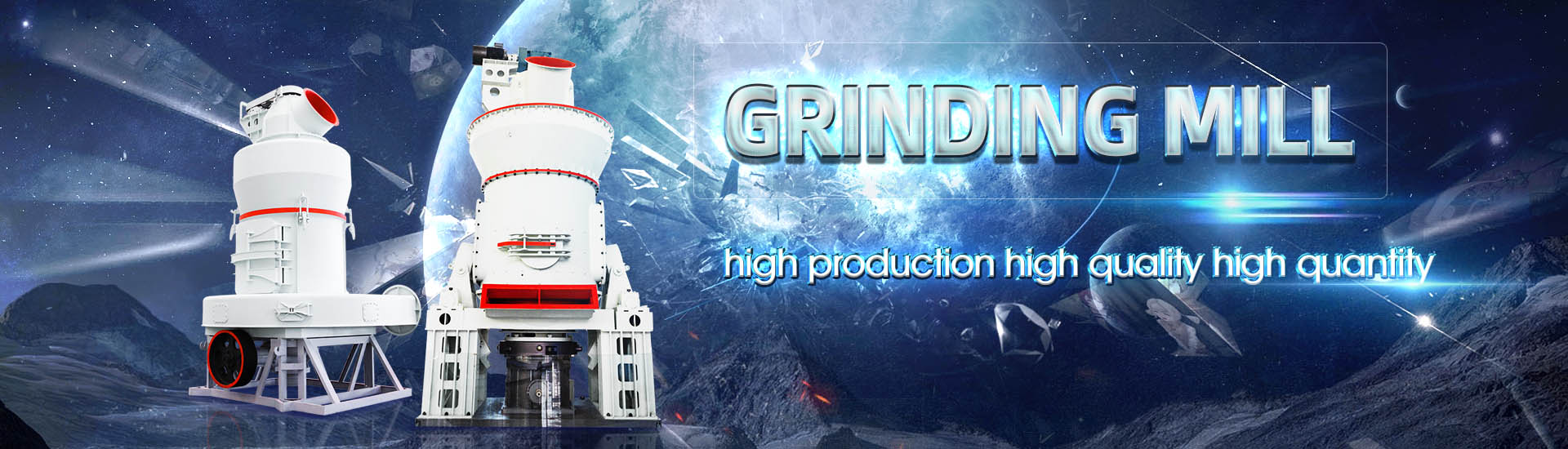
Air leakage from cold slag hopper of 1050 tons pulverized coal furnace in power plant
.jpg)
Effect of air ingress on the energy performance of coal fired
2007年7月1日 This paper presents the effects of air ingress in the combustion zone, postcombustion zone and air preheater (APH) on the energy efficiency and loading capacity of a 2023年7月1日 Coalpulverized power plants need frequent and deep peaking in new energy impact So it is imperative to study the heat exchange between bottom ash and air to reduce Study on heat transfer characteristics of aircooled dry bottom ash 为避免漏风问题,提出一种新型间接水冷干排渣方式,采用数值模拟的方法研究了新排渣方式下,底渣的运动状态和冷却效果,对比了新排渣方式和传统排渣方式的优缺点,结果表明:新排渣方式在运 Research on Dry Slagging Technique of WaterCooled Scraper in 2024年2月3日 Fine slag (FS) is an unavoidable byproduct of coal gasification FS, which is a simple heap of solid waste left in the open air, easily causes environmental pollution and has a Multiscale analysis of fine slag from pulverized coal gasification in
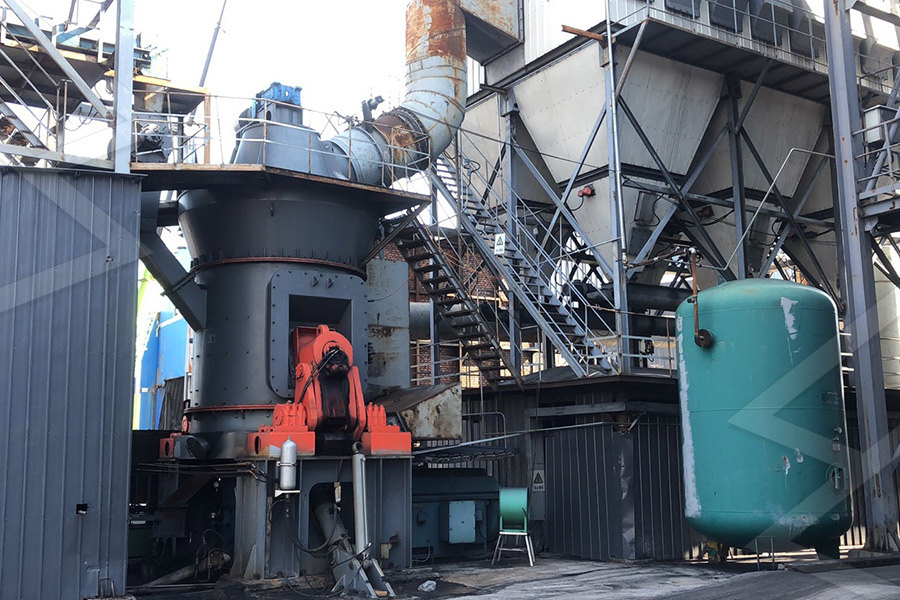
Characterization of unburned carbon separated from power plant
2020年2月1日 This article presents the results of slag property studies, for characterization of unburned carbon separated Size composition and lossonignition distribution as a function of Pulverized coal combustion (PCC) is the most widely used technology for coal power generation In this process, coal is milled, pulverized, and injected in the boiler with air to allow Pulverised Coal Combustion an overview ScienceDirect TopicsExcessive ash deposits on a coalfired boiler’s heat transfer surfaces will reduce its efficiency, and in extreme cases a boiler can be shut down by ashrelated problems Ash deposits are known Slagging and fouling in coalfired boilers ICSC2021年11月15日 Chunlong Liu et al [4] have studied the excess air ratio in a pulverized coal 800 MW boiler They have concluded that at excess air low case, coal resident time inside the Optimization and Analysis of Design Parameters, Excess Air Ratio,
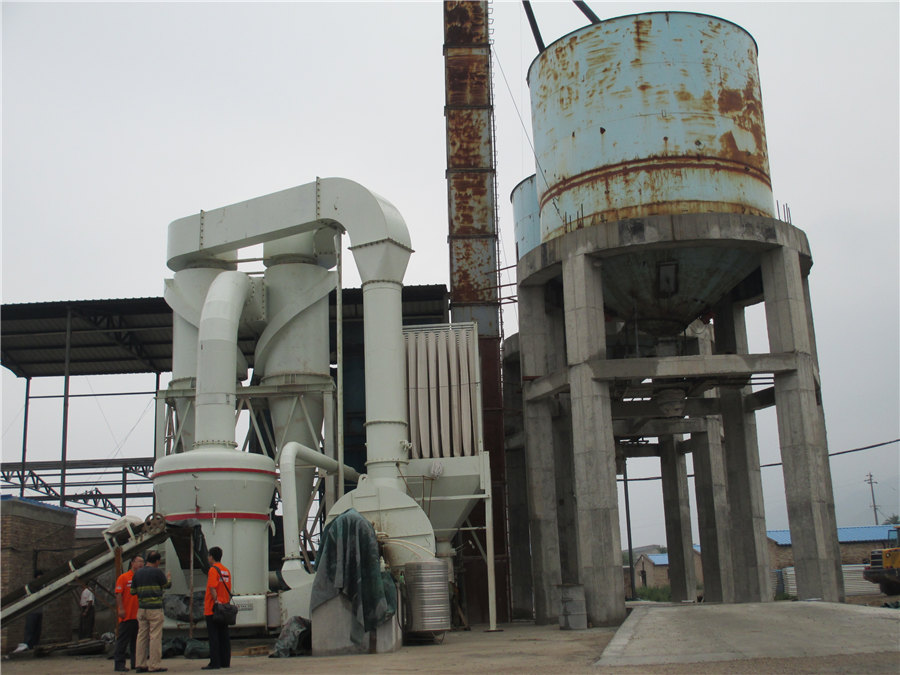
AirStaged Combustion Characteristics of Pulverized Coal under
2014年2月10日 The results indicate that, to maximize NO x removal efficiency by airstaged combustion, the reducing zone should be under high temperature and strong reducing 2011年10月19日 This study analyses the thermodynamic performance of an existing 625 MWe conventional Rankine cycle power plant using pulverized coal firing (PF) (reference plant with Thermodynamic analysis of a coalfired power plant repowered 2021年11月15日 This work discusses the supercritical technology that has been instrumental in reducing pollution levels and quick load response from the thermal plant Various operating parameters such as main steam pressure and temperature; reheat steam pressure and temperature; excess air ratio for a given fuel, feedwater heater bleed steam pressure and Optimization and Analysis of Design Parameters, Excess Air Ratio, 2020年10月31日 The potential utilization of boiler slag generated in large amounts from pulverizedcoalcombustion (PCC) power plants has recently drawn much attention due to the serious problems caused to (PDF) Utilization of Boiler Slag from PulverizedCoal
.jpg)
Power 101: Improving the Performance of Boiler
2010年12月1日 The effects of APH air leakage on the flue gas flow rate and CO 2 concentration in the flue gas are presented in Figures 9 and 10 for a bisector APH installed on a typical 400MW power plant Pulverized Coal Furnace Water Turbine Electricity Pulverized coal is converted to electricity through the Rankine cycle: 1 The coal is blown into the furnace, becomes airborne, and is burned 2 The heat generated from the burning heats water flowing through tubes in the furnace 3 The water turns into pressurized steam which exits the The Production of Electricity Power from Coal University of The concept of burning coal that has been pulverized into a fine powder stems from the belief that if the coal is made fine enough, it will burn almost as easily and efficiently as a gas The feeding rate of the pulverized coal is controlled by computers, and is varied according to the boiler demand and the amount of air available for drying and transporting fuelPulverized coalfired boiler Wikipedia2021年3月1日 The biomass cofiring test was conducted at a pulverized coal power plant with a capacity of 300 MWe to determine the effect of cofiring on the operating parameters, such as Mill Outlet Cofiring characteristics of wood pellets on pulverized coal power plant
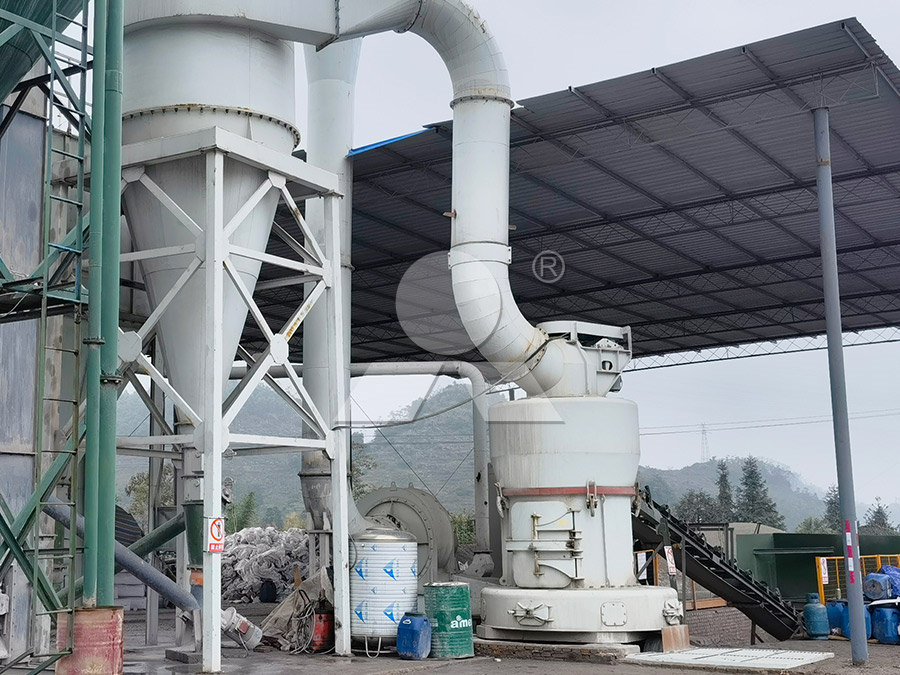
Developments in Pulverized CoalFired Boiler Technology
1996年4月10日 Exhaust gas temperature in coalfired power plants can reach approximately 120 °C to 140 °C, with the thermal energy accounting for approximately 3% to 8% of the total input energy2019年1月1日 Review of the investigations of pulverized coal combustion processes in 6 secondary air channel, 5 coal dust with Startup and Fire Stabilization in Thermal Power Plant Furnace (PDF) Review of the investigations of pulverized coal combustion 2023年7月1日 Furthermore, furnace nowadays primarily uses low nitrogen burners, and air leakage from the bottom of furnace affects the air distribution ratio and increases the generation of fuelbased NO X [16, 20] Coalpulverized power plants Study on heat transfer characteristics of aircooled dry bottom ash 2018年10月21日 Fig 1 Pulverized coal combustion and gas composition in raceway The extent of combustion (combustion efficiency), and hence the amount of unburnt material transported out of the raceway, depends on several parameters which include (i) properties of the coal, such as the VM content, particle size and density, and (ii) operating conditions, for example, blast gas Understanding Pulverized Coal Injection in Blast Furnace
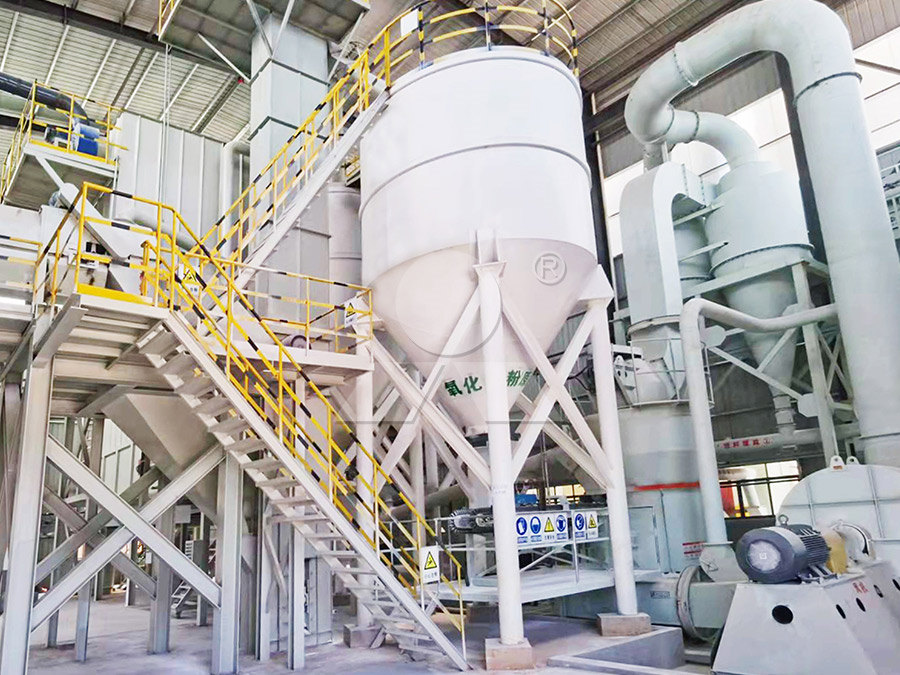
ANALYSIS ON MASS FLOW RATE OF FLUE GAS FOR A
2017年12月18日 In this paper, mass flow rate of flue gas at inlet outlet for pulverized coal power plant are analyzed with consecutive steps For this required coal input for a specific power generation is 2015年2月1日 Advanced coal plant emissions controls are the norm, and PRB coal is in use to some extent at most power plants in the US, and the Environmental Protection Agency (EPA) has proposed standards Understanding Coal Power Plant Heat Rate and 2022年8月1日 Fig 1 shows a simplified diagram of a typical PC plant Pulverized coal and air are combusted in the boiler to generate steam that flows to the HP, IP, and LP stages of the turbine to generate power After the condenser, the water flows through the FWH section before cycling back into the boilerPredictive modeling of a subcritical pulverizedcoal power plant 2022年3月15日 Recently, cofiring coal with the novel carbonfree fuel ammonia (NH 3) is proposed and recognized as a promising route for mitigating the CO 2 emission from the power plant [12]For the future production of ammonia fuel [13], the "blue ammonia" is supposed to be produced by using the CCS to bring the carbon emission of the production to zero and the Mitigating CO2 emission in pulverized coalfired power plant via
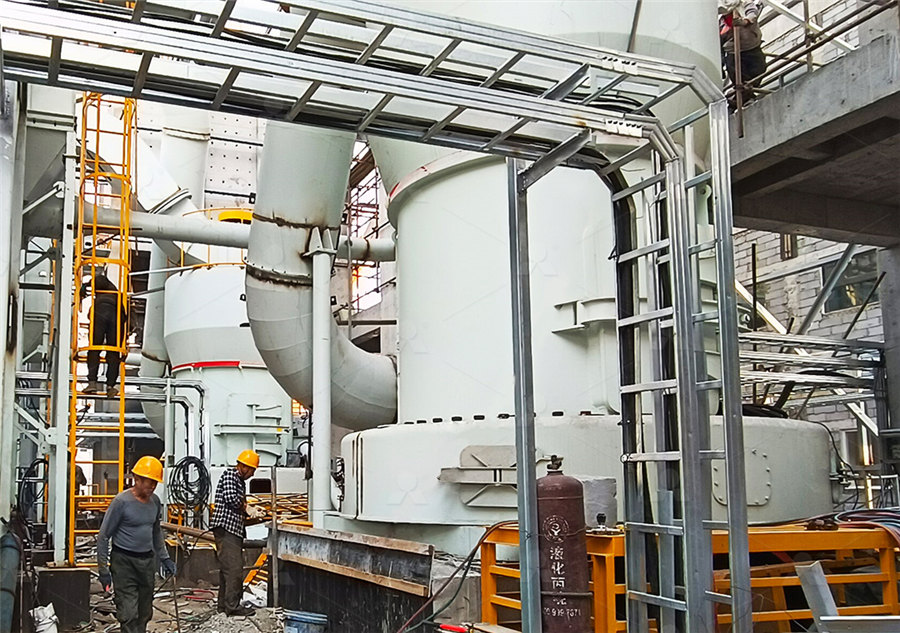
Pulverized Coal Injection of Blast Furnace Ironmaking
2024年1月1日 (3) Fixed carbon is one of the main bases for coal selection, and pulverized coal for blast furnace injection should have high fixed carbon content and carbon hydrogen ratio (4) The ignition point is the temperature when the coal is heated to combustion in the presence of oxidant (air) and pulverized coal, also called the ignition temperatureIn order to comply with the Clean Air Act Amendments of 1990, electric utilities could either switch to low sulfur coal, add equipment (eg, scrubbers) to existing coalfired power plants in order to remove SO 2 emissions, purchase permits from other utilities that exceeded the reductions needed to comply with the cap, or use any other means of reducing emissions below the cap, The Facts About Air Quality and CoalFired Power Plants2019年7月1日 CFD analysis of the combustion process in a boiler of a 160 MWe power plant: leakage influence air leakage into the furnace Brazilian pulverized coal type CE3100 was adopted as fuel, CFD analysis of the combustion process in a boiler of a 160 MWe power When pulverized coal is burned in a slagtap furnace, as much as 50 percent of the ash is retained in the furnace as boiler slag In a cyclone furnace, which burns crushed coal, 70 to 85 percent of the ash is retained as boiler slag (NETL 2006) The American Coal Ash Association (ACAA) (ACAA 2007) estimates that during 2006, theUSER GUIDELINE FOR COAL BOTTOM ASH and BOILER SLAG IN
.jpg)
Technical feasibility of a 1000 MWe pulverized coal power plant
2024年3月1日 Ammonia has attracted the attention as a practical way to reach carbon free power generation Ammonia cocombustion characteristics in 1000MWe pulverized coal power plant was simulated by using Aspen Plus and evaluated under an excess air ratio of 10–12, air of 2642–3457 ton/hr, coal of 2082–3555 ton/hr, ammonia of 0–18614 ton/hr and various coalsA 2000 MW power station could be handling coal in the range of 1600 tons/hr or around 12 million tons of coal annually A single 500 MW unit consumes in the range of 400 tons/hr of coal The coal input to the boiler of the power plant passes through three different phases before combustion in the boilerWhy Pulverized Coal is Used in a Power Plant Bright Hub power generation in 2019, accounting for 502% of the world's total power generation by coalfired power plants Many power plants consider various aspects to improve power generation efficiency and reduce environmental pollution caused by coal burning Among them, the rotary air preheater has a good effect (hereinafterResearch on Ash Clogging of Rotary Air Preheater in Coalfired Power Plant2024年7月9日 Gasification technology enables the clean and efficient utilization of coal However, the process generates a significant amount of solid waste—coal gasification slag This paper focuses on the Jinhua furnace coal gasification Composition and Structural Characteristics of Coal
.jpg)
CFD analysis of the combustion process in a boiler of a 160 MWe power
2019年6月15日 This paper presents a developed and validated CFD model of a boiler with the objective of studying a presumed defective actual operating condition, that is, air leakage into the furnace Three cases were assessed, concerning the amount of air leakage across the boiler water seal The base case considered the actual operational condition of 5% air leakage Case 2022年7月27日 Coalfired thermal power plants (TPPs) still make a significant contribution of 40% to energy production [1, 2]A substantial share of coal fuel in electricity generation is due to large world reserves of 1,055 billion tons and competitively low prices []One of the most important stages of TPP launch is the startup and heating of the boiler to the installed minimum Plasma Ignition System to Start Up Pulverized Coal Boilers 2008年10月1日 In the IPCC 1 Special Report on CO 2 capture and storage it is already discussed that adding CO 2 capture to a pulverized coal fired power plant will result in a reduction of net generating efficiency and will proportionally increase 2: emissions to air of substances not affected by the capture process, the use of resources (limestone and ammonia for respectively Life cycle assessment of a pulverized coal power plant with post 2007年3月1日 A pulverized coal preparation system is one of the indispensable main systems for coalfired boilers in thermal power plants and its operation safety, reliability and costeffectiveness directly Causes of pulverizedcoal leakage from a race pulverizer and its
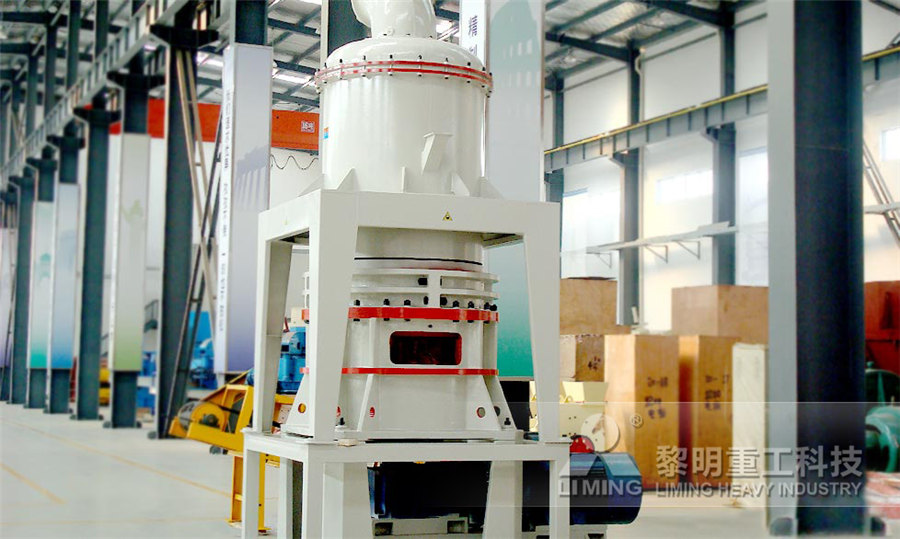
Advantages and Disadvantages of Pulverized Coal Firing
2022年11月27日 In a pulverized coal firing system, coal is ground into fine particles and blown into a furnace, which is burned to generate heat This type of system is typically used in power plants and is designed to provide a high level of heat input to the boilercast abrasionresistant liners and partially filled with hardened steel balls Coal and preheated primary air enter one or both ends of the mill from a crusher/dryer or feeder As the mill rotates, the balls cascade and pulverize the coal by impact and attrition The pulverized coal is then conveyed by air to centrifugal classifiersA Comparison of Three Types of Coal Pulverizers Babcock Power2023年1月13日 Exemplary scheme of a dust duct (gas: air; INLET 1: air temperature of 100°C; air flow rate of 27 m/s; INLET 2: air temperature of 20°C; air flow rate of 20 m/s; isopropanol particle diameter (PDF) Pulverized CoalFired Boilers: Future Directions of Scientific 2020年9月11日 Schematic of pulverized coal injection in the lower part (lanceblowpipetuyereracewaycoke bed) of a BF [49] Technological advancements in evaluating the performance of
.jpg)
Life cycle assessment of postcombustion carbon capture and
2024年6月1日 In this paper, different emerging postcombustion technologies, ie, monoethanolamine (MEA), aqueous ammonia, pressure swing adsorption (PSA), temperature swing adsorption (TSA), membrane and calcium looping, were applied to an ultrasupercritical coalfired power plant for carbon capture A ‘cradletograve’ life cycle assessment (LCA) was 2023年6月15日 (3) Fixed carbon is one of the main bases for coal selection, and pulverized coal for blast furnace injection should have high fixed carbon content and carbon hydrogen ratio (4) The ignition point is the temperature when the coal is heated to combustion in the presence of oxidant (air) and pulverized coal, also called the ignition temperaturePulverized Coal Injection of Blast Furnace Ironmaking2010年12月1日 CFD Analysis of the Pulverized Coal Combustion Processes in a 160 MWe TangentiallyFiredBoiler of a Thermal Power Plantpdf Available via license: CC BYNC 40 Content may be subject to copyrightCFD Analysis of the Pulverized Coal Combustion 2017年1月1日 Most of the people in this world are concerned about the environmental impacts of coal based power plants Coal fired power plants are one of the sources of SOx, NOx and mercury emissions(PDF) Coal Fired Power Plants: Emission Problems and
.jpg)
SAFETY GUIDELINES FOR IRON STEEL SECTOR BLAST FURNACE
vi) Slag Granulation Plant (SGP) / Slag Dumping Yard: During the process of iron making, the impurities are fluxed and removed as slag The hot liquid slag is made into slag granules by means of high pressure water jets in the Slag Granulation Plant in the Cast House itself (sometimes separate SGP is located at a distance from the furnace proper)2024年7月1日 The development of cofiring of biomass technology provides a good idea to solve this problem In previous years, numerous researchers have extensively studied the feasibility and adaptability of cofiring biomass in coalfired boilers [5, 6]Oladejo et al [7] found that by cofiring Yunnan coal with oat straw and rice hulls at a biomass mixing ratio of 30 wt%, a significant Numerical simulation of the cofiring of pulverized coal and 2013年12月1日 1 Introduction World coal consumption will increase by 50% in 2008–2035, mainly due to the nonOECD countries, and the participation of coal in world energy consumption will remain flat about 28% over the same period, as stated in IEO 2011 reference case [1]Furthermore, power plants of pulverized coal are the largest suppliers of electricity in the Numerical study of a 350 MWe tangentially fired pulverized coal furnace 2011年7月6日 Use of Cold Air Velocity Test (CAVT) to Locate Erosion Prone Zones in Pulverized Coal Fired Utility Boiler July 2011 Conference: World Congress on Engineering 2011(PDF) Use of Cold Air Velocity Test (CAVT) to Locate Erosion Prone
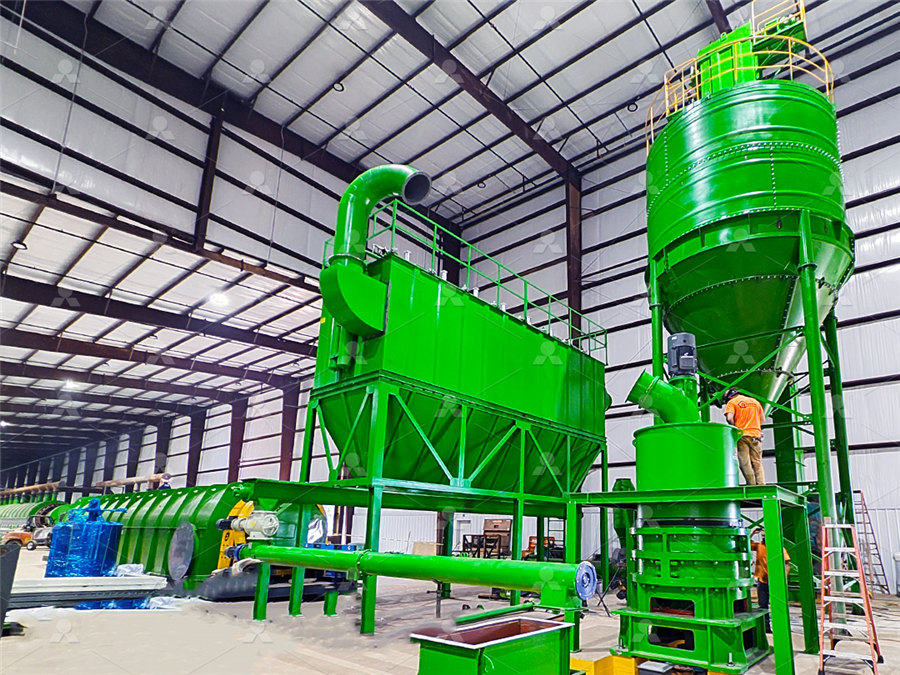
Predicted formation and deposition of slag from lignite
Moh power plant is a steam power plant that utilizes this lignite as fuel Its pulverized coal boilers are generating electricity with the total capacity of 2,400 MW, accounting for about 12% of the national electricity consumption The fuel consumption is about 1517 million tons per year, obtaining from the Mae Moh mine2021年5月1日 The purpose of this work is to evaluate how blast furnace slag composition changes when fossil‐based coke is replaced with bio‐coke and pulverized coal is replaced with charcoalEffect of Coal and Coke Ash on Blast Furnace Slag Properties: A