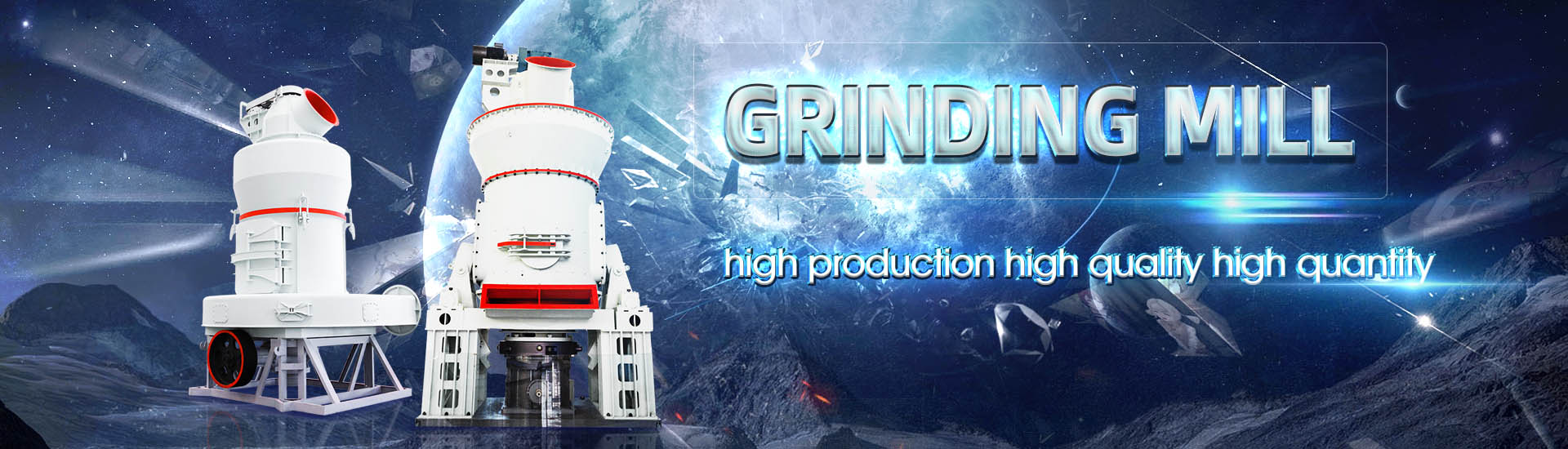
Design of PCK1010 ore mill rotor
.jpg)
Energy efficient rotor design for HIGmills Swiss Tower Mills
Extensive research with HIGmill grinding rotors has shown that flat grinding discs in stirred media mills in hardrock applications experience poorer process performance compared to 2017年4月1日 A model has been developed to describe the power draw of the new design rotors for Outotec’s fine grinding HIGmill The equation is in the form of an algebraic equation (power A power model for fine grinding HIGmills with castellated rotors2018年11月1日 HIGmill is an energy efficient grinding solution for fine grinding Extensive research with HIGmill grinding rotors has shown that flat grinding discs in stirred media mills in Energy efficient rotor design for HIGmills ScienceDirectAs a first step toward the multidisciplinary design of open rotors, this paper describes a new adjointbased methodology to be used for the ecient optimal shape design of rotating Optimal Shape Design for Open Rotor Blades Stanford University
.jpg)
Extracting potential ABB
Traditional ringgeared mill drives comprise a ringshaped gear that encircles the mill and drives it through one or two pinions followed by conventional motors GMDs mount rotor poles directly The objective of this paper is to provide a historical perspective of the evolution of rotor and blade design during the last 20 years This evolution is a balanced integration of economic, The Evolution of Rotor and Blade Design National Renewable PDF On Dec 18, 2015, Hanafi A Radwan and others published DESIGN AND EVALUATE OF A SMALL HAMMER MILL Find, read and cite all the research you need on ResearchGate DESIGN AND EVALUATE OF A SMALL HAMMER MILL ResearchGate2017年4月1日 In this study, pilot scale tests were performed with a mobile verticalrollermill grinding plant to investigate the relationships between operational parameters The Operational parameters affecting the vertical roller mill
.jpg)
IsaMill Technology Used in Effecient Grinding Circuits
High intensity stirred milling is now an industry accepted method to efficiently grind fine and coarse particles In particular, the IsaMillTM, which was invented for, and transformed the fine Process and mechanical design Based on the vigorous testwork and strict design criteria, a HIGmill size of 3500kW with a 23,000L body was selected To match the finer grind size, Case story Grinding solutions Metso Outotec HIGmill increases 2014年8月2日 This work analyses the link between the aspect ratio of a verticalaxis straightbladed (HRotor) wind turbine and its performance (power coefficient) The aspect ratio of this particular wind turbine is defined as the ratio between blade length and rotor radius Since the aspect ratio variations of a verticalaxis wind turbine cause Reynolds number variations, any Design of a verticalaxis wind turbine: how the aspect ratio 2019年3月1日 5 shows the proposed rotor slot shape for the analytical study Rotor slot width and height are varied keeping all other dimensions fixed The dimensions of the rotor slot are given in Table 4 The dimensions of the rotor Optimal design of stator and rotor slot of induction
.jpg)
A STUDY INTO HAMMER MILL ROTOR AND HAMMER
A STUDY INTO HAMMER MILL ROTOR AND HAMMER CONSTRUCTION AND SHOCK EQUILIBRATION Gh Voicu 1, G Moiceanu *, M Chițoiu, G Paraschiv 1, DC CarpCiocârdia 1 University Politehnica of Bucharest, Bucharest, ROMANIA, *moiceanugeorgiana@gmail Abstract (TNR 9 pt Bold): Hammer mill grinding process must be researched from two points 2021年4月8日 Diameter of the rotor of shaft of machine has been designed and theoretical calculations done by using PTC Mathcad software for new learning experience and ease and actual capacity of machine is calculated by using conventional method The project deals with the Manufacturing with Design and Analysis of Hammer Mill Machine and Rotor Assembly of Design and Analysis of Rotor Assembly of Hammer Mill Machine2011年1月1日 However, when evaluating the rotor design after the aerodynamic rotor design process has been carried out, the weighting between the structural and the aerodynamic performance could possibly change the thickness distribution In Fig 613, a polynomial is shown to describe the thickness distribution from 514 m and outwardsAerodynamic design of wind turbine rotors ScienceDirectA largescale hammer mill, as described by Koch (2002), has a rotor speed of approximately 1,800 rpm, should have about 10 inches (254mm) long hammers The width should be 25 inches (635 mm), and thickness should be 025 inches (64 mm) Koch (2002) also added that rotor speed about 3,600Design, Fabrication, and Performance Evaluation of a Hammer Mill
.jpg)
(PDF) Design, construction and performance evaluation of a
2018年7月19日 The detailed design procedure for a hammer mill machine is presented The system designed is a modification to the conventional hammer mill with a circular bottom casing and a semicircular screen2016年6月6日 Good Mill Liner Alloys And Design Installation and Prudent Operational Practices Prior to finalization of mill design the owner/operator or his appointee should meet with the mill designer/vendor, contracting/plant design engineer and foundry source to thoroughly review and consider such key factors (1) as: The milling application (See Table I)SAG Mill Liner Design 911Metallurgist2019 The performance of a hammer mill fabricated in Uganda was evaluated and the optimal performance conditions were determined The evaluation was done with screen hole diameters (S) of 15, 20, and 30 mm, hammer tip speeds (H) of 6812, 8181, 10217 m s and hammer thicknesses (T) of 40, 50, and 60 mm for determination of energy consumption and Design and Evaluation of Crushing Hammer mill AcademiaDesign, construction and performance evaluation of a flat screen hammer mill machine B O Ezurike 1 *, O J Osazuwa 1 , CA Okoronkwo 2 and KI Okoji 1 1 Department of Mechanical Engineering Design, construction and performance evaluation of a flat
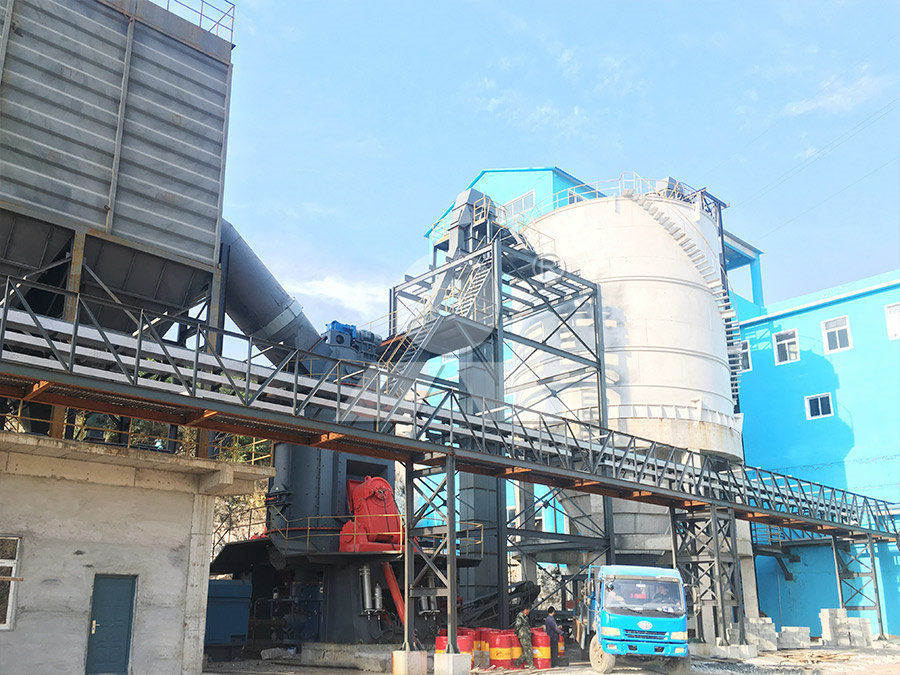
Design of a Dual Rotor Wind Turbine and
2020年7月1日 This project aims to design, build and test a prototype Dual Rotor Wind Turbine to determine the energy gain from the incorporation of the additional rotor 2 P a g e2023年11月29日 Abstract The efficiency of a hammer mill with combined methods for suspending hammers by the rotor was estimated under the production conditions of the fractional preparation of fluxes in the agglomeration shop of branch No 1 of the Alchevsk Metallurgical Plant (Southern Mining and Smelting Enterprise) Tests of a DMRiE 145 × 13 hammer mill Estimating the Efficiency of a Hammer Mill with Combined nd computed number of Cases (DL Fatigue Damage Loads Maximu deflection Placem frequencie harmonics Stability: , ) tuators Design Optimization of GE wind turbine (from inhabitat) Wi Turbines Loads: envelope from largeWind Turbine Design National Renewable Energy Laboratory wrapped around the mill and its rotor poles installed at an extension of the mill head The air gap between the rotor poles and the laminated core of the motor measures only some millimeters, the outer diameter of the rotor up to 14 meters and more Deformations of the motor must be limited to avoid contact between rotor and statorDesign and dynamic behavior of large Ring Motors for grinding
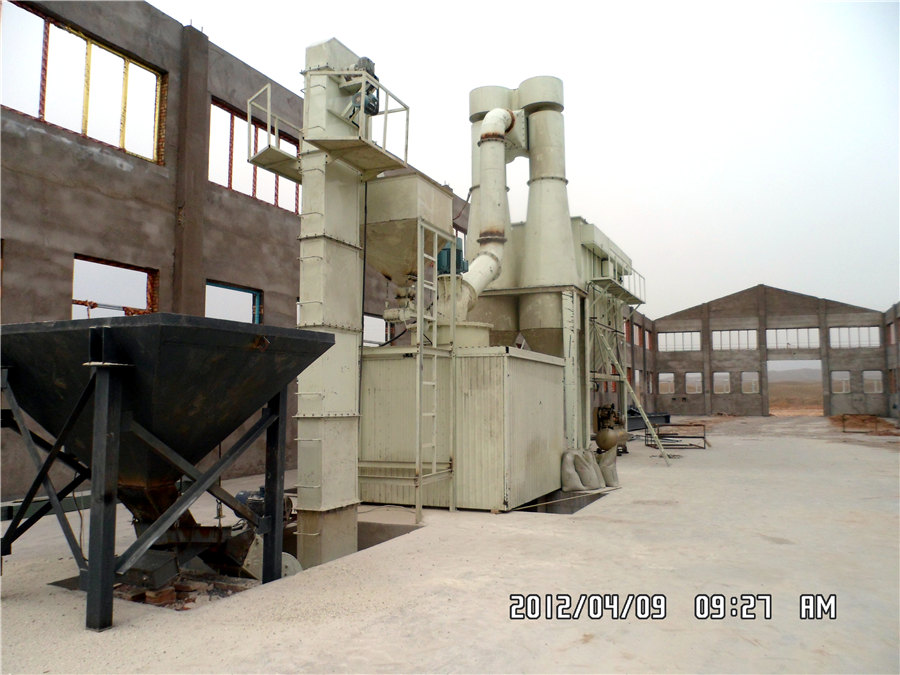
Design and Analysis of Rotor Shaft Assembly of Hammer
International Journal of Engineering and Management Research, Volume3, Issue2, April 2013 ISSN No: 22500758 Pages: 2230 ijemr Design and Analysis of Rotor Shaft Assembly of Hammer Mill Crusher EVijaya Kumar Assistant Professor, Department of Mechanical Engineering, Siddhartha Institute of Technology amp; Sciences, Ghatkesar, Hyderabad, 2016年1月1日 The aerodynamic performance of an upwind, threebladed, small horizontal axis wind turbine (HAWT) rotor of 22 m in diameter was investigated experimentally and theoretically in order to assess (PDF) Design of Horizontal Axis Wind Turbine ResearchGateInternational Journal of Engineering and Management Research eISSN: 22500758 pISSN: 23946962 Volume11, Issue2 (April 2021)Design and Analysis of Rotor Assembly of Hammer Mill MachineOre mill Ore mills 21 companies 42 products My filters for ore Delete all DM 200 is used for grinding mediumhard, hard and brittle materials Thanks to its robust design it is suitable for usage under rough conditions in pilot plants and rotor mill HCP media field many more times and more efficiently than any other Ore mill, Ore grinding mill All industrial manufacturers
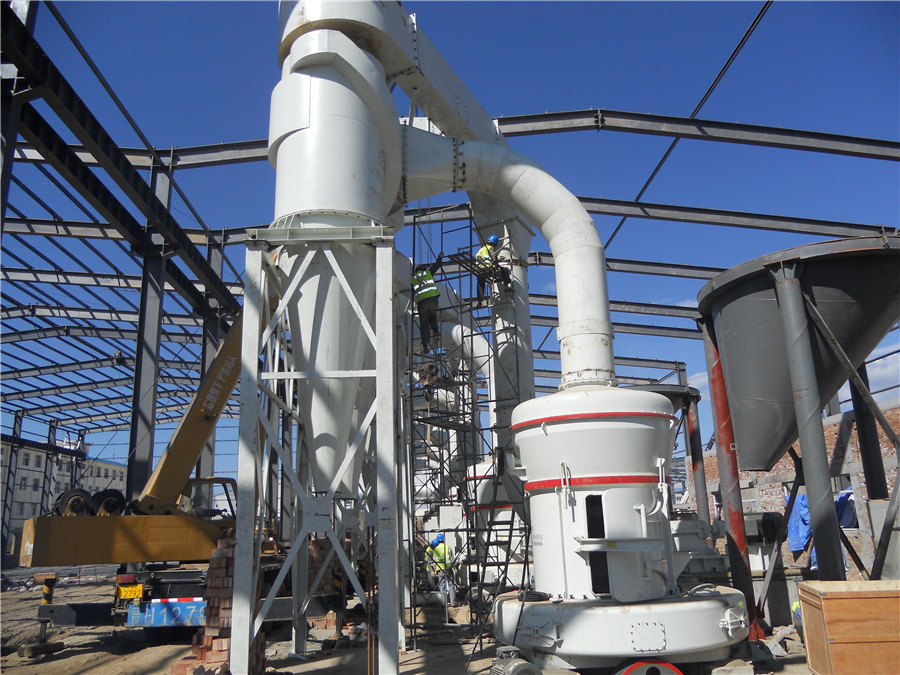
DESIGN, FABRICATION AND TESTING OF A LABORATORY SIZE HAMMER MILL
products with improved design The machine is portable, design to be power operated KEYWORDS: Design, Fabrication, Laboratory Size Hammer Mill INTRODUCTION Crushing is an integral part of the comminution flow sheet for mineral processing operations and is critical for the preparation of ore for downstream processingattributed to increased rotor control through pitch and yaw control The HAWT has therefore emerged as the dominant design configuration, capitalised by all of today’s leading large scale turbine manufacturers 2 Theoretical Maximum Efficiency High rotor efficiency is desirable for increased wind energy extraction and should be maximisedWind Turbine Blade Design Semantic Scholar2012年12月28日 Design of a rotor of a wind mill is very crucial to harness wind energy The aerodynamic design of rotor involves optimizing the rotor and its components to produce maximum power coefficient which is the ratio of actual rotor output to the wind energy available for a given rotor area The design of a wind mill although looks simple but involves complex Optimized Design of Rotor Blade for a Wind PumpThe design and construction of hammer mill becomes imperative as that will go a long way in getting processed cereals grains easily within developing nations Rotational speed of the rotor, radians/second Mass of the ore The ore stiffness to breakage, Where; = Number of revolutionsImprovement on the Design,Construction and Testing of Hammer Mill
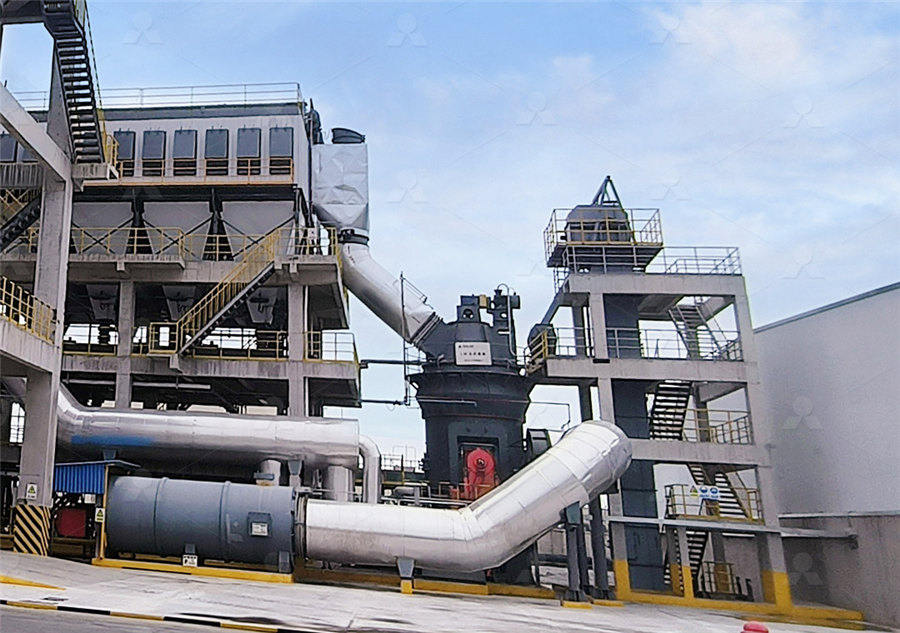
Principle of Rotor Design for Horizontal Axis Wind
The wind potential in where the wind turbine rotor will operate: Wind potential in where the wind turbine will be installed is very important For this reason it is one of the parameters that have to be considered in rotor design Wind speed 2015年9月6日 Schematic of design hammer mill 1Main frame ,2Single phase Electrical motor 1 k Watt, Rotational speed of the rotor, radians/seconds; m = Mass of the ore, kg; rDESIGN AND EVALUATE OF A SMALL HAMMER MILL2019年12月23日 A hammer mill has been designed with due considerations to standard design requirements and cost to cater to this need The rotor speed is obtained as 12891 rpmDEVELOPMENT OF A HORIZONTAL SHAFT HAMMER MILL CHAPTER 2018年10月15日 The role of rotor impact mill screen plate design in biomass grinding has attracted limited interest This study aimed to clarify the effect of operational parameters and various screen designs on the fine grinding of Sphagnum mossContoured screens having forward (rasp) and backward (inverse rasp) inclined trapezoidal apertures of nominal sizes 02, Role of screen plate design in the performance of a rotor impact mill
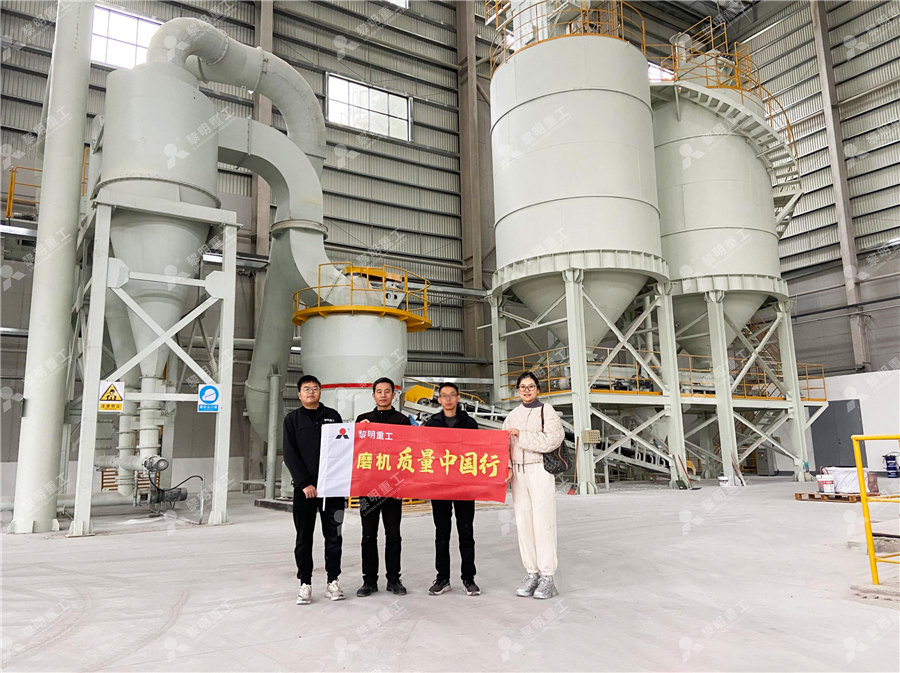
Small Wind Turbine Blade Design and Optimization
2019年12月19日 Finally, the rotordesign was obtained, which consists of three blades with a diameter of 4 m, a hub of 20 cm radius, a tipspeed ratio of 65 and can obtain about 650 W with a Power coefficient 2021年3月15日 The design of the HSMs commercially available are colloidal mill, radial discharge (rotor–stator) operates in both batch and inline mode and axial discharge mixers The HSMs assembly can have a single or multi stage rotor and stator configurations and the principle of operation can be batch, semibatch, and inlineDesign and development of high shear mixers ScienceDirect2007年6月3日 Optimal Design of Rotor Slot Geometry of SquirrelCage Type Induction Motors June 2007; and a m ore imp orta nt increase of the breakdown torque, Fig 17 A / m m 2 Figure 15 Current (PDF) Optimal Design of Rotor Slot Geometry of SquirrelCage 2022年10月1日 The flux linkage characteristics of SRMs exhibit nonlinear relations concerning the phase currents and rotor positions, as presented in Fig 1 Optimal design of a switched reluctance motor with magnetically disconnected rotor modules using a design of experiments differential evolution FEAbased method IEEE Trans Magn, 54 (2018 Design optimization of switched reluctance machines for
.jpg)
Rotor Blade Structure SpringerLink
2023年6月17日 Finally, a fullscale blade test is required for the component certificate of the rotor blade This serves to validate the design assumptions on the one hand and to identify relevant failure modes or critical manufacturing details on the other []In the fullscale blade test, the rotor blade is subjected to a testing program comprising static and cyclic tests, if applicable []ADVERTISEMENTS: In this article we will discuss about the design of wind turbine rotor with the help of suitable diagrams In a propeller type wind turbine, the following two forces operate on the blades: 1 Axial Thrust: ADVERTISEMENTS: It acts in the same direction as that of the flowing wind stream 2 Circumferential Force: It []Design of Wind Turbine Rotor (With Diagram) Wind Energy1995年9月13日 The most dramatic improvements in inverterfed induction motors are achieved by the change of rotor slot geometry, which can reduce the harmonic winding losses of the rotor to a minimum Based on an immense number of finiteelement calculations, optimal values of different geometrical dimensions of the rotor slot with a Ushaped bridge have been Rotor slot design of inverterfed induction motors IEEE Xplore2023年1月16日 The objective of this research is to design and construct a hammer mill for grinding leonardite charcoal (Lignite, class J) The conditions for the design and construction of the grinder are Optimum Design of Hammer Mill for Grinding Leonardite
.jpg)
DESIGN AND FABRICATION OF A MILL PULVERIZER
Unlike the normal hammer mill, it does not use a screen classifier; rather it employs air classifier in which the conceptual design was based on the principle of design by analysis (Nortion, 2006) The methodology was to introduce special features into the hammer mill pulveriser so that certain lapses noticed in the convectional hammer mill is reduced to a bearable levelSIZE HAMMER MILL AJAKA EO and ADESINA A immensely in the design of various components of the rotor r = radius of the rotor, m s = the ore stiffness to breakage, N/m Determination of Hammer Shaft Diameter I b max s M Y 1 allowable Z M Z Y I b V s max Spolt, 1988 (10) Where Y max = Distance from neutral axis to outer fibersDESIGN, FABRICATION AND TESTING OF A LABORATORY SIZE HAMMER MILL2020年6月3日 The design of such grinding mills is extremely critical, requiring sophisticated software tools, proprietary calculation worksheets, and experienced technical engineers and drafters This blog will review how the mill design process has changed over the last 30 years While most of the changes have been positive, new issues and problems have risen in the How grinding mill design changed over the last 30 years2019年5月31日 In my previous blog post, “How the Design of a Wind Turbine Differs from other Types of Turbines”, I showed that the very small pressure drop across the rotor makes wind turbine design different from other types of turbines This blog will focus on the best method to design a wind turbine rotor based on the fact that only kinetic energy is available to extract How to Design a Wind Turbine Rotor Concepts NREC
.jpg)
(PDF) DESIGN AND OPERATIONS CHALLENGES OF A SINGLE
2017年6月30日 A review on the design and operations challenges of a single toggle jaw crusher is presented Strength and fracture toughness of the material to be crushed are intrinsic properties that determine PROJECT REPORT – PHASE I on ANALYSIS AND DESIGN OF BALL MILL FOUNDATION FOR TATA IRON ORE PELLET PLANT AT JAMSHEDPUR Submitted in partial fulfillment for the award of the degree of BACHELOR OF TECHNOLOGY in CIVIL ENGINEERING by MOHD ADEEL ANKIT GOYAL VIVEK BABU Under the (DOC) PROJECT REPORT – PHASE I ANALYSIS AND DESIGN OF BALL MILL