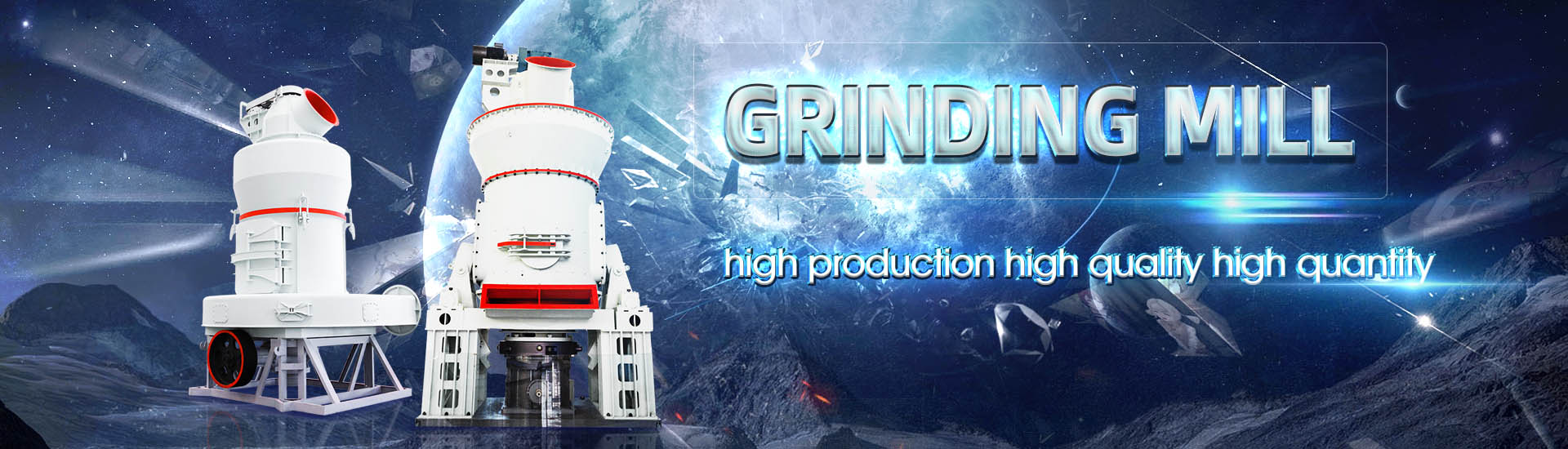
Coal mill tumbling mechanism
.jpg)
Coal Mill an overview ScienceDirect Topics
Mills are mechanical devices used to break different types of solid materials in small pieces by grinding, crushing or cutting In pulverised coalfired power plants, a pulveriser coal mill grinds the raw coal into a combustible dustTUMBLING MILL MECHANICS A tumbling mill is a collective name for the generally known ball mills, rod mills, tube mills, pebble mills and autogeneous mills For all these kinds of mills the TUMBLING MILL MECHANICS2015年11月1日 Coal mills are bottleneck in coal–fired power generation process due to difficulty in developing efficient controls and faults occurring inside the mills In this paper, a dynamic A unified thermomechanical model for coal mill operationNumerical modelling of grinding in tumbling mills is traditionally done with the discrete element method (DEM) The grinding balls are then represented by DEM particles and the mill Development of physically based tumbling mill models DiVA
.jpg)
Comminution mechanisms, particle shape evolution and collision
2016年2月1日 Particle shape change due to rounding and chipping is quantified for a tumbling mill The split of energy between colliding particles is critical to breakage prediction A A tumbling mill is a collective name for the generally known ball mills, rod mills, tube mills, pebble mills and autogeneous mills For all these kinds of mills the mechanics can be dealt with Tumbling Mill Mechanics SpringerLink2016年2月1日 Chipping and rounding are mechanisms that lead to preferential mass loss from corners and edges of particles and which produce shape change for the particles as well as Comminution mechanisms, particle shape evolution and collision The Tube Ball mill used by EDF is a motor driven tumbling barrel charged with steel grinding balls as shown in Figure 2 The mill drive is via a 16MW, 740 RPM, 33KV 3ph 50 Hz constant Development of a Tubeball Coal Mill Mathematical Model Using
.jpg)
Dynamic characteristics and deterioration mechanism of coal
2023年9月5日 Additional to dynamic and static superimposed loads, gas effects frequently affect coal seams throughout the coal mining process It is crucial to comprehend coal samples’ mechanical properties and deterioration mechanisms under distinct initial gas pressure conditions Consequently, the dynamic compression experiment of coal samples was conducted utilizing a 2020年8月12日 This study shows the performance of a currently running vertical roller coal mill (VRM) in an existing coalfired power plant In a power plant, the coal mill is the critical equipment, whose An investigation of performance characteristics and 2012年11月17日 20 131Fineness Fineness is an indicator of the quality of the pulverizer action Specifically, fineness is a measurement of the percentage of a coal sample that passes through a set of test sieves usually designated at 50, Coal mill pulverizer in thermal power plants PPT2020年1月1日 Coal has an important role in electricity generation worldwide According to data from the World Coal Association, coalfueled power plants currently provide 37% of the global electricity [1]In 2017, China's coalfired power generation accounted for 645% of the total power generation [2]Nearly 176 billion tons coal produced in China is used for generating electricity Wet and dry grinding of coal in a laboratoryscale ball mill:
.jpg)
TUMBLING MILL MECHANICS
A tumbling mill is a collective name for the generally known ball mills, rod mills, tube mills, pebble mills and autogeneous mills For all these kinds of mills the mechanics can be dealt with together, there being no substantial difference in the grinding process There are two 2023年10月30日 The object of the study reported here is the grinding process in a tumbling mill where the mechanism of destruction by crushing is implemented, which is caused by the mechanism of compression loadingBuilding a model of the compression grinding mechanism in a tumbling Development of a Tubeball Coal Mill Mathematical Model Using Particle Swarm Optimization (PSO) The Tube Ball mill used by EDF is a motor driven tumbling barrel charged with steel grinding balls as shown in principle of a vertical spindle mill There is a rotating mechanism that acts like a paddle spinning inside the millDevelopment of a Tubeball Coal Mill Mathematical Model Using 2019年10月1日 Request PDF Wet and dry grinding of coal in a laboratoryscale ball mill: Particlesize distributions In this study, experimental data for wet and dryground coal samples under wet and dry Wet and dry grinding of coal in a laboratoryscale ball mill: Particle
.jpg)
Investigation of the effect of industrial ball mill liner type on their
SAG mill length and analyzing the charge trajectory and shape variation at given operating conditions (ie, ball filling, mill speed, liner type), the impact of the endwall effect on the charge The cataract regime in mill is eliminated by a mechanism to measure the impact and abrasion wear separately The comparisons show the appropriate accordance of predicted and measured liner wear Prediction of tumbling mill liner wear: Abrasion and impact effects2016年2月1日 Request PDF Comminution mechanisms, particle shape evolution and collision energy partitioning in tumbling mills A computational model for use with DEM (Discrete Element Method) is proposed Comminution mechanisms, particle shape evolution and 2009年9月20日 A control oriented model was then developed by Fan (1994) and Fan and Rees (1994) In 2009, coal flow and outlet temperature of mill were modelled using mass and heat balance equations for startup Modeling and Parameter Identification of Coal Mill
.jpg)
Grinding Media in Ball Mills for Mineral Processing
2023年11月24日 Tumbling mills convert electrical energy into phase structure, and corrosive–abrasive characteristics of the slurry The wear mechanisms involved in a ball mill are impact, abrasion D Exploratory investigation on the use of lowcost alternative media for ultrafine grinding of coal Int J Coal Prep Util 2024年7月12日 The ball mill works on the principle of impact and attrition Size reduction occurs as the small balls drop from near the top of the shell What is the difference between a ball mill and a tumbling mill? A ball mill and a tumbling mill are What Is a Ball Mill and How Does It Work? Certified MTP Blog2023年9月5日 Dynamic characteristics and deterioration mechanism of coal under distinct initial clamped to avert the coal from tumbling off using 30 mm were prepared by a cutting mill For coal samDynamic characteristics and deterioration mechanism of coal 2023年7月10日 Mechanism of grinding in a tumbling mill (white shapes—grinding media, black shapes—particles, and arrow marks—forces acting on RR; Hagy, JT Fine grinding of coal using the Pitt mill In Proceedings of the 7th Annual International Pittsburgh Coal Conference, Pittsburgh, PA, USA, 3–6 September 2019; 1990; pp 643–652 EnergyEfficient Advanced Ultrafine Grinding of Particles Using
.jpg)
A unified thermomechanical model for coal mill operation
2015年11月1日 As presented by Andersen et al (2009) and Odgaard, Stoustrup, and Mataji (2007), coal moisture imposes limit on the maximum load at which a coal mill can be operated and the load gradient (how fast the mill may change its operating point), if it is desired that the pulverized coal entering the furnace has moisture content less than or equal to a certain value 2020年7月1日 Considerable investments have been made on the development of alternative equipment It is reported that the use of stirred media mills and high pressure grinding rolls (HPGR) improved grinding efficiencies compared to the conventional tumbling mills – balls mills and rod mills [11], [30], [31]The development of new approaches to mineral processing, such A critical review on the mechanisms of chemical additives used in 2017年7月1日 Please cite this article as: R Panjipour, K Barani, The effect of ball size distribution on power draw, charge motion and breakage mechanism of tumbling ball mill by discrete element method (DEM The effect of ball size distribution on power draw, charge motion 2020年8月12日 In a power plant, the coal mill is the critical equipment, whose effectiveness impacts the overall power plant efficiency Uniform coal feeding mass flow rate and required particle size and temperature at the outlet channel throughout with better classifier performance are crucial indicators that characterize the coal mill performanceAn investigation of performance characteristics and energetic
.jpg)
Comminution Handbook – Contents AusIMM
Breakage mechanisms Classification mechanisms Comminution machines Chapter 2 Tumbling Mills Mill Liners 125 The role of liners in tumbling mills Variations in liners for ore mills Materials of construction Potential issues with liners Types of liners 55 known as the distribution function [45, 46]) describes the distribution of fragment sizes obtained after a breakage of particles of size xjThus, b1j, b2j, , bnj are the mass fractions of particles in size classes 1, 2, , n after a breakage of particles in size class j The mechanism of breakage is illustrated in [23] by a diagram shown in Fig 3Grinding in Ball Mills: Modeling and Process Control SciendoIn tumbling mills, the mill shell is rotated and motion is imparted to the charge via the mill shell The grinding medium may be steel rods, balls, or rock itself Media ball sizes, for example, range from about 20 mm for fine grinding to 150 mm for coarse grindingGrinding Mill an overview ScienceDirect Topics2022年11月30日 A ball mill also known as pebble mill or tumbling mill is a milling machine that consists of a hallow cylinder containing balls; mounted on a metallic frame such that it can be rotated along its longitudinal axis The balls which could be of different diameter occupy 30 – 50 % of the mill volume and its size depends on the feed and mill sizeBall Mill: Operating principles, components, Uses, Advantages and
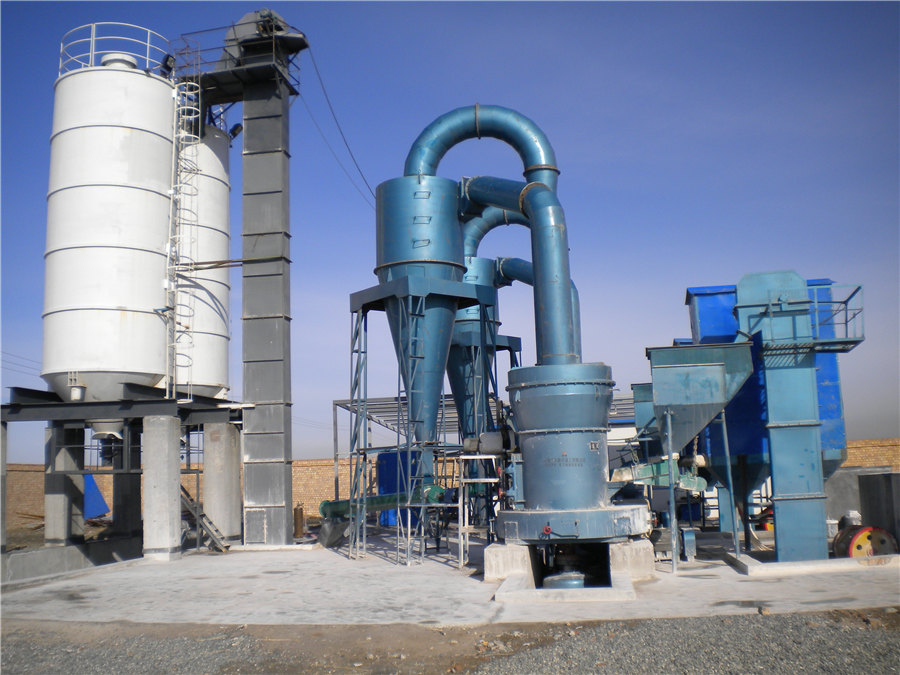
Tumbling strength and reactivity characteristics of hybrid fuel
2021年4月4日 This paper presents an assessment of the tumbling strength and reactivity behaviour of hybrid fuel briquette (HFB) produced from coal and torrefied woody biomass wastes2020年4月7日 mechanism of coal mill system; Dynamic model derivation, model para meter identification and verification are introduced in Section 3 and Section 4 separatelyModeling of Coal Mill System Used for Fault Simulation2014年3月1日 The crushing efficiency and coal grinding characteristics of the medium speed roller mill and ball mill in power plants were studied by Rubiera and Cho The influence of the coal blending and minerals in coal on the grinding efficiency was studied and the optimization scheme was put forward [8], [9]Breakage and separation mechanism of ZGM coal mill based on 2009年12月1日 Request PDF Experimental investigation of load behaviour of an industrial scale tumbling mill using noise and vibration signature techniques Mill load (ie the load level of coal powder Experimental investigation of load behaviour of an industrial scale
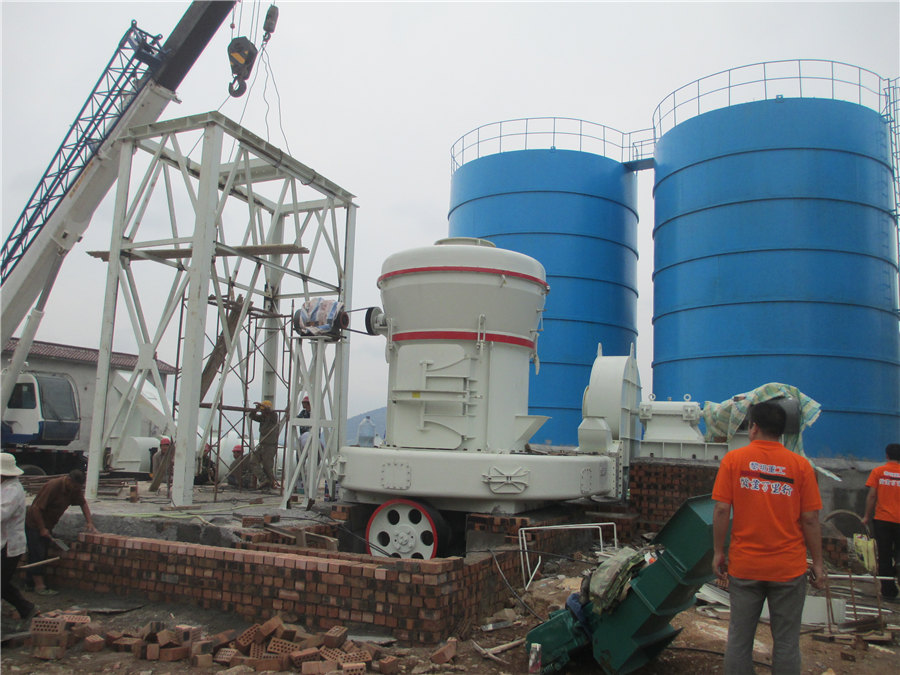
Investigation of the effect of industrial ball mill liner type on their
2021年6月21日 Effects of mill shell liner type on charge shoulder, toe, impact, and head points, also on head height and impact zone length as well as on the creation of cascading, cataracting, and centrifuging 2014年3月1日 Request PDF Breakage and separation mechanism of ZGM coal mill based on parameters optimization model Sampling ports were firstly drilled on a ZGM95 coal mill in the power plant in China, and Breakage and separation mechanism of ZGM coal mill based 2018年5月2日 Coal mill malfunctions are some of the most common causes of failing to keep the power plant crucial operating parameters or even unplanned power plant shutdowns Therefore, an algorithm has been developed that Detection of Malfunctions and Abnormal Working 2020年7月2日 Please cite this article as: R Panjipour, K Barani, The effect of ball size distribution on power draw, charge motion and breakage mechanism of tumbling ball mill by discrete element method (DEM (PDF) Effects of Ball Size Distribution and Mill Speed and Their
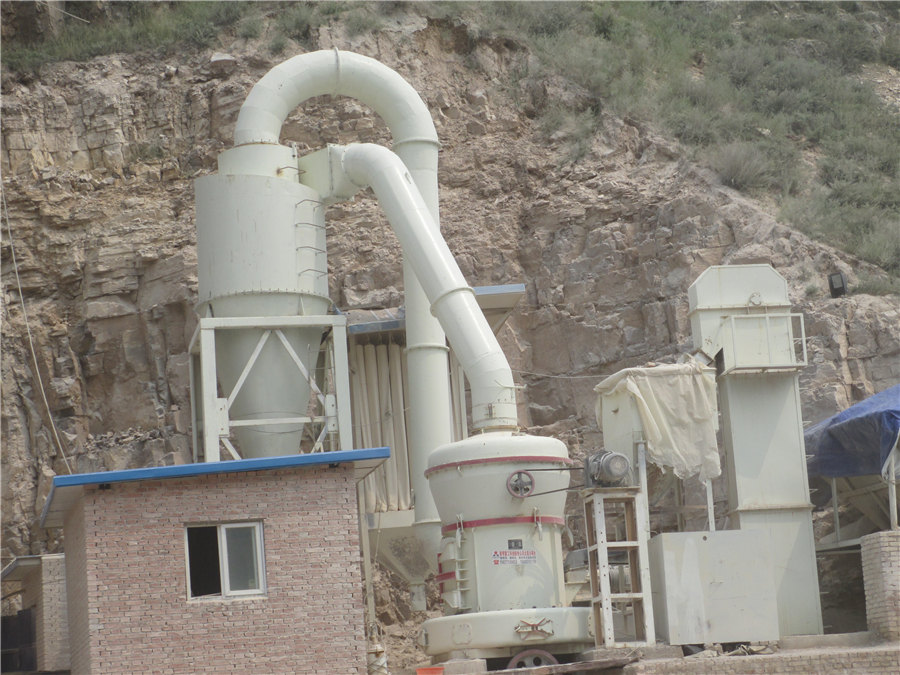
A Review of the Grinding Media in Ball Mills for Mineral Processing
2023年10月27日 The ball mill is a rotating cylindrical vessel with grinding media inside, which is responsible for breaking the ore particles Grinding media play an important role in the comminution of mineral ores in these mills This work reviews the application of balls in mineral processing as a function of the materials used to manufacture them and the mass loss, as A popular type of vertical spindle mill is the ringroller mill General Information In ringroller mills rollers feed solid coarse particles against a stationary grinding ring The particles are broken apart by the resulting compression forces Equipment Design In a ringroller mill, the material to be milled is fed into the grinding sectionSize Reduction – Visual Encyclopedia of Chemical Engineering 2008年1月1日 The Sarcheshmeh mine processes 40 000 t/d of ore grading 09% Cu and 0035% Mo Grinding is effected in single stage ball mills using 80 mm forged steel bails, with an average consumption of 850 g/tWear of Grinding Balls with a Size Distribution in Dry and Wet Tumbling 2019年10月14日 28 mechanisms between wet and dry grinding 29 Keywords: particle size distribution, coal, ball milling, wet grinding, dry grinding 30 1 Introduction 31 Coal has an important role in electricity generation worldwide According to data 32 from the World Coal Association, coalfueled power plants currently provide 37% of theWet and dry grinding of coal in a laboratoryscale ball mill:
.jpg)
Differences in dry and wet grinding with a high solid
2019年8月1日 Request PDF Differences in dry and wet grinding with a high solid concentration of coking coal using a laboratory conical ball mill: Breakage rate, morphological characterization, and induction 2024年11月1日 Understanding the EnergySaving mechanism of ceramic balls in tumbling mills Author links open overlay panel Xin Fang a, Caibin Wu a b, Ningning Liao a, Chengfang Yuan a, The first attempt of applying ceramic balls in industrial tumbling mill: A case study Miner Eng, 180 (2022), Article View PDF View article View in Understanding the EnergySaving mechanism of ceramic balls in tumbling 2023年4月23日 Tumbling mills are an old technology that is still commonly This may be due to the energy transfer mechanisms in ball mill 492 mm and a mixture of the grinding media on a coal sample, (PDF) Grinding Media in Ball MillsA Review ResearchGate2020年6月30日 Online mill charge detection methods have been developed with two primary approaches, imbedding strain gauges and integrated circuitry with grinding steel balls [10], and imbedding sensors on the mill shell/liner [[11], [12], [13], [14]]The former approach records the movements of the mill charge both in the rotating and the longitude directions of the millIdentifying grinding mill dynamics using acoustic beamforming