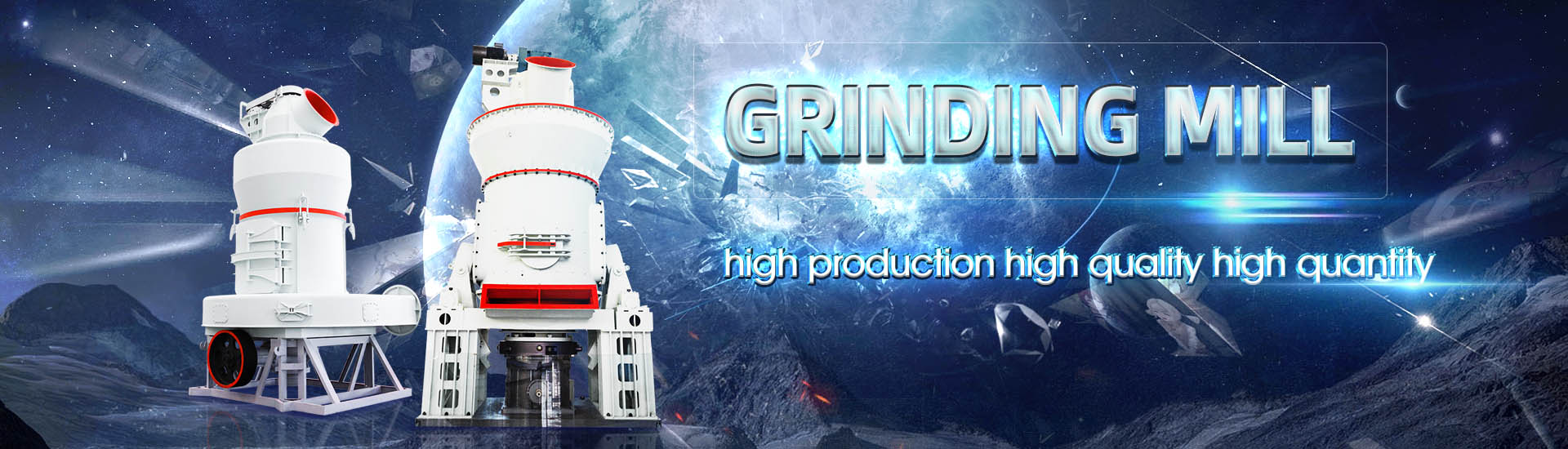
HOME→Overhaul of 200 mesh pulverized coal mill Overhaul of 200 mesh pulverized coal mill Overhaul of 200 mesh pulverized coal mill
Overhaul of 200 mesh pulverized coal mill Overhaul of 200 mesh pulverized coal mill Overhaul of 200 mesh pulverized coal mill
.jpg)
Coal mill pulverizer in thermal power plants PPT
2012年11月17日 The document discusses coal mill/pulverizers used in thermal power plants It describes how pulverized coal is dried, ground, circulated, and classified within the mill to produce a fine powder that is then transported to 2021年3月31日 IMPACT ON FUEL HANDLING PULVERIZATION SYSTEM • Moisture in coal impacts, mill capacity, heat rate unit capacity • Grind ability affects mill capacity power consumption • Fineness can be optimized by Effect of Coal Quality and Performance of Coal Today's coalfired utility boiler operation needs pulverizer designs to supply pulverized coal with required throughput and coal fineness, and also perform with lower specific power Coal Pulverizer Design Upgrades to Meet the Demands of Low Typical Triggers for a Pulverizer Overhaul: • Prescribed maintenance interval (hours, tons throughput, months • Noise, Coal Rejects excessive, Capacity Short • Repair damaged or Performance Driven Maintenance of Coal Pulverizers

Coal Pulverizer – Power Plant Pall Corporation
Pulverization of coal is currently the favored method of preparing coal for burning Mechanically pulverizing coal into a fine powder enables it to be burned like a gas, thus allowing more In this research, grinding tests and combustion tests using superhighmoisture coal were carried out by Mitsubishi Hitachi Power Systems, Ltd (MHPS), and the stable grinding conditions for Development of Millburner System for Lowrank Coal with Super pulverize the coal by impact and attrition The pulverized coal is then conveyed by air to centrifugal classifiers Properly sized pulverized coal exits the classifier into coal piping for A Comparison of Three Types of Coal Pulverizers Babcock PowerThis paper discusses the background of one such fuel change, operational effects thereof, and events leading ultimately to Riley Stoker Corporation's (RSC) application of newtotheUSA WorldProven Coal Pulverizer Technology Debuts in the US
.jpg)
CFD Modeling of MPS Coal Mill for Improved Performance and
2009年1月1日 Design modifications are being evaluated to alter the aircoal flow distribution within the mill aimed at obtaining a more uniform coal flow at the mill outlet as well as 2015年11月1日 Studies have shown that 70 75% of the pulverized coal passing a 200 mesh screen is optimal for the mill and combustion performance Values greater than 70% require A unified thermomechanical model for coal mill operation1800 rpm primary air fan, and four mill outlets supplying pulverized coal to one of the three horizontal rows of (4) dualfuel burners When operating at boiler MCR, each mill had a coal throughput of approximately 53,000 #ffir Specified product fineness was 70% thru 200 mesh and 98% thru 50 mesh Diminishing supply of the original Kansas coalWorldProven Coal Pulverizer Technology Debuts in the USIn the pulverized coal combustion system, coal ground to a very fine size (70–80% passing through a 200mesh screen or 75 μm) is blown into a furnace Approximately about 10% of the total air required for combustion is used to transport the coalPulverised Coal Combustion an overview ScienceDirect Topics
CFB石灰石脱硫剂制备——磨机公众号12.8 推送案例(8)51.jpg)
Performance Driven Maintenance of Coal Pulverizers
200 MESH SIEVE (COARSE ASH) BOTTOM PAN (FINE ASH) Place 50 grams of ash on the 200 MESH for sieve analysis DETERMINE LOI OF RESIDUE ON 200 MESH SCREEN AND IN PAN LOI OF FINE ASH MUST BE LESS THAN 2% (low volatile eastern fuels); or less than 05% ( high volatile western fuels) This is a Test to “Referee” the cause of2021年3月31日 24 mill performance monitoring using non iso kinetic technique • dirty pitot testing to be carried out before and after mill overhaul • non iso kinetic sampling to be used for routine checking of fineness • pf fineness data to be trended mill wise • sample to be collected from each pipe in case of major degradationEffect of Coal Quality and Performance of Coal pulverisers / Mills2 Raw coal properties – Hardgrove index and moisture level 3 Pulverized coal fineness The raw coal is fed into a rotating bowl via a center feed pipe The rate of coal feed is normally determined automatically by a combustion control system, taking into account the MW demand on the unit, coal quality, and the number of coal pulverizers in Bowl Mill Coal Pulverizer COAL HANDLING PLANTSCan GE service my boiler mills? YES Our boiler mills and coal pulverizers span the globe and are built in a variety of sizes and capacitiesWe provide customized maintenance solutions, and offer a full spectrum of highquality solutions for each—in addition to our thousands of standard boiler mill parts and boiler service solutionsThis is the Power of YesBoiler Mill and Coal Pulverizer Performance GE Steam Power
.jpg)
A complete review based on various aspects of pulverized coal
2019年2月14日 The aim of present paper is to review various aspects of pulverized coal combustion such as oxyfuel combustion, cocombustion of coal and biomass, emissions from pulverized coal furnaces, ash formation and deposition, and carbon capture and sequestration (CCS) technologies to outline the progress made in these aspectsTypically a mill will be controlled so that 70% of the coal powder it produces will pass through a 200 mesh, indicating a particle size of less than 75 microns Operation of coal mills is affected by both the moisture content and volatiles content of the coal and so will vary from coal to coal, therefore coal processing must normally be tuned to a particular type of coalCoal Mill an overview ScienceDirect Topics2012年4月24日 In power generation, particle size distribution (PSD) of pulverized coal used in a power plant was 65%70% passing 200 mesh or known as 76 microns Since coal took hundreds of millions of years to Relationship between Particle Size Distribution of LowRank Pulverized Gas turbine combined cycle Shigehiro Shiozaki, Akira Yamada, in Advances in Power Boilers, 2021 637 Gasifier facilities 6371 Coal pulverizing and feeding system The purpose of the coal drying system is drying and grinding the raw coal for stable transportation of pulverized coal to gasifier and stable/highefficiency gasification at the gasifierCoal Pulverizers an overview ScienceDirect Topics
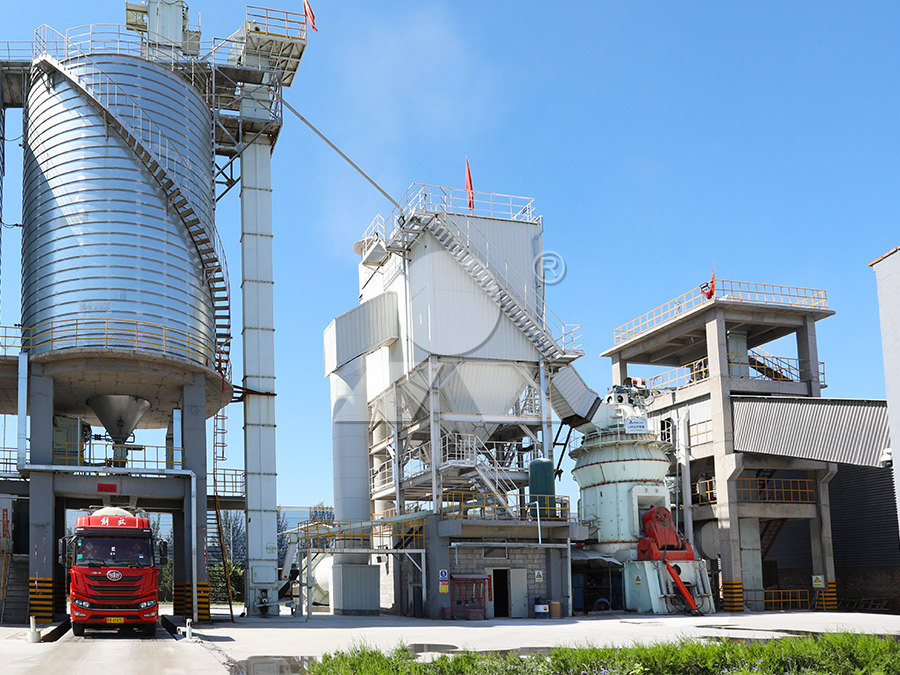
Improving Coal Pulverizer Performance and Reliability Pall
pulverized coal can be introduced directly into the boiler for combustion Combustion Engineering 783RP BowlMill Coal Pulverizer enclosed chamber with wear resistant plates The hammers impact on the coal, cleanable mesh or 200micron cleanable, stacked disk filters Such OEMsupplied2023年1月13日 The paper provides an outlook on future directions of research and the possible applications for pulverized coalfired boilers One potential direction for future research is to focus on the ways (PDF) Pulverized CoalFired Boilers: Future Directions of Scientific 2024年8月23日 Hourly production of 3120 tons of coal mill, 200 mesh pulverized coal processing equipmentHourly production of 3120 tons of coal mill, 200 mesh pulverized coal 2020年6月29日 ROLE OF MILLS • Produces Pulverized coal 80% of which passes through 200 mesh • Air mixed with Pulverized coal (PF) is carried to the coal nozzle in the wind box assembly • PF from coal nozzle is directed towards the center of boiler burning zone • Preheated secondary air enters boiler and surrounds the PF and help in combustionclassifications and working of mills in a power plant PPT
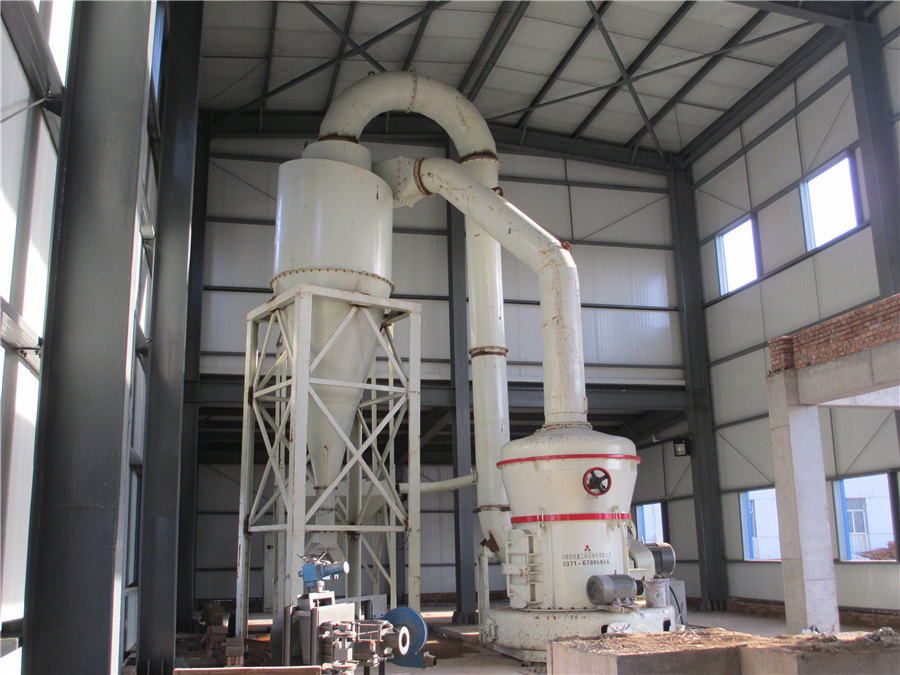
Pulverized Coal Pipe Testing and Balancing
The worst single pipe was about 60% passing 200 mesh The best pipe of the eight measured above 68% passing 200 mesh On average, the pipes were about 65% passing 200 mesh, short of our standard of 75% minimum passing 200 mesh on a mass weighted average basis The actual data are shown in Figure 62022年1月26日 Numerical mesh and geometrical model for pulverized coal ducts for mill 1, mesh for difference in residue on the 200 sieve max 018% (Table 1)) erosiv e defect is significantNumerical Study of the Erosion Process and Transport of Pulverized Coal Maximum mill capacity vs HGI at coal moisture of 12 % 3000 3200 3400 3600 3800 4000 4200 60 70 80 HGI 90 100 110 120) Output at coal fineness of 70 % passing through 200 Mesh Output at coal fineness of 75 % passing through 200 mesh 24Pulverizer Plant OM Aspects2010年10月7日 Coal pipe F9 on pulverizer B was the only pipe that met the original plant fuel specification guarantee of 70% passing 200 mesh, which is far short of the 75% minimum we usePulverized Coal Pipe Testing and Balancing POWER Magazine
.jpg)
Developments in Pulverized CoalFired Boiler
1996年4月10日 A new generation of pulverized coalfired boiler technology is currently under development which will permit generating mit superior mill turndown without the 200 150 100 50 0 NO xCoal mill is suitable for types of coal with various hardness and humidity Coal ball mill is mainly used in coal power plant or mineral calcining system The fineness of pulverized coal has a great influence on the ignition temperature Coal Ball Mill Grinding for Different Kinds of 2021年3月1日 The biomass cofiring test was conducted at a pulverized coal power plant with a capacity of 300 MWe to determine the effect of cofiring on the operating parameters, such as Mill Outlet (PDF) Cofiring characteristics of wood pellets on pulverized coal 2020年8月12日 This study shows the performance of a currently running vertical roller coal mill (VRM) in an existing coalfired power plant In a power plant, the coal mill is the critical equipment, whose An investigation of performance characteristics and energetic
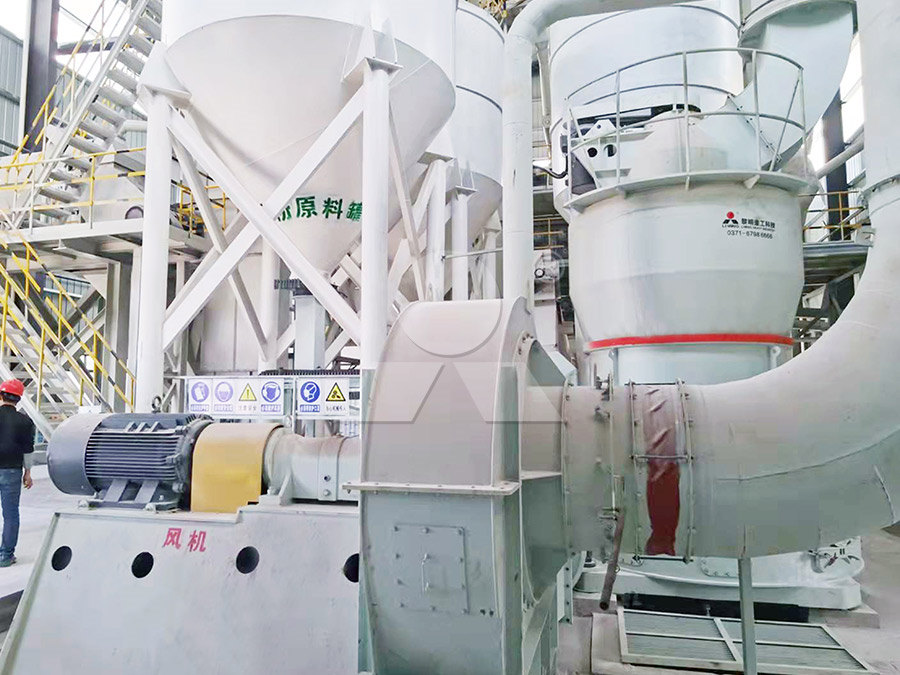
CPRI Online Coal Flow Balancing and Fineness Adjustment
ONLINE COAL FLOW MEASURING AND BALANCING (CONTROL) AND ONLINE COAL FINENESS MEASURING SYSTEM FOR COMBUSTION OPTIMISATION IN A THERMAL BOILER Suresh G Chandwani1, Dr Francesco Turoni2, Reinhardt Kock2, Dr Michael Haug2, Dr Michael Schreiber2 1NSGuzder Company Pty Ltd, Neville House, Currimbhoy Road, 3) Pulverized coal storage: The pulverized coal coming out of the explosionproof bag dust collector enters the storage silo; a fire extinguishing system is installed on the storage silo, the explosionproof bag dust collector and the pulverized coal vertical mill; then it is discharged from the storage silo The pulverized coal is shipped in bulkWhat is the process flow of vertical mill to produce pulverized coal?2015年10月1日 This paper focuses on the flow control of pulverized fuel (pf flow) of the coal mill on the basis of the real measuring data registered in the Polish power unit with a capacity of 200 MW(PDF) Control for pulverized fuel coal mill ResearchGatemill performance This test showed that a pulverized coal (PC) boiler can operate on 100% TW fuel with minimal operational changes INTRODUCTION The value of this work is that it is one of the first 100% test burns of TW pellets in a large pulverized coal boiler with positive results Many questions were answered about100% TEST BURN OF TORREFIED WOOD PELLETS AT A FULLSCALE PULVERIZED
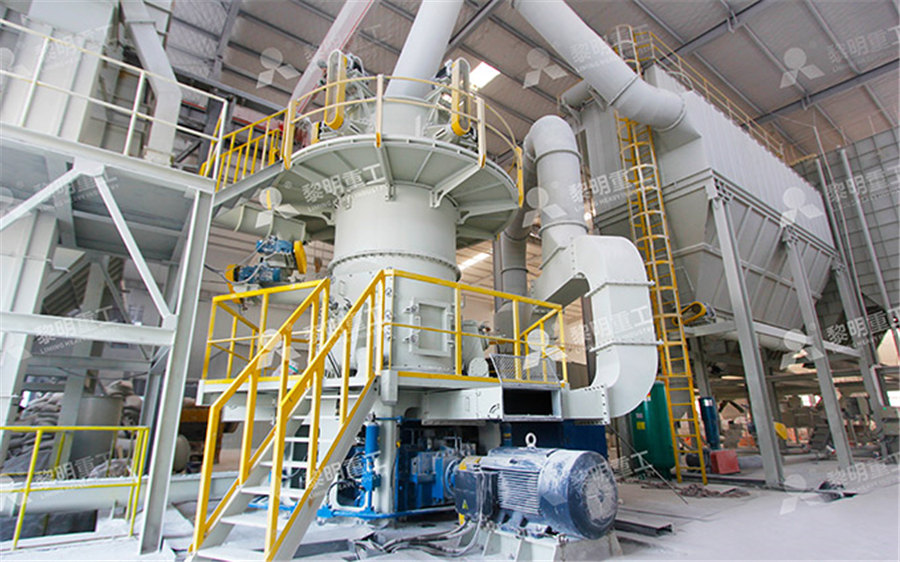
Pulverizers 101: Part I POWER Magazine
2011年8月1日 The pulverizer will then have the capability to produce pulverized coal that is 70% passing 200 mesh fineness (Figure 2, red line) This is commonly expected performance for this model pulverizerPulverized coal is the most efficient way of using coal in a steam generator The coal is ground so that about 70 % will pass through 200 mesh (0075 mm) and 99 % will pass through 50 mesh (0300 mm) A pulverized coal boiler can be easily adapted for other fuels like gas if required later without much difficulty However, during the design Coil Pulverizers for Boilers Bright Hub EngineeringA pulverized coalfired boiler is an industrial or utility boiler that generates thermal energy by burning pulverized coal (also known as powdered coal or coal dust since it is as fine as face powder in cosmetic makeup) that is blown into the firebox The basic idea of a firing system using pulverised fuel is to use the whole volume of the furnace for the combustion of solid fuelsPulverized coalfired boiler Wikipediafuel and greater than passing of 200 mesh requires the maximum pressure of the grinding elements Keep in mind that in operation there is no metaltometal contact, and all coal grinding results from the pressure applied coal particle–to–coal particle on a bed of coal squeezed between the grinding elements“Blueprint” Your Pulverizer for Improved Performance
.jpg)
Hourly production of 3120 tons of coal mill, 200 mesh pulverized coal
Hourly production of 3120 tons of coal mill, 200 mesh pulverized coal processing equipment2019年1月1日 Review of the investigations of pulverized coal combustion processes in large power plants in laboratory for thermal engineering and energy: Part B January 2019 Thermal Science 23(Suppl 5):16111626(PDF) Review of the investigations of pulverized coal combustion a pulverized coal firing system These systems utilize a pulverizer or mill to grind coal to a desired fineness and subsequently transport the coal to the 50, 100, 140 and 200 Mesh FLOW 10' INCLINE MANOMETER DETAIL DIRTY AIR PROBE BOTTOM VIEW DUSTLESS CONNECTOR 1 1/4" FULL PORTEDInnovative Combustion Technologies, Inc2019年1月1日 For coal and gas dualfired boiler, pulverized coal mass flow and gas volume flow into furnace are important criteria for boiler operation adjustment, and they are important input parameters for Calculation Method of Pulverized Coal Mass Flow Into Coal and
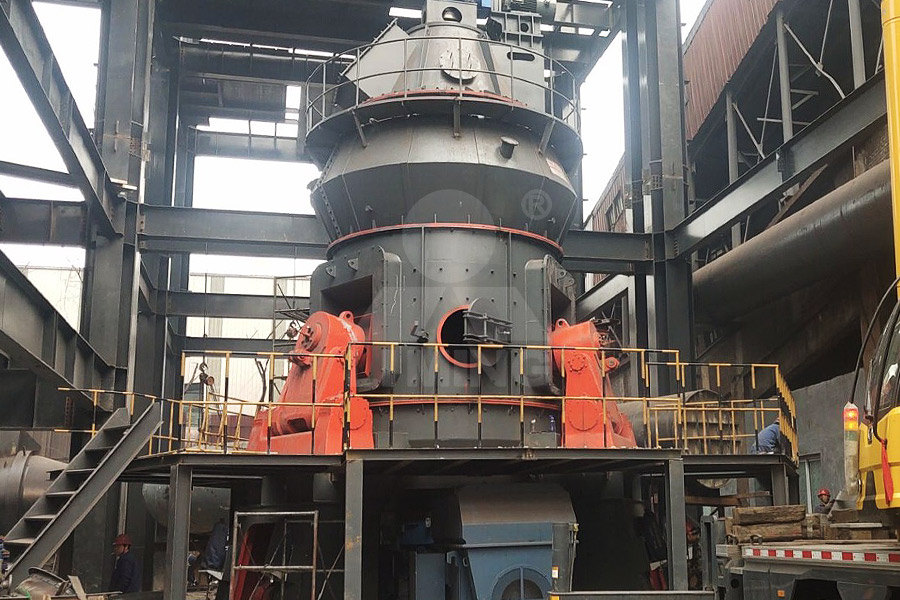
How is pulverized coal processed? SBM Ultrafine Powder
2022年2月24日 Production of clean pulverized coal for boiler combustion heating and power supply Fineness: 200 mesh, D8090, according to the needs of backend combustion Suitable coal types: bituminous coal, anthracite, blue carbon, etc The production of clean pulverized coal is used for boiler combustion heating and power supply to improve the operating efficiency of 2014年10月1日 Numerical and experimental analysis of pulverized coal mill classifier performance in the Soma B Power Plant that have been considered, were time of mesh generation, accuracy of the results, Numerical and experimental analysis of pulverized coal mill 2016年10月1日 NUMERICAL AND EXPERIMENTAL INVESTIGATION OF A PULVERIZED COAL MILL DUCT SYSTEM IN THE SOMA B THERMAL (200 9) They stated that a The orthogonal mesh q uality ranges from 0 NUMERICAL AND EXPERIMENTAL INVESTIGATION OF A PULVERIZED COAL MILL