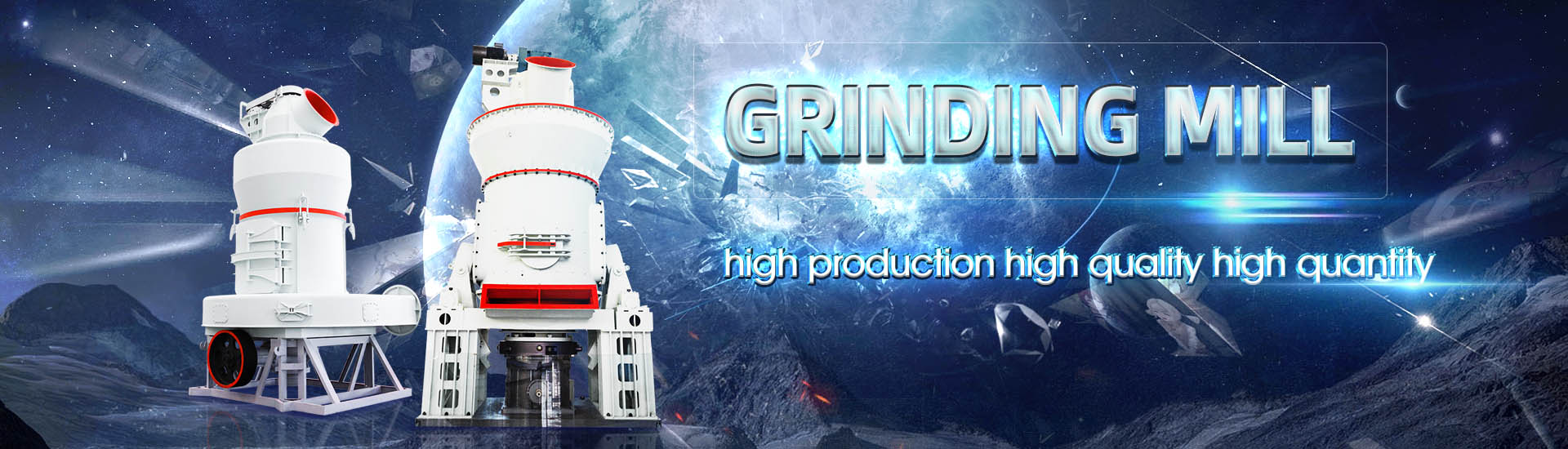
Calcite ore rotary kiln
.jpg)
Clay calcination technology: stateoftheart review by the RILEM
This paper, produced by RILEM TC 282CCL on calcined clays as supplementary cementitious materials (working group 2), focuses on the production of calcined clays, presents an overview 2021年12月20日 This paper, produced by RILEM TC 282CCL on calcined clays as supplementary cementitious materials (working group 2), focuses on the production of calcined clays, presents an overview of clayClay calcination technology: stateoftheart review by 2023年2月25日 The rotary kiln is employed in different solid processes including drying, incineration, heating, calcination, pyrolysis, soil remediation, and waste reduction This Rotary kiln process: An overview of physical mechanisms, models 2023年3月1日 All the previous literature studied electrically heated rotary calciner with external heating This work presents a novel design of an electrical rotary calciner through which Novel design of a rotary calciner internally heated with electrical
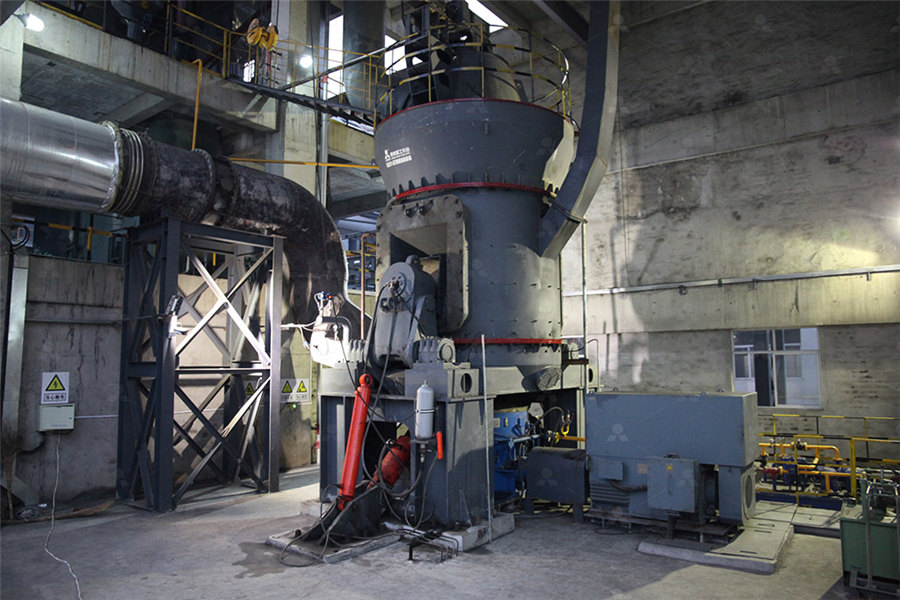
(PDF) CFD Modelling of Calcination in a Rotary Lime Kiln
2022年8月1日 A 2D axisymmetric computational fluid dynamics (CFD) model, coupled to a 1D bed model, has been developed to capture the key processes that occur within rotary lime kilns2017年3月2日 Rotary kiln is important equipment in heavy industries and its calcination process is the key impact to the product quality Due to the difficulty in obtaining the accurate algebraic Modeling for the Calcination Process of Industry Rotary Kiln Using 1981年10月22日 Limestone Calcination in a Rotary Kiln AP WATKINSON and J K BRIMACOMBE An experimental study of the calcination of limestone has been carried out in a Limestone calcination in a rotary kiln Springer2022年8月1日 Therefore, the objective of this work is to develop a detailed heat transfer model of both dry and wet rotary lime kilns, including the modelling of the calcination reaction, to determine where calcination starts in the kiln, as well CFD Modelling of Calcination in a Rotary Lime Kiln
[GYQ0R)ZQ]ESS4NJ.jpg)
The Aerodynamics of an Iron Ore Pelletizing Rotary
2022年5月5日 The heat transfer in an iron ore rotary kiln, both with and without a bed of pellets present, was modeled in fullscale and three dimensions by Gunnarsson et al [41, 42] using2023年2月25日 The rotary kiln is used in many solid processes, including drying, incineration, heating, cooling, humidification, calcination and reduction This widespread application can be attributed to factors such as the ability to handle varied loads, with large variations in particle size [1]The rotary kiln is a slightly inclined steel cylinder that rests on supports (bearing rollers) Rotary kiln process: An overview of physical mechanisms, models 2023年11月20日 Rotary kilnelectric furnace (RKEF) technology accounts for 95 pct of the lateritic nickel ore processing Coal is commonly used as fuel and reducing agent in the rotary kiln to produce solid reduction product which is then melted in the electric furnace The use of coal in the process leads to the emission of approximately 70 tons of CO2 for every 1 ton of nickel in The Impacts of Temperature, Gas Composition and Reaction2019年9月3日 Industrially, the pyrometallurgical treatment of laterites is mostly accomplished with a wellestablished method, namely, the rotary kiln–electric arc furnace (RKEF) process, which includes (PDF) Nickel Laterite Smelting Processes and Some ResearchGate
.jpg)
Rotary kiln process: An overview of physical mechanisms, models
2023年2月25日 As the rotary kiln rotates, solid particles within the kiln undergo movement Researchers have proposed corresponding predictive models, as shown in Table 2 (Bisulandu and Huchet, 2023) YL Wu et al (2018) studied a pilotscale rotary kiln that can be directly heated and found a characteristic Ushaped in temperature distribution around the kiln's cylinder2015年11月26日 Coproduction of DRI Powder and Semicoke from Siderite Ore and Low Rank Coal by Excessive Coalbased Direct Reduction in Rotary Kiln November 2015 ISIJ International 56(1)(PDF) Coproduction of DRI Powder and Semicoke from Siderite Ore THE ROTARY KILN IN THE METALLURGICAL INDUSTRY About 1900, various metallurgists were experimenting with the rotary kiln for nodulizing fluedust, fine iron ores, etc Edison conducted experiments, for example, on the fine concentrates obtained from his magnetic separators Within a few years plants were established for this purpose(PDF) History of the rotary kiln Fathi Habashi Academia2024年5月23日 After understanding, the local cement industry is relatively close to raw material resources (rich in calcite ore), with convenient transportation and sufficient water resources Subsequently, they are transferred back to the rotary kiln and calcined at temperatures between 1200°C and 1500°C until partially melted, Calcite: A Key Ingredient in Efficient Cement Manufacturing
.jpg)
Rotary Kiln Plant Manufacturer,Beneficiation Plant
Rotary kiln calcination plants are large, custombuilt facilities They utilize long, steel cylinders lined with firebrick to rotate materials under intense heat, driving off undesired elements like water or CO2Download scientific diagram Magnetization roasting process of iron ores in the rotary kiln from publication: Recent Advances in Magnetization Roasting of Refractory Iron Ores: A Technological Magnetization roasting process of iron ores in the rotary kilnKINC Mineral Technologies Pvt Ltd is established in the year 2004 with turnover 100 million, established as a leading Manufacturer, Exporter, Wholesaler and Distributor of Wet Grinding Mill that characterizes adequate force for reducing mineral to particles of the require size at the desirable speed in terms of rpm and rate of feedWet Grinding Mill Manufacturer,Grinding Mill Supplier,Exporter2019年12月26日 Rotary Kiln satyendra; December 26, 2019; For example, in the kiln used for iron ore reduction, lowiron alumina or magnesium – spinel bricks are used, while in a cement kiln usually magnesite brick lining in the clinker Rotary Kiln IspatGuru
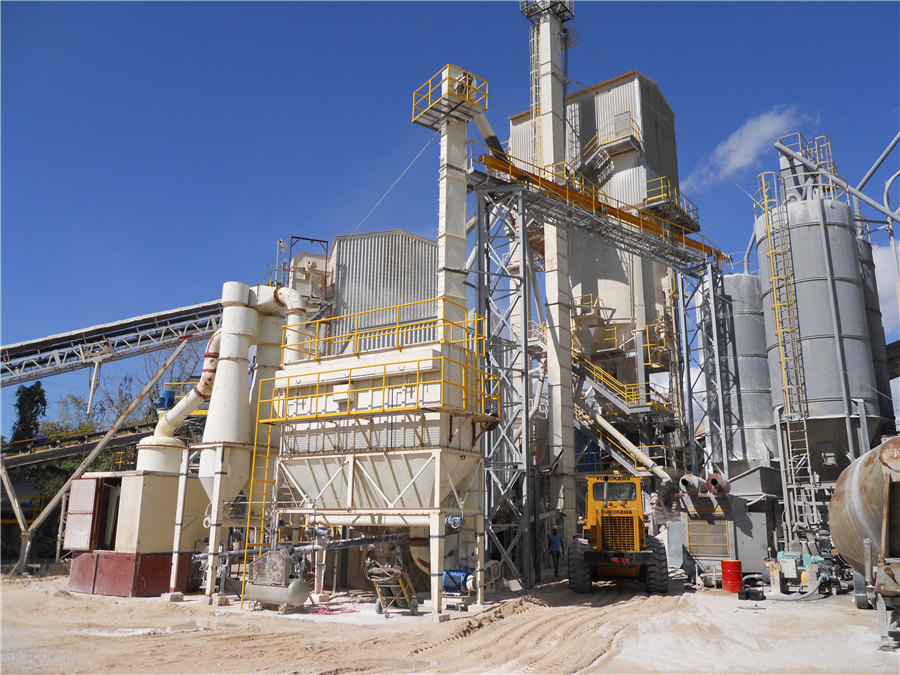
The Deposit Formation Mechanism in CoalFired
2021年8月17日 The depositforming problem is one of the main bottlenecks restricting the yield and production benefit of iron ore pellets produced by coalfired rotary kilnsPerformance of Dolomite Calcination in a BenchScale Rotary Kiln × Close Log In Log in On "Evaluation of Process conditions for Magnesium Production from Dolomite Ore Using CALPHAD Method dolomite decomposed directly to CaCO3, accompanied by the formation of MgO between 550 and 765∘C Calcite decomposed to CaO between 900 and Performance of Dolomite Calcination in a BenchScale Rotary Kiln2021年9月16日 The primary pyrometallurgical route to produce ferronickel from laterite nickel ores is the Rotary KilnElectric Furnace (RKEF) process In the RKEF process, (PDF) Improving the rotary kilnelectric furnace process for 2020年4月2日 In this study, sulfuric acid leaching and gravity shakingtable separation by shaking a table are used to extract lead and zinc from a PbZn oxidizing roasting cinder The oxidizing roasting cinder—containing 169% Pb, 305% Zn, 103% Fe and 251% S—was obtained from a PbZn sulfide ore in the Hanyuan area of China by a flotationrotary kiln Extraction of Lead and Zinc from a Rotary Kiln Oxidizing MDPI
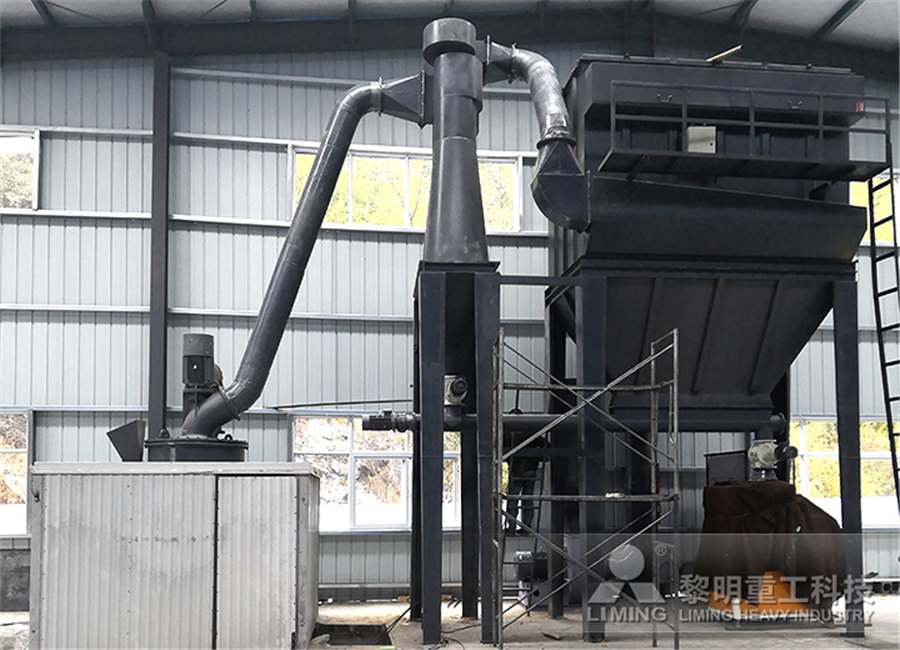
The Aerodynamics of an Iron Ore Pelletizing Rotary Kiln MDPI
2022年5月5日 The pelletizing process, where the crude ore from the mine is upgraded, involves several steps, including grinding, balling, and induration; see Figure 1 to the left In the gratekiln induration process []—see Figure 1 to the right—the sintering is mainly taking place in a rotary kiln, where the pellets increase their strength and metallurgical properties2016年3月30日 In book: Encyclopedia of Iron, Steel, and Their Alloys (pppp 10821108) Chapter: i) Direct Reduced Iron: Production; Publisher: CRC Press, Taylor and Francis Group, New York(PDF) i) Direct Reduced Iron: Production ResearchGateRequest PDF On Feb 1, 2021, Sanghun Lee and others published Feasibility of Applying a Rotary Kiln to Roast Vanadium in Domestic TitaniumMagnetite Ore Find, read and cite all the research Feasibility of Applying a Rotary Kiln to Roast Vanadium in Spodumene ore naturally occurs in the crystal structure of monoclinic alpha form (αform) In order to extract lithium from the ore via the leaching process, however, the ore’s crystal structure must be in the tetragonal beta form (βform)¹ This conversion is achieved through decrepitation, or the shattering of the crystal structureThe Role of Calcination in the Extraction of Lithium from Spodumene
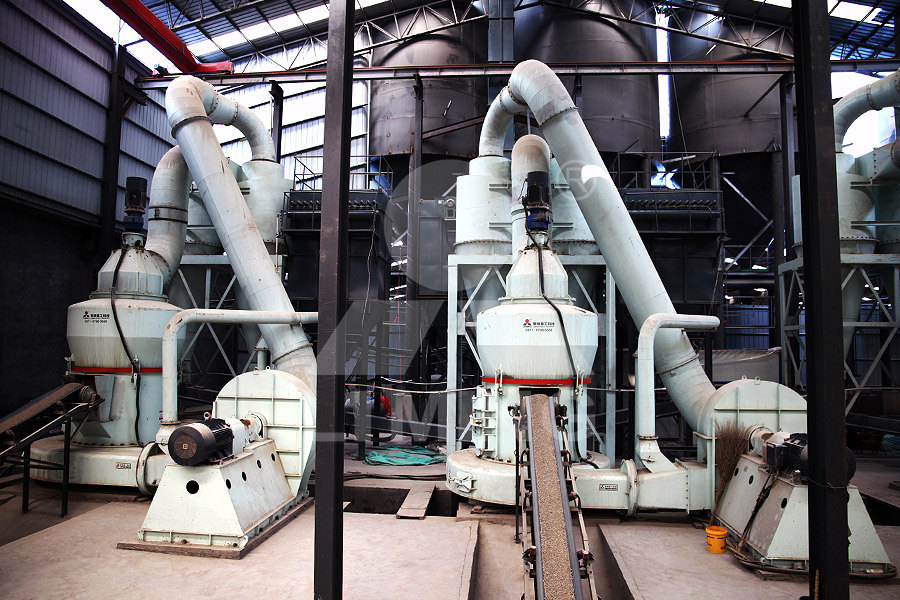
Rotary Kiln in MagneticReduction Roasting
2020年2月14日 Of the many different conditions that affect roasting, a major one is the size of feed With no special preparation of the ore fines, a rotary kiln is able to handle ores with a larger proportion of fines than a shaft furnace or traveling Deposit formation in the coalfired rotary kiln is frequently found in the production of fluxed iron ore pellets by the gratekiln process and affects normal production In this paper, the effects of pellet basicity (CaO/SiO2 mass ratio) on the simulated deposit formation were investigated The results show that the porosity of deposits samples increases from 308 to 415% as the pellet Effects of Pellet Basicity on the Simulated Deposit Formation in 2022年8月1日 A 2D axisymmetric computational fluid dynamics (CFD) model, coupled to a 1D bed model, has been developed to capture the key processes that occur within rotary lime kilns The model simulates the calcination CFD Modelling of Calcination in a Rotary Lime KilnThis work analyzes the heat transfer conditions in a rotary kiln used for the heat treatment of iron ore pellets in the gratekiln process The analysis concerns conditions relevant to fuel switching from coal to hydrogen gas A modeling assessment of the radiative heat transfer in the kiln is conducted including the pellet bed and inner kiln wall temperature conditions The results Heat Transfer Conditions in HydrogenFired Rotary Kilns for Iron Ore

Rotary kiln for producing ferronickel from Indonesia Sulawesi
The utility model provides a rotary kiln for producing ferronickel from Indonesia Sulawesi nickel laterite ore through RKEF technical processing The rotary kiln comprises a kiln body and a bracket provided with riding wheels to support the kiln body, wherein a drive and transmission device enabling the kiln body to rotate on the riding wheels is arranged on the bracket; the kiln 2012年11月15日 The mechanism of SR (SlagRing) formation in the actual rotary kiln that proposed in the previous paper has been examined by the firing experiment of the anthracite and limestone composite Niore briquettes using the batch type experimental kiln The rapid increases in the degree of reduction and CO gas content and the sticking begin to take place at about Ring Formation in the Smelting of Saprolite Niore in a Rotary Kiln 3D Rotary Kiln Dam Rendering FEECO Rotary Kilns at Production Plant Rotary Kiln in Fabrication Indirect Rotary Kiln System Supply Rotary Kiln Inspection in Progress DirectFired Batch Kiln for Rotary Kiln Testing Thermocouples in a batch rotary kiln Red mud samples taken during rotary kiln testing Batch indirect rotary kiln used for testingRotary Kilns FEECO International Inc2020年11月16日 The NOx reduction in the iron ore pelletizing process becomes an important environmental concern owing to its role in the formation of photochemical smog and acid rain Thus, it is essential to develop new technologies for reducing NOx emissions in order to contribute to the cleaner production of pellets In this paper, NOx reduction by advanced reburning NOx Emission Reduction by Advanced Reburning in GrateRotary Kiln
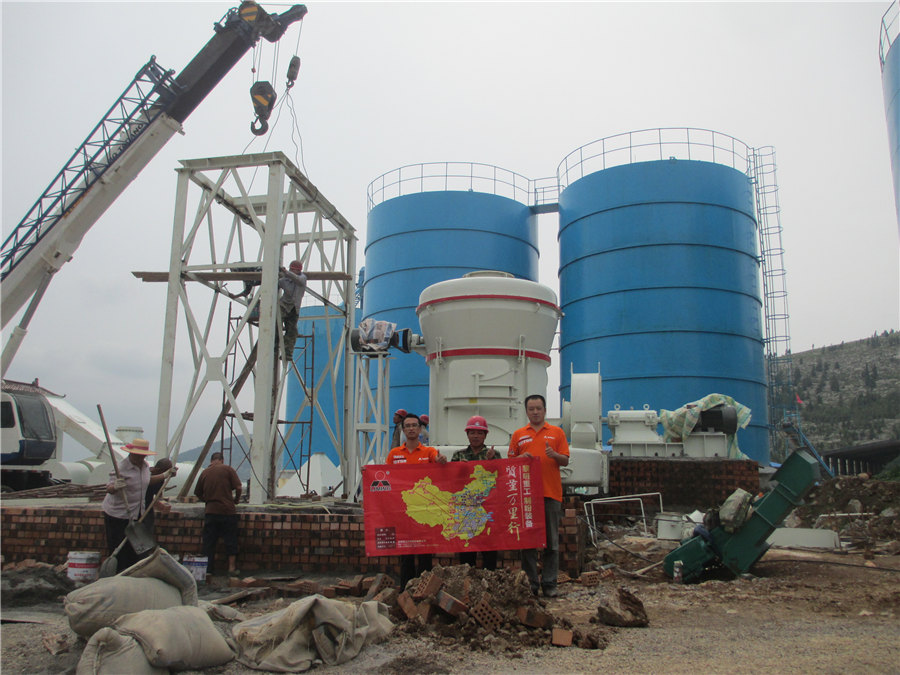
Thermal Treatment of Mercury Mine Wastes Using a Rotary Solar Kiln
2014年1月28日 Thermal desorption, by a rotary kiln of mercury contaminated soil and mine wastes has been used in order to volatilize mercury from the contaminated medium2022年5月1日 Large and ParticleScale Energy Assessment of Reduction Roasting of Nickel Laterite Ore for Ferronickel Production via the Rotary KilnElectric Furnace Process May 2022 Thermal Science and (PDF) Large and ParticleScale Energy Assessment of2023年1月19日 Tsuji H (2012) Behavior of reduction and growth of metal in smelting of saprolite Niore in a rotary kiln for production of ferronickel alloy ISIJ Int 52(6):1000–1009 Article Google Scholar Kobayashi Y, Todoroki H, Tsuji H An Overview of Nickel Utilization from Laterite Ore2015年6月25日 Using an integrated method of calcination (performed in a rotary kiln) and shaking table for concentrating the lowgrade phosphate ore, the results show promise at producing grades of 3077% P2O5 Beneficiation of LowGrade Phosphate Deposits by a
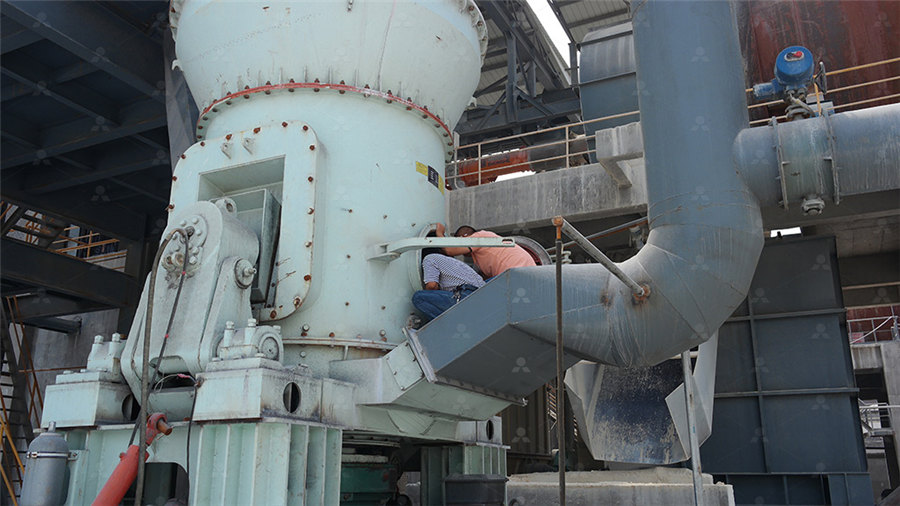
Coprocessing of StainlessSteel Pickling Sludge with Laterite Ore
2020年6月1日 KruppRenn process is an energysaving technology for ferronickel production from saprolitic laterite ores, in which a semifused zone (1 3001 350°C) in the rotary kiln is required for the KILN TEMPERATURE PROFILE In a rotary kiln system producing cement clinker, gas flows are countercurrent to material flows Gases enter the kiln as secondary air at about 600°C – 1100°C and rise abruptly to over 1750°C as heat from fuel combustion, and the exothermic heat of clinker formation are releasedEverything you need to know about Kiln System Operations in 2017年2月14日 The quality of these materials has direct bearing on the process as well as the product Some plants do not use iron ore directly These plants use iron ore pellets in the rotary kiln Raw material mix consisting of iron ore, dolomite and noncoking coal is fed at the one end of the rotary kiln and is heated by coal burners to produce DRICoal based Direct Reduction Rotary Kiln Process – IspatGuru• Prereduce the ore in absence of C with CO gas from furnace • Transfer hot blend to the furnace 4 years project: 20182022 5 Lab scale Pilot scale scale Outotec Screening process to select pretreatment unit technology Rotary kiln Shaft furnace Eramet Ideas Rotary kiln pilot campaign Preheating prereduction Melting reductionPreheating manganese ore in a pilotscale rotary kiln Prometia
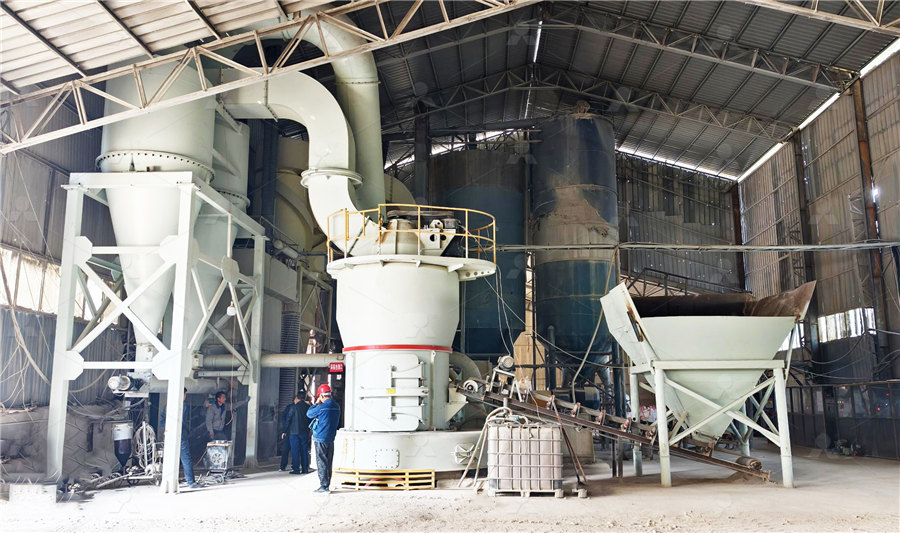
Operating Key Factor Analysis of a Rotary Kiln Using a MDPI
2024年9月13日 The global smelting business of nickel using rotary kilns and electric furnaces is expanding due to the growth of the secondary battery market Efficient operation of electric furnaces requires consistent calcine temperature in rotary kilns Direct measurement of calcine temperature in rotary kilns presents challenges due to inaccuracies and operational limitations, 2018年8月7日 Electricity consumption is the largest cost contributing factor in the production of ferrochrome Currently the pelletized chromite prereduction process (solidstate reduction of chromite) is the process option with the lowest specific electricity consumption (MWh/ton) In this process, pelletized chromite is fed into a rotary kiln at 1573 K (1300 °C), where partial pre Damring Formation During Rotary Kiln Chromite Prereduction: process may be to heat treat the ore prior to smelting, as in the Rotary KilnElectric Furnace (RKEF) process used in ferronickel smelting [3] The main concept is illustrated in Figure 1 In the RKEF process the ore is dried, clacined and prereduced in a rotary kiln The hot calcine from the rotary kiln can be directly charged into the arc Thermal upgrading of manganese ores prior to smelting2024年5月28日 The rotary kiln at the iron ore pellet company has a diameter of 61 m and length of 40 m After suspending production, ten samples of deposit formation were collected from the rotary kiln at 4m intervals Each sample was taken from a different position around the wall surface of the rotary kiln and labeled as S1 to S10Inhibiting the Accretion in the CoalFired Rotary Kiln of High