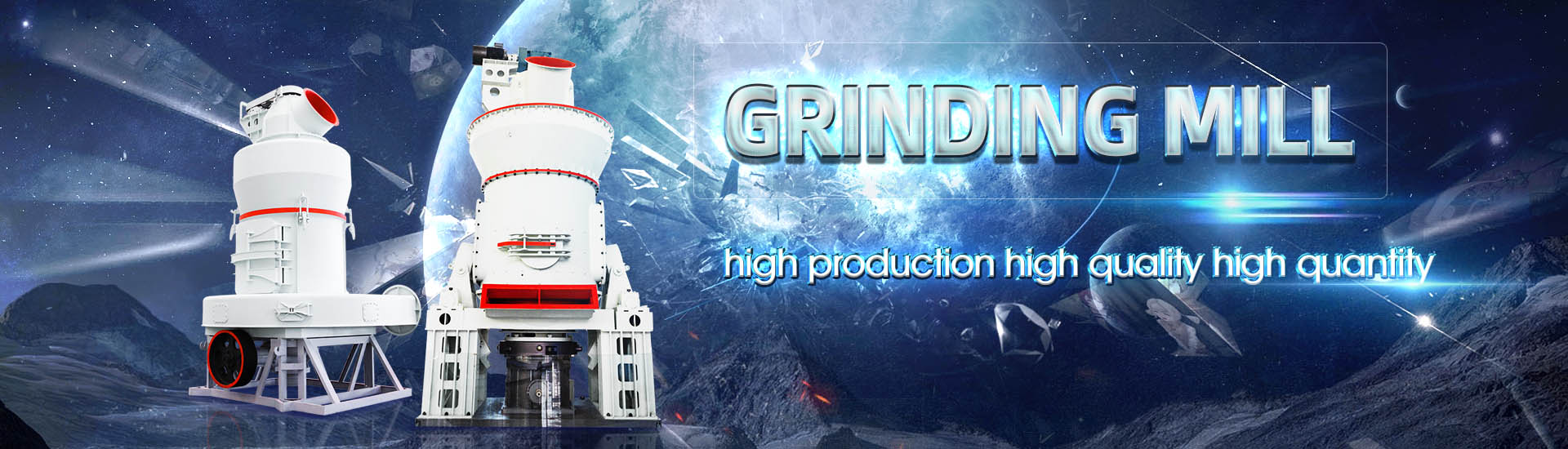
Electrolytic manganese mill
.jpg)
Electrolytic manganese residue to metal phosphides via ball
2023年11月30日 Electrolytic manganese residue (EMR) is an industrial solid waste generated during the electrolytic manganese production process [8] However, improper handling of EMR 2024年6月13日 The Electrolytic Manganese Residue (EMR) is a byproduct of the electrolytic manganese metal (EMM) industry, containing high concentrations of potential pollutants such Study on harmless treatment of electrolytic manganese residue by 2024年3月5日 The reclamation and reuse of electrolytic manganese residue (EMR) as a bulk hazard solid waste are limited by its residual ammonia nitrogen (NH 4 +N) and manganese Enhanced green remediation and refinement disposal of 电解锰残渣 (EMR) 由于释放锰 (Mn) 和铵态氮 (NHN) 而造成严重的环境风险。 本研究介绍了一种利用腐殖质和氢氧化钠 (NaOH) 组合对 EMR 进行无害化处理和资源化的方法,并从渗滤液中 深入了解从电解锰渣 (EMR) 中回收 Mn 和 Mg 去除 Mn 和 NH4
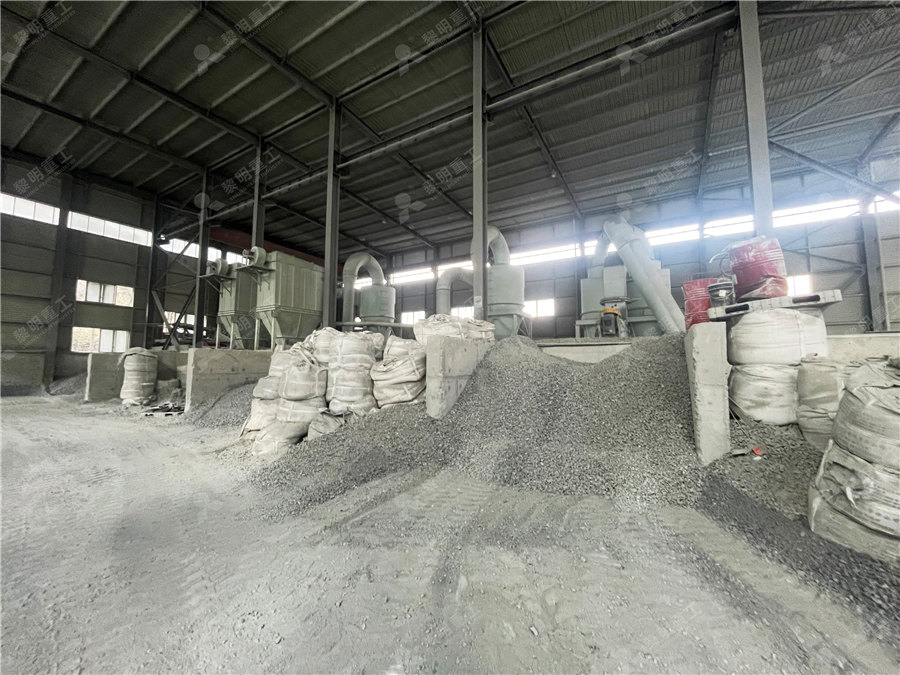
Progress in comprehensive utilization of electrolytic manganese
Electrolytic manganese residue (EMR) is a solid waste produced in the process of electrolytic manganese metal (EMM) production In recent years, the accumulation of EMR has caused Electrolytic Manganese Residue (EMR) is a secondary material generated during the process of manganese production, poses significant environmental challenges, including land Innovative Techniques for Electrolytic Manganese Residue MDPI2023年12月1日 Enhanced green remediation and refinement disposal of electrolytic manganese residue using airjet milling and horizontalshaking leaching The massive stockpiling of Enhanced green remediation and refinement disposal of 2021年8月5日 This research aimed to address the issue of residual manganese in electrolytic manganese residue (EMR), which is difficult to recycle and can easily become an Selective recovery of manganese from electrolytic manganese
.jpg)
Production assessment in the electrolytic manganese metal
2012年2月2日 In this paper, based on the practice of manganese production in China, a preliminary life cycle assessment (LCA) of the electrolytic manganese industry is provided, 2012年2月2日 Production assessment in the electrolytic manganese metal industry in China Volume 108 Issue 78 Skip to main content Accessibility help We use cookies to distinguish you from other users and to provide you with a better experience on our websitesProduction assessment in the electrolytic manganese metal Electrolytic manganese slag is a filtered acid residue produced by treating manganese ore with sulfuric acid during the production of electrolytic metallic manganese from manganese carbonate ore It is acidic or weakly alkaline, with a density between 23g/cm3 and a Where is electrolytic manganese slag used? What is the harmless 2023年3月8日 Electrolytic manganese residue (EMR) is a solid waste produced in the process of electrolytic manganese metal (EMM) production In recent years, the accumulation of EMR has caused increasingly serious environmental problems To better understand the state of EMR recycling in recent years, this paper used a comprehensive literature database to conduct a Progress in comprehensive utilization of electrolytic manganese
.jpg)
Electrolytic Manganese Dioxide CSIRNML
Electrolytic Manganese Dioxide 2 IPR Status 3 Application/Uses In dry batteries 4 Salient Technical Features including Competing Features Process utilizes sulphuric acid for leaching, utlilizes low and medium grade manganese ores, equipments are indigenously available 5 Level/Scale of Development 50Kg/Day 6 Environmental Considerations2024年3月20日 Electrolytic manganese residue (EMR) is a mixed filter slag generated during electrolytic metal manganese (EMM) production the EMR filter cake was dried and then ground for 60 s using a ZM1B vibratory mill The rhodochrosite is an ore mud after wet grinding, Efficient leaching of manganese from electrolytic manganese 2016年12月31日 The rapid development of the manganese electrolysis industry is accompanied by the production of large quantities of electrolytic manganese anode mud (EMAM), the valueadded reuse of which is Treatment and Characterization Analysis of Electrolytic Manganese 2016年5月1日 Electrolytic manganese metal production from manganese carbonate precipitate @article{Lu2016ElectrolyticMM, title={Electrolytic manganese metal production from manganese carbonate precipitate}, author={Jianming Lu and David Dreisinger and Thomas Gl{\"u}ck}, journal={Hydrometallurgy}, year={2016} Electrolytic manganese metal production from manganese
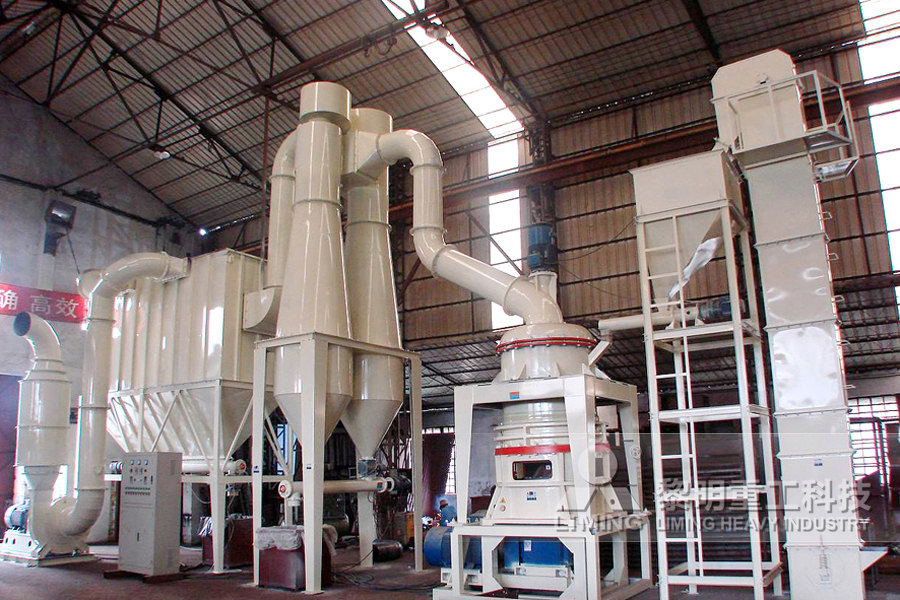
How is Manganese Processed: An InDepth Exploration M
2024年4月9日 Manganese of technical purity (95–998% Mn) is called metallic and is obtained by electrosilicothermic and electrolytic methods Carbonate manganese ores, containing 190194% of Mn, or carbonate concentrates, containing 2425% of Mn, are the starting raw materials for producing of metallic manganeseManganese ore excavated from the mine is ground into powder by using manganese powder Raymond mill, which is called manganese powder The metallic manganese obtained by electrolysis after the manganese powder is treated with sulfuric acid and other chemical materials is called “electrolytic manganese”How Can Manganese Powder Be Refined Into Electrolytic Manganese The system for producing an electrolytic manganese metal according to claim 1, wherein the liquid preparation unit comprises a Raymond mill for preparing manganese ore from 80 to 130 mesh, and preparing the pyrite a Raymond mill of 80 130 mesh pyrite powder, a leaching tank with a mixer, a heating boiler, a temperature control device and a primary pressure filter device; Manufacturing system for producing electrolytic manganese 2023年10月1日 In China, manganese is a significant chemical raw material (Jouini et al, 2020)Electrolytic manganese slag (EMS) is one of the most significant solid wastes created during the electrolysis of manganese (Tang et al, 2019); for every 10 ton of manganese metal produced, 10−20 tons of EMS are produced (Zhang et al, 2019)Electrolytic manganese is Remediation of arsenic contaminated water and soil using
.jpg)
Life cycle assessment of electrolytic manganese metal production
2020年4月20日 As an important metal element, manganese (Mn) is widely used in industrial fields, such as the steel (Elliott et al, 2018), dry cell batteries (Yamaguchi et al, 2018), and specialty chemical industries (Lu et al, 2014)Most of Mn ore is directly or indirectly consumed by steel production (USGS, 2018)In recent years, with the development of the steel industry and A process for the production of electrolytic manganese dioxide, the process comprising the method steps of: (i) Reducing a manganese dioxide containing ore to produce a manganese oxide product; either directly or via the wet Process for the production of electrolytic 1990年1月1日 The process flowsheet for the production of electrolytic manganese metal, as developed by the National metallurgical laboratoiy on per tonne of electrolytic manganese dioxide (90 % 2 minimum) Quantity per tonne of90%MnO9 L Raw materials: Manganese ore (based on 50% Mn) Sulphuric acid Energy: (a) Electrolysis All other operations, including PILOT PLANT STUDIES FOR THE PRODUCTION OF ELECTROLYTIC MANGANESE 2021年3月1日 Request PDF Selective recovery of manganese from electrolytic manganese residue by using water as extractant under mechanochemical ball grinding: Mechanism and kinetics This research aimed to Selective recovery of manganese from electrolytic manganese
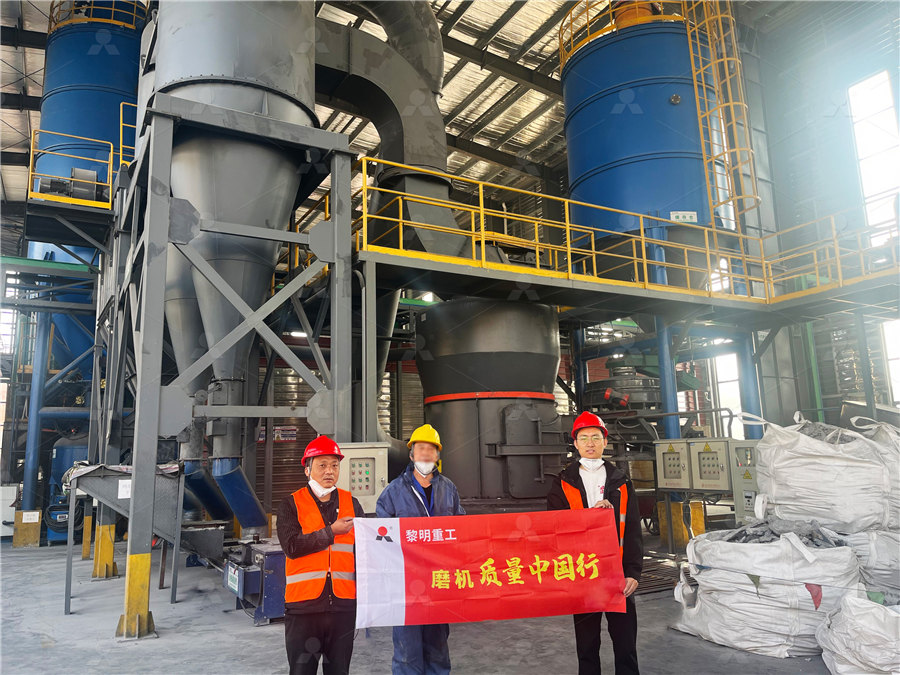
Treatment and Characterization Analysis of Electrolytic Manganese
2016年1月1日 This research aims at providing the basic database for reasonable treatment of electrolytic manganese anode slime by comparing its composition, After grinding electrolytic manganese anode slime in the mechanical rod mill for 30 min, add a small amount of dodecyl benzene sulfonic acid sodium into the mill, 2020年8月20日 PDF The aim of this paper is to study the feasibility of using an electrolytic manganese residue (EMR) as modified asphalt energy ball mill After grinding for 25 min and 50 min, theElectrolytic Manganese ResidueModified Asphalt Performance The invention relates to a production method of electrolytic manganese dioxide, F Carrying out powder grinding on the rinsed electrolytic manganese dioxide; sending the rinsed electrolytic manganese dioxide to a swing Raymond mill for milling, and collecting product powder (the particle size is 325 meshes) Production method of electrolytic manganese dioxideElectrolytic manganese metal (EMM) is a significant basic material used in metallurgy, aerospace, chemistry, etc Then the dried residue was ground using a ball mill and sieved through an 80 mesh screen for experiments Refering to the standard of Carbonation precipitation of manganese from electrolytic manganese
.jpg)
Innovative cotreatment technology for effective disposal of
2023年10月15日 Electrolytic manganese residue (EMR) stockpiles contain significant amounts of Mn 2+ and NH 4 +N which pose a risk of environmental pollutionFor EMR safe disposal, an innovative approach is proposed that involves direct sodium silicatesodium hydroxide (Na 2 SiO 3 –NaOH) collaborative technology This approach utilises Na 2 SiO 3 and NaOH as the 2024年6月1日 Manganese (Mn) is a metallic element in transitional group located in the fourth cycle and group VIIB of the periodic table Mn is hard but fragile and has a melting point of 1246 °C (Sun et al, 2020)In terms of chemical properties, the monomers of Mn are reflected that Mn readily is oxidized by oxygen under heating conditions, and are dissolved in dilute sulfuric acidImprovement of manganese electrolytic process and secondary ganese dioxide is electrolytic manganese dioxideEMD Though anodic oxidation of Mn2* salt to manganese dioxide goes back to 1830, yet the The slurry from the ball mill is then leached with the depleated electrolyte from the EMD cells, to which make up acid (98% sulphuric acid or 30% hydrochloric acid) is addedEXECUTIVE SUMMARY DSIRfirst electrolytic manganese metal in South Africa was produced from manganese ore in 1954 The experimental cell consisted of two cathodes and three anodes, each Wilcox vertical spindle mill Production rates of 10 tjh have been achieved from this airswept mill at a fineness of 80 per cent minus 74 (Lm TABLE IThe production of electrolytic manganese in South Africa
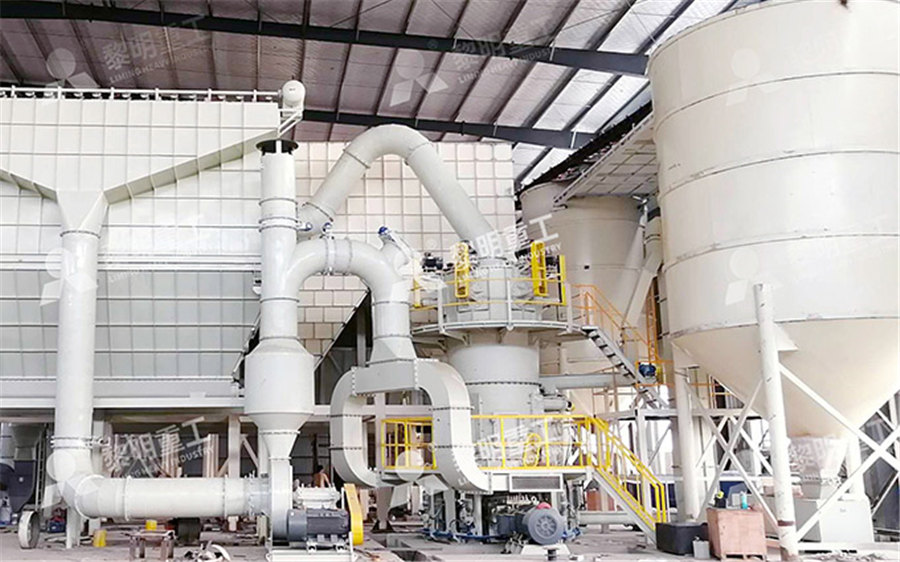
Electrolytic manganese residue and red mud cotreatment:
Electrolytic manganese residue (EMR), the industrial waste residue from the manufacturing process of electrolytic metallic manganese (EMM) Phosphorus and potassium recovery from anaerobically digested olive mill wastewater using modified zeolite, fly ash and zeolitic fly ash: a comparative study2007年11月1日 PDF Electrolytic manganese is an important alloying element for aluminium and steel melts Site B was a rolling mill facility that used manganese alloys free of selenium, Selenium in electrolytic manganese as a reference material for 2013年6月1日 Electrolytic manganese residue (EMR) is a solid waste found in filters after sulphuric acid leaching of manganese carbonate ore, MnO 2 oxidative deferrisation and lime neutralisation Approximately 6–7 tons of residue is discharged into the environment per ton of electrolytic manganese product [4]The accumulated amount of EMR during the past years is Preparation of electrolytic manganese residue–ground 2024年3月5日 Electrolytic manganese metal plays a pivotal role in steel, alloy, and electronic materials production [40], [46]Due to the imperative demands of economic and social development, the rapid growth in demand for manganese ore has resulted in an exceptional level of consumption, particularly evident within China [9], [11]China is currently the largest Enhanced green remediation and refinement disposal of electrolytic
.jpg)
Electrolytic manganese metal production from manganese
2016年5月1日 Sulfur dioxide was first used to produce electrolytic manganese commercially with a reasonable current efficiency (60–65%) The effects of SO 2 are: (1) increasing the overpotential of hydrogen evolution and hence the manganese current efficiency; (2) promoting the formation of stable αmanganese, (3) counteracting the harmful effects of impurities, and (4) suppressing which contains between 28 to 48% manganese, and thus the sustainability of this industry is important for renewing the growth of the South African economy (Chamber of Mines of South Africa, 2016) Manganese sales increased by nearly 140% and production by almost 40% between 2016 and 2017 Manganese prices accelerated by 20% over the same periodSustainable Production of Electrolytic Manganese Dioxide (EMD)first electrolytic manganese metal inSouth Africa was produced frommanganese orein1954Theexperimental cellconsisted oftwo cathodes and three anodes, each Wilcox vertical spindle mill Production rates of10tjh havebeenachieved fromthisairswept millatafineness of80percentminus 74(Lm TABLEI TYPICAL ANALYSIS OFMANGANESE ORE % 48,0 10,0 Theproduction ofelectrolytic manganese in SouthAfrica SAIMM2021年9月15日 Electrolytic manganese residue (EMR) has become a barrier to the sustainable development of the electrolytic metallic manganese (EMM) industry EMR has a great potential to harm local ecosystems and human health, due to it contains high concentrations of soluble pollutant, especially NH 4 + and Mn 2+, and also the possible dam break risk because of its A critical review on approaches for electrolytic manganese
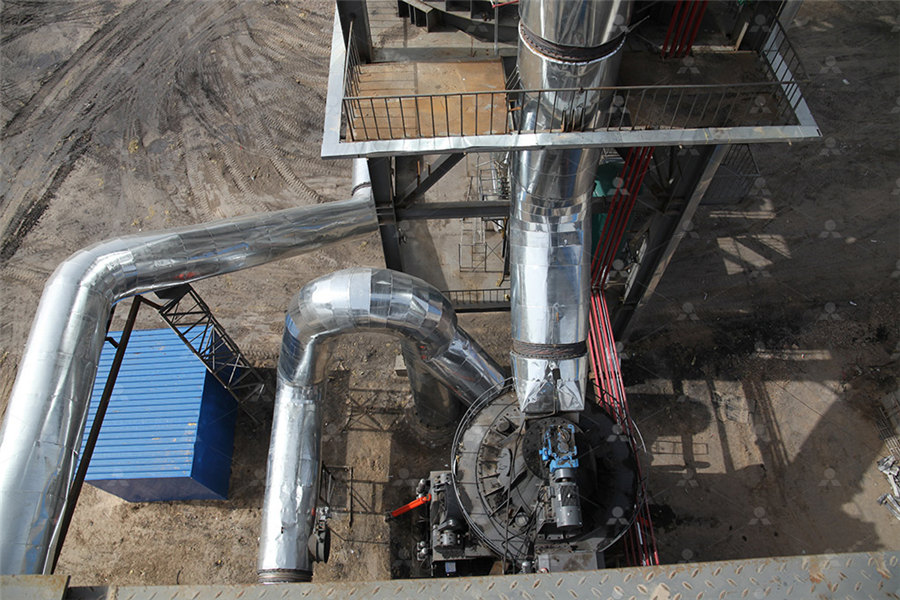
Study on harmless treatment of electrolytic manganese
The Electrolytic Manganese Residue (EMR) is a byproduct of the electrolytic manganese metal (EMM) industry, containing quently, the dried EMR underwent grinding using a ball mill and sieving through a 100mesh sieve, with a sieve margin of less than 2%2023年11月1日 Electrolytic manganese is produced by leaching manganese ore with sulfuric acid; gypsum is produced by the reaction of CaMg(CO 3) EMR, whereby the Mn is enriched and recovered Subsequently, the EMR powder is processed using a highpressure roller mill, powder separator, and ball mill Finally, Remediation treatment and resource utilization trends of electrolytic HCM's HC1700 vertical pendulum Raymond mill, HLM series manganese carbonate vertical mill and other equipment have a high reputation in manganese ore enterprises all over the world market share, the following two types of electrolytic manganese powder grinding mill equipment will be introduced to youNews How to choose the electrolytic manganese powder grinding mill Electrolytic manganese metal (EMM) is a significant basic material used in metallurgy, Then the dried residue was ground using a ball mill and sieved through an 80 meshCarbonation precipitation of manganese from electrolytic manganese
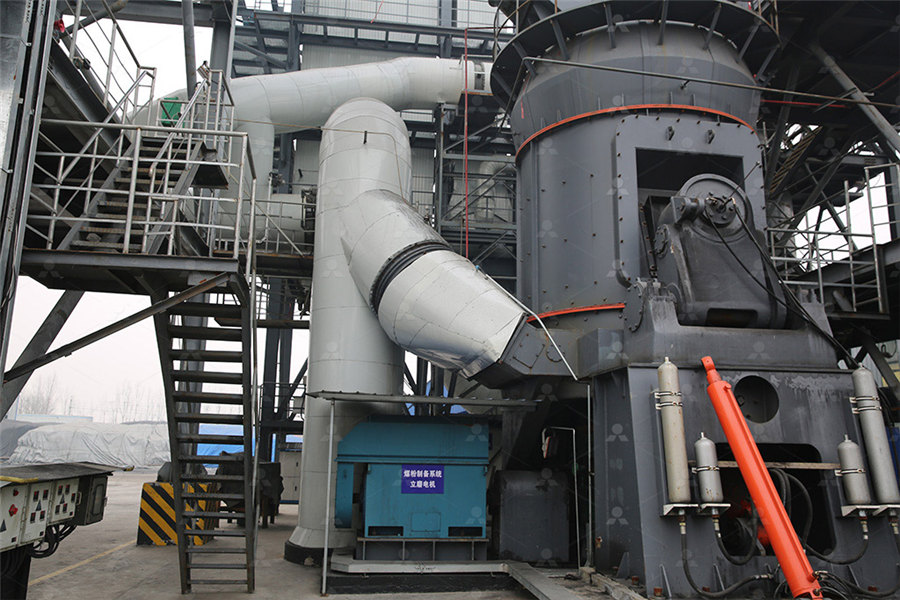
Study on harmless treatment of electrolytic manganese residue
2024年1月19日 33 electrolytic manganese metal (EMM), contributing over 97% to the global production (Du et al 2014) Electrolytic 74 ball mill and sieving through a 100mesh sieve, 2022年10月1日 Electrolytic manganese residue (EMR) is the waste slag generated from the electrolysis manganese industry As a promising exploitable adsorbent, EMR has become a hot research topic However, EMR’s low adsorption capacity has limited its applications as an efficient adsorbent In this study, the EMR was mixed with serpentine and calcined (at 800 °C for 2 h) A novel electrolyticmanganeseresiduesandserpentinebased 2024年3月21日 Liet al [21] calcined electrolytic manganese slag mixed CG, and FA were all dried in an oven at 105 C for 4 h and ground in a ball mill for 60 min before being cooled to room temperature; the materials were sieved using a 100 mesh sieve before being set aside (2) Synthesis of Electrolytic Manganese Slag Solid WasteBased manganese processing, preparation of the ore for use in various products Manganese (Mn) is a hard, silvery white metal with a melting point of 1,244 °C (2,271 °F) Ordinarily too brittle to be of structural value itself, it is an essential agent in steelmaking, in which it removes impurities such as sulfur and oxygen and adds important physical properties to the metalManganese processing Extraction, Uses Benefits Britannica