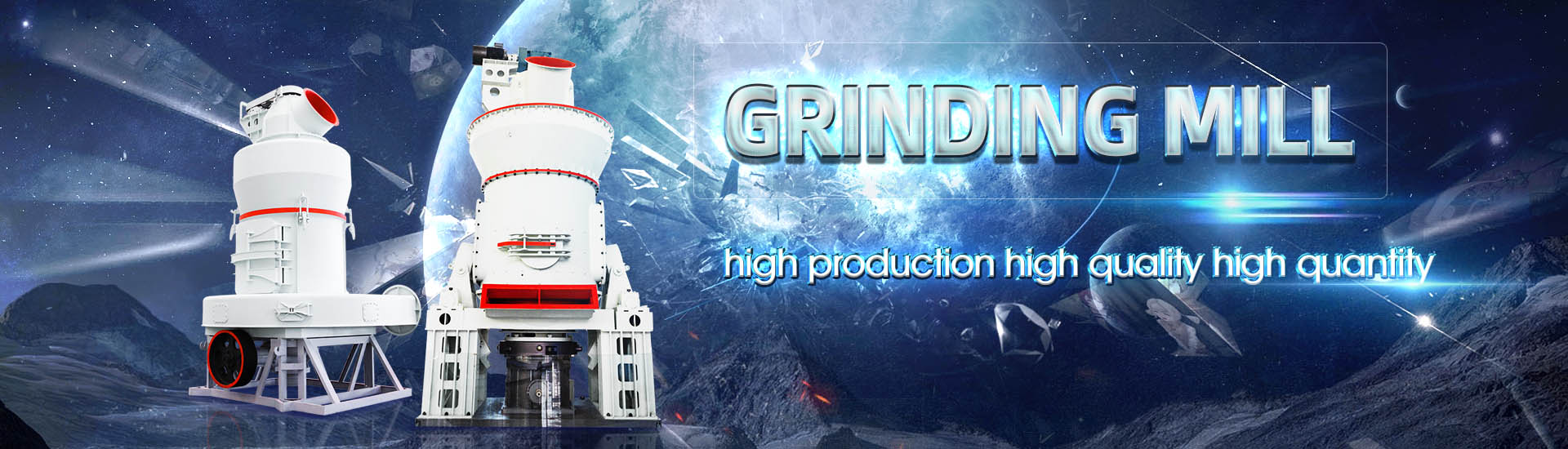
Working principle of coal drying mill
.jpg)
Vertical Grinding Mill (Coal Pulverizer) Explained saVRee
This article concerns itself with vertical grinding mills used for coal pulverization only (coal pulverizers), although vertical grinding mills can and are used for other purposes The 3D model in the saVRee database represents a vertical grinding bowl mill Other grinding mill types include the ball tube mill, hammer mill, 展开Working Principle During the operation of the ball mill, the raw coal first enters the drying chamber through the feed inlet for drying, and the dried raw coal enters the grinding chamber for grinding and second drying The pulverized coal is Coal Mill in Cement PlantCoal mills or pulverizers play a very essential part in the coalfired power production system Coal mills grind the coal into fine powder, and the primary air entering the mill dries and drives the Coal Mill an overview ScienceDirect Topics2012年11月17日 The document discusses coal mill/pulverizers used in thermal power plants It describes how pulverized coal is dried, ground, circulated, and classified within the mill to produce a fine powder that is then transported to Coal mill pulverizer in thermal power plants PPT
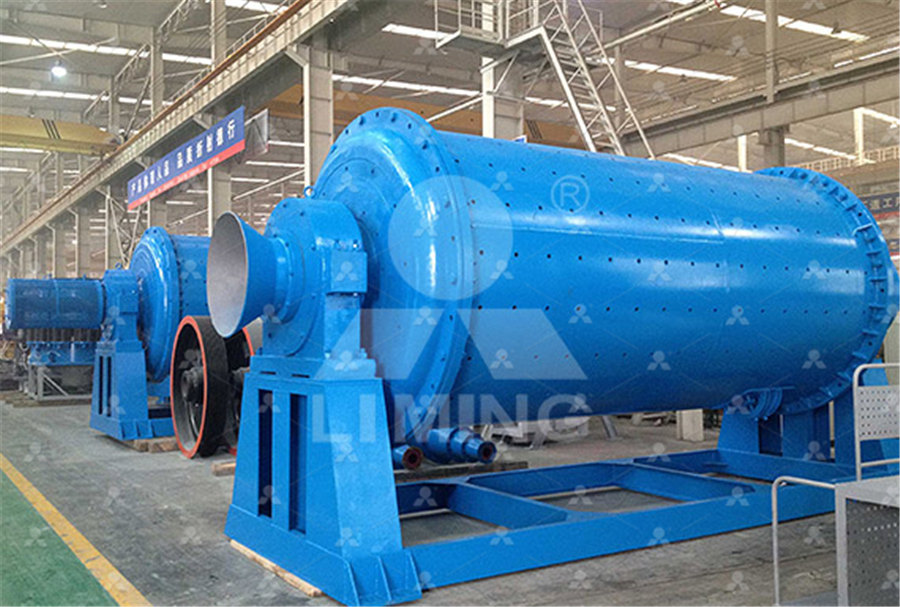
(PDF) 43 Drying of Coal ResearchGate
2006年11月8日 Coal must also be dried for the following processes: (1) briquetting, (2) coking, (3) gasication, (4) lowtemperature carbonization, (5) liquid fuel synthesis, and others The nal moisture2009年2月25日 In this study, a coal drying system was designed using waste heat recovery systems, R134a refrigerant as working fluid, air source heat pumps, and vacuum tube solar (PDF) LowRank Coal Drying Technologies—Current Status and Coal ball mill is the main equipment for grinding pulverized coal The raw material of coal powder is coal with various hardness, and it drying in the coal mill grinding process to obtain finished coal powder which can be efficiently burnedCoal Ball Mill Grinding for Different Kinds of Coal feeders provide coal to the coal pulverizers (mills) where the coal is pulverized and dried Dryer coal is easier to pulverize, and less mill power is needed to achieve the same coal Coal Drying Improves Performance and Reduces Emissions
.jpg)
Derivation and validation of a coal mill model for control
2012年5月1日 The paper presents development and validation of a coal mill model to be used for improved mill control, which may lead to a better load following capability of power plants 2020年4月7日 Working Principle of a Coal Mill System MPS mediumspeed coal mill is a rolltype mediumspeed coal mill designed and manufactured by Babcock, the specific heat capacity of coal drying basis and the specific Modeling of Coal Mill System Used for Fault Air Swept Coal Mill Working Principle First, the raw coal is fed into the feed chute by the feeding device Then, the hot air with a temperature of about 300 ℃ enters through the air intake pipe and begins to dry the raw coal while they are Air Swept Coal Mill Coal Mill In Cement PlantClosed mill housing pressureshock proof up to 35 bar: 3: Optimized free flow areas: 4: Maintenance door with LiftandSwing System: 5: Design measures preventing pulverized coal deposits: 6: Rollers can be lifted off: 7: Pull rods Coal mill, gypsum mill, clay mill, etc Pfeiffer MPS mills
.jpg)
Ball mill: Principles, construction, working, uses, merits, and
2024年1月28日 2 Liners: An abrasionresistant material such as manganese steel or rubber typically lines the inner surface of the cylindrical shell to protect it from wear due to the grinding action 3 Balls: They place steel or ceramic balls, typically used as grinding media in a ball mill, inside the shell and rotate them with it 4 Feed and Discharge: Entering the hollow shell at the 2020年6月15日 Industrial hammer mills are employed in particle reduction applications for processing material Though machine designs vary, the basic hammer mill working principle remains the same—uniform size reduction of aggregate raw material is achieved by repeated blows with hammers mounted to a rotating shaftUnderstanding the Working Principle of Hammer Mills PraterWorking Principle During the operation of the ball mill, the raw coal first enters the drying chamber through the feed inlet for drying, and the dried raw coal enters the grinding chamber for grinding and second drying The pulverized coal is taken out of the mill by hot airCoal Mill in Cement Plant Vertical Roller Mill AirSwept Ball Mill2 The hot air is used for transportation of the recirculating coal within the mill and also for transporting the coal from the pulverizer to the furnace As the coal is continuously reduced in size, the smaller/lighter particles are swept from the bowl by the hot air Hot air (and cool tempering air) is provided by the primary air fansBowl Mill Coal Pulverizer COAL HANDLING PLANTS

Thermal Power Plants: Components Working Principle
2020年6月3日 Working Principle of a Thermal Plant The working fluid is water and steam This is called feed water and steam cycle The ideal Thermodynamic Cycle to which the operation of a Thermal Power Station closely resembles is the RANKINE CYCLE In a steam boiler, the water is heated up by burning the fuel in the air in the furnace, and the function of the boiler is to give Coal mill has reasonable structure and high grinding efficiency, which is the ideal equipment for coal preparation Coal Mill Working Principle of Coal Mill Coal mill is mainly composed of feeding device, main bearing, rotating part, pulverized coal burner, discharging device, highpressure starting device and lubrication systemCoal Mill with Industrial Solutions Fote Machinery(FTM)2020年8月12日 As one of the three major forces of coal mills, the grinding force exerts a significant impact on the working process of coal mills and parameters like mill current and outlet temperatureAn investigation of performance characteristics and energetic Firstly, an improved coal mill dynamic model considering the joint influence of drying force, ventilation force, and grinding force is established, and a synchronous optimization approach of model The layout of the coal mill with a rotary classifier
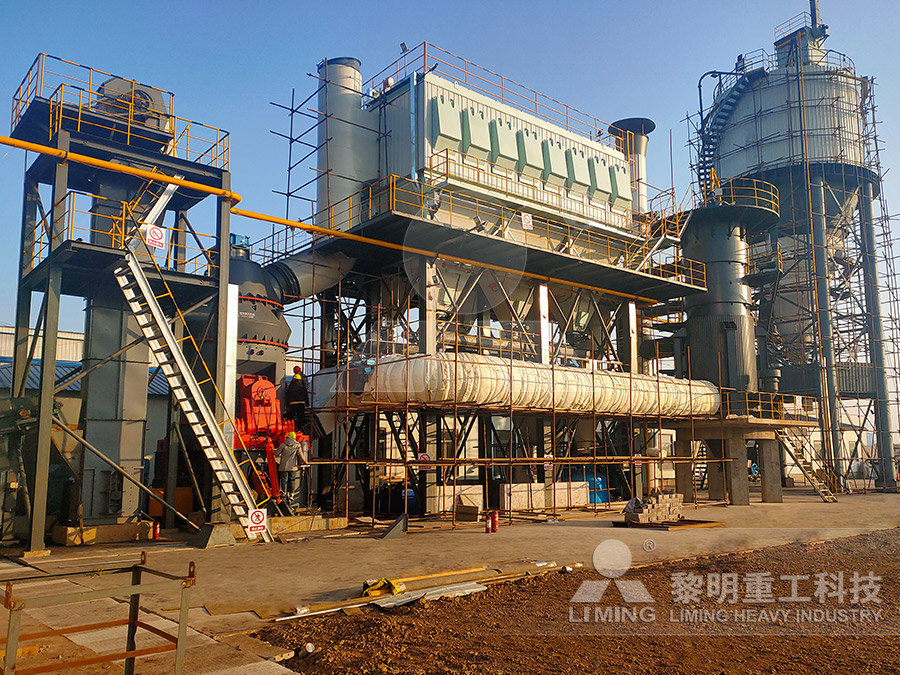
Modeling and Parameter Identification of Coal Mill
2009年9月20日 A control oriented model was then developed by Fan (1994) and Fan and Rees (1994) In 2009, coal flow and outlet temperature of mill were modelled using mass and heat balance equations for startup 2023年7月20日 Rotary drum dryers are versatile industrial machines that play a crucial role in the drying process across various industries1 They are designed to efficiently remove moisture from different types of materials, ensuring optimal The Ultimate Guide to Rotary Drum Dryers TCPELThe air swept ball mill is an ideal grinding machine that merges pulverizing and drying into a single It has the characteristics of high efficiency, energy saving, and environmental protection It is often used as the main equipment in the coal preparation system, which is capable to grind coal of various hardness (the fineness of pulverized coal can reach 85% and the moisture content Air Swept Coal Mill AGICO Ball Grinding Mill ball mill machines2020年4月7日 Working Principle of a Coal Mill System The primary air system of a coal mill is mainly responsible for two tasks of coal po wder drying and transmittingModeling of Coal Mill System Used for Fault Simulation
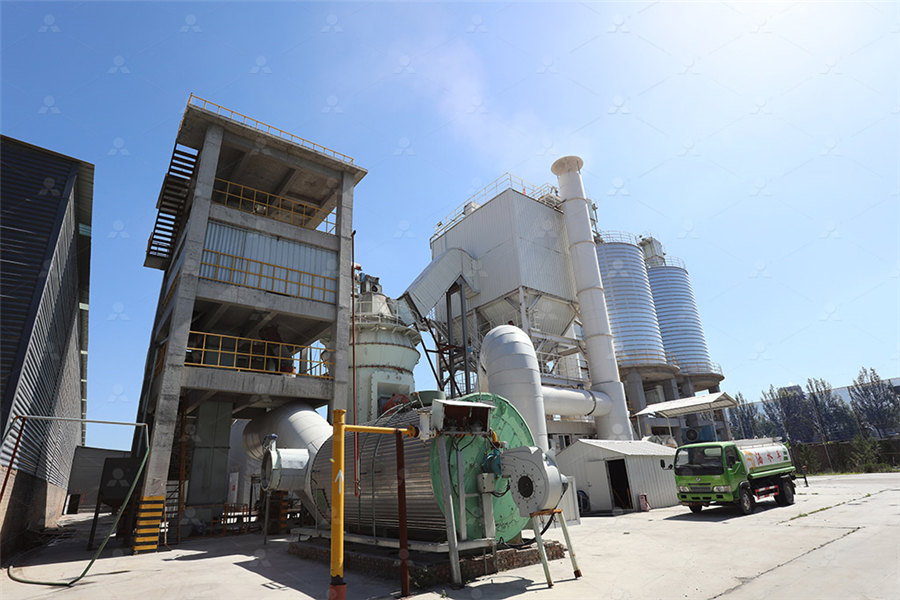
Hydrocyclone Working Principle 911Metallurgist
2015年8月7日 The centrifugal force (the central Hydrocyclone Working Principle) that is generated by this spin, forces the “bigger particles outwards towards the wall of the cyclone If you were able to do a cross section of a cyclone while it is operating, you could see that the ground rock will become finer the closer that you get to the centre of the cyclone2016年6月1日 For evaporating moisture from concentrates or other products from plant operations, Rotary Dryers are designed and constructed for high efficiency and economy in fuel consumption Whenever possible to apply heat direct to the material to be dried, Rotary Dryers of the Direct Heating Design are used If it is not possible to apply heat direct to the material to Rotary Dryer Design Working Principle 911MetallurgistVertical mills can be operated either wet or dry, depending on the application requirements Wet grinding is commonly used in mineral processing while dry grinding is ideal for cement production Understanding the working principle of vertical mills is crucial in maximizing their efficiency and performance in various industriesWorking principle and characteristics of vertical mill2013年3月1日 Working principle of a coal fired power plant (Niemczk Andersen, 2009) Therefore the air, the coarse and the fine coal particles all have the same temperature T out at the outlet of the mill • The coal drying is described by the term m Nonlinear coal mill modeling and its application to model
.jpg)
Derivation and validation of a coal mill model for control
2012年5月1日 Coal fired power plants are heavily used due to large and long lasting coal resources compared with oil or natural gas An important bottleneck in the operation of this particular kind of plants, however, is the coal pulverization process, which gives rise to slow takeup rates and frequent plant shutdowns (Rees Fan, 2003)In typical coal fired power plants, 2022年10月17日 Normal speed: At Normal speed balls are carried almost to the top of the mill and then fall into a cascade across the diameter of the mill, in this way maximum size reduction is obtained Related: Hammer Mill Ball mill Ball Mill; Principle, Working, and Construction » (2012) is used to develop the coal mill model The following assumptions are made to develop the coal mill model: (1) Coal in the mill is either pulverised or unpulverised, ie different particle sizes are not considered Variations of the mass of coal particles (eg depending on th e moistureModeling and Control of Coal MillDownload scientific diagram Schematic diagram of the working principle of MPS medium speed coal mill [1] from publication: Fault Diagnosis of Coal Mill Based on Kernel Extreme Learning Machine Schematic diagram of the working principle of MPS
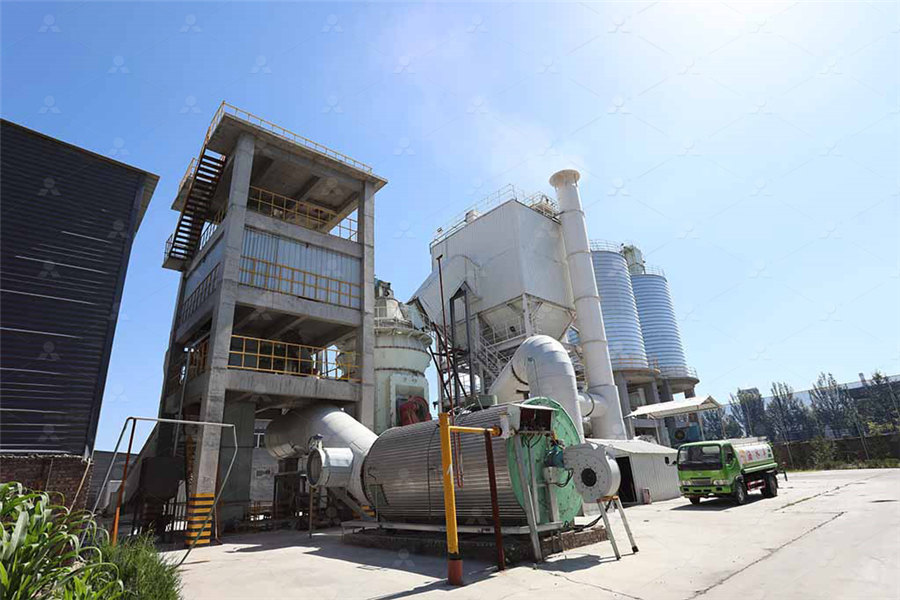
Jet mill working principle
This article aims to describe the working principle of a jet mill A jet mill, Injectable drugs and dry powder inhalants require particlesize distributions in the range of 220 microns with a steep distribution curve and a minimum of fine and oversized particlesI INTRODUCTION AND PRINCIPLES In this presentation we will discuss the principle of the Attritor and its applications The Attritor is a grinding mill containing internally agitated media It has been generically referred to as a “stirred ball mill” There are quite a few types of Attritors; we can categorize them as dry grindWe will discuss the principle of the Attritor and its applications2015年11月1日 From Fig 3, Fig 4, Fig 5, Fig 6 and Table 5, it can be seen that the measured outputs of the proposed model (mill differential pressure, current, outlet temperature) approach the onsite values very well and unmeasured outputs (pulverized fuel flow, mass accumulated inside the mill, outlet moisture content, moisture in accumulated coal inside the mill, mill A unified thermomechanical model for coal mill operationIn addition, coal drying machine is also applied for drying other material of certain humidity and particle size in building materials, Working Principle of Coal Dryer Machine We have been professional on grinding mill, stone crushers, sand making machines, Coal Dryer Zoneding Machine
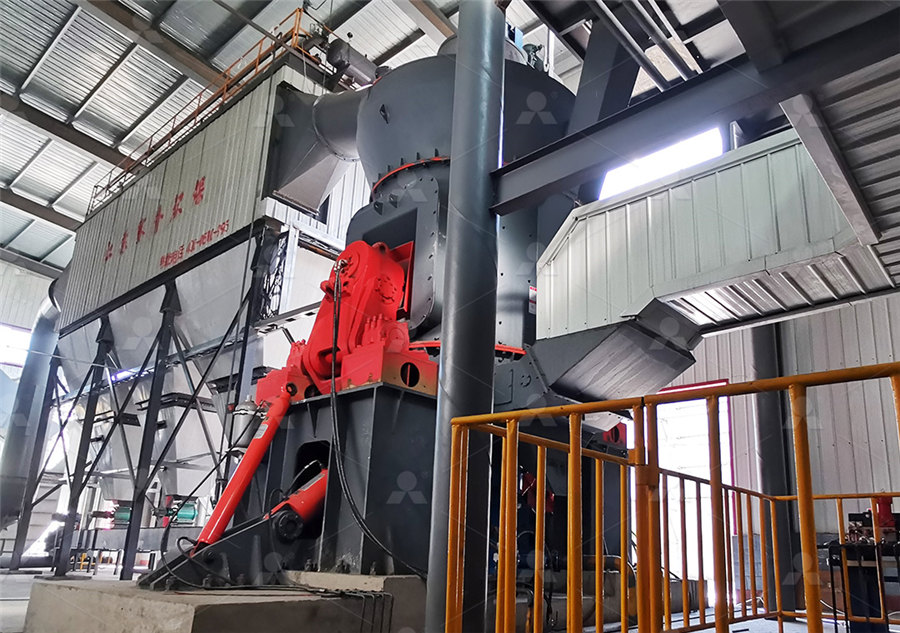
Rod Mills Grinding Mills DOVE
DOVE Rod Mills are supplied in a wide range of capacities and specifications DOVE supplies 2 models of small Rod Mills designed for laboratories milling process, capacity range of (5000g/Hr – 20 Kg/Hr) For small to large scale grinding operations, DOVE Rod Mills are supplied in 15 models, capacity range of (15 TPH – 580 TPH)Ball Mill, Working Principle, Types, Parts, Applications and Advantages Ball Mill Grinding Machines: Exploring the Working Principle, Types, Parts, Applications, Advantages, and Recent Developments Ball mill grinding machines are widely used in various industries for the comminution of materials into fine powdersBall Mill Grinding Machines: Working Principle, Types, Parts Pebble ball mill: Pebble mills are sometimes called jar mill or pot mill which works on the principle of attrition and impact The grinding is effected by placing the substance in the cylindrical vessel or jar vessels that are lined by porcelain or Ball Mill Principle, Construction, Working, and More The surface of the cone mill machine is made of stainless steel material Besides, the mirrorpolished surfaces of the machine have an excellent nonstick and smooth finish Cone Mill Working Principle Now, we are at the core part of Cone Mill Machine Working Principle: A Complete
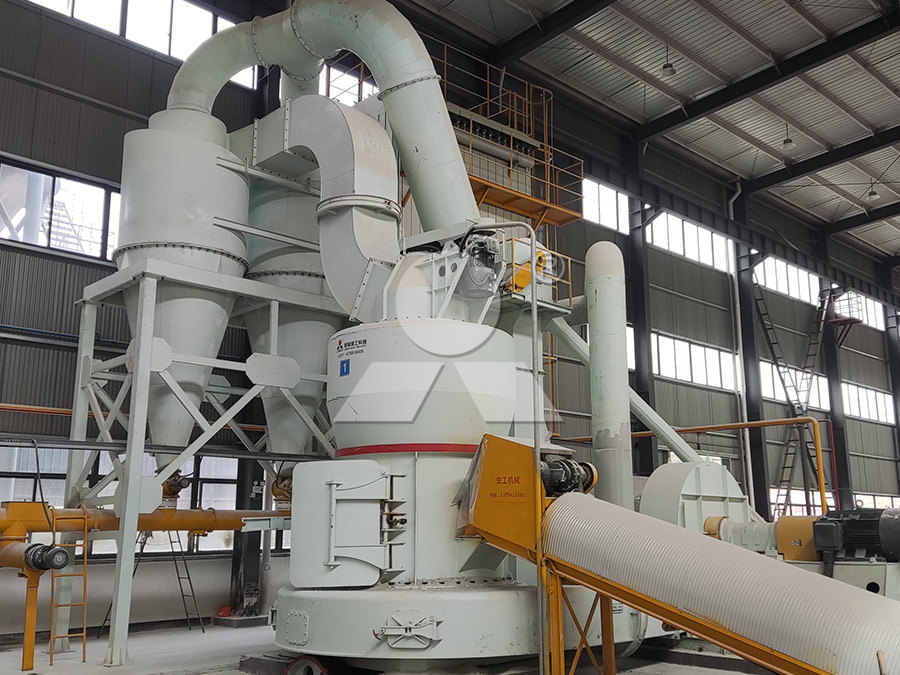
Coal Pulverizers an overview ScienceDirect Topics
The purpose of the coal drying system is drying and grinding the raw coal for stable transportation of Measuring principle is based on the generation of standing radio waves in the et al [84] proposed the hierarchical fuzzy control for normal conditions, and the predictive fuzzy control for abnormal working conditions of the millBall Mill, Construction, Working Principle, Application, Advantages and Disadvantage Ball Mill Applications Critical Speed of Ball Mill The ball mill is used for grinding materials such as coal, The disadvantage of wet grinding includes the necessity to dry the product and high wear on the grinding medium Ball Mill Working Principle, Construction, Applications, Working principle Coal is sent into vertical mill through central entrance by coal feeder, and falls down on the grinding table Under the action of centrifugal force, coal is pushed to the edge of table Under the force of spring loaded roller, coal is compressed and shearedVertical mill for coal pulverizing in power plant Geckointech2024年2月3日 Multimill; Working and principle Last Updated on: February 3, 2024 by Naresh Bhakar Multimill is used widely in pharmaceuticals (granulation section), cosmetics, chemicals, and bulk drugs for cutting granules into small particle sizes by using cutting, Pulverization, and hammering mechanismsMultimill; Working and principle in Pharmaceutical » Pharmaguddu

LOESCHEMILLS
1927 First Loesche coal mill delivered for the Klingenberg power station in Berlin 1953 500th coal mill plant sold worldwide 1961 Introduction of hydraulic spring assembly system 1965 Construction of first pressure mill (LM 122 D) 1980 Delivery of first modular coal mill (LM 263 D) 1985 Delivery of first selfinerting coal grinding plant (LM 212 D) for the steel industry (PCI A mill’s heat balance evaluation was done using an Excel spreadsheet to evaluate the mill drying capacity constraint Coal analysis was done on hard grove grind ability, abrasive indices and calorific value of coal The effect of low calorific value coal was observed on mill’s response to match the boiler energy requirementsPerformance optimisation of vertical spindle coal pulverisersNomenclatureBowl Mills 583 XRS / 803 XRP Bowl mills 58,80 stands for bowl diameter in inches If the number is even then its shallow bowl mill If the number is odd then its deep bowl mill 3 number of rollers three nos X frequency of power supply 50 cyclesIn USA ’x’ means 60 cycles R Raymond, name of the inventorPulverizer Plant OM Aspects2024年2月5日 By knowing the working principle of hammer mills and various aspects that determine production, your equipment will definitely operate optimally Conclusion Clearly, the working principle of hammer mill is simple to understand It only requires choosing an appropriate motor, crushing hammers/knives and material you intend to crushThe Working Principle of Hammer Mills (Stepbystep Guide)