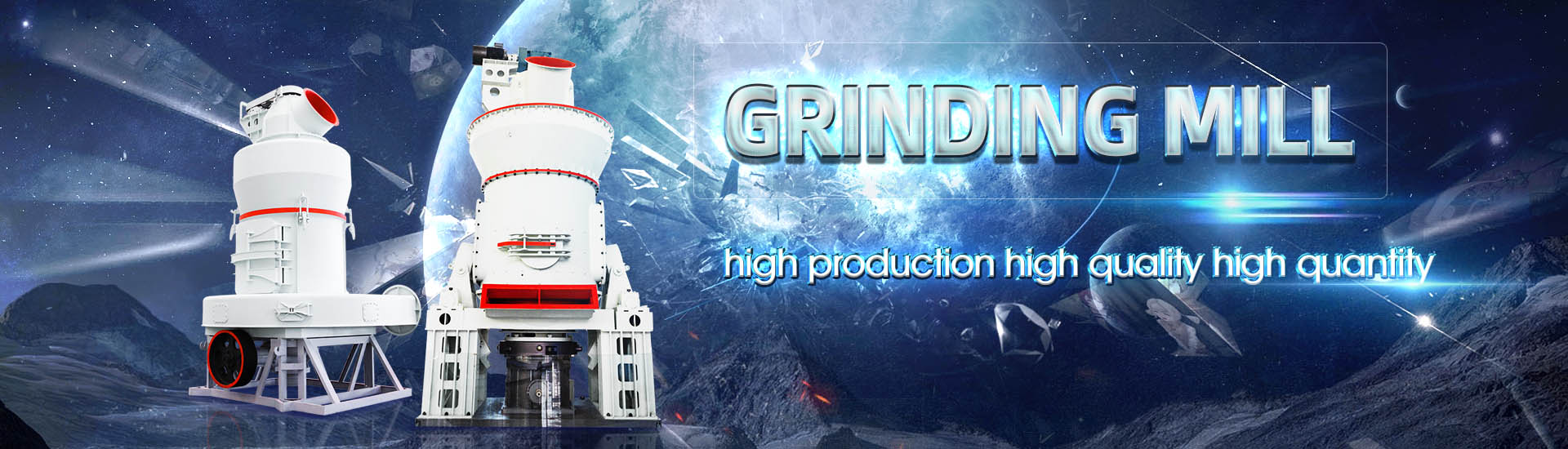
How to adjust the particle size of vertical coal mill

PREDICTING THE PRODUCT PARTICLE SIZE DISTRIBUTION FROM
of a laboratory scale vertical stirred mill using a Bond ball mill An energybased population balance model was developed to analyze the response in product size resulting from changingthis dissertation was to investigate the effect of coal feedstock property variation on the vertical spindle coal pulverising mill’s performance to facilitate optimal plant performance Plant design Performance optimisation of vertical spindle coal pulverisers2020年8月12日 To understand the performance of a vertical roller coal mill, the real operational tests have been performed considering three different coal sources Obtained results indicate thatAn investigation of performance characteristics and 2022年5月31日 The metaparticle size ratio (representing feed size) has a significant effect on the performance of the VRM By increasing the metaparticle size ratio, the crushing rate firstly Analysis of vertical roller mill performance with changes in material
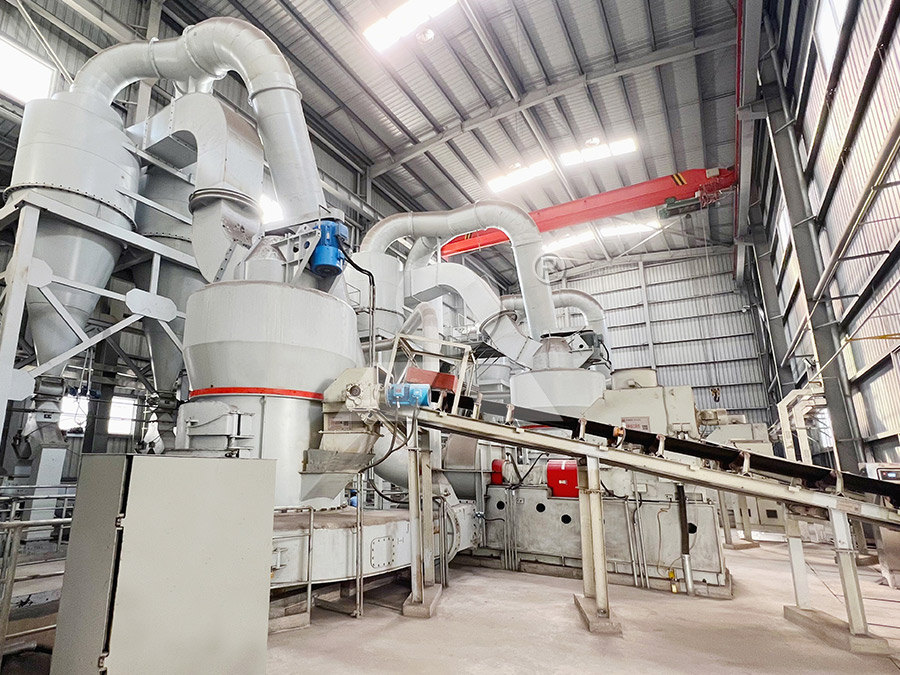
Mass flow and particle size monitoring of pulverised
2016年8月1日 The following paper presents and analyses methods of monitoring the key performance factors of a vertical spindle mill that is suited The following paper presents and analyses methods of monitoring the key performance factors of a vertical spindle mill that is suited for implementation on older power stations, ie theASS FLOW AND PARTICLE SIZE MONITORING OF PULVERISED design features will increase coal processing capacity The first part of this series, “Finessing Fuel Fineness,” published in the October 2008 issue of POWER, explored the importance of “Blueprint” Your Pulverizer for Improved Performance2024年8月1日 Powdered coal (0–1 mm) is produced through adjusting VSM’s operating parameters The vertical spindle mill (VSM) is the key equipment to realize the preparation of Experimental investigation on the preparation of macroscopic 0–1
.jpg)
Modelling of vertical spindle mills Part 2: Integrated models for E
2015年3月1日 The model explicitly incorporates mill design data (mill diameter, grinding table diameter, air classifier geometry) and operational conditions (coal feed rate, air flow rate, air 2020年8月12日 Uniform coal feeding mass flow rate and required particle size and temperature at the outlet channel throughout with better classifier performance are crucial indicators that An investigation of performance characteristics and energetic 2022年5月31日 An increase in metaparticle size ratio from 08 to 12 (about a 50% increase) leads to a 927 times increase in throughput The crushing rate first increases and then decreases with the metaparticle size ratio An increase in metaparticle size ratio from 11 to 12 leads to an 187% reductionAnalysis of vertical roller mill performance with changes in 2017年4月1日 Separation operation of verticalrollermill will be modelled by application of current models The model shall enable the prediction of the throughput, the particle size distributions around the verticalrollermill circuit, the specific energy consumption and in a later stage the wear to be expected in dependency of ore treatedOperational parameters affecting the vertical roller mill
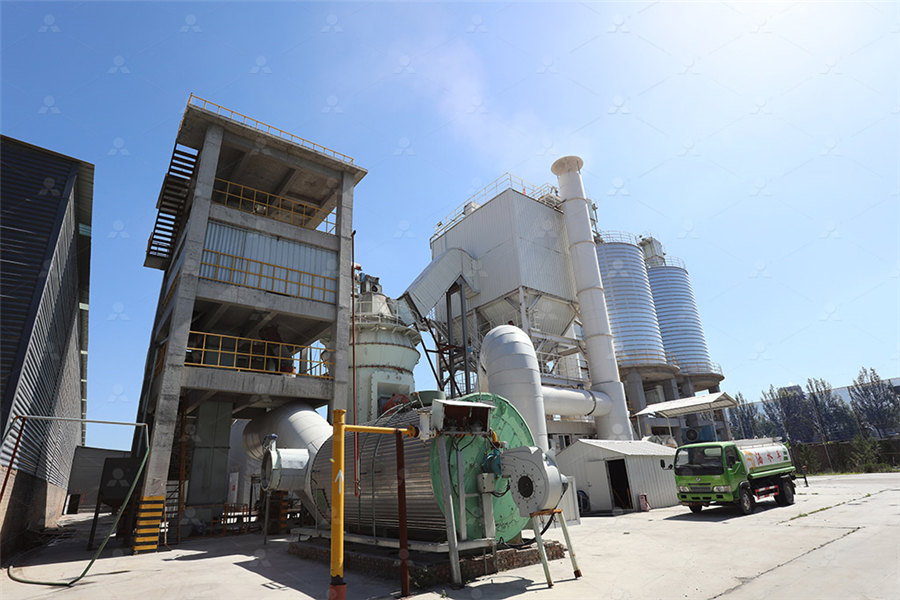
Roller Mill SpringerLink
2023年7月4日 The column mill is a vertical mill using high speed, medium pressure, and continuous, repeated grinding It consists of the belt pulley, the gearbox, the main shaft, the feeding device, the discharging device, the spreading plate, the Depending on the required coal fineness, there are two types of classifier that may be selected for an MPS mill The SLS dynamic classifier, which consists of a stationary angled inlet vane assembly surrounding a rotating vane assembly or cage, is capable of producing micron fine pulverized coal with a narrow particle size distributionCoal Pulverizer Design Upgrades to Meet the Demands of Low 2017年9月1日 The first stirred mill was installed in the platinum industry in 2002, and by the year 2010, forty stirred mills had been installed at various platinum operations in South Africa, and these led to a step change in flotation recoveries (Rule, 2011, Rule, 2010)Over the last decade, approximately 200 Automated Scanning Electron Microscopy (AutoSEMEDS) systems have Fine grinding: How mill type affects particle shape characteristics 2018年3月20日 A pin mill is one of the most commonly used impact mills for grinding bulk solid materials to medium fineness The mill can accept feed materials with a particle size ranging from 20 microns to 05 in and a Mohs hardness of 4, reducing particles down to as small as 10 microns, depending on the mill type and feed sizeIdentifying a Pin Mill for Optimal Performance and Minimal
.jpg)
Technical specifications of vertical roller coal mill
Vertical Coal Mill (VCM) is equipment for grinding and pulverizing coal into micron size Rotary kilns then use the powders as fuel burners The VCM has a housing section equipped with a lining this dissertation was to investigate the effect of coal feedstock property variation on the vertical spindle coal pulverising mill’s performance to facilitate optimal plant performance 331 Mill coal feeder Mill particle size distribution 38 Table 54: Boiler guaranteed operation data Performance optimisation of vertical spindle coal pulverisers2020年3月1日 The classification performance of the air classifier in a vertical coal mill determines the size of pulverized coal particles Thus, the classification performance will influence the ignition, burning, and burnout of the coal particle, and NO x formation in the furnace as well [[1], [2], [3], [4]]Classification performance of model coal mill classifiers with 2024年6月17日 The shaft rotates at a high speed and the hammering aids in particle size reduction Additionally, particleonparticle contact can also cause size reduction or contact in the grinding chamber with the breaker plate The discharge from this hammer mill is then subjected to gravity You can use this mill to crush: Coal; Glass; Resin ; Brass Hammer Mill Types Explained Pulva Corporation
.jpg)
Mass flow and particle size monitoring of pulverised
2016年8月1日 This study shows the performance of a currently running vertical roller coal mill (VRM) in an existing coalfired power plant In a power plant, the coal mill is the critical equipment, whose 2021年1月1日 Grinding Mill Vertical Roller Mill or Ball Mill: Coal is ground in Coal mill, which is a fuel for use in Kiln firing: 5: It can be achieved by adjusting the speed of the classifier The particle size of the mill feed material and its size distribution Review on vertical roller mill in cement industry its particle size distribution curve By these measures it has been possible to obtain particle size distributions for cement ground in OK mills similar to those for cement ground in ball mills (BM), as shown in Figure 6 Figure 6: B It should be noted, however, that operation to achieve a wide particle size distribution (low nvalue) has a costCement grinding Vertical roller mills versus ball millsBetter particle size distribution: Vertical roller mills produce a more consistent and higher quality particle size distribution than traditional mills In conclusion, vertical roller mills offer a more efficient and costeffective way to grind materials than traditional ball mills or highpressure grinding rollersHow does Vertical Roller Mill Work? ball mills supplier
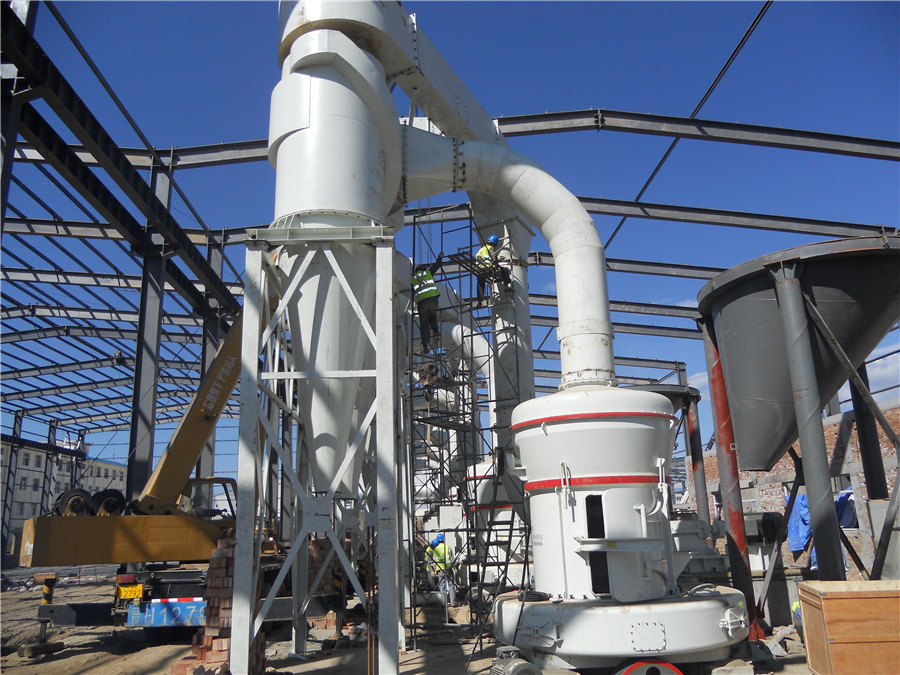
Advantages and disadvantages of vertical roller mill
The vertical roller mill has a big feed size (can grind the material with particle size of 5% of the grinding roller diameter: the feed size is generally 40100mm, and the large vertical mill can reach 120mm), which simplifies the crushing system and saves secondary crushing2017年3月4日 A stamp mill (or stamp battery or stamping mill) is a type of mill machine that cru shes material by pounding rather than grinding, either for furthe r processing or for extraction of metallic oresSIZE REDUCTION BY GRINDING METHODS ResearchGate2024年9月4日 Raymond Mill Ultrafine Mill: This machine is used for grinding extremely fine materials, even down to 3000 mesh It’s often used for materials that are challenging to process with regular milling machines, such as graphite, coal, and others Its advantages include the ability to produce extremely fine powder, even up to 3000 meshWhat is Raymond Mill? How Does It Work? alwepo2013年8月3日 In Grinding, selecting (calculate) the correct or optimum ball size that allows for the best and optimum/ideal or target grind size to be achieved by your ball mill is an important thing for a Mineral Processing Engineer AKA Metallurgist to do Often, the ball used in ball mills is oversize “just in case” Well, this safety factor can cost you much in recovery and/or mill liner Calculate and Select Ball Mill Ball Size for Optimum Grinding
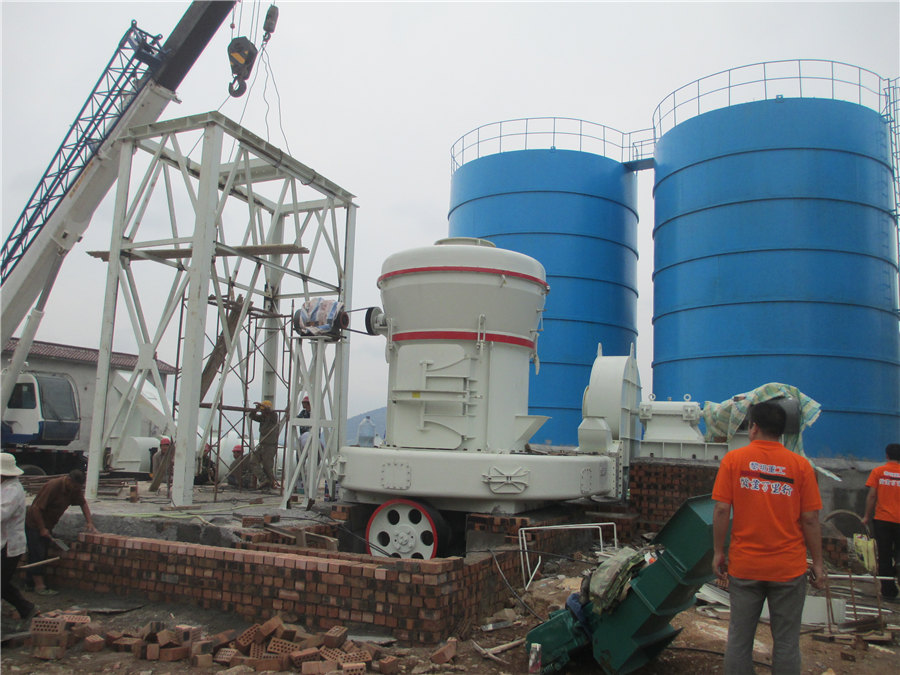
Effect of ball and feed particle size distribution on the milling
2018年2月1日 In another study to investigate ball size distribution on ball mill efficiency by Hlabangana et al [50] using the attainable region technique on a silica ore by dry milling, a threeball mix of Table 1 From Table 1 we can learn that if the particle size of the feed material is reduced from 25 mm to less than 2 mm, the mill output can be increased by at least 60%, which is relatively consistent with the actual productionHow to Improve Cement Ball Mill Performance2022年5月31日 It was found that trends in the particle size distribution of product and changes in throughput and crushing rate could be identified with alterations in material properties and the operating conditions Numerical Study of Flow Field and Particle Motion Characteristics on Raw Coal Vertical Roller Mill Circuits 2024, Analysis of vertical roller mill performance with changes in 2012年5月1日 Coal fired power plants are heavily used due to large and long lasting coal resources compared with oil or natural gas An important bottleneck in the operation of this particular kind of plants, however, is the coal pulverization process, which gives rise to slow takeup rates and frequent plant shutdowns (Rees Fan, 2003)In typical coal fired power plants, Derivation and validation of a coal mill model for control
.jpg)
An investigation of performance characteristics and energetic
Energetic Efficiency 2024年3月16日 This grinding action results in the reduction of coal particle size, facilitating efficient combustion and energy production Subsequently, the pulverized coal is carried upward by a highspeed airflow generated by the rotating table and How Does a Vertical Coal Mill WorkFig2 Schematic process flow of vertical roller mill for grinding of raw materials Vertical roller mills are adopted in 20 cement plants (44 mills) in Japan Results Table Energy saving effect of the vertical roller mill Ball mill Specific power Cost estimationVertical roller mill for raw Application p rocess materials2015年11月1日 Physical structure of a vertical spindle bowl mill (Agrawal, Panigrahi, Subbarao (2015)) 3 The detailed particletracking calculations are not performed and for different air flows, critical size of the coal particle which can reach the top of the separator is determined using reasonable guess of experienced operatorsA unified thermomechanical model for coal mill operation
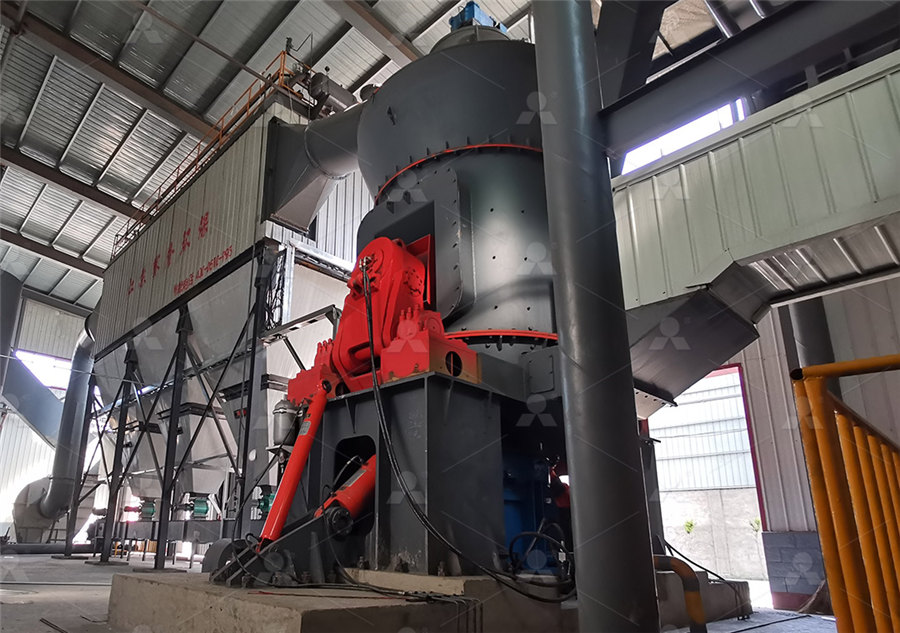
Classification performance of model coal mill classifiers with
2020年3月1日 The classification performance of the air classifier in a vertical coal mill determines the size of pulverized coal particles Thus, the classification performance will influence the ignition, burning, and burnout of the coal particle, and NO x formation in the furnace as well [[1], [2], [3], [4]]The first generation of the coal mill classifier used static guide vanes to 2023年7月10日 Too small of a media size or too large of one can decrease the mill efficiency , making the media size dependable on the ground particle size That is, in the case of a particle size below 10 μm, finer media sizes were more effective, and when the media sizes were between 17 and 12 mm, efficient grinding was performed [ 24 ]EnergyEfficient Advanced Ultrafine Grinding of Particles Using DOI: 101016/JMINENG201809016 Corpus ID: ; Predicting the product particle size distribution from a laboratory vertical stirred mill @article{Rocha2018PredictingTP, title={Predicting the product particle size distribution from a laboratory vertical stirred mill}, author={Danielle Campos Rocha and Erik Spiller and Patrick R Taylor and Hugh B Miller}, Predicting the product particle size distribution from a laboratory 2023年9月22日 Reduce the grinding particle size of materials The feed particle size had been increased from 1229mm to 2411mm due to work reasons Now the feed particle size has been reduced and adjusted to 1108mm, but the screen residue situation has not improved Adjust the grate seams of the partition board The grate seams of the partition plate are How to Adjust Cement Mill Fineness?
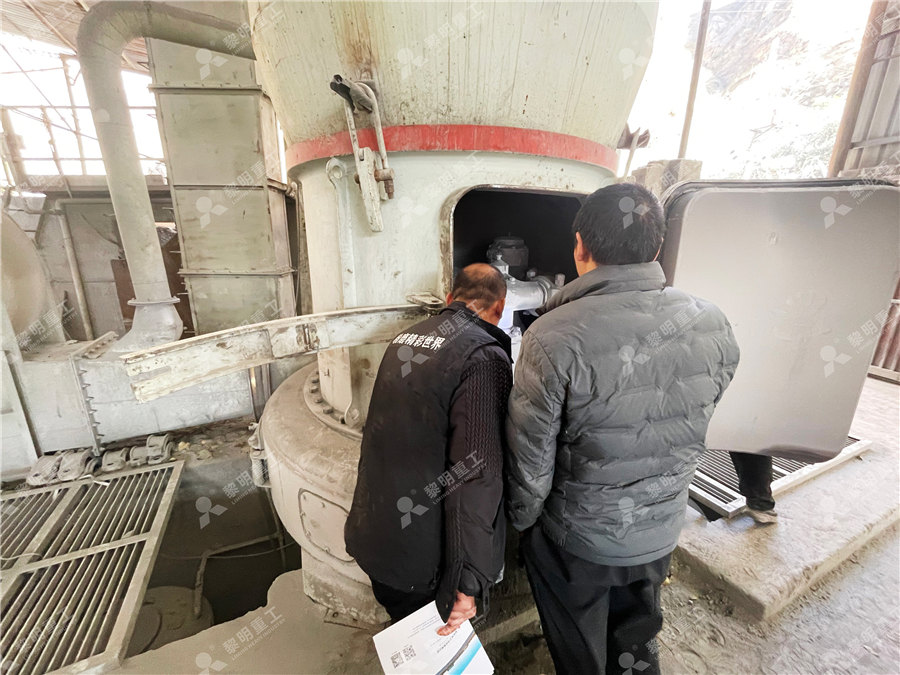
Roller mills: Precisely reducing particle size with greater efficiency
How the mill achieves uniform particle size To achieve a uniform final particle size with minimal fines, the roller mill must have the right roll surface, roll speed ratio, and roll gap for your application Roll surface Typically, the roll surface is corrugated rather than smooth to achieve efficient size reduction, as shown in Figure 3Finished particle size: 10–40 μm (370–1,250 mesh) Capacity: 245 t/h Other types include ore vertical mills and pregrinding vertical mills For Equipment: 3 sets of HLM1900M coal vertical mill Auxiliary equipment: Jaw crusher, Energysaving and Efficient Vertical Roller Mill Fote 2023年6月5日 Regularly monitor and adjust the pulverizer settings to achieve the desired particle size distribution Upgrade to modern technology: Consider upgrading your pulverizer to a more advanced and How can we increase the efficiency of a vertical bowl coal2023年12月4日 A vertical roller mill (VRM) simulated and validated the capability of DEM to estimate the product particle size distribution, Wang S, Lv W (2017) Effect of lifters and mill speed on particle behaviour, torque, and power consumption of a tumbling ball mill: experimental Study and DEM simulation Miner Eng 105:22–35Numerical Investigation of Vertical Roller Mill Operation Using
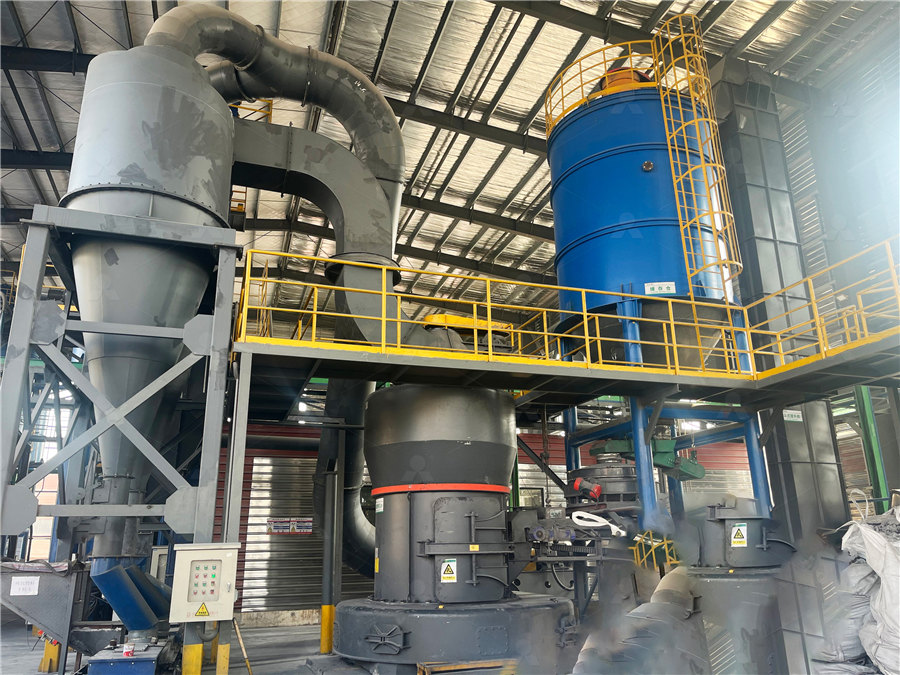
Grinding circuit optimisation to increase throughput and
Placed on a mill feed conveyor belt, it is used to estimate the particle size of the fresh feed All of our systems have Deep Neural Network capability, and can be used for detecting objects on the surface Typically fed back into a control system: LoadIQ (adjust load target for ore size) or crusher optimisation (css/oss setting)vertical spindle mill optimization First of all, 200mesh results in a mean particle size of about 30 microns vs a preferable mean particle size of 4550 passing 200mesh is a particle surface area difference of about 85%! Average Collected Particle Size (from Isokinetic Coal Sampling Test) 400 450 500 550 600 650 700 750 800 A case study of how vertical spindle pulverizer performance is Fig 1 Schematic operation principle of a verticalrollermill nantly occurs by particleparticlecontacts or phase–phasecontacts(Fandrich et al, 2007) Both breakage modes enhance the liberation of the valuable mineral phases, which may lead to further improvements in the beneficiation process (Reichert et al, 2015)Modeling and simulation of vertical roller mill using population 2024年1月15日 Particle size distribution is one of the most important characteristics of powders for any industry involved in the production and/or carried out multiphase CFD modelling of a roller mill used as coal pulveriser to investigate wear pattern in the mill Based on CFD An industrialscale vertical roller mill (M600) Optimisation of the performance of a new vertical roller mill by
.jpg)
How to adjust the fineness of the mine ball mill
2024年10月28日 3 Adjust the ore feed particle size and ore feed volume The particle size of the ore feed can be said to be the foundation of the problem In the same grinding time, if the particle size of the ore feed is small, the particle size of the ground product will be finer In addition, by controlling the amount of ore feed, the ball mill can also A simple energy balance model of the coal mill is derived in (Odgaard and Mataji 2006), this model is based on a more detailed model found in (Rees and Fan 2003)In this model the coal mill is seen as one body with the mass m mThe following variables are defined: T(t) is the temperature in the coal dust flow in the mill, ṁ PA (t) is the primary air mass flow, T PA (t) is Coal Mill an overview ScienceDirect Topics