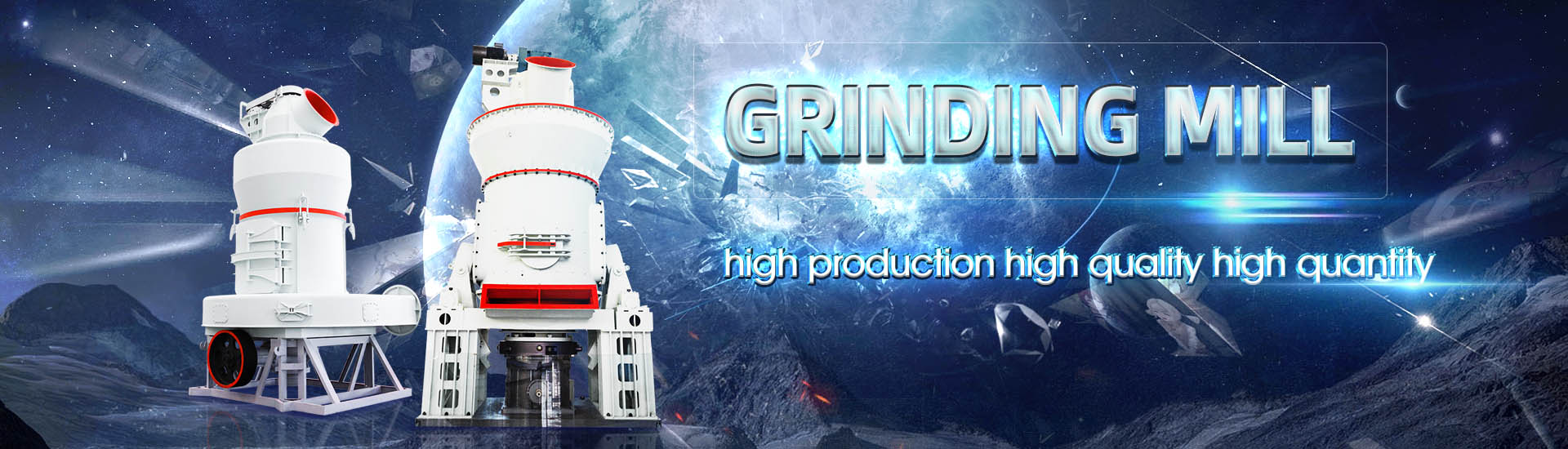
Iron slag crushing magnetic separation environmental protection
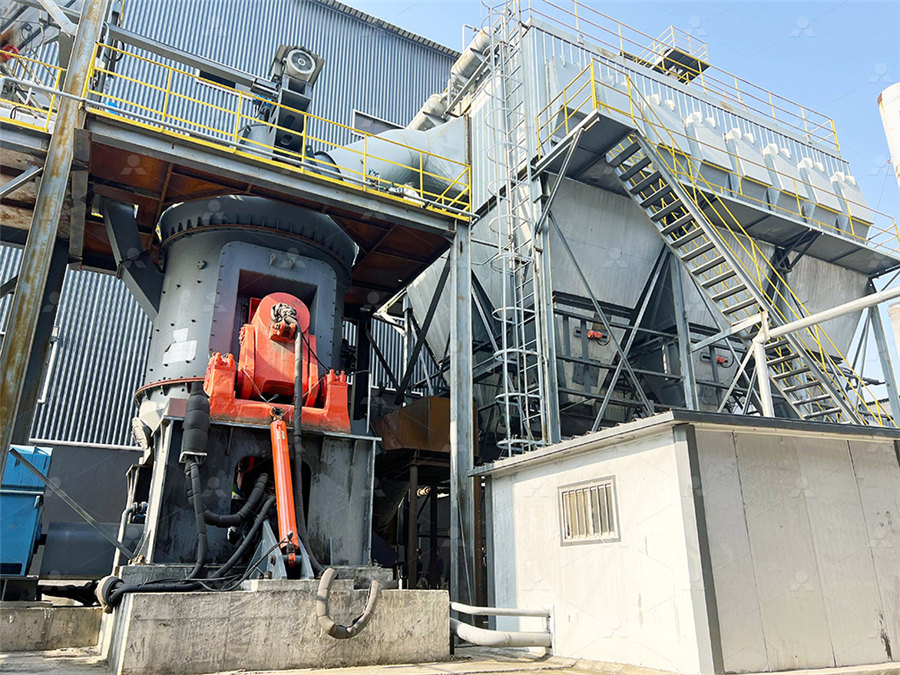
Separation and extraction of iron resources from hazardous
2024年10月1日 Systematically study the influence of magnetic field strength, slag particle size, basicity on the separation of EAF slag magnetic separation, to achieve the efficient separation 2017年2月1日 To improve the efficiency of iron recovery from steel slag and reduce the wearandtear on facilities, a new method was proposed by adding a secondary screen sizer to the Optimization of magnetic separation process for iron recovery 2023年2月1日 In order to solve the problem of solid waste pollution of basic oxygen furnace (BOF) slag in the metallurgical process, this paper took BOF slag as the research object, and Efficient separation of iron elements from steel slag based on Due to limited modes of practices of utilization, huge amount of steel slag is dumped, engaging important agricultural land and causing grave pollution to the environment The best Iron and Steel Slag Utilization: A Comprehensive Analysis
.jpg)
Separation and extraction of iron resources from hazardous
Multistage wet weak magnetic separation of treatment slag resulted in the highest concentrate yield of 4905 % at an basicity of 1, with a TFe content of 56711 %, and 7032 % of the iron 2023年11月7日 Magnetic separation is a highefficiency, lowcost, and selective technique that relies on the magnetic properties of the minerals present in the slags The magnetic properties of minerals are determined according to their Characterization of Magnetic and Mineralogical 2022年4月11日 At present, there are two common methods for recovering iron and iron oxides from BOF slag: reduction and oxidation The reduction method is mainly to reduce the ironcontaining oxides in the BOF slag to metallic iron, Optimization of Iron Recovery from BOF Slag by 2022年1月21日 Results showed that MS with 18 wt% modifier addition exhibited an iron recovery rate of 610%, much higher than that (346%) of the original slag Steel slag is an Novel method for improving iron recovery from electric arc
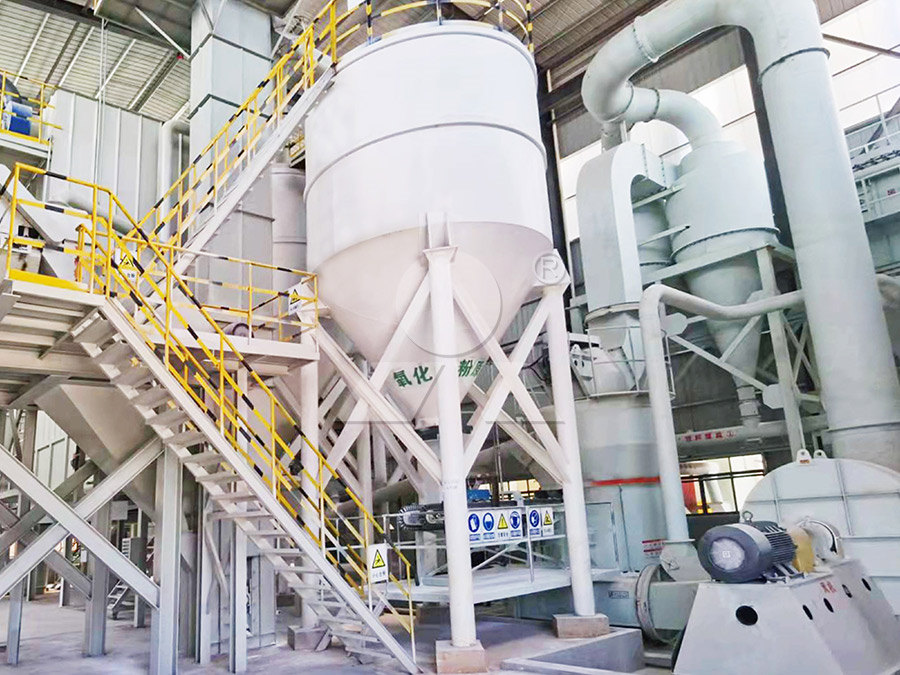
(PDF) An airfluidized magnetic separator and its separation
2024年3月1日 Primary magnetic separation tests on a steel slag fine powder material demonstrate that the air fluidized dry magnetic separator effectively separates inert minerals 2024年3月1日 The presence of magnetic inert minerals (RO phase, Fe 3 O 4, Fe) in steel slag powder 13 enables the separation of these minerals from the slag to enhance its gelling properties and facilitate iron resource recovery, An airfluidized magnetic separator and its separation 2023年11月20日 Mineral process wastes, such as metallurgical slags nowadays, are of significant metals and materials resources in the circular economy The usability of ironmaking slag is well established; however, steel A Review on Environmental Concerns and 2024年10月1日 The main components of EAF slag are Fe x O, Fe, CaO, SiO 2, MgO, and MnOThe EAF slag contains more iron, but it is mainly dominated by RO phase, which is difficult to be recovered by magnetic separation, resulting in low utilization of iron in slag (Liu et al, 2023, Zhang et al, 2019)Separation and extraction of iron resources from hazardous
.jpg)
Life cycle assessment of melting reduction treatment for iron and
2022年11月1日 The raw steel slag refers to the lowgrade steel slag which gets from the cooling and pretreatment of a hightemperature converter After crushing and magnetic separation, the raw steel slag become preselected steel slag (the total percentage of Fe approximates to 395%) and tailings steel slag (Fe% approximates to 16%)2024年4月24日 Magnetic separation technology is a physical separation method that uses the differences in magnetism between matter to separate them from each other by different motion behaviors in a nonuniform magnetic field It is highly efficient, green, and environmentally friendly, with little change in the physical and chemical properties of raw materials Magnetic separation Application of Magnetic Separation Technology in Resource2023年8月5日 The steel slag after crushing magnetic separation and iron has more minerals such as The heavy slag after crushing magnetic separation and iron removal has the characteristics of good density and In line with national industrial policies for energy conservation and environmental protection Taking Xinyu Iron and Steel Treatment and comprehensive utilization of steel slag iron slag2017年2月1日 To improve the efficiency of iron recovery from steel slag and reduce the wearandtear on facilities, a new method was proposed by adding a secondary screen sizer to the magnetic separation Optimization of magnetic separation process for iron recovery

Oxidative modification of industrial basic oxygen furnace slag for
2023年3月1日 The grade of magnetic slag obtained by magnetic separation is 4026%, and the iron recovery is 7095% By grinding the oxidation slag to fine enough, although the grade of magnetic slag is improved, it does not conform to the actual production situation on site, so the particle size should be controlled at 48 µm∼74 µm2024年3月1日 The iron grade in the magnetic products reaches 2181%, which is 688% higher than that of the original steel slag, while the iron grade in nonmagnetic products decreases to 1193%, representing (PDF) An airfluidized magnetic separator and its separation The magnetic steel slag water washing, ball mill, magnetic separation, purification process and comprehensive slag recycling technology and complete sets of equipment developed and developed by CM Mining Machinery can not only realize water recycling, but also have high purification grade of slag steel (TFe>90%), iron content The grade of slag powder reaches 55%Steel slag recycling crushing and grinding production line2022年4月27日 In order to solve the problem of solid waste pollution from basic oxygen furnace (BOF) slag, Lan et al investigated oxidation reconstruction of BOF slag and alcohol wet magnetic separation Optimization of Iron Recovery from BOF Slag by Oxidation and Magnetic

Novel method for improving iron recovery from electric arc furnace slag
2022年1月21日 The iron element in electric arc furnace (EAF) slag is extremely difficult to recycle due to the low specific magnetic susceptibility of the RO phase (a solid solution of FeO, MgO, CaO, and MnO) Landfilling EAF slag is strictly forbidden for environmental consideration because of poisonous Cr6+ leaching The original RO phase could be transformed to a spinel 2015年12月31日 This chapter introduces the principle of how lowgrade iron ores are upgraded to highquality iron ore concentrates by magnetic separation Magnetite is the most magnetic of all the naturally Developments in the physical separation of iron ore: Magnetic 2019年4月9日 PDF This work presents a semismelting reduction and magnetic separation process for the recovery of iron and alumina slag from iron rich bauxite ore Find, read and cite all the research SemiSmelting Reduction and Magnetic Separation for the 2014年1月10日 Two variants of magnetic separation were performed on LD slag The first one deals with treatment of ground LD slag at different particle size fractions of 1 mm, 400 μm, 200 μm and 200 μm by dry magnetic separation This technique may be applied on the coarse fraction of LD slag to recover only iron scrapsRecovery of high grade iron compounds from LD slag by enhanced magnetic
.jpg)
Recovery of high grade iron compounds from LD slag by enhanced magnetic
2013年1月1日 It was shown that 3334% of the wastes can be recycled with 5490% iron recovery and 7443% sulphur removal after dry magnetic separation experiments while 1466% of the wastes can be recycled recycling of iron primarily includes dry magnetic separation of bulk slag, wet stage grinding and magnetic separation, wet magnetic separation for full grain level, finegrained level flotation, and gravity separation [12] Usually, the wet magnetic separation method is used to separate the metallic iron particles form the slag powder [13]SEPARATION OF THE MAGNETIC FRACTION FROM THE SLAGS After BOF slag was oxidized at 1300 ℃ for 240 min and cooled in the furnace (1 ℃/min), the grade of magnetic slag obtained by magnetic separation had a grade of 4026%, a recovery of 7095%, and a P and S content of 0042 and 0456, respectively, which may be used as an important supplement to the raw materials for sinteringOxidative modification of industrial basic oxygen furnace slag for 2024年2月7日 Direct reduction refers to the process of reducing iron minerals in copper slag to metallic iron particles below the melting temperature of copper slag []Using direct reduction–magnetic separation technology to recover iron resources in copper slag has fair recovery effect and short reaction time, which is the development trend of comprehensive Recovery of Iron from Copper Tailings Using a Combined Direct
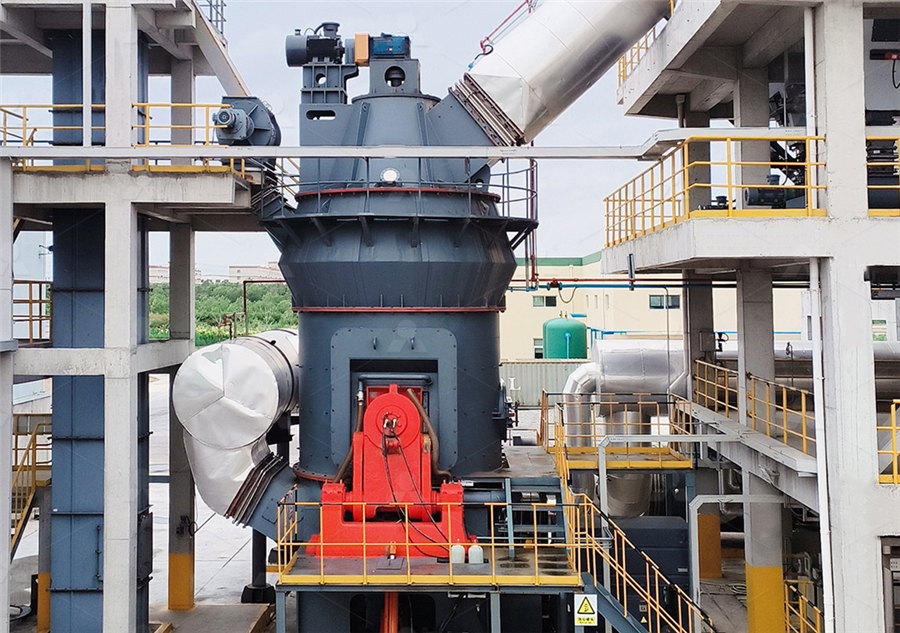
Study on Separation of Iron from Waste Slag of Pyrite Processing
2015年1月22日 The work presented here investigates the optimum conditions for maximum recovery of iron from the waste slag The most advantageous option for industrial trial is roasting of the waste slag under reducing condition followed by magnetic separation selected from various options for recovery of iron from the waste slag The experimental results show that under the 2023年5月15日 Steel slag is the main solid waste generated in the steelmaking process, accounting for 15 to 20% of crude steel output [1]China's crude steel output in 2021 was 1035 billion tons [2], more than half of the global crude steel output (19505 billion tons) [3], and the steel slag output exceeded 120 million tonsIn contrast, the comprehensive utilization rate of Comprehensive utilization of steel slag: A review ScienceDirect2013年11月1日 Request PDF Utilization of nickel slag using selective reduction followed by magnetic separation In order to utilize slag discarded by nickel plants, the selective recovery of nickel and Utilization of nickel slag using selective reduction followed by 2023年3月1日 BOFSP was obtained from BOF slag after removing metallic iron by crushing and magnetic separation BOFSP and SP were ground to below 74 µm, respectively, and dried in a vacuum drying oven for 4 h Previous studies had shown basicity (R=CaO/SiO 2 , a parameter to measure the performance of slag) had a significant effect on the oxidative modification of Oxidative modification of industrial basic oxygen furnace slag for
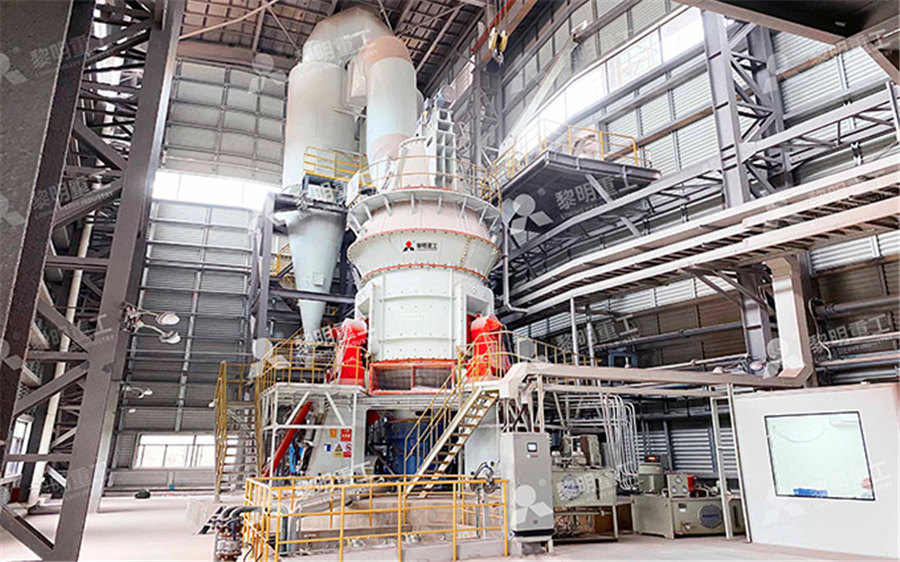
Processing and Reusing Technologies for Steelmaking Slag
The iron/steel slag processing flow is schematically shown in Fig 2 Steelmaking slag is subjected to the following four processes: ① solidify and cooling of the hot molten slag, ② crushing and magnetic separation treatment of the slag to recover the metal iron, ③ crushing and classification of the slag for grain size adjustment2024年3月1日 Coalbased direct reduction (CBDR) in iron ore smelting, emerging as a prominent method in the mid20th century, represents a significant evolution in response to energy crises and environmental concerns, entails the removal of oxygen from solid iron ore to produce solid sponge iron that can be used in electric arc furnace (EAF) steel production Application of coalbased direct reductionmagnetic separation 2021年12月29日 This study investigates the potential to recover iron and chromium from a chromiumbearing carbon steel Electric Arc Furnace (EAF) slag This slag contains indeed about 30 wt% Fe and 25 wt% CrCharacterization of a ChromiumBearing Carbon Steel Electric Arc Magnetic separation is primarily used in solid waste treatment systems to recover or enrich ferrous metals, or in certain processes to remove ferrous materials from solid waste Overhead magnetic separation equipment is used in some large Magnetic Separation an overview ScienceDirect Topics
.jpg)
Steel Slag Recycling: The Definitive Processing Solution
2024年3月12日 Steel slag separation typically employs magnetic separation, aiming to extract useful iron metals from the slag Both steel particles and iron powder in the steel slag exhibit magnetism Therefore, magnetic separators are used to further purify the steel slag, obtaining a mixture of steel particles and iron powder, as well as waste residue2022年2月26日 Blast furnace slag can be processed into the following materials by various processes In China, blast furnace slag is usually processed into water slag, slag gravel, expanded slag and slag beadsWater slag is the process of putting the hotmelt blast furnace slag into water for rapid cooling, which mainly includes slag pool water quenching or furnace front What is Blast Furnace Slag and How to Process It?2014年1月16日 Iron recovery from a lead slag in Henan province was carried out with the technique of coalbased direct reduction followed by magnetic separation Scanning electron microscopy (SEM) was used to investigate the transformation of ironcontaining minerals and the particle size of metallic iron generated by coal reduction The results showed that technique is Recovery of Iron from Lead Slag with CoalBased Direct Reduction 2024年11月1日 SS Varanasi [12] investigated the utilization of SS after crushing and magnetic separation as a flux in steelmaking, discovering that the addition of SiO 2 and Al 2 O 3 enhanced slag stability But this method was only suitable for lowphosphorus slag to avoid increasing the steelmaking burdenRecent research progress on recycling metallurgical waste slag
.jpg)
XRD patterns of LD slag treated by magnetic separation
It was shown that 3334% of the wastes can be recycled with 5490% iron recovery and 7443% sulphur removal after dry magnetic separation experiments while 1466% of the wastes can be recycled 2024年10月1日 Metallurgical solid waste slag is mainly composed of blast furnace slag (Laihao et al, 2024), converter slag, and electric furnace slag (Theint et al, 2021)Its composition is complex, containing iron, calcium, silicon, and magnesium, along with other elements (Jamieson et al, 2019)During iron and steel smelting, these elements exist in the form of oxides in the Process Safety and Environmental Protection ScienceDirect2020年10月31日 iron to form nonmagnetic iron ca rbide lost in the magnetic separation Therefore, the 35 wt% coal addition was the optimal condition for the copper slag direct reduction(PDF) Recovery of Iron from Copper Slag Using CoalBased Direct 2024年8月8日 The presented work offers an innovative process scheme for valorizing PbZn slag, which involves crushing, grinding, and separation techniques to concentrate valuable components (nonferrous metals) This methodology could have a significant impact on the global beneficiation of metallurgical slags since it is significantly more simple, environmentally Exploring the Efficiency of Magnetic Separation and Gravity
.jpg)
Magnetic Separation Technology for Mineral Processing Plants:
2024年5月9日 Magnetic separation technology plays a pivotal role in mineral processing, offering efficient and versatile solutions for separating valuable minerals from gangue materials By harnessing the magnetic properties of minerals, magnetic separators can selectively capture and concentrate target minerals based on their magnetic susceptibility, facilitating highpurity 2023年12月27日 Due to the strong magnetism of the above components, the process of steel slag beneficiation is magnetic beneficiation, and the required equipment is a magnetic separator The magnetic separation of steel slag includes drymagnetic separation and wetmagnetic separation Dry magnetic separation mainly recovers large blocks of iron, while wet Steel Slag Processing Plant Equipment SelectionT he ways for magnetic separation of slag usually va ry with cooling methods of liquid steel slag and its chemical/mineralogical composition Mostly , steel slag magnetic separation process includes crushing/ grinding, screening and magnetic separation':", In order to liberate metallic iro n and other ferrous minOptimization of magnetic separation process for iron recovery 2024年4月15日 This results in an increase in the grade of the iron concentrate and the small portion of the metallic iron is ground too finely with the chondrites into the magnetic separation tailings At the grinding time of 45 min, the magnetic separation iron ore concentrate exhibits improved iron grade and recovery rate (9361% and 9071%, respectively)Iron recovery from lead smelting waterquenching slag by
.jpg)
The recycling and reuse of steelmaking slags — A review
2019年7月1日 The way that the slag has been cooled can have an influence on the amount of metallic iron that can be recovered from the slag (Wang et al, 2012) The magnetic separation process and the crushing process are often repeated several times to increase the amount and quality of metallic iron that can be recovered from the process (Horii et al, 2013)