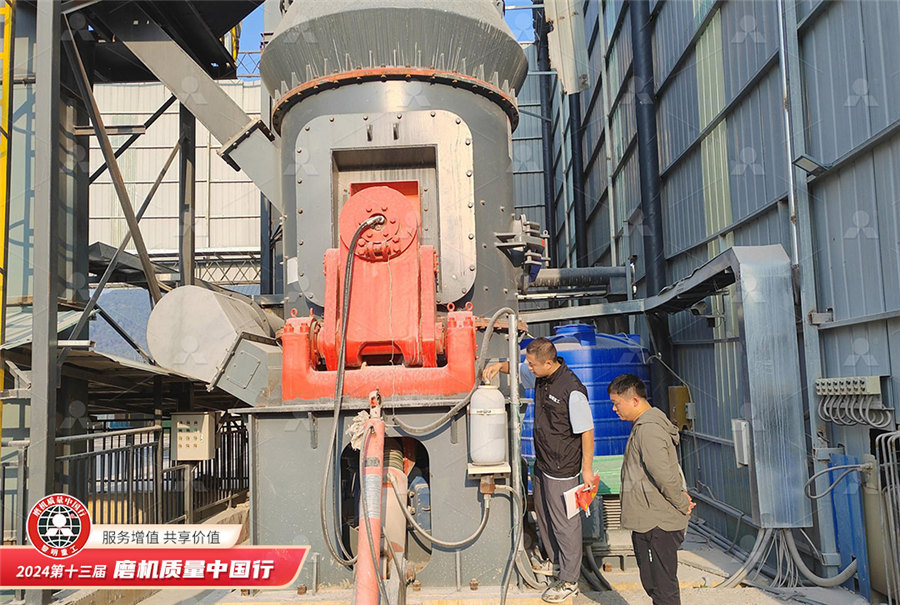
Predicting the overall specific energy requirement
2009年5月1日 The characteristic particle size D80 gradually decreased and the reduction ratio gradually increased with the increase in specific energy consumption The specific energy consumption of high Breaking Down Energy Consumption in Industry Grinding Mills J Bouchard (1), G LeBlanc (2), M Levesque (3), P Radziszewski (4) and D GeorgesFilteau (1) 49th Annual Canadian Minerals Processors Conference, Ottawa, Canada, 2017 ABSTRACT Grinding mills are infamous for their extremely low energy efficiencyBreaking Down Energy Consumption in Industry Grinding MillsFrom the breakdown of energy consumption, it was found that comminution accounts for 25% of final energy consumption of an “average” mine site Diesel in mobile equipment accounts for 46%, electricity in mining (ventilation) 15% and other electricity 14%MINING ENERGY CONSUMPTION 2021 CEEC (Coalition for Eco Fine crushing and rod grinding have been investigated using a laboratoryscale jaw crusher and a rod mill The net energy consumption in both crushing and grinding was evaluated from torque measurements An empirical relationship was established between energy consumption, particle size and operating parameters When the mill feed size is reduced, through fine crushing, to Energy consumption in fine crushing and dry rod grinding
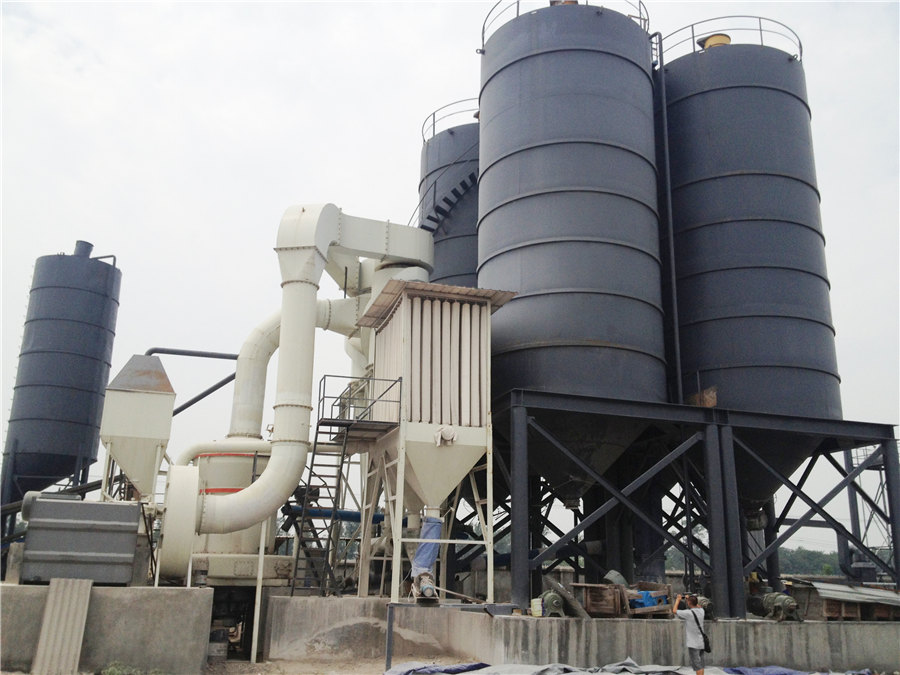
Energy consumption model and energy efficiency evaluation
2017年6月15日 Process energy efficiency is the ratio of the effective energy consumption of a manufacturing process or a period time and the total energy input of a mechanical manufacture system Because CNC continuous generating grinding machine tool is mainly used for grinding metal, its effective energy consumption refers to the grinding energy2023年12月16日 The energy dissipation under high gas pressure conditions was found to be dominated by crushing energy, whereas under The release and consumption of energy during an outburst are 982, and 16,571 J, accounting for 332%, 37%, and 631%, respectively The residual kinetic energy accounted for a relatively large Energy Evolution and Coal Crushing Mechanisms Involved in Coal 2017年1月27日 It was revealed that the greatest energy consumption during the operation of crushers goes into the kinetic energy of the crushing plates and the potential energy of deformation of the springs(PDF) Analysis of Energy Consumption of Crushing Processes minimum to be twothirds of the way from the best practice energy consumption to the theoretical minimum energy consumption3 To reflect more inclusive energy savings, the bandwidth analysis used tacit energy values of electrical energy consumption (ie, generation and distribution losses are factored in addition toUS Mining Industry Energy Bandwidth Study Department of Energy
.jpg)
Enzymeassisted mechanical grinding for cellulose
2018年10月10日 Grinding energy consumption of bagasse fibers was significantly lower than softwood, by 731%, and enzyme pretreatment further improved the energy efficiency, by 5971%, Therefore, the idle energy crushing, milling, agitation, burning, grinding and bagging operations The total energy evaluation was based on the three primary energy sources which include electrical, combustion and human The total estimated energy intensities were 6545 MJ/ton and 4197 MJ/ton for wet and dry processes respectively The percentage consumption of energy inEnergy and Cost Analysis of Cement Production Using the Wet 2024年3月11日 Sustainable grinding refers to using environmentally and socially responsible methods in grinding materials Grinding is a mechanical process that involves the reduction of the size of particles or materials, often to create powders or finely ground substances [1, 2]Sustainable grinding aims to minimize energy consumption during the processTowards Sustainable Grinding of DifficulttoCut Alloys—A 2023年12月1日 We find that the mining industry is currently responsible for approximately 17% of global final energy consumption However, the mining industry’s final energy consumption is likely to increase significantly, by a factor in the range 2–8 by 2060, depending on the future economic trajectory, on the evolution of energy intensities, and on future recycling ratesGlobal energy consumption of the mineral mining industry:
.jpg)
Energy Efficiency Measurement of Mechanical Crushing Based on
2024年6月28日 assesses the energy efficiency of crushing equipment by measuring its energy consumption during the crushing process, which illustrates that the crushing and grinding of particles2016年11月22日 Energy consumed during grinding process will raise the grinding zone temperature Therefore, all influential factors on grinding force will in turn affect the thermal performance of grinding The grinding zone temperature elevation is dependent on the grinding efficiency and the proportion of grinding energy that enters the workpieceEffect of different parameters on grinding efficiency and its 2018年5月1日 The prediction models of energy consumption (Ecs) and grinding energy efficiency (η) were established respectively with the operating parameters (loading pressure, rotation speed and moisture Influence of Operating Conditions and Crushing Chamber on Energy 2016年1月18日 The rising awareness of energy consumption and the environmental impact of manufacturing underline the need to implement structured approaches, such as a life cycle assessment, or metrics for process evaluation Energy savings on their own are not sufficient to increase the process efficiency of industrial finishing operations, since the results, in terms of Qualityconscious optimization of energy consumption in a grinding
.jpg)
(PDF) An industrial comparative study of cement clinker grinding
From Table 2 it can be seen that the combined grinding system had the least specific energy consumption (306 kWh/t), followed by the HPRMonly system (340 kWh/t) and the horizontal roller mill system (373 kWh/t) The HPRM circuit in the combined grinding system accounted for about 60% of the measured total energy (kWhours) consumption2023年8月14日 Grinding is a critical surfacefinishing process in the manufacturing industry One of the challenging problems is that the specific grinding energy is greater than in ordinary procedures, while energy efficiency is lower However, an integrated energy model and analysis of energy distribution during grinding is still lacking To bridge this gap, the grinding time Energy Prediction Models and Distributed Analysis of the Grinding