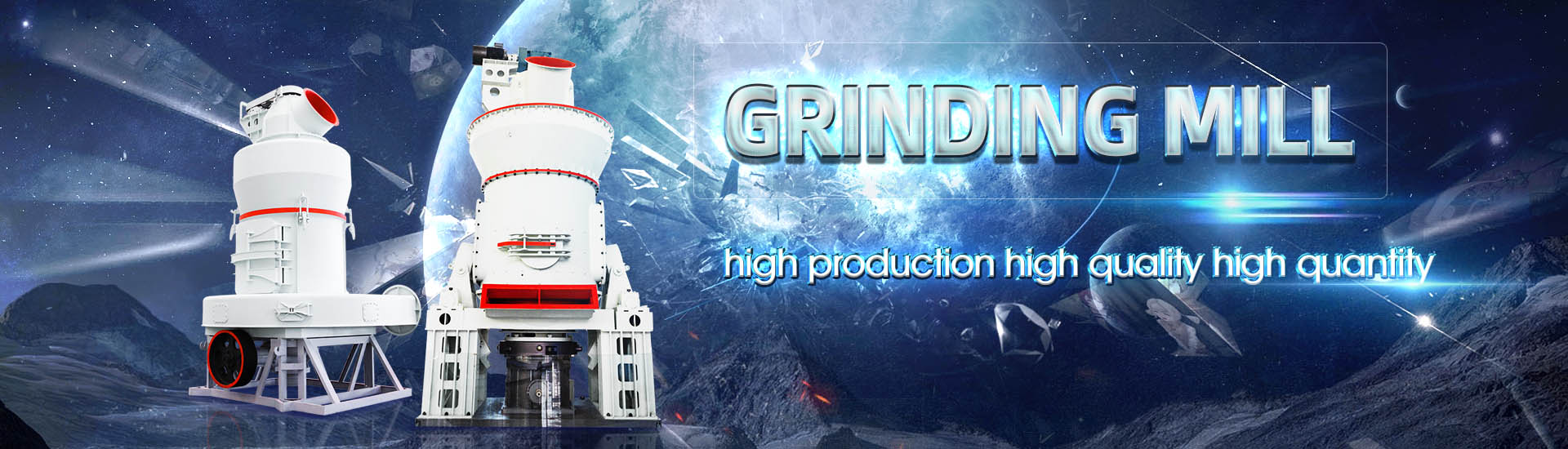
MMD1000 ore mill energy consumption
.jpg)
Breaking down energy consumption in industrial
2017年1月17日 This paper reports the results of an investigation targeting two objectives: (1) characterising energy outputs in industrial grinding mill circuits, and (2) identifying the potential for 2013年12月18日 While fine grinding consumes less energy than primary grinding, it can still account for a substantial part of a mill’s energy budget Overall energy use and media use are strongly related to stress intensity, as well as to Energy Use of Fine Grinding in Mineral ProcessingThe paper presents investigations on grinding energy consumption, size distribution and microfracturing of HPGR products, which affect the efficiency of the whole comminution and Quantification of HPGR energy efficiency effects on downstream 2023年11月1日 Grinding efficiency is the unit energy consumption rate of the mill, which represents the amount of material with a particle size of −0043 mm newly generated for every Energy conservation and consumption reduction in grinding
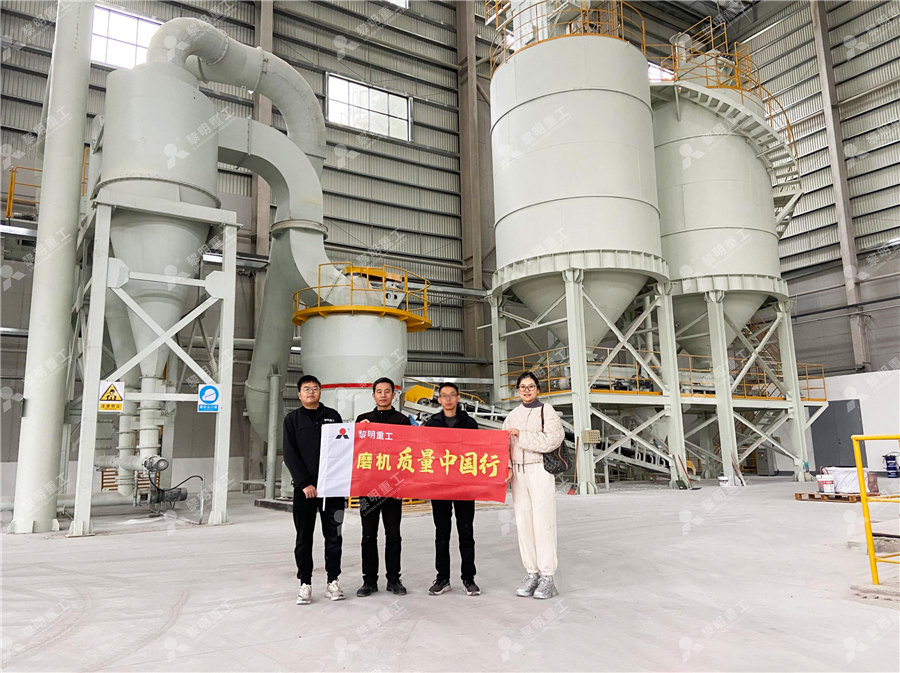
Breaking down energy consumption in industrial grinding mills
2019年11月15日 The present literature review explores the energyefficient ultrafine grinding of particles using stirred mills The review provides an overview of the different techniques for It is generally accepted that the energy required to produce new mineral surfaces is less than 1% of the electricity consumed to operate ball mills The remaining 99% is assumed to be Breaking Down Energy Consumption in Industry Grinding Mills2013年3月1日 Fine grinding, to P80 sizes as low as 7 μm, is becoming increasingly important as mines treat ores with smaller liberation sizes This grinding is typically done using stirred mills Energy Use of Fine Grinding in Mineral Processing2015年2月1日 A model of specific energy consumption (kW h/tonne milled) versus throughput (% design capacity) was developed for a base metal milling facility, from hourly electricity and The link between operational practices and specific energy
.jpg)
Improving Energy Efficiency Across Mineral Processing and
Concentrators and smelters individually may be running efficiently, but are they optimising energy consumption of the overall system? A key step towards answering this question is to 2013年7月15日 The ball mill in closed circuit with hydrocyclones is an industry standard, and well known methodologies exist for equipment sizing, selection and design(PDF) Energy Efficient Ball Mill Circuit – Equipment Two major factors contribute to the high unit energy consumption for AG and SAG operations The first is related to variability in the size and competency of rock fed to the mill Mine planning, ore blasting and primary crusher controls, while quite advanced from years ago, are not sufficient to limit the inherent variability that occursAUTOGENOUS MILL FEED PREPARATION TO REDUCE UNIT ENERGY CONSUMPTIONEnergies 2021, 14, 1786 2 of 14 size [11] The cost of the energy used in comminution represents 50 ÷ 60% of the entire ore processing costs [12]Energy Efficiency Analysis of Copper Ore Ball Mill Drive Systems
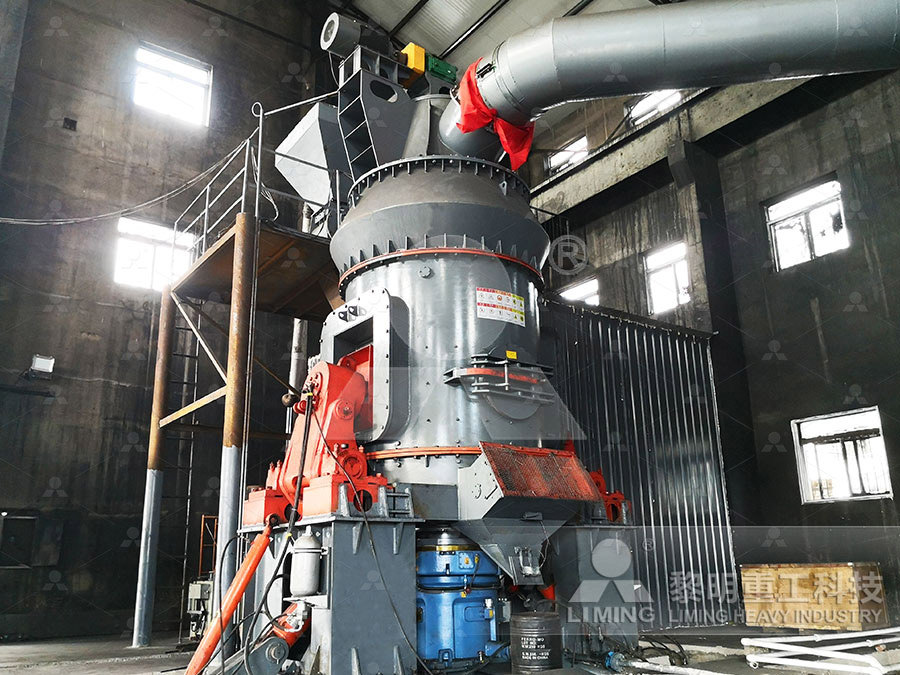
Fixed Mobile Sizer Stations MMD
Fixed Sizer Stations are commonly fixed in position for the life of the mine and process ore or waste delivered by truck Our revolutionary Sizer technology is geared towards lessening energy consumption for your mining operations The Fixed Sizer Station is no exception2022年1月30日 Energy consumption and pollution are current strategic issues that need to be addressed in the mining model and to evaluate the correct operation of the rod mill with potash ore Each batch of(PDF) Rod Mill Product Control and Its Relation to Energy Consumption 2012年6月1日 The industry is producing only the 20 tex and 30 tex cotton yarns It is observed from the study that the 8% of the total energy consumed by the mill has been reduced by applying different (PDF) Investigation of Specific Energy Consumption and 2012年12月1日 Optimization of inmill ball loading and slurry solids concentration in grinding of UG2 ores: A statistical experimental design approach(PDF) Optimization of inmill ball loading and slurry solids
.jpg)
Energy conservation and consumption reduction in grinding
2023年11月1日 Grinding efficiency is the unit energy consumption rate of the mill, which represents the amount of material with a particle size of −0043 mm newly generated for every 1 kW•h of energy consumed by the mill The grinding efficiency was calculated by 2020年6月16日 Request PDF Machine Learning and Deep Learning Methods in Mining Operations: a DataDriven SAG Mill Energy Consumption Prediction Application Semiautogenous grinding mills play a critical Machine Learning and Deep Learning Methods in MiningFrom the breakdown of energy consumption, it was found that comminution accounts for 25% of final energy consumption of an “average” mine site Diesel in mobile equipment accounts for 46%, electricity in mining (ventilation) 15% and other electricity 14%MINING ENERGY CONSUMPTION 2021 CEEC (Coalition for Eco Two major factors contribute to the high unit energy consumption for AG and SAG operations The first is related to variability in the size and competency of rock fed to the mill Mine planning, ore blasting and primary crusher controls, while quite advanced from years ago, are not sufficient to limit the inherent variability that occursAUTOGENOUS MILL FEED PREPARATION TO REDUCE UNIT ENERGY CONSUMPTION
.jpg)
Energy Efficiency Analysis of Copper Ore Ball Mill Drive Systems
4% of global electric energy consumption [3–6] In the United States, the milling process is estimated to account for 05% of the primary energy consumption, 38% of the total electric energy consumption, and 40% of the total energy consumption in the mining industry [7] In Poland, the annual electric energy consumption from copper ore 2002年11月1日 Average ore loss in mining 19%;average ore loss in mineral processing 10% Energy wastage in Mining and Mineral Processing A vast amount of energy is consumed in mining industry, eg, in the USA The energy efficiency of ball milling in comminution2012年7月13日 The production of paper and board is an energy intensive process With an energy use of 64 EJ in 2005, the pulp and paper industry was responsible for about 6 % of the world’s total industrial energy consumption (International Energy Agency (IEA) 2008), being the fourth largest industrial energy user worldwideEnergy prices rose drastically from 2005 until Benchmarking energy use in the paper industry: a benchmarking study 2022年5月9日 Scientific Reports Modeling of energy consumption factors for an industrial cement vertical roller mill by SHAPXGBoost: a "conscious lab" approach Skip to main content Thank you for visiting Modeling of energy consumption factors for an industrial cement
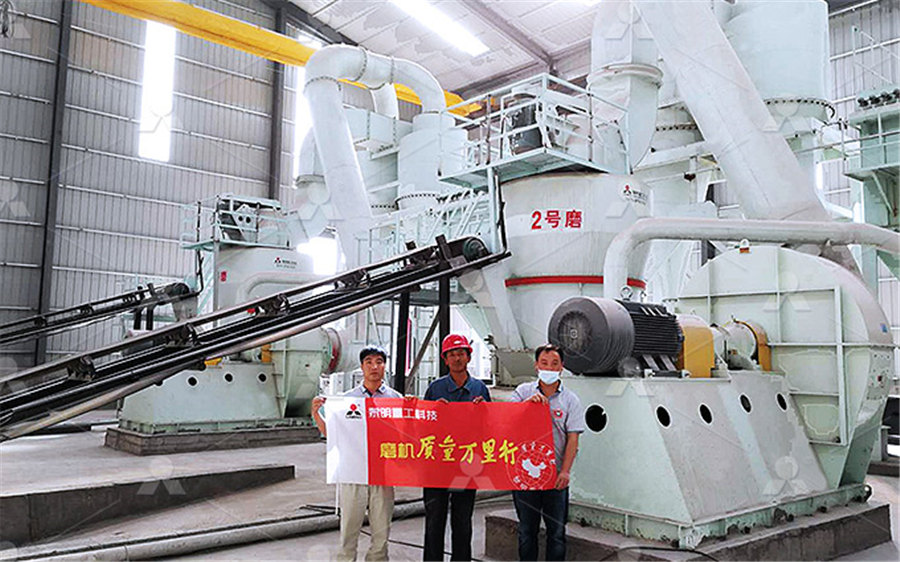
Optimization and Prediction of Specific Energy Consumption
2022年1月12日 In nowadays, improve energy efficiency in the metal cutting industry is one of the main challenges The selection of machining parameters and cooling/lubrication conditions is an important issue to assure better energy efficiency in the milling process The present study explores the influence of three cutting parameters, namely, cooling/lubrication conditions, 2023年12月12日 water consumption required for the mill, u 2 – ore arrival speed, u 3 – percentage of the critical speed of the mill, u 4 – pulp water consumption a nd u 5 – mill incoming pulp(PDF) Control of ball mill operation depending on ball load and ore BREAKING DOWN ENERGY CONSUMPTION IN INDUSTRIAL GRINDING MILLS *Jocelyn Bouchard1, Gilles LeBlanc2, Michelle Levesque3, Peter Radziszewski4, and David GeorgesFilteau1 1 Université Laval BREAKING DOWN ENERGY CONSUMPTION IN INDUSTRIAL GRINDING MILLS2019年7月2日 Iron orebiomass composite is another option to reduce the energy consumption and CO 2 emission in the BF These composites could enhance the reduction of iron oxideModern blast furnace ironmaking technology: potentials to
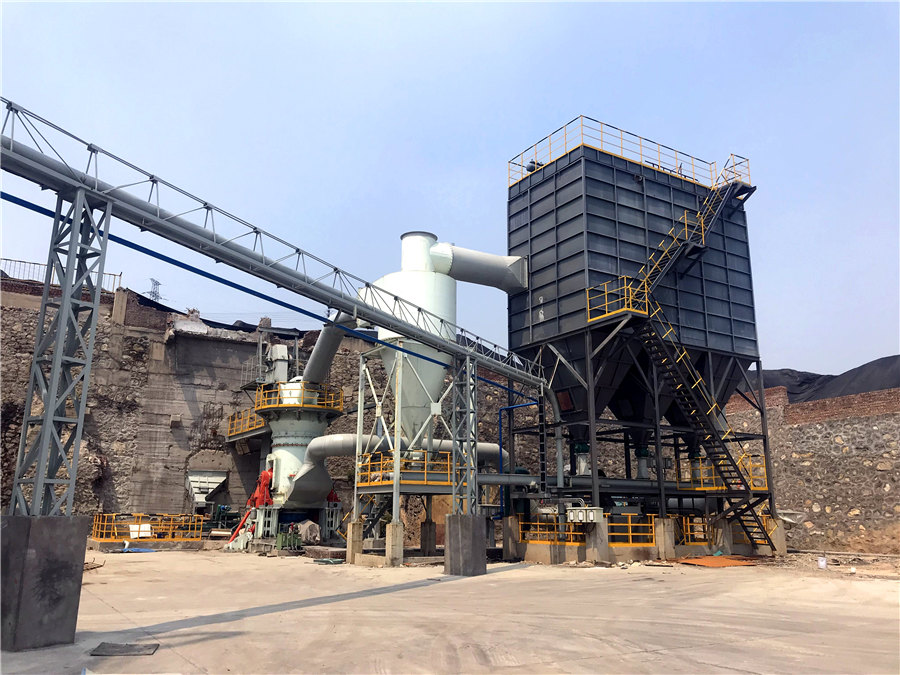
(PDF) Specific Energy Consumption of a Belt Conveyor System
2020年10月13日 Schematic crosssection and a plan view of the lignite surface mine: 1belt conveyor routes, 2excavators, 3spreader; blue linesoverburden mining levels, red lineslignite mining levels, green to reducing energy consumption The literature gives us some clues in this regard: one of th e first conditions controlling the rod mill product is precisely the feed size distribution, and it has been demonstrated that a rod mill achieves the same level of fine particles at a lower energy consumption level [15]Rod Mill Product Control and Its Relation to Energy ConsumptionReducing Grinding Energy and Cost Magnetite Iron Ore Design Case Study A Jankovic and W Valery Metso Process Technology Innovation, PO Box 1028, Eagle Farm Qld, 4009, Australia ABSTRACT:Efficiency of the comminution (PDF) Reducing Grinding Energy and Cost and Geology “St Ivan Rilski”, „, , ANALYTICAL STUDY OF THE ENERGY CONSUMPTION OF DRUM
.jpg)
Title: Benchmarking comminution energy consumption for the
energy consumption and clearly displays the potential energy and cost benefits of moving down the mill power measurements and ore hardness parameters Installed power requirements were obtained from a minerals processing survey published in 2023年4月23日 the grinding media reduces energy and material consumption in a ball mill Different performances are achieved when different sizes and shapes of grinding media are used [ 12 ](PDF) Grinding Media in Ball MillsA Review ResearchGate2013年12月18日 Fine grinding, to P80 sizes as low as 7 μm, is becoming increasingly important as mines treat ores with smaller liberation sizes This grinding is typically done using stirred mills such as the Isamill or Stirred Media Detritor While fine grinding consumes less energy than primary grinding, it can still account for a substantial part of a mill’s energy budget Overall Energy Use of Fine Grinding in Mineral Processing2022年3月15日 tics for Ores for Ball Mill Modelling Australias Inst Min Metall, 286, 3139 and the power (kW), which are used to determine the energy consumption of the mill [4 (PDF) Power consumption management and simulation of
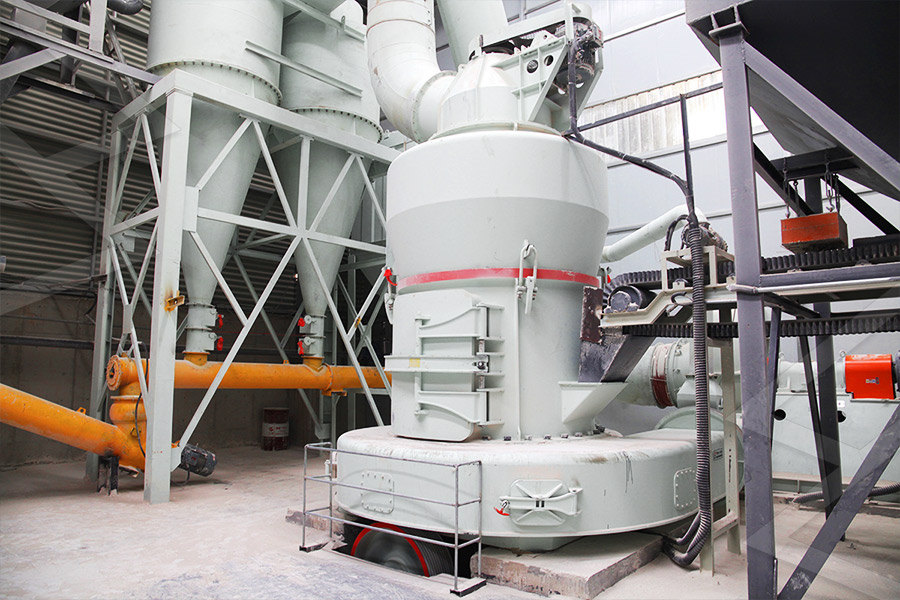
ITP Mining: Improving Energy Efficiency in SAG Mills
Improving Energy Efficiency in SAG Mills PilotScale SAG Mill Facility Will Help to Optimize Charge Motion and Slurry Flow in PlantScale SAG Mills Reducing Energy Consumption The US mining industry operates approximately 80 semiautogenous grinding mills (SAG) throughout the United States Both mine and mill site variables determine SAGwater consumption required for the mill, u2– ore arrival speed, u3 – percentage of the critical speed of the mill, u4 – pulp water consumption and u5– mill incoming pulp consumption Output parameters can be controlled by these variable values[3,5]: x1 the mass fraction of the product whose particle sizeControl of ball mill operation depending on ball load and ore energy consumption Comminution is generally the single largest consumer of energy on a mine site, accounting for an average of a 53% (CEEC the future, 2012) The average grade of ores is falling in most places in the mining industry, resulting in even higher costs, due to higher energy consumption per unit of metal productionModelling SAG milling power and specific energy consumption ores *Adam Mc Elroy1, Dr Caroline Woywadt2, Bruno Kovacs2 1 Boliden Mineral AB Finnforsvägen 4 Kankberg mill and mill circuit specific energy consumption for AG and VRM Feed AG VRM VRM VRM/AG P80 circuitMoisture millcircuit Drying µm kWh/t% kWh/t kWh/t % 45 2,0 5337,6 40,6 9,4 21,6Vertical Roller Mills used for the comminution of mineral ores
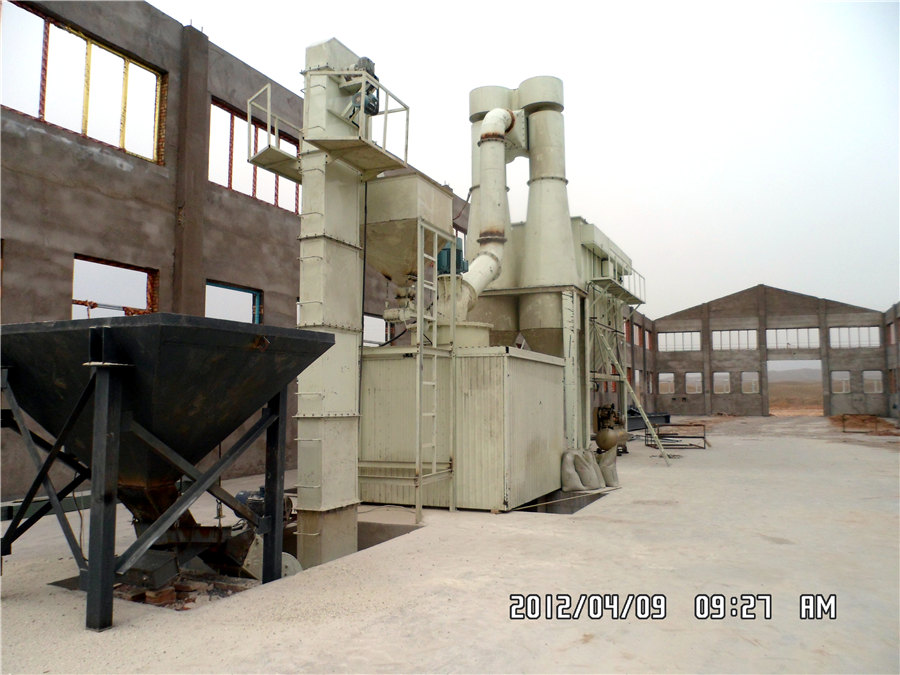
Energy Efficiency Analysis of Copper Ore Ball Mill
2021年2月26日 Milling is among the most energyconsuming technological stages of copper ore processing It is performed in mills, which are machines of high rotational masses The start of a mill filled to capacity requires 2023年9月1日 This study examines energy consumption as a function of ore grade decline for Nickel, Cobalt, and platinum group metals (PGMs), using simulations created with HSC Chemistry software A limit of recovery and are within the same order of magnitude As shown in Table 3, the highest energy consumption is from Ball Mill 1, Limit of recovery: How future evolution of ore grades could Reducing Grinding Energy and Cost Magnetite Iron Ore Design Case Study A Jankovic and W Valery Metso Process Technology Innovation, PO Box 1028, Eagle Farm Qld, 4009, AustraliaReducing Grinding Energy and Cost Magnetite Iron Ore2001年8月1日 Discrete element method (DEM) modelling has been used to systematically study the effects of changes in mill operating parameters and particle properties on the charge shape and power draw of a 5 Charge behaviour and power consumption in ball mills: Sensitivity
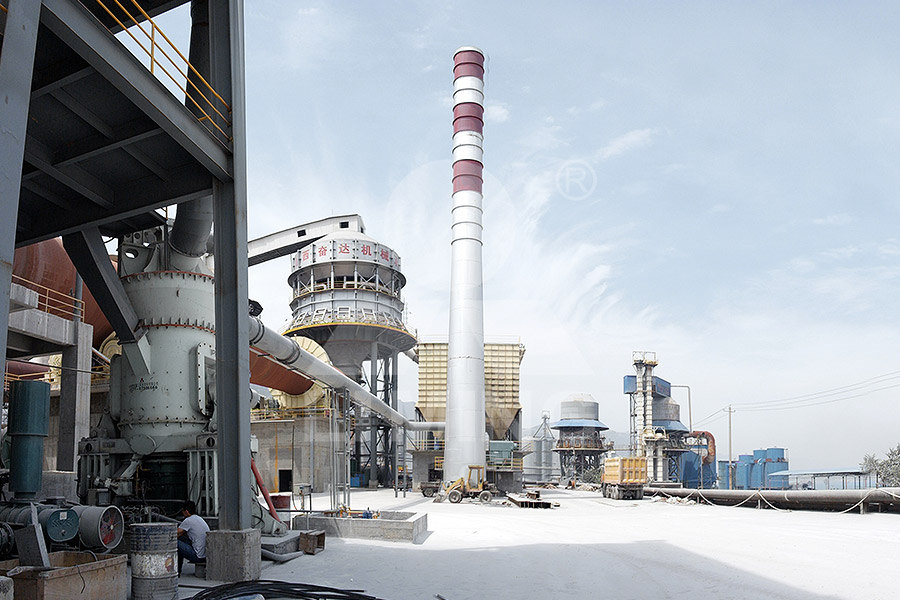
Improvement of methods to ensure energy efficiency of ball mills
2023年8月21日 increasing energy consumption with increasing mill productivity The increase in the mass of ball mills occurs due to the crushed material supplied to the mill ore and pulp2014年11月28日 An analysis during an energy audit at Wesfrob Mines Ltd (now closed) showed that the relationship between specific electricity consumption (kW h/tonne) and throughput for the total operation as well as for the separate crushing and grinding stages was inversely related (Doyle, 1979); energy savings at the mill could be achieved either by increasing the amount of The link between operational practices and specific energy consumption 3RZGHU 7HFKQRORJ\ , 1 Introduction Grinding operation is the last preparation stage before beneficiation In this stage, the material undergoes the combined action of impact andEnergy conservation and consumption reduction in grinding 2020年7月24日 The energy consumption of grinding is the subject of many studies, especially in the case of ball mills for grinding clinkers [8, 9], fuels [10], iron ore [11], hematite ore [12], sulfide ore [13 Determination of granulometrical composition of the clinker
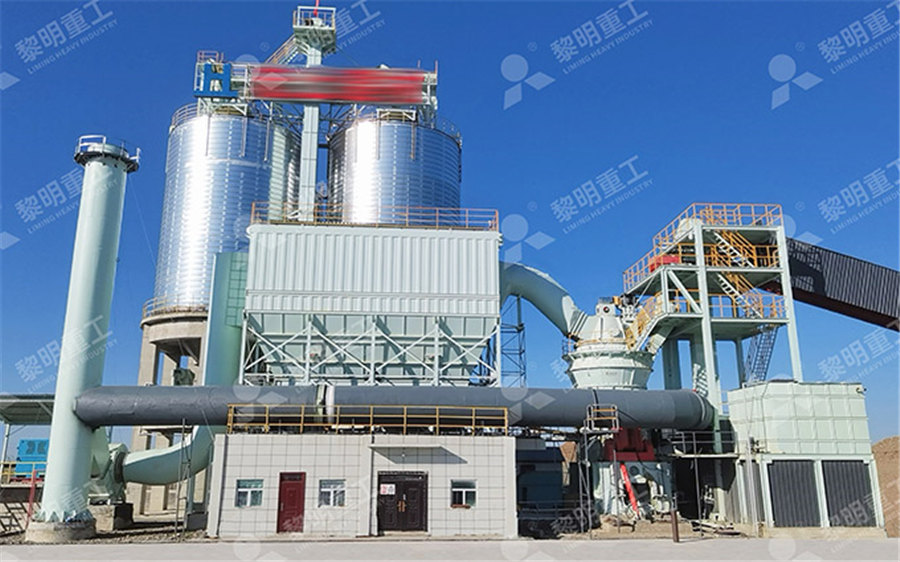
Breaking down energy consumption in industrial grinding mills
2019年11月15日 Semantic Scholar extracted view of "Breaking down energy consumption in industrial grinding mills" by J Bouchard et al Building a model of the impact grinding mechanism in a tumbling mill based on data The link between operational practices and specific energy consumption in metal ore milling plants – Ontario experiences