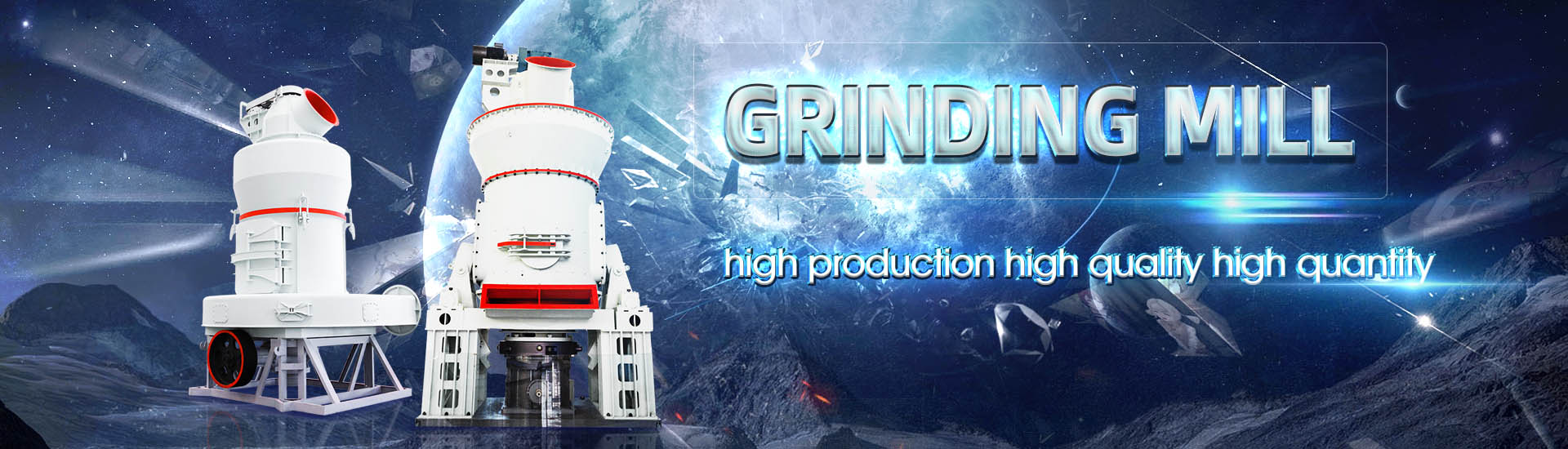
HOME→Details of cement grinding station production license application Management rules Cement grinding station production license application rules
Details of cement grinding station production license application Management rules Cement grinding station production license application rules
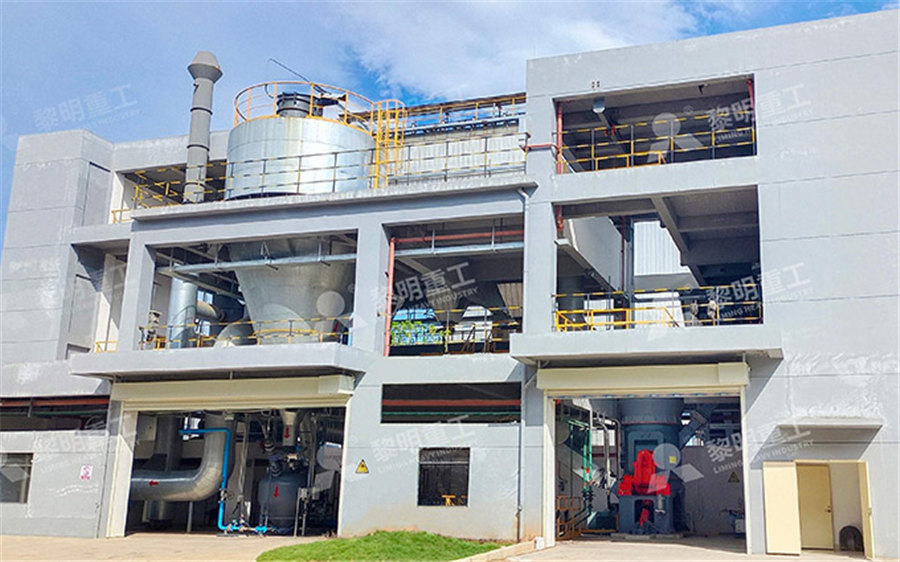
Concrete Sustainability Council
Cement grinding stations: Cement production in cement grinding plants is performed by cogrinding clinker and gypsum in dedicated mills (eg ball mills, vertical roller mills), and by 2017年5月19日 PDF Grinding is an essential operation in cement production given that it permits to obtain fine powder which reacts quickly with water, sets in few Find, read and Overview of cement grinding: fundamentals, additives, technologiesAll plants must have an environmental management system in place to ensure that all environmental impacts and risks are effectively managed and mitigated Integrated cement Cement Environmental Directive Holcimoptimization of cement grinding operation in ball mills Several energy efficient options for cement grinding are available today such as vertical roller mills, roller presses (typically in combination OPTIMIZATION OF CEMENT GRINDING OPERATION IN BALL MILLS
.jpg)
Process technology for efficient and sustainable cement production
2015年12月1日 While vertical roller mills (VRMs) are predominantly used for raw material grinding, different types of grinding systems are used for the finish grinding of cement VRMs Raw material and cement grinding are the first and the last major process steps during cement production The energy demand of these two processes amounts to up to ~70% of the Grinding Technology in Cement ProductionIn this article, we will describe how cement is made with six cement manufacturing process stages There are six main stages of the cement manufacturing process The raw cement How Cement is Made Cement Manufacturing Process2019年1月3日 Clinker grinding technology is the most energyintensive process in cement manufacturing Traditionally, it was treated as "low on technology" and "high on energy" as Clinker grinding technology in cement manufacturing
.jpg)
Cement Grinding Unit Process High Quality Cement Grinding
Explore Amrit Cement's stateoftheart cement grinding unit Learn about our cement grinding process and plant stages for high quality cement2016年10月5日 1 Introduction Cement is an energyintensive industry in which the grinding circuits use more than 60 % of the total electrical energy consumed and account for most of the manufacturing cost []The requirements for the EnergyEfficient Technologies in Cement GrindingCement grinding unit, or called cement grinding plant, cement grinding station is an individual step in the cement production line In the grinding plant, the cement clinker is added with the proper amount of mixed materials for grinding to Cement Grinding Unit Cement Grinding PlantApplication: mine industry, cement plant, cement grinding station, is an individual grinding plant in the finished cement production Cement grinding plants are primarily used to produce finished cement products by grinding cement Cement Grinding Plant CHAENG
.jpg)
(PDF) Review of the Effect of Grinding Aids and Admixtures on the
2023年11月6日 The influence of the GAs incorporation in cement grinding on properties such as workability and setting times of the placed concrete and/or mortar has been covered in this review2017年12月19日 Diamond grinding of Portland cement concrete (PCC) pavement surfaces, a maintenance operation carried out to remove irregularities, generates a highpH, highalkalinity slurry (water, concrete Characterisation and management of concrete grinding residuals2023年5月24日 Text mining and association rulesbased analysis of 245 cement production accidents in a and the themes are named according to the application Management license, contract Text mining and association rulesbased analysis of 245 cement Raw material and cement grinding are the first and the last major process steps during cement production The energy demand of these two processes amounts to up to ~70% of the electrical energy used in a cement plant For you as participant, this training will help to obtain a better understanding of the comminution processes as well as the equipment used for grindingGrinding Technology in Cement Production
.jpg)
Cement Grinding Station FTM Machinery
Advantages : It can make 1,000 tons to 6,000 tons of cement per day It can finish the jobs of grinding and packaging cement Case Description: Cement grinding station is one production unit of cement finished products, which doesn't include the last finished stage of the cement production processCost Savings: While there may be initial investments in setting up a cement grinding station, the longterm benefits include reduced energy costs, increased production efficiency, and potential savings on raw material usage Customization and Adaptability: Cement grinding stations can be customized to meet specific production requirementsCement Grinding Plants Cement Grinding Unit Cement Grinding Station2023年7月19日 Commons Attribu tion License 40 For over 60 years technological additives used in process of grinding cement Application of and reduce the production cost to a great extent Cement (PDF) Intensifying the cement grinding processLarge cement plants usually include both clinker production lines and cement grinding lines, but there are also independent grinding plants that are only responsible for grinding and processing clinker into finished cement products Cement Grinding Plant Expert Cement Grinding
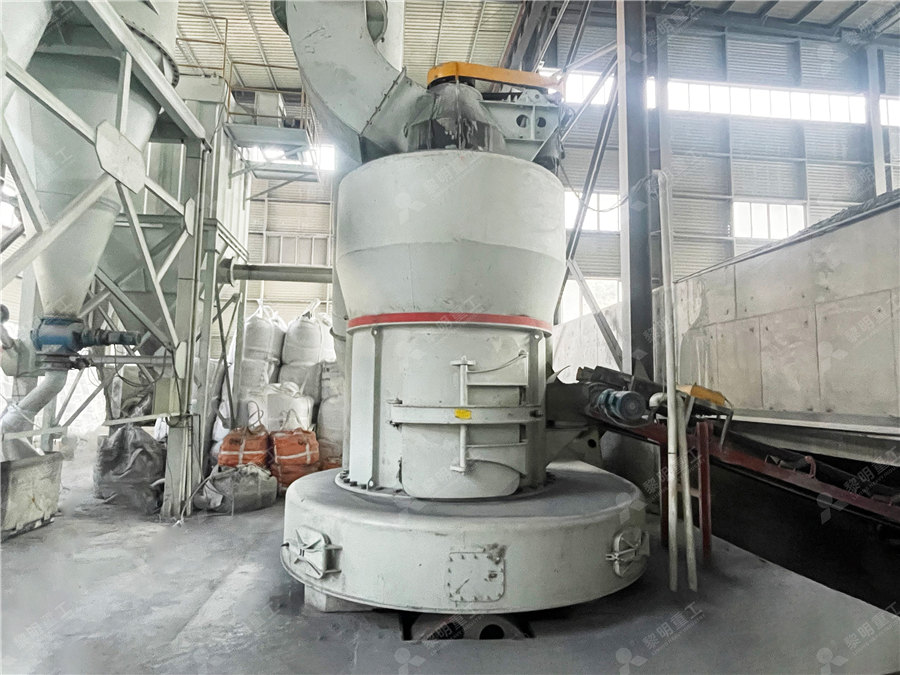
New Features of Cement Grinding Station Design
2024年6月14日 If the cement grinding station and clinker production line are set near the limestone mine, unnecessary transportation expenses of cement mixture will be incurred Therefore, the cement grinding station is built near the sales Stage 2: Grinding, Proportioning, and Blending The crushed raw ingredients are made ready for the cementmaking process in the kiln by combining them with additives and grinding them to ensure a fine homogenous mixture The composition of cement is proportioned here depending on the desired properties of the cement Generally, limestone is 80%, and the remaining 20% How Cement is Made Cement Manufacturing Process2020年5月1日 of raw meal grinding production line, clinker calcination production line and cement grinding station, the manager can grasp the quality information in the cement production process in real time Design and implementation of quality management system for cement Therefore, this paper decides to use the cement specific surface area, which reflects the cement product quality, and the unit power consumption, which reflects the production efficiency, as the objective functions, with the 14 variables selected in Table 1 as the decision variables to optimize the cement grinding processDOUDCGAN: Optimization of cement grinding operational
.jpg)
Global database of cement production assets and upstream
2023年10月13日 Owing to their largescale use, production of cement and concrete results in substantial emission of greenhouse gases and places strain on the availability of natural resources, such as water2020年2月1日 Also, the results demonstrated that cement production rate increases (185–224 t/h) and the electrical consumption decreases (411–331 kWh/t) when cement fineness decreases (3250 cm²/g–2820 Energy and exergy analyses for a cement ball mill of a new 2018年8月1日 GAs incorporation in cement grinding enhance enlargement of the separation distance between cement particles as they get adsorbed on the surface of cement particles which reduces agglomeration and Effect of Grinding Aids in Cement Grinding ResearchGate2023年10月19日 Clinker is a critical component in the production of cement and forms the intermediate product during the cement manufacturing process It can be best described as a nodular material, usually grayish in color, which is produced by sintering limestone and aluminosilicate materials such as clay at high temperatures in a cement kilnUnderstanding the Role of Clinker Grinding in Cement Production
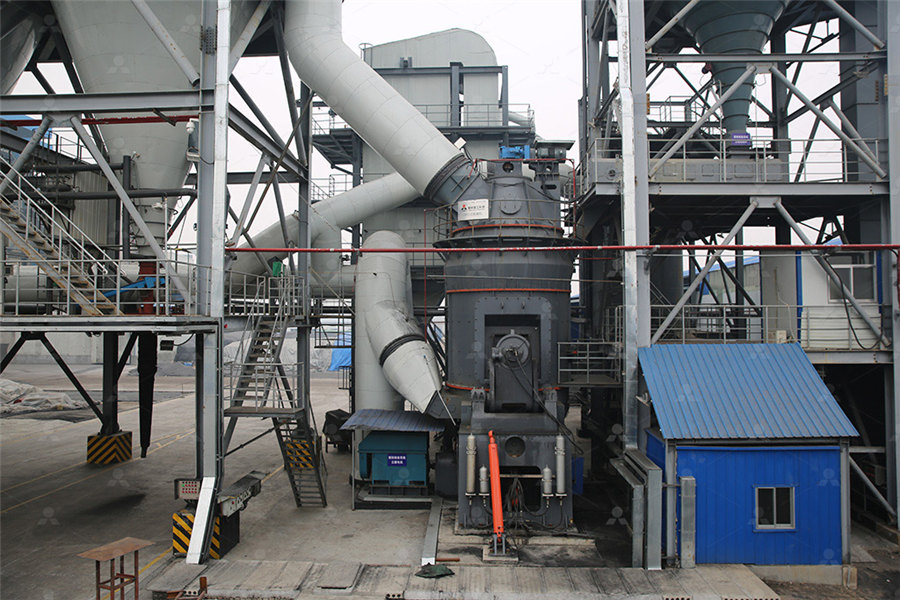
Modular Mobile Cement Grinding Plant For Sale
Exfactory price cement grinding units for sale! AGICO Cement offers EPC cement grinding station projects with more than 20 years of experience Feel free to contact us! AGICO Cement is a Chinese company that specialized in Grinding aids are primarily used to reduce energy consumption by increasing grinding efficiency and mill productivity Better dry powder dispersion of the ground cement increases mill productivity and cement fineness for the same energy consumption, and produces improvement in flow, leading to faster unloading and improved storage volume of bulk cement storagePhysical Chemical Mechanisms of Cement Grinding AidsTechnical personnel are designing the optimal cement grinding station program for you The cement grinding station equipment are assembled here The cement grinding station equipment are processed and shaped here Storage the cement grinding stationThe production of cement, generally can be divided into raw meal preparation, clinker calcining and finished cement three processes, etc Silicate cement production technology is representative in the cement production, is a limestone and clay as the main raw material, through crushing, ingredients, which takes limestone and clay as the main raw materials, through crushing, Cement Grinding StationHenan Zhongke Engineering
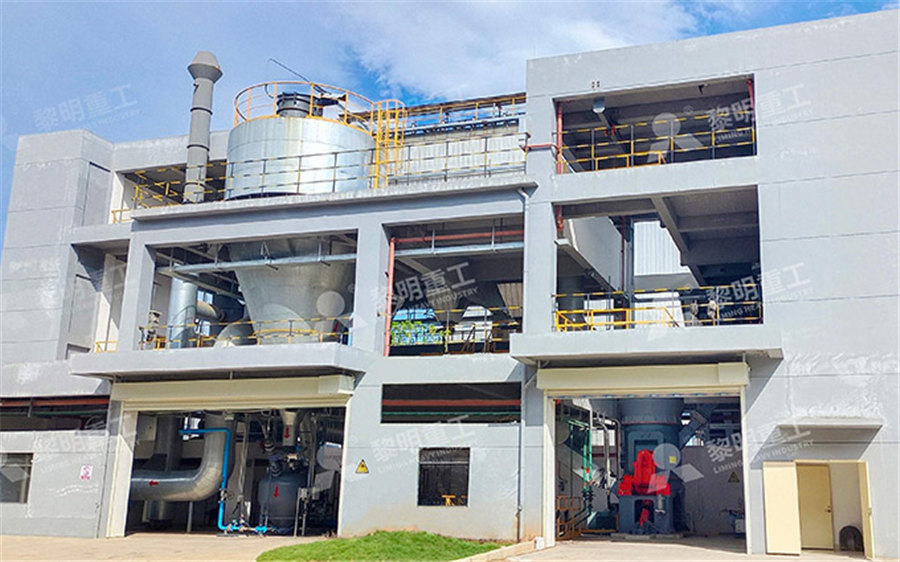
Cement manufacturing process PPT Free Download SlideShare
2014年6月10日 This document discusses Portland cement and the cement manufacturing process It begins with an overview of what cement is and how it is used to make concrete It then describes the industrial process for manufacturing cement, involving grinding raw materials like limestone and clay at high temperatures in a kiln to form clinker, which is then pulverized with The layout of cement production is to establish cement clinker production lines in mining areas and cement grinding stations near cement sales markets to reduce transportation costs If the clinker production line is built near a city, about 16 tons of cement raw material will be needed for every 1 ton of clinker produced, which will increase transportation costs by 60%Cement Grinding StationHongji Mining Machinery2018年10月10日 Heat transfer in cement production with raw mill considering the minimum temperature difference 1Hot composite curve; 2cold composite curve, 3heat exchangers (developed after [30])Heat Integration in a Cement Production ResearchGate2004年11月1日 For all dry grinding applications, cement production is certainly the most important The estimate for the world energy consumption for cement production is 187 TWh which is approximately 002% of total world energy consumption per yearThe world consumption of cement was about 172 billion tonnes in 2002 and it is increasing at about 1% per annumCement grinding optimisation ScienceDirect
.jpg)
(PDF) Analysis of material flow and consumption in cement production
2015年8月1日 The results show that approximately 248t, 469t, and 341t of materials are required to produce a ton of the product in raw material preparation, clinker production, and cement grinding stages PDF On Dec 9, 2015, Momen Marwan Mohsen published Cement Manufacturing Find, read and cite all the research you need on ResearchGate(PDF) Cement Manufacturing ResearchGate2009年6月1日 In this study, the milling of clinker was evaluated by varying the mill speed (24 and 72 RPM), residence time (3 and 5 hours) and grinding media load (30 and 40 %) in a ball millCement clinker grinding: Evaluation of mill spin speed, 2020年9月9日 Italian cement industries are among the major cement producers in the European panorama In the last decades, because of the increasingly stringent specifications on environmental impact and energy saving, technology in the cement plant has been significantly improved []In this context, Advanced Process Control (APC) systems have become the Optimization of the Clinker Production Phase in a Cement
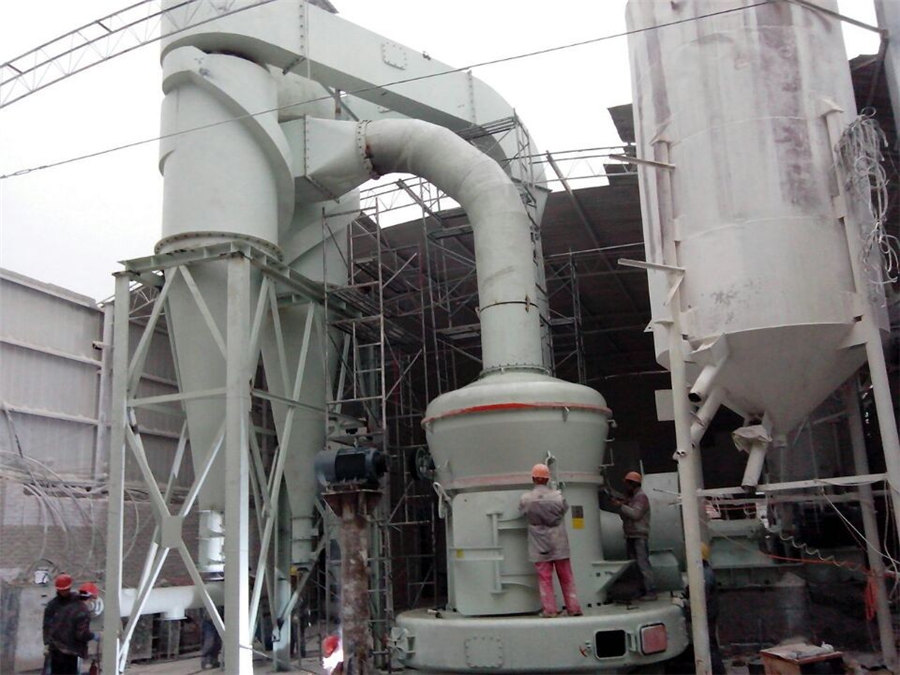
Analysis on Influencing Factors of Grinding Aid Effect of Cement
2021年2月1日 (Characteristics of different cement grinding aids and their effects on cement properties Cement, 2011,(10))P1316 Hu Penggang and Feng Yun (On the application and popularization of cement 2024年11月23日 Cement Extraction, Processing, Manufacturing: Raw materials employed in the manufacture of cement are extracted by quarrying in the case of hard rocks such as limestones, slates, and some shales, with the aid of blasting when necessary Some deposits are mined by underground methods Softer rocks such as chalk and clay can be dug directly by Cement Extraction, Processing, Manufacturing Britannicaof cement production accidents, and establishes cement accident causation analysis model to provide a basis for current safety management decisions Firstly, 245 accident records were collected to Text mining and association rulesbased analysis of 245 cement 2009年5月1日 Fig 5 shows the FTIR spectra of ground muscovite, TEA, and muscovite ground with 2000 g/t TEA The stretching vibration band of OH is detected between 3000 and 3600 cm 1 in the FTIR spectrum of Characterization of Various Cement Grinding Aids and their
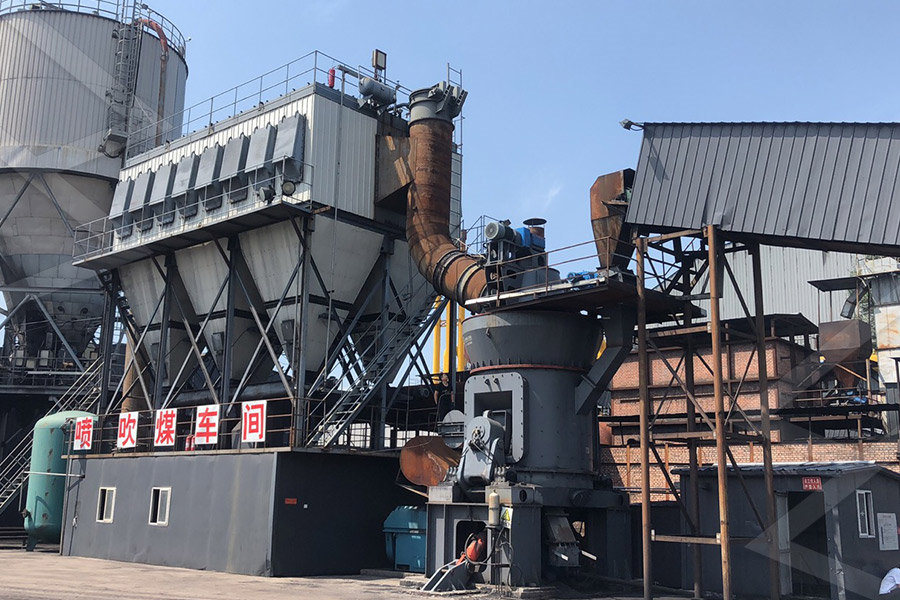
Cement grinding capacity expansion Indian Cement Review
2021年7月1日 The clinker quality assessment can best be done by Lab Ball Mill grinding of day average clinker with mineral gypsum (with SO3 of the lab ground cement targeted at 22 to 24 with fixed grinding time to achieve Blaine’s of around 300320 M2/kg with the residue on 45 microns of the cement in range of 18 per cent to 20 per cent, at this fineness, the clinker is 2014年12月11日 The cement grinding facility, which makes the bulk of cement made in Botswana, is operated by South Africa's PPC under a local subsidiary, PPC Botswana This 04Mt/yr facility is the result of a plan that dates back to the 1980s that sought to establish an integrated cement plant close to a limestone reserve at NakalaPhalaThe cement industries of southern Africa2020年8月25日 Clinker storage capacity can be based on the market, and a cement plant usually stores 525% of the annual clinker production Cement grinding: For spare parts: size and dimensions, material and weight, and your drawings with details, you can send the drawing to t Production Process Cement Manufacturing Process AGICO CEMENTSemantic Scholar extracted view of "Cement grinding optimisation" by A Jankovic et al In this study the process flow diagram for the cement production was simulated using Aspen HYSYS 88 software to achieve high energy optimization and optimum cement flow rate by Application of comminution and classification modelling to grinding of [PDF] Cement grinding optimisation Semantic Scholar