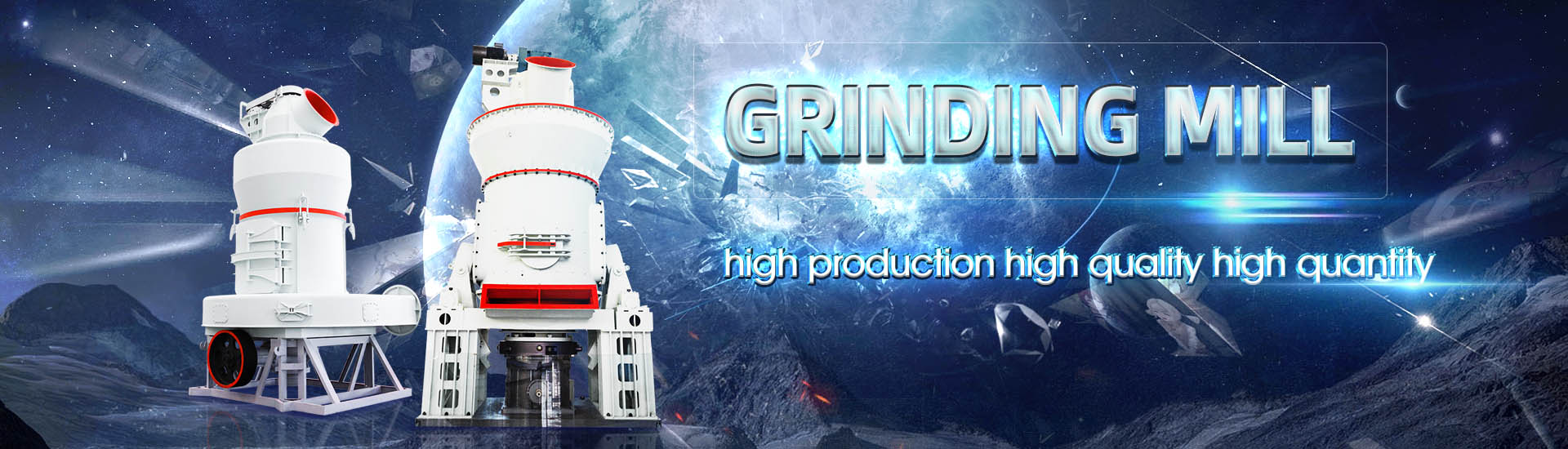
Dry grinding and flaking separation principle
.jpg)
A comprehensive review and recent advances in dry mineral
2023年10月1日 Dry mineral processing methods are classified broadly into size reduction (comminution) and separation Dry separation uses forces generated by gravity, centrifuges, 2019年9月1日 Dry grinding consumes higher energy and produces wider particle size distributions compared with wet grinding It significantly decreases the rate of media A comparative study on the effects of dry and wet grinding on This paper will try to answer the WHY, WHAT, and HOW of attrition fine dry milling using Attritors in continuous or batch type modes The principle of Attritor dry grind processing is achieved by Attrition Dry Milling In Continuous And Batch Modes Union 2022年2月28日 Compared to the wet grinding method, dry grinding requires more energy and time to achieve a particular particle size distribution Consequently, parts of this required Grinding SpringerLink
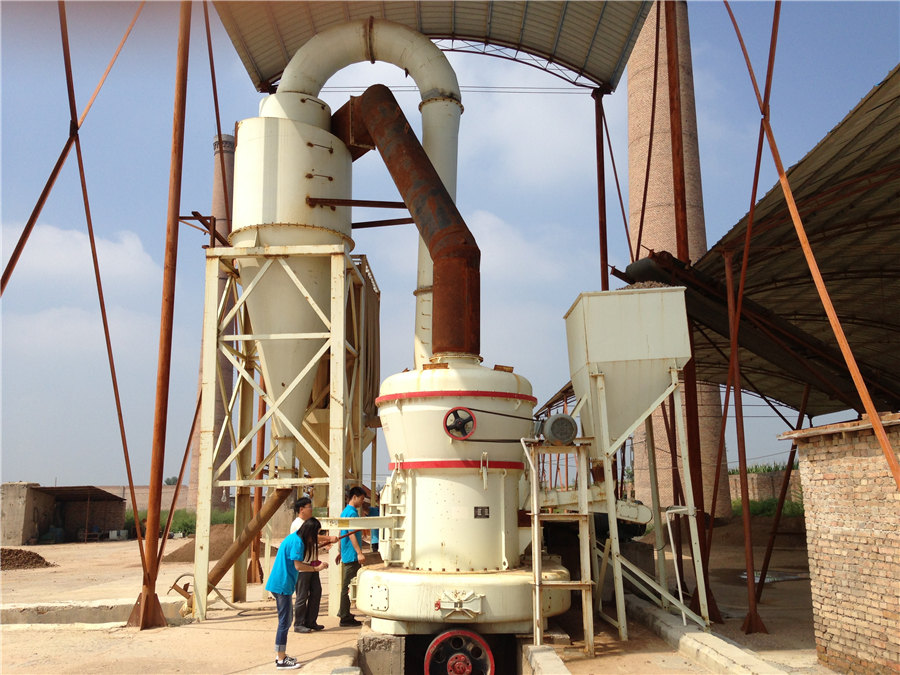
Principles of Modern Grinding Technology ResearchGate
2013年1月1日 Principles of Modern Grinding Technology explains the principles that led to rapid improvements in modern grinding technology over recent decades Removal rates and quality Drying and cooling After the flaking roller mill, hot air is passed through the warm and damp flakes to dry them and achieve the desired final moisture content, after which they are cooled down Machines and steps for the flaking process Streckel SchraderDry grinding, a sustainable process, achieves rapid workpiece material removal by increasing the spindle speed of the machine tool, relying on the removal of heat through chip formationDry Grinding an overview ScienceDirect Topics2020年3月18日 Wheat grain milling has for aim to isolate the smaller starchy endosperm particles (ie flours, semolina) from the larger fragments of peripheral tissues The mechanical Understanding the Mechanics of Wheat Grain Fractionation and
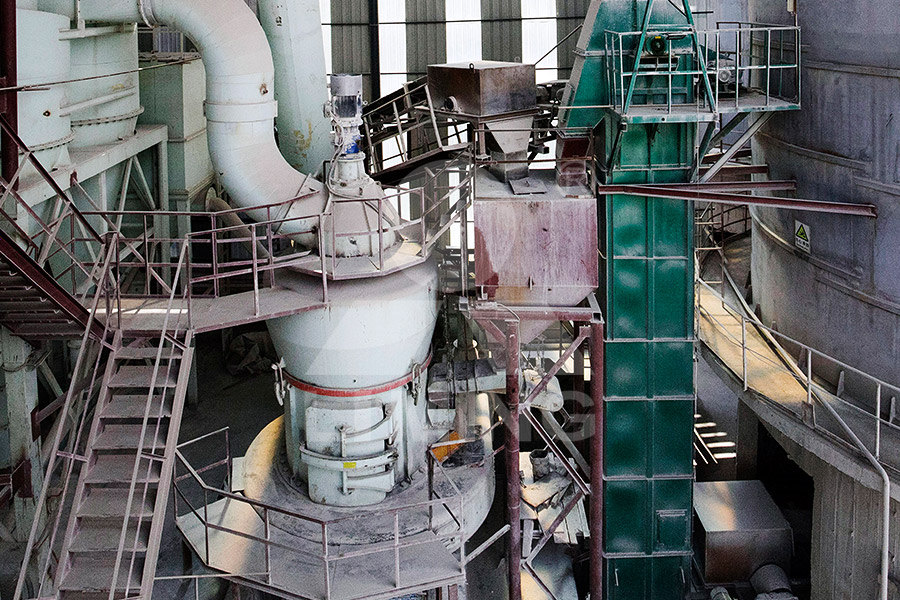
Dry Permanent Magnetic Separator: Present Status and Future
2022年9月9日 Dry magnetic separation is mainly applied to discard nonmagnetic gangue prior to the grinding of iron minerals, cut the volume of pregrinding materials, and reduce grinding June 2022; ARCHIVE Proceedings of the Institution of Mechanical Engineers Part C Journal of Mechanical Engineering Science 19891996 (vols 203210) 236(2):1107(PDF) A comprehensive review on the grinding process: 2021年9月28日 The principle of grinding precision machining: During dry grinding, generally no or only a small amount of lubricating abrasive is applied It is generally used for the fine grinding of planes, and the production efficiency What Is Grinding and Its Working Principle and Type?2023年11月20日 Grinding Principles Types of Grinders Types of Grinding Balls Density of Grinding Balls Ball mills and grinding balls Ball mills and grinding balls are divided into dry and wet grinding Types, selection, and working principles of grinders
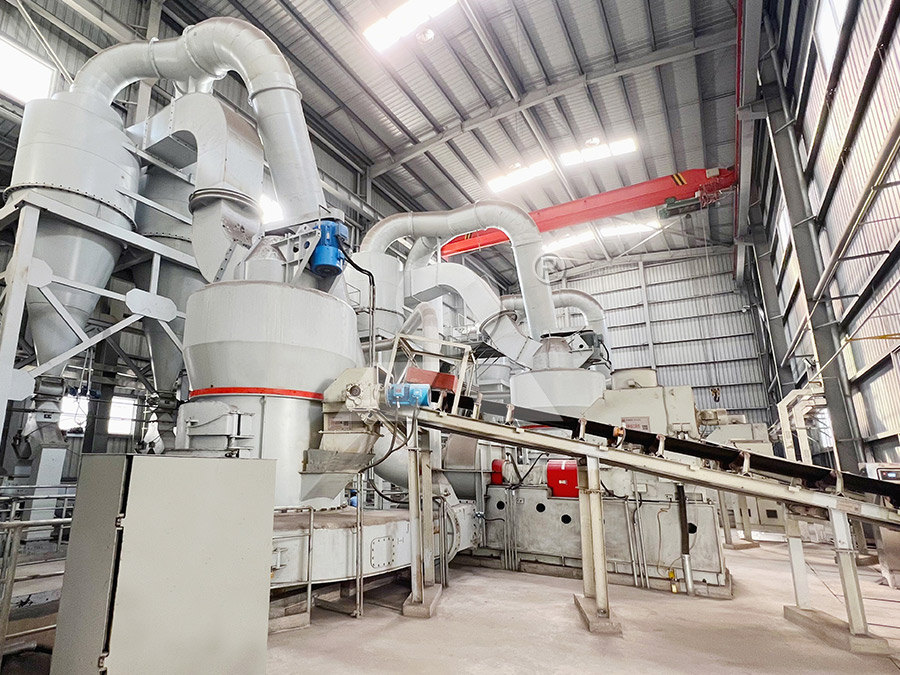
introduction of new type iron ore grinding and dry separation
dry process is low, which can be reduced by 3050% Features Small footprint, modular design, fast installation and movement The production cost per ton of fine powder is greatly reduced, which makes some lean iron ores economical Dry grinding process is short, avoid over grinding, no magnetic agglomeration ore grade is high 5 6 8 7 9 New 2018年2月14日 The most common cereal processes include dry milling (wheat and rye), pearling (rice, oat, and barley), wet milling (corn and wheat), and malting (barley, corn, and wheat)(PDF) 1 Introduction to cereal processing and byproductsFlaking roller mill type FWS Production of grain flakes After the flaking roller mill, hot air is passed through the warm and damp flakes to dry them and achieve the desired final moisture content, after which they are cooled down using cold air Control sieve type KSMachines and steps for the flaking process Streckel Schrader2019年2月5日 Companies such as KHD, who deal in dry separation equipment, have produced several commercially used airbased classification systems including the V separator and SKS dynamic cage wheel separatorCase Study of Dry HPGR Grinding and Classification in Ore Processing
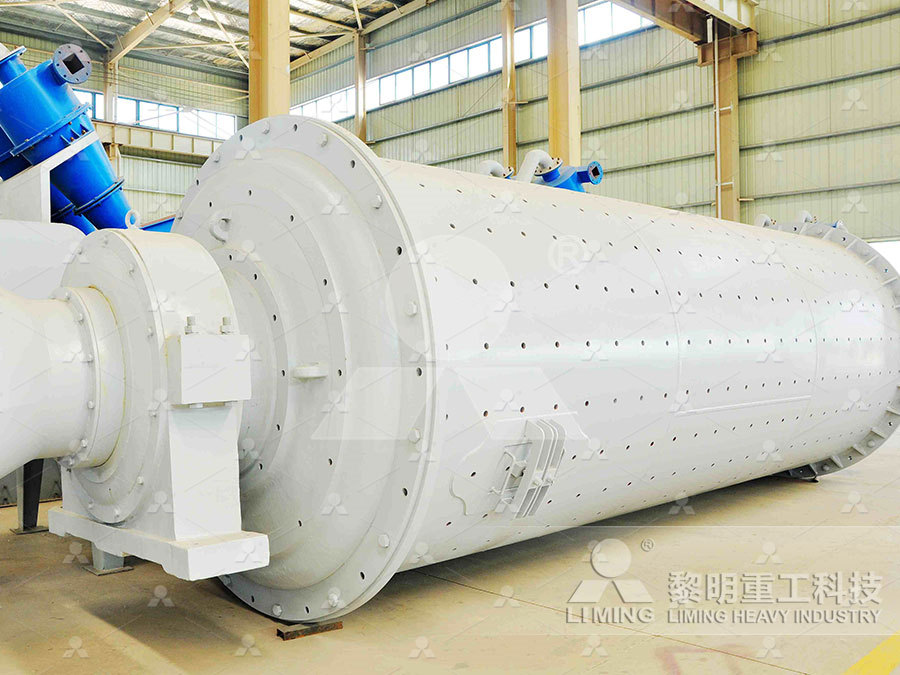
Classification of Materials and Types of Classifiers IspatGuru
2015年10月31日 Based on their separation principles, classifiers are classified into two major types This classifier can be integrated into a conventional closed or open dry grinding circuit It can also be utilized in a classification only system complete with Dry Ginger Grinding Machine: Dry Ginger grinding machine is a grinder used to grind the dry ginger into powder between 1cm to 300mesh We have small and extra large dry grinding machine LINKER grinding machine can customize small Dry Ginger grinding machine or large grinding machine as to your requirementWhat is the difference between wet grinding and dry grinding?2020年9月20日 The inconsistencies of these studies may be explained by a study of Prziwara et al [54] on the impacts of grinding aids on the dry stirred milling of limestone: The authors found that the strategy of adding the grinding aid only influences the grinding result, if an early (or delayed) addition of chemicals influences the flow behavior of the product in such a way, that Grinding aids for dry fine grinding processes ScienceDirect2022年9月9日 Dry permanent magnetic separators have been widely used in the mineral and coal processing industries due to their simple operation and high separation efficiency These tools not only discard some amount of bulk Dry Permanent Magnetic Separator: Present Status
.jpg)
Dry Grinding and Classifying of Ceramic Materials
Explore advanced dry grinding and classifying for ceramics with NETZSCH jet mills and classifiers the Pamir operates with very small grinding media, thanks to the separation systems developed and patented by NETZSCH, Principle of Classification and Function of the HighEfficiency Fine Classifier CFS/HDSDownload Citation On Jan 1, 2019, Brian Anderson and others published Corn Dry Milling: Processes, Products, and Applications Find, read and cite all the research you need on ResearchGateCorn Dry Milling: Processes, Products, and ApplicationsThere are other applications of the DRY principle which help you create cleaner programming Avoid Duplication in Comments of code: Often a developer would use //, *, or # sign to explain the functionality of a code and then start coding Hence there is a known duplication in the functionality which deviates from the DRY principleKey principles in Software – DRY, KISS, YAGNI, SOLID and other 2 Gravity methods of separation are used to treat a great variety of materials, ranging from heavy metal sulphides such as galena (sp gr 75) to coal (sp gr 13), at particle sizes in some GRAVITY SEPARATION IN ORE DRESSING By ResearchGate
.jpg)
EnergyEfficient Technologies in Cement Grinding IntechOpen
2016年10月5日 In this chapter an introduction of widely applied energyefficient grinding technologies in cement grinding and description of the operating principles of the related equipments and comparisons over each other in terms of grinding efficiency, specific energy consumption, production capacity and cement quality are given A case study performed on a 2023年10月1日 They addressed grinding and conventional separation techniques, such as magnetism, gravity, and electrostatic forcebased methods, as well as novel sensorbased and mixed separation methods While Chelgani and Neisiani ’s book encompassed various aspects of dry mineral processing, this article focuses specifically on dry mineral classification technology A comprehensive review and recent advances in dry mineral 2017年3月8日 In an in vivo study using lactating dairy cows, we observed that the grinding versus steamflaking barley grain did not affect dry matter intake (236 kg/day), digestibility of dry matter in the total digestive tract (710%), milk yield (434 kg/day), milk components, rumen pH, and molar proportions of acetate, propionate, and butyrateEffects of Grain Processing with Focus on Grinding and Steam Flaking 2017年3月7日 the demands of almost any dry separation requir ement This equipment offers solutions to the m ining, construction, industrial mineral and chem ical industries(PDF) ORE SEPARATION BY CLASSIFICATION ResearchGate
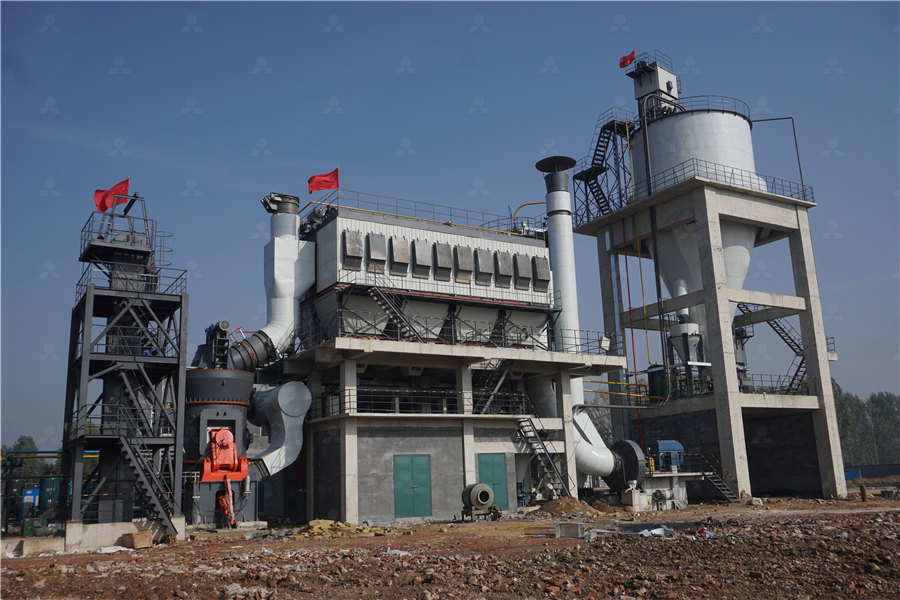
Understanding the Mechanics of Wheat Grain Fractionation
2020年3月18日 Symes is credited as being among the first to conclusively show that a single major genetic factor determines the development of either soft or hard endosperm in common wheatIn a landmark study, grain texture was quantified using a particle size index, where the mechanical resistance of grain was related to the particle size distribution after grinding 2017年3月8日 Effects of Grain Processing with Focus on Grinding and Steam Flaking on Dairy Cow Performance March 2017; DOI:105772/67344 In book: as compared with dryrolling or grinding [12]Effects of Grain Processing with Focus on Grinding and Steam Flaking 2019年9月1日 To select dry or wet grinding, the differences between their process conditions should be taken into consideration Transfer and motion of particles by air in case of dry grinding or water may significantly affect power draw and energy consumption of grinding circuits [5]Particularly, these energy differences become significant when considering that around 3% A comparative study on the effects of dry and wet grinding on In Bühler’s frontend dehulling system cold and dry soybeans are processed and can be flaked down to a flake thickness of 03 mm or less Weighing Cleaning Destoning Cracking Dehulling Conditioning Flaking Bühler Oilseeds Preparation Preparation of soybeans for direct extraction Equipment for cleaning, cracking and flakingPreparation Bühler Group
.jpg)
A comparative study on the effects of dry and wet grinding on
2019年8月31日 (DOI: 101016/JJMRT201907053) Water scarcity dictates to limit the use of water in ore processing plants particularly in arid regions Since wet grinding is the most common method for particle size reduction and mineral liberation, there is a lack of understanding about the effects of dry grinding on downstream separation processes such as flotation This allows relatively large samples for analysis or separation, that the principles are easy to understand and that the sieves and sieving equipment are relatively cheap Also, size fractions are being obtained, which can be used for other purposes (eg, further analysis or Chapter 8 Sieves and Sieving2014年7月12日 In this article, modern methods of fine milling and air classification of materials by the dry method, making possible precise sizing of particles as well as clean processing of the initial product without foreign impurities, are presented Special wearresistant construction of the working units permits the finest milling and classification of even the hardest materials, FineMilling and Air Classification of Ceramic Materials by the Dry In some cases, a combination of directindirect heated rotary dryers is also available to improve the overall efficiency A rotary dryer is suitable to dry metallic and nonmetallic mineral, clay in cement industrial and coal slime in coal mine, etc Rotary dryers can be widely used to dry various materials, and are simple to operateUnit Processes in Pyrometallurgy: Drying, Calcination, Roasting
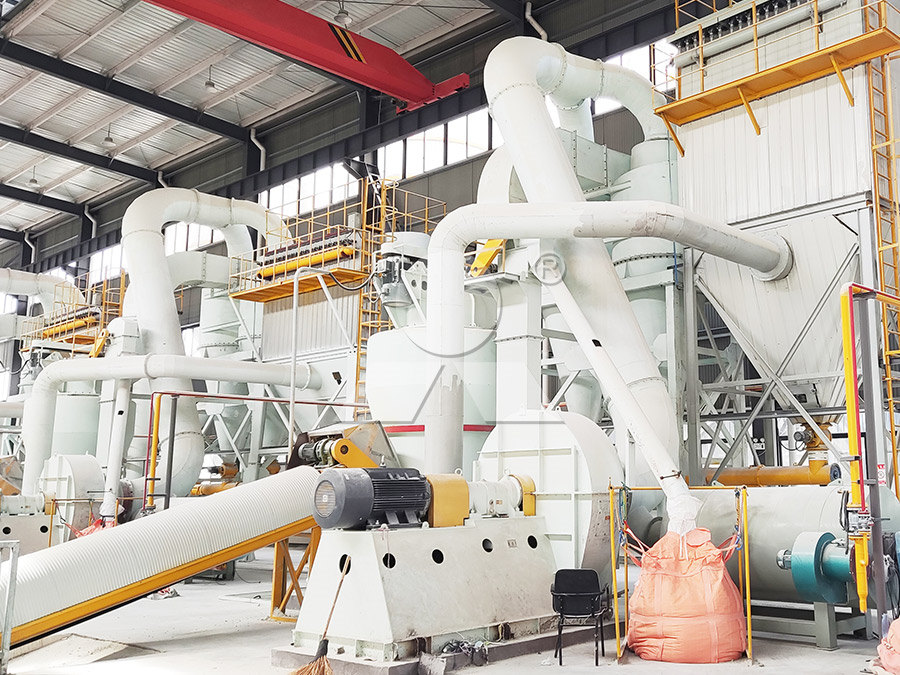
Lupine protein enrichment by milling and electrostatic separation
2015年12月1日 Lupine seeds are excellent source of plant protein We here report on dry fractionation by combining milling and electrostatic separation providing an alternative to wet extraction of protein from 2008年11月1日 The oil recovered after traditional drygrind ethanol production was highly deteriorated, with 22% FFAs and 9 meq/kg peroxide value because the germ was broken into small pieces during dry grindingEffect of the Corn Breaking Method on Oil Distribution2019年8月11日 Request PDF A comparative study on the effects of dry and wet grinding on mineral flotation separationA review Water scarcity dictates to limit the use of water in ore processing plants A comparative study on the effects of dry and wet grinding on 2021年5月5日 Wet and Dry Grinding Operation: Here In Wet, we sprayed coolant generally water or any other coolant to cool the surface so that the longevity of the grinding wheel increases and also we get a fine surface finish Grinding Machine: Definition, Parts, Working
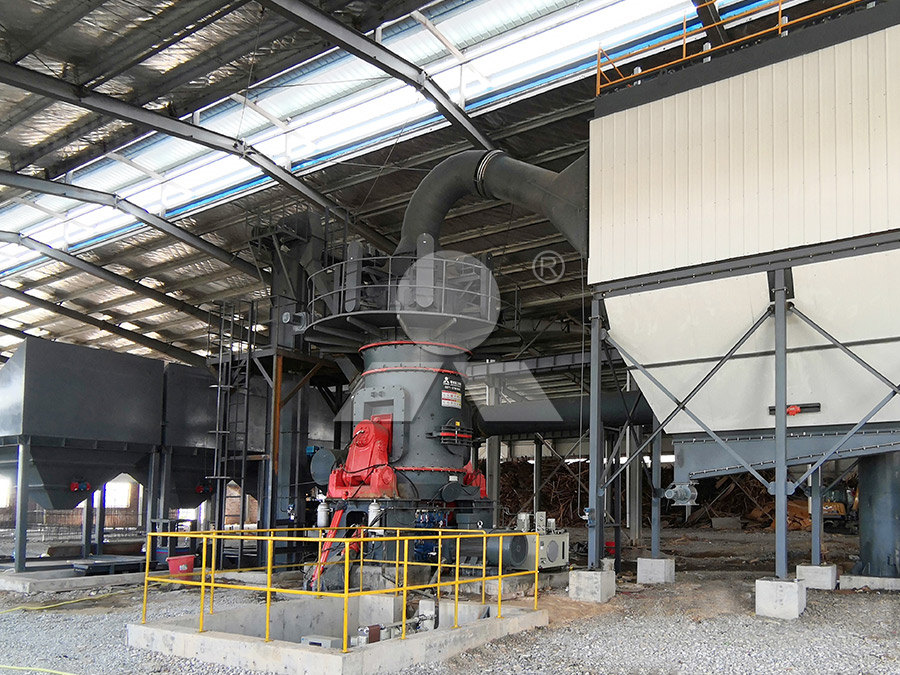
Dry Gravity Separation 911Metallurgist
2018年8月11日 Conditions for a Successful Separation As a basic condition feed material has to be as dry as it can be classified into size fractions by dry screening The frequency of the vibration has great influence on the efficiency of DGS Throughput capacity is a strict function of the machine parameters and is also dependent on the size fraction of To maximize the process output of oilseed, grain and pulses, you need to separate hulls from their kernels efficiently Bühler offers a wide range of dehulling and hull separation processes which you can tailor to your productDehulling Processes Bühler Group2022年11月28日 1 Advantages Compared with other separation methods, gravity separation has the following advantages: (1) The gravity separation method has a wide range of applications, and the particle size range of the material that can be processed is wide, up to several hundred millimeters in thickness and up to 001 mm in fine;The Beginner's Guide to Gravity Separation MiningpediaForsberg designs and manufactures the destoner that other destoners are compared to The destoner operates on the basic principle of flowing dry granular material over a vibrating, screen covered deck that is inclined Forsberg manufactures two types of destoners: Pressuretype with an open deck and the fan placed inside the box creating a positive air pressureDestoners Forsberg's Inc
.jpg)
DenseHeavy Medium Separation HMS / DMS Process
2015年6月24日 HMS and DMS are acronyms for Heavy (Dense) Medium Separation and is applied to the process of preconcentration of minerals – mainly the production of a high weight, low assay product, which may be rejected as waste In principle it is the simplest of all gravity processes and is a standard laboratory method for separating minerals of different specific DOI: 101016/JJMRT201907053 Corpus ID: ; A comparative study on the effects of dry and wet grinding on mineral flotation separation–a review @article{Chelgani2019ACS, title={A comparative study on the effects of dry and wet grinding on mineral flotation separation–a review}, author={Saeed Chehreh Chelgani and Mehdi Parian and Parisa Semsari Parapari and Yousef A comparative study on the effects of dry and wet grinding on 2018年7月15日 Request PDF Impact of grinding aids and process parameters on dry stirred media milling The demand on minerals with increasing product fineness is currently rising in many industrial Impact of grinding aids and process parameters on dry stirred media Principle 2: Stage Grinding and Stage Separation Process The stage grinding and stage separation process means that when the scattered size of the ore is uneven and fine grinding is required to obtain highgrade concentrate, appropriate separation methods should be used to throw away some tailings and separate some qualified after rough 3 Principles of Choosing the Crushing and Grinding Process
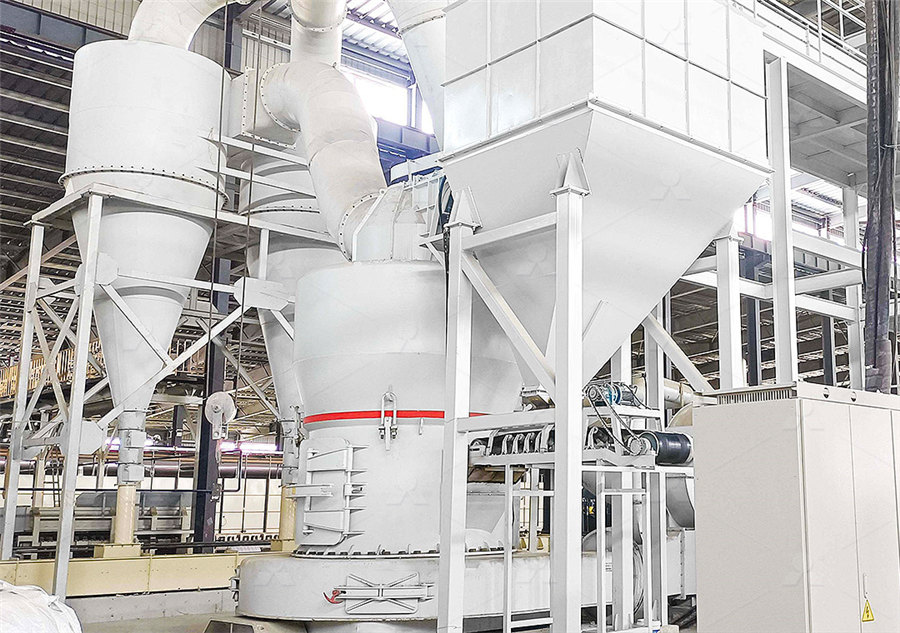
Dry Grinding VS Wet Grinding 911Metallurgist
2017年5月25日 The choice between wet and dry milling is, in general, unimportant in smallscale milling but is a major technical problem when largescale milling in the metallurgical industries is involved On purely mechanical grounds it is difficult to see any great difference in fundamental principles between wet and dry milling, since dry milling may be regarded as wet milling with a