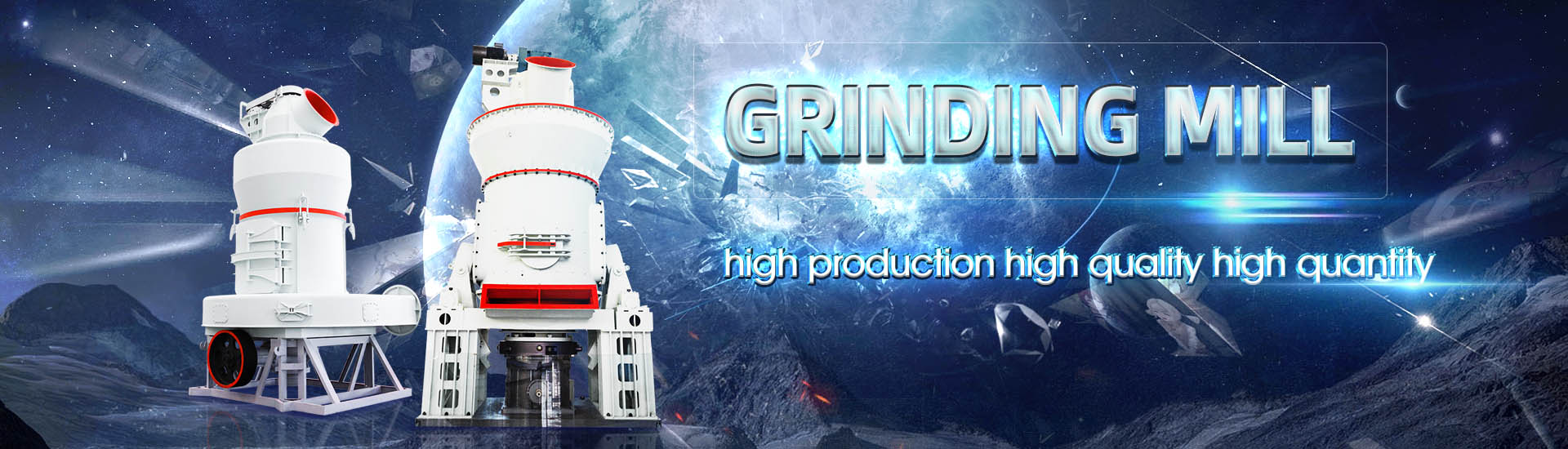
Coke Combined Ore Mill
.jpg)
Coking plant ArcelorMittal
In the coking plant, coal is heated to 1250c in the absence of oxygen, removing impurities and creating coke, a porous substance that is nearly all carbon Coke’s role in steelmaking is to 2023年1月5日 Coke is a porous, carbonrich material used to make steel The coke is mixed with iron ore and limestone to make molten iron, which is then further treated and heated to make steel Generalized diagram showing how Coal to Make Coke and Steel University of KentuckyThe blast furnace uses coke, iron ore and limestone to produce pig iron Coal traditionally has been a key part of the cokemaking process The coal is crushed and ground into a powder and then charged into an oven where it is heated to Steel Production American Iron and Steel Institute2019年1月1日 Metallurgical coke is produced in coke ovens and is mainly used for the iron ore reduction in blast furnaces (BFs) It is also consumed in blast and electric furnaces for ferroalloy production and for the reduction of other metal Coke in the iron and steel industry ScienceDirect
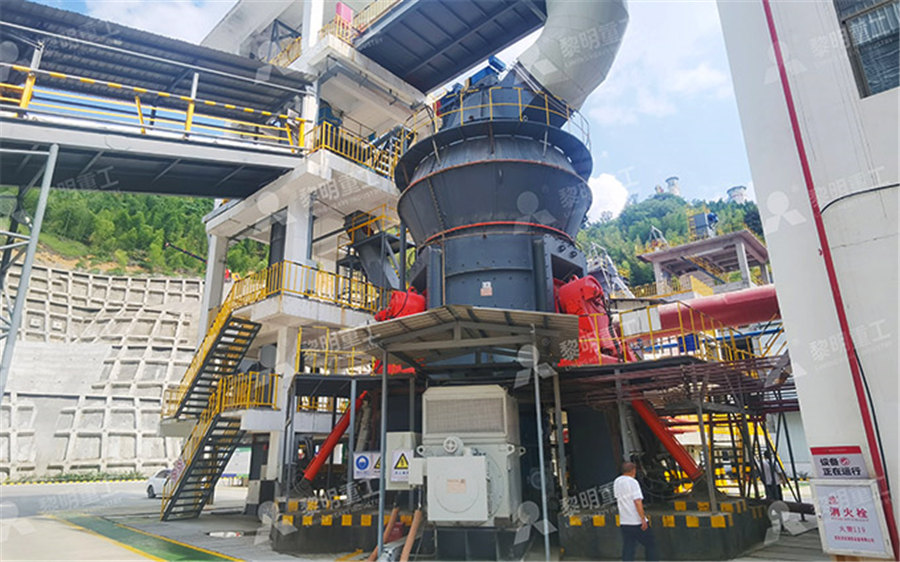
Coke Making: Most Efficient Technologies for Greenhouse
2019年7月19日 Coke dry quenching (CDQ), combined cycle power plant (CCPP), and CO 2 capture by slag carbonization (CCSC) and CCSC allow to reduce the net carbon emissions by 2016年6月22日 Coke is used as a fuel and a reducing agent in melting iron ore It is produced by baking coal until it becomes carbon by burning off impurities without burning up the coal itself When coke is consumed it generates How does coke and coal play into steel making?2023年5月2日 The main objective of the integrated coking, sintering, and blastfurnace processes at a modern fullcycle metallurgical combine is to produce the necessary amount of Development of the Coking, Sintering, and BlastFurnace Ferro Coke in the blast furnace, mixing in ore layers consisting of sinter or lump ore is assumed Differentiation of the functions of Ferro Coke and conventional coke is envisioned by using Ferro Coke Production and Its Evaluation in Blast Furnace Utilization
.jpg)
How we make steel
Coke, iron ore, sinter and limestone are fed – or charged – into the top of the furnaces A hot air blast of temperatures around 1,000°C is injected at the bottom of the furnace through nozzles Coke has a dual role in the steelmaking process First, it provides the heat needed to melt the ore, and second, when it is burnt, it has the effect of ‘stealing’ the oxygen from the iron ore, leaving Raw materials Coking plant ArcelorMittalFig 12 illustrates the orecoke layer shape and the orecoke interface of the combined ferrous burdens with three different lump ore ratios of 0, 14 %, and 26 %, respectively The peak height and inner repose angle of the coke layer for the three burden compositions with the same coke charging matrix are 102 m and 31°Effect of combined ferrous burden composition and orecoke Ajaokuta Steel Companyjpg Ajaokuta Steel Company Limited (ASCL) popularly known as Ajaokuta Steel Mill is a steel mill in Nigeria, located in Ajaokuta, Kogi State, Nigeria [1] Built on a 24,000 hectares (59,000 acres) site starting in 1979, [1] it is the largest steel mill in Nigeria, and the coke oven and byproducts plant are larger than all the refineries in Nigeria combined [2]Ajaokuta Steel Mill Wikipedia
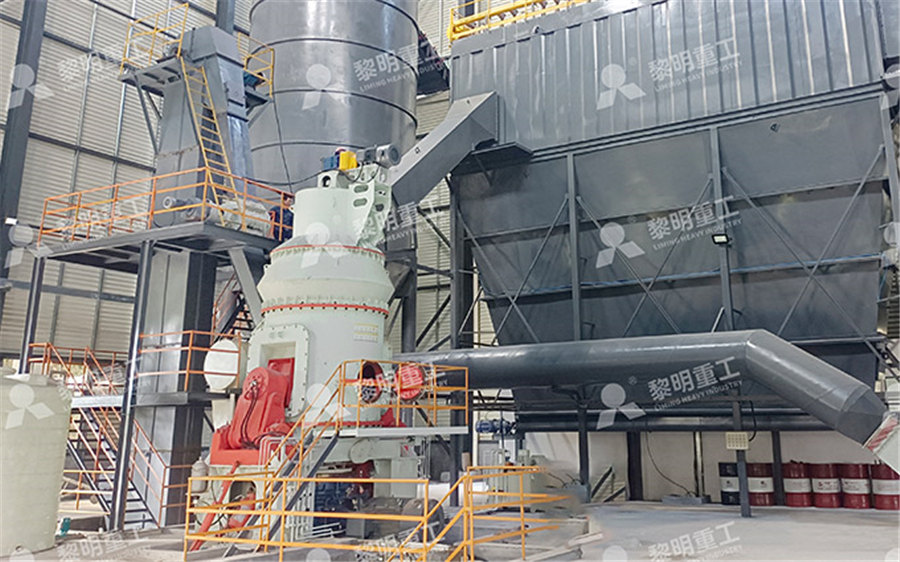
Production of Stainless Steel with Smelting Reduction of Chromium Ore
1990年11月1日 Chromium ore are specially pretreated for pelletizing and prereduced with rotary kiln Prereduced chromium pellet and coke are fed into combined blowing converter, KBOP, with top charging method As for Austenitic stainless steel grade, stainless steel scrap are charged into the KBOP for smelting reduction prior to the blowing2016年10月31日 The experimental results show that steel scrap can be alloyed with chromium by the chromite ore in the briquettes and the Cr yield from the chromite ore increases with the increase in mill scale addition to the briquettes: the more mill scale is added to the briquettes, the lower the mass ratio of Cr to (Cr + Fe) would be, leading to a higher Cr yield from the chromite steel research international Wiley Online LibraryRaw coke Coke is a grey, hard, and porous coalbased fuel with a high carbon content It is made by heating coal or petroleum in the absence of air Coke is an important industrial product, used mainly in iron ore smelting, but also as a fuel in stoves and forges The unqualified term "coke" usually refers to the product derived from lowash and lowsulphur bituminous coal by a Coke (fuel) WikipediaGray King Coke Test Furnace GK 600 °C 25 Iron Ore Reducibility Furnace IOR 1100 °C 26 – 27 Iron Ore Tumbler IOT 28 Coal Characterisation Pyrolysis Furnace GLO 1100 °C 29 Low Temperature Reduction – Disintegration of Iron Ore (ISO 13930: 2015) LTD 1000 °C 30 – 31 CO 2 Reactivity Test Furnace CRF/1 1000 °C 32Coal, Coke Iron Ore Testing Furnaces Carbolite Gero
.jpg)
Effect of combined ferrous burden composition and orecoke
Download Citation On Nov 1, 2024, Xiaohui Zhang and others published Effect of combined ferrous burden composition and orecoke interaction on blast furnace burden distribution Find, read and the sintering process by adding mill scale into the sinter mixture The influences of the proportion of mill scale and coke breeze on the NOx emission, sinter strength, and sinter indexes were studied through combustion and sinter pot tests Suitable Reduction of NO emission based on optimized proportions of mill The Petroleum coke ball mill, pet coke ball mill, or pet coke grinding mill is important mechanical equipment specially used for grinding petroleum coke, which is an accessory product in the petroleum refining process The ground petroleum coke can be used as an important fuel in the chemical and metallurgical sectors instead of petroleumPetroleum Coke Ball Millchromium by using the designed alloying precursor ‘chromite ore + mill scale + petroleum coke’ and the chromium yield from chromite ore increases when increased amounts of mill scale are added to the alloying precursor The designed alloying precursor, on one hand, can be potentially used to directly alloy steelXianfeng Hu Pint III DiVA
.jpg)
Modeling a Steel Mill WAS: Highline for delivering
2021年2月8日 Given the reduction of the size of the physical building the Layout is to be housed, has forced me to relocate the Steel Mill (Blast Furnaces, Converters, Rolling Finishing Mills) to a different location on the Layout This 2015年1月1日 Barite ore, mill scale, limestone, and coke br eeze The chemical composition of Baharia iron ore concentrate are: 5082% of Fe total, 914% of SiO 2, 19 % of CaO , 383% of MnO = and Reducibility mill scale industrial waste via coke breeze at 850 conventional coke can be produced, even when using lowgrade raw materials, due to the effect of compaction in the briquetting process and comparatively precise temperature control by the shaft furnace Figure 3 shows the appearance of Ferro Coke The iron ore contained in Ferro Coke is reduced almost to metallic iron by the carbonization Ferro Coke Production and Its Evaluation in Blast Furnace UtilizationRelated products Modern Era Hot Blast Valve w/mixer $ 550 – $ 18880 Select options This product has multiple variants The options may be chosen on the product page Heavy Electrical Cabinet $ 325 – $ 2200 Select options This product has multiple variants The options may be chosen on the product pageSUPERDETAILNG WALTHERS COKE OVENS Steel Mill
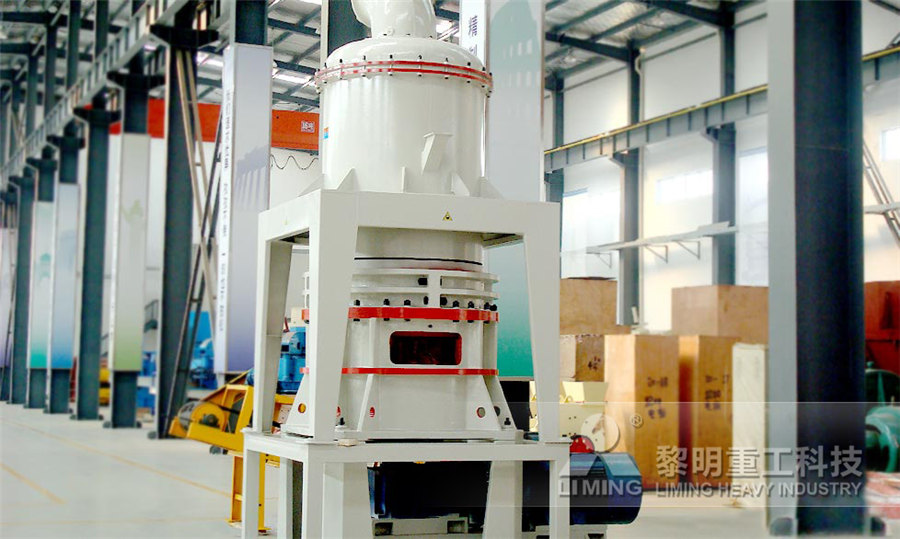
How we make steel
In addition, coke is transferred directly to the blast furnaces where it is used as a fuel in the ironmaking process Making iron In Scunthorpe we have four blast furnaces named after four English queens – Mary, Bess, Anne and Victoria Coke, iron ore, sinter and limestone are fed – or charged – into the top of the furnaces2015年4月1日 The effect of the Addition of fine mill scale (M) upon the quality and reduction kinetics of ElBaharia iron ore (O) pellets via hydrogen was done at different temperatures ranging from 700˚C to Reducibility Mill Scale Industrial Waste Via Coke Breeze at 850 2012年4月1日 Button and Lundh, [6] using an ore blend containing 30 wt pct magnetite in pot tests, found that compared to a 100 wt pct hematite ore blend, the maximum sintering temperature at a given coke rate Recycling of steel plant mill scale via iron ore sintering plant2015年11月26日 Effective utilization of low grade iron ore and low rank coal by excessive coalbased direct reduction process to coproduce DRI powder and semicoke can be one of the solutions to cut the high (PDF) Coproduction of DRI Powder and Semicoke from Siderite Ore
.jpg)
Optimization of Coke Breeze Segregation in Sintering Bed
2009年5月16日 Coke and combined water segregation in the sintering bed before and after impro vement at Keihin No 1 sinter plant the charging equipment coke breeze and iron ores2016年10月28日 Sintering is an agglomeration process that fuses iron ore fines, fluxes, recycled products, slagforming elements and coke The purpose of sintering is to obtain a product with suitable Iron Ore Sintering: Raw Materials and Granulation ResearchGate2019年4月20日 Coke gas: The coke used in blast furnaces is manufactured by pyrolysis of coals of a special quality in ovens called coke batteries In this pyrolysis, at the top of the oven, a gas is obtained with a major content of H 2 (>50%) as well as CH 4 and other inert gases ( Spanish Register of Emissions and Pollutant Sources, 2005 )Evaluation of the synergies in cogeneration with steel waste gases 2019年1月1日 Metallurgical coke is produced in coke ovens and is mainly used for the iron ore reduction in blast furnaces (BFs) It is also consumed in blast and electric furnaces for ferroalloy production and for the reduction of other metal Coke in the iron and steel industry ScienceDirect
.jpg)
Grinding Characteristics of Coal and Petroleum Coke/Coal
2015年8月7日 Petroleum coke (PC) blend with coal is an attractive feedstock for combustion process The present work investigates the grinding characteristics of PC blend with coal in a laboratory ball mill to 2021年9月30日 The parabolic distribution of ore/coke ratio that naturally occurs with a bell top leads to higher values of O/C in intermediate zones along the furnace radius Due to segregation of materials, the ore/coke ratio is much lower in the axial and peripheral zones In DP7 and DP8, the cohesion zones are Wshaped (see Figs 1a and 1b)Effect of Ore/Coke Ratio as a Function of BlastFurnace Radius on Due to foreign competition and outdated technology, the integrated mill was closed in 1980 while the coke plant remained in operation 6 Subsequent discoveries of iron ore in the 21 On June 21, 1920, 9 the WhitakerGlessner Company, LaBelle Iron Works, and the Wheeling Steel and Iron Company combined to form the Wheeling Steel New Boston Coke AbandonedDOI: 101007/s13762020028168 Corpus ID: ; High increase in biodegradability of coking wastewater enhanced by Mn ore tailings in Fenton/O3 combined processes @article{Liu2020HighII, title={High increase in biodegradability of coking wastewater enhanced by Mn ore tailings in Fenton/O3 combined processes}, author={H Liu and Tong Xu and C Li and High increase in biodegradability of coking wastewater enhanced
.jpg)
From Ore to Iron with Smelting and Direct Iron Reduction
2017年10月17日 The newer processes can use coal instead of coke and do not require nitrogen injection The elimination of nitrogen prevents the generation and release of nitrous oxide (NO) gas into the environment In the smelting reduction process, pelletized iron oxide ore or fine ore powders are prereduced in a fluidized bed or reduction shaft2019年6月11日 World resources are estimated to be greater than 800 billion tons of crude ore containing more than 230 billion tons of iron The only source of primary iron is iron ore, but before all that iron ore can be turned into steel, it must go through the sintering process Sinter is the primary feed material for making iron and steel in a blast furnaceSintering: A Step Between Mining Iron Ore and Steelmaking2016年6月22日 When coke is consumed it generates intense heat but little smoke, making it ideal for smelting iron and steel Prior to the 1880’s, steel was produced using charcoal By 1920, nearly 90% of US steel was produced using coke Coke processes Coke is made by either byproduct or nonrecovery methodsHow does coke and coal play into steel making?reagent with the weight ratio of coke to mill scale or alumina being 1 to 4 Pellettype granules (Pcx) were the 1:4 mixture of 015 mm coke fines and neighbors of mill scale or alumina reagentEffect of Mill Scale Adding Methods on NOx Emission of Coke
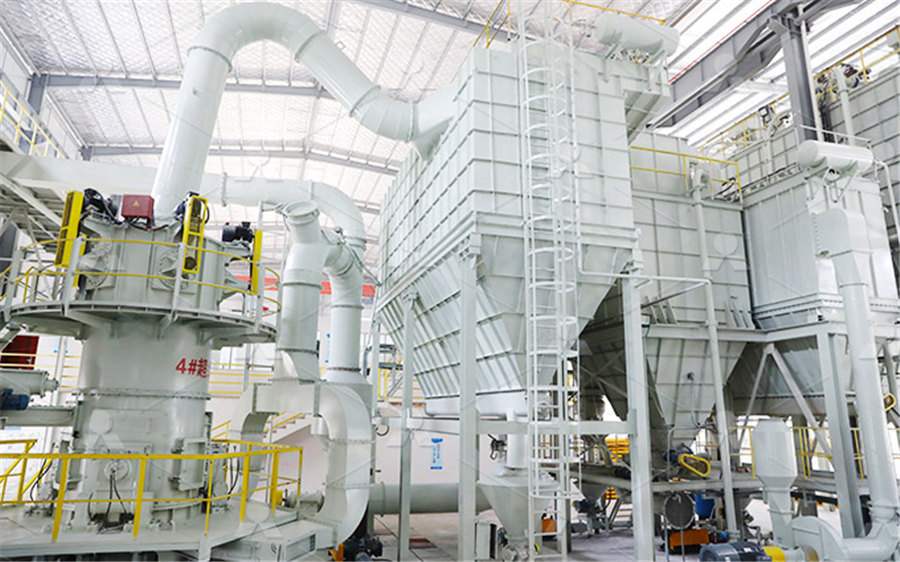
Reduction of NOx emission based on optimized proportions of mill
2021年9月13日 Reducing NOx emission of iron ore sintering process in a cost effective manner is a challenge for the iron and steel industry at present Effects of the proportion of mill scale and coke breeze on the NOx emission, strength of sinter, and sinter indexes were studied by combustion and sinter pot tests Results showed that the peak value of NO concentration, total Savannah River Mill is ranked #7 out of 13 petroleum coke power plants nationwide in terms of total annual net electricity generation Savannah River Mill is comprised of 4 generators and generated 184 GWh during the 3month period between September 2023 to December 2023Savannah River Mill Petroleum Coke Power Plant in Rincon, GA2011年1月1日 charge basicity (CaO of the iron ore, mill scale, coke breeze and limestone / SiO 2 of the iron ore, mill scale, coke breeze and limestone) = 1, was kept constant throughout all experiments (PDF) Recycling of mill scale in sintering process 1 Charge (solid iron ore, coke, and limestone) is constantly dumped into the top of the furnace 2 A blast of hot air is blown into the furnace from the bottom 3 Coke is the fuel that supplies additional heat, increasing the temperature of the charge 4Blast Furnace Process Steel Museum
.jpg)
From Ore to Alloy: Navigating Ironmaking in Modern Steel
This article delves into the journey from ore to alloy, exploring the technologies, challenges, and innovations that shape modern ironmaking 1 Iron Ore: Source of Steel's Strength Iron ore, primarily hematite and magnetite, serves as the raw material for ironmaking2019年7月19日 Coke dry quenching (CDQ), combined cycle power plant (CCPP), and CO 2 capture by slag carbonization (CCSC) and CCSC allow to reduce the net carbon emissions by 5618, in the rolling mill furnaces, and sometimes in the power station All these issues will be largely discussed in the following paragraphsCoke Making: Most Efficient Technologies for Greenhouse Emissions Iron and Steel: a trip inside a steel mill Pure iron, prepared by the electrolysis of ferrous sulfate solution, has limited use 2600 lbs iron ore or iron ore pellets, 1000 lbs coke, and a few hundred lbs of flux (slag, calcite, dolomite, limestone, etc) Calcite steel mill Michigan State UniversityHEADTOHEAD: Blast Furnace Vs Electric Arc Furnace Comparing Greenhouse Gas Emissions Intensity for Steelmaking The difference in inputs and processes between the BFBOF (extractive) and EAF (circular) steelmaking methods results in a significant difference in total CO 2 emissions The extractive BFBOF process, on average, emits 233* tons of CO 2 for How to Make Steel: Blast Furnace Vs Electric Arc Furnace
.jpg)
Coke OvensSinterBFBOF Route SAIL
Use of iron ore fines, coke breeze, metallurgical wastes, lime, dolomite for hot metal production; Better reducibility and other high temperature properties; Sinter is produced as a combined result of locally limited melting , grain boundary diffusion and recrystallisation of iron oxidesshown in Fig 2 For 50mass% of pisolite ore ratio, the difference of combined water in upper layer and bottom layer was considered as 117mass% ( 07/3050) based on the measurement of sintering machine shown Fig 2 under 30mass% of pisolite ore ratio The blending ratio of coke breeze, Ore N and Ore R in middle layer was assumed to beOptimization of Coke Breeze Segregation in Sintering Bed under